
4 minute read
Flashback
Parts Forming Machines — 1960/1970
(Editor’s note: In this edition of Flashback, we rewind to the October 1971 issue of Springs. As this current issue is devoted to the topic of plant industrialization, this article describes the landscape of new forming machines from 50 years ago designed to help springmakers improve their methods and processes. To make these improvements, the dilemma has always been and continues to be: how to design one machine that meets the needs of all springmakers.) In the United States, the early sixties promised a rebirth of the American spirit on all fronts. As a nation, we were wrestling with data processing and computers, soaring into space, strengthening the technical domains of our educational systems, and gearing our attitudes for the new tomorrows. Machine tool sales and marketing experts were gaining rapidly on the technical problems associated with numerically controlled machines, but couldn’t overcome the “Return on Investment” arguments.
We in the metalforming machinery building business were also exploring. Market requests were many and varied. Let’s consider some: • Automatic looping devices were needed to reduce labor costs. • Coilers and torsion winders needed redesign to reduce the level of setup skills presently required. • Automatic gaging with feedback was needed to reduce scrap and operator costs. • Compensation for material variations was needed. Feed, diameter and pitch tolerances would have to be held more closely. • More tonnage and stroke length were needed on fourslides. The list was longer, but I haven’t yet touched upon the real problem faced by machinery builders. Here it is. How does one provide the answer to ABC company’s needs that also meets the requirements of XYZ’s with a single machine or manufacturing concept?
This question, if applied to nearly all of the above listed market requests, would clearly explain why 1971 arrived without answers to all of the above listed problems. However, here are some of the answers that were provided: • In spring looping, there were several combination coiler loopers introduced with varying degrees of sophistication.
The conceptual effort employed here was directed toward dropping the spring completed to spec with minimum handling. An entirely different concept separated the coiler from the looper to allow optimum performance of each unit with minimum handling when used with an automatic feeder.
Both systems worked and offered the marketplace a choice. • In torsion winders, there were two major domestic efforts made. One offered a completely new design of a machine capable of extending all the previous specifications with better secondary capabilities on the machine. • Another company offered a numerically controlled torsion winder also capable of extending previous specs with improved secondary capabilities on the machine. The numerically controlled advantages permit setup with reduced skills but at a higher initial cost.
Again, the market had a choice. Coiler buyers had newcomers to consider. From England came a new coiler utilizing both forward and reverse strokes of the crank mechanism. From Italy came a new coiler with continuous feed embodying a flying cutoff and, naturally, high production speeds. In the United States, we introduced new sizes and new attachments designed to extend the universal coilers versatility. We improved materials and manufacturing tolerances for better life and precision. Adaptive controls offered both by machine manufacturers and independent suppliers added to the buyer’s confusion, especially in companies employing their own designs. As 1970 closed, a new domestic coiler appeared with the intent of offering advantages in versatility and ease of setup.
Fourslide manufacturers were very active during this period, oftentimes going in seemingly opposite directions. Let’s look at the results: • New massive horizontal fourslides appeared for the first time. • A large new vertical fourslide was introduced to automated assembly lines and parts production. • New designs of very small fourslides competed vigorously for electronic parts production. • A principal manufacturer of lower priced machines introduced the first line of higher priced versions. • A principal manufacturer of higher priced machines introduced the first of a line of lower priced designs. • A principal manufacturer of horizontals, in an apparent attempt to please both vertical and horizontal proponents, offered an adjustable angle design. • Several European companies offered vertical designs with slides adjustable in a circular path. The intent here is to reduce tooling complexities by rearranging slides to best suit the part geometry. Adaptation of fourslides into new concepts of manufacturing by combining forming with both resistance and electronic beam welding have effectively reduced parts costs. The market again was offered a choice.
Additionally, new devices for secondary forming, load testing, stress relieving, wire payoff, hopper feeding, etc., have been employed with varying degrees of success.
