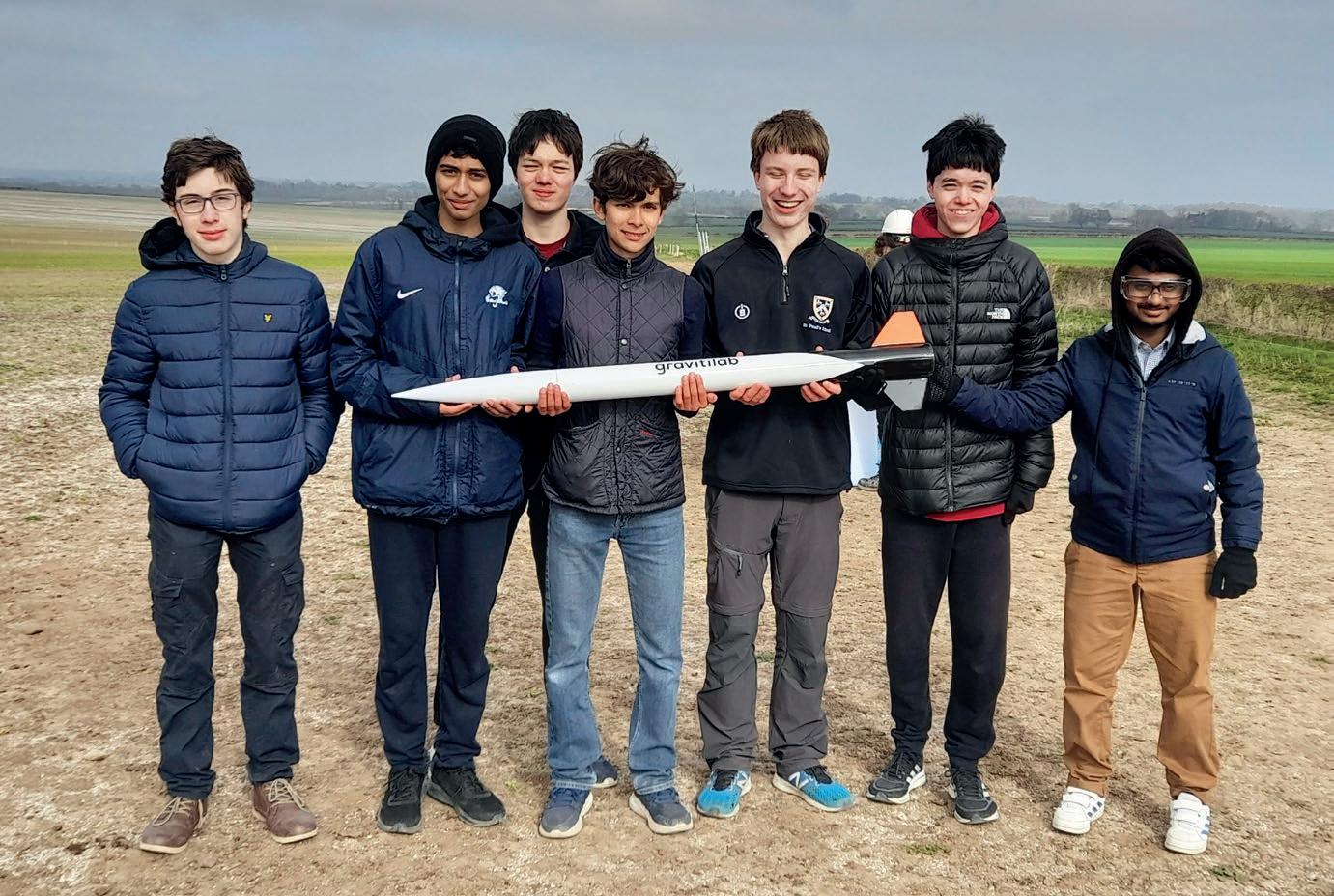
5 minute read
CanSat Competition
Have you ever found yourself not having enough space? The school’s CanSat team, Team Nebula, were not ones to let that stop them from building a satellite the size of a mere drinks can, to be launched hundreds of metres into the sky whilst collecting data such as air pressure and temperature.
The CanSat competition, run by the European Space Agency, requires that the satellite must also perform a “secondary mission” of the team’s choice. One example is the “controlled descent” – as the Can falls from the sky, mechanisms such as parachutes or motors can be deployed to slow the fall and even steer the satellite on a trajectory. From the beginning we brainstormed numerous extravagant ideas, including a drone that could double up as a rover once landed. We finally settled on the equally ambitious parafoil, a type of parachute with mechanical arms able to change the can’s direction of travel. We also decided that we wanted our satellite to drop a small “payload” as it fell, simulating the American military’s Joint Precision Airdrop System. Being able to pull off so many tasks successfully was not going to be easy – but we were up for a challenge.
