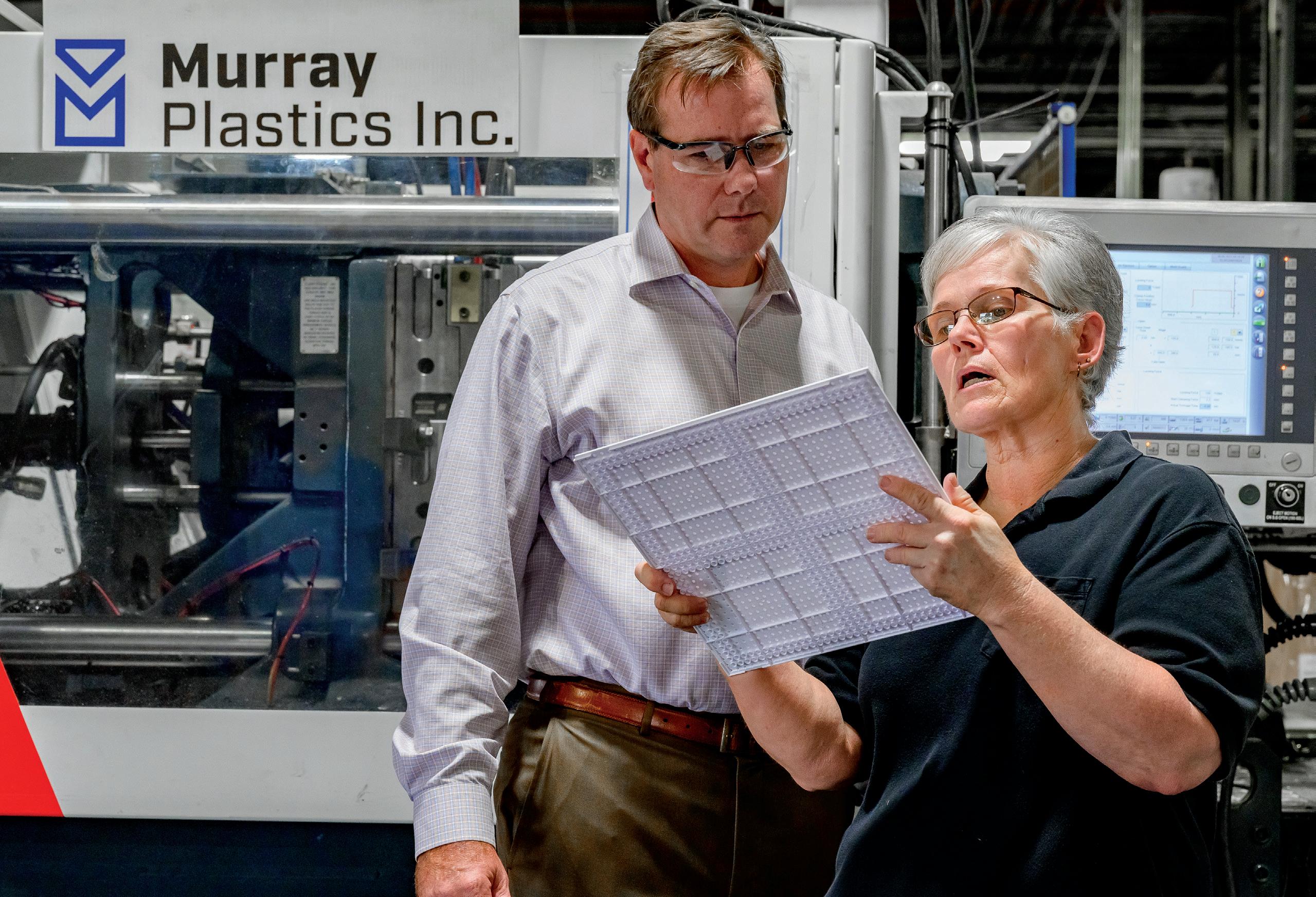
12 minute read
Made to Order
By Christy Simo
Imagine a training program that is customized down to the person, while also being specifically designed for your business. A program that provides on-the job technical skills to someone who is committed to working at your business long-term. All with financial support to make it happen.
