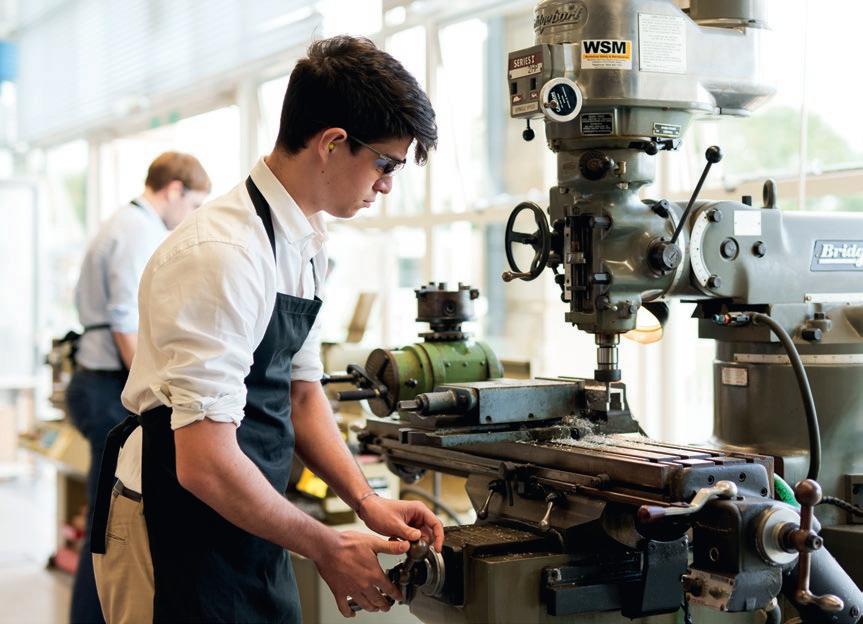
11 minute read
Engineering
KNRD
For almost all of us, it seems that Engineering, or a version of it, has been taught at St Paul’s for what seems like forever. So it was surprising for me to discover that the subject had only existed at the school since 1983, a mere 38 years in the school’s 513-yearold existence.
Milling Machine
Why this sudden interest in the Engineering department’s history, I hear you ask? Well, this year heralded the end of an era for the department. We were finally moved out of Old Science. But before we get to this point, let me tell you how the department came to be.
Engineering, or CDT as it was known back then, first started in the Centenary Building in the then Colet Court. It took over the ground floor of the building in the space that had previously held the minibus garage. It proved to be such a hit that the tiny department soon recruited Alan Goodridge in 1985 to help the department grow, and it started being taught to St Paul’s pupils as a non-examined subject. A new workshop was built on the ground floor of Old Science to accommodate this growth. Alan also worked with a small group of enthusiastic Coletines to build a hovercraft, which was still in the department when I joined in 2010.
Kevin Campbell joined in 1988, and the subject gained a new name, Design & Technology. John Siviter from the Physics Department started teaching Electronics and became the overall head of the department. The need for new facilities was obvious, so work soon began on the Bernard Sunley Technology Centre, which opened in 1991 and is still our main workshop.
Once Design & Technology moved into the new workshop in 1991, the old workshop in Old Science was refurbished into a state-of-the-art Electronics lab. Dr Peter Bullett took over from John, and Okan Avni also joined to teach Physics and Electronics. David Emery joined as the new Electronics technician and soon-to-be teacher (and celebrated his 30 years of working at SPS this year).