We immediately set to work: Rahul Marchand painstakingly hand-crafted multiple possible parafoils for the Can to use; Charles Calzia, Vikram Bhamre and Harishan Ganeshan got to work on designing the electronic systems and writing code for them; and Peter Baker, Henry Squire and Ryan Rundstrom began designing and manufacturing the mechanisms and the Can-shaped housing. The overall design went through two iterations – the first design focused on collecting data for the primary mission, whilst the second added support for a GPS sensor and servos, the mechanical arms upon which the secondary mission heavily depended.
Our electronics design was greatly helped by a sponsorship by JLCPCB (https://ww1.jclpcb.com/), who manufactured our printed circuit boards (PCBs) at a greatly discounted price. We were also provided a 3D printing service discount by 3DPRINTUK, yet for convenience we opted for the school 3D printers and laser cutter instead to prototype our mechanical parts. Testing of the Can’s systems was performed by throwing it off the top of the Art building and praying that it did not break.
On the day of the launch, the team woke up incredibly early, and left school by coach before sunrise. We took advantage of the 2 hour trip to the Midlands Rocketry Club to make last minute adjustments and modifications to our systems. We used a pit stop on the journey to solder at a cafe, where we managed to fix some problematic wiring, whilst drinking coffee and eating sandwiches. To our relief, this got the GPS module working.
As soon as we arrived at the launch site, we were greeted by a thick, sinister white fog. We got to our work benches to set up our satellite, but the mist would persist for the rest of the morning.

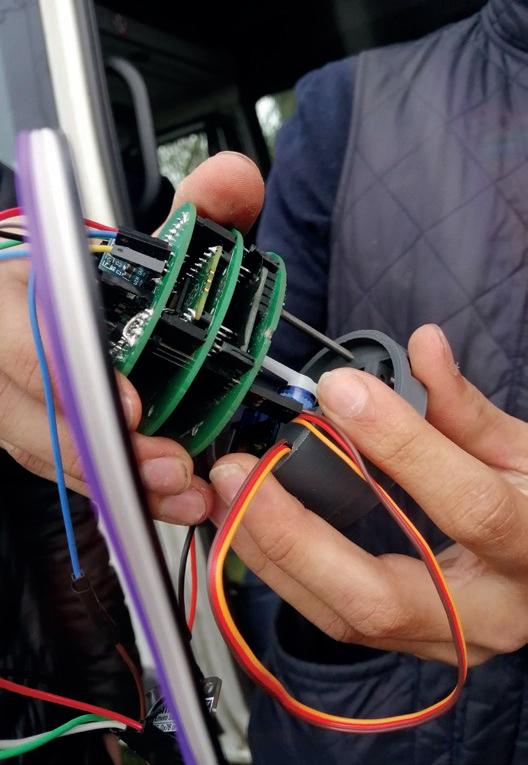
Meanwhile a new problem arose – we couldn’t get new code to upload to the microcontroller, the brains of the PCB. Right before our lunch break, the event organisers had announced that if the fog chose to stay for the afternoon, they would have to postpone the entire launch to a later date.
Our lunch trip was to McDonalds where, amidst the guzzling of nuggets and fries, our programming team wrote some more code, optimistic that we would get to see our satellite launch. As our luck would have it, the fog lifted later in the afternoon. This conveniently gave us enough time to fix some of the critical issues we were having with our satellite. Despite this, there still remained problems with uploading code to our electronic systems, which meant that the GPS and the servomotors required for the secondary mission, to steer the can and drop a payload, did not function in the end.
Nevertheless, hopeful that we could at least collect some environmental data, we handed over our Can to be inserted into a launch rocket. Moments after watching the rocket blast off into the air, we could see our satellite in the sky, exceeding expectations by hovering in the air for a long time before landing. Once it landed, we all ran towards our satellite and nervously extracted its contents. Thankfully, it survived the impact from the 250 metre fall and all the internal systems remained in one piece. What’s more, the data from the flight had been successfully recorded to the satellite’s SD card, thereby fulfilling our primary mission. We saw this as an overall victory, and left the site feeling satisfied that our months of planning and progress had been a success, although vowing never to use lead-free solder again.
Unfortunately, we didn’t make it through to the next round of the competition; regardless, we are proud of what we have achieved as a team, and hope that one day we may be able to get it to work fully as intended.
Over several months, we learned invaluable skills that furthered our engineering capabilities – from designing complex PCBs and programming elaborate scripts, to manning sewing machines to craft parachutes, and thinking unconventionally to solve our problems. We learnt how to work together as a team, and how good communication between subteams helped get things done efficiently and effectively.
Students who are interested in engineering, science and technology, and would like to work with a team of talented like-minded people to be able to create something extraordinary and beyond the scope of a typical home or school project, should definitely consider joining CanSat 2023!
Team Nebula would like to thank Dr Patterson in particular for his supervision of the project and all of the time he gave us over the course of the year. Many thanks also to Dr Harrison for driving us to the regional launch, leaving at 5:30am to make it in time!
The team included: Henry Squire, Vikram Bhamre, Peter Baker, Rahul Marchand, Charles Calzia, Ryan Rundstrom, and Harishan Ganeshan. ❚