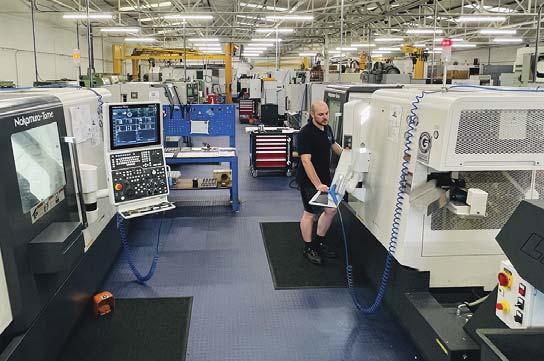
13 minute read
TURNED PARTS
Four multi-tasking turning centres are helping Quest Precision win offshore industry machining work from Chinese competitors.
Serving customers in the oil & gas, electronics, automotive and aerospace industries, ISO9001:2015 certified Quest Precision machines everything from simple parts to the most complex of components. It is this requirement for one-hit machining of complex parts from challenging materials that led to the installation of its first Nakamura-Tome multi-tasking turning centre in December 2019, a twin-spindle twin turret WT150II. The impact of the Nakamura-Tome WT150II resulted in a second machine being installed four months later and this has now been followed by two more machines that were delivered at the end of July.
Advertisement
Before Quest installed its first Nakamura-Tome WT150II, it was machining autonomous valves for the oil and gas industry in five operations on four machine tools. The production of the complex 2inch diameter Inconel 718 valves that control the flow of oil from wells was time-consuming and not cost-effective enough to compete with an existing Chinese supplier. To win more of the business from the overseas supplier, Quest needed to increase productivity and reduce costs – the answer was the Nakamura-Tome WT150II.
Discussing the situation, Quest Precision’s Managing Director, Mr Gordon Deuchars says: “There are 25-30 different valves in the family of parts and for us to win more business, we had to increase throughput and reduce costs to be cost-competitive with China. The first two machines made a huge impact and brought us significantly more business. To support the subsequent growth and do more R&D work, we bought the next two machines.”
Depending upon the valve variant, the majority of valves were processed in 2-4 hours on four machine tools with an additional 25% set-up time across the numerous machines. Running everything from prototypes right through to production runs of 1000-off, producing such volumes on the existing machine tools was unfeasible. The first twin-turret twin-spindle Nakamura-Tome WT150II immediately alleviated the situation, the second machine solved it and machines 3 and 4 are helping the company cope with its influx of new orders.
One hit machining on the WT150II initially reduced cycle times by 50% to 1.5 hours whilst freeing capacity and labour requirements throughout the shop floor. As Gordon recalls: “The WT150II made such a difference to our production and set-ups that we ordered a second machine within weeks. Instead of using multiple machines and up to five staff on the valves, we have one operator running the two Nakamura’s. With one staff member running the machines on days and another on nights, the first two WT150II machines
Offshore work reshored
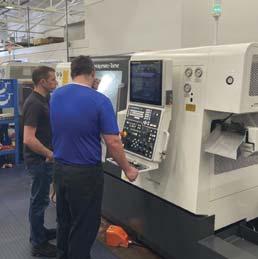
increased our productivity by 500%, making us cost-competitive with China. They also reduced our tooling costs considerably due to the machine set-up and rigidity. The latest two machines have immediately mirrored the success of the first two.”
The result of investing in the first two Nakamura machines significantly increased business from this particular offshore customer – and this is why two more WT150II machines have followed. As Gordon recalls: “The challenge this offshore customer had with supply from China was proximity. Proximity made any R&D work, amendments or part inspection an issue. Now, they can visit our facility to discuss projects, look at our production methods and equipment and investigate opportunities to enhance and develop their product lines with a local supplier and that is exactly what they are doing.”
