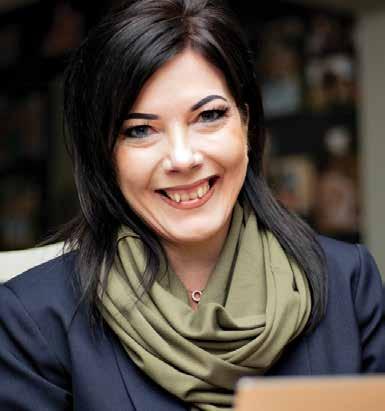
31 minute read
Women in Mining
PUTTING THE “HUMAN” BACK IN HUMAN RESOURCES
Janine Oliver. New president of the South African Collieries Human Resources Association (SACHRA) Janine Olivier talks about improving workers’ lives and advancing the role of women in the mining sector

Janine Olivier took on the role of president at SACHRA at the start of July and is human resources (HR) manager at the Thungela-owned Zibulo Colliery. Thungela, the largest coal exporter in the country, was certified as a Top Employer in South Africa by the Global Top Employers’ Institute early this year.
SACHRA, a forum for HR professionals in the coal mining sector, gives members an opportunity to grow in a field that is o en seen as a support function. However HR has a critical strategic role to play in any organisation’s success, she says.
“As HR, we’re responsible for attracting the right talent and then developing and retaining that talent so that we can take our business forward.
“At the same time, we must give our people every opportunity to reach their personal and professional potential.”
Added to this, she believes, positive people practices have the power to influence behavioural safety.
“It’s up to us to ensure that our people can bring their best selves to work so that they can be safe and productive. Are they happy and healthy? Do they feel rewarded and that their work is meaningful? Are they responsible and accountable? And, if not, what are we as HR professionals doing about it?”
During her presidency Olivier will be building on the work the mining sector has done to create an enabling environment for women.
She notes that if the industry hopes to increase the participation of women, it is imperative that they are seen to occupy senior positions.
“The question is no longer whether women can achieve success in mining. They’ve been doing that for years. Now it’s more about how we can grow women into positions that will strengthen the sector as a whole.
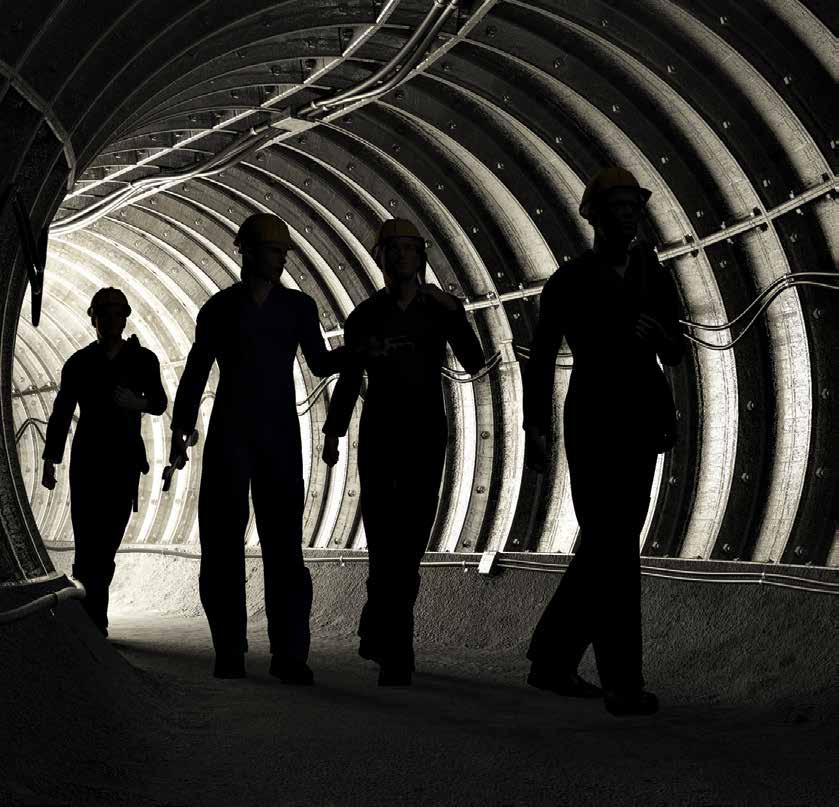
We should be asking how we can grow“ “ women into positions that will strengthen the organisation as a whole. – Olivier
“HR has a crucial role to play here too, especially in changing gender perceptions. We need to have programmes in place to help women grow their careers, while still being able to focus on their families. While equality and parity have not yet been achieved, we have seen a tangible uptick over the last decade; we simply need to continue on this path,” Olivier concludes.
In her role at SACHRA, she’s on a drive to grow the association’s membership by attracting bright, diverse and dynamic new talent and putting a fresh new face on a body that has been serving the industry for more than 20 years. ■

Lindiwe Nakedi.
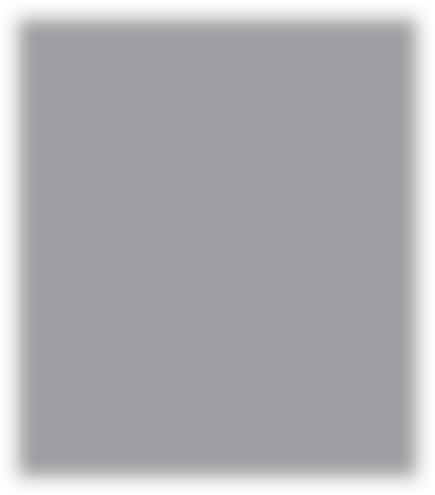
It has o en been said that women are capable of doing anything, but Lindiwe Nakedi takes this to a whole new level. She describes herself as a wife, mother, and owner/MD of Gubhani Exploration, a surface exploration diamond drilling company started in 2009. On top of this, she served as chairperson of Women in Mining South Africa in 2017 and 2018, and is now a board member and patron. Nakedi is also co-founder and director on the board of Women In Mining
Business, and in 2018 she was selected as one of Top 100 Global Inspirational Women in Mining by Women in Mining UK. “My husband, who was working at the time as an exploration geologist for Sasol, sparked my interest in the industry,” says
Nakedi. “I loved the huge scale of mining operations, something that still fascinates me today. However, the main reason we chose to start the business was to work towards our vision, which is to make a di erence in people’s lives. A er all, drilling is a very lucrative business, so it enables us do that.
KNOWLEDGE IS POWER
As the fi rst black female to own a surface drilling company, Lindiwe Nakedi wants to be a role model for young women everywhere
“I am a very adaptable and teachable person, which is a good thing as I did not study anything mining or engineering related. Instead, I saw an opportunity to learn something about which I had no clue. This gave me the opportunity to build relationships, by accepting the fact that people would feel the need to educate me when they got the chance. This worked for me too as, a er all, knowledge is power!”
ROOM FOR ALL
Nakedi believes that there is enough room for everyone in this industry as the mining pie is large enough, referring to this mindset as an “abundance mentality”. She quotes Stephen Covey, author of The Seven Habits of Highly E ective People: “Have an abundance mentality – if you think and believe there is more, there will be more,” adding that this means there is no need to scramble for opportunities.
“I also feel that men are now more accepting of the increasing number of women professionals and business owners in the sector, as we have proved our knowledge, resilience and passion,” says Nakedi. “They recognise that we add value and make a positive impact in the industry, and that ultimately our purpose is the same as theirs: to help others grow.”
Nakedi is firm in her belief that women need to be present in every area of the economy, in order for young women to see what is possible and feel aspirations. “I also believe that what I do isn’t just about me; I have a responsibility to the other young women who come a er me. Being the first black female to own a surface drilling company is great, but it is important that other owners follow and hopefully find it a little easier to become whatever they choose.
“My advice to women entering this sector is to understand that opportunities are vast if you are willing to ask questions and learn. Also, be willing to start right at the bottom, and remain committed and professional in your work ethic and attitude, as this is what will speak loudest for you,” says Nakedi. ■
Women need to be present in every area of “ “ the economy, in order for young women to see what is possible. – Nakedi
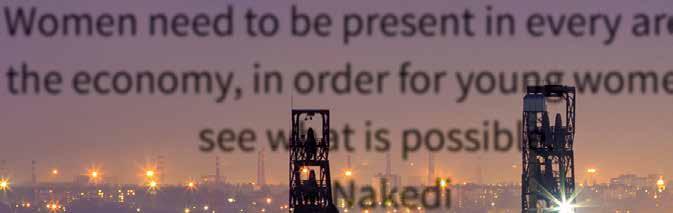


Noluthando Zulu.
