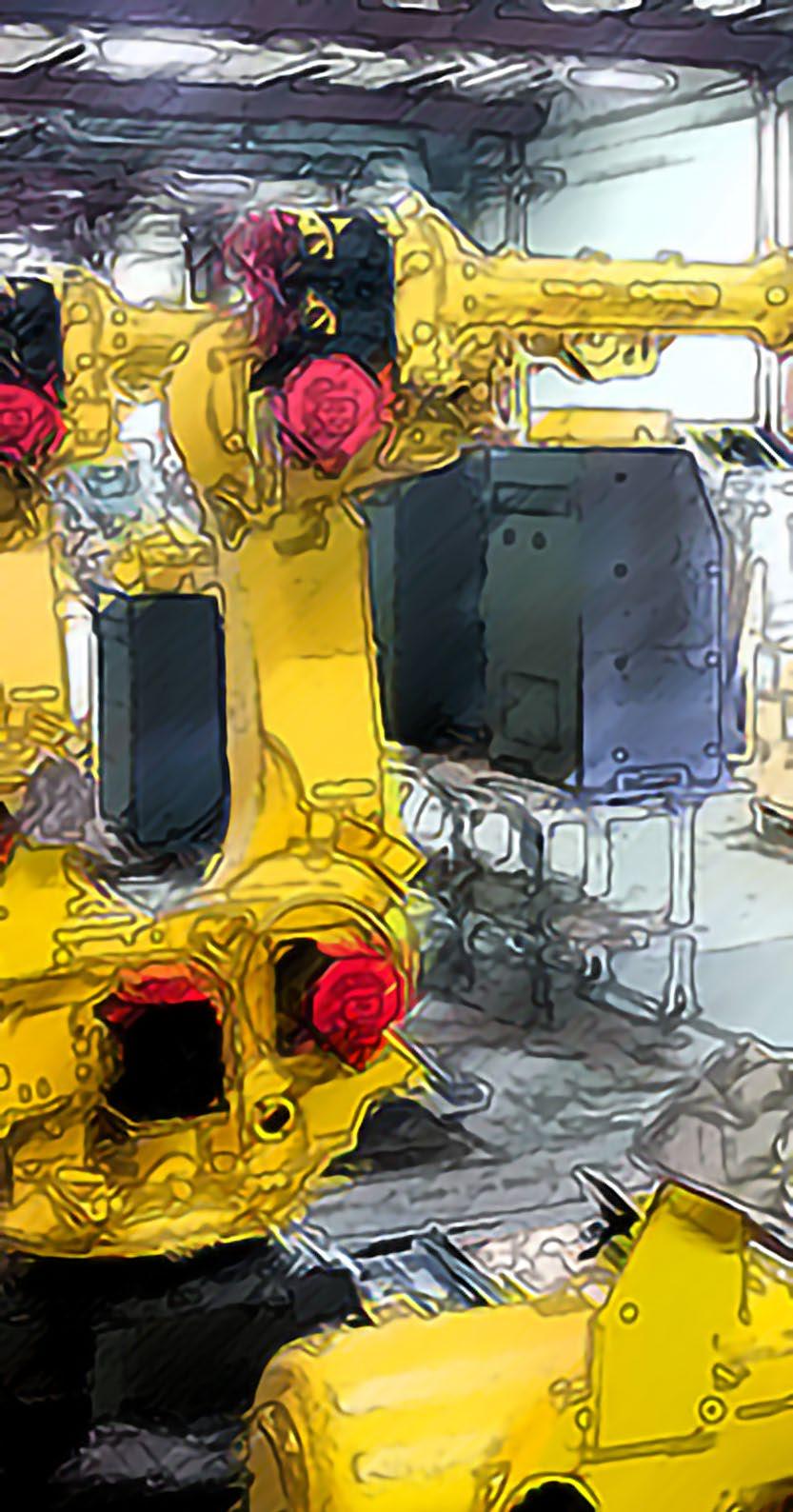
11 minute read
NEW TECH
like all manufacturers, aerospace and defense firms must engineer existing or new facilities in preparation for much higher levels of robotic automation. To do otherwise places them at a competitive disadvantage.
By Josh Tuttle
Regarding robotics, the future is the present — in that it is already here. For advanced economies, robots are providing domestic companies with the efficiency edge they need to support the reshoring trend where manufacturing production returns from lower-wage manufacturing outsourcers located in other parts of the world. But you cannot simply deploy robots into existing manufacturing plants and expect things to move smoothly. Plants must be retrofitted or even redesigned to make the most effective use of this new 24/7/365 workforce. Additionally, new plants should be built around the robotic operations to ensure safe and smooth workflows throughout the facility. Consider an aerospace or defense manufacturer that is preparing to build or renovate a facility they plan to use for the next 10, 20, 30 years or longer for multiple product lines. That building and infrastructure need to be futureproofed to ensure that, as well as being suitable for current work processes, they’ll be adaptable and cost-efficient for the newer processes that are coming. Partnering with a key robotics integrator in the planning phase is a crucial step to ensure your company has the correct floorspace, excess utilities and electrical expansion capabilities. This will also help to avoid common problems like having to upgrade a brand-new building because no one asked the right questions. Here are four ways in which aerospace and defense manufacturers can prepare for the robot revolution: 1. Leave Disappointments in the Past
Robots have been available for years, and perhaps your company has tried them in the past, with results that did not impress. If so, do not remain anti-robot. Today’s robots are already better than the ones that let you down yesterday, and tomorrow’s robots will be even better still.