Sound like a dream situation? Here in Georgia, it’s happening right now through dozens of apprenticeship programs at Georgia’s 22 technical colleges. “An apprenticeship gives an opportunity for someone to gain immediate employment at a lower salary, then get into a formalized training program so they can grow into their future job at their company,” says Tim McDonald, president of Lanier Technical College, which serves a seven-county area in Northeast Georgia. “It’s a great opportunity for someone who is looking for immediate employment, but still wants to get the training to increase their skills and knowledge to have upward mobility on the job.”
In an apprenticeship, a business partners with the Technical College System of Georgia to train one to several people on the job for a specific skill set. The company pays a wage that increases through the apprenticeship, and the employee also commits to taking classes related to their apprenticeship.
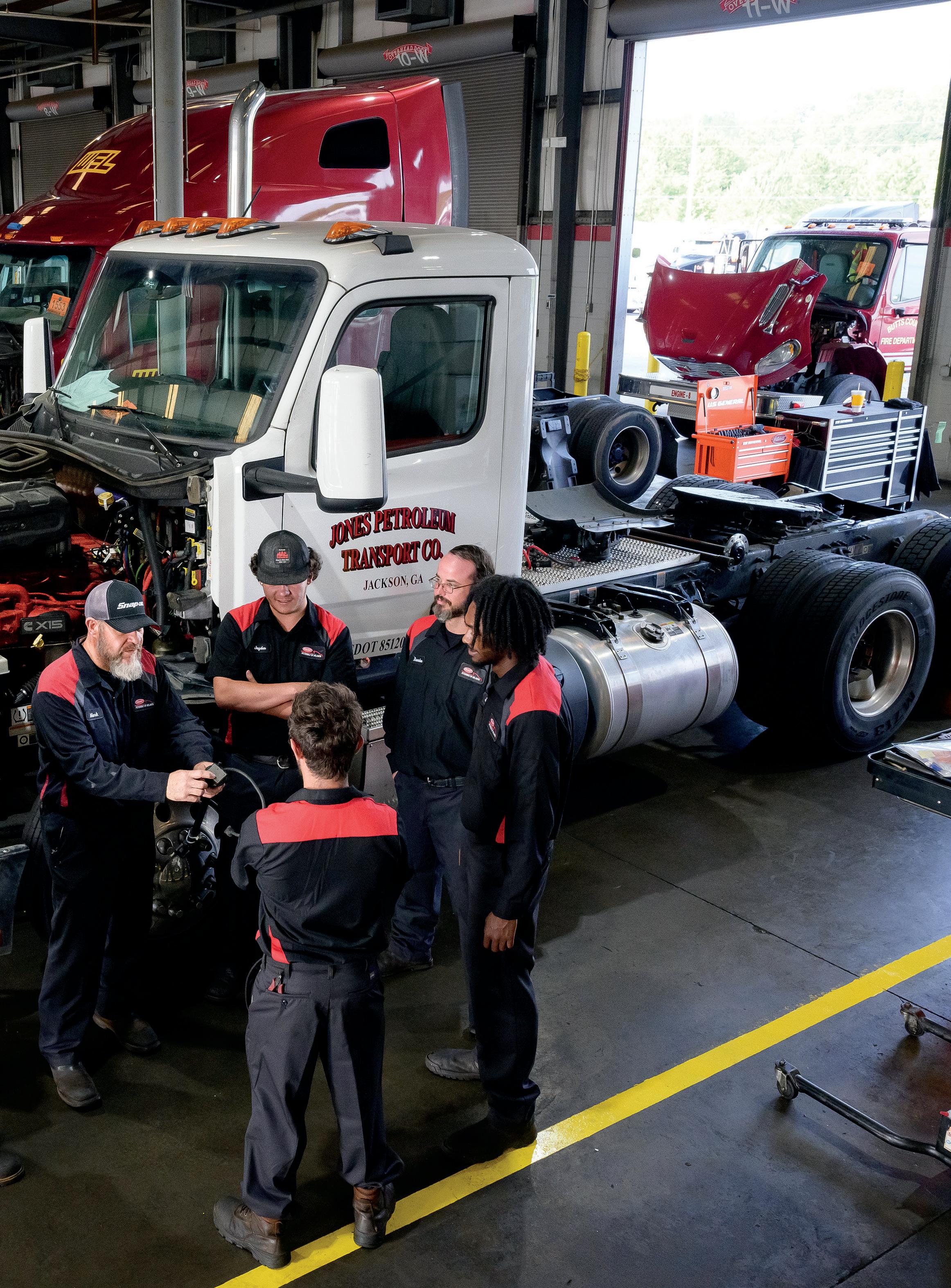
“Everybody’s looking for talent across the state,” says Dr. Irvin Clark, president of Southern Crescent Technical College, which covers an eight-county area south of Atlanta. “Apprenticeships are a proven model to resolve that issue because it allows employers to look within their organizations to upskill an employee … for a high demand sector job that they’re having a hard time recruiting externally. But it also allows a company to attract talent into an organization. A lot of people want to attend college, but they also want work.”