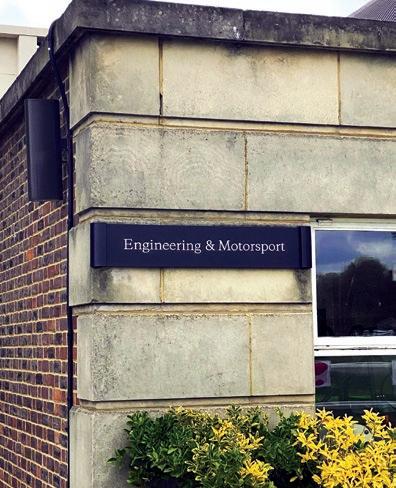
Plunge Routing
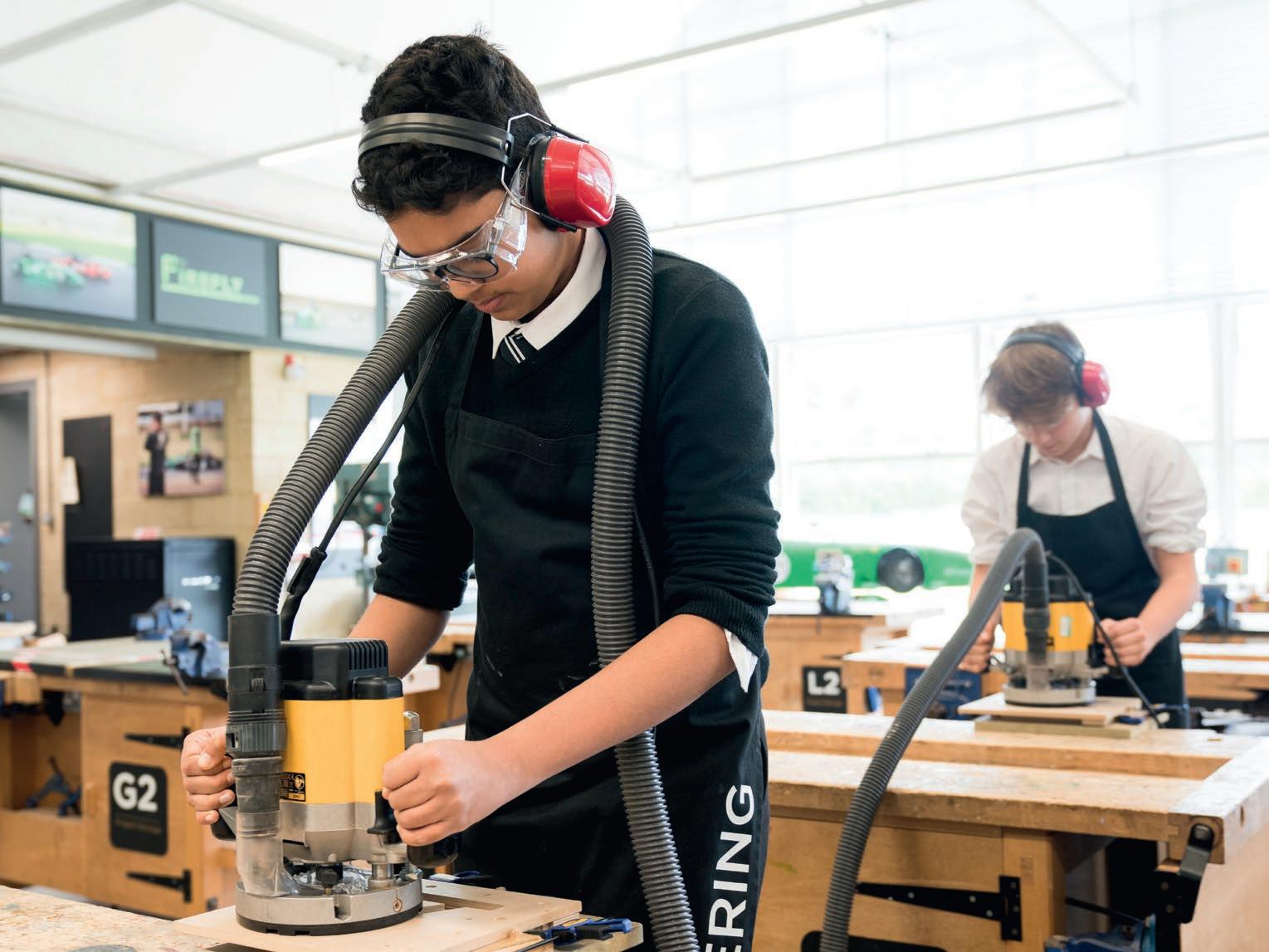
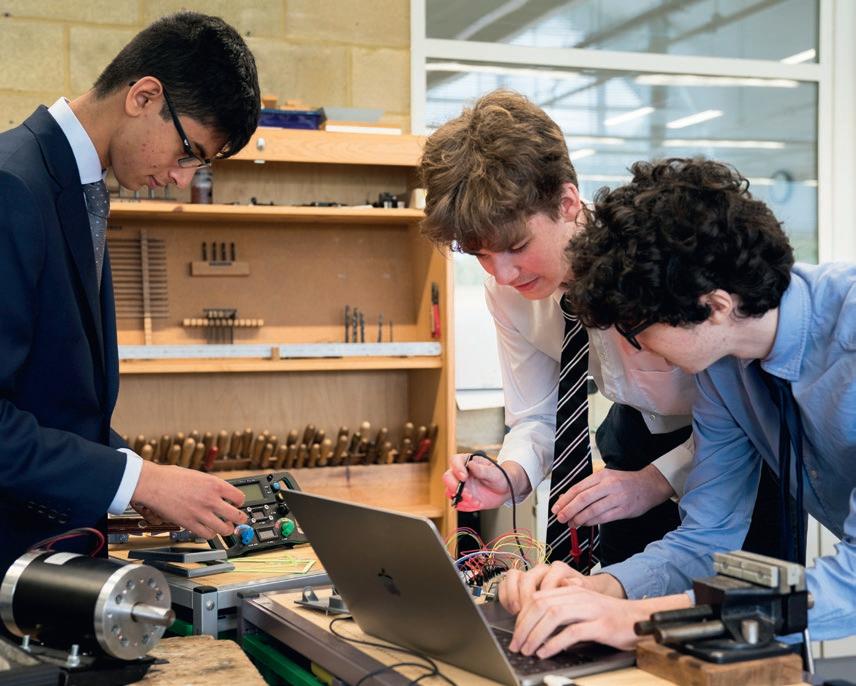
During the ’90s, the use of computers and coding became ever more important. So to respond to this, the department expanded to include Systems & Control. In 2000 they took over another room on the ground floor of Old Science to create a modern lab full of LEGO Dacta and Apple Macs. Now the department as we know it today was complete. Systems & Control and Electronics lived on the ground floor of Old Science and Resistant Materials (now Product Design) lived in the Technology Centre. But we were still called the Technology Department. It wasn’t until the arrival of Dr Alan Gardam and some careful subject renaming that our department became known as Engineering in 2012.
The department has had many other fantastic teachers and technicians over the years, including Derek Hardy, Shirley Rollitt, Gary Nava, Graham Collard, Chris Fry, Barry Brook, Richard Barker, ➦
Oliver Rokison, Jacques Du Plessis, Ciaran Malik, Rob Humphrey, Sally Hamma, Matthew Holder, Jack Keech and Tomi Herceg. Not to mention the current team David Emery, Brian Clark, Steve Patterson, Ruth Afonso, Edd Bailey, Dom Boydell, Leigh Eadie, Arthur Jenkins, Simon Roberts, and of course myself.
So back to the present day, old Science is once again being repurposed. But this time, the Engineering department wasn’t able to stay put. Our state-ofthe-art classrooms aren’t quite as state-of-the-art any more. So it was time to sit down with architects to redesign existing spaces in the Milton Building. Electronics and Systems & Control would finally be in the same building as Product Design. As I write this, I can hear the noise of builders ripping out walls, tearing up carpets and cutting floor boxes into concrete. But come September, we look forward to welcoming everyone back to our new, hopefully, state-of-the-art facilities for the next era of Engineering at St Paul’s.
