5 minute read
ENGINEERING
from TCT EU 28.1
by TCT Magazine
Next Article
ENGINEERING THE EXQUISITE WORDS: LAURA GRIFFITHS
Topologically designed brackets for aeroplanes, latticed heat exchangers for racing vehicles, medical implants with organic architectures; these are the sorts of applications we’ve come to expect from additive manufacturing. But additive innovation can come in many different forms, as FIT AG recently discovered in a project commissioned by a small parish church in Altmühldorf, Upper Bavaria.
“Inside our own company, we opened up a lot of eyes. It doesn’t always need to be a purely technical application so that 3D printing shines,” says Bruno Knychalla, Project Engineer at FIT AG, who led the technical development for a unique retable sculpture at St. Laurentius parish church. “Sometimes this new form of freedom can open up new possibilities that you yourself didn’t even think of.”
The structure, an impressive, topology optimised 8-metre-high golden lattice which sits as the focal point of the church altar, was developed by Oliver Tessin and artist duo Corbinian Böhm and Michael Gruber, known as Empfangshalle, as part of the church’s renovation project last Spring. The design is influenced by the underlying philosophy of Gothic architecture adapting nature’s design principles which can be found in the church’s pointed arches and ribbed vault. Rather than being a case of technology meeting the traditional, the artists saw the retable as more of a continuation of a centuries-old tradition around sites of cultural heritage using the latest architectural methodologies.
With a clear vision and additive already in mind, specifically Wire Arc Additive Manufacturing (WAAM), Tessin came to FIT following a talk Knychalla gave at the Technical University of Munich. Drawn to WAAM’s unique appearance and haptic properties, the artists had already approached a number of service providers, but there were questions around the feasibility of cost, geometric restrictions and the longevity of WAAM parts. Working with FIT AG’s team in Germany, they
032 / www.tctmagazine.com / 28.1 were able to test a number of the AM provider’s in-house processes, including hybrid manufacturing strategies but, laser sintering, with a sizeable build platform offering strong mechanical properties, reduced weight and design freedom, came out on top.
SHOWN: CLOSE-UP SHOWING DETAILED, TEXTURED AESTHETIC (CREDIT: ANDREAS HEDDERGOTT)
“[WAAM] has a really fascinating surface […] but we showed them that through coating technologies we can also achieve a completely novel look,” Knychalla told TCT. “We knew that there was no way to fabricate the design in one piece. We had to look at which is the most effective and economic way to fabricate it. We developed a concept, where an optimised core was generated, representing the geometry, that was then coated with a structural coating.”
While initially metal and ceramic materials were thought to be the best choice for this type of architectural project, the team opted to manufacture the structure in a white polyamide powder on an EOS P 700. A total of 60 individual parts were printed and stacked to maximise space in the build chamber. Once assembled together, they were then coated in a structural bronze-aluminium alloy using a thermal spraying technique and a metallic lacquer to create a glowing metallic finish.
The next challenge was construction. Working with the artists, architects and structural engineers, the team went to great lengths to build a framework around the 350 kg structure so that they could assemble the final pieces together on-site and give it one final layer of coating.
“We had to build a small building to coat it,” Knychalla explained. “There were a lot of skilled people involved, like our model makers, they really gave it their all to assemble this big thing.”
The project took around six months to complete, but Knychalla says the printing itself was the most effortless part of the process.
5 ABOVE: STRUCTURAL COATING PROCESS (CREDIT: FIT AG)
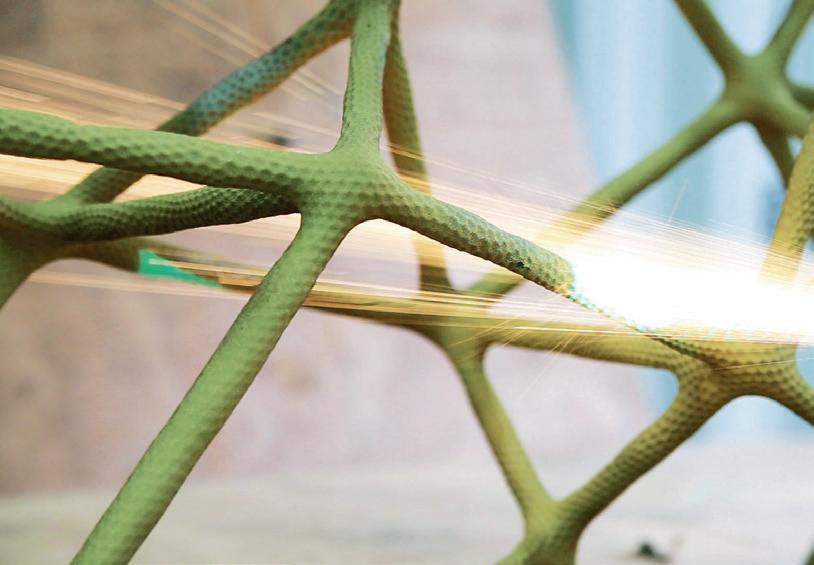
“THIS NEW FORM OF FREEDOM CAN OPEN UP NEW POSSIBILITIES.”
