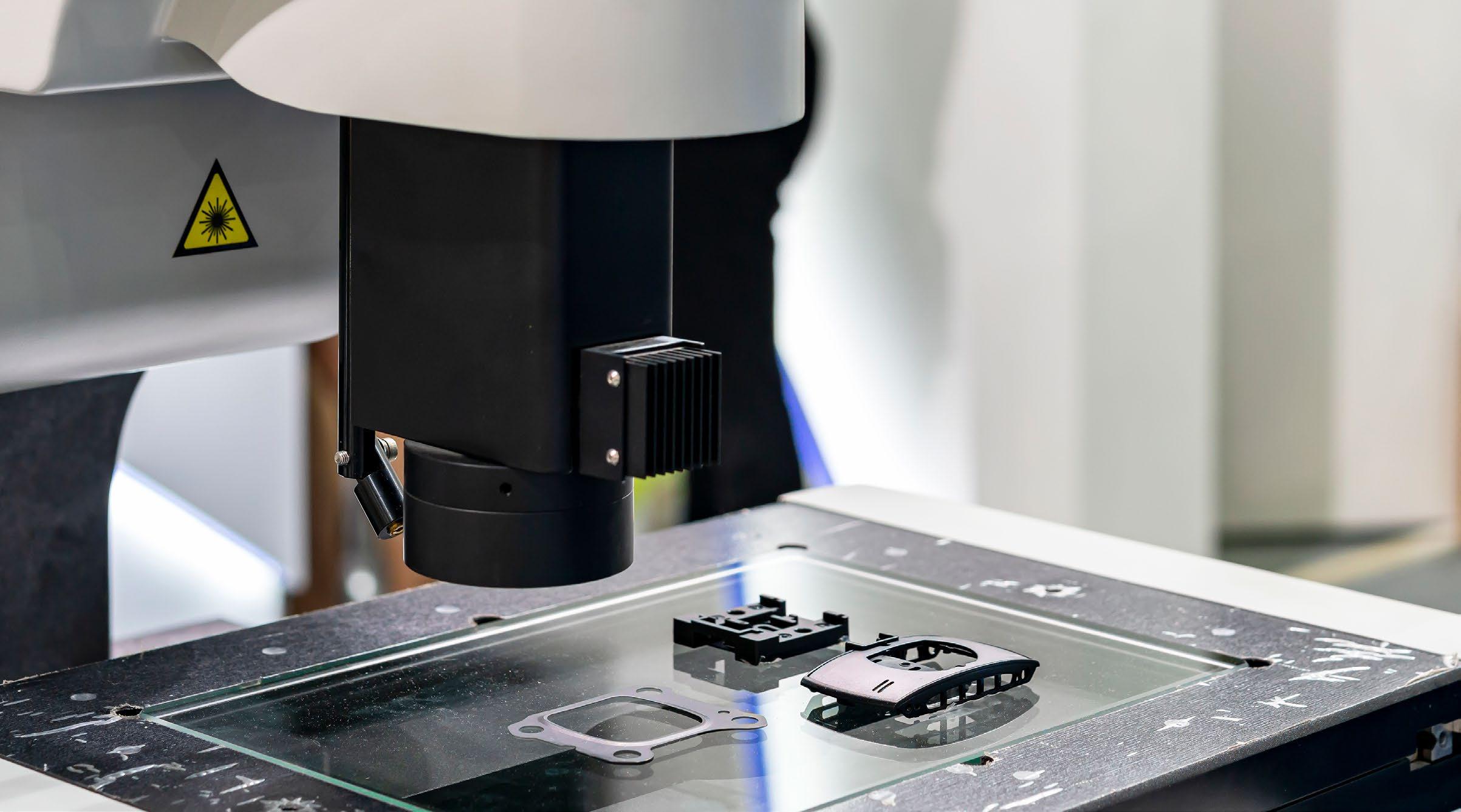
4 minute read
Seeing is Believing
Machine vision inspection is an essential technology that has significantly impacted the manufacturing industry. The global machine vision market size is valued at USD 10.7 billion in 2020 and expected to reach USD 14.7 billion by 2025, growing at a CAGR of 6.5% over that time. This includes the value of installed systems as well as the value of components, software, and services related to machine vision. The technology has undergone a series of developments over the years since its inception in the 1970s and 1980s. Today, machine vision systems are widely used across different sectors, including automotive, aerospace, electronics, and pharmaceuticals.
The use of machine vision technology in manufacturing is set to increase in the coming years. In addition to its current applications, machine vision is expected to be integrated with other technologies, such as artificial intelligence (AI) and the Internet of Things (IoT), to improve its functionality and performance.
Making Machine Vision Systems Work for You
A machine vision system consists of various components that work together to capture, process, and analyze images of products or components. The essential components of a machine vision system include a camera, lighting, optics, image processing hardware and software, a display, and a control system.
One of the key benefits of machine vision is its ability to perform tasks that would be difficult or impossible for human inspectors. Machine vision systems can operate 24/7 without fatigue and inspect products at a much higher speed and accuracy than human inspectors. This makes them ideal for applications such as sorting, quality control, and defect detection.
