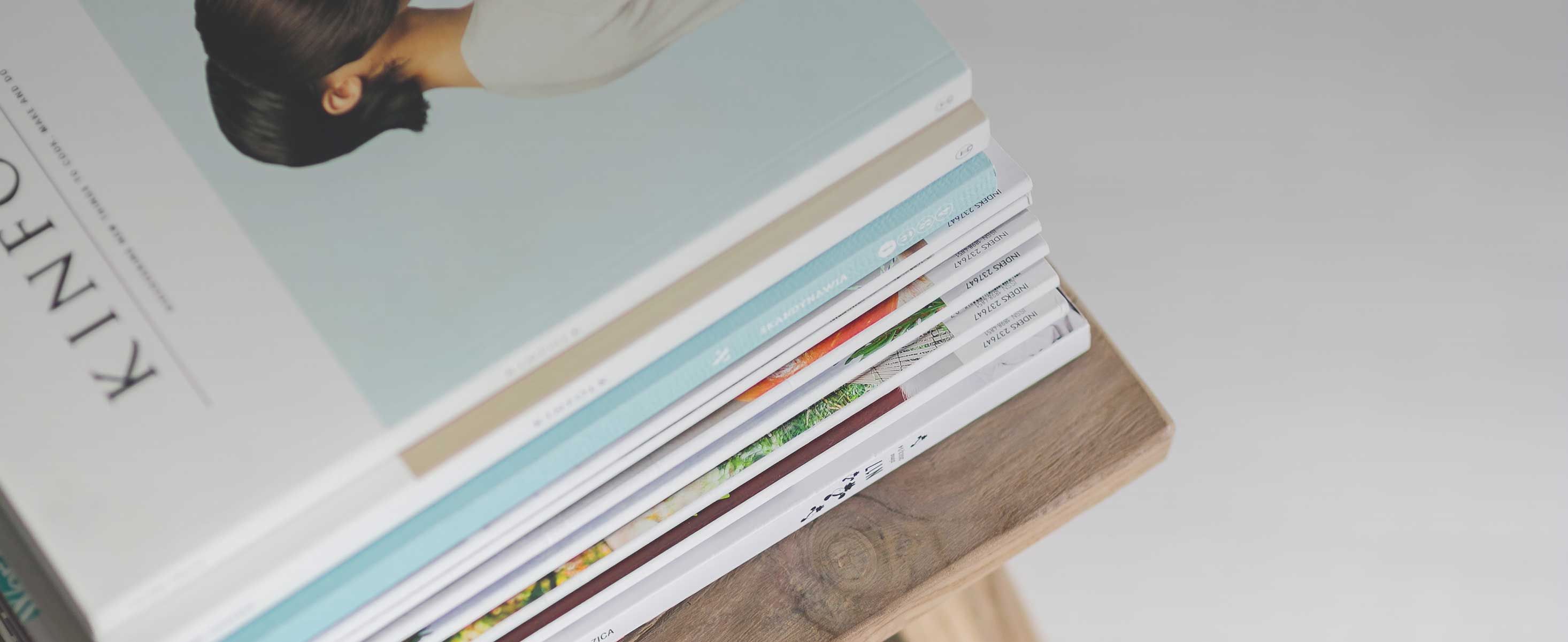
8 minute read
Digital Textile Printing - Dr.N.N. Mahapatra
At present the textile industry produces the majority of its 34 billion square yards of printed textile fabric by screen printing. However as we move into the digital age developments in digital printing of paper are being adapted more and more for the textile market. Inkjet textile printing is growing while growth in analog textile printing remains stagnant. As digital print technologies improve offering faster production and larger cost-effective print runs, digital printing will grow to become the technology that provides the majority of the world’s printed textiles. Digital technology is the fastest growing method of printing textiles, according to a report in the latest issue of Textile Outlook International. Between 2000 and 2005 digitally printed textile output rose by 300% to 70m square metres. Although digital methods still account for less than 1% of the global market for printed textiles, their share is likely to expand to as much as 10% by the early part of the next decade.
Screen printing still dominates the textile printing market with 80% of global output. However, this share is expected to fall as digital printing gains more of a foothold in the market.