SHOWN: SCULPTURE AT ST. LAURENTIUS PARISH CHURCH (CREDIT: ANDREAS HEDDERGOTT)
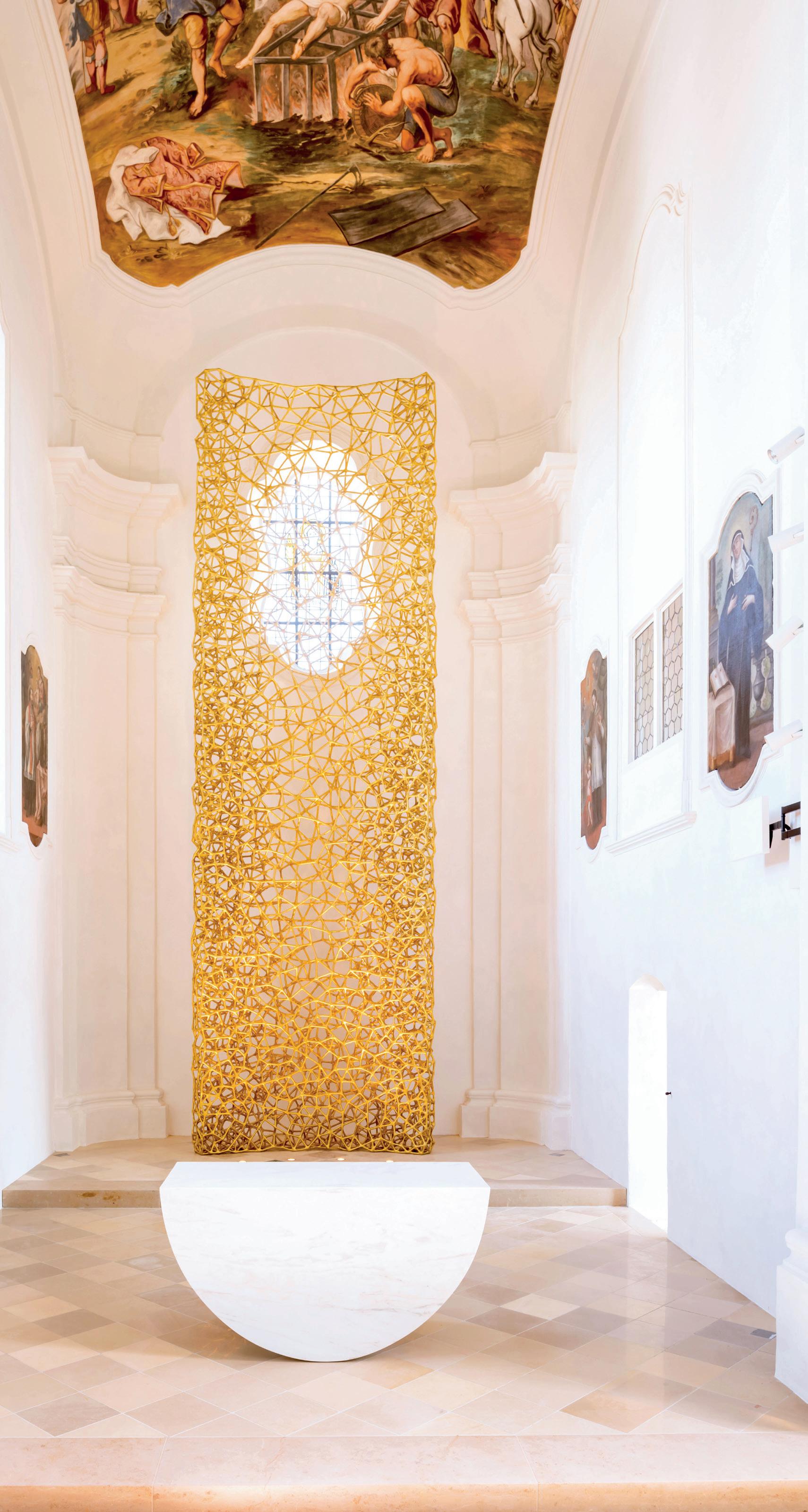
For this type of project, AM is a very new process and crucially, it wasn’t just the designer or the architect that the team needed to get final approval from. They also needed to convince the people of the town, who were leading the church renovations, that this technology was going to work.
“New technologies and spiritual artefacts are not combined so often,” Knychalla commented. “I think our broad range of technological understanding and our interdisciplinary team convinced people that we can make something bold and new with a certain masterful quality that leaves an impression like high handicraft with timeless elegance. I think that people were really astonished.”
The final seals of approval came in the form of a blessing from highest member of the German Catholic church, Cardinal Marx, and from peers in the AM industry who selected the retable as the Highly Commended winner in the Creative Applications category at last year’s TCT Awards. For that, Knychalla says, the success of the project is all down to collaboration.
“We had to speak the same language as our clients, so we adjusted our workflow to be able to do a back and forth inside the digital designto-construction workflow. It was a computationally cutting-edge project,” says Knychalla, acknowledging how FIT AG’s internal design and architecture specialists played an imperative role in communicating new ideas with the studio and artists.
For example, if you look closely, you will see the lattice also features a unique textured aesthetic, the result of a collaborative process between both teams of designers and engineers. It drives home Knychalla’s comments that often, the most creative possibilities are the ones that no single person or team could even imagine.
“We proposed functional surface structures that we could put on top of the structure,” Knychalla adds. “From this proposal, the architect and artists developed their own way of expressing it. We basically exchanged algorithms back and forth to come up with a good solution because this surface had to also be a carrier for the aluminium coating, which acted as the dominant load carrying layer. We basically gave them computational input and they developed it perfectly into a surface that was not just beautiful, but also technically important.”