Where are we, where will we go? Our market is still concerned with versatility, cost, ease of setup, extended specifications, reduced secondaries, cost of tooling, reliability, durability and all the others. Machinery builders will continue their best efforts to supply equipment answers to these demands. n
PTC - Pretension Control INTERNATIONAL PATENT HIGH SPEED CNC COILERS
FX 5 Ø 0.10 - 0.80 FX 10 Ø 0.15 - 1.10 FX 15 Ø 0.25 - 1.50 FX 30 Ø 0.40 - 3.00
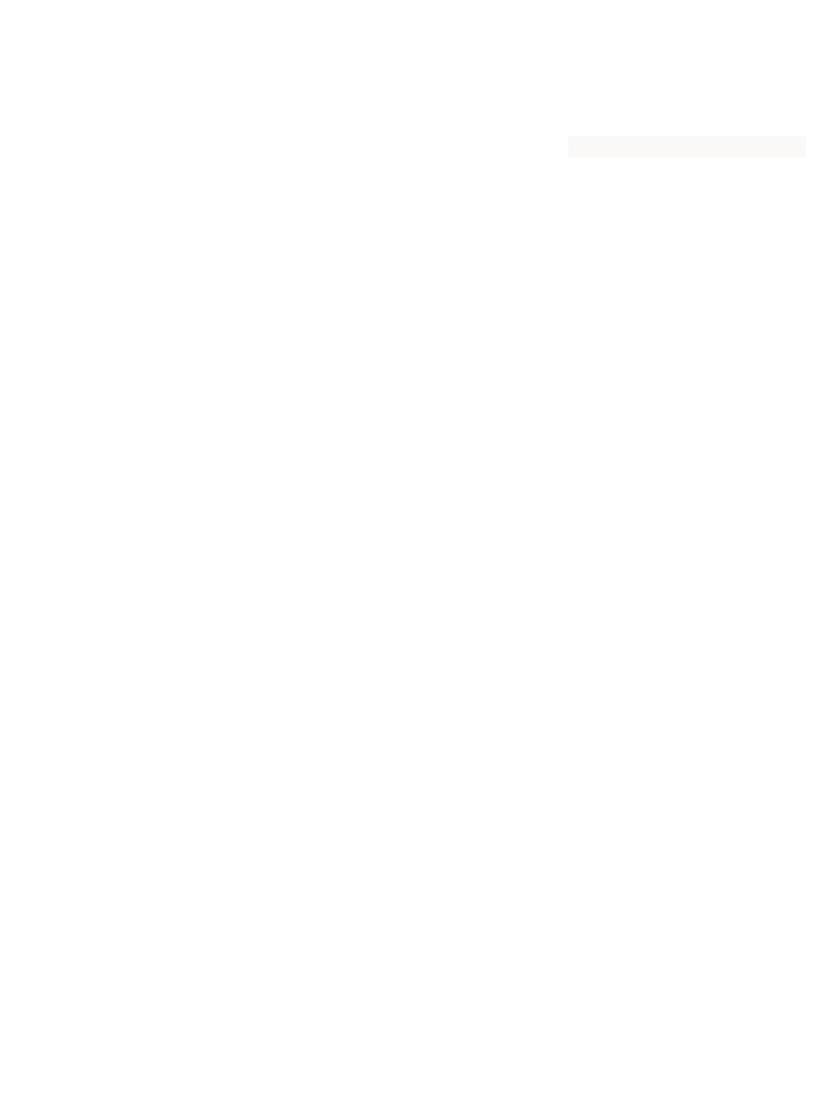