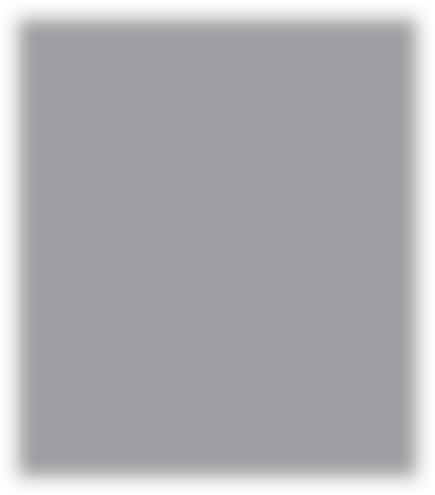

Dwala Mining MD Noluthando Zulu was born in raised in Durban. She was not exposed to the mining industry or any mining professionals until the day, at the age of 17, when she saw a picture of Patrice
Motsepe on the cover of Business Times with the headline: “Mining tycoon Motsepe now worth R8 billion”. “For the first time in my life, I saw a di erent image of mining compared to what
I had grown up seeing on TV,” says Zulu. “It was not the miner who was living in terrible conditions in a hostel; instead I saw a person who looked like me, thriving through their participation in the industry. “The result was me considering the di erent careers I could follow in the mining sector, and becoming a geologist. I studied
Geology at the University of KwaZulu-Natal, completing my undergraduate and honours degrees.”
STARTING FROM THE BOTTOM
Zulu started her mining career as an underground production geologist at Royal Bafokeng Platinum, where she worked her way up the ranks in the geology department.
TAKING THE PLUNGE
Noluthando Zulu has worked her way from under the ground to the top of her own mining company
A desire to understand the entire value chain and the business of mining saw her transition into the financial sector, as an equity analyst covering mining equities.
“I spent the bulk of my career in the financial sector at the Public Investment Corporation, as part of a team managing the listed mining fund. I was honoured to be given the opportunity to work as an executive assistant to the group director of Anglo American South Africa for two years, before taking the plunge and following my dream: to be a well-rounded leader of my own organisation. Today I am the MD of Dwala Mining, a junior mining and services business established in 2014 with my business partner, Nompilo Sindane.”
LEAP OF FAITH
Asked what unique attributes she thinks women bring to the industry, Zulu says that while she can’t speak for others, she believes her relationship-building and networking skills have assisted her greatly in winning people over and getting them to buy into a common goal. “Focusing on people’s humanity, by simply greeting with a warm smile and giving a big congratulations and thank you when they have done well, or gone above and beyond what is required, was my ‘superpower’ when managing people underground.”
Zulu believes that the mining industry is better thanks to the inclusion of women. She hopes that through their engagement with female peers, men in mining will recognise that women are intelligent, strong and competent.
“With Dwala Mining, Nompilo and I were two young female geologists who took a leap of faith a er 10 years of building careers within the mining industry. I hope our story of courage and self-belief inspires young women to believe in themselves and grab the opportunities that lie before them in the same manner we did.
“To young women, I say: There is no industry that is reserved for men and there are no rooms where women don’t belong. We have to educate and equip ourselves with the relevant skills, search for opportunities and take advantage of all the amazing local pro-women policies. In the end, the pie is massive, and we as women need to get involved and take our share,” she says. ■
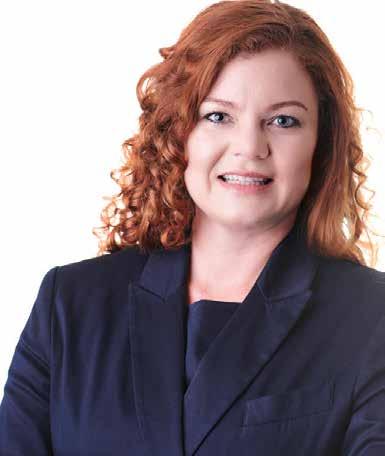
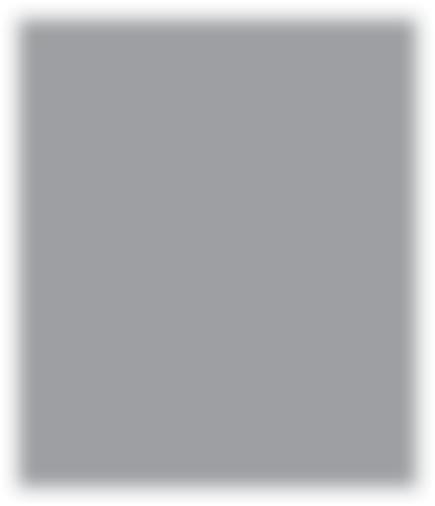
Ingrid Osborne
Ingrid Osborne briefly worked for a boss following her graduation, but it wasn’t long before she founded Saryx Engineering Group with Julie Mathieson – her long-time friend and business partner. “Julie and I wanted to create a version of a company that we would be proud of, that suited working women, especially in the engineering world. A business that was perhaps aware and cognisant of the challenges that working parents face when trying to build a career, while also being a present parent,” she says. An electronic engineer by trade,
Osborne studied for her Bachelor of
Electronic Engineering at the University of
Stellenbosch, and did her Honours at the
University of KwaZulu-Natal. “Julie and I have always had very similar ideas on where we would like to go, and the financial challenges that engineering projects come with. It can be a bit of a rollercoaster ride. Creating our own internal suite of products provided much-needed stability and continuity. The success of these solutions can be measured by the fact that it is available in 14 countries, and Saryx is in the process of expanding the business into the United States.” She is not one for grouping women together with stereotypical attributes, suggesting instead that each individual has their own set of attributes. Nonetheless, , she believes the inclusion of women powerfully changes the conversation. “With anything, the moment you have someone di erent in the conversation, it changes the discussion and provides a di erent perspective. And this is very important when it comes to engineering. All engineers, simply stated, are professional problem solvers – so having new ideas and alternative perspectives is critical for innovation and problem solving.” Perceptions of women in engineering haven’t really changed all that much, she says, even though there are no barriers to women studying engineering. Many men and women still seem surprised when a woman declares that she is an engineer.
She points to studies, including one by ResearchGate, in which professors evaluated the application of an undergraduate science student who was applying for a science manager position. The only di erence in the application was that the gender of the applicant was changed.
Professors of either gender judged a female student to be less competent and less worthy of being hired than the identical male student, and also o ered her a smaller starting salary and less career mentoring. It is these perceptions that need to be changed, says Osborne.
“So I guess seeing women succeed in the engineering world starts to change these biases we have, and hopefully will start to encourage women to enter into engineering with confidence and certainty. It’s always good if you can see someone else like you has succeeded already, as it makes it easier to believe that you can too – and you can!”
And what words of advice would she o er women considering a career in this field?
“It takes hard work. The course is tough and takes dedication and grit, so engineering must be something you really want to do. It is still a male-dominated industry, but that’s okay – there are plenty of male engineers who are great to work with; and in all honesty, your attitude will determine your work experiences.