Advertisement
One reason for the expected growth in digital printing is that more textile manufacturers are able to provide “prepared for print” (PFP) fabrics to digital printers. But much of the increase will be due to improvements in digital printing equipment, such as printheads and ink dispersion techniques. Growth will also stem from advances in pigment-based inks. The inkjet textile printing technology has been rapidly getting accepted in the past few years. The history of applying inkjet to textile printing is rather long, as an alternative convenient method to conventional printing technology. It was expected to be suitable for quick delivery, short-run production and photographic print with multi-level tone reproduction, which is difficult to achieve with existing analog technology. Some advanced users have already used inkjet for years to manufacture a wide variety of products, mainly for short-run production or sample-making. Recently, however, improved reliability of inkjet printers, along with the introduction of digital technology in design process has made this technology a realistic option to be utilized for massproduction. Market expectation for more productive inkjet textile printer has also contributed to this new trend. Digital Textile Printing in nature is quite separate from traditional Textile Printing, that is the reason why digital textile printing is often termed as “the next generation printing”. Novel techniques in textile printing create new opportunities in business. As technology advanced in the printing process, color inkjet printers became a vital part in the printing process of the fabric market as well. Utilizing the advantages of the digital printing technology, this is a process of printing on textiles and garments, through specialized or modified inkjet technology. It is done by using an inkjet printer and using fabric sheets with a removable paper backing. A transport mechanism for the fabric, and special textile inks are applied to textiles directly and are absorbed by the fibres.
Digital textile printing is an excellent reflection or original artworks with a right blend of classic and elegant view. Also known as direct to garment printing, the process prints designs on fabrics from the computer without any other sources like designing on paper and printing. It enables for changes in color and design easily, and quickly prior to printing. This technology offers faster production technology, cost effective print runs, and provides majority of the worlds printed textiles. This process consumes less water, and dyes, thereby proving to be environmentally friendly. Family photos too can be used for digital printing on the fabric of ones own choice.
DIGITAL TEXTILE PRINTING
Dr.N.N. MAHAPATRA
Business Head (Dyes) SHREE PUSHKAR CHEMICALS & FERTILISERS LTD.
Consumers of today are more demanding with specific choices relating to style, design, and color combinations. This business enables quick turn-around, economic and flexible, efficient set-up and speed. Main advantage of this process is color applications through latest printers, and software applications. Recent concepts of shimmering, shadow, reflection, blurring, layering, and superimposing is also possible through digital fabric printing.
The art of digital printing has influenced both the style and process of textile printing. Digital textile printing has realigned conventional textile printing processes with innovation, and technological advancement.
The dyes used for digital textile printing are different from the dyes used in traditional printing. The most popular dyes for digital printing are acid dye, reactive dye and disperse dye. These dyes can be used for all commercial applications, and have properties like bright colors, low to medium salt content and high color fastness. Various dyes are used depending on the fabric for digital printing, like acid inks are used on silk and nylon; disperse inks on polyesters and reactive inks are used on all cellulose based fabrics such as cotton, linen and rayon. Moreover, these dyes are compatible with low cost ink systems. Colour Pigment Dispersion are premium quality aqueous suspensions of organic pigments in water. They impart bright and clean colors and a very fine particle size distribution enhances performance. They give high performances in thermal and piezo inkjet application.
Essential Features
• A very stable dispersion. • Perfectly applicable for both indoor and
outdoor ink application. • After dispersion into inkjet inks, the images on the paper show excellent light fastness and optical density over wide range of paper quality. • Dispersion is perfectly compatible with most co-solvents, surfactants etc. That have popular usage in inkjet formulations.