In writing this article, I wanted to ensure that I adequately documented the history of our department somewhere. Often it is too easy to look to the future without properly acknowledging the past and the hard work of our predecessors to get us where we are today. So many wonderful photographs document the school’s illustrious history, but sadly, almost none of the Engineering department. I would like to ask the Pauline community if they have any photos from the past 38 years that they would like to share so that I can properly enter them into the school’s archive.
As we enter the 39th year of teaching Engineering at St Paul’s, at least now I know I have a year to prepare for the 40th anniversary celebration… ❚
Electronics Lab (photo by David Emery)
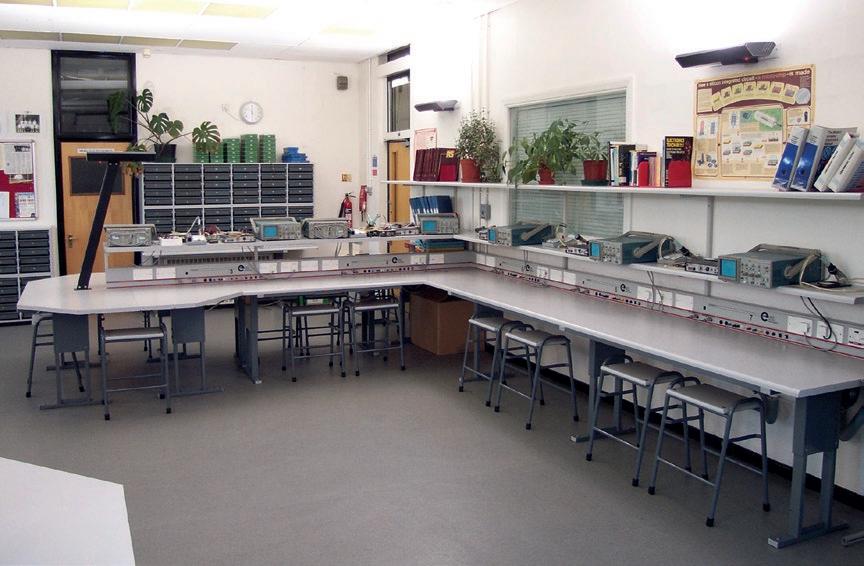
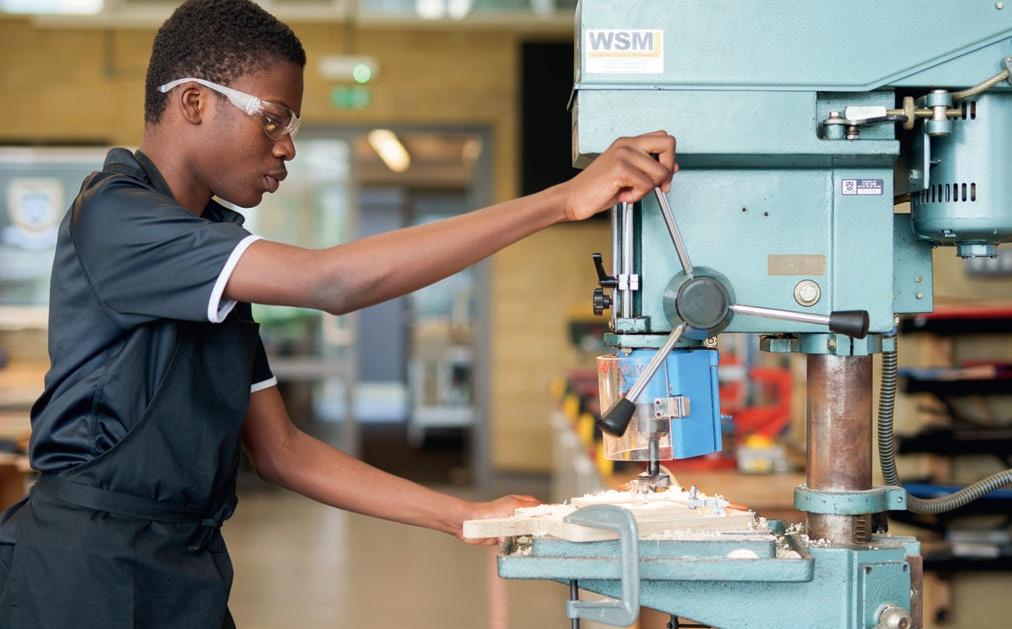
Pillar Drill
FF03: A First Year of Racing
Ishan Madhok, Vyom Chamaria and Daniel Cheung
Team Firefly is the school racing team that builds battery-powered racing cars and participates in F24 (and F24+) races across the country. There are many of such events, but in this article, we will mainly focus on Goodwood and Lotus Hethel – the two we have participated in so far. As Fourth Formers, we took control of FF03 which is the kit car in the team – FF01+FF02 being scratch builds.