“Most importantly, make it something you love. You will spend an extraordinary amount of time at work, and you need to love what you do in order to stay in the industry,” she says. ■
ENGINEERING A MORE EQUAL WORLD
While seeing women engineers still surprises some people, Saryx Engineering Group CEO Ingrid Osborne is doing her best to destroy stereotypes

I believe that the inclusion of women powerfully changes the conversation. “ “ – Osborne

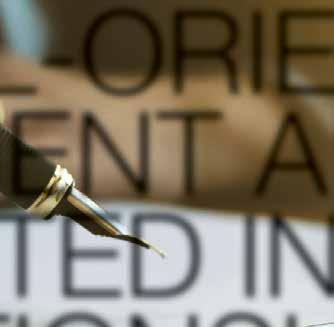
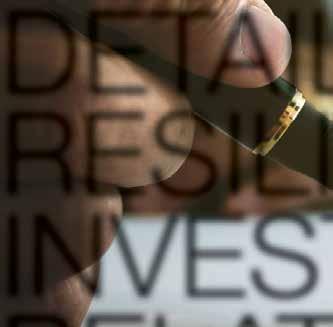
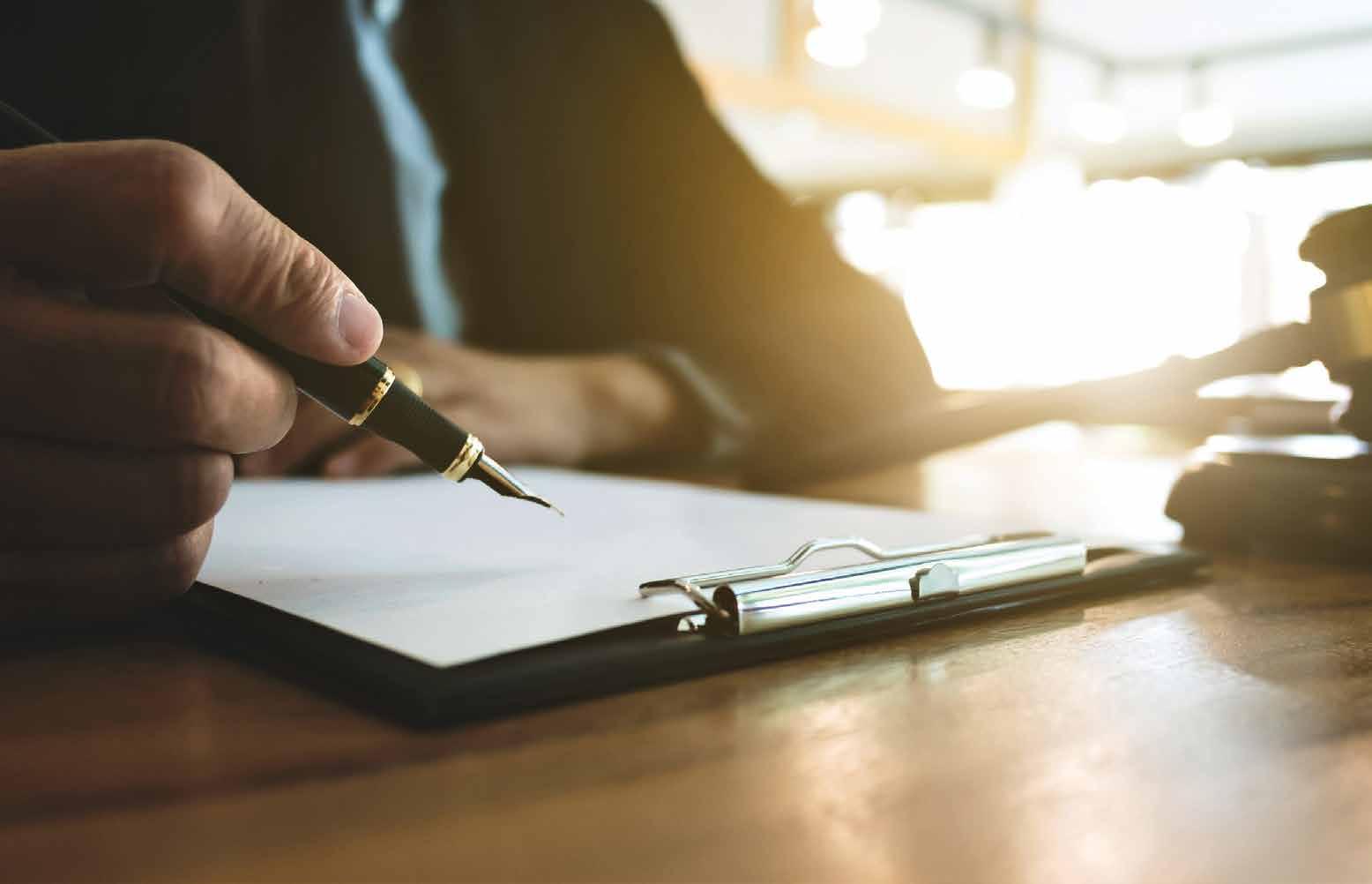
Chantal Murdock, law fi rm NSDV’s Mining Regulatory Compliance director, believes that women need to embrace their own strengths
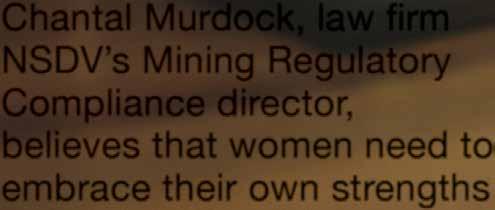
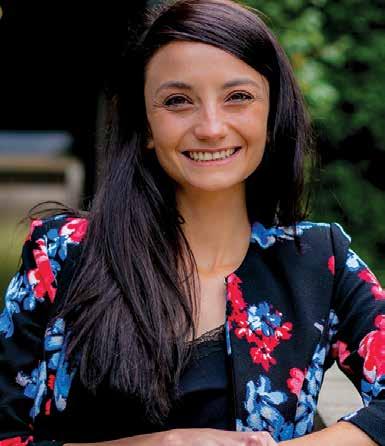
Chantal Murdock’s career started at C Bekker and Associates, where she believes she received “the best legal training any candidate attorney could ask for”. Her principal entrusted her to help him with a few disputes relating to mining rights granted under the Mineral and Petroleum
Resources Development Act – and her fascination with mining began.
“Once I completed my articles and practised as an attorney for a short while,
I joined the late Kevin Pietersen at his own niche firm (Pietersen Inc.), which specialised in mining and commercial law. Kevin gave me an opportunity to join the Hogan Lovells mining department.”
She enjoyed mining law “because it touches so many facets of the law and is always developing”. She spent five years at
Hogan Lovells before “hearing about the waves that NSDV was making in the industry.
The rest, as they say, is history”.
“I started in March 2020 with NSDV as a senior associate in the mining team. I was incredibly nervous as I was completely unsure of myself. But director Lili Nupen was so supportive of me (even when the world went into lockdown) and kept motivating me to embrace my career and the experiences that I had been so fortunate to have had. Under her guidance and leadership I have grown tremendously in confidence (and I believe, ability too), having been promoted to director last year.”
As a director in the mining team, she says her current role centres around reviewing associates’ work, training, managing workflow and engaging with clients. It carries with it great responsibility, but is very satisfying and rewarding, she says.
“I am detail-oriented, resilient and deeply invested in my relationships with people. This has not only helped me to remain openminded and adaptable to change, but has also taught me to be ‘mentally tough’ and keep going until I get the necessary results – something which I believe transcends gender prejudice.
“I am testament to the fact that women (and men) supporting women has definitely assisted the legal industry over the past few years in making substantial progress in closing the gap between genders in the legal industry. There is, however, still significant gender prejudice against women in mining at an operational level.”
She notes that the Department of Mineral Resources and Energy has recognised this, and has indicated that it’s in the process of dra ing a mining sector Women Empowerment and Gender Equality Strategy.
“This is an opportunity for a me as a female lawyer to encourage other young women, by assisting them in engaging and commenting on the strategy, so that it can be developed to cater specifically for our needs.
“If I were to o er a word of advice to women either seeking a career in, or wanting to join, the mining industry, here it is: although there will be challenges, embrace and nurture your own strengths as a woman – and don’t take ‘no’ for an answer.” ■
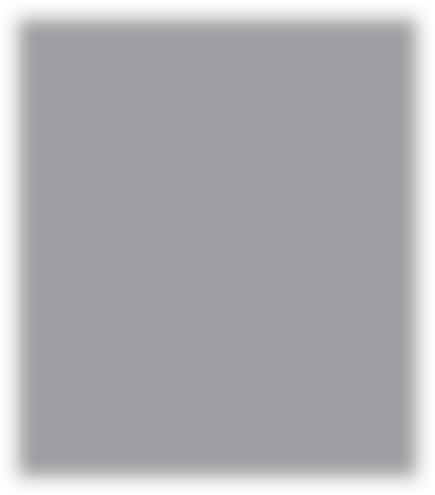
I am testament to the fact that women (and “ “ men) supporting women has definitely assisted the legal industry over the past few years. – Murdock
Chantal Murdock.