“We started production on what they called the Mach 1, 2 and 3 valve designs. Now, we are fully integrated into the customers' R&D infrastructure, and we are working closely with them on the development of the Mach 4 valve. Since investing in the Nakamura machines, we have won much more business from this customer and the Nakamura’s are 95% dedicated to producing and undertaking R&D work on the Inconel valves.” 8 questprecision.co.uk
Wealdpark Limited
Stand number 5126

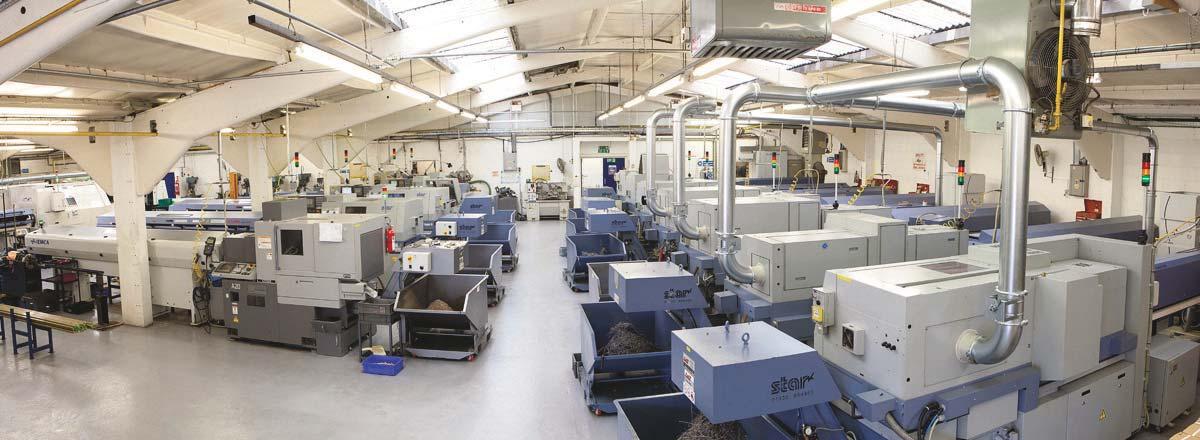

Subcontract Capacity
BS EN ISO 9001:2008. Approved by BSI since 1991.
Company Contact Details
Phil Smith, Director, Wealdpark Limited Sutton Road, St. Helens, Merseyside, WA9 3DJ Tel. 01744 22567 / 732083 Fax. 01744 451339 E: sales@wealdpark.co.uk www.wealdpark.co.uk
A new sliding head turning centre gives PES Engineering the capability, productivity and flexibility it needs to serve its customers.
Owner Martin Lock believes that it is difficult to justify using a fixed-headstock CNC lathe on turned and milled components under 38mm diameter.
Underlining this, he recently invested in a Cincom L32-XLFV sliding head machine supplied by Citizen Machinery UK.
He said, "We held off investing in this technology before, as up to about five years ago sliding-head lathes were not as flexible as their fixed-head counterparts in terms of their power or the number of tools in the working area. Consequently they could not produce such a wide variety of components, but that is no longer the case. "Modern sliding-head lathes are able to produce anything a fixed-head equivalent can, and on average completes the same cycles in two-thirds of the time. It is down to the speed of movement of the gang tooling and the wealth of static and live cutters that can be deployed."
Materials machined include stainless steels, which account for half of throughput and plastics, which make up another 20%. Both tend to generate stringy swarf when machined on the subcontractor's fixed-head lathes.
This can lead to reduced tool life and productivity.
The Cincom slider overcomes these swarf problems by using Citizen’s low frequency vibration (LFV) software that breaks the swarf into smaller chips.
Mr Lock continued, "LFV has removed much of the aggravation of turning stainless steels, which gives us a much easier life. We can machine efficiently everything from 304, which is billed as free cutting but really is not, through to highly alloyed marine grades. "We have LFV switched on permanently when machining plastics and it works perfectly, even on nylon. When processing stainless steel, for nine out of 10 components we produce it is engaged for typically half of the cycle and always for parting-off. "
At the end of last year, two 40 mm capacity fixed-head lathes producing 304 stainless steel medical parts broke down on the same afternoon, prompting Mr Lock to look for a replacement. As sliding-head technology had advanced sufficiently to consider it, he decided to go down this route.
