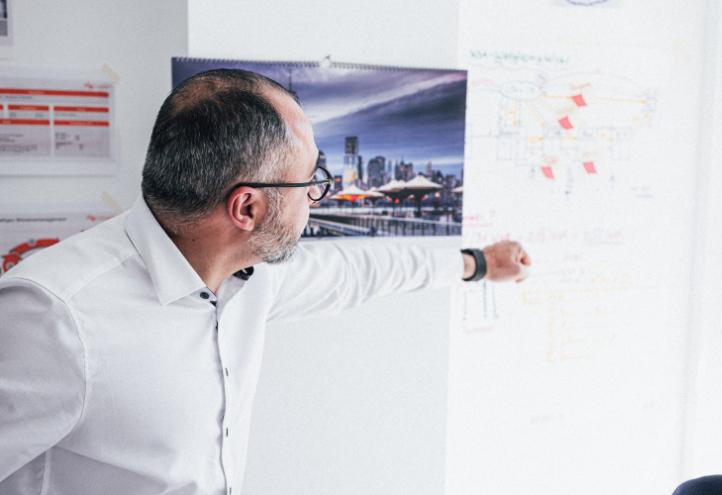
6 minute read
Die Grundlagen einer Lean Production
| ImLeanManagementwurdenimLaufederZeiteineVielzahl von Methodiken entwickelt, um verschiedenste Herausforderungen zu bewältigen und die im Unternehmen liegendenPotenzialeabzurufen.
Bei der Lean Production geht es um schlanke bzw. verschwendungsarme Prozesse. Um ein Problem, eine Verschwendung zu beheben ist es immer erforderlich gewisseBedingungenzuschaffen:
Advertisement
Bedingung 1
Man muss die Ursachen ausfindig machen/kennen. Hierzu kann man auf Methoden der Praktischen Problemlösungen (PPL) zurückgreifen, wie dem Ishikawa Diagramm oder die 5WMethode.
Nehmen wir als Beispiel den Betrieb einer Stanzmaschine. Diese kann pro Stunde ca. 3600 Stanzungen durchführen. Tatsächlichfindenallerdingsnur3000statt. Wir wenden 5W an:
Warum führen wir 600 weniger Stanzungen durch als möglich?
Weil die Maschine aufgrund von Materialmangel gelegentlich anhalten muss. Die Verschwendung ist also WAITING.
Warum haben wir an der Maschine Materialmangel?
Weil vom vorhergehenden Prozess nicht schnell genug nachgeliefert wird.
Warum wird nicht schnell genug nachgeliefert
Weil unklar ist, wann genau die nächste Lieferung erfolgen muss, bevor der Restbestand an Material an der Maschine verarbeitet ist.
Warum ist unklar wann die Lieferung erfolgen muss?
Weil kein klarer Standard definiert ist, ab welchem Mindestbestand der Lieferungsprozess starten soll.
Wir müssen also einen klaren und einfachen Standard einführen, zu welchem Zeitpunkt der vorhergehende Prozess die nächste Lieferung durchführen muss.
Methodenbeschreibung
5W Methode
Die 5W Methode ist eine Methode der praktischen Problemlösungen (PPL). Dem sogenannten Werkzeugkoffer des Lean Managements. Die PPL umfassen eine Vielzahl von Methoden die bei der Ermittlung und Beschreibung der Ursachen von Verschwendungen unterstützen und organisatorische Strukturen anbieten, mit denen die Verschwendungen systematisch behoben werden können.
Die 5W Methode basiert auf der Überlegung, dass man, wie Kinder es gerne tun, nur hartnäckig WARUM? Fragen muss, um den Kern eines Problems zu ermitteln. Durch konsequentes Hinterfragen stößt man auf die Ursache, welche es zu beheben gilt.
Bedingung 2
Man muss den IST-Zustand genau kennen. Um den ISTZustand eines Prozesses zu kennen ist es unbedingt erforderlich eine konkrete Zahlenbasis erheben zu können. Oftmals existieren für Prozesse keine konkreten Kennzahlen und auch keine Standards für die Messung. Damit die Auswirkungen von Optimierungsprojekten gemessen werden können, müssen Prozesse allerdings messbar sein. Hier kann man mit der 5S Methode Arbeitsbereiche strukturieren und messbarmachen.
