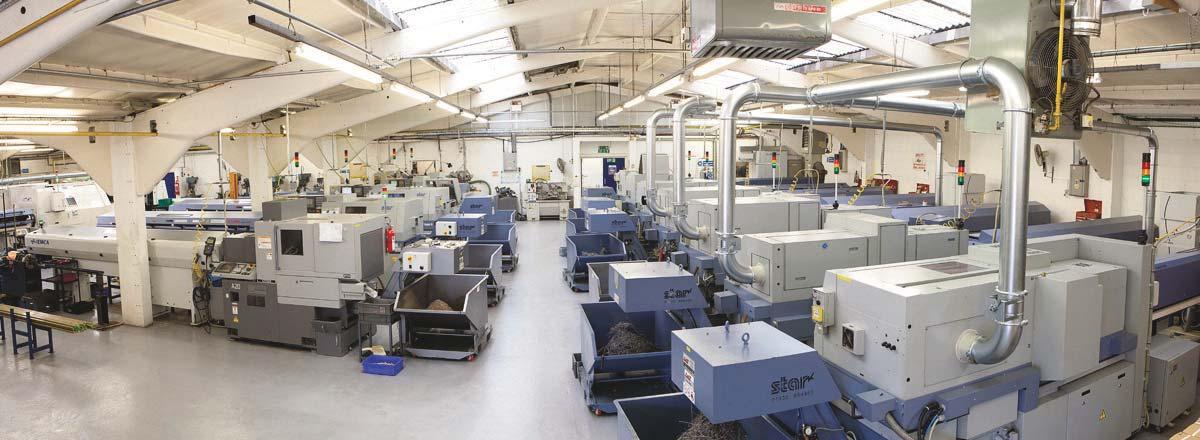
1 minute read
Aluminium Mini engine
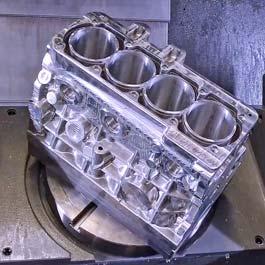
headcount today of 70 and annual sales of over £7 million. Managing Director Mark Wingfield supported Gary’s ambition, believing that that the addition of a proprietary product would enhance the subcontractor’s portfolio.
Advertisement
Gary built his first Mini engine at the age of 12. Even then he had a vision of building a block with five main bearings rather than three, with two extra columns either side of the central bearing to provide extra support for the crankshaft. The Covid pandemic combined with forward-thinking management at A&M EDM finally gave him the opportunity to design and produce it.
The block is machined on a Hurco VMX42Ui 5-axis VMC, while the crankshaft is produced from a solid billet using the swivelling B-axis of a Hurco VMX60SRTi VMC synchronised with the motions of a Kitagawa GT320 rotary 4th axis table. The initial engine design was for the front-wheel-drive, transverse engine layout of the Mini, but a crankshaft has also been developed for an in-line engine. So, with adapter plates it can be used in sports cars with rear wheel drive, such as the AustinHealey or MG Midget. There is even the possibility of starting a new race series if the engine is put into track cars.
Mr Surman said, "We have served the Formula One, automotive, marine and aerospace industries for many years and were able to employ those skills to manufacture our own engine. The original had three main bearings but the new version has five, so it can rev at higher speeds up to 10,000 rpm and accept a load in excess of 350 BHP.”

8 amedm.co.uk
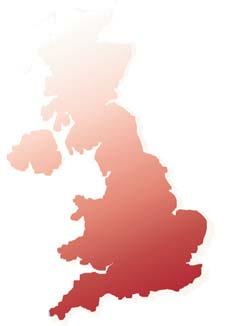