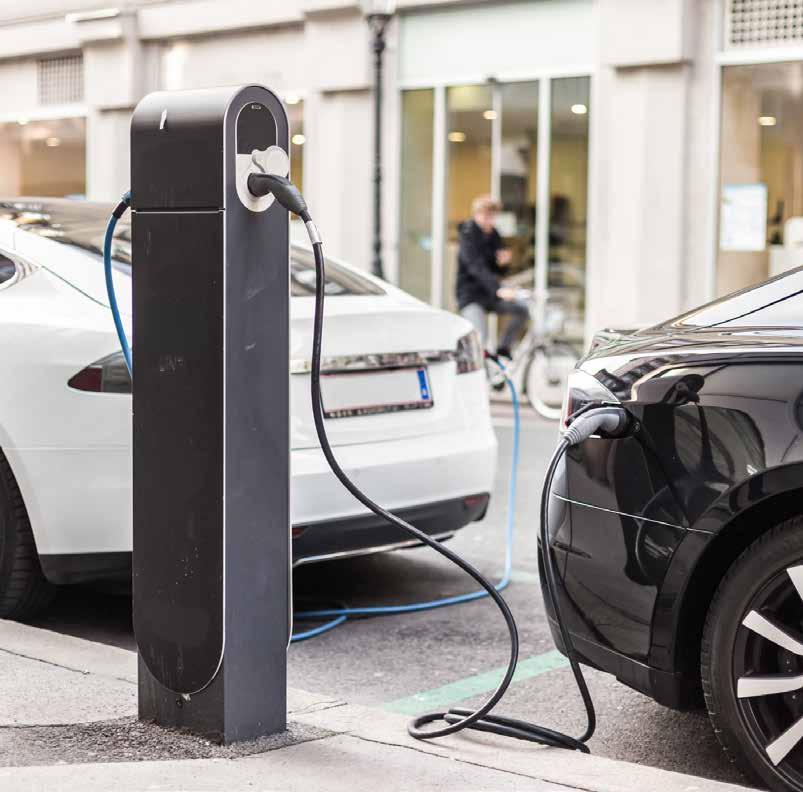
7 minute read
PROCESS
Power Skiving for Electric Vehicles
How manufacturers can achieve 90% machine use reduction with power skiving
Tesla’s automobiles are frequently cited as examples that electric vehicles (EVs) don’t need multiple gears or dual transmission. That is, except for all the models that do. As the multi-gear EV trend begins to pick up speed Mats Wennmo, Global Automotive Transmission Manager at Sandvik Coromant, the global leader in metal cutting, explains how a process known as power skiving can help EV manufacturers keep-up, but with greatly-reduced machining times.
Tesla’s Dual-motor Model S, Model X and Model 3 vehicles each have two different gears, one in the front and one in the back. The potential of EVs with multiple gears has also been explored by Porsche, which has confirmed its electric Taycan will have a two-speed gearbox. Electric vehicles by the likes of Polestar, Volvo, Lucid and Volkswagen all have transmissions, too, but not transmissions like cars have had in the past. New technologies include a two-speed EV transaxle drive unit announced by ZF, the manufacturer of technical systems for vehicles.
There are several performance advantages of multiple gear ratios in EVs, which we’ll explore in this article. But, if multi-gear EVs by the likes of Porsche and Tesla do prove successful, then how can other manufacturers follow suit while also keeping their production cost-effective?
There are two main reasons why EVs need to have transmissions, shown in Figure 1. First, the torque/revolutions per minute (rpm) ratio is not the same in an EV as in an internal combustion vehicle. In the EV, it is hard to achieve torque/ acceleration from the battery without a transmission. The high torque puts higher loads on the gear flanks and, together with
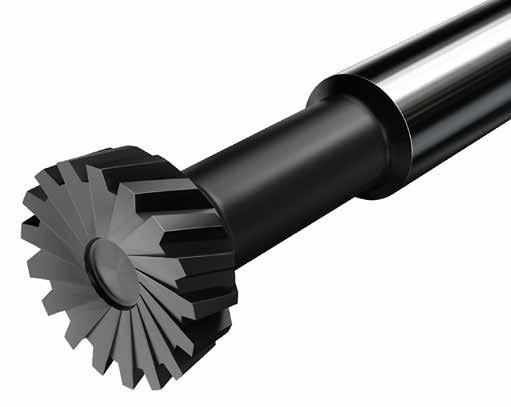
Sandvik Coromant’s CoroMill® 180 is an indexable insert cutter used for power skiving.