Am Beispiel der Stanzmaschine sehen wir, dass ohne eine standardisierte Vorgehensweise für die Lieferung neuen Materials Produktionsstopps an der Maschine eintreten können.Waskönnenwiralsotun?
VondenMitarbeiternwissenwir,dieLieferungvon3600Teilen für eine Stunde für die Stanzbearbeitung benötigt 10 Minuten. In den 10 Minuten kann die Stanzmaschine 600 Stanzungen durchführen. Wir brauchen also ein Zwischenlager im Arbeitsbereichbeidemklarerkennbarist,wanndieMarkevon 600Teilen unterschritten wird und eine neue Materiallieferung initiiertwerdenmuss.
Hierzukönntenmittels5SsechsgleichgroßeLagerflächenfür dieTeilemarkiertwerden,injedemPlatzfür600Teile.Sinddie erstenfünfFlächenfreiundnurnocheineFlächebelegt,muss dienächsteLieferungspätestenserfolgen,damitdasMaterial rechtzeitigeintrifft.WirhabenalsoeinenStandardgeschaffen ausdemklarabgelesenwerdenkann,wievielMaterialvorliegt und wann konkret Neues geliefert werden muss. So wird ersichtlich, dass vorab immer erst Material bestellt wurde, wenndieletzteFlächenurnochzurHälftegefülltwar.
Bedingung 3
Den Informationsfluss optimieren. Im letzten Schritt können dieInformationenfürdieLieferungenunddieKennzahlen:
• Liefermenge
• Dauer
• Materialbezeichnung
• Undmehr auf einer Karte festgehalten werden. Sobald das Mindestmaß an Bestand bei der Maschine unterschritten wird, wird mit dieser Karte dem vorhergehenden Prozess exakt mitgeteilt was, wie viel, wann und wohin geliefert werden soll. Dieses KANBAN-System stellt reibungslose PULL-Vorgänge in der Produktion sicher, sodass Material immer in der benötigten Menge an rechten Platz rechtzeitig ankommt. Nun wird die Stanzmaschine ihr volles Potenzial von 3600 Stanzungen abrufenkönnen,eineVerbesserungvon20%.
Methodenbeschreibung
5S Methode
Bei der 5S Methode geht es darum, Strukturen zu erschaffen in denen Standards definiert werden können. Die Methode geht dabei in 5 Schritten vor:
1. Seiri (Aussortieren von nicht benötigten Gegenständen)
2. Seiton (Aufräumen des Arbeitsplatzes)
3. Seiso (Anordnen aller benötigten Materialien)
4. Seiketsu (Arbeitsplatz sauber halten, Standards definieren)
5. Shitsuke (Anordnung zur Regel machen, Standards einhalten)
Ein Beispiel für 5S sind Shadowboards. An einem Shadowboard werden die Umrisse der benötigten Werkzeuge dargestellt. Für jedes Werkzeug gibt es einen festen Platz und der Umriss zeigt an wo dieser ist. Sollte ein Werkzeug fehlen, fällt dies sofort auf und muss umgehend ersetzt werden. Durch diesen Standard ist es ausgeschlossen, das Material oder Werkzeug, welches für den Arbeitsbereich unabdingbar ist, fehlen sollte.
Methodenbeschreibung
Kanban
Kanban ist die am häufigsten ausgeführte PULL-Methode und wird auch SupermarktPrinzip genannt. Wenn wir im Supermarkt an der Kasse bezahlen, werden die gekauften Produkte gescannt. So erkennt das System, welche Produkte aus den Regalen entnommen wurden und sendet automatisch Informationen an das Lager (den vorgelagerten Prozess), aus dem das Regal wieder aufgefüllt wird.
