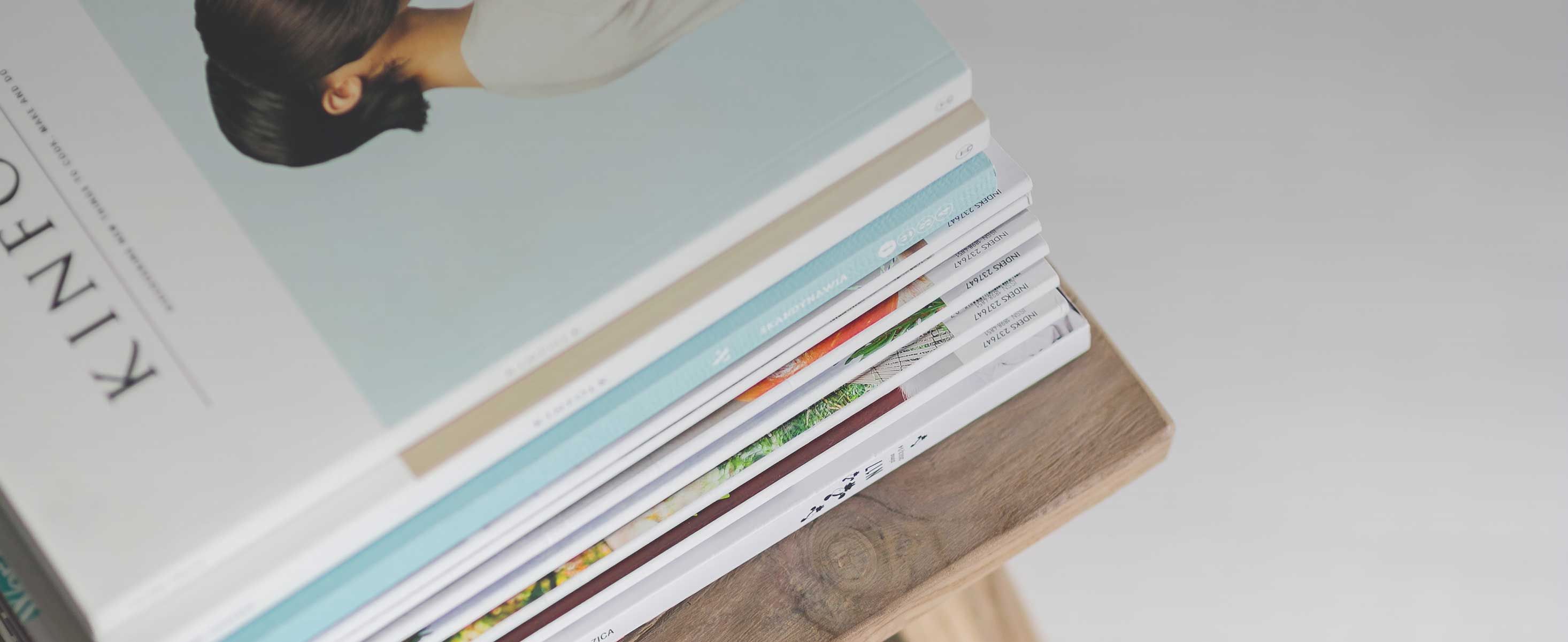
3 minute read
MODERN CAMERA DESIGNS
SMALL LENS, BIG EFFECT
MODERN CAMERA DESIGNS WANTS TO BRING THE HIGHVOLUME PRODUCTION OF SMALL IMAGING OPTICS BACK TO EUROPE
SPRIND AND MODERN CAMERA
Designs
PROMOTING EUROPE'S INDEPENDENCE
Why We Are Committed
Because we are initiating an industry revolution with mcd’s production technology. Because we have a production technology that addresses all applications for high-precision miniature- and microlenses. Because this production technology overcomes existing limitations and lays new foundations for imaging innovations.
A key technology is being brought back to Germany with the help of this production technology and is consequently promoting the innovation location Germany.
NETWORKING AND THINKING BIGGER
SPRIND supports mcd with its extensive expert network and contacts to partners and users to advance the potential of the project in the fastest way possible and put the technology to work in applications.