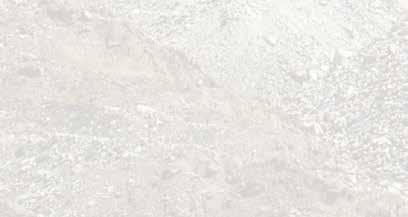

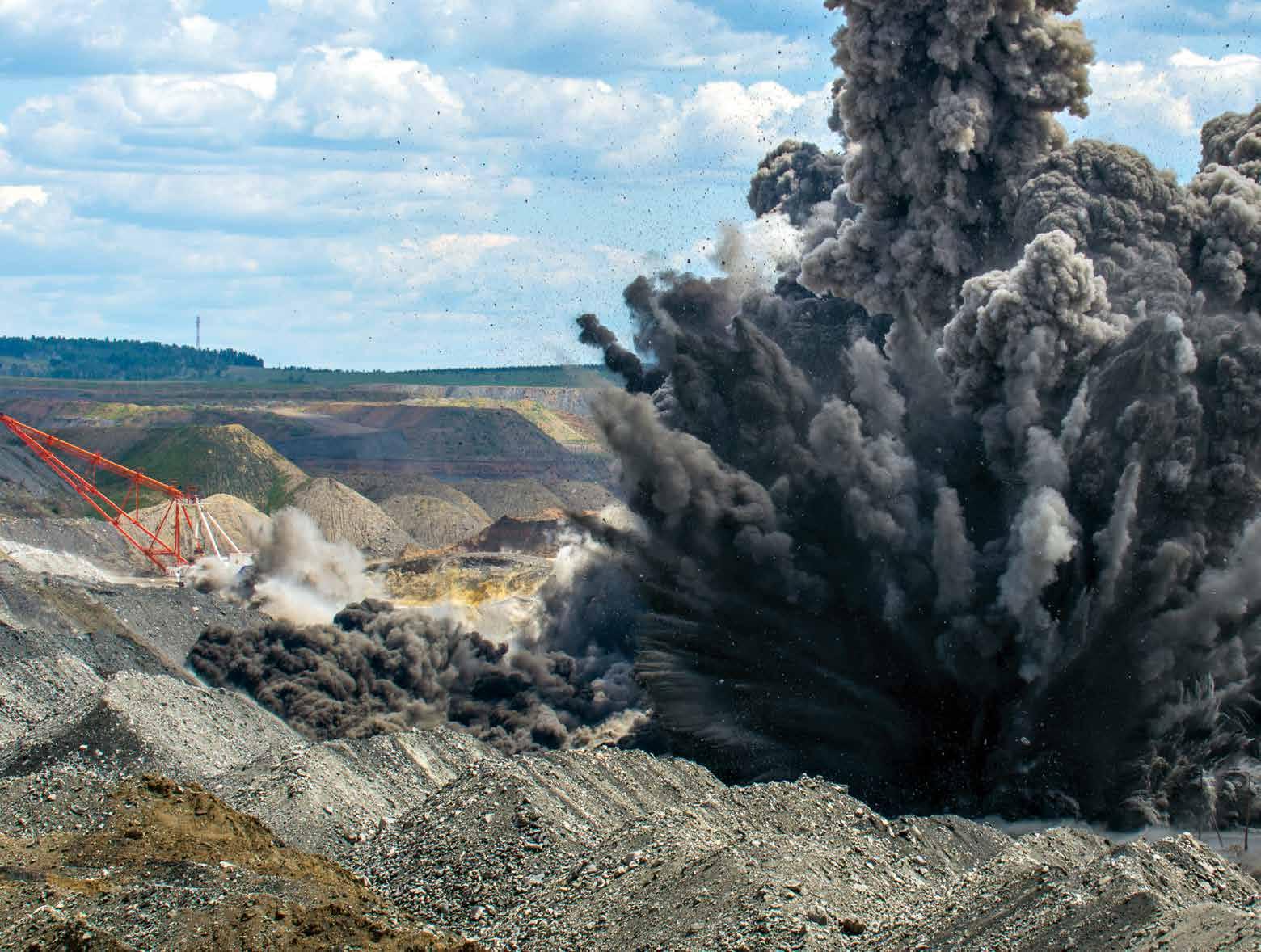
A BOOMING MARKET IN EXPLOSIVE TECHNOLOGIES
Two new technologies entering the market are designed to make blasting less dangerous
By Benjamin van der Veen
Safety and good fragmentation are two parameters of principal significance in any blasting process, says Ashlin Pillay, Initiating Systems product manager at AECI Mining Explosives.
“By introducing an increased level of autonomy to the blast hole tagging process, a global positioning system enables faster blast deployment, greater accuracy and increased e iciency. The significance to the customer is improved safety and fragmentation.
“Uniform fragmentation to the customer’s desired size contributes massively to e icient blasting and o ers increased e iciency throughout the beneficiation process,” he says.
These words set the stage for some of the most recent innovations and developments in blasting and explosive technology.
Both AECI and Omnia’s BME have developed and released cutting-edge technologies that will ensure that blasting in both large and small mines is safer and more accurate, resulting in sustainable and e icient mining.
This feature looks at AECI’s PowerBoost technology and Omnia’s BME AXXISS Titanium™.
SIMPLER, SAFER BOOSTER TECHNOLOGY
AECI Mining Explosives has launched its new PowerBoost booster. PowerBoost is described as a global industry first, something that will transform the explosives sector, due to its use of non-explosive raw materials in its manufacture.
“Moving away from conventional industry practices of combining explosives mixtures of PETN, TNT and/or RDX in the manufacture of explosives boosters, AECI’s new PowerBoost booster creates a powerful booster from nonexplosive raw materials,” says Hazel Bomba, AECI Mining Explosives product manager.
“We have been working on developing the PowerBoost booster for some time, with a keen objective to commercialise alternative technologies to meet the growing market demand for boosters worldwide.”
PowerBoost technology pivots away from the industry norm by eliminating the use, management, handling and storage of traditionally used explosives-based mixtures, which come with high costs in regulatory and legislative obligations.
“We’ve managed to successfully introduce a simplified, safer manner of manufacturing boosters, while still providing a premium o ering to the market,” she adds.
An ongoing concern within the global mining explosives industry is the risk inherent in storing and transporting bulk explosive material. Paramount to AECI Mining’s vision is an acute focus on rendering the explosives value chain safer.
The PowerBoost technology contributes to this quest, explicitly enhancing the safety surrounding the manufacture of explosives. Additionally, decoupling the booster raw materials from the established supply chains for global TNT and PETN has strengthened AECI’s ability to supply boosters into the market.
ADVANCED ELECTRONIC BLAST DETONATION SYSTEM
Safe and e icient blasting has taken a leap forward with BME’s launch of AXXIS Titanium™, one of the world’s most advanced electronic blast detonation systems.
BME managing director for the Southern African Development Community Ralf Hennecke has hailed the solution as a significant advance for the company’s everevolving technology o ering, securing BME’s position among the leaders in electronic delay detonator design.