In der Produktion werden die Kanban ebenfalls verwendet, um Informationen über Produkttyp und Menge des Bedarfs an den vorgelagerten Prozess zu vermitteln. Dieser bekommt mit dem Kanban also einen Produktionsauftrag über die bereitzustellende Menge und den Produkttyp für den nachfolgenden Prozess. Die Produktionslinie wird hierbei Rückwärts betrachtet, wobei der Kunde mit seiner Bestellung den Produktionsprozess initialisiert.
Was folgt? Fazit
| Wennmanalsoanalysiert,wodasProblemliegt, welche Verschwendung zu Grunde liegt und die Prozessetransparentundmessbarmacht,dann können die Potenziale systematisch abgeschöpft werden und die Verschwendungen werdeneliminiert.Sobilden5Sund8Vhäufigdie Basis für eine Lean Production, mit der die Effizienz der eigenen Produktion drastisch erhöhtwerdenkann.
Mit Lean Management sind wir nicht nur in der LageeinzelneVerschwendungenzueliminieren, sondern mit Lean Management haben wir ein ganzheitliches System, welches uns befähigt Verschwendungenumfassendzubeseitigen.Da diese Verschwendungen in Relation zueinander stehen werden wir nur messbare Erfolge haben, wenn auf dem gesamten Wertstrom die Verschwendungeneliminiertwerden.
Praxisbeispiel Tag 1
Gemeinsam haben wir mit unserem Kunden einen KVP Workshop mit dem Focus 5S organisiert. Ziel der Veranstaltung war es das Methodenwissen und Lean Verständnis zu fördern indem wir die Methoden nicht nur theoretisch erklären, sondern auch die Wirkweise im Arbeitsalltag der Mitarbeiter des Kundenaufzeigen.
Dazu haben wir in dem zweitägigen Workshop zunächst Wirkweise und Anwendung der Methodevermittelt,umdieTeilnehmerinhaltlich abzuholen und das Potenzial von 5S aufzuzeigen, als auch die Zusammenhänge zu anderenMethodenzuerläutern.
5S spielt dabei in vielen Feldern eine Rolle. Wie vorab bereits beschrieben dient diese Methode alsFundamentfürvieleLeanAnsätze.
Zum Beispiel:
SolltemaneinenwenigerganzheitlichenAnsatz wählen, sind die Effekte bei Optimierungsprojekten kaum spürbar. Denn behebe ich nur ein separiertes Problem, treten zumeist einfach nur an anderer Stelle neue Problemeauf.
Beispielsweise kann ich einen Bottleneck im Wertstrom beheben, indem ich an dieser Stelle mehr Personal oder Maschinen einsetze. Doch meistens wird sich der Bottleneck dann nur an eine andere Stelle des Wertstroms verschieben, denn die nachgelagerten Prozesse werden Ihrerseits nun, wo das Bottleneck im vorgelagerten Prozess behoben ist mit der Produktionnichthinterherkommen. Man benötigt also eine ganzheitliche Betrachtung für den Wertstrom, also eine Austaktung vom Kunden bis zum Lieferanten, damitkeineBottlenecksauftreten.
GLEICHZEITIG…
Werden auf diesem Wege viele weitere Probleme vermieden oder behoben, wie wir im nachfolgenden Beispiel aus unseren Projekten aufzeigenwollen.
Anlageneffektivität
Ordnung und Sauberkeit
Shopfloor Management
KPI´s
Qualität
Sicherheit
Visualisierung
Standardisierung
KANBAN
LINE BACK
POKA YOKE
Und vielen mehr…
Die Methode behandelt dabei nicht nur die Themen rund um Sauberkeit und Ordnung, vielmehr befasst sie sich mit unserem Mindset, dem Willen das Beste aus sich herauszuholen. Wie sehen wir die Herausforderungen und wie stehen wir zu ihnenimLEANKontext?Genauhiersetztenwir an bei unseren Schulungen und das Ergebnis ist, dass die Teilnehmer eine Reflektion Ihrer eigenen Arbeit bekommen, wie Sie mit den Arbeitsmitteln bzw. Anlagen und Werkzeugen tagtäglichumgehen,dieIhnenderArbeitgeber zurVerfügungstellt.Unddawirdesmanchem klar, dass die Anlagen mehrere Millionen Euro kostenunddieMitarbeiterselbstinnerhalbder Arbeitszeit die Verantwortung dafür haben, eben das Beste aus diesen Anlagen und Werkzeugerauszuholen.