MILANO - ITALY NIMSCO LLC North American distributor 5115 B Tremont Ave. Davenport, IA 52807 Ph: 563-391-0400 Fax: 563-391-0403 i in nf fo o@ @n ni im ms sc co o. .c co om m
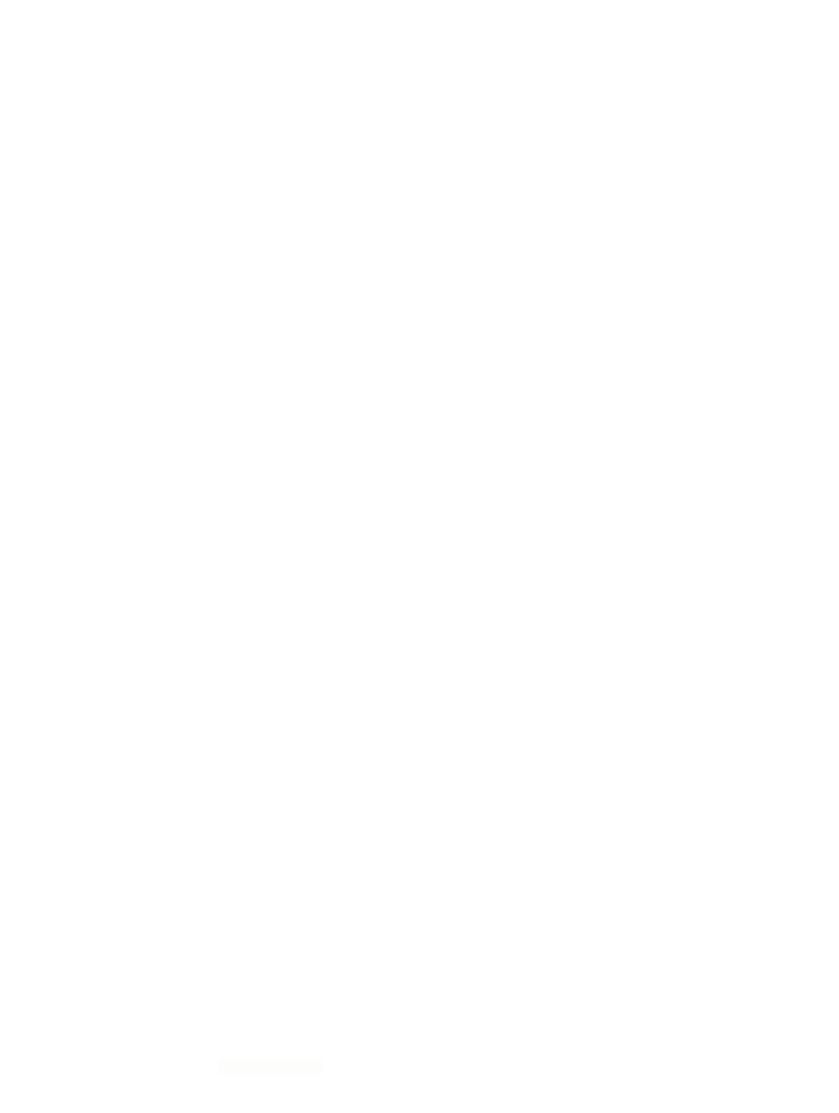

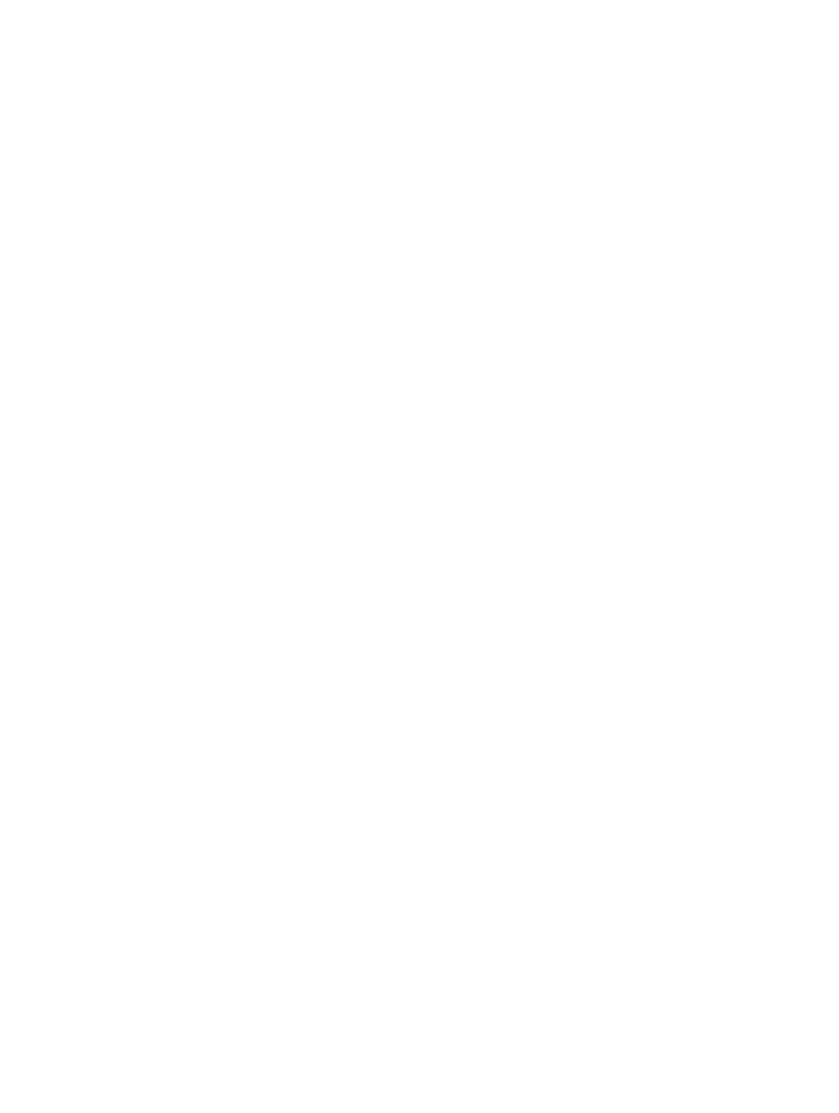
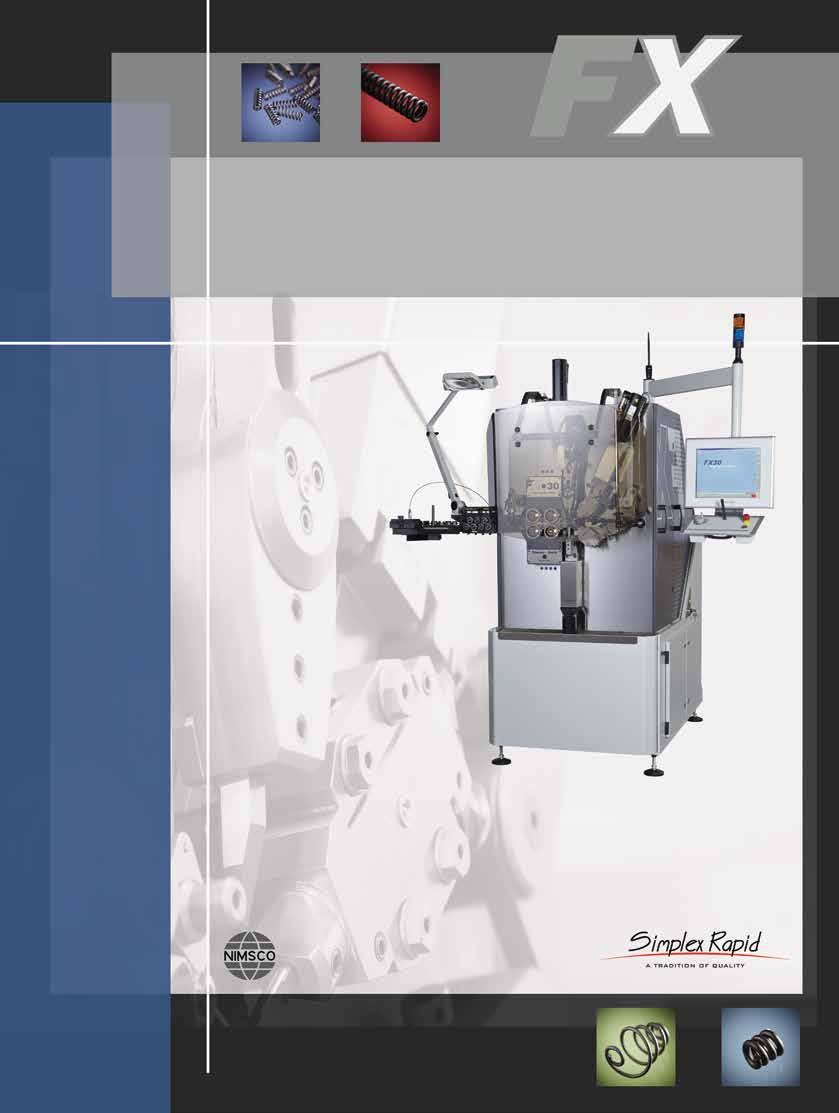