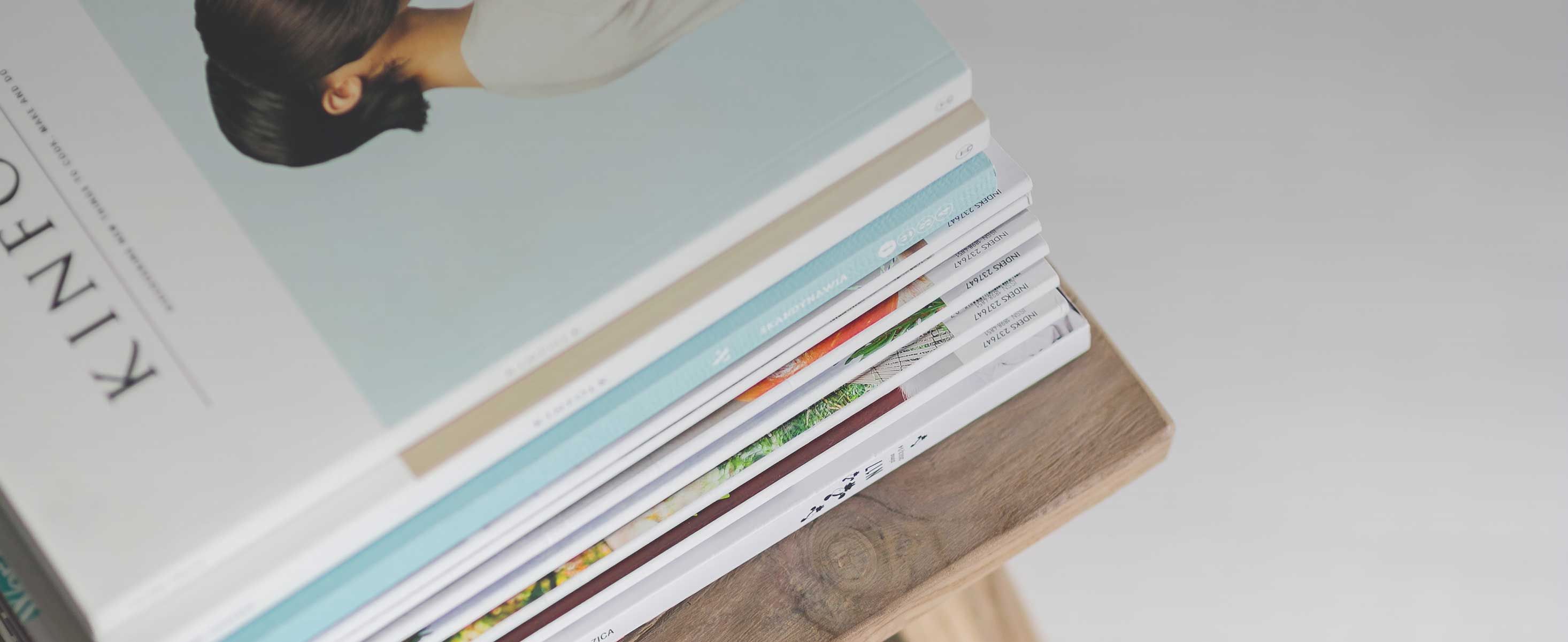
8 minute read
New Site Launch
THE BOEING COMPANY – DELIVERY OPERATIONS
Production System Stability through Structured Problem Solving
Advertisement
BOEING COMPANY DELIVERY OPERATIONS Student Team: Benjamin Hambleton – Master of Business Administration Ryan Skorka – EGL (BSE Aerospace Engineering & MSE in Industrial and Operations Engineering) Tomás Vonderheide – EGL (BSE & MSE in Industrial and Operations Engineering)
Project Sponsors: Michael Martinez – One BPS Integrator, BCA Delivery Operations Craig Trewet – Boeing Production System Leader, BCA Delivery Operations
Faculty Advisors: Richard Hughes – College of Engineering Tariq Mughal – Ross School of Business
The Boeing Company is the world’s largest aerospace company whose aircraft comprise more than 50% of the global fleet of active commercial jetliners. In recent years, Boeing’s ability to deliver airplanes has been unstable due to the global COVID-19 pandemic and quality defects found in their 737 MAX and 787 airplanes. During this period of lower production rates, One Boeing Production System (One BPS) was initiated in 2019 to stabilize, standardize, and continuously improve the production system by aligning to common practices, Lean principles, and systematic problem solving on the production line. The highest level of this problem-solving method is the Factory Support Collaboration Center (FSCC), which is an organization that solves Boeing’s toughest, most systemic problems through accelerated project management. To date, the FSCC has already generated hundreds of millions of dollars in savings annually for factory initiatives, however, the organization has not been used in delivery operations.