He therefore ordered an L32XLFV with a conversion kit that allows stock up to 38 mm in diameter to be fed from an Iemca three-metre bar magazine.
The speed of the machine means that many parts are coming off more than twice as quickly compared with the output from one of the ageing fixed-head lathes. In one extreme case when turning a plastic part unattended, 400-off were produced in two hours instead of over a full manned shift. 8 pesengineering.co.uk
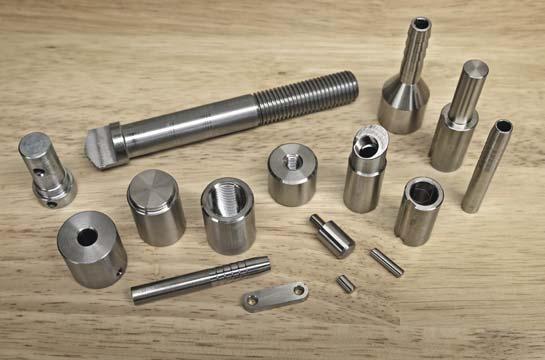
Sliding head productivity
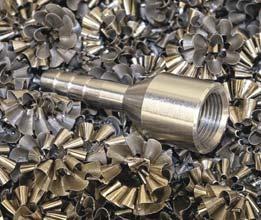
Aerospace interiors partnership
Donite Plastics has partnered with Queen’s University, Belfast to develop automated assembly processes and introduce a new product for aerospace interiors.
The funding for the project was awarded by the National Aerospace Technology Exploitation Programme (NATEP), co-funded by Innovate UK and the Aerospace Technology Institute (ATI).
Stephen Kissick, Donite Plastics’ Business Development Manager, claims that the funding award is testament to the company’s commitment to continuous improvement, adopting new technologies and pioneering in the thermoforming sector.
“On behalf of the entire team at Donite Plastics, we are very proud to have been selected to partner with Queen’s University on this prestigious project,” Stephen said. “We’re very excited to be able to use our knowledge and expertise to help further the aerospace sector, particularly after the challenges posed by the pandemic.”
Patrick Knight, Engineering and R&D Manager at Donite Plastics said; “The aerospace sector is renowned for its innovation, and through continuous improvement in both staff, technologies and machinery, we have the capability to provide quality products in a rapid turnaround time, which stands us in very good stead for this project.
“As the leading industrial thermoforming company in Ireland, this latest project now cements Donite Plastics as a centre for innovation and pioneering technology with highly skilled staff and a breadth of capabilities.
“Working on a project with a range of partners is something quite new for Donite Plastics, but we are confident that we can deliver and that we will continue to build upon our advanced capabilities.”
Meanwhile, Rory Collins, from the Northern Ireland Technology Centre at Queen’s University added: “We’re delighted to be partnering with Donite Plastics on what we know will be a very successful project.
“One of our main aims is to put Northern Ireland on the map as a world leader in terms of technology, manufacturing and innovation, which this project will achieve.
“We have a wealth of fantastic companies right on our doorstep, as well as a highly skilled workforce that can make a real difference to the aerospace sector and indeed all other sectors.” 8 donite.com
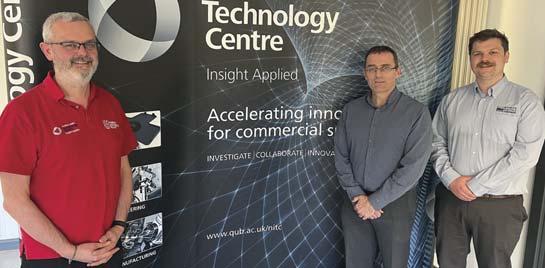
PRECISION ENGINEERING
Aerospace Oil & Gas Nuclear Defence
www.thomas-brown-engineering.co.uk
Tel: 01484 548903
Automotive Electronics Hi Fi Industrial & High Volume Machining
Advanced etching capacity
Two new high technology machines will expand capacity by 30% and help Advanced Chemical Etching meet growing demand from the aerospace, electric vehicle and fuel cell markets.
