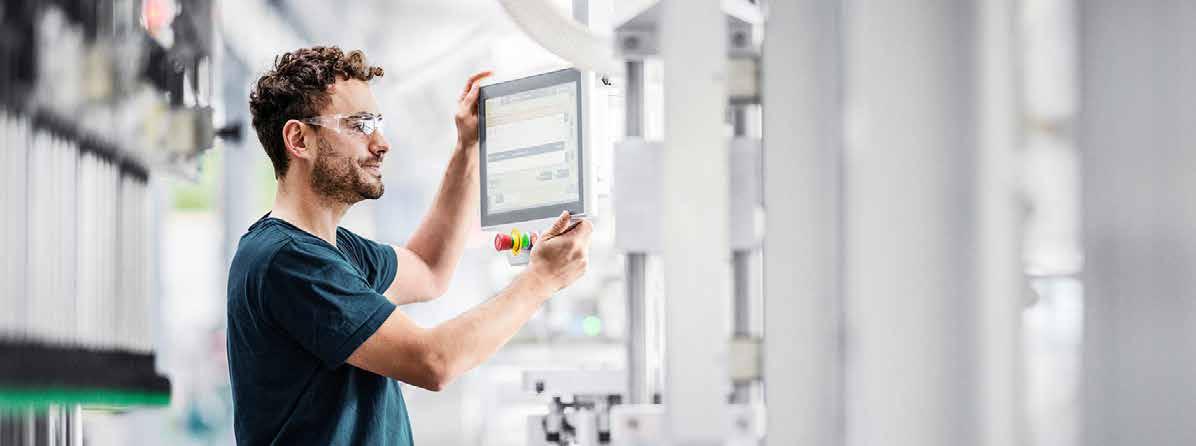
7 minute read
Syntegon - Special Feature Driving Change
from SPN April 2023
by spnews.com
SPN Invited Syntegon for their current assessment of the global packaging market and how their drive towards greater sustainability and the Circular Economy were being endorsed by their innovation and the on-going optimisation of its advanced technology equipment.
“Food producing companies across Europe must therefore invest in innovative technologies that protect people and the environment, while still maintaining competitiveness across different industries”
Advertisement
Syntegon continued: “Food companies are facing many challenges due to fluctuating raw material prices, changing regulations, and demanding consumers. One of their major hurdles is to achieve sustainability goals, while acting in an economically and ecologically viable way. Food producers, therefore, need the support from technology experts to flexibly and efficiently meet market demands. Syntegon is ready and able to take on that role.
Plastic has long been considered the packaging material of choice across most industries. These times are slowly, but steadily, coming to an end. For instance, in the EU, several countries are aiming for a significant reduction in plastic, each with a different strategy. France is taking a particularly bold stance: by 2040, single-use packaging is to disappear from French consumers’ lives. The phased plan includes plasticbased products, from disposable cups to register receipts.
Europe – Setting new Standards
France is not alone in this endeavour, however; countries such as Belgium and Spain are following suit and even going beyond the EU regulations, which state all plastic packaging on the European market must be recyclable or reusable by 2030. In Spain, for example, plastic beverage or food containers may no longer be distributed free of charge as of January 1, 2023, provided they are intended for direct food consumption. If this packaging is still used, consumers are charged a fee.
By doing this, legislation hopes to reduce sales of these products by 50 percent by 2026 and 70 percent by 2030. In 2020, the EU saw the introduction of the so-called “plastics tax”. It includes a levy of 0.80 euros per kilogram of nonrecycled plastic packaging waste generated in each respective member states. Germany alone had to pay 1.3 billion euros in tax money to the EU in 2021 due to this. The current German government wants to hold manufacturers and distributors of plastic packaging more accountable. According to its coalition agreement, these companies are intended to pay the EU plastics tax in the long term.