Our first project entailed putting together a spare Greenpower kit car chassis, which took a few weeks. During this time, we learnt a lot about the structure of the car, and familiarised ourselves with the practical element of engineering, the physics behind the car, and had some vital team-building time.
Our next main project was focused on the steering of the car. Firstly, we removed the side panels from our existing car and added a steering damper. This would remove any undesired oscillation in the steering system and in general make the driving more smooth – in turn reducing energy consumption. Finally, we looked at what setup would alter the steering sensitivity to the optimum amount, by altering how the track rod was fastened to the steering plate on the steering column, and at the other end, changing where the track rods connected to the steering arms (part of uprights) until a suitable value was found.
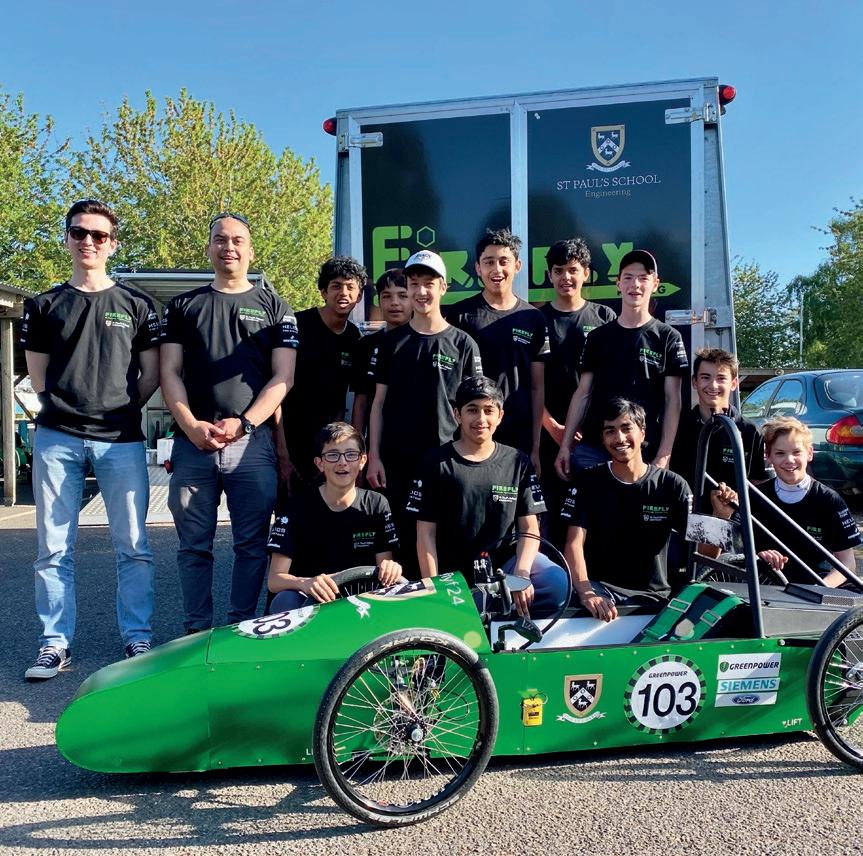
After this, our first race at Goodwood shortly ensued, so in preparation, we installed a new horn in our car, removed our old sponsors’ stickers from the exterior, and reattached the side panels. Also, it was vital that we were able to transport our batteries (the fuel for our car) safely, as well as keeping them at the optimum temperature so they performed well on race day. To do this, a housing for the batteries was first digitally modelled to fit in the space at the back of the trailer, and then created with wood and foam to provide insulation and padding in time for the upcoming race. For context, the trailer is where we store the cars and the batteries while travelling to the race location.
