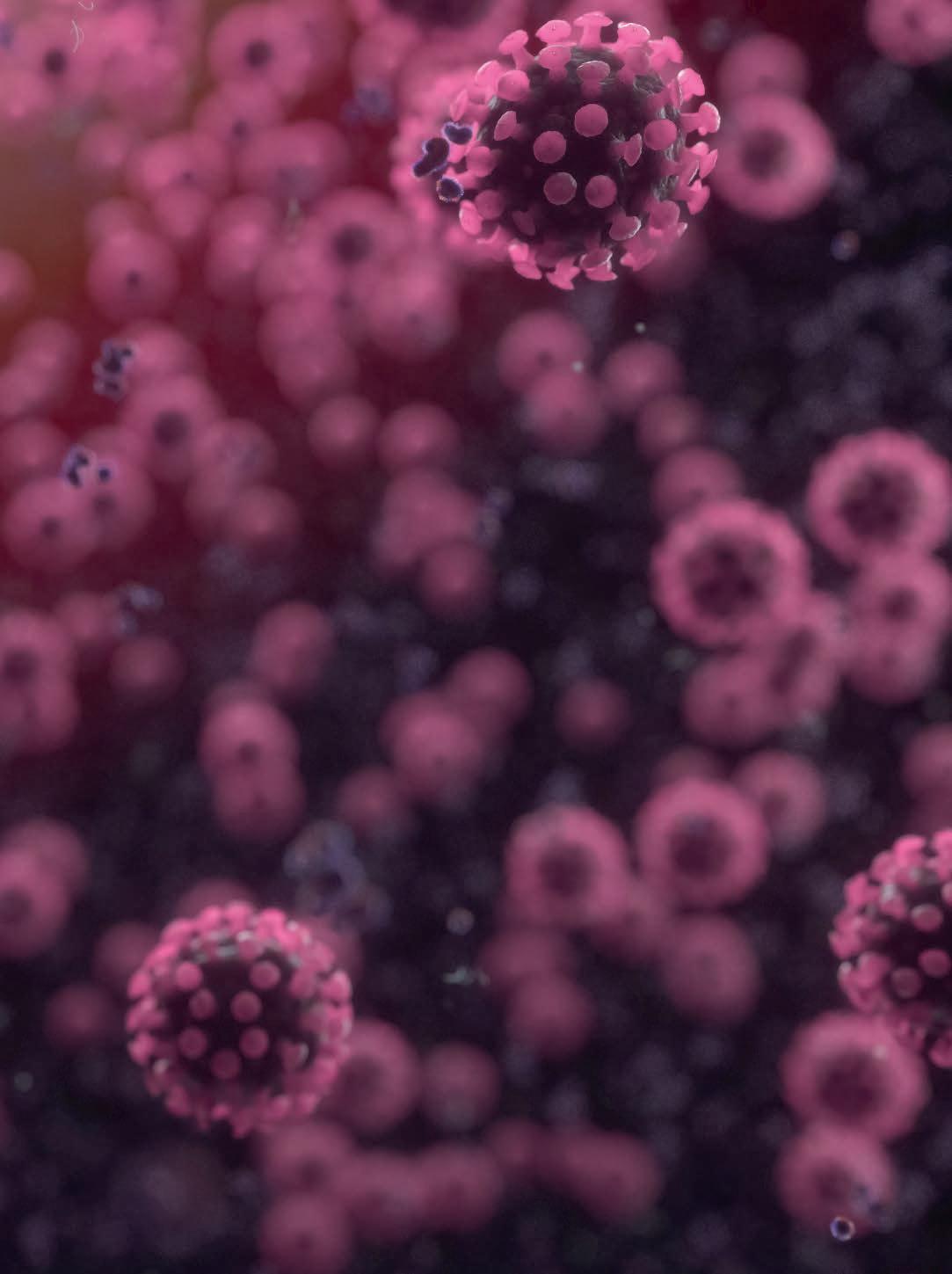
16 minute read
COVID-19 and the Spring Industry
The novel coronavirus (COVID-19) has touched virtually everyone’s way of life both personally and professionally. The spring industry is no different.