A world with less plastic
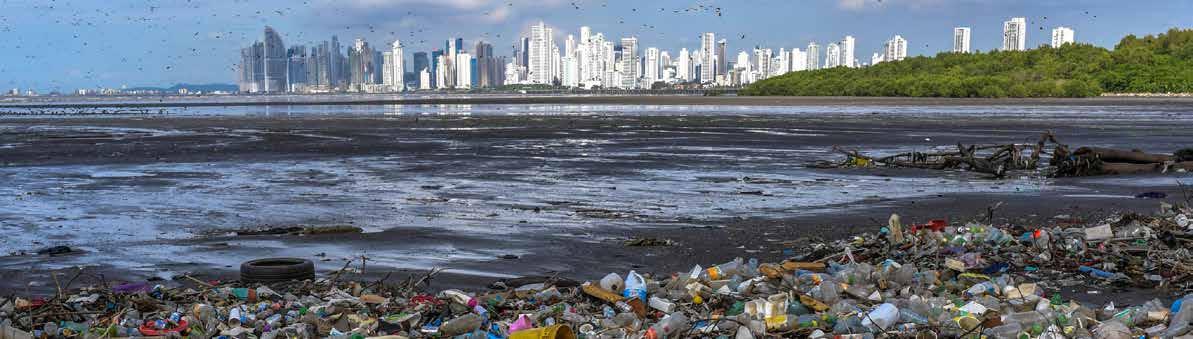
Regulatory pressure has the food industry turning towards alternative packaging solutions, with paper as the new packaging material of choice. In the public perception, paper is seen as more environmentally friendly. Unlike plastic, it also decomposes faster and is easy to recycle. However, while paper accounts for a considerable share of the overall packaging solution, especially with liquid or viscous foods, it is not the only used material. Current paper packaging solutions are composite materials, since they need a plastic barrier for tightness and product protection.
Germany has again defined strict rules: paper-based packaging material may not exceed a plastic content of five percent. This ensures the recyclability of paper-based packaging so that it can enter the established value streams like conventional paper – provided it is not too heavily contaminated after use. As an alternative to paper-based packaging, innovative solutions made of mono-materials are available to food companies: films, cups, and blanks made of polyethylene (PE) or polypropylene (PP) offer the same protection as classic composite materials – with the advantage of significantly higher recyclability.
Where Ecology meets Economy
Food producers have plenty of options to ensure an ecological production that complies with regulations. The challenge consists in aligning complex legal requirements with the demands of their own products – and in acting both ecologically and economically in the process. This affects both their own interests as well as their consumers’ for besides food quality and innovative recipes, ecological packaging solutions and manufacturing processes influence purchasing decisions significantly.
Producers must therefore be flexible in their choice of packaging formats and materials. “This enables them to implement solutions that meet the requirements of the respective products and consumers without disregarding company-specific sustainability goals,” says Ilona Junker, Project Manager Sustainable Solutions at Syntegon.
Product protection a key requirement
According to Ilona Junker, food manufacturers must consider the packaging needs of each product to achieve this balance. Ecological and quality aspects play an equally important role, especially in the food industry where hygienic considerations are decisive. Dairy and delicatessen products such as yogurt, sour cream, spreads, deli salads, dips, and sauces often require continuous cooling. Food brands usually fill these products under clean or ultra-clean conditions. The strict hygiene requirements for filling drinkable and baby foods, on the other hand, demand aseptic processing with even higher sterilization rates. This retains the products’ shelf life for a long time even without refrigeration or additional additives and prevents product loss.
“Producers always face the challenge of investing in equipment that meets the right hygiene requirements – in addition to the high expectations regarding product sustainability,” says Ilona Junker. Syntegon works with a holistic approach that covers both packaging and machine technology. The company advises food manufacturers on paper or mono-material usage and offers an equipment portfolio for all hygiene classes. “Our technology ensures sustainable and safe products in the long term – and future-proof production.”
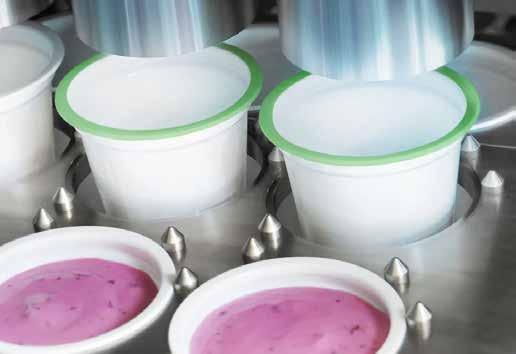
Expanding portfolio
Flexible and efficient solutions are in high demand among food producers and technology providers alike. State-of-theart equipment should enable them to take ecological and economical aspects into account and to reconcile social needs and product protection. To this effect, the equipment must be able to process different products and packaging materials safely and operate in an energy-efficient way. But what exactly does that mean?