Furthermore, in preparation for the race, we did work on the simulator to allow us to learn the track and did pit stop practice, which enabled us to save time during the race. We also calibrated the corner weights on our car; by making sure that the corner weights are equal, the weight of our car is split evenly among the four wheels which provides stability and in turn conserves energy.
On the 8 May, St Paul’s school F24 and F24+ teams had their first race of the season and it was at one of the biggest events of the year, Goodwood.
It was a beautiful day, the sky was clear and the sun lit up the racetrack – ideal racing conditions. We had to wake up early for an 8am start at Goodwood. We prepped the cars by setting up the batteries and making sure everything was working and then we had a race ➦
briefing. We had practice from 9:30am until 11:00am. During this time, we practised pit stops and drove around the circuit, getting used to the car and familiarising ourselves with the layout of the track. At 11:30am we had our first race in which we had to drive as far as we could in 1 hour 30 minutes. We also had two mandatory pit stops per race in which we changed the driver; this includes strapping the next driver’s seat belt in, plugging in the radio and this pit stop would take 25-30 seconds (not including wheeling the car down the pit lane) on a good stop.
After the race, we had a break for some time while there was the F24 race. Subsequently, we had our second race at 3:30pm, and placed 34th out of 84, which is very impressive considering we started at the back of the grid, and our car was a kit car as opposed to a scratch build which is typically faster.
Since our car had performed well at Goodwood, the interlude between races was primarily focused on making small changes based on what we thought we could improve on. In particular, we noticed that the wheels created a lot of drag due to their positioning, so we installed fresh black wheel covers to them. This created a sleek and elegant look as well as better aerodynamics. The preparation for Lotus was mostly the same as for Goodwood, and entailed simulator practice, pit stop practice and car preparation.