Black Pigment Dispersion, PD-30, is a premium quality tailor-made dispersion. It is made up of a very high grade carbon black in water. It has been kept in mind keeping in mind the high end applications like high performance thermal and piezo ink jet application. DuPont ,USA has combined over 70 years of innovation and expertise in textile fibres with its extensive knowledge of ink jet inks to develop an innovative family of inks for digital textile printing. DuPont™ Artistri® inks are available in both pigment and dye-based formulations that combine DuPont proprietary pigment dispersion, polymer and ink formulation technology. Because they are formulated with the same dyes and pigments used in conventional textile printing, Artistri® inks offer superior results for digital textile printing – brilliant colors, excellent fastness properties, and robust print reliability. DuPont has leveraged a long history in textiles together with its core competency in colour and ink technologies to provide digital textile inks that are robust and reliable. Aqueous-based Artistri® inks, printable on a full range of fabrics, offer brilliant colors, sharp image quality and reliable jetting performance. DyStar offers Jettex D disperse dye inks for digital textile printing. Jettex D inks set new standards in direct printing: unlike sublimation transfer inks, they ensure optimum depth of shade and brilliancy, sharpness, high color fastness and good fixation.
The textile digital printing inks are particularly suitable for digital printing of flags, banners, advertising materials and ladies’ wear. Good light fastness is obtained on flame-retardant fabrics without any reduction in flame retardancy.
Huntsman has recently launched 11 new inkjet inks under its Terasil DI-HL brand. These have sufficiently high lightfastness to meet standards set by automotive manufacturers for direct inkjet printing on to polyester. The inks are also suitable for applications such as home furnishings, outdoor fabrics and apparel. Even silk can be printed using inkjet systems, and such techniques are being utilised to print silk for the Italian and other European high fashion sectors. DyStar is marketing inkjet inks for silk based on its Procion and Levafix reactive dyes.
Huntsman has extended its Novacron (formerly Cibacron) range of dyes for inkjet inks. The company claims that these achieve much greater colour intensity than inks based on conventional dyes. By employing dyes of higher colour strength, printers are able to use lower concentrations of dye to achieve the same depth of colour. This, in turn, results in technical advantages during the printing operation.
Pigment-based inks
Technological improvements are enabling manufacturers to use pigments rather than dyes when making inks for printing textiles using digital technology. Pigments are intrinsically more light-fast and wash-fast than dyes, and are often less expensive. Unfortunately, pigmented inks tend to flow less well than dye-based inks. This is important when delivering ink through an inkjet printhead. Fortunately, advances in pigment dispersion techniques and printheads have mitigated this problem. Furthermore, technological advances in digital printing have led to improvements in the way that pigment-based inks adhere to the surface of the fabric. Pigment particles are coated with advanced surfactants in order to improve dispersion stability. And the same technology is used to help the inks adhere properly to the fabric.
Companies with long-established expertise in pigments - such as Ciba, BASF, DuPont and Clariant - have become technological leaders in the development of pigment-based inkjet inks for textiles. Pigments have a number of advantages over dyes in inkjet printing, and these benefits have contributed to the growth in demand for pigment-based inks. For example, pigment-based inks can be printed on to a broad variety of fibres and fabrics, whereas dye-based inks are restricted to specific types of fibres and fabrics.
Also, pigment-based inks are more robust than dye-based inks. Furthermore, pigment-based inks do not need to go through a fixation process using steam to ensure that the ink adheres to the fabric. This makes pigment-based printing more economical in terms of running costs. Moreover, textiles which have been coloured with pigment-based inks have higher levels of weather fastness and light fastness than those coloured with dye-based inks. Consequently, they are particularly suitable for large fabrics which are printed for outdoor use. Dye-based inks suffer from a number of disadvantages compared with pigmentbased inks. For example, they often contain impurities which can disrupt the sensitive mechanisms of printheads. In this regard, dye-based inks sometimes need to be purified, which can increase operating costs. Unlike dye-based inks, pigmented inks do not require a solvent to dissolve the colorant. Such solvents are often based on volatile organic compounds, which means that dye-based inks tend to be less environmentally friendly than pigmented inks.
Pigment-based inks also offer textile printers the opportunity to employ ultraviolet curing technology during the drying stage. Using this technology, the ink dries almost instantaneously and the fabric can be handled and further processed immediately. Conventional printing processes use heat to dry the ink, which is much slower and less convenient. At present, only around 5% of textile printing employs ultra-violet curing. However this share is expected to exceed 10% within the next five years, according to Textiles Intelligence. BASF is in the process of upgrading its range of pigment-based inkjet inks. These products are sold under the company’s Helizarin label, which is also used for