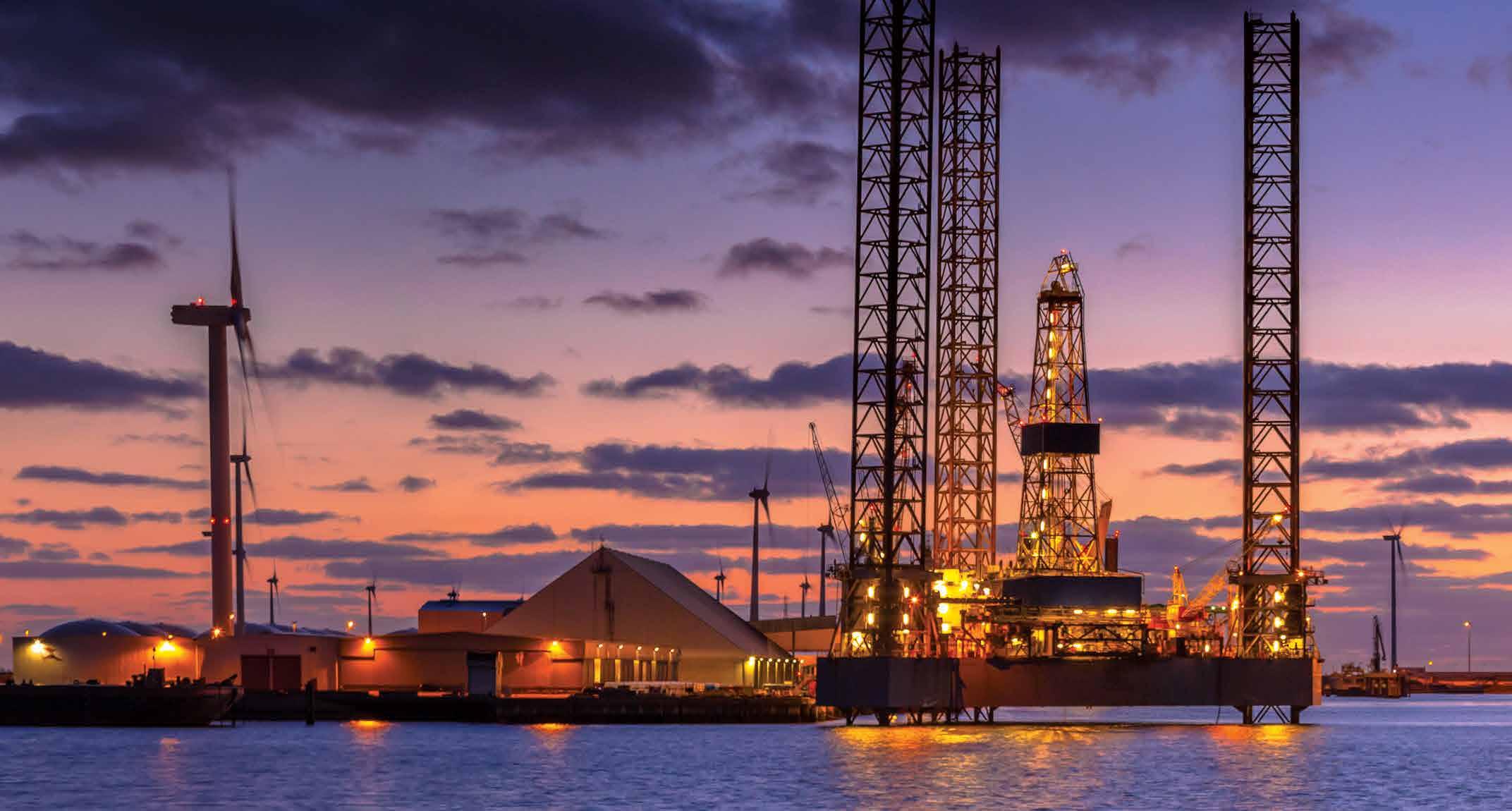
12 minute read
End-to-end safety
BETTER SAFE THAN SORRY
By Rodney Weidemann
Safety, driven by the principle of zero harm, lies at the core of the mining industry. Digital technologies now offer new innovative ways to improve safety in this arena.