To bridge this gap, the Tauber team was asked to leverage the existing factory FSCC framework to lead the first three Delivery Center FSCC projects. First, the team facilitated a tooling redesign to eliminate a high safety crush hazard caused by the non-standard 767 wing stand insert design. This demonstrated to delivery center team members that the Boeing Problem Solving Model and flexible staffing effectively solved high-impact production system problems. Second, the team investigated the feasibility of weighing airplanes in the factory rather than later downstream at a bottleneck point of the build to balance the utilization of the production line. This particular effort helped reveal the need to prioritize Delivery Center FSCC projects by developing a “likelihood score” in the FSCC’s project prioritization tool. Third, the team led a root cause investigation in missing paint defects, the top driver of rework hours for 767 airplanes. This final pilot project not only revealed previously unknown defect root causes, but also ensured the Delivery Center FSCC was in a mature enough state to operate without the Tauber team’s leadership.
Through completion of the three pilot projects, the Tauber team prevented one severe injury per year, eliminated 20 hours of overtime per airplane, identified root causes for an average 100 hours of rework per airplane, and created the potential for a 4% throughput increase in directly attributable impact. Most importantly, the Tauber team paved the way for a functional FSCC in the delivery center to generate tens of millions of dollars in annual savings by efficiently solving the highest impact systemic issues faced on BCA delivery center production lines.
THE BOEING COMPANY – SUSTAINABLE MATERIAL
Sustainability Strategy
Student Team: Allison Lesovoy –MBA and MS in Environmental Science Josh Reid – MBA Noah Zaatar – EGL (BSE Mechanical Engineering & MSE in Industrial and Operations Engineering)
Project Sponsors: James Holden – Manager Amy Goodell – BCA Interiors / Payloads Engineer Kelsea Ballantyne – Leader BCA Product Development - Manufacturing Strategy and Sustainability Tia BensonTolle – Advanced Materials
Faculty Advisors: Brian Love – College of Engineering Michael Metzger – Ross School of Business
Climate change is a fundamental global challenge, and Boeing has taken the initiative over the last few years to become an industry leader in sustainability. Currently, the focus of sustainability within Boeing has been on reducing in-use emissions; the company has yet to put significant resources towards a clear strategy elsewhere in the lifecycle. Outside of in-use sustainability exists complex processes and long lead times to develop new materials and products, and industry solutions to supply chain sustainability are nascent. The business world is adapting to climate change, and Boeing must follow suit. Boeing’s top investors have begun evaluating the sustainability of their companies to prioritize forward-thinking groups. A positive development in sustainability is also linked to positive business growth, so Boeing is motivated to accelerate their sustainability processes. Sustainability is hardly a new phenomenon, and many analogous companies and industries have integrated innovative sustainability practices to gain a competitive advantage. A review of the top companies with supply chains similar to Boeing’s revealed that leaders in sustainability exhibited exceptional decision modeling, collaboration, and measurement and reporting. Internally, Boeing has invested heavily in their up-and-coming sustainability office, and the company has mapped sustainability goals to reach their high expectations. Boeing has narrowed its focus on a few projects and forecasts that these will create a lasting industry impact. One area that has been specifically overlooked is cradle-to-gate, or the stages before Boeing receives the material at their factory gate. The Tauber team was brought in to strategically evaluate and improve the sustainability of supply chain and product development for Boeing Commercial Airplanes. Through evaluation of this objective, the Tauber team has determined that no method to holistically evaluate the portfolio of sustainability projects to ensure the projects are completely exhaustive and that individual projects are funded according to their alignment to strategic goals. To reach this goal, the Tauber team recommends a three-part approach to addressing this need, comprised of strategies to increase visibility, improve prioritization, and create alignment within Boeing’s sustainability efforts. Firstly, to increase visibility, the Tauber team created a project portfolio dashboard to analyze the commitment towards sustainability across Boeing; the dashboard visualizes the current state of sustainability funding, the most prominent scopes, the strongest departments, etc. To improve prioritization, the team recommends the integration of sustainability considerations into the existing processes within Product Development. Lastly, to align each department, the team supports increasing communication and councils with other departments. These recommendations create an avenue towards the ideal state for sustainability within Boeing. By increasing visibility, prioritization, and alignment for sustainability, executives will be empowered to collaborate towards a more complete understanding of Boeing’s current state of sustainability and the sustainability opportunities that exist. Project managers will understand where to invest their time and energy, saving Boeing millions of dollars. With the Tauber team’s recommendations, Boeing will be one step closer to global leadership in sustainability.
