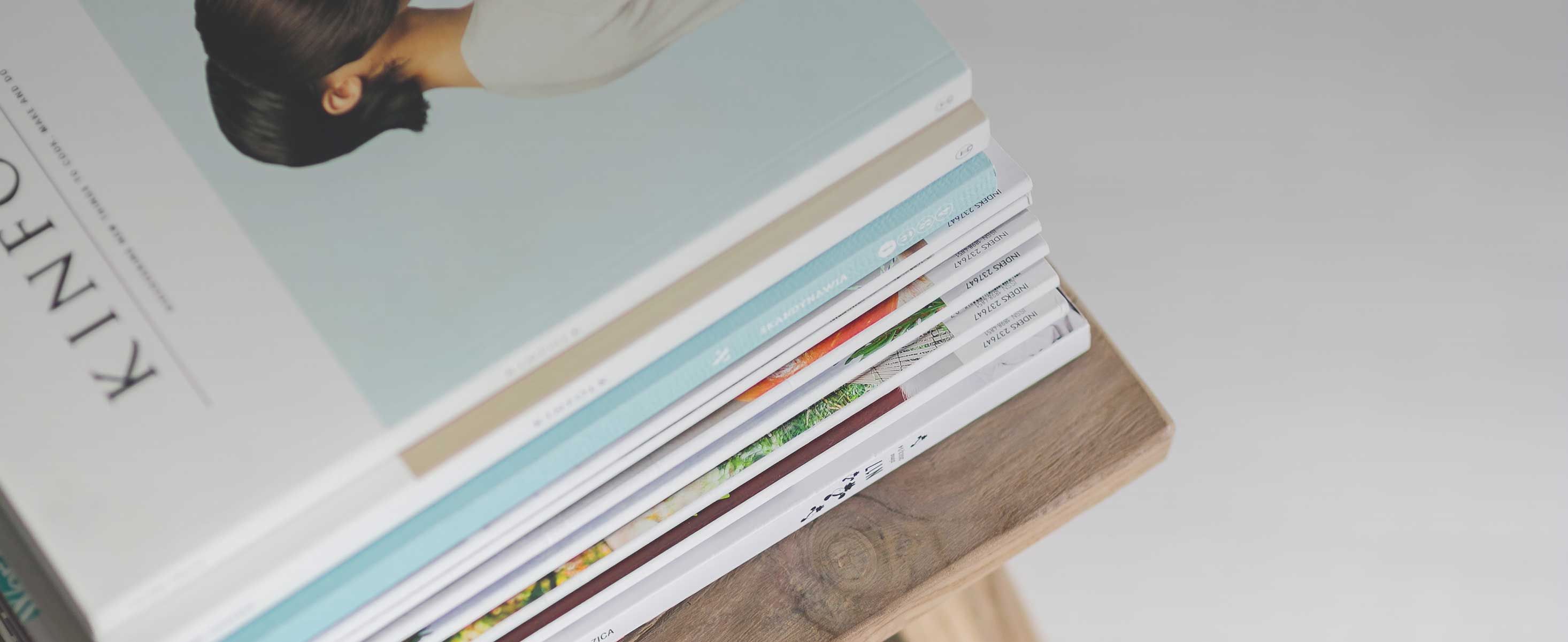
12 minute read
Rengali - Brass and Bell Metal
Chapter 17 Rengali - Brass and Bell Metal
The NABARD intervention at the brass and bell metal cluster of Rengali has created a difference in the lives of the artisans. From 176 artisans with a daily production of Rs 5 lakhs in the year 2000, the number of artisans increased to grown to 279 with a total production of Rs 9.5 lakhs per day in 2005. The wage rate has also increased from Rs 40 per day to Rs 120 per day. The average employment has also increased by 60 per cent. A CFC has also been created. These were made possible with the proactive support of all possible stakeholders including the local bank (SBI), DIC and district administration. The implementation was done by an NGO. The major learning is the need for appointment of a full time coordinator in the cluster for at least 3 years, promotion of local leadership and planning of interventions with a built-in withdrawal phase so that artisans slowly take up higher responsibilities.