Technology, and the innovation that drives it, offers enormous benefits to the mining industry in the way it can be leveraged to improve safety across the sector.
This encompasses everything from safety training to solutions for on-the-job safety, and even includes using technology to help in handling the risks involved in the postmining closure phase.
LEVERAGING TECHNOLOGY
The latest technological advances in training, in the form of virtual reality (VR), are being introduced locally by KBC Health & Safety. Innovation manager Natalie Pitout explains that using VR allows learners to experience a simulated version of real-life dangerous scenarios. In this way, they can safely learn to mitigate the associated risks.
“The benefit of simulation is that it is not a real-life situation where a possible fatality could result. Instead, any wrong actions can be addressed safely and proactively,” says Pitout. She adds that VR is not a standalone competency module, but is being introduced as part of a blended learning approach.
Blended learning means there is a theoretical component designed to impart the necessary knowledge, which learners are then assessed on, followed by a virtual reality experiential component by means of headset goggles.
“A major benefit of virtual reality is that we can put people from different industries together in one room with the same virtual setting,” she says. “For example, coal and platinum miners can be engaged together to identify common hazards in their respective segments, and we can actually see how different workers react in different situations.”
By introducing analytics on the back end, she says, it becomes possible to identify if people are making the same mistakes, or whether they are identifying similar risks.
“If people are seen to be making the same mistakes, the hazards or risks can be identified for clients, and an appropriate virtual reality simulation suggested to remedy that problem.”