Drill. Tap. Assemble.
VISIT US – BOOTH #A3525
Friction drilling is a proven technology that’s been around for more than 40 years. Friction is used to produce bushings in thin metal tubing or sheet metal.

Form your own inserts on standard shop equipment.
Advantages & Benefits
• Cost savings (up to 90%) • High load threads - stronger joints • High process reliability • Faster production cycles • No special machinery required • Small investment • Increased material thickness • Long tool life • Chipless process • Innovative technology suitable for steel, stainless steel, copper, brass, and aluminum
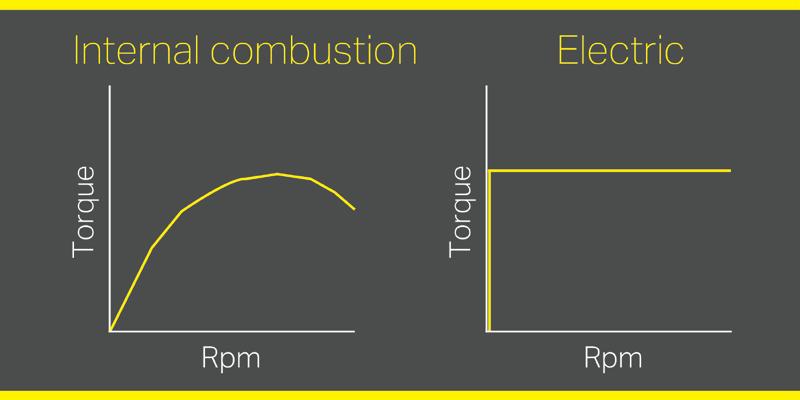
In EVs, it’s hard to achieve torque/acceleration from the battery without a transmission. The higher rate of rpms in EVs also puts extra demands on the transmission.
high rpms, this brings noise reduction into focus since EVs don’t have an engine to cover the noise.
Second, the higher rate of rpms in EVs puts higher quality demands on the transmission, which makes it increasingly difficult to use conventional machining methods. That includes when machines are standing in a line, adding deviations to the gears every time the gear component is moved to the next machine.
The EV transmissions are mainly planetary transmissions where the compact design also reduced weight and space needed for the transmission. Some transmissions are also called reduction transmissions since the task is to reduce torque and rpm at the start.
SERVING AMERICAN MANUFACTURERS FOR OVER 35
YEARS
IndustrialMachineryDigest.com July 2019
GOING MOBILE Cruising Kitchens Relies on ESAB Mobile Welders to Feed the Mobile Vending Boom » Machining Large or Long Parts with a Single Set-up » Black Belt Training Benefits Companies and Their Customers » An American Manufacturing Legacy, Still Going Strong
MANUFACTURING SHOWCASE: KENNEDY MANUFACTURING COMPANY Built with Purpose, Built for Life
IndustrialMachineryDigest.com March 2019
IMPACTING
the DROP ZONE
Wildeck Provides Increased Safety for Moving Palletized Loads
» Empowering Employees » Surpassing Energy Savings
Manufacturer in Oxnard, CA experiences the benefits of Green Hydraulic Power Units
» Lifting Higher
Combi-PPT - A High Capacity
Powered Pallet Truck
» Streamlining Control
Siemens Offers Optimized Control
Panel Construction to Machine
Tool Builders
MANUFACTURING SHOWCASE: TAP ASSOCIATES INC
A Good Tool Is Like A Bar Of Gold
THIS IS SOME TEST HERE
THIS IS SOME TEST HERE
THIS IS SOME TEST HERE
THIS IS SOME TEST HERE
THIS IS SOME TEST HERE
IndustrialMachineryDigest.com June 2019 » Don’t Fear The Robotics How the coming automation revolution is changing the workforce, for the better » Enabling On-The-Fly Product Experts: The New Era of Sales and Marketing in Manufacturing » 2019 Featured Suppliers » 2019 Annual Suppliers Guide Listings
ESTABLISHED IN 1986 AND IS THE INDUSTRY’S Most Extensive Industrial Publication
SERVING AMERICAN MANUFACTURERS FOR OVER 33 YEARS
Industrial Machinery Digest | Established in 1986 and is the industry’s
MOST EXTENSIVE INDUSTRIAL PUBLICATION
SUBSCRIBE & Stay Informed
Power Skiving in Practice
So, what is the best way for manufacturers to produce these higher-quality transmission components? The answer lies in concept that’s been around for more than a century: power skiving. The process combines shaping and hobbing — a machining process for gear cutting — into a single continuous cutting process.