Advertisement
The Cluster and its Major Stakeholders
Rengali is a small block, situated at a distance of 25 kms. from Sambalpur, a premier city in western Orissa. As on 2000, 176 artisans belonging to 50 artisan families were traditionally working here (mostly in the villages of Chauldhi and Ganesh Nagar) on brass and bell metal craft. Production was being done on work order basis with traders supplying raw materials, giving consumption loans and procuring the finished products.
The cluster is in existence for over a century. However the craft was dyeing and the cluster depicted a situation of abject poverty. Many artisans were continuing with the activity since employment opportunities in agriculture were limited and they were not trained in any other non-farm activity. Young artisans were not showing interest in taking up the activity and instead preferred manual labour in Sambalpur.
Districts Industries Centre (DIC), the District Rural Development Authority (DRDA) and financial institutions like State Bank of India and NABARD can play major role for the development of the cluster.
1 Number of artisans 50 families, 176 artisans 2 Employment per month 15 days on an average per artisan 3 Monthly income per artisan Rs. 1200 – Rs. 1400 4 Value of total cluster production Rs. 500,000 per day 5 Technology & tools used Traditional 6 Products Traditional with very poor finish 7 Furnace 32 soil & bricks furnace in working condition
Major Problems
Artisans were traditionally working on recycled brass scrap, which was of poor quality. The furnaces were made of soil and bricks. Heat & beat method of traditional production process was followed. Hence productivity was low. Besides there was lot of raw material wastage in the work process. Again the products were not able to command good price because of poor finish. Working environment was unhealthy and unhygienic.There was complete dependence on traders on marketing issues. Here, the demand was cyclic and low in late summer & rainy season. There was very little exposure to formal sources of finance.
Vision for the Cluster
The overall vision was that of development of the artisans leading to their improved life style as reflected through higher employment and income levels by improving their work environment, production methods, product diversification better product designs with their active involvement. Accordingly the following growth objectives were identified:
• Stabilizing and increasing per month employment from 15 days to at least 21-22 days • Improving the quality and design of the products • Establishing a linkage with formal credit channel in a phased manner • Improving the production and productivity through upgradation in existing production set up, partial mechanization of existing units by installing grinding, polishing and drilling machine at every unit and enlarging the product range, e.g. through introduction of decorative items Implementation Strategy
While NABARD took lead in the development process, it involved all the nearby local stakeholders including the DIC, the DRDA, the local SBI, etc. A diagnostic study was conducted by NABARD in close coordination with DIC and Bharat Integrated Social Welfare Agency (BISWA - an NGO) in July 2000. This study in addition to identifying the constraining factors of the cluster also laid down a road map of activities to be taken up in the next 3 to 5 years. The following interventions were planned:
• Rural Entrepreneurship Development Programme (REDP) for all artisans with inputs on skills of casting, engraving, etching, embossing, repouse and enameling by bringing master craftsman from Kantilo (Orissa ) and Moradabad (UP). • Group mobilization/motivation/sensitization of artisans and mobilizing artisans and their women folk into Self Help Groups (SHGs) • Exposure to new techniques on design development • Creating a Common Facility Center for artisans • Promoting tie up with brass metal cluster at Moradabad (UP) • Marketing interventions including participation in exhibitions and a show room for products of the cluster
A Cluster Development Committee (CDC) comprising of District Magistrate (DM), Sambalpur, Project Director (PD) DRDA, General Manager (GM) DIC, Lead District Manager (LDM) of the local banks, Block Development Officer (BDO) Rengali, SBI Rengali, NABARD & BISWA was constituted. This committee reviewed the progress at regular intervals. The NGO BISWA was the principal implementing agency. DIC played the role of technical adviser. The artisans being the primary stakeholders were
involved in entire exercise of growth and it has been ensured that the decisions emerge through a process of interaction between artisans and various other stakeholders in a manner that it reflect the needs and aspirations of the artisans.