WEARABLE SOLUTIONS
When it comes to the safety of mine workers, says Thando Sibindi, managing executive for Mining, Manufacturing and Utilities at Vodacom Business, the company has developed smart technology known as the “connected worker”. This involves a smart device based on narrow band technology, which doesn’t draw a lot of power and can provide longer battery life.
“This device can be worn on the wrist or on their workwear, and as the employee moves around the mine, it sends back realtime information on what is going on in their environment. This allows for reactions in real time.
“For example, if they enter a geo-fenced area they are not supposed to be in, the device will instantly alert them to that fact. At the same time, of course, the operations centre undertaking the monitoring is also able to track that they are in a hazardous zone,” he says.
“The beauty of technology like this is that it not only improves safety, but also boosts efficiencies. For example, we have installed mobile private networks delivering high connectivity and low latency, to enhance the operation of these devices, which has the
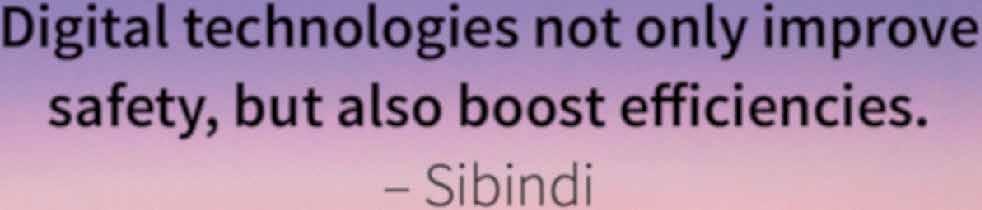
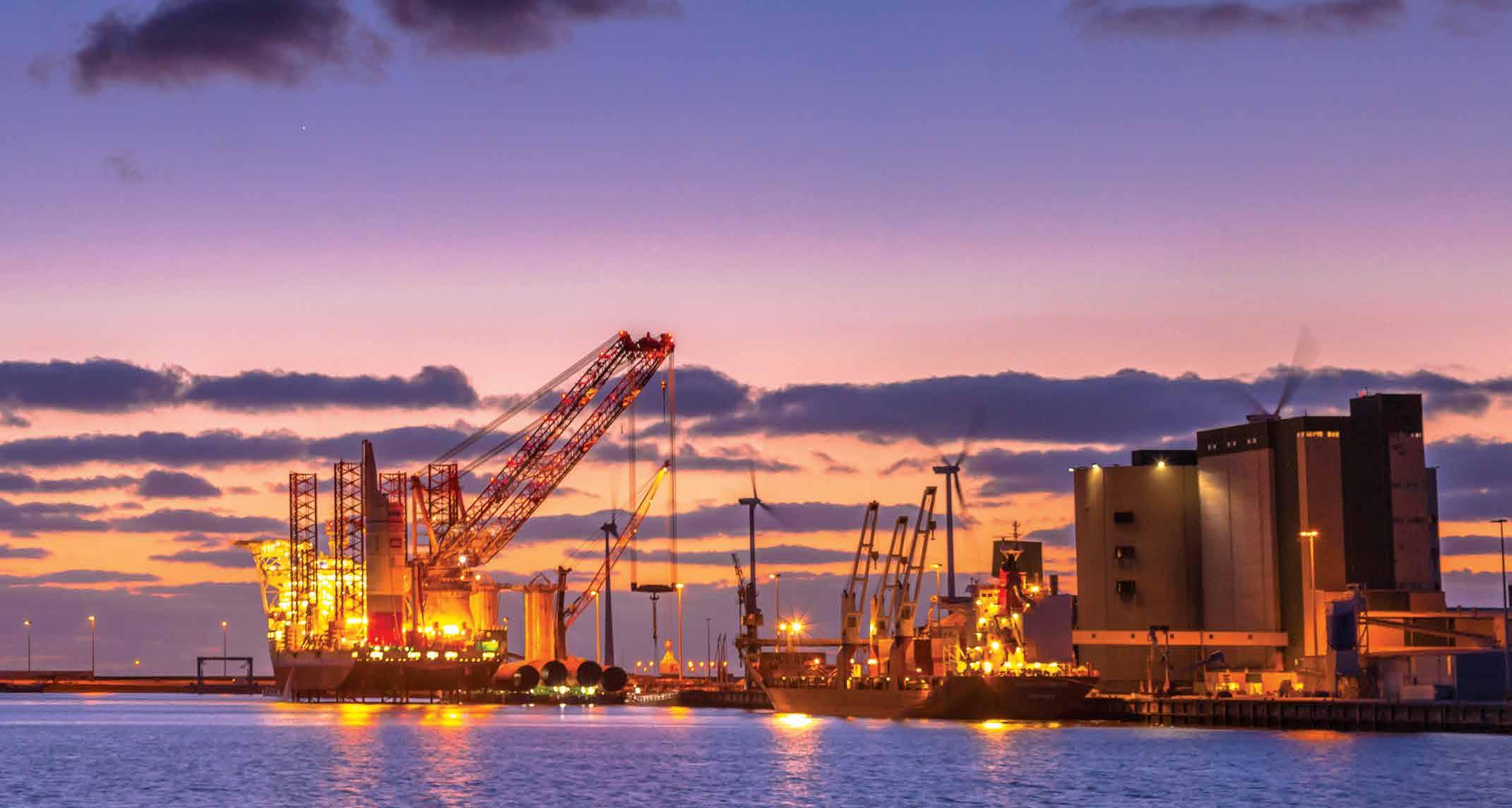
“Digital technologies not only improve safety, but also boost e iciencies. “ – Sibindi
SAFETY BEST PRACTICE

added benefit of improving communications too. Naturally, workers may be concerned that such monitoring is intrusive, but this simply requires worker education so they understand that this is for their safety.”
A practical example of how it improves safety, he adds, is how – with increasing automation of large mining vehicles occurring – people on the ground are equipped with sensors so that the computer driving the vehicle is aware of where all personnel are at all times.