Machine vision systems can also be programmed to detect a wide range of defects and irregularities, including those that might be missed by human inspectors. This helps to improve product quality and reduce waste, and can also help to ensure compliance with industry regulations and standards.
The primary application of machine vision in manufacturing is quality control. Machine vision systems can be used to inspect products for defects such as scratches, dents, or other imperfections. By detecting these defects early in the manufacturing process, manufacturers can reduce waste and improve product quality.
In addition, machine vision systems can be used for dimensional measurement to ensure that products are within specified tolerances. This is particularly important in industries such as aerospace and automotive, where tight tolerances are critical to ensuring product performance and safety.
Another application of machine vision is in sorting and classification. Machine vision systems can be used to sort products based on criteria such as size, shape, color, or texture. This is useful for applications such as packaging, where products need to be sorted and packaged in a specific way.
Despite the many benefits of machine vision, there are some challenges to implementing this technology in manufacturing. One of the primary challenges is the complexity of the systems, which requires specialized expertise to design, install, and maintain. In addition, machine vision systems can be expensive, particularly for applications that require high-speed cameras or specialized hardware.
However, as the technology continues to evolve and become more accessible, we can expect to see more widespread adoption of machine vision in manufacturing. With its ability to improve efficiency, quality, and safety, machine vision is driving the transformation of modern manufacturing.
Using Software for Upgrading Systems
Retrofitting an industrial visual inspection system is one way of upgrading or modifying an existing system to improve its performance or functionality. This can be a cost-effective way to enhance the capabilities of an older system or to adapt it to changing manufacturing requirements.
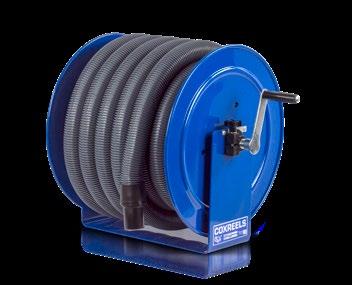
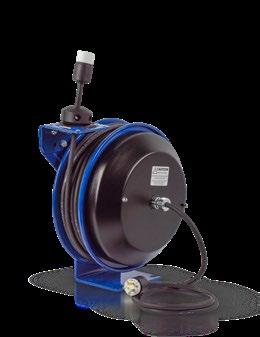
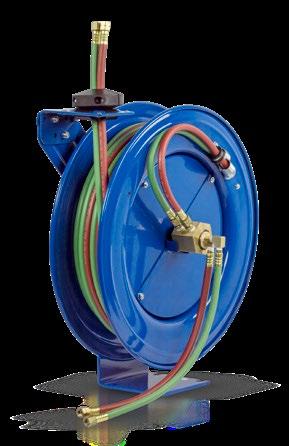
The specific steps involved in retrofitting a visual inspection system can vary depending on the system and the desired upgrades. However, careful planning and execution of the retrofit plan can ensure that the upgraded system meets the requirements and operates effectively.
There is an alternative solution to retrofitting of which many quality managers and plant managers are not fully aware. If a software solution is equipment-agnostic, meaning it is designed to operate with hardware from different vendors rather than being exclusive to one, you can bring new capacity to old investments.
If your existing image acquisition equipment is perfectly okay in terms of image quality and illumination, then the software was the problem. Leveraging your existing hardware by finding a software solution that will work in tandem with it is a good path for consideration. Lean AI is currently putting this theory into practice with a leading powder metal company in Canada. Lean AI’s artificial intelligence algorithms are designed to work with any hardware, so the software can make use of cameras and computer hardware already in the plant, removing the need for the customer to rip out existing equipment and start again. Retrofitting in this way saves time, money and reduces risk.
Emerging Trends
One of the emerging trends in machine vision is the use of deep learning algorithms for image recognition and analysis. Deep learning algorithms can enable machine vision systems to learn and adapt to new situations and make more accurate and reliable decisions. This can significantly improve the performance of machine vision systems in areas such as defect detection, quality control, and object recognition.

Another emerging trend in machine vision is the use of 3D imaging technology. 3D imaging can provide more detailed and accurate information about the shape, size, and position of objects, which can be useful for applications such as robotics, autonomous vehicles, and medical imaging.
Machine vision systems are a critical technology driving the transformation of modern manufacturing. With its ability to improve efficiency, quality, and safety, machine vision is an essential component of many modern manufacturing systems. Despite some challenges, the continued evolution and accessibility of machine vision technology are likely to result in its increasing adoption in manufacturing in the years to come. Retrofitting an industrial visual inspection system is one way to upgrade or modify an existing system to enhance its capabilities or adapt it to changing manufacturing requirements. As the technology continues to evolve, we can expect to see more advanced and sophisticated machine vision systems integrated with other technologies to provide more accurate, reliable, and efficient manufacturing solutions.
Suppliers of these systems include companies such as Keyence Corporation (www.keyence.com), Epson Corporation (www.epson.com), Matrox® Imaging, now part of Zebra Technologies Corporation, as well as several software providers.