At the beginning of May, SMI reached out to members with a short survey to assess the impact of the COVID-19 pandemic. This story is not meant to be an exhaustive report. It is a snapshot at a moment in time. The final chapter of the story is yet to be written. With the uncertainty of this pandemic, no one can safely say when that date will arrive.
I agree with the sentiment in an editorial piece about COVID-19 written by Jonah Goldberg and published in the Chicago Tribune April 24. The head line got to the essence of his thesis that our shared experience with the pandemic will change us in countless ways. As Goldberg writes at the end of his article, “There are far more unknowns waiting for us in the years ahead, because we’re about to enter a new era when every single American can start a conversation by asking ‘What did you do?’, or ‘What happened to you when?’” Here is a look at how the pandemic has changed the spring industry so far.
Impact
The first question in our survey asked,
“How has the coronavirus impacted your business?”
For most springmakers, the impact has been dramatic. Typical of the answers was one from Michael Johnson at Spiros Industries, who said, “Sales revenue impact is severe; we are shipping roughly 30 percent of our normal volumes.”
Kurt Witham at AIM said, “The state of Michigan suspended work for nonessential businesses in mid-March. Because we serve essential businesses such as defense and medical device with equipment, we were justified in continuing operations. Thirty percent of our staff were uncomfortable with COVID-19 in the work environment and chose to stay home with unemployment compensation.” Witham was hopeful that AIM would be back in full force by May 15.
Jim Rudolph at ASW Pengg, LLC commented, “We have been deemed essential and continue to produce wire,
How has the coronavirusimpacted your business?
but we are seeing a significant drop off in orders and many move outs of orders as well.”
At Industrial Spring of St. Louis, Inc., Sean Doyle reported that business is down 20 percent.
Without citing a percentage, Andrew Kattula of J&J Spring Enter prises, LLC said, “We have seen a slow up in demand of quantity across almost all industries, but part numbers are moving consistently.”
Rick Richter at R-R Spring Corporation said, “With some of our largest customers being closed, our incoming work is down 14.4 percent and sales for April are down 31.4 percent.”
At Dayco in Roseville, Michigan, Felix Buccellato said the company has experienced a drop in customer demand. “Due to this reduction, we reduced many of the employees to 32 hours per week.”
In a note of optimism, Dave Deerwester at The Yost Superior Co. exclaimed, “We are open! That is very good news, and most important, we are designated as essential manufacturing.”
Deerwester said keeping up with the “orders” is time-consuming and a drain on productivity. “After six weeks of
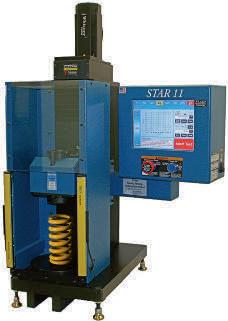
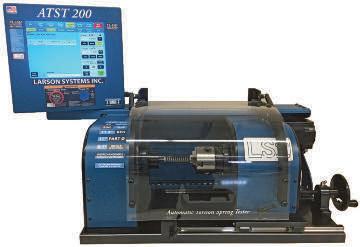
Keeping Employees Safe

One SMI member came up with a product to help protect employees during the COVID-19 pandemic.
R. Hale Foote at Scandic Springs in San Leandro, California worked with one of his employees to produce the “No-Touch Door Opener.” He said they manufactured the opener on the company’s waterjet machine to give away to employees and family members.
“The idea behind this was to keep our employees safe, so they can open a door without having to touch it,” explained Foote. “It was also meant as a reminder to our employees that things have changed.”
Does he have any plans to sell this product? “51 years as a job shop, and finally we have a product,” he said with a laugh. “As great of an idea that this product is, and I’ve seen people selling them on the internet for as much as $25, we have no plans to market this.”
He added, “My smart daughter-in-law found that it also opens beer bottles!”
disinfecting three to four times per day, we now have to wear masks. Our incoming orders dropped about 20 percent in April; this could be a tough summer.”
“FENN has been fortunate during this time, being able to remain open,” said Ryan Cutter at FENN-Torin. “Many of our office personnel are able to work from home. FENN’s shop operations, spare parts and service departments are doing everything they can to remain safe while continuing to work and meet customers’ production demands.”