The Chemcut Etch machines will help customers bring their designs and prototypes to market quicker, a decisive selling point that the business hopes will help it meet its two-year plan to hit £10m in sales.
Ian Whateley, Managing Director of Advanced Chemical Etching, commented: “We are always looking at ways where we can reduce lead times and have greater control over the tolerances we can offer, and this latest investment reinforces that.
“The two etching machines are currently being installed and should be fully up and running by late summer. When they go live, we’ll have a third more production capability, which means we can go after new opportunities and there’s plenty of those currently, whether its supplying busbars and lead frames to EV or critical components to the medical sector.”
The company specialises in the development of precision components to customers in more than 25 countries, spanning aerospace, space, general engineering, automotive, electronics, medical, telecoms and renewables.
The scope of its activities is wide ranging and can include anything from safety critical components for aircraft and F1 cars, to meshes and electronic connectors, battery interconnectors, fuel cell
DNow Accredited to

FM10101
Manufacturers of High Quality Mill-Turned Parts bi-polar plates, cooling plates and heat exchangers.
It works to the most exacting tolerances and can manufacture components in materials, such as stainless steel, nickel alloys, copper, beryllium copper, phosphor bronze, brass and, thanks to new processes, aluminium, molybdenum, titanium, nitinol and Elgiloy.
Chris Ball, Executive Director said: “In addition to our recent investment drive, we have also strengthened our workforce with eight new people joining across our inspection, facility and plant maintenance, and our sales and marketing departments.
“There has been an increase in the number of special operation products we are getting involved in and this would necessitate the need for people to be multi-skilled and internally work across numerous projects. That’s why investment in ongoing training will be so crucial.” 8 ace-uk.net
Multi-tasking machine tools have allowed a specialist aerospace supplier to mitigate the impact of the recent turbulent business climate.
Prior to the pandemic, Merc Aerospace in Barrowford made a conscious effort to incorporate more ‘one-hit’ machining technology into its facility. The company initially replaced five older machine tools with two Nakamura WT150IIs as part of its commitment to lean manufacturing, reducing lead times for customers that include Airbus, AgustaWestland, BAE Systems and Bombardier. The sustained investment drive increased orders and subsequently turnover with the 50-employee company reducing costs, set-ups, lead times and improved throughput with the Nakamura machines.
Merc Aerospace took delivery of its first Nakamura-Tome WT150 IIF twin-spindle twin turret turning centre in October 2017 and it immediately replaced two existing machines whilst drastically improving productivity. This model was once again adopted when the second WT150 IIF arrived in March 2018.
The company then took delivery of a twin spindle triple turret Nakamura NTY3-150 multi-axis turning centre in April 2019. With the aerospace industry returning to prepandemic levels and Merc being well positioned to support its customers, the company took delivery of a Nakamura AS200LMSY sub-spindle turning centre in 2021 – and another in May 2022.
Merc Aerospace Managing Director, Mr Richard Meade said: “Historically, we had invested ad hoc in our machine shop and the turning centres on our shop floor were a representation of numerous high-end brands. We developed a strategy for investment and we knew the Nakamura brand had an outstanding reputation and are installed at a lot of prestigious businesses. We looked at several Nakamura machines and the WT150 IIF was the perfect fit. Typically, we machine relatively complex parts from exotic materials that range from 5-off to 100s and our set-ups could be an hour to days. The WT150 IIF machines changed all this.
