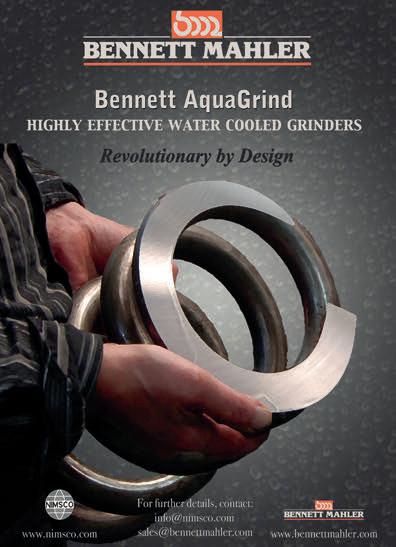
2 minute read
Dean of Springs
What Are the Causes of Spring Tolerances?
By Dan Sebastian
One main issue in springmaking has been the use of commercial tolerances for springs. It is worth looking at the origin of the published data. Some of the first tables were presented in 1944, when A.M. Wahl copyrighted his book “Mechanical Springs.” In his book, which continues to be one of the most used references in the spring industry, Wahl presented some tables that were developed by Westinghouse Electric’s research and development center. In subsequent years, empirical data from a research team at Associated Spring augmented the original data.
The original tables were segregated based on key design variables. The tables were later converted into an algorithm. These key variables included:
d = wire diameter C = index D = mean diameter N = number of coils
The basic variables fit neatly into mathematical modeling. In basic predictability, there are other factors that contribute to variability that cannot be modeled. Among these are the material, the equipment used and the quality of the setup. The good news is the empirical data established a basic standard with the equipment and setup quality that was within the best industry standards. The material was from a limited number of sources. The actual data collected was then evaluated and reported after applying a statistical confidence factor.
The material may be one of the most significant factors in any specific design and setup (that is why we do process capability studies on each setup). Early in my career, I worked at one of the greatest statistical laboratories in the spring industry, a plant that made high-volume engine valve springs. Our studies uncovered real differences between material suppliers with regard to meeting tolerances. Some of the differences were so significant, they impacted our procurement practices (price is not the only factor). These differences forced us to look more carefully at the material by looking at factors that go beyond the traditional specifications.
One of the things we discovered was the cast in the wire; the curvature and the pitch had a significant effect on the tolerances. You can see this phenomenon by cutting a few coils loose and letting them set on the floor. You will see what looks like a snake coiled up. This appeared to be related to the material packaging at the mill. A secondary material factor that impacted the tolerances was the roundness.
Another factor causing tolerance variation was the distance from the coiling point to the unspooling reel. The distance must be sufficiently large to compensate for the torque created in the coiling process, allowing it to be dampened.
The original tables and the subsequent algorithms used were from empirical data which had variation from the material and equipment/setup built in. The factor that was designed to give +/- 3 sigma capability was the basis for the “standard tolerances.” Most springmakers can easily manufacture within the standard tolerance band, but the standard was for all. After accounting for the natural variation based on geometry, material becomes a significant source of variation. In any manufacturing process, the use of statistical controls will assure that quality and adherence to specified tolerances is maintained. n
Dan Sebastian is a former SMI president and currently serves as a technical consultant to the association. He holds a degree in metallurgical engineering from Lehigh University and his industry career spans more than four decades in various technical and management roles. He may be reached by contacting SMI at 630-495-8588.