Plus, it is not the robot that failed, but the process. All good robotic integrations are process driven with clear expectations established. If those aren’t clear at the
all good robotic integrations are process driven with clear expectations established. if those aren’t clear at the beginning of the project, it probably won’t be very clear at the end either.
beginning of the project, it probably won’t be very clear at the end either. If the process still needs to be defined, the best place to figure it out is in the lab. At our robotics company, we leverage our in-house lab on almost every project to eliminate any potential risk. The lab can be used as an early technology demonstrator before the project gets started. This is the lowest risk and cheapest route to a successful robotic system.
2. Future-Proof Your Infrastructure
Even if your company will not be using robots much in the short term, you should take their needs into account when building a new manufacturing plant or refitting an existing one. By making minor adjustments to ensure your plant is robot-future friendly, you can spare yourself the major expense of having to do a total rebuild or refit in five, 10 or 15 years from now. Building the “Factory of the Future” begins today.
Robots consume a lot of power and company’s need the grid to support them. Along with the robot, all the ancillary equipment has some hefty power requirements. It’s safe to estimate a traditional industrial at peak usage will use 30 amps at 480 volts and the newer collaborative robots can run off of 20 amps at 120 volts. When you start pairing multiple robot cells together, it can add up quickly.
As robots become smarter and are being integrated with more sensors, they have more data that they’re harvesting. What good is all that data if it’s stuck on a PC? Setting up a network for your robots to operate on is more than just plugging in an Ethernet connection. Automation equipment and robots need their own independent network to communicate with each other. Working with your robotics partner to set up a system network diagram early on will help you and your IT team understand the network needs for the robotic systems.
3. Hire the Right Humans
As more aerospace and defense manufacturers integrate robots into their work processes, their human workers need to include the right combination of computer- and mechanical-savvy operators. A good robotic system operator needs to be comfortable sitting behind a computer or a teaching pendant, but also knowledgeable enough to troubleshoot a system alarm on the robot. Do not
KEEP YOUR SHOP RUNNING SMOOTHLY WITH A ONE-OFF PART SPECIALIST.
CNC MILLS | CNC LATHES | CNC PLASMA TABLES | CNC ROUTERS | INDUSTRIAL ROBOTS | AUTOMATIC FEED BANDSAWS
An 1100MX can tackle small-batch parts while bigger machines keep humming along.
The Tormach 1100MX runs on PathPilot®, our exclusive and intuitive control software. It has the capability and ease-of-use that makes it ideal for low volume jobs. Tormach equipment fits into small spaces and complements your current machine lineup. There’s no need to distract your bigger CNC machines from profitable larger jobs. What do Tormach owners love about Tormach?
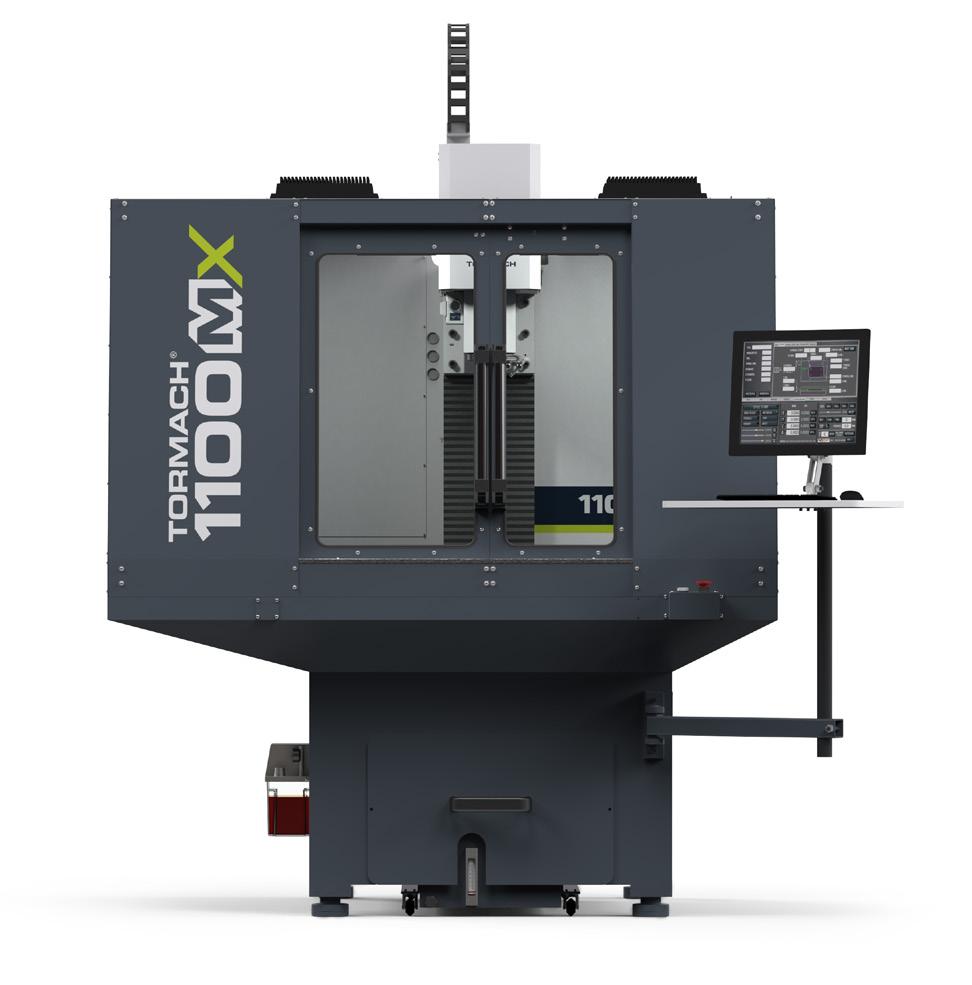
• Maintain your right to update, upgrade, and upkeep. • Buy-what-you-need, upgrade-as-you-go modular equipment. • Experienced machinists make up our no-cost, USA-based
Tech Support crew.
