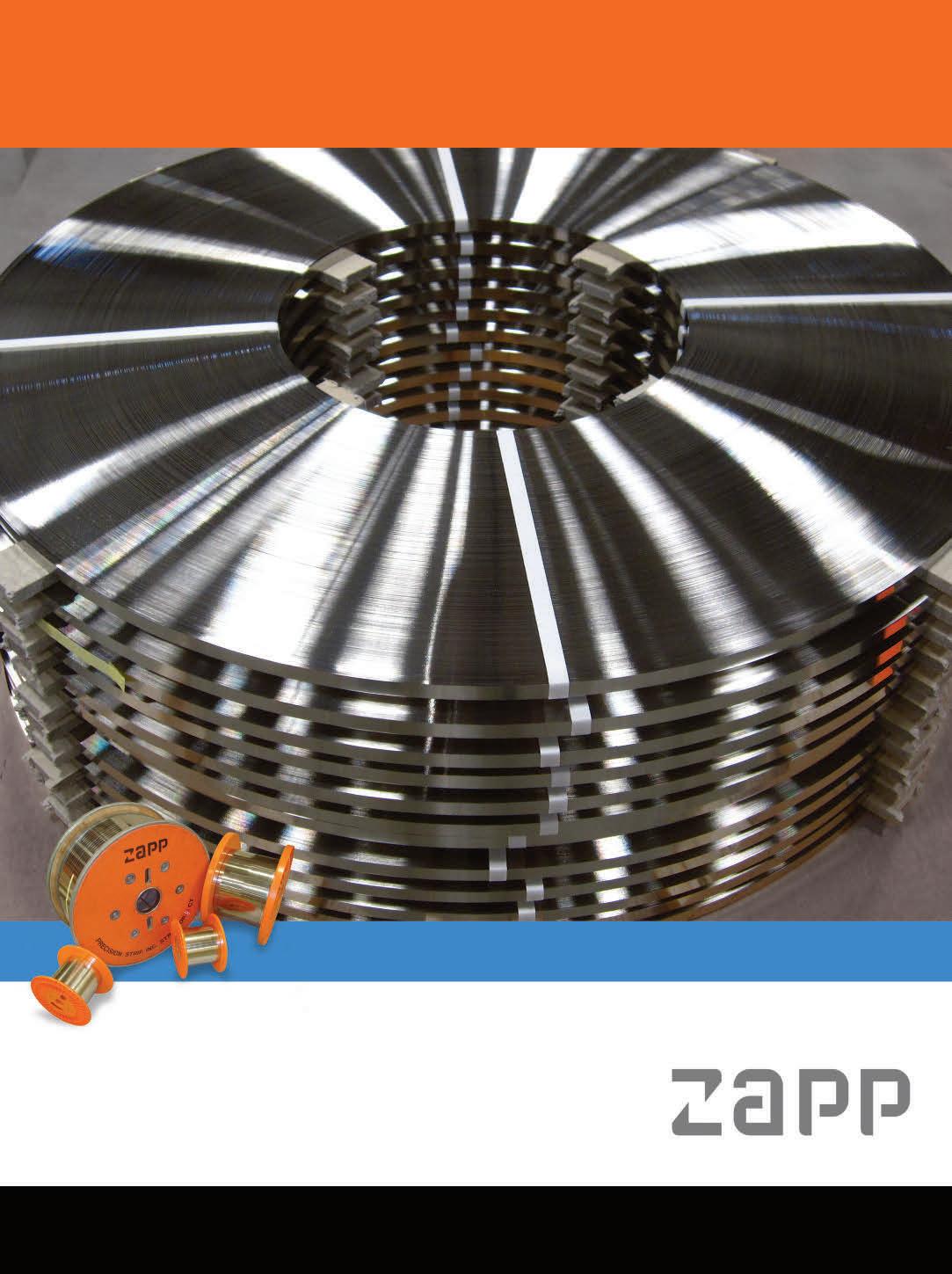
6 minute read
Be Aware Safety Tips
How Much Can an Employee Safely Lift?
By Laura Helmrich-Rhodes, CSP, Ed.D.
Afrequently asked question is, “How much can we ask an employee to lift?” As with many safety and health questions, the answer is not simple. The good news is there are several resources available to help you answer this question.