Gaining Popularity
The concept of apprenticeships is nothing new – they’ve been an important way of learning a trade since the Middle Ages. But with the increased emphasis on a fouryear college education during the late 20th century, their popularity dipped.
With the current job market, however, many are discovering that apprenticeships are a viable way to gain an education and start a high-paying career without incurring a ton of student debt. And employers are also finding that in today’s hiring climate, hand-picking future employees and providing them an education that is tailor-made to the culture and needs of their own company is a successful avenue for both long-term employee loyalty and business growth.
“It presents this opportunity for industry to really grow their talent,” says Dr. Clark. “It contributes to retention of that employee. It allows for a business to really be innovative in terms of how they provide workforce training for their employees. And it engages this synergy with the local technical college.”
According to the most recent statistics from the U.S. Department of Labor, there have been more than 2 million new apprentices nationwide since 2012, a 64% increase over the past decade. Here in Georgia, in 2021, there were 9,380 people participating in apprenticeships, 2,828 of which were new. And that number continues to increase every year.
There are several reasons why the workforce training model is gaining in popularity. For one, it allows apprentices to earn a wage while they learn a trade on the job. Then there’s the rising cost of college tuition, which may encourage some students to seek out alternative paths to high-wage work. Plus, there’s the growing demand for people who have the technical skills needed for specific jobs in Georgia’s in-demand industries.
Georgia’s technical colleges have offered apprenticeships for some time, in partnership with the U.S. Department of Labor, and are the state’s largest network of registered apprenticeship sponsors. Now, thanks to support from both the Georgia legislature and the governor, the number of apprenticeships offered in Georgia is growing exponentially.
Last year, Gov. Brian Kemp and TCSG established the first-ever state-funded apprenticeship expansion program. The $1 million High Demand Career Initiative (HDCI) Program awards up to $50,000 ($10,000 per apprentice) in funding to Georgia business to train students and upskill existing workers through registered apprenticeships in 11 high-demand fields like healthcare, advanced manufacturing, and construction, creating 120 new apprenticeships.
Also in 2022, a $4.2-million Apprenticeships for Economic Recovery Grant was established to create apprenticeships for industries critical to Georgia’s economic recovery post-pandemic. This will support more than 900 new apprentices in strategic industries like healthcare, logistics, and broadband. The Apprenticeship State Expansion Grant will support an additional 685 apprentices and 127 Georgia employers.
Anyone can become an apprentice – current TCSG students, existing employees, high schoolers over the age of 16, even someone who is not attending college but wants to launch their career in a specific industry.
“We have apprentices who are young, who are just getting into the workforce and taking advantage of an opportunity,” says Cory Addison, director of business and industry for Lanier Tech. “We have apprentices who have been in the workforce for five+ years, and they’re going back and continuing their education and taking advantage of those opportunities that are out there.”
“It’s a great opportunity for someone who is looking for immediate employment,” McDonald adds, “but still wants to get the training to increase their skills, increase their knowledge to have upward mobility on the job.”