A matter of perspectives
Take the processing of liquid foods. Here, different hygiene classes have different effects on energy consumption during production and storage. The storage of food produced under clean conditions requires more energy than aseptic production, which does away with cold chains. Cups or other packaging are not pre-sterilized during clean manufacturing. As a result, the packaged foods have a shorter shelf life and require continuous cooling. With aseptic and ultra-clean filling, on the other hand, the packaged products can be stored without additional refrigeration due to the previous packaging sterilisation.
“Our portfolio offers manufacturers the required flexibility to process products according to their respective quality and sustainability goals,” says Ilona Junker. While pre-sterilization may make sense and be feasible for company A, company B may opt for clean filling due to product characteristics or budget constraints – for example, if it mainly has products with a short shelf life in its portfolio. The ideal solution must be determined case by case. “Each package or product has an individual carbon footprint. Knowing this in advance can help companies find the right machine and manage their own sustainability measures in a more targeted manner,” Ilona Junker explains.
In line with its holistic approach, Syntegon offers its customers consulting services. With its software-based methodology certified by TÜV Rheinland, companies in the pharmaceutical and food industries receive full transparency regarding the carbon footprint of their Syntegon machines. The calculation method developed by Syntegon can be carried out on request, covering parameters such as electricity, compressed air, media, and packaging materials. Moreover, the flexible methodology allows to examine both packaging and processing equipment by linking the parameters to the respective carbon emissions. This way, Syntegon’s calculation can help to holistically determine resource consumption for each customer.
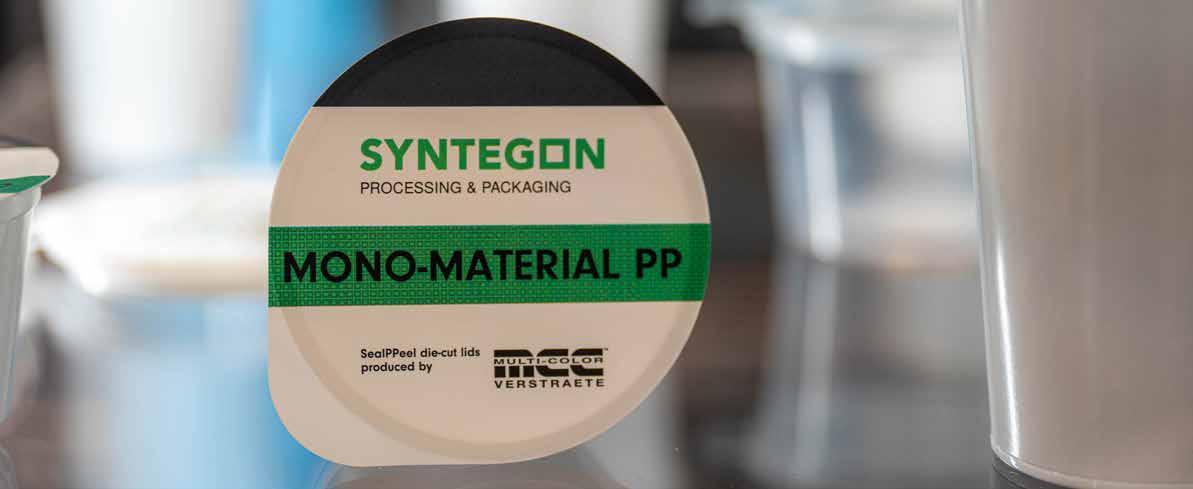
Flexibility via modularity
Food producers also benefit from modern equipment that can be flexibly expanded to enable future-proof production. Modular systems allow them to efficiently adapt production to specific applications – for example, if regulations urge companies to process paper instead of plastic or if they must achieve higher energy savings. The modular LFS from Syntegon, for example, can be equipped with up to three servo-controlled dosing systems, filling 7,000 to over 20,000 cups per hour.
