
17 minute read
Electronics
Clean manufacturing facility
Electronics manufacturing specialist Cogent Technology has unveiled a new production facility with advanced production lines and two cleanrooms for medical and healthcare products.
Advertisement
Cogent moved into its new 80,000ft² facility in Felixstowe, to serve its clients with world class manufacturing. The new facility features state of the art production lines, including two ISO 14644-1 Class 7 Rapidbloc cleanrooms.
Rapidbloc Cleanrooms have been developed by Connect 2 Cleanrooms (C2C) to meet the urgent critical demands of some of the world’s fastest moving industries, such as healthcare and advanced manufacturing. Clean production will enable Cogent to grow its product offering and expand services to clients with consumables and accessories that complement existing PCB assembly product ranges.
The two Rapidbloc cleanrooms were designed and built in just 8 weeks, including validation to ISO 14644-1 class 7. This expedited time-scale was important to Cogent as the cleanrooms were able to be coordinated within its wider facility fit-out programme and so production was not interrupted.
A monobloc cleanroom project of this scale would usually have a lead time of up to 4 months, whereas Rapidbloc Cleanrooms generate significant productivity gains to enable a faster return on investment. Rapidbloc cleanroom layouts are fully configurable and as parts are shipped from stock from C2C’s warehouse and distribution hub, on-site assembly is fast and efficient.
Robert Stainer, Commercial Director at Cogent says, “As part of our relocation to a new 80,000ft² facility we are proud to be enhancing our Medical Device manufacturing capabilities with the commissioning of two class 7 cleanrooms validated to ISO 14644-1.
“This investment will not only enable Cogent to meet our current clients’ needs, but also position the team to facilitate the provision of associated device consumables capacity as med tech businesses rethink their supply chain strategies in light of changing attitudes to sourcing.
“The term ‘short supply chain’ is resonating throughout the business world after recent events in 2020. A more robust supply chain is needed for resilience against future events.”
Michael Wright, Managing Director at Connect 2 Cleanrooms says, “Whilst there are now a number of quick build cleanroom solutions on the market, including our own Rapid Room range, none offer the same level flexibility around configuration and specification as Rapidbloc. The choice of size, classification and optional extras is yours, in just 4 to 6 weeks.
“This modular approach delivers a precision-engineered cleanroom with ISO-compliant performance, within an expedited time frame. Thanks to the use of standard parts and pre-determined design calculations, even the quotation and design stages are expedited, so clients benefit from a rapid response through the entire project.” 8 cogent-technology.co.uk
Electroplating specialist EC Williams is one of six companies participating in a Government funded project to recover gallium from used LED lights.
The nine-month project, which began on 1 November, is titled Recovery of Gallium Ionic Liquid (ReGAIL) and is partly financed by Innovate UK.
Williams will be studying opportunities for recovering gallium metal from LED lights. Gallium is usually only recovered from offcuts and shavings, and this is the first time the high-performance semiconductor will be recovered from end-of-life components.
The LED lights will come from WEEE (Waste Electrical and Electronic Equipment). There is currently no recovery for gallium when LED lamps are being recycled, and this project is hoping to determine a method that will hopefully reduce the need for extracting raw gallium and create a circular supply chain from the recovered waste gallium.
Used in a wide range of applications, gallium is a metal with the widest liquid temperature range of all the elements. Although it is not known as a precious metal, it has a reasonably high value of approximately £2,500 per tonne however this fluctuates. The EU classifies the element as a Critical Raw Material, and its largest producer is China (attributing to around 80% of it). Used in lasers, solar cells, Radio Frequency amplifiers, wireless chargers, and light detection systems, gallium is very versatile and is predicted to be
Leading lights in LED recycling
in increasing demand over the next decade as the use of electrical vehicles rises. This is as a result of the fact that it will be used in Power, Electronics and Machine Drives. One of its most common uses is in LED lamps, which currently account for around 2% of the tonnage of UK waste lamps.
