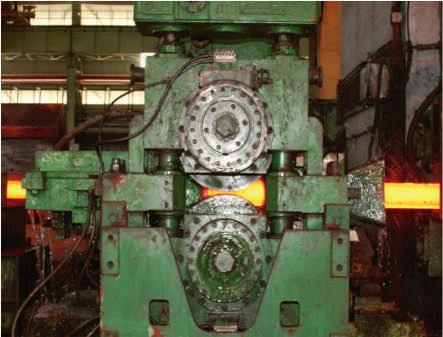
7 minute read
Technically Speaking
Advances in Springmaking Materials — Part 2: Rod Rolling
By C. Richard Gordon
(Editor’s note: Rick Gordon’s article was developed as part of the overall theme of “Advances in Springmaking.” This is the second in the series articles on advances in springmaking materials. Additional articles on wire drawing and heat treating are planned for future issues of Springs.)
Advances in the production of springmaking materials over time have resulted in improvements in spring performance. Since the majority of springs are produced from carbon and alloy steels, production methods of these materials will be described here.
Production improvements have occurred in the areas of steelmaking, continuous casting, rod rolling, wire drawing and wire processing (heat treatment). Improvements in springmaking machine technology were discussed previously1. Improvements in the areas of steelmaking and continuous casting were also discussed previously2 .
Materials Design Philosophy
In the Fall 2019 issue of Springs3, I discussed the relatively simple engineering concept known as the materials design philosophy, which can be used as a tool to better understand compositionproperty relationships. Briefly, the materials design philosophy shows the relationship between the composition of the material and the final product properties (Figure 1).
A material with a specific composition is processed in a given operation. The combination of the material and the processing results in a particular structure (metallurgical microstructure). The microstructure in turn results in the specific material properties. In reality, the process of design occurs from right to left. Engineers are interested in specific material properties, which in turn are dependent on the structure, which is a function of designed processing of a material with a specific composition.
Material properties such as tensile strength and ductility are determined through mechanical testing, which have been discussed in past Springs articles4,5,6,7,8,9 .
For the purpose of this article, Figure 2 shows an expansion of Figure 1 which includes our process of interest: rod rolling. From a materials perspective, a goal of any process improvement is to improve the uniformity of the product as well as enhance product properties. From an operations perspective, a goal is to improve productivity with the attendant reduction in cost.
Composition Processing Structure Properties
Figure 1. Materials Design Philosophy
Thus, the challenge is to obtain both the materials goal and the productivity goal; how to achieve the balance is a subject beyond the scope of this article.
In this article, only the rod rolling process is discussed.
Rod Rolling
In the past, billets used to hot roll wire rods were produced from steel cast into ingots. Ingots were rolled to billets, which were subsequently rolled to rods. Today, essentially all steel is produced using the continuous casting process. For the highest quality high carbon wire products, such as valve spring quality wire, continuously cast blooms are rolled to billets. Billets are then subjected to surface inspection and conditioning prior to rolling to wire rods10. These steps are aimed at producing wire rods with the highest level of surface quality.
Over time, there has been a dramatic improvement in hot rolled steel wire rod processing speed due to equipment improvements. This has resulted in new modern single strand wire rod mills replacing older mills with four strands. A top finished rolling speed of 110 mps (21,654 fpm) is routinely achieved.
Converting billets into wire rod is an extremely complex process that requires excellence in a multitude of areas to consistently manufacture high quality finished products11. An excellent article is included as reference 11, which describes many of the improvements made in rod mill rolling equipment and operating practices which can be utilized for superior product production.
Rick Gordon is the technical director for SMI. He is available to help SMI members and non-members with metallurgical challenges such as fatigue life, corrosion, material and process-related problems. He is also available to help manage and oversee processes related to failure analysis. This includes sourcing reputable testing labs throughout North America, forwarding member requests to the appropriate lab and reporting results and recommendations. He can be reached at c.richard.gordon@gmail. com or 574-514-9367.
Composition Processing
Figure 2. Materials Design Philosophy — Expanded • Rod Rolling • Austenite • Pearlite • Ferrite • Bainite • Martensite • Tensile Stregth • 0.2% Offset Yield Strength • % Elongation • % Reduction of Area
Structure Properties
From the metallurgical perspective, control of microstructure (including the high temperature austenite phase in hot rolling and subsequent desirable transformation products which form during cooling) is of paramount importance to assure uniformity throughout a rod coil and around each rod loop. Variation in mechanical properties is typically related to uneven heating in the furnace or nonuniform cooling.
An overview of the steel wire rod rolling mill process is shown schematically in Figure 3.
Several key areas cited include:
Billet Reheating Furnace
Improved instrumentation for furnace atmosphere and temperature control have been developed in order to minimize decarburization and variation in mechanical properties related to uneven billet heating.
Rolling Mill
Figure 4 shows a typical rolling mill stand used in the production of hot rolled wire rod.
Pre-finishing Block
The pre-finishing block is an option that has been included in some modern rod mill installations. Sometimes described as a second intermediate mill, it utilizes mini-blocks using carbide rolls with good section control.