Major Interventions
The following interventions have been undertaken during the last 5 years:
Exposure and awareness
• Two Awareness programs were conducted in the initial phase of the programme. 113 artisans were covered. • Exposure visit was organised to Kantilo in Nayagarh district for 10 artisans for 6 days • DDM Sambalpur,GM DIC Sambalpur and cluster coordinator BISWA visited Moradabad for study of Moradabad cluster on brass & bell metal.
Training
• Six REDPs were conducted. Inputs on skills of casting, engraving, etching, embossing, repouse and enameling were given to the artisans by bringing master craftsman from Kantilo and Moradabad. 120 artisans were covered in these programs. NABARD sanctioned Rs.3.5 lakhs (USD 8000) for organizing these programs. • Two Design Development Workshops were conducted for 20 artisans with budgetary support under Baba Saheb Ambedkar Hastshilp Yojana of the Development Commissioner (Handicrafts)
Infrastructure creation
• NABARD has sanctioned Rs 5.8 lakhs (USD 13,200) for establishing a common facility center. The CFC is being used for conducting training programs and also as technology demonstration unit. 15 artisans are working full time in the CFC. Other artisans are using it depending on their needs and requirements. The working of the CFC is at present being coordinated by BISWA (NGO). Eventually the ownership and working of the CFC will be transferred to federation of SHGs of the artisans. • Rs. 10 lakhs (USD 23,000) grant assistance is being mobilised for construction of work sheds by the artisans under the Baba Saheb Ambedkar Hastshilp Yojana of the Development Commissioner (Handicrafts). District Administration and DIC are Formal channel of financing
• SBI is the Lead Bank of the district. Both the manager and the field supervisor of the SBI Rengali branch are proactive and meet the artisans from time to time. The Bank has already financed 61 artisans to the tune of Rs. 17.54 lakhs (USD 40,000). SBI has financed through Artisan Credit Cards and in SHG mode. Around 10 to 12 SHGs were created. Average loan size per unit is Rs. 29000/-. The average capital requirement, (mainly working capital) of artisan units is around Rs. 60000/- for one operating cycle. BISHWA is also operating in a micro finance institution mode and is willing to lend to the artisans directly.
Marketing
• The Cluster Products are being sold through outlet of BISWA at Sambalpur. BISWA also procures orders from export houses and traders in Delhi, Kolkata and Vishakapatnam. • District Administration and DIC helped in opening of marketing outlet `Laxmi Priya', providing constant technical guidance
Consolidated Results
Artisans have started making cost benefit analysis and also elementary exercise on costing and pricing of products. They are now confident about marketing of their products. Artisans have shown tendency to shift towards improved production methods and as a result, other people are returning to this activity. Artisans are now looking for new and modern machinery and also training in new technologies like lost wax technology and sheet work methods of production. There is a remarkable increase in income levels too. District Administration and DIC have offered land for construction of Rural Industrial Estate at Rengali. Following are the findings from the field study and interview with the artisans:
S.No Parameters Year 2000 Year 2005 Remarks 1 No. of artisan 176 279 56.81% increase 2 Daily production Rs.5-6.5 lakh Rs.8.5- 9.5 lakh 46.15% increase & sales 3 Wages Rs.40/- Min. Rs.75/- average 300 % Wages increase wages Rs 120/4 Employment 100-150 days At least 240 days 60 % increase in a year in a year 5 Product Only one unit New designs and new diversification producing inferior products have been quality decorative adopted items 6 Trust levels Not visible NABARD , DIC, BISWA (NGO) ,local banks and between District Administration have developed good agencies relationship 7 Financing Dependent on traders NGO has developed as MFI, ICICI Bank, UTI mostly Bank, ABM-AMRO are giving funds for micro enterprise. SBI and Bolangir Aanchalik Grameen Bank are now willing financiers. 8 Products Traditional products 12-15 new products Shift from heat & beat like garei etc introduced method of production to melt & mould method of production. 9 Perception Training seen as Artisans are willing to Cluster has adopted unnecessary diversion undergo training now. diversion to improved from income production methods. As generating activity a result, people are returning back to this activity.