“The twin-spindle, twin-turret configuration has been a game changer. It has increased flexibility and throughput and one Nakamura proved 30% more productive than the two machines that it replaced. Additionally, we had a range of sliding head machines that are better suited to higher production runs rather than the batches we run in the hundreds. The Nakamura’s wiped out our sliding head machines as the sliders were restricted to diameters well below 50mm and the set-up and changeover times were excessive for our batch sizes.”
With the WT150 IIF machines making such an impact at Merc, the company took the next step and opted for the Nakamura NTY3150 – a twin spindle machine with three tooling turrets that can all be engaged simultaneously. Primarily machining fuel injection and gas turbine components, the ability to engage three tool turrets simultaneously has made a tremendous impact. In one of many instances, the NTY3-150 has reduced cycle times from 1 hour 10 minutes on a previous twinspindle machine to just 35 minutes. 8 mercaerospace.co.uk
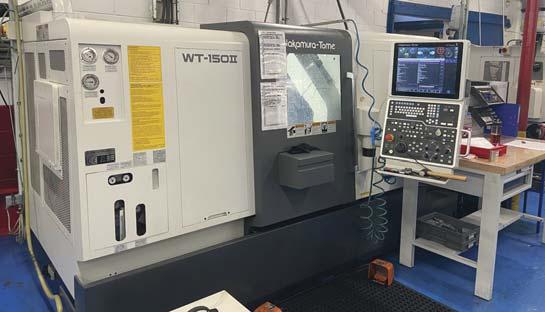
Multi-tasking resilience
Tube anniversary in Plymouth
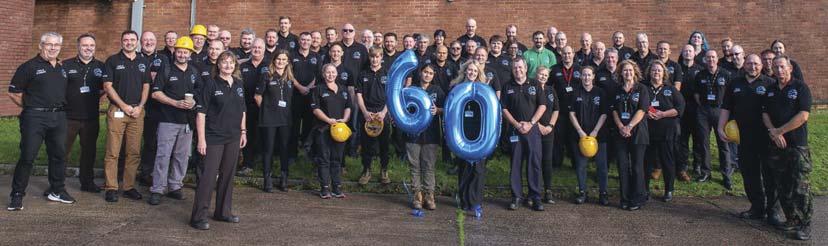
AMETEK Fine Tubes is marking 60 years since moving to purpose-built premises in Plymouth, Devon, in 1962. The business was originally founded in Surbiton in Surrey in 1943.
The company manufactures high-performance tubes in a range of specialty alloys for critical applications. As well as a large number of business milestones, Fine Tubes employees have raised an impressive £17,000 for local charities over the past four years.
In 1965, the business manufactured AM350 tubes for the Concorde program, while 1977 saw Fine Tubes make major strides in the nuclear field by developing 20/25 Nb nuclear fuel cladding tubes.
Over the years that followed, Fine Tubes expanded into new and ambitious projects, including seamless titanium 3AI/2.5V tubes for aircraft hydraulic systems, clean bore tubing for semiconductors, and data logging tubes for the downhole oil and gas markets. The manufacturer also pioneered several innovations within the medical sector, including titanium tubing for femur and tibia bone nail implants.
Fine Tubes was involved in several high-profile aerospace programs during the late 1990s and 2000s. Projects included supplying high pressure titanium tubing for the hydraulic systems of the Eurofighter, Airbus A380, and Airbus A350.
Other prestigious projects including developing 130 kilometres of cooling tubes for the Large Hadron Collider at CERN in 2008 and, more recently, specialist titanium tubing for the Chemical Propulsion System of the Solar Orbiter project.
Dave Cawse, Operations Director at Fine Tubes, says: “Fine Tubes has been operating successfully for almost 80 years and much of our success is attributed to the dedicated, loyal, and talented teams we have working at our production base in Plymouth. We are proud to have been manufacturing in Britain’s beautiful ocean city for 60 years and will be celebrating our diamond anniversary over the course of the year.” 8 finetubes.com