Whilst LED lamps are currently only making a small percentage of lamp wastage, the timing of this new project is perfect. Put simply, it is providing the opportunity to create a sustainable solution for waste gallium before LEDs begin to take up large quantities of waste. Due to its low heat loss properties and smaller space requirements, gallium is very likely to replace silicon in the future when it comes to power system semiconductors. With this in mind, identifying ways to capture the element through recycling processes will reduce the need for raw extraction, and therefore increase the country’s supply chain efficiency. A viable solution will also decrease the chances of the UK needing to import gallium from abroad in the future.
The company said: “EC Williams Ltd is delighted to be working alongside five other reputable companies on research that could truly create a more renewable, cost-effective, and environmentally-friendly process for the future of gallium extraction and the recycling of LED lamps. As a consortium of companies, we are prepared for the challenges that may be faced over the next 9 months of studies, however we are confident that we will establish success.” 8 ecwilliams.co.uk

Robotic process automation has for some time assisted in the field of additive manufacturing. But such are the benefits being attributed to robotics, such as repeatability, accuracy and consistency, automated additive manufacturing as a process, is quickly emerging as a disruptive technology, that is significantly altering the way that industries such as construction and ship building manufacture products. 3D printing, also known as additive manufacturing, is the process of producing three dimensional solid objects from a digital file, utilising additive processes; the repeated application of layers of composite material, to form solid state products. There are several benefits to the adoption of additive manufacturing processes. The most significant, aside from product integrity, is affordability – 3D printing enables manufacturers to produce complex shapes using less material than traditional manufacturing methods, and as a process has been used to support mass customisation; aligning mass production to multiple product iterations to satisfy consumer demand.
Additive manufacturing, as a flexible production process, is faster, more economic and can be undertaken using several different

Credit: JCDA materials, according to the structural and aesthetic demands of the end product. In the case of manufacturing using plastic composites, the 3D printing process is free of any retooling or mould changes. The manufacturing process itself is also quicker. If we consider 3D printing using concrete, as an example within the construction industry, increased design flexibility and zero material waste considerations are satisfied. Intensive labour is also significantly reduced, so health and safety considerations are met.
Aside from the conventional, additive manufacturing can also be utilised to satisfy the not so conventional and creative, within areas such as architecture with projects being realised through automated robotic means. One great example is the world's largest concrete 3D printed pedestrian bridge, installed in the Wisdom Bay Industrial Park, Baoshan District,

Shanghai, developed by Professor Xu Weiguo from Tsinghua University (School of Architecture) and Zoina Land Joint Research Center for Digital Architecture (JCDA). 26.3 meters in length and 3.6 meters wide, the bridge’s structure is inspired by the ancient Anji Bridge in Zhaoxian, China. Adopting a single arch structure to bear the load, the distance between the abutments is 14.4 meters. Before being produced, a 1:4 scale physical model was constructed, and structure failure testing was undertaken to prove construction integrity across the entire bridge.
All the concrete components of the bridge were printed using two KUKA robotic arms and an independently developed 3D printing systems in just 450 hours. Compared with conventional bridges of similar sizes, its construction costs compared to traditional manufacturing methods were significantly lower, by almost a third. This was mainly attributed to not using any templates, nor reinforcing bars within the bridge’s structure and design, that was comprised of three-dimensional solid modelled sections.
These same manufacturing principles could be realised across multiple sectors. Additive manufacturing has the capability as a process to potentially revolutionise businesses by providing an entirely new means of production, allowing designs to be realised at reduced cost with enhanced productivity, transforming existing supply chains.
The UK manufacturing sector has suffered its most challenging year in its recent history. COVID-19 is forcing businesses to realign their production footprints, add to that the challenges that we may face post BREXIT, such as the impact upon our access to low-cost labour. For many businesses, this is a serious problem, but robots can help future-proof operations from the vagaries of labour supply. The adoption of robot process automation must be a very real consideration within manufacturing sectors such as construction. It has widely been


Credit: JCDA reported how the skills gap has impacted manufacturing, and this is set to worsen. The skill shortage crisis is one that has been jeopardising the construction industry and considering increased concern, it is expected to inflate the cost of labour as the pool of skilled labour decreases.