Different product viscosities can be filled with high precision and low product loss. In case of product changes, operators only need to replace the nozzles of the dosing stations in a few simple steps. A mobile cleaning bar ensures fully automated intermediate rinsing and cleaning of the dosing unit.
Syntegon Cup & Bottle Filling machines
“With our modular approach, we support companies that have so far shied away from investments due to volatile market conditions. Since our machines can be converted or retrofitted at any time, they offer an ideal basis for production, especially in times of increasing efficiency requirements and high sustainability standards,” Ilona Junker emphasises.
Thanks to various retrofit options, existing machines can also be adapted to meet the changing standards of sustainable and quality-oriented production, for example with special forming shoulders for paper packaging. Manufacturing companies remain flexible in their choice of packaging materials.
Depending on market and legal needs, modular systems can be used to process paper, PP, or PET mono-materials. “This wealth of options helps companies respond to current trends in a product-specific way without having to commit to a specific solution from the outset. As a result, they remain competitive in the current production environment,” Ilona Junker explains. Manufacturing companies can count on Syntegon to navigate the alternatives. “Since we have a holistic approach to sustainability and production, we support companies both as technology experts and as consultants.” In addition to its CO2 analysis, Syntegon also offers legal advice. “We see it as our duty to know current regulations and global sustainability trends and to advise customers accordingly – especially with regard to the right machine solution,” says Ilona Junker.
What regulations will the food industry face across the globe? How must manufacturers adapt their systems to remain competitive? Syntegon’s experts provide the answers to these questions. “Decision-makers of manufacturing companies rely on these consulting services and our support.”
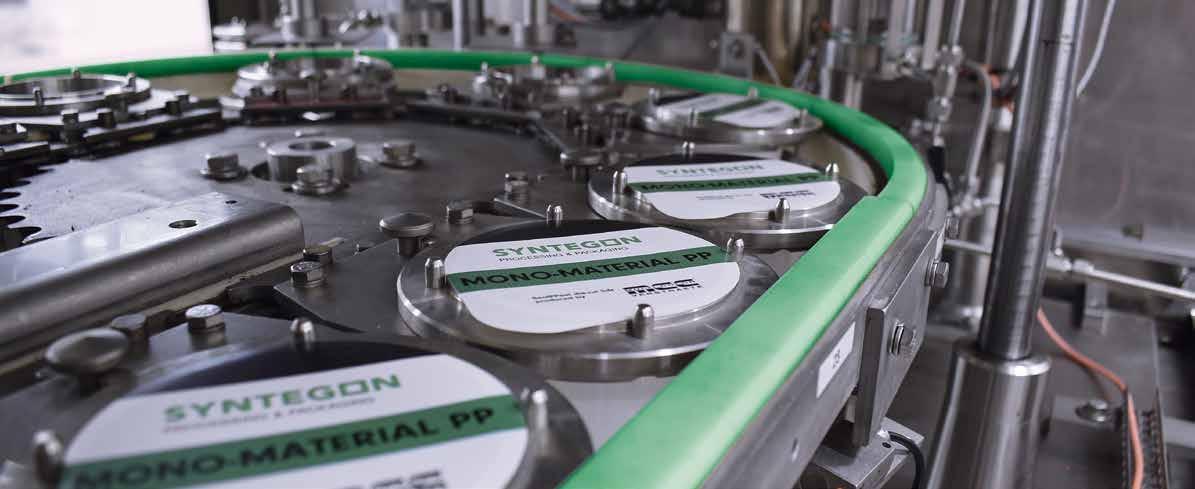
Ambitious goals
Within the scope of its holistic approach, Syntegon also has an eye on its own activities as a sustainable equipment manufacturer – with ambitious goals for the coming years. By 2025, the company aims to reduce its worldwide carbon emissions by 25 percent and even by 50 percent five years from there. In addition to the calculations for its own machines and the derived optimisation potential, the company also relies on professional cooperations. With the support from packaging material suppliers and academia, Syntegon seeks to harmonise sustainable action and efficient production – for itself and for its customers. In other words, in a fully sustainable way!