Keeping Workers Healthy
Former SMI president Reb Banas of Stanley Spring & Stamping said the company’s Florida division, Stanron Steel Specialties, had to completely shut down for two weeks after an employee tested positive for COVID-19. That facility is back up and running, and Banas says overall sales have dropped by 25 percent due to customer reschedules and canceled orders.
Banas said Stanley Spring & Stamping has repositioned key employees “who are willing to do anything to help,” to assist with multiple operations. He said the company has also initiated capital improvements and upgrades by utilizing employees with available extra time.
Bill Lathrop said Hardware Products in Chelsea, Massachusetts is an essential business due to the customer base it serves. Lathrop says the company’s
operations have continued through the state of Massachusetts shutdown period.
“However, the challenge has been keeping the employees healthy and feeling safe at work,” explained Lathrop. “Some stayed away due to underlying conditions, others because of highrisk family members in the home and some with symptoms that later tested negative, and even a couple of positive COVID tests.”
Companies tied to the automotive industry have been hard hit by the pandemic. Joe Owoc at Interwire said the coronavirus overall has had a significant impact. “Our non-automotive business is down, but relatively unharmed as compared to our automotive business. That sector was down between 50 and 80 percent for the month of April.”
In addition, Owoc said oil and gasrelated business was also impacted. “The biggest impact is regarding receivables. Cash flow and aging issues were damaging.”
Jessica Marco at Spring Dynamics, Inc. just outside of Detroit said 75 percent of the company’s staff have been laid off since March 23. Marco said the remaining 25 percent have been laid off periodically since then. She said sales are at about 5 percent of normal.
What is it like in Canada? Jeff Wharin of Bohne Spring in Toronto says the company determined early on that they fit the qualifications of an essential business in their juris diction, due to their diverse customer base in industries such as defense, aircraft, nuclear and power genera tion equipment. “We have remained open throughout; the largest industry which negatively impacted us was the closure of automotive assembly plants and their subcontractors. This will definitely impact our revenue for 2020.”
Attracting new customers seems to be taking a hit as well. Rick Guard at Newcomb Spring of California said, “New business is down drastically.”
Chris Witham at Motion Dynamics Corporation is more of an outlier. He said only a small number of customers have pushed out delivery dates, and
total revenue for Motion Dynamics has not been impacted.
“In fact, we set a record for revenue in the month of April,” said Witham. “We do have approximately 10 percent of our workforce out on extended leave.” He said they have had a couple of R&D requests for springs used on a ventilator system.
Jacklyn Edwards at Duer/Carolina Coil said the company has only noticed a “slight decline in sales from customers, but nothing major.”
Safety Changes
The second question in the survey asked, “What changes have you made to your business due to COVID-19?”
Spring companies who continue to operate have adapted to social distancing guidelines and other precautions as they operate as essential businesses during the pandemic.
Guard of Newcomb Spring of California said they are following social distancing guidelines, along with “training, conducting continuous
sanitizing and ensuring we have masks and cleaners for all.”
Similarly, Susie Lindsey at M & S Spring Co. Inc. in Fraser, Michigan said they are following guidelines for hand-washing, social distancing and wearing masks. “We are a small business with only 17 employees right now, so social distancing is not a problem.”
Rhonda Miller at Action Spring in Tulsa outlined seven measures they have taken due to COVID-19: 1.
2.
3.
4. Not allowing any outside visitors at this time (Miller said she will decide on this at a later date). Installing hand sanitizer stations for employees to use. Meetings with the employees about hygiene, i.e., washing hands often. Employees are to wear masks if they are going to be closer than six feet with other employees; other wise, they do not have to wear a mask.