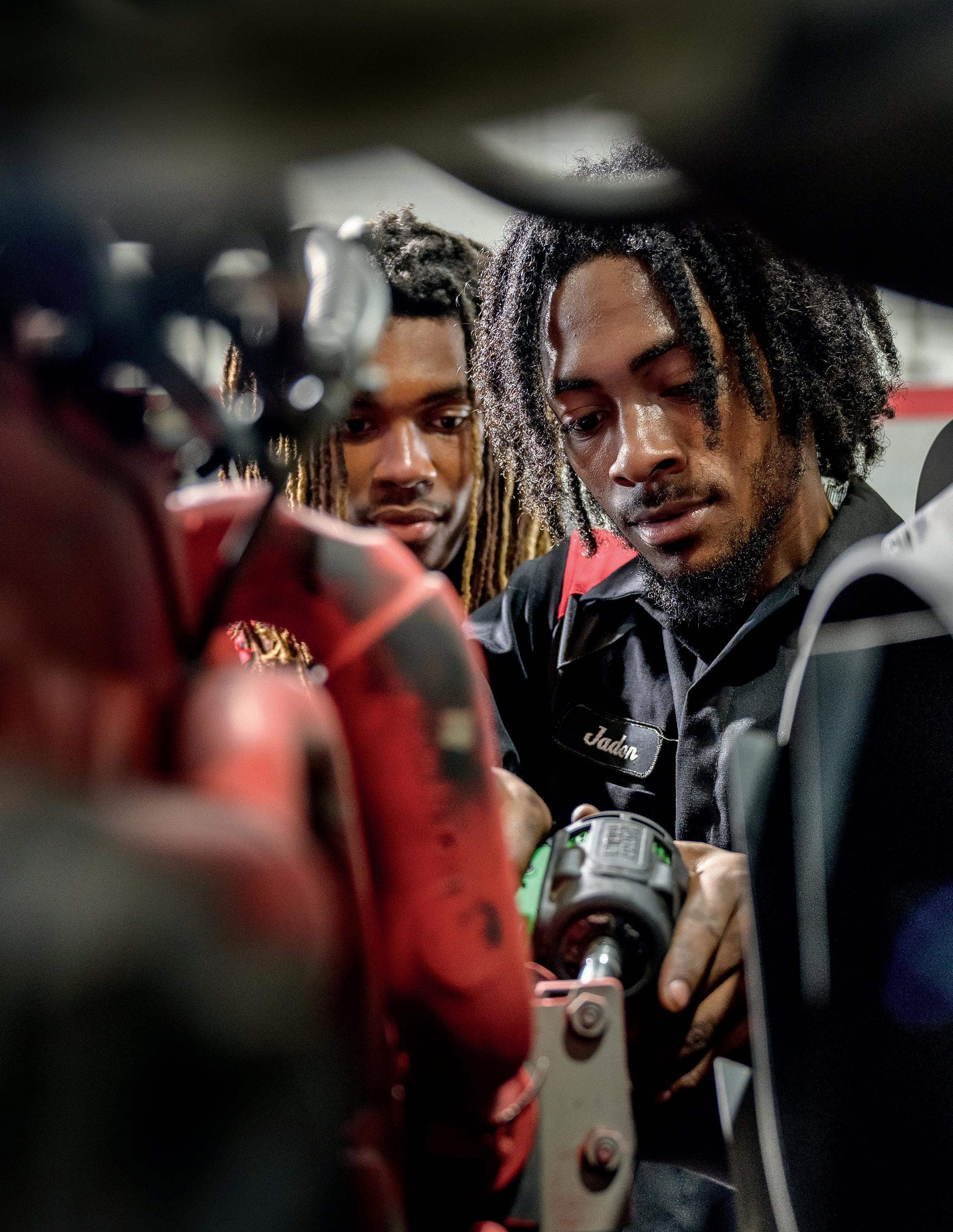
Growing a Workforce
Georgia has been named the top state to do business for several years in a row, and that translates to a lot of companies coming to the state – and a lot of existing businesses looking to grow. An apprenticeship program can help many employers do just that.
“We have so much growth in our area, and manufacturers are very desperate to hire new individuals. But we’re also learning that they’re just as desperate to upskill their existing workforce,” Addison says. “So, for businesses in our area, there’s such value when our apprentices are coming through and gaining that additional training. It’s helping to close the skills gap.”
PeterBilt of Atlanta is one such company that turned to TCSG and its apprentice programs to grow its workforce. The truck manufacturer needed more diesel technicians, so Southern Crescent Technical College (SCTC) put together a special career day just to recruit apprentices for PeterBilt.
“We had a great turnout that night,” recalls Lemuel Mercado, dean of academic affairs.
Anyone interested in an apprenticeship with PeterBilt – whether SCTC students, existing PeterBilt employees, or someone just interested in starting a career in diesel mechanics – was invited to attend. The school’s admissions and financial aid teams were there to assist with registration and financial support as needed, and each person interviewed with the PeterBilt staff.
“Two days later, they sent me the names of the five candidates they selected, and then they became apprentices,” Mercado says. That group is currently working through their two-year apprenticeship at PeterBilt.