A focus upon cost savings is an omnipresent consideration across several manufacturing sectors; reductions in waste, time savings, increased throughput capabilities, to name but a few. 3D printing is still quite a new concept, though we as an industry have moved on considerably since the 1980’s. The last decade has seen an explosion in technologies and 3D printing innovations, and robotic applications are increasing in the additive manufacturing field, providing a powerful combination for numerous options in the design and production of precise, lightweight and inexpensive components from a wide range of different materials.
The possibilities are endless; new geometries be satisfied; assemblies of parts can now be produced as one piece; post processing of individual parts is eliminated. As with any automated robotic process, manufacturers need to embrace the technology, as a means to drive innovation, diversity and maintain competitive advantage. 8 www.kuka.com
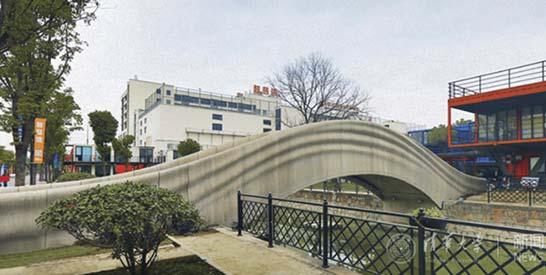
Growth drives EDM investment
Excel Precision has recorded several consecutive months of record sales figures during the Covid pandemic. This has spurred investment in a new Sodick ALC600G CNC wire-erosion machine from Sodi-Tech EDM.
The machine, which is sited at the company’s Birmingham facility, adds to an identical model at its Gloucester site – and becomes the sixth Sodick EDM across all three Excel Precision locations (Leeds, Gloucester and Birmingham).
Founded in 2011, Excel Precision provides EDM services to sectors that include aerospace, defence, oil and gas, petrochemical, nuclear, bio-medical, automotive, motorsport and white goods. The UK’s reliance on a number of these industries during the pandemic has helped the 30+ employee company to thrive.
“We’ve remained fully operational throughout the pandemic as we are acutely aware of the importance of the services we provide our customers, many of which help ‘keep the lights on’, such as those in the power generation, nuclear and oil and gas sectors,” explains Tony Sitek, Director of Business Development and the company’s majority shareholder. “A consequence of remaining fully operational was record months in terms of revenue in April, May, June and July. Excel Precision has always held a very strong position in the marketplace, however our performance during the pandemic has shown both existing and new customers our commitment to providing the highest levels of service in the most difficult of circumstances.”
“The reason we can assist new clients so readily is that we’re not afraid to invest,” states Mr Sitek. “We’ve invested £1.2 million since January 2019, with new machines going into all three of our manufacturing facilities. If we fill up a shop, we buy another one. We started with Leeds in 2011, adding Gloucester in 2013 and Birmingham in 2019, doubling our capacity each time. In the process we’ve slowly been replacing older machines with the latest manufacturing technologies – faster, more accurate and more energy efficient. This strategy has allowed us to increase turnover by 100% in the past three years alone.”
8 Ghawsuddeen Popalzia Apprentice
and Steve Batt MD with Sodick technology installed at Excel Precision
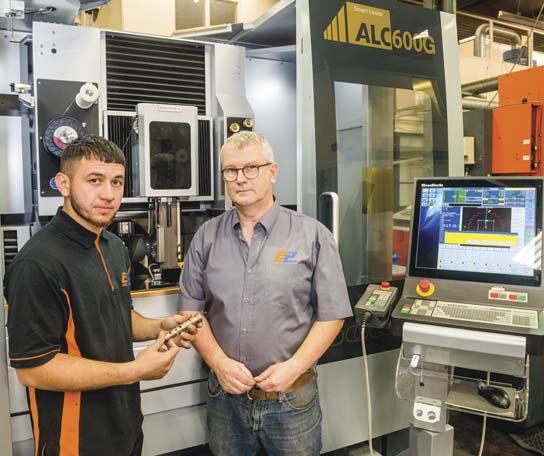
A case in point is the latest Sodick ALC600G wire EDM for the company’s Birmingham site, which specialises in both the military and commercial aerospace sectors. Excel Precision holds approvals with a number of leading aerospace OEMs, and carries AS9100 rev D certification, as well as NADCAP AC7116/3 rev B approval for both wire and spark erosion.