“Personally, I think that mining organisations are reaching a tipping point as far as digital technologies go. It is critical to stay on top of technologies like this, as they roll out. Wearables like this are a great first step, but mines really need to consider digital transformation and automation as well. A er all, the more safety-focused technologies you have in place, the more easily they can adhere to the principles of zero harm,” says Sibindi.
SAFETY AFTER CLOSURE
Ettiene Van Der Watt, regional director of Axis Communications, a provider of internet of things (IoT) solutions, points out that when it comes to decommissioning a mine, there is legislation to be followed around issues of safety and public health.
“O en mines are re-established as grazing land or forest, and sometimes even for residential development. The public health and safety laws speak to the power of o -site monitoring – technology that can be the eyes and ears of the customer, even when no one is onsite,” he says.
“The use of motion detection, cameras and IoT sensors allows the customer to monitor the site, check for movement in certain classified zones, and even grant access rights to relevant individuals – via facial recognition technology – during the decommissioning phase.”
From a security perspective, he says, monitoring starts with security for those high-value autonomous vehicles that can take time to remove from the site. It then shi s to watching for illegal activities onsite during decommissioning.
He notes that in the closure phase, Axis recommends thermal sensors, which can cover tremendous distances, and don’t require lights to do their job.
“These devices can pick up heat signatures and are useful in multiple ways. They can identify accidental trespassers so they can be alerted to possible danger, but can also be used to track and monitor how well wildlife is returning to a decommissioned area, for example.
“The mining industry’s rich history also carries some important lessons, and one of these is that poor closure or abandonment of mines by the industry is a global challenge. It is thus imperative that companies evaluate the risks involved and invest in safety and security measures in the post-mining closure rehabilitation phase.
“Video surveillance systems that are designed to monitor a site with a high level of activity and thermal-based intrusion protection technology are some of the best tools available for securing vast remote perimeters,” he says. ■
Surface mining industry association ASPASA has released a comprehensive best-practice guideline that shows the correct way to deal with accidents and properly document findings in order to avoid similar accidents in future.
ASPASA director Nico Pienaar says: “Accident investigation is an important part of any safety management system. Without a detailed and thorough investigation, management has no true knowledge of the reasons why accidents occur and how to prevent re-occurrence.
“The idea is to give management a tool to use in the heat of the moment when confusion and uncertainty still surround events leading to the accident and subsequent outcome. Under these circumstances the simply written and easy-tounderstand document can ensure that all the necessary procedures are undertaken timeously.”

WORKER SAFETY

AND REHABILITATION
should be top of mind
Working closely with the Compensation Fund, RMA is focused on supporting employers to inculcate a culture of safety and a deeper understanding of injury rehabilitation in the mining and metal, iron and steel, and manufacturing industries.
There are several pieces of national legislation on health and safety (in both mining and manufacturing) that direct organisations on what to include in their health and safety systems and the set-up to prevent injuries and diseases in the workplace. These have very specific sections on the responsibilities of the employer and employees. But employers need to understand and appreciate that they also have a moral imperative to ensure the safety of their workers.
Moreover, suggests Dr Miranda Moloto, head of Rehabilitation at Rand Mutual Assurance (RMA), they must understand that there is a holistic benefit and broader contribution to the organisation through enhanced productivity and cost management for employers and improved wellness for employees.
“RMA, as an organisation that focuses on administration compensation of occupational injuries and diseases, we constantly witness that compensation involves far more than just the payment of a disability claim.
“It also encompasses the impact of an injury/disease on an employee’s health, posta liction mental state and sexual health, as well as the family’s earnings and dependents, due to workers sometimes being sole providers, not only for their immediate but also o en their extended families,” she says.
“To this end, we encourage companies to implement codes of good practice that are in line with the Mine Health and Safety Act and the Occupational Health and Safety Act and their respective regulations.
“This includes aspects such as training, elimination of hazards and/or management of risk exposures in a workplace, providing relevant warning signs and safety equipment etc.