“It’s going very well,” says Scott Pearson, president of PeterBilt of Atlanta. “The neat thing about it is we get exposed to young people as they enter the trade. We can see their performance, how well they do what they’re doing. We get the opportunity to get them on board quickly and help them understand our culture while they’re learning their skill set.
“It goes beyond just classroom or hands-on in a laboratory,” he adds. “They’re learning what it’s like to be in a shop environment. It’s a production environment. You’ve got customers waiting on their truck. … So, you’re building their skill set and their knowledge with an understanding that this is a true profession, not just further education.”
Like with PeterBilt, each apprenticeship is tailored to the company and its needs.
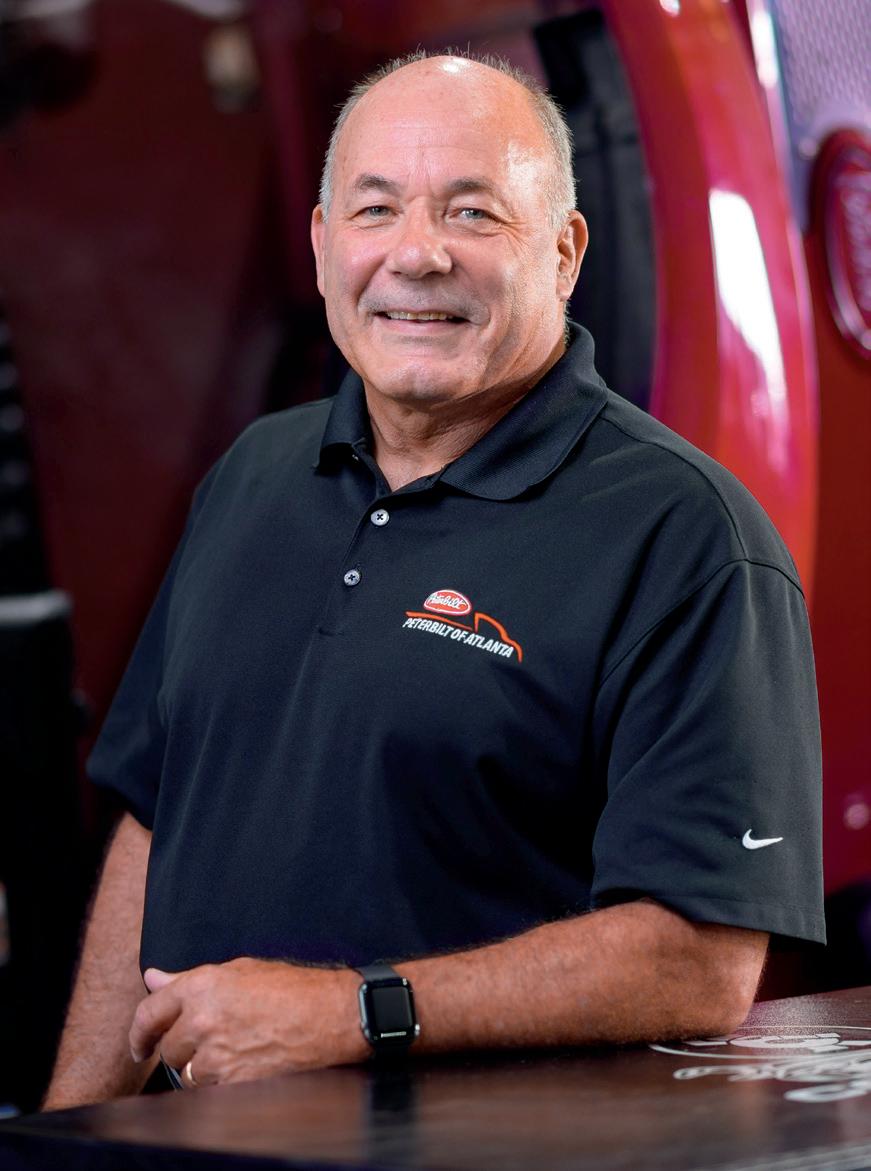
“When we do apprenticeships, what’s happening is the company is selecting the specific courses they want their employees to take, a lot of times in the order they want them to take them so that they can match it up with their in-house or on-the-job learning opportunities,” McDonald says.
“That’s the piece that makes the apprenticeship so powerful. We work with the company to match the technical training or the technical instruction up to the on-the-job learning and the competencies that they’re mastering on the job.”
Apprenticeships help with employee retention, too.