Our race at Lotus Hethel was on the 19 June. The general structure of the day was very similar to Goodwood, and at the end, we were delighted with our result of 12th out of 33 out of all cars and 6th out of 12 kit cars. We also won the Siemens sustainability award due to an ongoing project about sustainably powering our trailer with solar panels.
So far, we are happy about our results so far and hope to do even better in our next races (Castle Combe and Dunsfold Park) in order to qualify for the finals. Currently we are changing our tyres to lighter and more efficient ones. We are also planning to create a new rear floor which will massively help our aerodynamics. These upgrades will boost our performance and should allow us to qualify for the finals. All the work that we have done on the car would not have been possible without the assistance and expertise of the teachers, in particular Mr Jenkins, Mr Clark, and Miss Douglass, and we sincerely thank them for all their hard work. ❚
FF03 being pushed down the pit lane at Goodwood
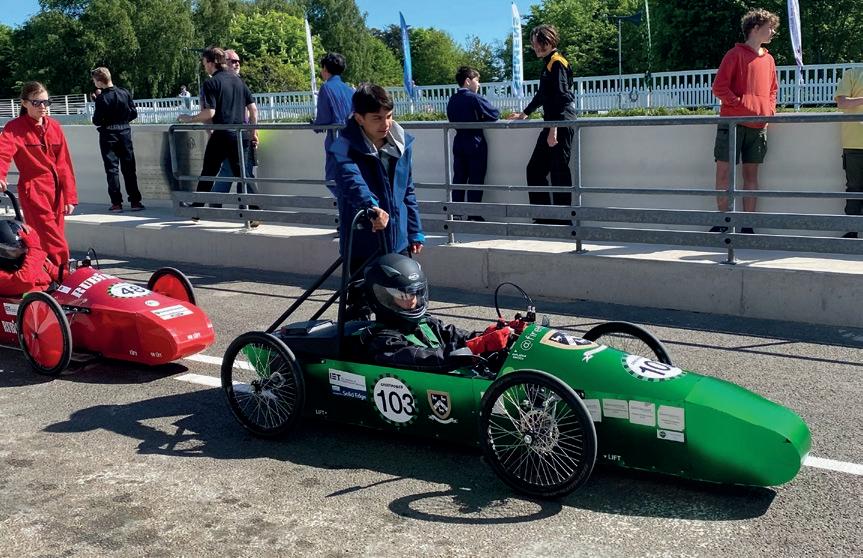
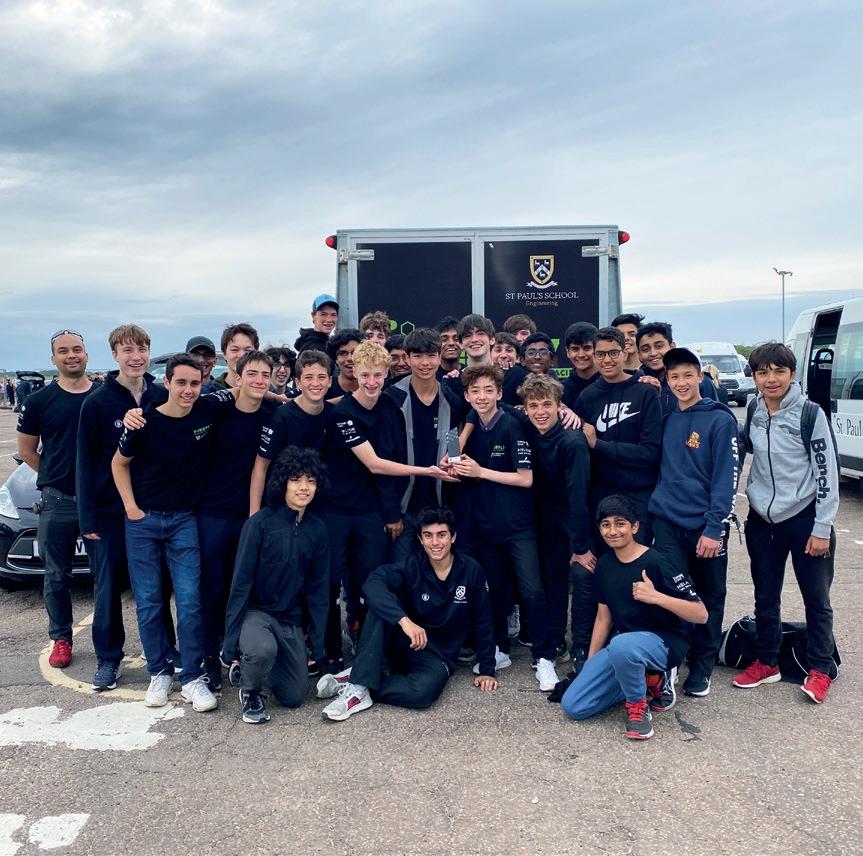
The Firefly Trailer
James Williams
The Firefly trailer. You all have most likely seen it as you walk into school each morning or while playing on Bigside, but you don’t know what actually goes on inside it. Behind the scenes, a few Firefly members and I have been planning, designing, manufacturing, and installing a great deal of exciting features that will come into play on our racedays, which I will detail in this article.
At the start of the year, all the trailer was used for was to transport our three cars to races, and so it was almost completely empty when we got our hands on it. Our primary goal was to not only make transporting cars, batteries, and other equipment much easier, but we also wanted to turn the trailer into our own data-centre on racedays.
Looking for inspiration, we turned –as we often do in Firefly – to Formula 1. If you’ve ever watched an F1 race, you will have seen how teams control their races from the pit wall (see below). We wanted to try and replicate this on a smaller scale (inside the trailer) which would all have to fold away at the end of a raceday in order to fit the cars back in for transport.