That is the spirit totally in accord with SPRIND: the two micro-optics specialists Dr. Frank Wippermann and Dr. Jacques Duparré from mcd—modern camera designs GmbH in Jena—are not only launching their own disruptive innovation, but are also preparing it for those of tomorrow. They are revolutionizing the manufacturing process for miniaturized imaging optics in a groundbreaking way with their innovation.
The fact that there is still room for improvement with this process is demonstrated by the two currently dominating methods for the production of miniature lenses: “Injection molding makes this possible in the required high quality, whereby the disadvantage is that the process is very expensive for small quantities and can only be parallelized to a limited extent,” Frank Wippermann explained, who is dedicated to miniaturizing cameras. “On the other hand, wafer-level optics similar to semiconductor manufacturing can be used well for optical sensors, but not for high-resolution camera lenses. However, it provides the opportunity to produce large quantities in an energy-efficient and cost-effective manner, because it is a highly parallelized process.” The market for small imaging optics, currently dominated by the Far East, is huge: several lenses are used in each camera for endoscopy, cars, PCs, tablets and smartphones. At the same time, you can find multiple cameras in a single product, up to five in a smartphone and even up to 16 in a single car. “It is an art to get optics in perfect, consistent quality at a good price,” Frank Wippermann stated, who holds a doctorate in physical engineering and wants to make this project possible: the four-member mcd team has found a way to eliminate the disadvantages of both methods and to combine their advantages. This results in new degrees of freedom in lens development and at the same time saves machines, space, money and an enormous amount of energy.
Reduce Energy Consumption
The whole approach also becomes so attractive because it paves the way for other innovators in the field of optics: there are often small quantities at the beginning of great visions, which are currently extremely expensive and therefore represent a major obstacle. “The low initial costs associated with the production of lenses by our process, even in the smallest quantities, make it easier to check new ideas,” physicist Jacques Duparré reported, whose hobby is bionics and how the visual principles of insects can be advantageously transferred into the world of digital imaging.
The founders are particularly proud of the energy savings. In the conventional injection molding process, polymers are melted at high temperatures, injected into the mold under high pressure and then cooled. You need many machines and huge facilities under clean room conditions. “By switching the process to room temperature, improving the parallelization and hence need fewer machines, we reduce energy consumption to up to five percent,” Frank Wippermann stated ambitiously. For this purpose, the founders rely on UV replication, which enables up to 1,000 aspherical, monolithic lenses of polymer in imaging quality to be produced simultaneously in a single step, which are required, for example, for high-end smartphone camera modules.
The fact that mcd is based in Jena is of course no coincidence. “Jena is one of the top addresses for optics in Germany and even worldwide, and we have been professionally connected since working at the same company in Jena for our diploma theses approx. 25 years ago,” Duparré explained, who previously worked for a start-up in Silicon Valley for seven years. He and Wippermann were and are also employed at the Fraunhofer Institute for Applied Optics and Precision Mechanics IOF, where they develop ideas for cameras that no longer protrude from the rear side of a smartphone. With their EXIST-funded company foundation in 2019, they initially planned only the design and construction of prototypes and small series for miniature cameras, for example, for disposable medical endoscopes. Because that worked almost surprisingly well and the customer satisfaction was so great, the two then “simply” continued and are now thinking big. They want nothing less than to bring high-volume production of miniature- and microlenses to Europe and Germany.
With SPRIND, the two founders and their team now want to expand production, “until we can produce multiple 100 lenses at once with ever higher complexity and lower tolerances,” Wippermann described the next milestone. Stacking three lens elements is sufficient for both disposable endoscopy and automotive applications. For this purpose, the company can already produce ‘aspheric meniscuses with a large sag height’: superlatives in microlens production. Aim of the ambitious founders: “We see lenses for cameras in smartphones as the main application. These have up to seven lenses with the highest quality requirements—and that is where we want to go.”
» YOU COULD SAY THAT WE BUILD PERFECT MOLDS AND THUS CREATE THE MOST BEAUTIFUL AND UNIFORM SAND FIGURES. «