“The new release raises the bar globally for the electronic detonator market,” says >

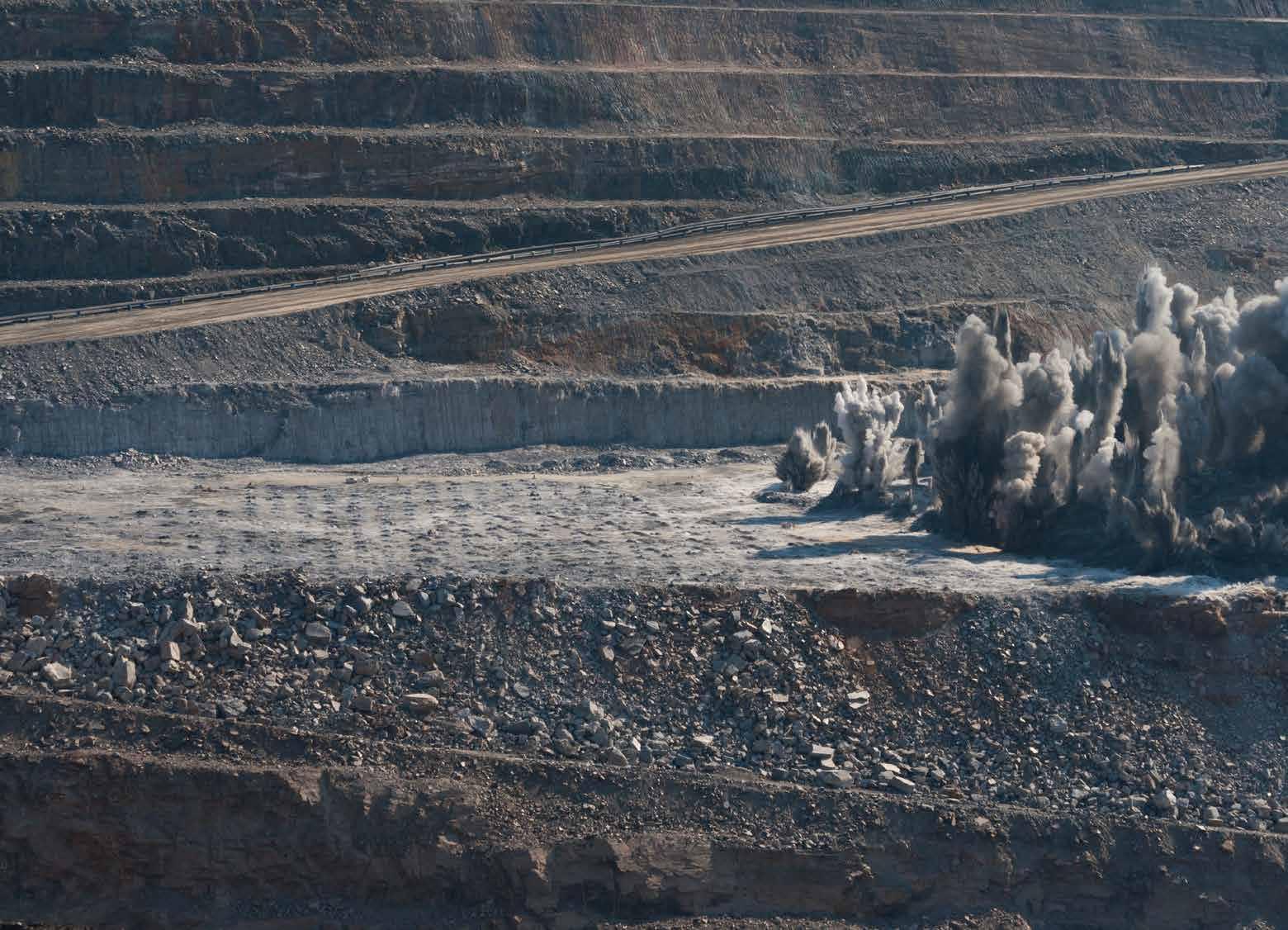
Hennecke. “This flagship product reflects our continued focus on digital advancement on mines, and is designed to seamlessly integrate with BME’s so ware systems and handheld digital tools.”
AXXIS Titanium™ improves safety levels and manufacturing quality through enhanced communication with the detonator during manufacturing, to avoid defects. Performance is raised through the increased blast duration per detonator, more units per blasting box and precise firing accuracy.
“Most importantly, the system was built for the blaster and blast engineers who work with the product every day,” he notes. “The robustness of the wire, the easy-to-use interface and the improved integration will improve e iciency in terms of time, data and reporting.”
As the latest generation of BME’s popular and well-proven AXXIS system, Titanium™ takes blasting safety and flexibility to a new level, according to Tinus Brits, BME’s global product manager for AXXIS. The company has, over the decades, made regular advances in the performance, safety and reliability of this innovative solution, he says.
“This latest iteration builds on the achievements of the AXXIS GII™ model and improves many of the features that have served our customers so well. These include further refinements in safety, accuracy, flexibility, ease of use and speed in preparing each blast.”
SAFETY REMAINS KEY
Safety remains the watchword, incorporating a Swiss-designed application-specific integrated circuit (ASIC) chip in the BME detonators, delivering several benefits. The ASIC gives the system more internal safety gates against stray current and lightning, enhancing safety levels and allowing for safe logging and testing.
“A unique innovation is the use of dual capacitors and dual voltage, allowing us to conduct low voltage logging, to avoid any chance of detonation. Blasts are initiated by a robust and encrypted blast command, ensuring that detonators receive their respective commands and fire as planned.”
He emphasises further that the detonator will only react if it receives the correct, encrypted firing sequence from the blasting equipment, not from any other source.
“We have developed AXXIS Titanium™ to be resistant to electro-magnetic pulses (EMPs) caused by the blast, which can a ect the accuracy of detonators or even cause them to fail,” he says. “Intensive tests in conjunction with the Council for Scientific and Industrial Research have shown that our detonators can withstand a significant EMP without any impact on their timing.”
The accuracy of the detonation delays has been further fine-tuned, he continues, reaching a 0.02% firing accuracy for consistent and quality blasting that results in better rock fragmentation and consistency. He highlights the positive impact this has on the e iciency of crucial mine measurables like loading rates and crusher throughput.
“This in turn helps mines improve their carbon footprints as they pursue increasingly vital sustainability targets,” says Brits. “In this way, BME’s technology innovation is closely aligned with the Omnia Group’s ongoing focus on sustainability, which prioritises zero harm and positive impact to build a better future.” ■
Blasts are initiated by a “ robust and encrypted blast command, ensuring that “ detonators receive their respective commands and fire as planned. – Brits
ENABLING

EXPLOSIVE OPPORTUNITIES
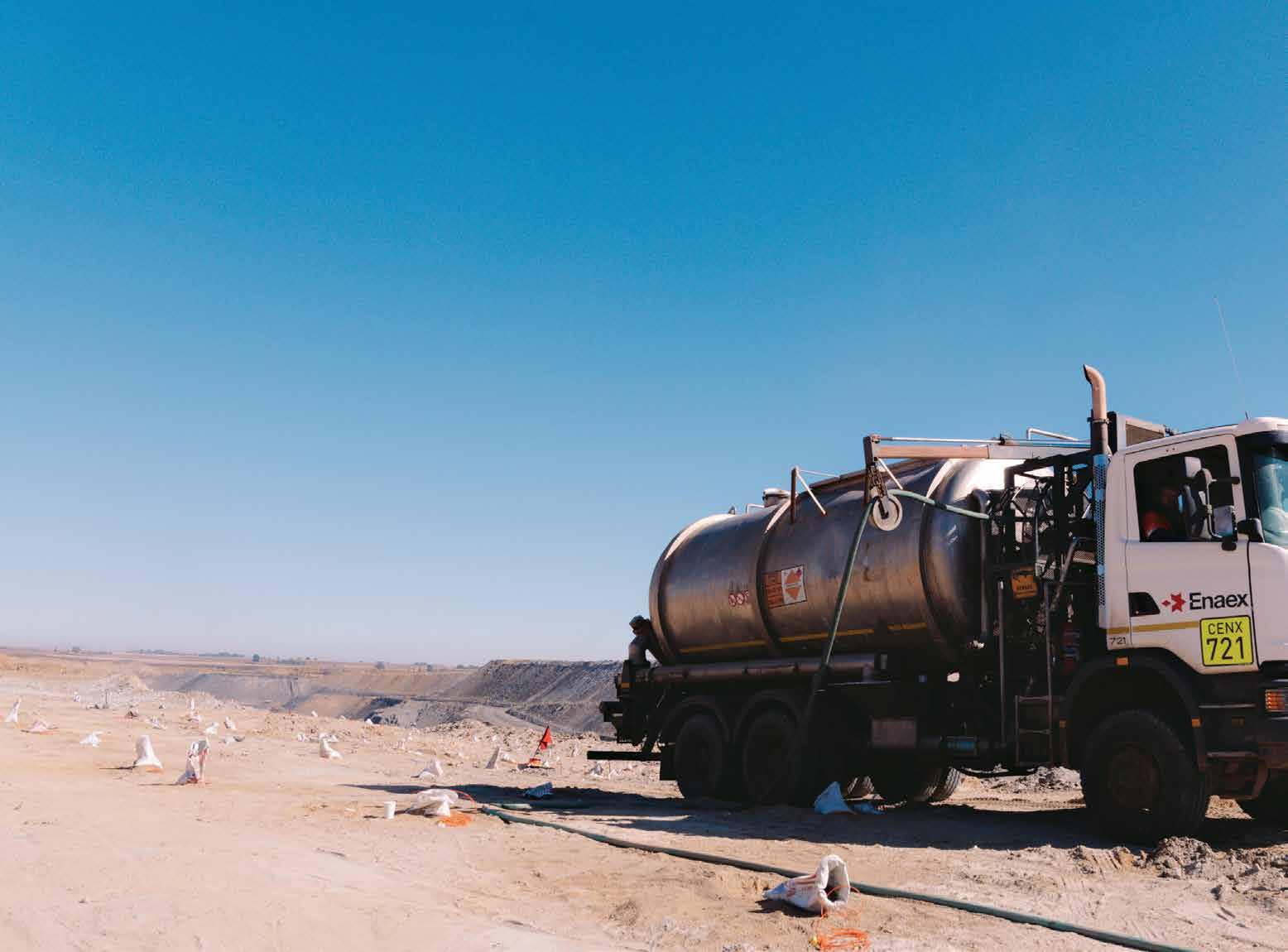
for Africa and women in mining
Enaex Africa is making waves on the continent – not only with its innovative technology that is transforming the mining industry, but also with its passion and drive to empower female employees. Enaex Africa is one of the largest explosives companies in Southern Africa.