Our technical director, Arthur, who helps us out in just about everything Fireflyrelated, drew up some plans for how we would populate the trailer interior.
The main features detailed here are: a folding table for data-engineers to be based during the race, with communications to the car available from the trailer; a compartment for batteries to be kept on the way to the race, which must be insulated as they must be kept as warm as possible; and full electrical power to the trailer, including interior and exterior lights, charging ports for devices, battery warming boxes, and anything else that we might need on a raceday. That was in September. It is now July, and – even after an enormous amount of time and effort – we still haven’t finished everything that we had actually hoped to be finished in time for our first race of the season in May. However, I think I can speak on behalf of the ‘trailerteam’ when I say that we could not be happier with what we have managed to achieve this year. On top of having to work on the cars, we have managed to: fully install the battery compartments, which have made transporting batteries a great deal easier; fit two folding tables on each side of the trailer, which provide enough space during racedays but also fold away to accommodate the cars; and have almost finished the unbelievably complex project of providing electrical power, complete with two control panels, a lot of cable, and what appears to be half of the department’s components.
This has been an immense project, involving at least ten members of the team, which I can’t wait to try out at our next race at the start of September! ❚
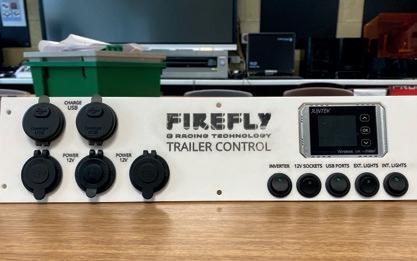
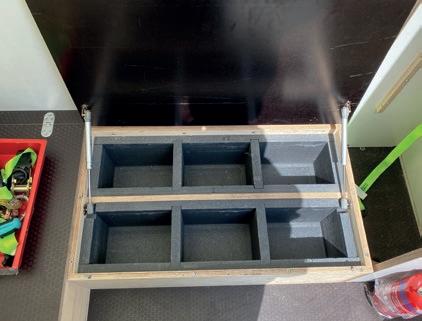
Top: Custom trailer control Bottom: Battery warming boxes
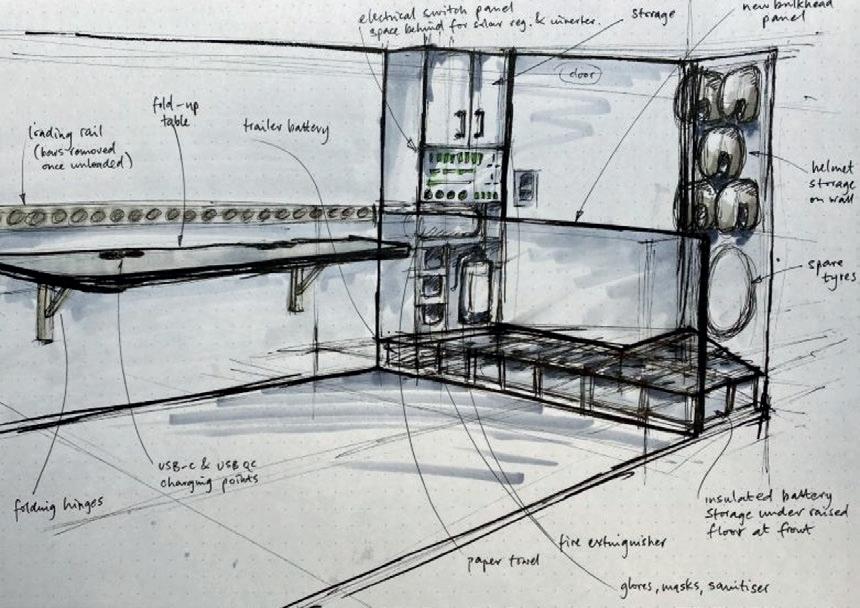