“When companies invest in these apprenticeships, they tend to have less turnover,” says Addison. “Because the apprentice knows that the companies are investing in them.” continued on page 28
What is a registered apprenticeship program?
A training model that is registered with and follows the U.S. Department of Labor guidelines
Requires at least 2,000 hours of on-the-job training
Requires 144 hours of classroom instruction
Is completed in 1 to 5 years (typical length is two years)
Must be 16 years + to participate
Types of grants
The state of Georgia offers several grants to businesses and students participating in an apprenticeship program in Georgia. For more information on these opportunities, visit tcsg.edu/ worksouce/resources-for-practitioners
Apprenticeship for Economic Recovery (AER) Grant
Provides funding up to $4,400 per apprentice to offset the costs of tuition, training fees, books, supplies, and assessments for eligible apprenticeship programs in occupations critical to the economic recovery of the state post-pandemic, including manufacturing, healthcare, and transportation, distribution, and logistics.
High Demand Career Initiative Program
Provides funding of up to $10,000 per apprentice (5 apprentices/$50,000 max) directly to employers for the successful completion of apprenticeships. Program occupation must be included as one of the High Demand Careers for Apprenticeship. (See tcsg. edu/HDCI for list.)
HOPE Career Grant
Combined with other apprenticeship-funding opportunities, this grant, which provides free tuition in 19 qualified programs of study, can fully cover the cost of an eligible apprenticeship program Related Technical Instruction (RTI).
Workforce Innovation & Opportunity Act (WIOA)
WorkSource Georgia administers this funding to support underemployed and unemployed individuals with skills training and other career services, typically by covering the cost of tuition, classroom materials, and supplies. The funding also supports Georgia businesses with upskilling new and existing workforce, covering a portion of apprentice wages for on-the-job learning, and employer training costs associated with upskilling existing employees.
Taking Care of Business
The thought of taking on even one apprentice can seem daunting to some companies. After all, you need an existing employee to mentor them while they are on the job, which often requires more hours and increased pay. Then there’s the paperwork required – apprenticeships are registered with the U.S. Department of Labor and require 2,000 hours of on-the-job training and 144 hours of study before the person completes the apprenticeship. And it requires a commitment – an apprenticeship can take anywhere from one to five years to complete, although the average time is two years.
Partnering with a TCSG college, however, makes the whole process easier.
“We take care of the paperwork piece of it. We make sure that all the documentation is in place and in order,” Addison says. “We just make the process easier for the employer for that apprentice to get that journey worker certification.”