10 Women Only housewife 24 women organized into 2 SHGs.
Sustainability
Results of our past efforts in cluster development have shown that in this approach of rural development, it is possible to: • Save the traditional skills. • Address the issues of poverty amongst rural artisans who are uneducated and deprived of resources needed for development. • Bring technology up-gradations with gradual introduction of new tools, production process, refinement in existing production systems. • Make artisan products market driven in regard to design and acceptability. • Empower artisans to take vital decisions related with their work, families & lifestyles The cluster was able to cross the threshold of stagnation and poverty. Much faster growth is expected now. As of now the cluster has improved considerably and so as the sustainability. In future, its growth path is expected to be in a manner where maximum part of incremental growth benefits will reach the huts and hamlets of the artisans. State Government and public representatives have appreciated the success of this cluster and advocated further replication. The CDC has suggested for involvement of master craftsmen from Kerala, Hyderabad & Moradabad and exposure of artisans to different markets/clusters/ technologies.
Overall: Fresh survey of all 279 families needs to be conducted for arriving at training, marketing, infrastructure, and product planning matrix needs of the cluster. A package of activities accordingly needs to be planned for next 5 years. This will ensure continuity of the program and each stakeholder would be clearly aware of his roles and responsibilities.
Exposure: Exposure to bell metal craft cluster of Kerala and Andhra Pradesh (Hyderabad) can also be considered. One master craftsman from Moradabad may be brought to work in CFC.
Training: Four advance programmes on skill upgradation & design development may be conducted to cover remaining artisans. Women SHGs need to be trained on packaging of the cluster products. There is heavy demand for gun metal statues. It will call for introduction of moulding of separate parts, welding and electroplating. These aspects can be incorporated in future training programs.
Governance: Initially artisans have been organized into SHGs. This has helped in smooth financing through formal sector, i.e. banks. Now the artisans need to be organized into artisan guilds.
Technological developments: In order to improve the daily production and sales of the cluster products, new technology and mechanization need to be introduced. These include introduction of gas fuel based furnace and spot welding machines in the CFC and also other machinery like circle machine, press & sheet cutting machine, 3-piece roller for moulding and electroplating process/machine. Introduction of lost wax method of production, switch over to virgin brass instead of recycled brass is necessary to have better product quality.
Marketing: There is need to tie up with export houses and dedicated web site for sale of the cluster products. This may call for cataloguing of products, visit by export house executives to cluster, etc. One educated person from amongst the artisans need to be trained in AUTO CAD software to have better product design. Long term collaboration with the Brass Manufacturing Association at Moradabad association is proposed will not only update the cluster with technology, but also buyers through Moradabad market can gradually get to know Rengali market. BISWA has started talks with M/s Bhusan Steel (a large firm) for meeting their requirement of Brass nut and bolts by outsourcing it from the cluster.
Some of the major learning is as follows:
• There is need for appointment of a full time coordinator in the cluster for at least 3 years. Subsequently leadership should emerge from the cluster • Exposing artisans to new markets, new technologies in phased manner helps • Commitment of various stakeholders can make vital difference between success and failure • One must give time to artisans for adopting new methods of production and emergence of local leadership • Artisans who have grown should be encouraged to take lead in formation of artisans' guild • Interventions should have built-in withdrawal phase so that artisans slowly take up higher responsibilities • Segmented growth of the cluster has made it necessary that process of ancilliarisation may be introduced and artisans may be encouraged to master one aspect of total production process. e.g. one artisan may specialize in casting and moulding, another in buffing and finishing and third in welding process. This can increase the total market size and production scales.
The brass and bell metal cluster of Rangeli is situated in district Sambalpur in the State of Orissa. National Bank for Agriculture and Rural Development (NABARD) adopted this cluster for development under the National Programme on Rural Industrialisation (NPRI) in July 2000. This article has been authored by Mr Sudhanshu K.K.Mishra, AGM, NABARD, Mumbai and Mr S P Mohapatra, Manager, NABARD, Bhubneshwar.