THE BOEING COMPANY — WAREHOUSING
Warehousing Business Case Analysis Toolkit for The Boeing Company
Student Team: Zackary Simmons — EGL (BSE Nuclear and Radiological Sciences /MSE in Industrial & Operations Engineering) Venkat Subramaniam — EGL (BSE & MSE in Aerospace Engineering)
Project Sponsors: Satish Bapanapalli — Fulfillment Operations Leader J.S. Iwasaki — Director Supply Chain Logistics Scott Mercer — Director, Packaging & Logistics Stephanie Wang — Site Leader, PDX Decorative Paint & Delivery
Faculty Advisors: Prakash Sathe — College of Engineering Brian Talbot — Ross School of Business
The Boeing Company (Boeing) is one of the world’s largest aerospace companies and a leading manufacturer of commercial jet transport aircraft, along with other products for the military, space and aircraft services industries. As the aviation industry starts to recover from the COVID-19 pandemic, along with the return to service of the 737 MAX aircraft, Boeing seeks to meet the demand for more aircraft while minimizing costs, especially the costs associated with the production of its aircraft: warehousing, parts kitting, and delivery in support of the manufacturing line. Currently, Boeing uses a decentralized network of 63 warehouses spread across the Puget Sound to store and kit parts into product specific totes, along with dozens of integration centers that assemble these totes into the final carts that are delivered to the manufacturing line. This process is complex and requires several delivery methods and many touches before a completed cart is delivered to the mechanic. To alleviate the challenges brought on by this complex process, the supply chain organization is pursuing a radical transformation of the warehousing model, in which all the warehouses will be consolidated into two Regional Distribution Centers (RDC). Ideally, the RDCs will receive, store, kit, and integrate all parts required for a manufacturing job into a cart and deliver it straight to the manufacturing point of use. Additionally, the RDC will incorporate automated storage and retrieval systems, transportation automation, new IT systems that will enable better customer support, and a new process design. As the supply chain organization pursued the RDC business case, it became evident that the improved process flow design will play a critical role in justifying the business case. We were brought in to help understand the impacts of process flow design on the overall business case. Our analysis of the business case showed that there was not clarity in how the process flow design will enable cost savings, quality improvements, and the reduction of safety incidences. An added challenge in clarifying the cost, quality, and safety improvement was the lack of detailed design for the new process, which is integral to how we could calculate and justify improvements. Our solution to this problem was to develop a set of tools and methodologies with which the business transformation team can rapidly evaluate design ideas for the future state along the three improvement perspectives. The Marginal Cost Tool calculates the total costs associated with the production of the “next” cart in the current and future state, and can be used to calculate the magnitude of cost savings influenced by design changes. The Predictive Quality Tool calculates the average likelihood that a cart contains a quality defect and can be used to predict the changes in quality performance for the overall system. We also authored a Systemic Safety Handbook, which spotlights hidden areas in the fulfillment process that have potential for safety improvement and may occur in the future RDC process. With these tools, the warehouse transformation team can design an RDC process flow that can capitalize on all the improvements and guarantee sizable cost savings. In the short term, the use of our tools will improve the RDC process design, which will improve quality and delivery performance of carts to manufacturing. Since one of the constraints to production is the delivery of parts, improvements in the warehousing process to better service manufacturing can unlock potential for higher production rates and better quality of work on the aircraft.