“The real challenge with some organisations is that the health and safety programmes are not supported by leadership, and the tone at the top is not strong in promoting a health and safety culture. Therefore no basic health and safety systems exist with procedures, performance indicators, incentives and toolkits.
“An e ective health and safety framework
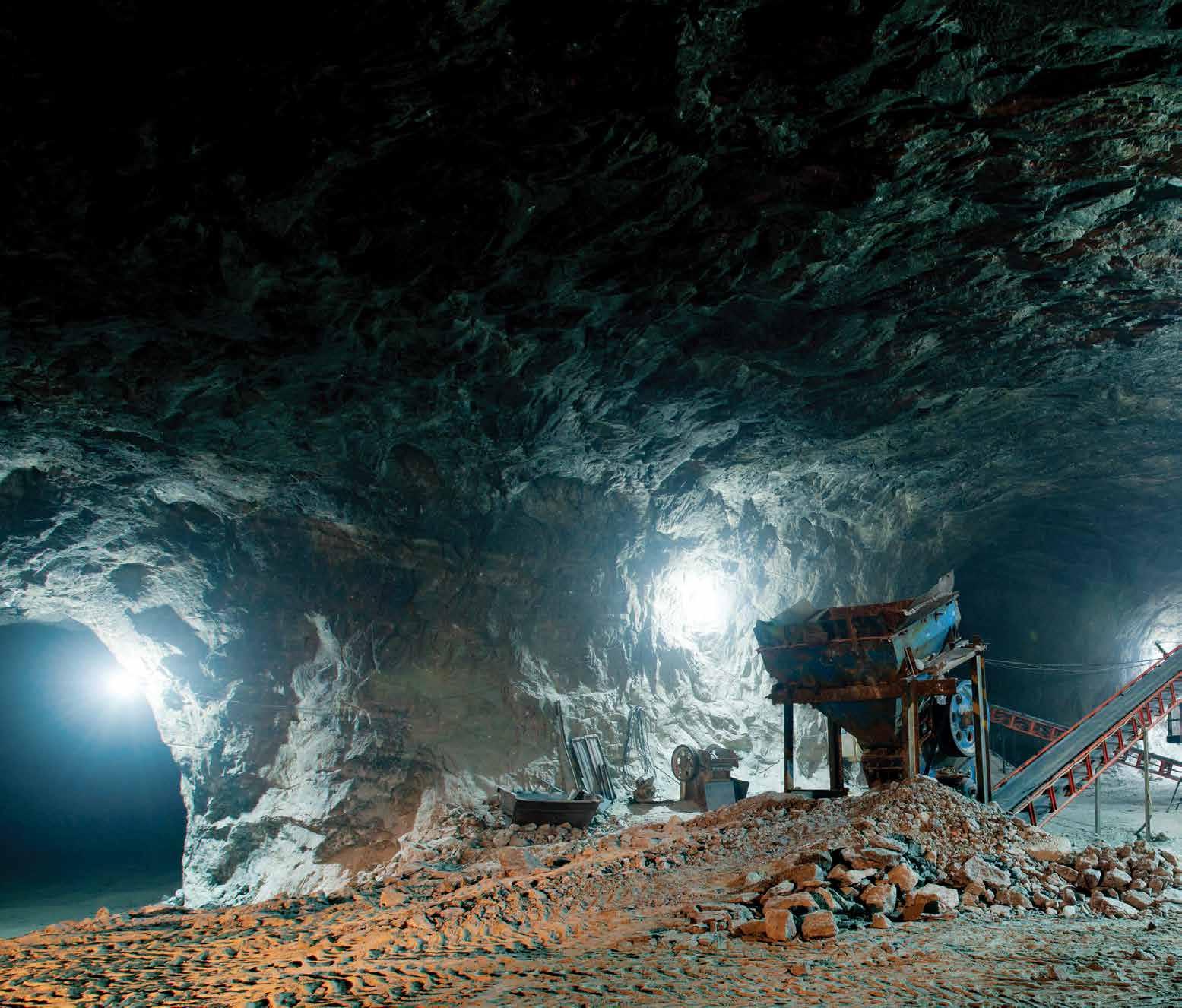
“Instilling a culture of safety in every aspect of the business begins with leadership. – Moloto
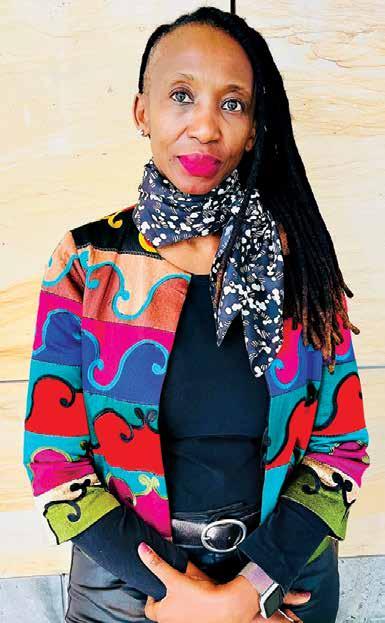
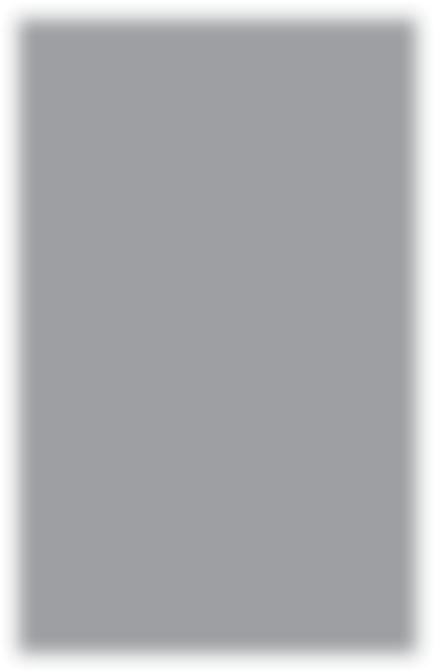
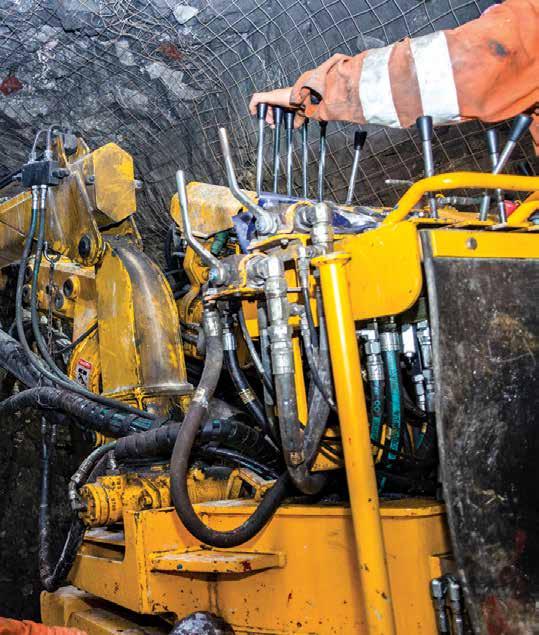

cannot simply begin with the provision of personal protective equipment.”
She adds that it is ironic that in the corporate world, data safety is high on the radar, with many programmes designed to inculcate a security mindset; yet in labourintensive industries, there is o en less focus on physical safety.
“Leadership sets the tone and direction for health and safety through various enablers – by including safety on the organisation’s strategic agenda. This provides direction for the broader organisation, including the promotion and importance of the safety and health function.
“The organisation’s health and safety policy and fundamentals then provide context on appointing the right people and safety performance requirements.”