SomitisteswichtigamerstenTageinoffenes Ohr zu haben und sich nicht gleich auf die Methodenanwendungzustürzen.
Man muss als Vermittler der Methode zuallererst einmal verstehen, warum die Mitarbeiter arbeiten, wie sie es tun. Von diesem IST-Zustand aus entwickeln wir dann gemeinsam mit den Mitarbeitern den SOLLZustand. Erst Verständnis schaffen, dann umsetzen, so erhält man eine größere AkzeptanzbeidenMitarbeitern.
Denn meist werden die Methoden dafür verantwortlich gemacht, wenn die gewünschten Ziele oder Bereichs KPIs nicht erreicht werden, obwohl die Methoden nicht odernichtrichtigeingesetztwurden.
Praxisbeispiel Tag 2
|
Nachdem die theoretischen Grundlagen vermittelt wurden und eine Akzeptanz für die Methode geschaffen wurde, geht es dann in diePraxis.
DabeiwerdendieTeilnehmerindie5SThemen verteilt und bilden kleine Gruppen, die für die Umsetzung verantwortlich sind. Die Umsetzung fand im Workshop am selben Tag direktanderMaschinestatt.
Die Gruppe „Säubern“ hat dann festgestellt, dass die BAND-Motoren einer Kunststoffanlage extrem verdreckt waren, sodass sich der Dreck in die Kettenglieder eingefressen hatte. Dies hat in der Maschine widerstand erzeugt. Die Bediener haben deswegen die Parameter der Anlage erhöht und mehr Energie aufgewendet, damit die
Maschine in derselben Geschwindigkeit wie zuvorfahrenkonnte.
Das führte dazu, dass es immer wieder zu abrissen im Kunststoff kam bei den unterschiedlichen Mitarbeiter-Schichten, da die einzelnen Mitarbeiter die Parameter jeder für sich immer neu eingestellt haben bei den UmrüstungenanderAnlage.
Nach dem wir die Reinigung innerhalb von 4h durchgeführt hatten und die Maschine nun wieder frei laufen konnte, musste die Anlage wiederaufdieursprünglichenaltenParameter eingestellt werden. Das heißt, dass erheblich weniger Energie und Kraft aufgewendet werden mussten, um die geforderte Geschwindigkeit einzuhalten und den Kunststoff durch die Anlage zu ziehen. So konnte an der Maschine der Stromverbrauch um 50% reduziert werden. Somit wird auch hier deutlich, wie wichtig das Verständnis ist fürdieLEANMethoden.
Es geht nicht nur darum die Methoden in einemUnternehmeneinzuführen.Dasistnicht die Herausforderung, sondern die richtige Anwendung und Begeisterung zu schaffen für dieKraftderVeränderungimUmgangmitden LEANMethoden.
-AlirezaSoltanyNoory
Wirkönnenalsofeststellen,dassimSinneder Nachhaltigkeit drastische Energieeinsparungen erreicht werden können, wenn man sich selbst die nötigen Standards setzt und diese einhält bei der Bedienung und WartungderMaschinen,wieauchProzesseim allgemeinen.
IndiesemBeispielkonntenMaschinenausfälle durch einen zuvor erhöhten Verschleiß reduziertwerden,weildieMaschinenachdem SäubernnichtmehrmitübermäßigvielEnergie gegen die Verschmutzung laufen muss. Weniger WAITING bei Maschinenstillstand durchWartung.
Ebenfalls konnte die Qualität im Kunststoff erhöht werden, der nicht, wie zuvor wegen der großen Kräfte in der Maschine und unsteter Einstellungenreißt.WenigerDEFECTS.
UndamEndekonnteauchderStromverbrauch drastisch reduziert werden im Sinne der Lean Sustainability. Denn ein insgesamt effizienter Wertstrom erzeugt sämtliche Verschwendungen in einem wesentlich geringeren Maße alsunausgereifteProzesse.