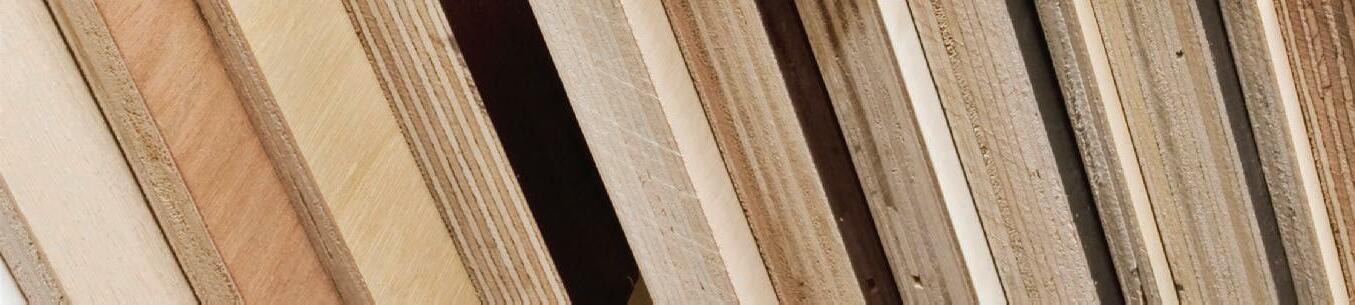
4 minute read
PLYWOOD PRODUCTS
SOFTWOOD PLYWOOD HARDWOOD PLYWOOD AIRCRAFT PLYWOOD MARINE PLYWOOD
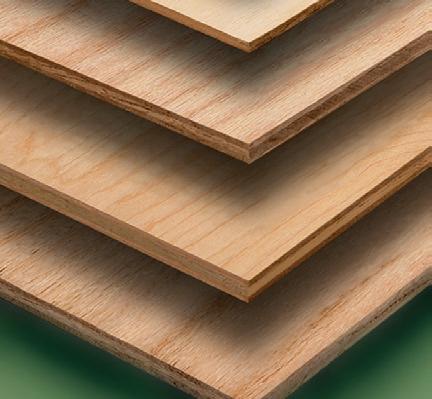
Often referred to as the “Granddaddy of engineered wood products,” plywood originated and later standardized the creation of a composite wood paneling unit stronger than the sum of its parts. And as one of the first such products to be made by bonding together pieces of wood, plywood has been around in one form or another for more than a thousand years.
Ancient Greeks and Egyptians used thinly cut wood and glued it into layers to help conserve their wood supplies, and in China, shaved wood was glued together to make furniture more than a thousand years ago. More modern iterations of plywood were used by the English, French and Russians.
Early plywood from the 19th and 20th centuries was typically made from hardwood for furniture and cabinet production. A patent for “plywood” was issued to John K. Mayo of New York City in 1865. The patent was reissued in 1868 and describes the product as “[consisting of] cementing or otherwise fastening together a number… of sheets, with the grain of the successive pieces, or some of them, running crosswise or diversely from that of the others…”
A few decades later, the World Fair came to Portland, Oregon, in 1905 to celebrate the 100th anniversary of the Lewis and Clark Expedition. Gustav Carlson, part owner and plant manager for the Portland Manufacturing Company, developed a technique making laminated panels from Pacific Northwest softwoods. His “3-ply veneer work” on display prompted orders from several cabinet, trunk and door manufacturers, and by 1907, Portland Manufacturing was producing more than 400 panels a day.
At first, the burgeoning industry served mainly door manufacturers, but in 1920, that focus shifted to the automobile market, and plywood was used for vehicle running boards. By 1929, 17 plywood mills dotted the Pacific Northwest, producing more than 350 million square feet of plywood that year. The rapid weathering of plywood running boards and subsequent drop in demand led to a 1934 breakthrough with the addition of a waterproof adhesive, which set up a new era and possible markets for plywood.
Standardizing the quality of plywood products led to the organization of the Douglas Fir Plywood Association in 1933. The improved quality and standardization of plywood helped boost sales and established the material as a mainstay in construction use. This continued through World War II, which saw plywood used for building everything from barracks to boats.
The Douglas Fir Plywood Association evolved into the American Plywood Association in 1964 and later into today’s APA—The Engineered Wood Association, a nonprofit trade organization based in Tacoma, Washington, that serves the U.S. and Canadian engineered wood products industry. Technological advances fueled by increasing demand for replenishable and reliable building products has only boosted plywood’s popularity and appeal to plywood manufacturers. It was found that the cross-lamination of wood veneer layers improve the inherent structural advantages of wood by distributing along-the-grain strength of wood in both directions. This idea of “reconstituting” wood fiber to produce better-thanwood building materials has led in more recent times to a technological revolution and the rise of a whole new engineered wood products industry, according to the APA. These products not only yield superior performance properties, but also make better use of precious forest resources. Today’s plywood is manufactured by assembling thin layers or plies of wood glued and pressed together using powerful adhesives, with adjacent layers having their wood grain rotated up to 90 degrees to one another, which increases the product’s strength and durability. Lower-quality or thinner plywoods may only have their plies arranged at right angles to each other, while some higher-quality products can feature five plies with staggered rotations (0, 45, 90, 135, and 180 degrees), offering even greater strength using the graduated steps. Typical plywood panels use face veneers of a higher grade than the core veneers. The core layers are mainly used to increase the separation between the outer layers where the bending stresses are highest, thus increasing the panel's resistance to bending. So thicker panels can span greater distances under the same loads. In bending, the maximum stress occurs in the outermost layers, one in tension, the other in compression. Bending stress decreases from the maximum at the face layers to nearly zero at the central layer. Shear stress, by contrast, is higher in the center of the panel, and at the outer fibers.

By utilizing wood scraps, so to speak, rather than solid, whole boards, plywood can be made with less impact on the environment. Today’s plywood is an economical, factory-produced sheet of wood with precise dimensions that does not distort or crack with changes in atmospheric moisture.
Because of this, plywood is widely used for diverse applications ranging from making designer furniture or wall and floor coverings to packaging—and even for making boats and airplanes. There are various specialty plywood materials available to serve these and many other markets