It’s focused on the mining industry and is a subsidiary of Enaex Group – one of the top three leading mining explosives companies in the world. It has introduced innovative technologies that are helping the local mining industry to increase e iciency and improve safety. Enaex was founded more than 100 years ago in 1920, and is part of a large, dynamic
Chilean conglomerate with a strong longterm investment approach, called Sigdo
Koppers Group. Enaex manufactures and supplies explosives to the mining industry and provides premium blasting services to prominent mining companies around the world. As part of its global growth and development strategy, the company identified Africa as a key mining region that forms a strategic pillar in the success of its global expansion plan. South Africa was chosen as the most relevant country to establish this new development as the gateway to starting operations in Africa.
In parallel, during 2017, Sasol South Africa commenced with a detailed asset review to ensure all assets in the company’s global portfolio delivered against stringent financial metrics and were aligned with the company’s growth strategy.
In line with this review, Sasol’s explosives business was identified as having substantial growth potential that could be unlocked through collaboration opportunities, including the possibility of partnering with a world-class explosives brand. This strategic opportunity was identified and enabled by a team led by Enaex Africa’s CEO, Francisco Baudrand.
In June 2019, a er a robust evaluation process and successful identification of an explosive partnership opportunity by Baudrand, the organisation was selected as

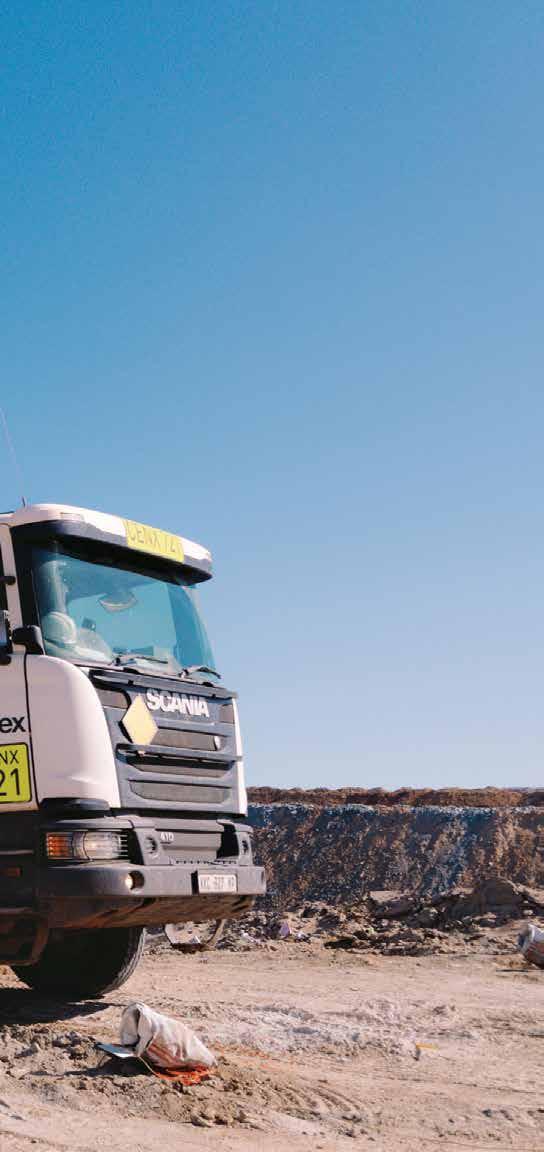
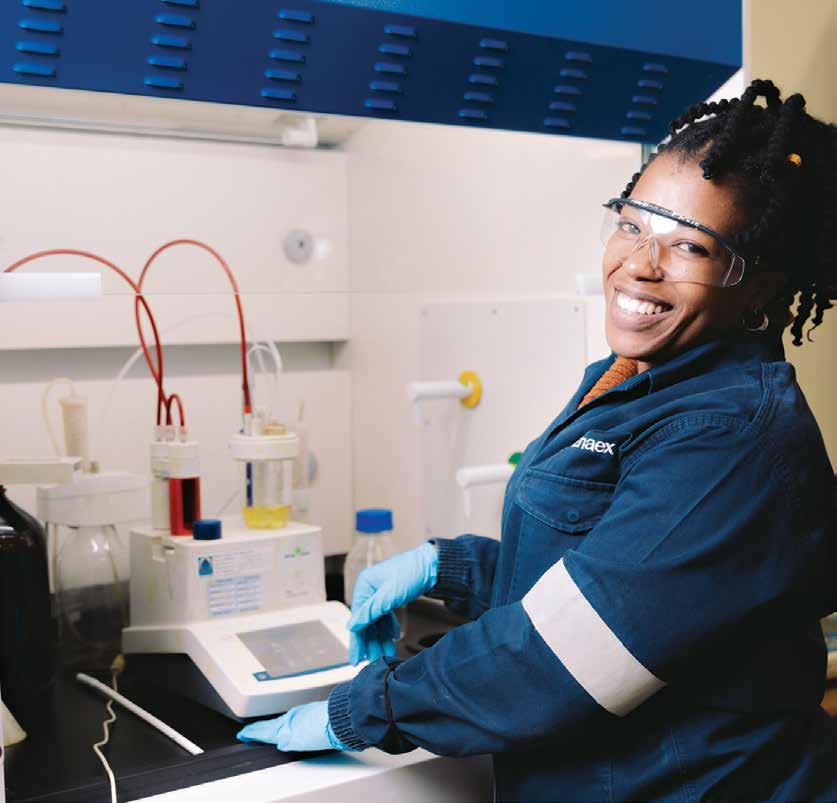
Enaex’s operations focus on “ “ protecting the environment and the people on the ground.
AFRICAN EXPANSION
Enaex Africa has grown its operations in: ■ South Africa ■ Namibia ■ Lesotho ■ Botswana
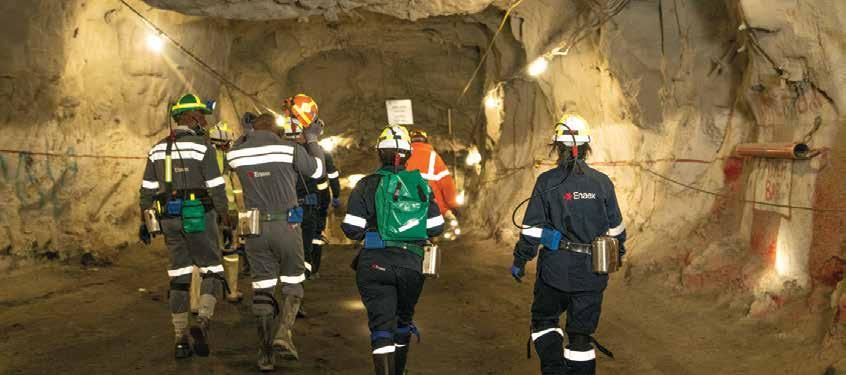

the preferred strategic partner to create a world-class explosives business in Africa.
In July 2020, Enaex Africa commenced operations as the majority shareholder and controlling partner. The current shareholding includes Enaex with 51% of the shares, Sasol South Africa with 23%, and Afris, as a BBBEE partner, with 26%.
