3 minute read
New Products
Inline quality control for process optimization
With the Radar Scan 6000, the Sikora company offers a system for non-contact inline measurement of the diameter and ovality of metal pipes and rods. According to the manufacturer, it is based on high-reso
lution radar technology and records the measured values over 360 degrees of the product circumference with micrometer accuracy. Due to its slim design, the system is also easy to integrate into the production process and is used for both hot and cold measurement. In addition, trend and statistics functions as well as data logging are available. Other products that Sikora will present in Dusseldorf are the Planowave 6000 for thickness measurement of slabs or metal strips and the Laser Series 2000 for measuring the diameter and ovality of tubes, wires and bars during production.
Sikora‘s Radar Scan 6000 is designed to provide accurate diameter readings under all environmental conditions including heat, dirt and steam.
Combined tube bending for the automotive sector
The Schwarze-Robitec company wants to address the high demands of the automotive sector with regard to speed and efficient use of material resources. For this reason, it has refined and further developed its tube bending machines. Its fully electric multi-radius tube bending machine CNC 80 E TB MR is capable of bending tubes with diameters of up to 80 millimeters and can cut them in one process step by means of an integrated fully electric cutting unit. By combining bending and cutting processes, the machine enhances efficiency and saves resources during processing, leading to shorter turnover times and up to a 90 percent reduction of material waste.
Schwarze-Robitec‘s fully electric multi-radius tube bending machine CNC 80 E TB MR is tailored to the requirements of the automotive industry.
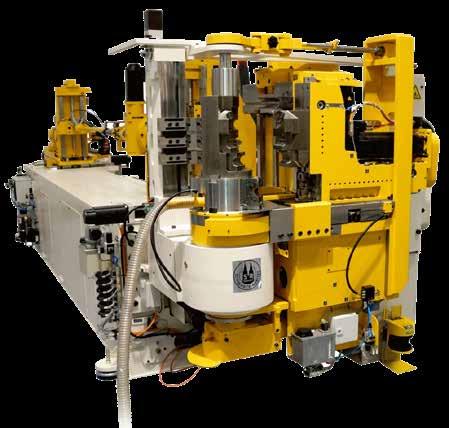
New surface roughness meter
The new surface roughness meter (profilometer) should allow stainless steel tubes to be precisely tested at each 10 th or 20 th standard production length.
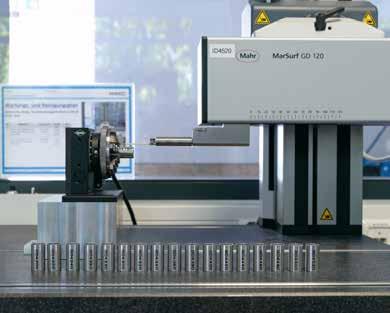
Schoeller Werk has introduced a new surface roughness meter (profilometer). The product should ensure compliance with relevant standards in the food and medical technology sector and allow stainless steel tubes to be precisely tested at each 10th or 20th standard production length. In addition, the surface roughness values can be measured both in longitudinal and transverse direction. Beyond that, the company has recently introduced a new device for the measurement of surface roughness values. The MarSurf GD 120 is controlled by software and permits the creation of its own measurement routines. In this way, Schoeller Werk can use pre-programmed settings for material samples, without having to alter the device setting manually to test a tube of different diameter.
Square and rectangular tubes made with a universal set of rolls
FIMIGroup has extended its product portfolio by tube mills able to produce square and rectangular tubes with a universal set of rolls and with an automatic adjustment system controlled by the PLC. This decreases dramatically the time needed to change size and permits to have the possibility to produce all the sizes needed without delivery time lost for rolls manufacturing, the company says. Moreover, the direct forming of the 90° edges of these tubes, without passing from the round mother tube, permits also to save raw material. Effectively, the thickness on the edges decreases instead of increasing as in the traditional forming when the round tube is squared. For this reason, the starting width of the coil can be from 4% to 8% narrower, saving tonnes of steel every year on the total production. The standard configuration of the mill is with eleven stands before the welding head, two or three sizing stands depending from the range of thicknesses
required and two turk heads. The first five stands are used to form the lips from the flat strip. Then, four stands complete the most of the forming using the internal rolls. Two fin-pass stands are then completing the forming creating the V channel with the shape to weld the tube correctly.
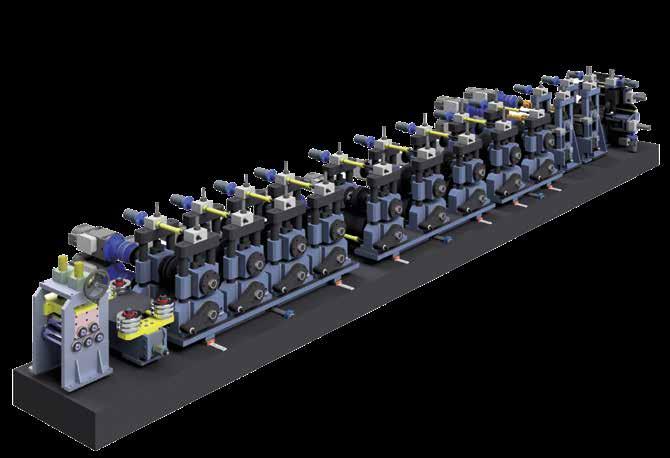