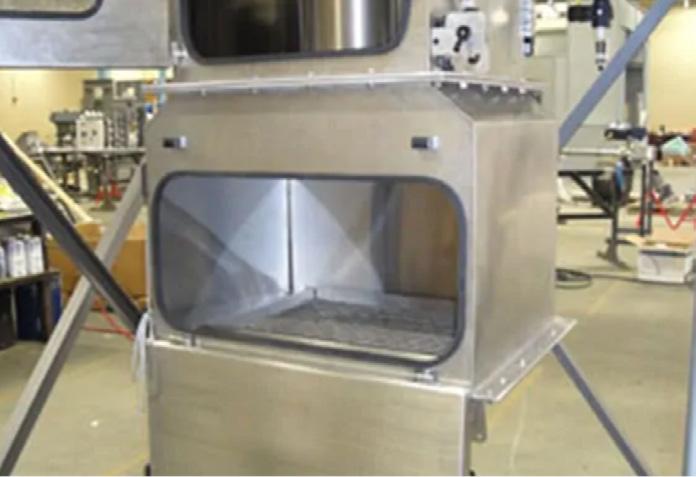
3 minute read
Step 6: Customize Bulk Bag Unloading Station
Many additional options can be added to a bulk bag discharger design.
Mobile Options
Advertisement
For manufacturers who need to move their unloader to different locations, this discharger can be locked in place while in use and then wheeled to another location in the plant easily.
Hygienic Requirements
It’s also important to understand any hygienic requirements, including the cleaning process of the discharger. Additional options can be added to the bulk bag unloader such as spray balls, drain ports, etc. in order to facilitate cleaning in place. Also, surface finishes, frame design, and materials of construction can all be specified to meet additional hygienic requirements.
Dish Cover Assembly
In order to prevent foreign material from entering the discharger and possibly contaminating the internal parts that come in contact with the material, a pneumatically operated cover can be used to seal the bulk bag discharger dish/tray/hopper when not in use.
Integral Bag Dump Station
For small (typically 50 lb) bags that also need to be emptied into a bulk bag discharger a second bag dump enclosure with safety grid can be incorporated under the standard untie chamber or an oversized untie chamber incorporating these features can be added.
Operator Safety Considerations
The design of the discharger must allow the operator to easily and safely untie/retie an outlet spouted bag, so dusting (see above) is often a critical safety consideration. Additionally, removing a partially emptied bulk bag from the discharger is often a requirement. In order to accomplish this task, a device must be included in the discharger design to close off the outlet spout so that it can be retied, allowing the partially emptied bag to be removed. It is clearly imperative that any such devices are safety interlocked to avoid inadvertent operation when the operator is working on a bag spout.
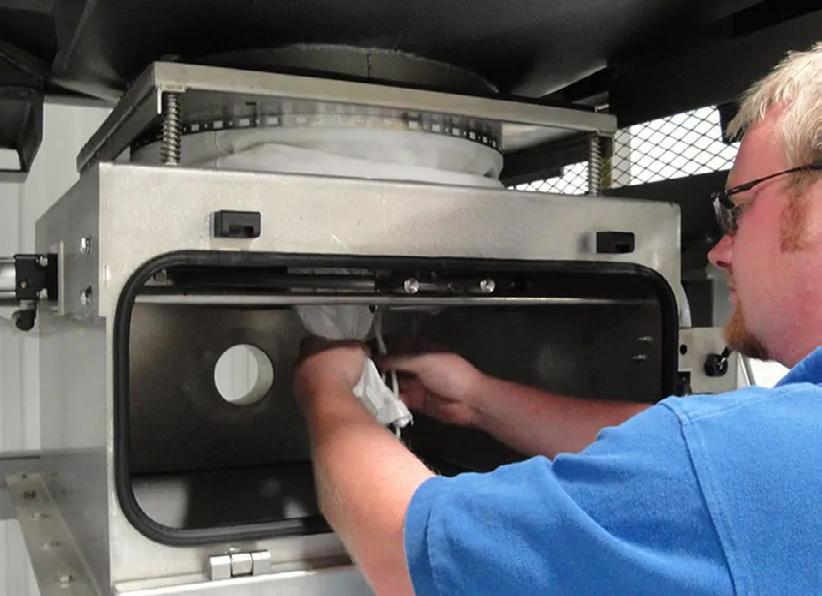
Bag Removal & Disposal
The potential for dusting must also be considered when removing the bag from the discharger. Every dry bulk material should be assessed for their risks and tendency to create dust. There are different methods of evacuating the dust laden air that remains in an empty bulk bag prior to removal and dust free bag compacting and sealing stations can be added as required in these circumstances.
Step 7: Testing your selected design
Following the steps above will help you to determine the right style or design of Bulk Bag Discharger for your specific process needs and what customizable options you should consider in order to maximize the safety and efficiency of your system. The final step in the process is to work with a reputable manufacturer who offers a broad range of designs and options that will meet your needs and who has the ability to test the recommended solution in order to confirm the most appropriate design has been reached.
Some examples of typical discharger designs available from Spiroflow Systems include the following:
Simple Support Frame
Simple support frames are suitable for applications in which the product is discharged without the need for flow aids, is dust-free, does not need regulation of the flow of materials at any point in the process, and has continuous operator supervision in place.
Discharge by Volume
This universal type of Bulk Bag Unloader provides controllable discharge rates by volume, and is typically used for applications with poor flowing materials.
Discharge by Weight
Loss-in-weight bulk bag unloaders offer total control over the amount of product that is successfully dispensed from the bag, and can be varied for individually-selected batch amounts, or fully-integrated with process controls for continuous batch production.
This Loss-in-Weight model has a specialized batch controller that offers both bulk and trickle feed options for optimal dispensing of materials. It also has a “Pause-Resume” feature that automatically pauses the discharging operation when a bulk bag is found to be empty, and retains in memory the amount that has been dispensed.
Discharge with Height Restrictions
Low Loader models, incorporating a split upper and lower frame, are ideal for areas in which there is restricted headroom that typically causes issues for bag handling operations. By pairing this type of Bulk Bag Discharger with a suitable conveyor system, ingredients can be fed from the bag by volume or by weight, and can be moved into other mixing or processing equipment proportionately.
In addition to handling bulk bags, the height of the access door can be designed to receive small bags as well (typically around 50 lbs or less), which is beneficial to processors who continue to receive minor ingredients in smaller bags. Processors with batching operations can also choose to have several upper frames in use with one discharge station in order to significantly speed up bag change over time.
Discharge without the Use of Forklift Assistance
An Integral Hoist model offers a fully self-contained environment for dust-free and controllable bulk bag emptying. This piece of equipment has an integral “I” beam and hoist that loads bags into the discharger, saving space and the need for forklift assistance.
Discharge of Rigid Bins, Octabins, or Sacks/Bulk Bags
This Multi-container discharger model is a versatile option that allows processors to discharge materials from a variety of container types, such as rigid IBCs, octabins, and bulk bags and sacks.
Suitable for batching operations that require multiple ingredients from several different sources or methods of supply.
Discharge Single Trip Bags
Single trip bulk bags are commonly used within plant environments that process low-value or hazardous materials, and therefore require a dust-free and controllable emptying method.
These disposable bags have no bottom spout, and require a static or pneumatic knife to open the bag during the unloading process.