DEALING WITH DISABLED EMPLOYEES
Moloto notes that despite the high levels of permanent disability in the industry, very little attention appears to be paid to the rights of disabled workers, and there are few comprehensive programmes to address their issues, post-injury or post-compensation.
“RMA, as a funder, is taking its cue from the imminent Compensation for Occupational Injuries and Diseases Amendment Bill on how organisations should deal with workers who have become disabled through injuries.
“It is important that companies work to ensure these employees can still have some level of earning capacity, even if they can’t go underground a er an amputation, for example. They should seek to instead find an above-ground position for them, allowing them to remain economically viable and restore their dignity.”
This dignity is critical, although organisations don’t always take it into account, she says. “You simply cannot put a value on something like this.”
When it comes to rehabilitation, Moloto says the programme has various pillars. Initially in the clinical rehabilitation pillar, which is the acute phase a er injury, they have access to the relevant healthcare and specialists for their type of injury or disease. In some cases the injured worker is able to be introduced early to rehabilitation for physical and occupational therapy. This is a vital step towards accelerated return to work.
The other two pillars of the programme include vocational rehabilitation, which
Dr Miranda Moloto.
COMPENSATION ENCOMPASSES:
■ payment of disability claims ■ impact on employee’s health ■ post-injury mental state ■ psycho-sexual health ■ families’ earnings and dependents’ future
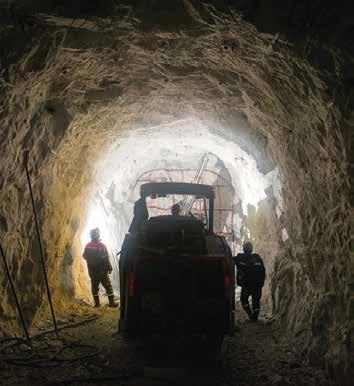
ensures reskilling and possibly returning the worker to meaningful employment even if it’s not their pre-morbid work. Social reintegration is the pillar beyond the workplace to return the newly abled worker back to their family and community.
CHANGING MINDSETS
“Enabling previously injured employees is all about changing the mindsets of workers and their employers and communities. Too often, an amputee is essentially ‘written off’ due to such an injury, when – with the appropriate vocational rehabilitation – they could be trained to do a different job.”
She says it all starts with the culture of the organisation and its leaders determining what they stand for as an organisation. Are they only in business for the profit, or does the focus also include protecting their employees from workplace injuries or diseases? If they choose the latter, then leadership must inculcate the culture of safety.
They are in a position to ensure that they introduce preventive strategies and programmes and by also employing the right health and safety officers and medical practitioners. They will also be able to ensure that employees are not only properly skilled, but are also compensated well if injured.
“We also encourage organisations to ensure they conduct a proper investigation of any incident leading to the injury. This is crucial, as it is important to close the loop by finding out exactly what went wrong and how the injury occurred, in order to prevent it from happening again – something that must also include consequence management.”
Moloto points to a strategic prevention programme introduced and launched in April by RMA. This, she says, is about making occupational health and safety abilities accessible to small and medium enterprises, which don’t always have capacity to purchase technology to help track injuries and investigations. More importantly it’s about RMA supporting employers in reducing the rate of accidents.
“We are committed to partnering with employers and bringing additional capabilities that might be required to supplement their health and safety strategies and programmes. This is a key project for us, and we are working with different stakeholders for the purpose of keeping the worker safe, supporting them in the rehabilitation process, but more importantly in ultimately preserving and restoring their dignity.
“We are very excited about both our prevention and rehabilitation programmes, which we feel will be a step change for occupational health and safety and rehabilitation, reintegration and early return to work.