AFRICAN EXPANSION
Enaex Africa has quickly expanded operations in South Africa, Namibia, Lesotho and Botswana, with deliberate targeted and successful growth strategies, and aims to grow further in the short term in other regions and countries on the continent. It has stayed true to its roots, having shared the culture and essence of the Enaex Group.
The local entity is changing the way the mining industry looks at its workforces, placing the people at its core. Enaex Africa is driven by the principle Baudrand lives by – to humanise mining and to empower individuals, especially women, in the industry. The mining sector has always been a tough industry. Therefore it has become increasingly important to protect customers and employees.
The group has developed its own fully teleoperated blasting solutions, which Enaex Africa is determined on implementing in South Africa and across the rest of the continent. It’s the first blasting company in the world to conduct teleoperations in the explosives industry.
This exciting and innovative breakthrough for the blasting industry took place inside an Anglo American mine in Chile.
Enaex has also executed the first ever trial on teleoperations in an underground mine. This strategic and innovative approach has been the first step in humanising mining, by ensuring that people can be removed from the first line risk in the blasting process.
The first hi-tech electronic detonator assembly plant will be launched in South Africa in late 2022, allowing local manufacturing instead of imported electronic initiation systems. This expansion is focused on implementing the safety value of “LIFE” in each process. It will reduce costs and o er a faster and more competitive route to African markets. >
Francisco Baudrand, CEO of Enaex Africa
Enaex Africa took on the challenge of implementing its safety value – “Our Priority is LIFE” – in the organisation, encouraging a safe way of life in the workplace and at home. The value is visible in all actions and procedures of the business, including its ambitions to bring teleoperated trucks and robotics to SA, and to implement further safety measures through new innovative technologies.
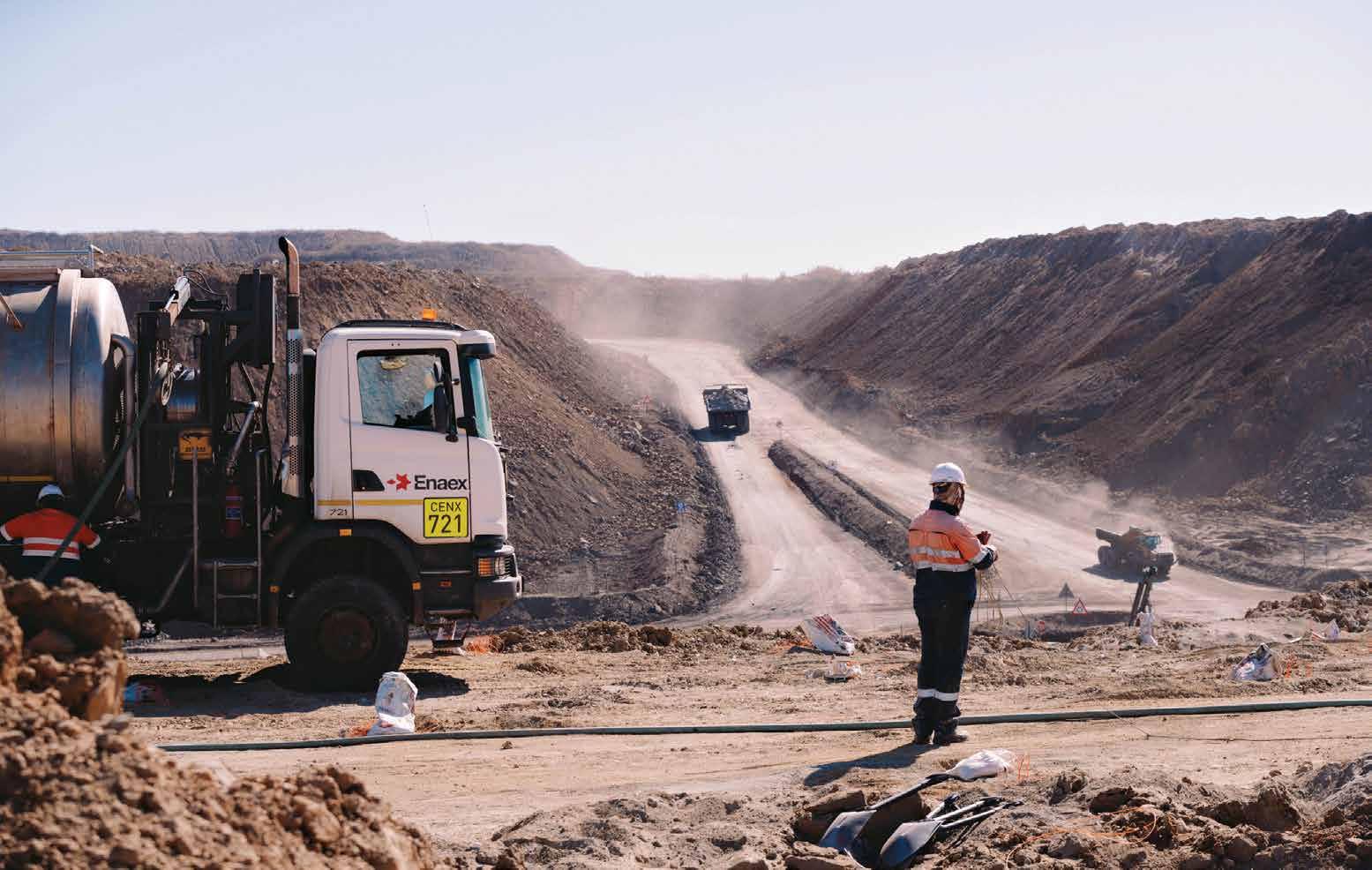
ALL ABOUT THE PEOPLE
The company sees itself as the vehicle of growth for the whole continent, one that is successfully being driven by the CEO, who has a desire to empower Enaex’s people. To do this, they are given the necessary resources required to grow and upskill themselves.
This has been the pinnacle of Enaex Africa’s journey, as Baudrand is focused on enabling young professionals to be promoted and placed in more important roles within the organisation where they can make an impact and be challenged.
With Baudrand’s passion to empower employees, special focus has been placed on young women in the mining industry. Baudrand and the Enaex Team have implemented a training programme that aims to hire newly graduated female mining engineers. This allows them to take supervisor-level roles in a short space of time, facilitating women’s representation in operations in the mining service industry.
“I have a passion for the growth and development of our people, putting special focus on women within the industry, so they can take the lead on gender equality, through time, in the mining sector,” he says.
Baudrand’s achievements are based on his own personal values: to impact and change the lives of others. As CEO, he has guided the implementation of a corporate social responsibility (CSR) programme that focuses on people, and on giving them the opportunity to empower themselves.
He is dedicated to implementing an early childhood development programme that will focus on holistic assistance through infrastructure development, teacher training and educational delivery improvement. This will upskill young people, and prepare them to contribute positively to society, offering the next generation opportunities to enhance both their futures and the lives of their families. Through such CSR initiatives, Enaex Africa has been able to support the fence line communities that surround the mining areas.
It is the company’s ultimate vision to become the leading provider of mining explosives in Africa, while at the same time being a driving force in upskilling young professionals – especially women – in mining. Its safety-first values ensure that operations are dedicated to protecting both the environment and the people on the ground – through teleoperations, upskilling and empowerment. n

“It is vital to upskill young professionals – especially women – in this industry. “

THE IMPORTANCE OF A FULL-SERVICE TYRE OFFERING
Tyres are vital to mine operations, and obtaining the toughest, most appropriate, most sustainable tyres plays a major role in both cost and ESG considerations.
There are many pressing mining challenges that organisations face across the various stages of tyre life. First it’s important to have access to a selection of brands, as well as understand the compound specification of the range of tyres available on the market, in order to start with a tyre that has a reasonably good probability of adapting to the prevailing conditions.
Furthermore, notes John Martin, VP: Southern Africa at Kal Tire’s Mining Tire Group, the perennial challenge of finding and maintaining access to best cost-per-hour performing tyres for the mining application remains a never-ending pursuit.
“Testing and proving new and alternative products or new technology should still be a standard procedure on any mine. It serves as a means to identify opportunities to positively contribute on an ongoing basis, in a manner that’s aligned with the mine’s tyre management strategy,” he says.
