5 minute read
CARBON’S NEXT CHAPTER
from TCT EU 28.1
by TCT Magazine
Next Article
CEO ELLEN KULLMAN TALKS CARBON’S NEXT CHAPTER
IN THE FIRST OF OUR NEW SERIES OF EXECUTIVE INTERVIEWS, TCT TALKS TO CARBON’S NEW CEO AND PRESIDENT ELLEN J. KULLMAN ABOUT THE FUTURE OF THE SILICON VALLEY ADDITIVE MANUFACTURING PIONEER.
TCT: You’ve served on the board at Carbon for a number of years, what made you want to take on this leadership role? EK: As a Carbon board member I had a first row seat to the incredible innovation coming out of this company. I really believe that Carbon is in a position to pave the way for a stronger manufacturing future. I always said it would take a compelling reason for me to take another operating role. And Carbon is compelling. Everything we are doing to reimagine the way products are designed, engineered, and manufactured across many different industries is inspiring. I have the relevant experience building and leading businesses so it’s really an honour to take on this responsibility to propel Carbon into our next chapter.
TCT: Can you give us a sense of what that next chapter may look like? EK: Right now, we’re focused on scaling our business and supply chain operations, pushing ahead on research and development, and delivering the best products and services to our customers and partners.
TCT: You previously served as CEO at DuPont for seven years. With your experience in the field of materials science, can we expect to see increased focus on Carbon’s materials roadmap? EK: I’m really excited about the role digital manufacturing will play in achieving a more sustainable future for our planet. Digital manufacturing can offer cleaner, more sustainable approaches to making things. For example, last year Carbon announced RPU 130, a new rigid polyurethane material for automotive and industrial applications. 30% of RPU 130 is composed of a fully plant-based material called Susterra, developed by DuPont Tate & Lyle BioProducts. A rigid, tough, high-temperature material comparable in performance to unfilled thermoplastics, RPU 130 demonstrates that achieving more sustainable materials for digital manufacturing can also simultaneously mean achieving better performing materials. This is a major focus for Carbon, and going forward, we are firmly committed to building on this work by continuing to expand efforts to achieve more sustainable materials and practices.
TCT: Coming into this industry, what applications or potential areas for AM excite you the most? EK: I’m really excited about the applications that are coming out of our performance and protection vertical. The Carbon Digital Manufacturing Platform is the perfect solution for any company looking to create superior, differentiated products, and especially previously unmakeable product designs. For example, our ability to create complex lattice structures that can be tuned to be both energy damping and absorbing with varying functional zones
within a single part enables superior performance for products previously made from foam. Further, partnerships with global brands such as
adidas, Riddell, Specialized, and CCM are examples showing how companies that
have adopted Carbon to advance product innovation can not only design and manufacture better products, but also bring products to market in timelines not possible with traditional manufacturing methods.
TCT: Much of the conversation around AM is about how we take the technology from prototyping to production, which Carbon has been exploring this through partnerships with the likes of Ford and Riddell. What challenges do we face in taking AM to that next level? How is Carbon tackling those challenges? EK: Sticking with the status quo is always the easy answer. Adopting a new
technology that fundamentally
transforms the way you make 4
Powder-Bed Fusion from

Powered by the patent-pending Xact Core™ gantry system the XM200C is making affordable quality metal printing readily accessible to a wider range of users and markets.
LEADING TECHNOLOGY 100W or 200W laser options Precision digital scanner/optics Patent-pending recoater User friendly modern design SOFTWARE Autodesk – Nettfab Materalise - Magics OPEN PLATFORM Users can create own build parameters Can process powder from a variety of material providers INTUITIVE TOUCHSCREEN Monitor builds in real-time Optimise print parameters during build

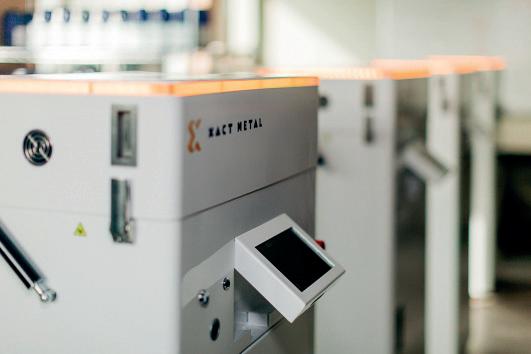
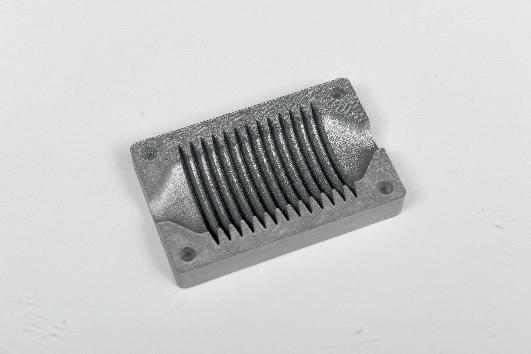
www.3dprinting.co.uk
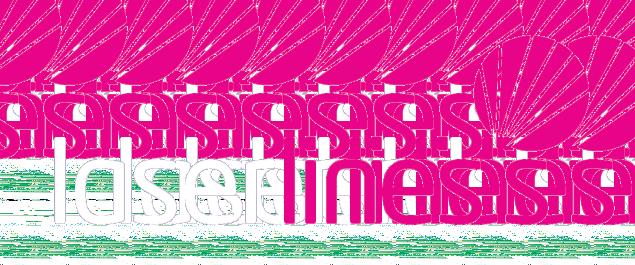
things requires a company to be open to thinking about innovation coming from the outside. Manufacturing and supply chain are generally not areas where companies are open to change or risk. The main challenge the AM industry faces is helping companies see the long-term value in adopting AM and how that will pay off in terms of shortening go-to-market timelines; achieving lighter, consolidated parts; making new, complex geometries for improved part performance; and the opportunity to make parts with better performing and more sustainable materials. The proof is there but we haven’t quite crossed the chasm as an industry to mainstream adoption of AM at scale.