“We have a moral obligation to keep employees safe. This means that safety, rehabilitation and compensation are absolutely critical aspects to a modern mining organisation’s business operations,” says Moloto. n
For business, there is a tangible legal and moral obligation to keep employees safe. “ “ – Moloto
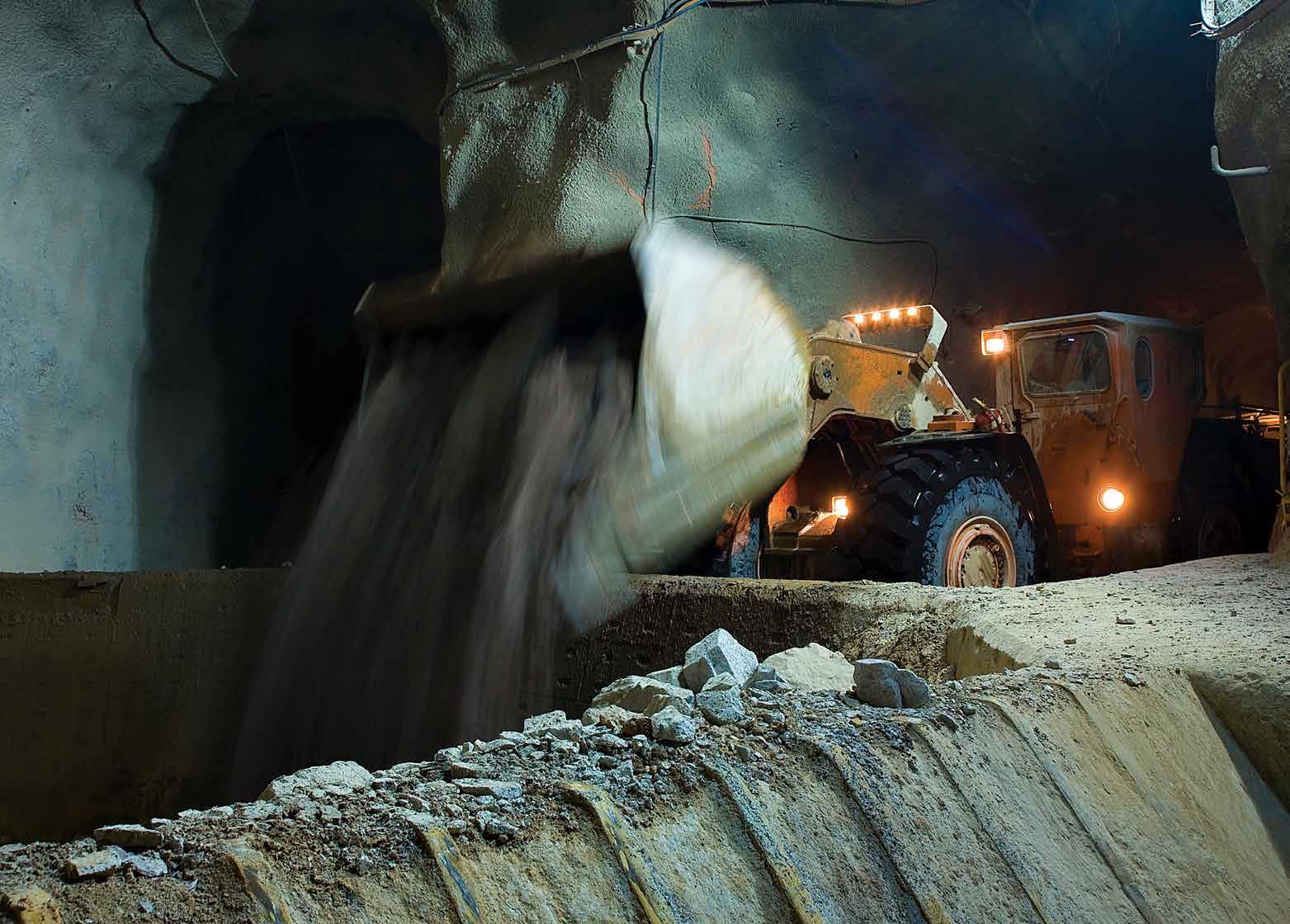