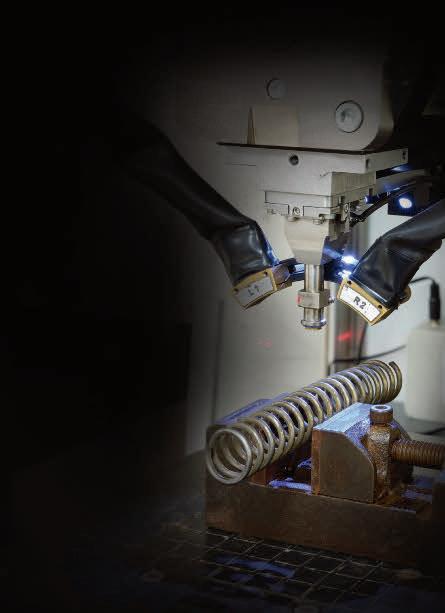
Spring Tooling for All Machines
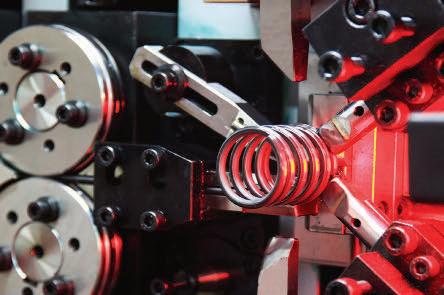
Complete line of carbide and steel tooling for the spring coiling industry.
6.
7. Employees who go out of state cannot come back to work for 14 days after returning to Tulsa. Employees who call in sick are told that they will not be allowed to work until an approved facility has administered a COVID-19 test stating that the employee does not have COVID-19. Taking employees’ temperatures before the workday starts (using a no-touch thermometer).
Lathrop at Hardware Products said they have instituted similar changes. “We split the lunch break into two sessions to permit social distancing in our lunchroom. We have increased sanitation efforts, and everyone is wearing a mask. If anyone misses time for any illness (COVID or not), we strictly enforce obtaining a release from a medical professional before returning to work.”
Regarding what has changed at The Yost Superior Co. in Springfield, Ohio, Deerwester said, “Besides wearing masks, checking temps and disinfecting? We are still serving customers and that’s still why we are here.”
At Spiros Industries in Wisconsin, Johnson says they have created daily cleaning processes, added masks to personal protective equipment (PPE), adjusted shift hours, and loosened up its sickness policy so employees are not penalized for staying home “just in case” they have it.
Richter at R-R Spring Corporation said they have also rethought their sick policy. “We have told our employees if they are feeling sick to stay home and they would be paid.” He said they have trained all their employees on social distancing, along with providing masks and gloves.
Edwards at Duer/Carolina Coil outlined some of the changes at their facility in Reidville, South Carolina: “We canceled all shift meetings, allowed office staff to work from home, provided masks and gloves and supplied disinfectant to each team and common areas.”
Witham at AIM said they have implemented safe working environment precautions, including social distancing, hand washing, disinfectants, masks, gloves and taking employees’ temperatures. “We’ve also developed new ways of working with customers, including more video conferencing, remote equipment runoffs and video documentation.”
Staffing Level Changes
At Bohne Spring, Wharin says they were quick to implement safety protocols to protect their employees. “We made it possible for most of our office staff to work from home, as needed. Typically, they come in two to three days a week and work from home the balance of the week. We have not had a need to lay off employees, but we did apply and receive approval for a work sharing program, which allows employees to work four days per week and receive unemployment for the fifth day.”
Concluding, Wharin says Bohne Spring will continue to operate four days a week until business picks up, especially in the automotive sector.
Debra Kolodge at FTR Associates and Foremost Spring said, “At FTR Associates, Inc., we have furloughed 14 people (of 36). We have had three of them return to work since, because work in their department picked up, but our long-term outlook isn’t good right now. At Foremost Spring Co., Inc., we had already downsized to what we consider our core crew of 10 people before the worst of the corona virus impact. We export to China and had been feeling an impact to our sales beginning late last year.”
Kolodge added, “Upper management has reduced our salary by 25 percent, and we are working hard to keep over head low. We are also lucky that the landlord for both businesses voluntarily gave us three months of rent free to help during this time.” They had applied for SBA loans but were waiting for a decision as of press time.
Banas at Stanley Spring and Stamp ing said they have instituted several changes, including mandatory use of vacation time and reduced hours based on customer shutdowns and re-openings. He said work hours are formulated on a week-to-week basis depending on demand, and all employees are informed each Thursday regarding work commitments for the following week.
“We have identified necessary operations versus operations that can be suspended,” explained Banas.
In addition, Banas said they are only producing products with firm orders and customers who are open for business.
In addition to daily taking employees’ temperatures, Witham at Motion Dynamics Corporation said they gave all employees a 10 percent increase in pay during the month of April and the first half of May. “We may extend this based on what happens in the state of Michigan.”