“I’M REALLY EXCITED ABOUT THE ROLE DIGITAL MANUFACTURING WILL PLAY IN ACHIEVING A MORE SUSTAINABLE FUTURE FOR OUR PLANET.”
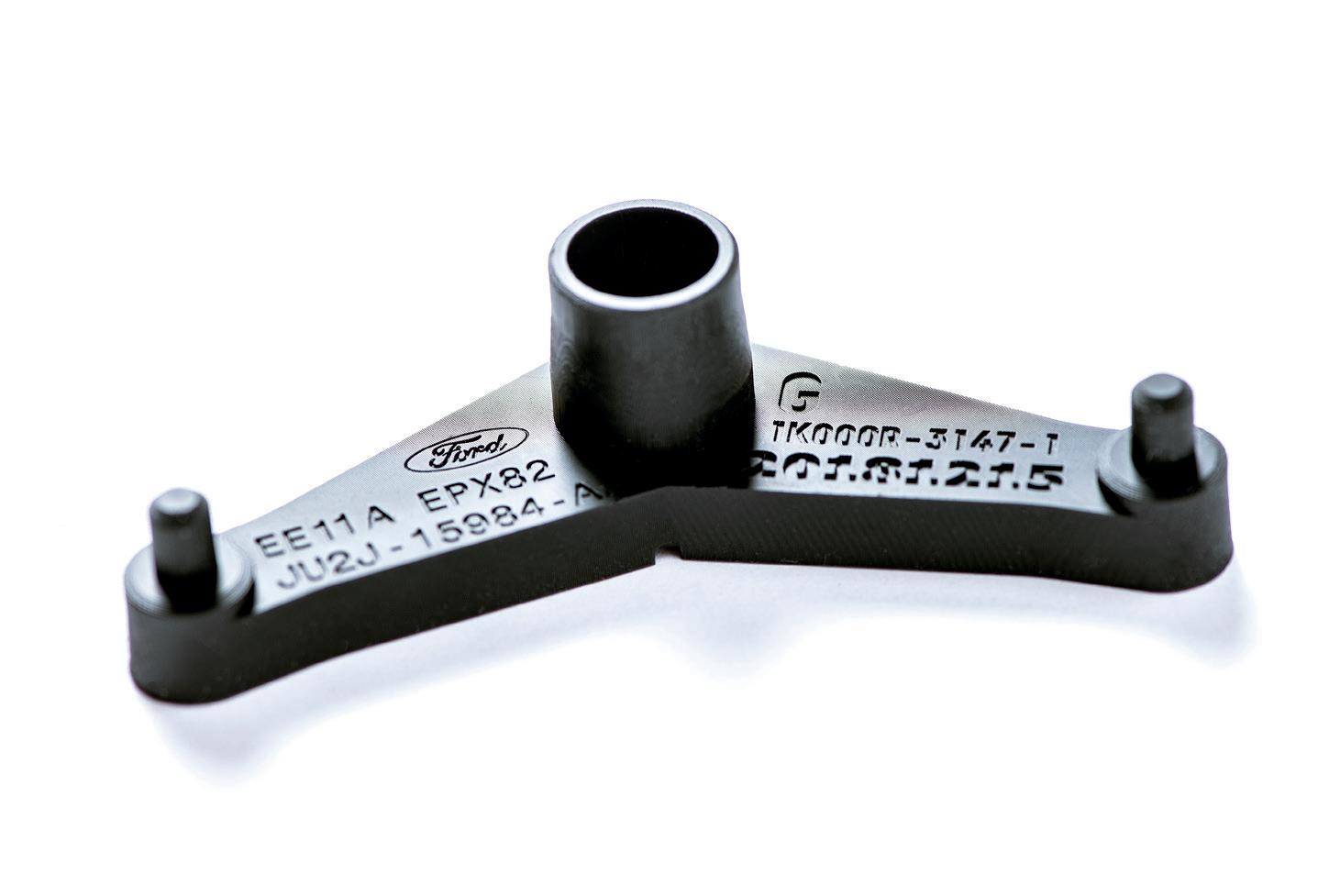
3 LEFT: PRODUCTION PARTS 3D PRINTED FOR FORD
TCT: You are one of the first female CEOs in the AM industry and are active in efforts to fix the gender gap in leadership through the Paradigm for Parity coalition - is that something you’re also aiming to champion in AM? EK: Absolutely. Throughout my career I’ve advocated for important issues like salary equity for people of the same job level regardless of gender, ethnicity, religion, or any other characteristics. I’m really proud to inherit a culture at Carbon where there is a very strong commitment to making a positive difference in the world and to creating a work environment that enables people of all genders to thrive. I believe we must embrace and celebrate the diversity of experiences, capabilities, talents, backgrounds, identities, and interests of all our employees, because not only is it the right thing to do, but it also strengthens our ability to innovate and better serve our customers and partners.