Finishing Blocks/Reducing/Sizing Block
The reducing/sizing block is another option that has been included in some modern rod mill installations. Product size and shape control are improved as a result.
For the most part, hot rolled wire rod is produced in sizes down to 5.5 mm. Some installations are now in place for producing wire rod down to 4.0 mm13. The smaller wire rod diameter offers the potential for faster cooling rates with resultant improved mechanical properties (higher tensile strength). Through the use of these products, drastic reductions in many secondary processes can be realized. The resulting benefits for customers may be recognized particularly in manufacturing of smaller drawn wire sizes.
Billet Reheating Furnace
Rolling Mill
Waterbox Cooling
Laying Head
Stelmor Conveyor Roughing Stands 1st Step Intermediate Stands 2nd Step
Pre-Finishing Block Finishing Block 3rd Step
Reducing/Sizing Block
Figure 3. Key elements of the steel wire rod rolling process.
Water Box Cooling
Water cooling for control of rod temperature is essential for uniform microstructure and the correct scale formation (composition), depending on the planned scale removal requirement (chemical descaling or mechanical descaling).
Stelmor Conveyor
Conventional Stelmor lines have used air for cooling. Figure 5 shows a typical Stelmor cooling conveyor.
New designs have been introduced for air flow and distribution, resulting in improved mechanical property uniformity. Nippon Steel Corporation developed a Stelmor cooling line with a two-step cooling process using molten salt (DLP) capable of producing microstructures and mechanical properties in hot rolled wire rod equivalent to lead patented material14. The DLP process will be discussed further in the article on heat treating.
Process Control / Instrumentation
Developments in sensor technology and the ability to process large amounts of data in real time are the promises for the future. Currently, online laser gauge instrumentation for size and shape measurement as well as eddy current instrumentation for surface imperfection detection have enabled operators to make real time decisions and adjustments, resulting in improved product quality.
Summary
Improvements in the quality of hot rolled wire rod, including improved dimensional control and uniformity of mechanical properties, offers the potential for improved quality of wire for springs.
In a nutshell, that is a good thing. n
Figure 4. Rolling mill stand with stock (moving right to left)12 . Figure 5. Hot rolled wire rod being deposited on a Stelmor cooling line (Photograph courtesy of Charter Steel).
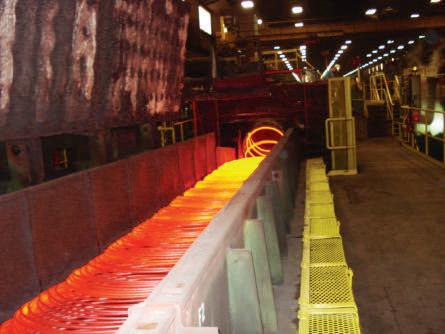
References
1. McCoy, G., Advances in Springmaking,
Springs, Spring 2021, p. 23. 2. Gordon, C.R., Advances in Springmaking Materials,
Springs, Spring 2021, p. 30. 3. Gordon, C.R., Springmaking Materials/Materials Design
Philosophy, Springs, Fall 2019, p.23 4. Gordon, C.R., Types of Tests Used to Characterize Springmaking
Materials — Part 1: The Tensile Test, Springs, Winter 2020, p.27 5. Gordon, C.R., Types of Tests Used to Characterize Springmaking
Materials — Part 2: The Coiling and Wrapping Tests,
Springs, Spring 2020, p. 27. 6. Gordon, C.R., Types of Tests Used to Characterize
Springmaking Materials — Part 3: The Torsional Ductility Test,
Springs, Summer 2020, p.17. 7. Gordon, C.R., Types of Tests Used to Characterize Springmaking
Materials — Part 4: Hardness Testing, Springs, Fall 2020, p.19. 8. Gordon, C.R., Types of Tests Used to Characterize Springmaking
Materials — Part 5: The Reverse Bend Testing,
Springs, Winter 2021, p.19. 9. Gordon, C.R., Types of Tests Used to Characterize Springmaking
Materials — Part 6: Fatigue Testing of Wire,
Springs, Summer 2021, p.21. 10. ASTM A877 / A877M-17, Standard Specification for Steel Wire,
Chromium-Silicon Alloys, Chrome-Silicon-Vanadium Alloy
Valve Spring Quality, ASTM International, West Conshohocken,
PA, 2017, www.astm.org 11. Gordon, R., Yalamanchili, B., Power, P., Cunha, L., Boudreaux, T.,
Kiefer, B., Krejdovsky, W., “Meeting Customer Demand for Rod
Qualities Through Improvements in Operating Practices and Rod
Mill Equipment,” WJI, Nov. 2016, p52. 12. Kiefer, B.V., The Two-roll Rolling Process for Long Products,
Wire Journal International, February 2016, p. 136. 13. https://www.nipponsteel.com/en/steelinc/product/xsteelia/ small_diameter.html 14. H. Ohba et al., High-Performance Wire Rods Produced with
DLP, NIPPON STEEL TECHNICAL REPORT, No. 96, July 2007.