For custom plastic injection molding company Murray Plastics, participating in several apprenticeship programs has brought in new clients and cost savings. Most recently, an existing employee, Cristy Norris, was interested in taking on a new role with the Gainesville-based company right when Lanier Tech was offering a two-year apprenticeship program in Quality Control. Norris completed the apprenticeship this past February.
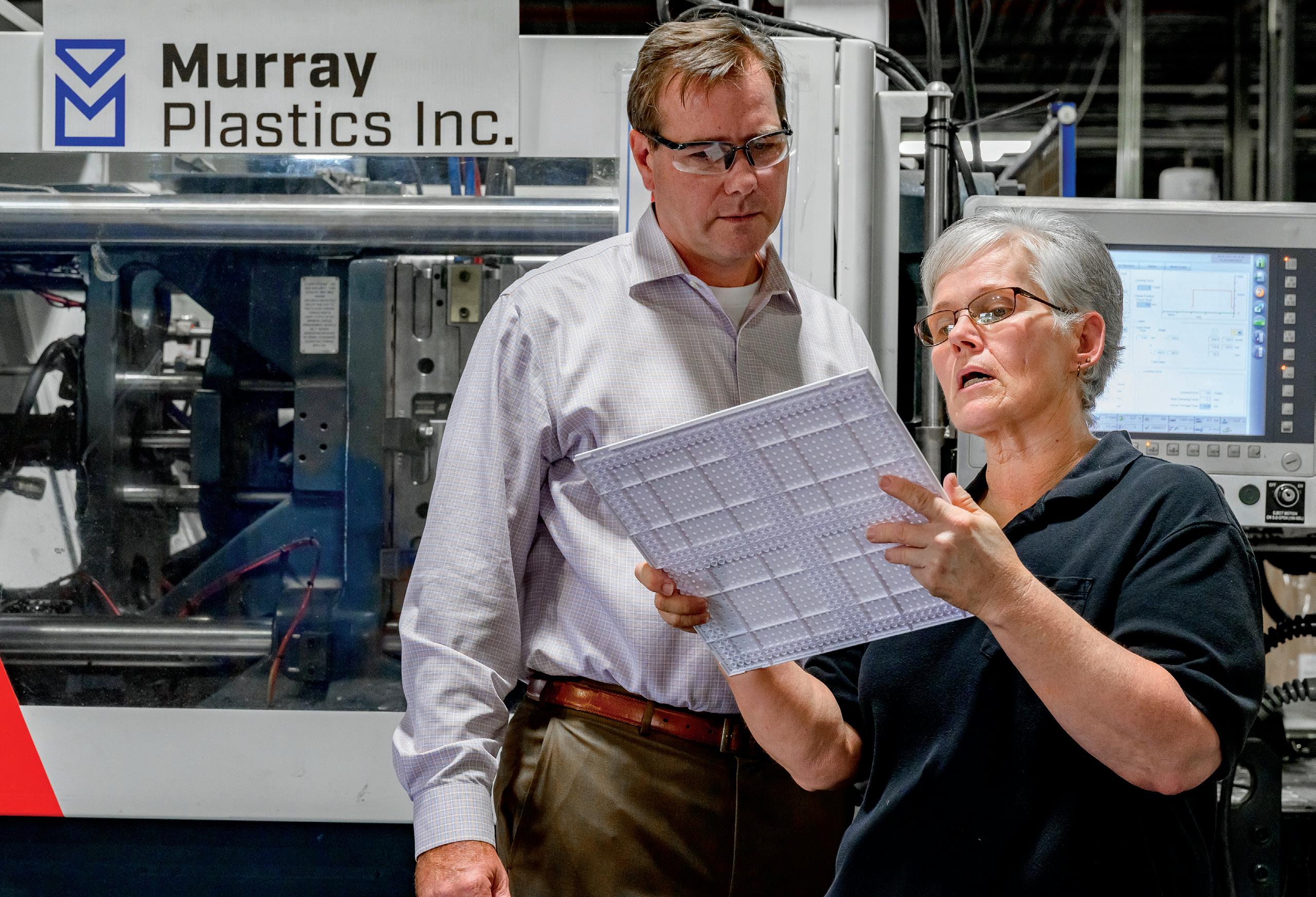
“It was a great program,” says Danielle Perkins, COO. “The quality control itself has increased the number of jobs that we’re able to quote and new jobs that we’re able to bring in.”
Perkins notes that the apprenticeship more than paid for itself since it allowed the company to take on new types of clients it couldn’t take on before they had a quality control manager in place.
“During her quality control apprenticeship, we started getting calls and requests for quotes, and we were like ‘oh, we can say we can do this now,’” Perkins says, adding that the company gained a new client soon after the apprenticeship started. “It was really good because she got the hands-on experience, we had a customer willing to walk through all the big steps with us, and she was learning it in class as well. So, it really helped us step up to that next level.”
Addison with Lanier Tech agrees that businesses often find unexpected value when bringing on an apprentice.
“Not only are the students learning and on the job, but they’re also bringing value to the employer during that time,” he notes, “and coming up with new ways and ideas to save the employers money and to make them more productive.”
TCSG also ensures that those future employees obtain some of the soft work skills related to appearance, communication, teamwork, and respect.
“There’s so many other ancillaries of what goes into the job besides just the technical learning of how to repair or fix a truck,” PeterBilt’s Pearson says. “It’s how to work with the tools, how to work with your co-associates out there, how to clock in and manage a time clock, how to manage the computer system and write up and report details in terms of a warranty repair. They learn all that from the ground up.”
“That’s the neat part about it,” he adds. “As they build their technical skills, they’re also building their knowledge base of how to work for a company.”
Setting up an apprenticeship program requires a financial commitment, but there, too, TCSG can help assist both businesses and students to obtain grants (see page 27) to defray the cost of setting up or participating in an apprenticeship program.
Ultimately, apprenticeships are yet another tool in the TCSG economic development kit. They’re a way for people to learn a trade and get a job, contribute to the economy, and help businesses grow and thrive.
“As companies look to expand in Georgia, one of the first things they look at is the available workforce,” Lanier Tech’s McDonald says. “That’s why it’s so important that we increase the number of young skilled technicians we have, because that’s what’s going to attract companies to continue to grow or locate in Georgia.”
###