“When we acquired the Birmingham site it had been underinvested for many years,” explains Mr Sitek. “We identified the need for a new CNC wire EDM machine to help the facility make parts quicker, more efficiently and more competitively, all while retaining the highest levels of accuracy and
surface finish – the Sodick ALC600G has brought all that.”
Excel Precision first switched to Sodick technology last year when trials revealed far quicker component cycle times – for less energy consumption – than could be achieved using its existing machines.
“We took the plunge and acquired our first two Sodick machines in January 2019, since when we haven’t looked back,” says Mr Sitek. “The latest Sodick ALC600G wire EDM is already making parts. Around 98% of what we do at Birmingham is aerospace work.”
Moving forward, Excel Precision remains on the lookout for further companies to acquire as it seeks expansion into other parts of the country.
“The UK does not have many subcontract EDM shops,” says Mr Sitek. “There’s probably around 25-30, a high proportion of which are owner-operator businesses. We are different. The way for us to grow is through the acquisition of like-minded companies. Currently, across our three premises, we have 32 CNC wire/spark erosion machines, which I think would define us as the UK’s largest provider of subcontract EDM services. And we will only get bigger.” 8 excel-precision.co.uk
Wealdpark Limited


Stand number 5126
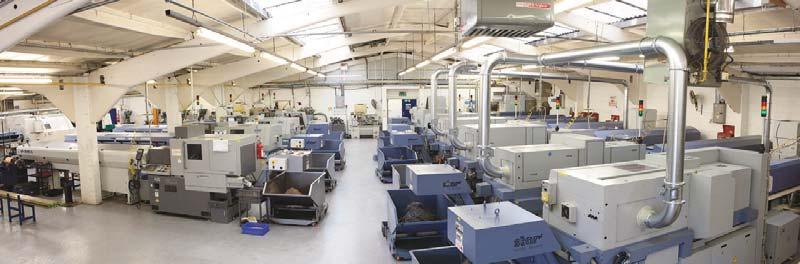
Subcontract Capacity
BS EN ISO 9001:2008. Approved by BSI since 1991.
Company Contact Details
Phil Smith, Director, Wealdpark Limited Sutton Road, St. Helens, Merseyside, WA9 3DJ Tel. 01744 22567 / 732083 Fax. 01744 451339 E: sales@wealdpark.co.uk www.wealdpark.co.uk
The newly created manufacturing arm of engineering and training consultancy Cutting Blue has invested in its first vertical machining centre.
The new Doosan, large capacity, machine was delivered by Mills CNC to Cutting Blue’s 2,000 square foot facility in Saltley.
The creation of the new venture is the brainchild of owner and managing director Piotr Parobczy.
Having started his working life, first as a machine tool setter and then as a CAD/CAM programmer, Mr. Parobczy used this knowledge and experience, gained from working in a number of different manufacturing environments, to develop and hone a range of specific engineering consultancy skills.
The acquisition of these skills ultimately enabled him to work as a contractor where he was responsible for the design and implementation of innovative and high-value projects for a number of UK- and internationally-based customers.
Following on from this success, in 2017 Mr Parobczy set up Cutting Blue Ltd - an engineering service company providing specialist training and consultancy services to blue-chip and progressive manufacturing companies.
He says: “Cutting Blue Ltd., began its life as an engineering consultancy. However, even back then it was always my ambition and intention to create a manufacturing company - when the time was right.”
That time, as it transpired, was in Spring 2020. “The pandemic
New manufacturing venture
outbreak had a detrimental effect on the availability of contract work and this proved to be the catalyst I was waiting for.
“Because the creation of a manufacturing company was a long-held ambition of mine I was not starting such an undertaking from scratch. To a large extent much of the spadework and planning had already been done.
“I chose Birmingham because of its central location and because I knew the area well.