TCT: Finally, as Carbon transitions from its start-up phase, what can we expect to see from the company in 2020? EK: Our focus in 2020 is to continue scaling Carbon’s Digital Manufacturing Platform to deliver on the promise of digital manufacturing. In 2019 our partnerships with global brands like adidas, Riddell, Specialized, Ford, Lamborghini, and Dentsply Sirona demonstrated how Carbon Digital Light Synthesis technology is accelerating product innovation, and we look forward to developing these programmes further. We’ll also continue to expand access of our platform to product designers and engineers around the world.
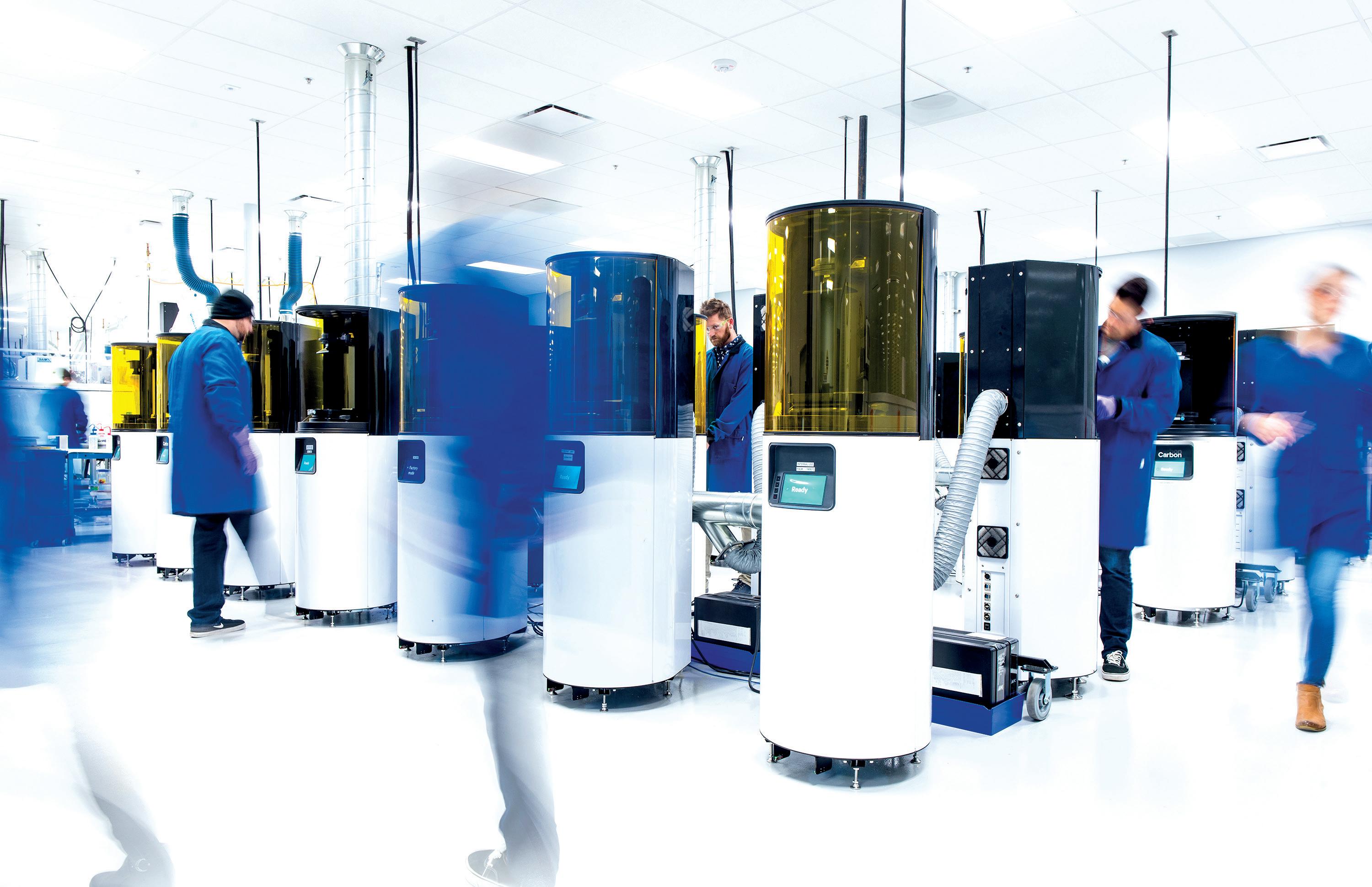