Seeing the total cost of potential injury is one incentive to help you assess and change job operations for prevention. The most recent publication of workers’ compensation costs by the National Safety Council showed that low back injuries cost American business on average $32,882. There is an additional cost of $61,510 for neck injuries. According to EHS Today, in 2019, “overexertion injuries accounted for nearly $14 billion annually in lost time, insurance and medical bills.” We should not overlook the potential for a dropped object (for example, a box of completed springs or wireforms ready for shipment) on a foot or leg, which account for more direct medical cost and potential lost time. Certainly, the cost of lost product in the precision spring industry due to drop/ loss of load should be a motivating factor in streamlining your material handling operations.
Can you be cited by the Occupational Safety and Health Administration (OSHA) for manual movement of heavy objects? It depends! If the company is located in a state-run OSHA program, and an ergonomics standard exists, then a company can be cited. In states under a federal OSHA plan, it is a bit more complex for the compliance officer to have the violation hold up in court. These fall under the General Duty Clause of the OSHA Act, which is very broad but has specific qualifications for use. Section 5(a)(1) of the Act says:
“Each employer — shall furnish to each of his employees employment and a place of employment which are free from recognized hazards that are causing or are likely to cause death or serious physical harm to his employees.”
The key here is “recognized.” A reasonable person knows that lifting excessive weight repeatedly will likely lead to injury. Compliance, workers’ compensation cost containment and moral obligation all make this a worthy investment in the time it takes to assess and possibly change company work processes.
There are many factors when eliminating back injuries due to lifting beyond the weight of the object(s). OSHA (in a Letter of Interpretation dated May 4, 2015) suggests the following minimum considerations: • How often (frequency) is the employee lifting something. • Whether the employee must bend or twist while lifting. • How high an object is lifted. • Where the origin of the lift occurs; specifically, whether it is below knuckle height.
Laura Helmrich-Rhodes, CSP, Ed.D., is an independent regulations compliance consultant to the Spring Manufacturers Institute (SMI). A former member of PA/OSHA Consultation, she is an associate professor in the Safety Sciences Department at Indiana University of Pennsylvania where she teaches graduate and undergraduate classes on topics such as OSHA standards, safety communications, workers’ compensation and human relations. Rhodes is available for safety advice and information. Contact SMI at 630-495-8588 or laurahrhodes@gmail.com. • Whether the employee must hold the object away from the body while lifting. • How long (time) the employee must lift or hold the object.
There are several sources available to help assess your job tasks. One is to use the Job Safety Analysis (JSA) discussed many times in previous “Be Aware” columns. This tool can be used to eliminate unnecessary lifting, moving, and increase overall efficiency in the work area. By breaking the job down into steps, it is easy to eliminate or change the way work is done to prevent injury and save time. This tool can help to pinpoint areas where engineering controls such as mechanical assistance or self-leveling carts might be considered. If your company is not using JSAs and needs help implementing this tool, please contact me for help.
The best resource for calculating lifting capacities is to turn to the National Institute for Occupational Safety and Health (NIOSH), the research branch of OSHA. They developed a mathematical model that helps predict the risk of injury based on the weight being lifted and other criteria mentioned. This equation has been revised as new information has emerged in the area of ergonomics. Keep in mind that research findings and guidelines published by NIOSH become “recommended practice,” not an OSHA regulation, until it is formally promulgated as a federal (or state) standard. Years ago, OSHA did attempt to establish a federal ergonomics standard. To make a long story short, the standard was passed by OSHA, but later repealed by Congress. It makes for a great history lesson for safety or law students, but is beyond the scope of the question at hand: How much can I ask an employee to lift?
The NIOSH lifting equation calculates a recommended weight limit for one person under different conditions. The
revised Recommended Weight Limit is calculated using the following equation:
RWL= LC x HM x VM x DM x AM x FM x CM
Where:
LC= Load Constant
HM=Horizonal Multiplier
VM=Vertical Multiplier
DM=Distance Multiplier
AM=Asymmetric Multiplier
FM=Frequency Multiplier
CM =Coupling Multiplier
The lifting equation establishes a maximum load of 51 pounds, which is then adjusted to account for how often (frequency) an employee lifts, twisting (asymmetric) the back during lifting, the vertical distance the load is lifted, the distance of the load from the body, the distance needed to move while lifting the load, and how easy it is to hold on to (coupling) the load. It is clear from this discussion that an employer cannot simply use the 51 pounds as their threshold. Each lift is different and needs to be assessed. NIOSH estimates a typical recommended weight limit for a task where employees must repeatedly lift loads and place them to lower locations, where torso twisting may be required, is about 8 to 12 pounds. Again, each job needs to be assessed using the equation if a more exact weight is desired.