Witham said they have closed the company’s exercise area, shifted start times, spread out lunch breaks and provided everyone with masks, cleaning wipes, gloves, hand sanitizer, etc. “We have selectively allowed some to work from home.”
Owoc said they are also allowing employees to work from home, which has produced a downside. “Office dynamics, as it turns out, plays more of a role than I realized,” explained Owoc. “The ability to effectively communicate is lost when team members work from home.”
Cutter at FENN-Torin said that with current travel restrictions, the company has been unable to have customers visit their Connecticut facility, and customer service techs have been unable to visit customers.
“To adapt, FENN has completed virtual factory acceptance tests, via videos and photos, for customers to see their machines running and feel comfortable with their performance and functionality prior to shipment,” explained Cutter. “To continue servicing customers, FENN has relied on remote
Communicate Proactively
In my role as president of Fairway Communications, I helped a company earlier this year that was attacked by ransomware. As the CEO of the company told me, “No one wants to wake up and learn that their company was the target of a malware incident, but it’s an ongoing reality in today’s world.”
Similarly, no one wanted to wake up to a world that was turned upside down by the coro navirus pandemic.
I admire this company for its resilience in the face of this cyberware attack. They went on the offense to communicate with their stakeholders. They demonstrated to everyone an openness and transparency. In simple terms, they shared how the attack happened, what they learned from it and how they planned to move forward. By all measures this message was well received.
I would suggest the same game plan for spring companies who have been impacted by COVID-19. Be open with your employees and customers about how the pandemic has changed your business. Also, tell them what you have learned so far (and more lessons are likely to come). Finally, communicate to your audiences (employees, customers, vendors, etc.) how you plan to move forward once the crisis has passed.
In the midst of this pandemic, there is a lot of good news out there. You can help create goodwill and hope through strategic communications to your employees and customers. Keep demonstrating your social responsibility in what you say and what you do.
Have you manufactured any new or updated products to help critical industries responding to the pandemic?
software access and telephone support to assist customers with production questions.”
New Products
The final question in our survey asked, “Have you manufactured any new
products or updated products to help critical industries responding to the
pandemic?”
Miller said some customers who were sourcing products from Mexico contacted Action Spring looking to have products manufactured for them.
Banas said they recently supplied five manufactured stainless steel components to Cepheid, a leading molecular diagnostics company. In March, the company announced it had received Emergency Use Authorization (EUA) from the U.S. Food & Drug Administration (FDA) for Xpert® Xpress SARS-CoV-2, a rapid molecular diagnostic test for qualitative detection of SARS-CoV-2, the virus causing COVID-19. The test has been designed to operate on any of Cepheid’s more than 23,000 automated GeneXpert® Systems worldwide, with a detection time of approximately 45 minutes.
Witham at Motion Dynamics said they have provided three different compression springs so far.
Deerwester at The Yost Superior Company said, “We’ve had a few customers with hot orders for the medical field.”
Doyle at Industrial Spring of St. Louis explained that while they have not manufactured any new products, the company’s existing customers have increased their orders due to the virus.
“We have not made any new products,” explained Richter at R-R Spring Corporation, “but we have had delivery moved up by customers making parts for ventilators.”
While Wharin said Bohne Spring has not manufactured any new products, he noted that some of their customers who were dormant have become busier. “We have looked for customers who have pivoted their production to make PPE for hospitals and front line workers, and we are still hopeful that we can participate in some new programs.”
On the raw material supplier side, Owoc said “we have been able to source materials for ventilators, masks, etc.”
Survive and Advance
“Survive and Advance” was the subject of an ESPN 30 for 30 documentary on the 1983 NC State Wolfpack men’s basketball team. Led by legendary coach Jim Valvano, who sadly died of cancer in 1993, the Wolfpack men’s basketball team became the national champs that year by winning a series of nine overtime and 1-point games, culminating in a thrilling final game where they triumphed in dramatic fashion against No. 1-ranked Houston.
Why do I mention this? I think the term “survive and advance” aptly applies during these turbulent times we are all facing. And it goes beyond the triviality of sports. Survival of people’s lives and livelihoods is paramount as we do our best to beat this unseen virus. One thing is certain: the pandemic has changed all of us in many different ways. n