
9 minute read
Be Aware Safety Tips
DIY: Meeting OSHA’s Employee Safety Training Mandates in the COVID-19 Era
By Laura Helmrich-Rhodes, CSP, Ed.D.
At the risk of putting myself and other training specialists out of business, it’s important during this COVID-19 era that every employer know what safety training topics need to be covered, even when a safety trainer/consultant is not the best option. Due to travel restrictions and social distancing guidelines, bringing large groups of employees together for education purposes is a challenge! Hazards still exist in the work setting, and as a result, informing employees on how to recognize and control those hazards still needs to be accomplished and documented. All employees must be trained (and/or retrained) on some subjects. We will review those topics and some creative DIY options.
OSHA Required Safety Topics
Every employer must provide a place of employment free of recognized hazards, and every employee is required to comply with safety and health standards (OSHA Act). Every employee has to be informed about all hazards associated with their work tasks and how to control those hazards. Training is one portion of the overall safety and health program and cannot be neglected, even in these uncertain times.
Specifically, OSHA states that employees must be provided with: • Knowledge and skills needed to do their work safely and avoid creating hazards that could place themselves or others at risk. • Awareness and understanding of workplace hazards and how to identify, report and control them. • Specialized training, when their work involves unique hazards.
Keep in mind that federal OSHA is just one agency that may obligate your company to employee training. Other government agencies and state-based OSHA and/or safety/health regulations should also be reviewed for content specifications. Illustration one (page 14) lists the basic required training topics mandated by OSHA for every employer. Many readers will need to sift through the list to determine if those topics apply to their specific operations. For example, some readers may not have any “Permit Required Confined Spaces” in their building, or overhead cranes, but every reader here is likely to have both machine guarding exposures and forklift operations. The same is true of illustration two: List of Toxic and Hazardous Substances (page 15). Most employers will find at least one topic there that requires employee training. For
Many general industry employers are not aware that they may need to include construction safety topics, such as fall protection, in their employee training if their employees are engaged in the definition of “construction.” According to OSHA, construction is high hazard work that comprises a wide range of “activities involving construction, alteration, and/or repair.”
example, blood borne pathogens is a realistic exposure in most machine shop type operations, and almost all U.S. employers are required to address “Hazard Communication,” which includes Safety Data Sheets (SDS), labeling, training, and current chemical inventories. However, only a few Springs magazine readers may be exposed to lead or chromium VI. The key is to review the lists and determine which are site specific to your organization.
Many general industry employers are not aware that they may need to include construction safety topics, such as fall protection, in their employee training if their employees are engaged in the definition of “construction.” According to OSHA, construction is high hazard work that comprises a wide range of “activities involving construction, alteration, and/or repair.”
Laura Helmrich-Rhodes, CSP, Ed.D., is an independent regulations compliance consultant to the Spring Manufacturers Institute (SMI). A former member of PA/OSHA Consultation, she is an associate professor in the Safety Sciences Department at Indiana University of Pennsylvania where she teaches graduate and undergraduate classes on topics such as OSHA standards, safety communications, workers’ compensation and human relations. Rhodes is available for safety advice and information. Contact SMI at 630-495-8588 or laurahrhodes@gmail.com.
Construction workers engage in many activities that may expose them to serious hazards, such as falling from heights onto hazardous machinery, being struck by heavy construction equipment, electrocutions, silica dust and asbestos. It is possible that the average spring/wireform manufacturing worker might get pulled into construction work at their industry-based company. For example, interior construction projects, repairs or alterations may be taking place at your company. Any work that is unusual in nature is a higher hazard to workers, especially if it involves working at heights and outside their normal work activities. If shop employees are pulled into such activities, then they must receive construction safety training as well as their ordinary mandated industrial training topics.
The bottom line is that employee safety training has to be relevant to their job tasks. Decisions on the topics covered should reflect hazards and previous accident trends and how those can be prevented.
The Best Training Methods
Perhaps skipping a year of large group training is appropriate under the current conditions, so what other education methods might be considered? The key is to formulate meaningful objectives for what you want to accomplish. In other words, what exactly do you want employees to be able to do after the instruction? Assuring that the objectives were met, regardless of the instruction method, is paramount. Many positives have come out of the COVID-19 conditions. Perhaps one is that we think of new ways to accomplish tasks, and employee training is certainly one of those!