Power skiving has several advantages over traditional machining methods, including higher productivity and flexibility. Using this method it’s possible to machine the complete component in a multi-task machine, or machining centre, with one single set-up. This shortens production time, improves quality and reduces handling and logistics costs. The process also aids manageable and predictable component machining.
Because all machining can be carried out in a single set-up, this removes the need for several specialized machines and machine changes. For automotive manufacturers— for whom downtime is incredibly costly — reducing machine changes can have a significant impact on their bottom line.
One Sandvik Coromant customer, put power skiving to the
test when it sought to shape main gear components made from low-alloy 16MnCr5 steel using the Sandvik Coromant CoroMill® 178 or the indexable CoroMill 180.
The workpiece would be subjected to roughing and finishing with CoroMill 178H PM-HSS solid power skiving cutter. Previously, the customer used a shape cutter for this process, run at cutting speeds of 40 m/min (131 ft/min) for the roughing stage and 50 m/ min (164 ft/min) for the finishing stage. Using this method, speeds could be increased to 250-300 m/min (820-980 ft/min) for both roughing and finishing.
Overall, the manufacturer applied the CoroMill 178H PM-HSS cutters to three-to-five steps for roughing and two steps of finishing. The customer also reported a reduced tool set-up and indexing time, increased process stability and considerably-improved component quality. The improved quality came mainly from that there was no need moving the component between different machines/machining operations, adding center deviations, and run out deviations. The complete machining was made in one set-up.
What’s more, by replacing the time-consuming shaping process with power skiving, cutting time was reduced and tool life increased considerably. This equated to a 90% reduction in machining time, leaving the customer with a large amount of valuable free capacity.
Choosing a Tool
Sandvik Coromant offers a series of carbide cutters for power skiving, CoroMill 178S, and also CoroMill 178H made from powder metallurgical high speed steel (PM-HSS). They are designed for extremely high accuracy and performance and are available for module 0.5–6 (DP 50–5). Sandvik Coromant also offers CoroMill 180. This is an indexable insert cutters with railed insert seats, for excellent and repeatable accuracy in modules ranging from 2.5–8 (DP 10–3).
Although power skiving has been around for a long time, it has recently taken a new turn as machines become more robust and rigid and manufacturers seek new methods of machining. Power skiving works particularly well in mass production where short lead times are decisive, as well as industries in which downtime is costly, like the automotive and EV manufacturing market.
ABOUT SANDVIK COROMANT
Part of global industrial engineering group Sandvik, Sandvik Coromant is at the forefront of manufacturing tools, machining solutions and knowledge that drive industry standards and innovations demanded by the metalworking industry now and into the next industrial era. Educational support, extensive R&D investment and strong customer partnerships ensure the development of machining technologies that change, lead and drive the future of manufacturing. Sandvik Coromant owns over 3100 patents worldwide, employs over 7,900 staff, and is represented in 150 countries.
For more information visit www.sandvik.coromant.com
UNEXPECTED. IN A GOOD WAY.
Prototyping. Second operations. Short-run production. Because it’s compact the 1100MX fits into spaces you’d think it wouldn’t, and with servo motors and a BT30 spindle, it does more than you’d think a compact machine would. It runs on our intuitive and easy-to-use CNC controller, PathPilot®. It’s a dealmaker for a lot of our users. And decked out with an automatic tool changer, it starts cutting at about $25K. What do Tormach owners love about Tormach?
• Owner assembly and commission keeps buying reasonable. • Owner maintenance and repair reduces cost of ownership. • Modular, buy-what-you-need-and-as-you-go machines. Get one now and install upgrades when you’re ready. • Veteran machinists make up our USA-based tech support. We’re dedicated to help people make things.
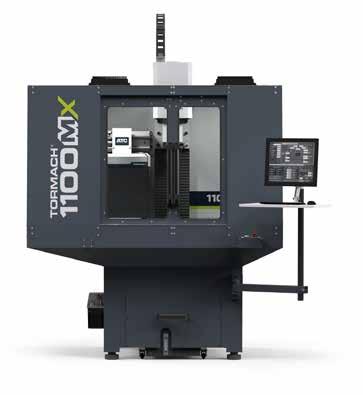