“From my background and experience the company would
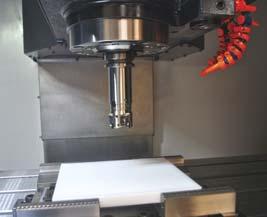
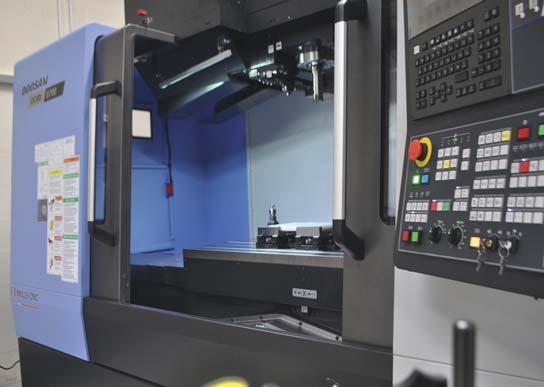
not be a ‘jack of all trades’ operation but instead would offer specialist, high-precision machining services to customers typically operating in the high-end motorsport, automotive and aerospace sectors.”
Says Piotr Parobczy: “The DNM 6700, with its large worktable, provides much needed capacity, capability and flexibility now and in the future, enabling us to machine large or multiple smaller parts in one set-up.
“Although still early days I am delighted with the DNM 6700 and am already looking at investing in second Doosan machine.” 8 cuttingblue.com
KMF has invested in a second high performance turning centre that will double critical capacity.
Due to an anticipated increase in demand post Covid-19, the group has purchased a second Yamazaki Mazak QUICK TURN 250MSY to complement its suite of Mazak equipment.
The Mazak QUICK TURN is a high-performance turning centre equipped with a Smooth Mill Drive turret capable of machining a range of parts accurately and efficiently. Materials such as standard steels, aluminium, stainless steel and more exotic materials such as Inconel are easily machined to precise tolerances.
The new equipment will further support clients in the aerospace, instrumentation, scientific and medical industries.
Keith Nicholl, Commercial Director at KMF Group said: “The machine is co-located with an existing QUICK TURN 250MSY, effectively doubling our capacity to allow us to respond to increased demands from our new and existing customers. Both machines are linked to our offline programming capability resulting in high levels of machine cutting efficiency, 24 hours a day and seven days per week and a quick response for short lead time or prototype needs.
“Covid-19 affected many businesses and as we emerge from the worst of the crisis we’re positioning ourselves to ensure that we’re fully prepared to support customers across various sectors with immediate effect. By investing
Preparing for post-Covid demand

now, and being business ready, we can proactively support our customers with their own revival.”
The QUICK TURN 250MSY has a 500mm bed capacity and is equipped with a 10inch chuck on the main spindle and a six-inch chuck on the secondary spindle enabling part sizes up to 380mm to be effectively machined. Its capability enables most components to be machined complete off the machine, which in turn improves efficiencies. It’s also equipped with a Hydrafeed Multifeed magazine bar feed enabling unmanned running of small to medium batch quantities.
Keith added: “This MSY complements KMF’s collection of other Mazak machines, which includes two HCN 5000-III horizontal machining centres served by an 18 station PALLETECH system, a VTC800/30SR vertical machining centre and a VARIAXIS i-500 simultaneous 5-axis machining centre. This machinery provides capabilities suitable for any of our customers’ machining requirements.”
Neil Coggins, Area Sales Manager at Yamazaki Mazak UK, concludes: “As production begins to increase across multiple industries following the disruption caused by the pandemic, it is vital that subcontractors have the engineering capacity to hit the group running.
“To that end, we have been delighted to provide KMF Group with an additional QUICK TURN 250MSY to accompany their company’s existing Mazak machines. Operating a wide array of solutions from a single provider like Mazak enables KMF to deliver a large variety of machining applications to suit their broad customer base. Alongside this, investing in Mazak machines ensures a baseline of quality in machining work that may not be possible with a mixture of different machining centre suppliers.” 8 kmf.co.uk