The instructional method used needs to assure that employees understand the material and will be able to
Exit Routes and Emergency Planning • Emergency action plans • Fire prevention plans
Powered Platforms, Manlifts and Vehicle-Mounted Work Platforms • Powered platforms for building maintenance
Occupational Health and Environmental Control • Occupational noise exposure
Hazardous Materials • Flammable liquids • Explosive and blasting agents • Storage and handling of liquefied petroleum gases • Storage and handling of anhydrous ammonia • Process safety management of highly hazardous chemicals • Hazardous waste operations and emergency response
Personal Protective Equipment • General requirements • Respiratory protection General Environmental Controls • Temporary labor camps • Specifications for accident prevention signs and tags • Permit required confined spaces • The control of hazardous energy (lockout/tagout)
Medical Services and First Aid • Medical services and first aid
Fire Protection • Fire protection • Fire brigades • Portable fire extinguishers • Standpipe and hose systems,
Fixed extinguishing systems, Fire detection systems • Employee alarm systems
Materials Handling and Storage • Servicing of multipiece and single-piece rim wheels • Powered industrial trucks • Overhead and gantry cranes • Crawler locomotive and truck cranes Machinery and Machine Guarding • Mechanical power presses • Forging machines
Welding, Cutting and Brazing • General requirements • Oxygen-fuel gas welding and cutting, Arc welding and cutting • Resistance welding
Special Industries (this is for a variety of business types—spring or metal forming is not specifically listed)
Electrical Safety-Related Work Practices • Training • Commercial Diving Operations • Qualifications of dive team
Toxic and Hazardous Substances (See separate list)
Construction Work (if being conducted on-site including Fall Protection)
Illustration 2: Toxic and Hazardous Substances (Subpart Z)
Training Topics • Asbestos • Carcinogens (4-Nitrobiphenyl, etc.) • Vinyl chloride • Inorganic arsenic • Lead • Chromium (VI) • Cadmium • Benzene • Coke oven emissions • Bloodborne pathogens • Cotton dust • 1,2-Dibromo-3-Chloropropane • Acrylonitrile (vinyl cyanide) • Ethylene oxide • Formaldehyde • Methylenedianiline • 1,3-Butadiene • Methylene chloride • Ionizing radiation • Hazard Communication • Occupational exposure to hazardous chemicals in laboratories
implement that knowledge. It goes without saying that training needs to happen in their primary language but understanding goes beyond language barriers.
Materials need to be easy to read and understand. The reading level and complexity of the language presented in handouts or posted materials should be considered. For example, printing out an OSHA standard and posting it is one method to inform employees, but many employees would not be able to follow, understand and most importantly implement the information. Creating a checklist or a handout with pictures or flow charts might be a great way to assure understanding regardless of literacy, cognitive hurdles or language barriers. A list of potential resources for quality safety training materials created by two different state consultation services are listed in the Helpful Websites on the next page. These include handouts, videos and even sample written programs that most Springs magazine readers need to have in place.
Being creative can help employees who learn differently truly enjoy the training events. Some may respond well to DVD/YouTube videos (visual and auditory learners), while some workers might learn best by obtaining a lockout procedure for a machine in his department, and then performing the task with their supervisor and discussing the process (kinesthetic learners).
WIRED FOR PRECISION
Unsurpassed Quality Since 1959
Swift Turnaround Times Award Winning Service Prototypes to Full-Run Production
Certified ISO 9001:2015
97 Ronzo Road, Bristol, CT 06010 | (860) 583-1305 | RadcliffWire.com
Being creative also means when and how often training events occur. For example, you might create a checklist of topics all employees must complete and provide multiple ways to accomplish the checklist. It could be online, handouts, one-on-one conversation with supervisors or even leading a toolbox talk in their department. Create a plan for when the training must be completed and be sure that any new employees are included in a very specific safety onboarding process. New employees should not be waiting months to receive their safety training.
Who Should Conduct the Training? The importance of your department supervisors and managers in your company’s safety effort, even in the best of conditions, cannot be overemphasized. It is true that these individuals are

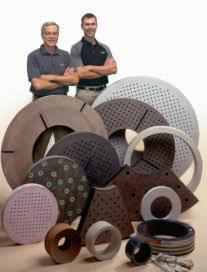
Leaders In Double Disc Technology
Jack and Jeff Shoemaker, second and third generations continuing the tradition at Anchor Abrasives. Certified to ISO 9001 since 1994.
At Anchor Abrasives we specialize in the design and manufacture of resin, epoxy and oxychloride bonded nut inserted discs and cylinders...plus centerless and rollwheels.
Today, in our modern manufacturing facility, we are ready to continue our tradition of innovative quality products and unmatched customer service. For more information contact Anchor Abrasives Company, 7651 West 185th Street, Tinley Park, IL 60477 U.S.A. Phone: 708-444-4300; Fax: 708-444-1300.
www.anchorabrasives.com often stretched to the limit. However, no one understands the work better or is more invested in the well-being of the workers. It doesn’t have to be a half-day Power Point. Checklists, handouts, JSA reviews and group discussions are all possible methods, but it is best if they are directed and overseen by department supervisors. If the organization has a safety committee, they could also be engaged in the creation and deployment of safety training materials. Don’t forget to document each training session with a sign-in sheet, along with what was covered and who attended.
It is important for supervisors and managers to explain the process for reporting safety and health concerns, as well as injuries and illnesses. This is a prime opportunity to build a safety culture without fear of retaliation. Getting employees engaged in safety is a key to success, and perhaps the COVID-19 conditions provide the perfect opportunity to show them just how much you care with a twist of ingenuity! n
Helpful Websites
Recommended Practices Education and Training
https://www.osha.gov/shpguidelines/educationtraining.html
Job Hazard Analysis (an important and often overlooked training tool)
https://www.osha.gov/Publications/osha3071.pdf
Recommended Practices for Safety and Health Programs (booklet)
https://www.osha.gov/Publications/OSHA3885.pdf
OSHA Training Tools
https://www.osha.gov/training/library/
OSHA Lockout Tagout Online Tutorial
https://www.osha.gov/dts/osta/lototraining/ index.html
PA/OSHA Consultation Focal Point Series (free training materials including videos)
https://www.iup.edu/pa-oshaconsultation/ focal-points/
Model Safety and Health Written Programs
https://alabamasafestate. ua.edu/safety-consultation/ model_safety_and_health_programs/