The advancement of computers and now phone-based apps make this assessment much more manageable than years ago. The NIOSH lifting equation is explained in detail on their website and includes a free downloadable app from Google or Apple iTunes https://www.cdc.gov/niosh/ topics/ergonomics/nlecalc.html
There are other free or low-cost sources available to help you eliminate lifting risks in the workplace. Workers’ compensation loss control representatives or ergonomic specialists may help you conduct a risk assessment at little or low cost. It is in the compensation carriers’ best interest to eliminate hazards, so they are often open to these requests.
The state bureau of workers’ compensation may also provide help to employers. For example, the Ohio Bureau of Workers’ Compensation has a calculator for assessing risk levels associated with lifting various weights, which is available at https://info.bwc.ohio.gov/wps/portal/ gov/bwc/for-employers/safety-and-training/safety-education/Lifting-guidelines The Washington State Department of Labor and Industry and the Oregon State Safety and Health Division have, jointly, developed a calculator for analyzing lifting tasks, based on the NIOSH lifting equation, which is available at https:// osha.oregon.gov/OSHAPubs/apps/liftcalc/lift-calculator.html
Also, WorkSafeBC (British Columbia) often has excellent safety resources. They include easy to understand illustrations for measuring lifting risks and infographics to use in safe work practice decision making. The information provided would also make excellent training materials for supervisors to discuss proper lifting with their departments.
The potential OSHA citation should not be the only impetus for risk assessments, especially for lifting. There are many factors that may change which can make an object safe to lift at one time but could cause serious injury another time. The great news is there are many people and technical resources available at low or no cost to help eliminate this common hazard. n
Helpful Resources For Assessing Lifting
National Safety Council Injury Facts — graphic overview of Workers’ Compensation Costs https://injuryfacts.nsc.org/work/costs/workers-compensation-costs/ NIOSH Manual for the Application of the Revised NIOSH Lifting Equation https://www.cdc.gov/niosh/docs/94-110/pdfs/94-110.pdf?id=10.26616/ NIOSHPUB94110
NIOSH Ergonomic Guidelines for Manual Material Handling (includes, pictures, assessment tools and recommendations for changes) www.cdc.gov/niosh/docs/2007-131/pdfs/2007-131.pdf OSHA www.osha.gov/SLTC/ergonomics/index.html Manual Lifting Risk Assessments: Use the Right Tool for the Job (article, excellent information for anyone performing the assessment at your facility) EHS Today, Retrieved 7/19/2021 https://www.ehstoday.com/health/article/21920427/ assessing-manual-lifting-risk-use-the-right-tool-for-the-job WorkSafeBC: Making It Right: Preventing Musculoskeletal Injuries in Manufacturing https://www.worksafebc.com/en/resources/health-safety/books-guides/ making-it-right-preventing-musculoskeletal-injuries-msis-in-manufacturing? lang=en WorkSafeBC Lift/Lower Calculator https://www.worksafebc.com/en/resources/health-safety/interactive-tools/ lift-lower-calculator?lang=en&origin=s&returnurl=https%3A%2F%2Fwww. worksafebc.com%2Fen%2Fsearch%23sort%3DRelevancy%26q%3DLiftin g%2520%26f%3Acontent-type-facet%3D%5BInteractive%2520tools%5D %26f%3Alanguage-facet%3D%5BEnglish%5D&highlight=Lifting
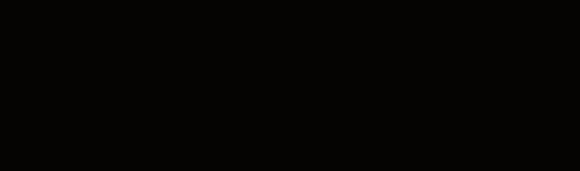