“There are also ongoing operational decisions as to what tyres to repair, and when to repair them, as well as considering the possibility of retreading off-the-road (OTR) tyres, and the value that these lifeextending decisions and actions can bring.”
Throughout the lifetime of the tyre, adds Martin, mine owners will be mindful of their respective commitments to environmental, social and governance (ESG) factors. This will drive decision making as to how best to deal with their tyres throughout their operational life cycle, as well as the tough decisions around how to deal with end-of-life tyres, and how these tyres are disposed of in an ethical manner.
“From a Kal Tire perspective, we have access to the performance data of many thousands of tyres and can therefore best advise in the initial stages of mine planning and development as to what
A full service tyre offering positively “ impacts cash flow and dilutes operational risk.
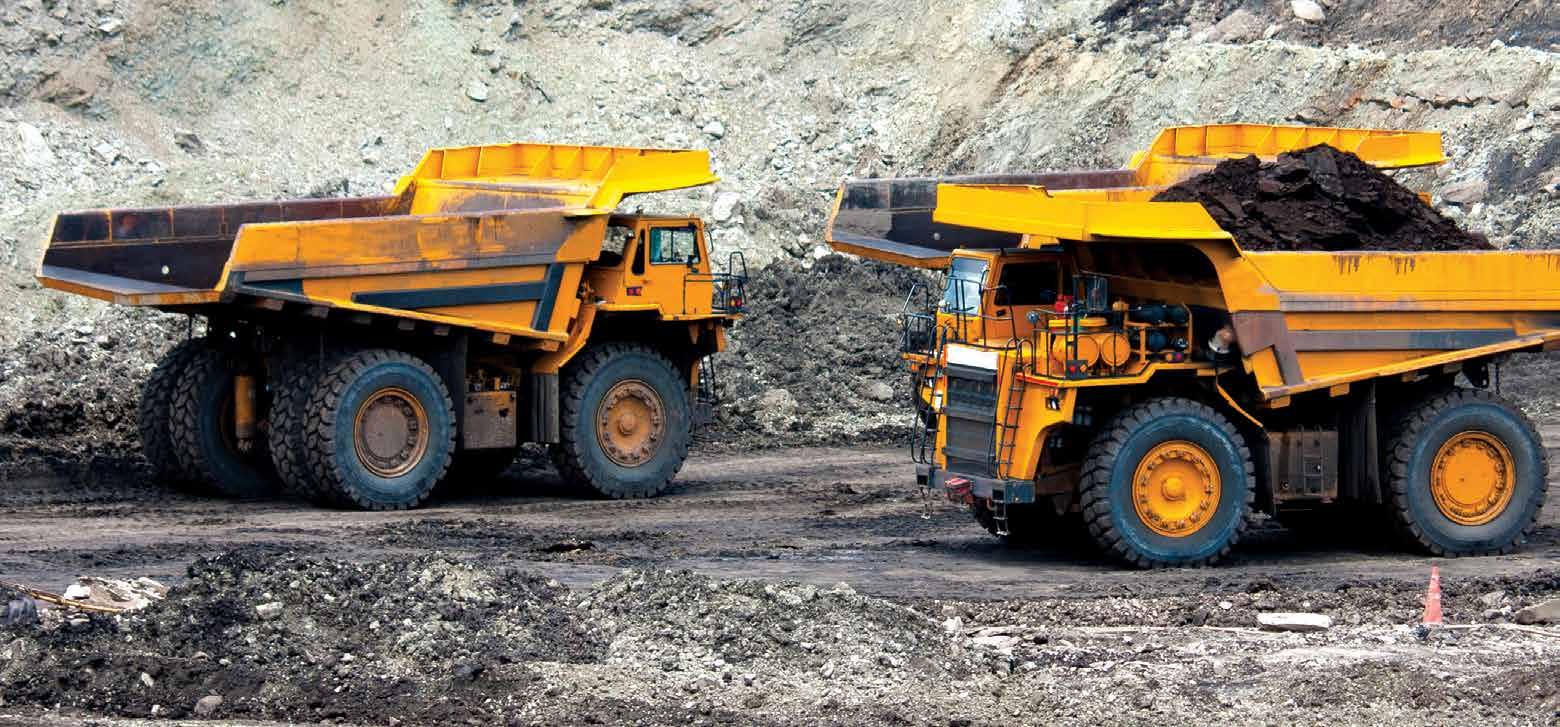
Innovation remains a core function of the group. “ “
tyre has the best chance of succeeding in the environment. We also maintain close relationships with all significant tyre manufacturers, as a means to access new products and technology that can potentially benefit such mining operations.”
Explaining what a full-service o ering means, he says it’s the ability to provide a range of all-encompassing services, starting at the point where a tyre leaves the manufacturing unit, through to the ethical recycling of the carcass at the very end of the useful life of the tyre.
The service is initialised with optimised planning and forecasting of tyre-related products, as a means to positively impact on customers’ cash flow, as well as diluting operational risk, specifically in remote operations in Africa.
“A comprehensive tyre-management strategy needs to be agreed between a mine and its service provider, with key performance indicators, which could include maximising mine operational performance and/or minimising tyre costs. Management systems should then be comprehensive in their capability to capture every aspect of the tyre’s life, including repairs, retreading and all related cost and performance data,” Martin says.
SUSTAINABILITY AND TRAINING
Once the tyre has fully contributed to the defined strategy, and has exhausted all opportunities for repair or retreading, it can be retired for recycling. As part of its services, where a Kal Tire recycling plant has been established, tyres can be recycled in an ethical manner, further contributing to the circular economy and supplementing the customer’s ESG targets.
“It’s important to note that risk is present in many forms for any mining operation. However, one way that Kal Tire can contribute to minimising its customers’ risk profiles is through providing highly competent OTR tyre-management specialists,” he says, adding that Africa has a shortage of skills for the growing mining footprint on the continent.
“To this end, Kal Tire’s Learning Management System is a standardised training system that is fully aligned and endorsed by the Tire Industry Association (TIA), which is used to develop team members to a consistent global standard, and can be applied in any mining operation with confidence.”
A core component of Kal Tire’s service strategy is to ensure that the customer extracts the maximum potential value from all tyres used on site. This philosophy on its own is a means to reduce the carbon footprint of the client, as fewer tyres are used during the course of the mine life. This combined with repairs and retreading can significantly contribute to reducing the carbon footprint.
“For Kal Tire, safety and sustainability are interdependent concepts that are applied throughout the company, as part of the service o ering to its customer base. One aspect of sustainability is evident in its local employment policies, where Kal Tire employs – as much as is practically possible – from local communities in and around customers’ operations,” he says.
“These team members are trained in a managed and measured fashion, of which health and safety training is inextricably intertwined in all the training modules, creating a sustainable skills development platform from which both competence and safe working practices can be honed. Customers can therefore benefit from using our team members, who in turn contribute to customers’ ESG commitments.”
There is only one globally recognised authority for safe work practices and training, continues Martin. This is the United States-based TIA, of which Kal Tire has been a member of good standing for almost 20 years. This has allowed Kal Tire to bring world-class OTR management standards, including safe work practices and globally consistent training standards, to all local markets in Africa and around the globe.
“Innovation remains a core function within Kal Tire’s Mining Tire Group, and all our innovations are recognised as contributing positively to both safety and productivity, while improving the cost e iciency of customers’ operations.” ■
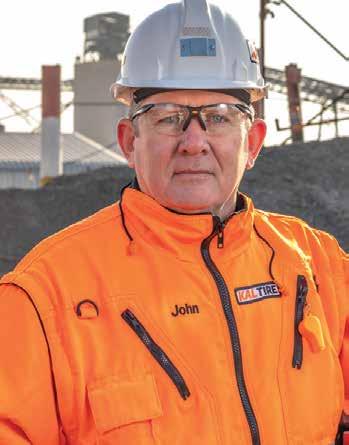
KEY INNOVATIONS BRINGING ADDED CUSTOMER VALUE
■ Gravity Assist System (GAS) – designed to support heavy tools like torque guns, reducing muscle strain and fatigue. ■ Ultra Repair™ technology – enables repairs to OTR tyre injuries that would otherwise be scrapped. ■ Tire Operations Management
System (TOMS) – innovative technology providing on-site real- time decision making capabilities.
John Martin.