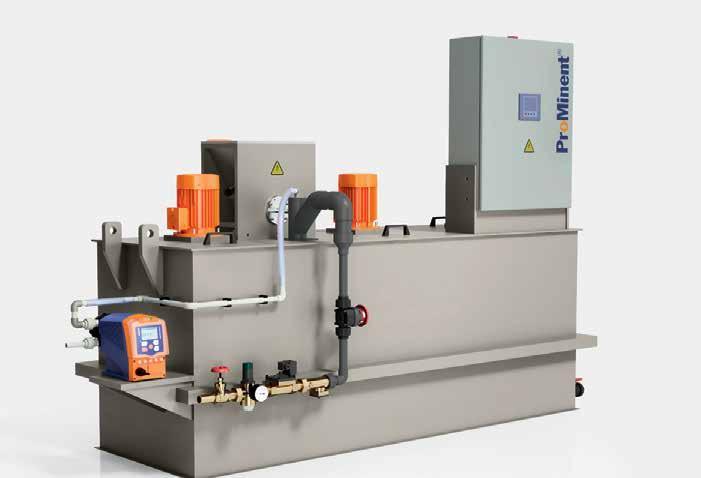
5 minute read
NEW PERISTALTIC PUMPS LAUNCHED
Given that ProMinent Fluid Controls’ goal is to increase product e iciency and ensure safety for your customers, how has this translated in terms of product development?
All of the ProMinent products are developed in-house at our factory in Germany. This ensures a high-quality product that is continuously developed. With the current focus on Industry 4.0 and remote monitoring of processes, the DFYa and DFXa o er not only control options that are currently not found on any other peristaltic pump in the market, but also the option to monitor all pumps via a cloud platform.
How do the DFYa and DFXa peristaltic pump ranges meet the drive for increased e iciency and safety?
The internal electronics in the pump o er a wide range of fault detection, and via the extensive range of communication options, faults and possible situations can be detected before they become a safety hazard.
Are the latest products available to the African market?
The products were launched in 2020 and are available to the African market, including South Africa. Already, one of the pumps
The ProMinent group of companies manufactures metering liquids and solutions for water treatment.
– MYBURG
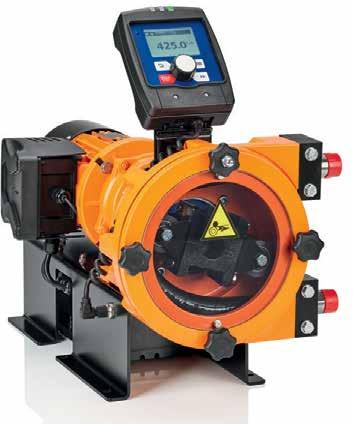
DFYa smart peristaltic pump.
PROMINENT FLUID CONTROLS
ProMinent Fluid Controls products are available in more than 100 countries around the world. Including its subsidiaries, the company employs around 2 600 people, focusing on sales, production and service.

Zone 1&2 solenoid dosing pump.
has been shipped to the Democratic Republic of the Congo, with six more awaiting dispatch to a local mine, while another is earmarked for a sweets manufacturer in Johannesburg. Further to this, we have demo pumps available for testing at our warehouse in Johannesburg.

What are other key defining features of the new products, and how well suited are they to the African mining market?
The ProMinent peristaltic pumps have been on the market for years and have an extremely good reputation for quality and reliability. Control for the pumps is new and o ers customers better functionality than just the standard on-o pumps that are on the market.
Other key features on the DFYa and DFXa are: Adjustment of the metering rate directly in l/h or gph. Simple hose change. Metering abrasive fluids, possibly containing particles. No problems with very gaseous media or air locks. Suitable for viscosities of up to 50 000 mPas. Sole contact with media in the hose. ■
Zone 1&2 solenoid dosing pump
DFYa smart peristaltic pump
DFXa smart peristaltic pump liquid end
ProMinent Fluid Control SA 3 Hurricane Avenue, Ext. 4, Germiston Tel no: 011 323 5000 E-mail: ZA-Sales@prominent.com www.prominent.co.za
Polymer makeup system Ultromat
CDE’S AGGMAX

THE PRIZE FOR PARTNERSHIP WITH CONSULMET
In 2018, CDE and Johannesburg-based minerals processing solutions provider Consulmet set up an agreement to collaborate on projects in the subSaharan Africa market.
Wet materials processing experts CDE and Consulmet committed to identifying ways to adapt wet minerals processing equipment into bespoke solutions that could help the broader mining industry unlock and maximise resources that have previously been disregarded.
Consulmet is a specialised engineering and project house serving the minerals and metals processing industries through the design, supply and construction of modular production-ready processing and beneficiation plants.
As part of this unique partnership,
CDE’s innovative technology is now being applied to various projects in the region. The partnership led to one of
CDE’s earliest successes in the region’s mining industry through the application of its technologies for both alluvial and kimberlite diamond operations.
The jewel in the crown of the partnership is CDE’s AggMax modular logwasher set-up for scrubbing and sizing.
Consisting of a RotoMax logwasher and dewatering screen, the AggMax delivers supreme scrubbing and unrivalled wear due to its alloy paddle design and helical arrangement.
Over the past two years, Consulmet has invested in four CDE AggMax plants and has also commissioned CDE’s R-Series primary scalping screens and EvoWashTM solutions as part of its various projects in the region.
One of the first projects commissioned was for the BK11 diamond mine in Botswana, following Consulmet securing the contract for upgrades and modifications to the existing on-site plant in 2015. Previously mothballed, the BK11 kimberlite mine in northern Botswana had been ine icient in scrubbing the highly weathered kimberlites, resulting in excessive clay being fed to the secondary cone crushing circuit, causing severe blockages.
The Consulmet/CDE team introduced a secondary cleaning process using CDE’s AggMax 83SR a er the primary rotary barrel scrubbing. The two fractions, a 1-35mm and 35-90mm material, were cleaned extremely well removing previously discarded, heavily clay-bound material ensuring optimised processing downstream.
An additional major benefit was the e icient removal of organics ahead of the XRT diamond recovery module. XRTs are material sorting systems used to identify and separate/classify material based on its atomic number. It allows for high material recovery and accurate classification.
Most recently the partnership has delivered solutions for two key diamond projects. One is a 500tph greenfield diamond plant in Zimbabwe, which benefits from two RotoMax 250s, discharging onto a single classification screen. This secondary scrubbing application has been integrated with the primary scrubbing, XRT sorting and crushing on site.
The second was a smaller processing plant, for a diamond mine in South Africa, that features a primary scrubbing and screening section, feeding into CDE’s RotoMax 80. This discharges onto a classification screen, separating into three fractions – 4-8mm, 8-16mm and 16-35mm. This module ensures adequate feed preparation and removal of organics, for processing through an XRT sorting system.
CDE’s AggMax technology is engineered to operate in the toughest of conditions to maximise product yield from the most abrasive of feedstocks. Combining feeding, scrubbing, screening and sizing on one chassis, the AggMax is suitable for various material streams and across di erent industries.