neglect mechanical or software engineers either, because robot support teams require both. These should be skilled operators who understand the process, whether it's painting, drilling or machining. Also, maintenance personnel who understand the equipment are a must, regardless of whether they’re internal or in partnership with your integrator.
There remains a fear among some that robots will take more jobs away from humans than they create, but the World Economic Forum predicts that this will not be the case. The jobs that will be eliminated are largely the ones that are the least attractive for humans, or that had previously been shipped offshore. They will include positions that are unsafe, repetitive or that must be performed in extreme temperatures – so-called “3D” jobs that are dangerous, dull or dirty. The jobs that the robot revolution will create for humans will be more highly skilled, interesting and challenging – and ultimately more satisfying.
4. Make Your Robot Fleet Flexible
Don’t be afraid to think big. Your manufacturing needs will change – day-to-day, project to project and over time. So, when you invest in robots, invest in applications that the robot will be doing today and possibly doing in the next few years. Might you be using mobile robots, automated guided vehicles or, even, mobile multi-use robots for new, advanced projects and products? Consider what these robots could be doing in the next five or 10 years and how else they can be utilized in the future. Talk to your integrator about what robot is best for the application needed and what other potential applications are best for your robot.
Be specific about what you want the robots to do, have a broad vision for your robotics solution and group your robotic operations together. A robot that has the ability and power to pick up heavy weights might not be the same robot that’s needed for more delicate projects like precision painting. Think about how you want your robots to function and the multiple tasks you might require of them before committing to buying a fleet of robots.
Final Thoughts
Companies can and will save substantial amounts of money by taking the requirements of a robotic future into consideration when making business decisions today. Ultimately, businesses that do not embrace this robot revolution will be left to play catch-up when robots become indispensable in helping manufacturers stay competitive and innovative. Start the process for your plant or facility now so that you’re a part of the revolution, rather than being upended by it later.
ABOUT THE AUTHOR
Josh Tuttle is the Business Development Manager at Aerobotix, an innovative leader in advanced metrology and robotic solutions for the aerospace and defense industries. The company specializes in the creation of cutting-edge automated robotic solutions for high-value, high-precision components, aircraft and vehicles.
applied Cobotics has taken another innovative step forward with the introduction of the automated storage and Retrieval system (asRs). This brings another piece of the automation tool to our collaborative robot system, offering more production power, flexibility, and ease-of-use. This is especially important to small- and medium-sized enterprises (sMes) that are looking to incrementally increase their automation.
By PBC Linear
Within the factory of the future program at Applied Cobotics, we have readily embraced the cobot (collaborative robot) nation. Initially, as we were implementing this new technology, we found that one tray of parts did not take advantage of the cobot’s full potential. We quickly realized that we needed some type of lift automation, combined with a storage and retrieval component, that would assist the cobot for much longer unattended production runs.
The solution? We designed and built the ASRS to enhance any robot's productivity, run a higher mix of parts, and ultimately recoup a greater return on investment. Collaborative technology for more production power

The ASRS assists most cobots and other robotic applications by providing a continuous arsenal of machinable parts over a much longer time frame. It does this by consistently loading and unloading dunnage trays onto the robot accessible work area, eliminating the need to manually
replace each one. The resulting boost in cobot production is 10- to 20-times that of standard means.
The ASRS from Applied Cobotics features a vertical lead screw-driven shelf, and a horizontal tray loader/unloader. In addition, tray rack towers engineered for the ASRS offer open-spaced shelving that accommodate various part sizes up to 18-inches in height. The rack towers are also capable of holding up to 17 trays. Customized dunnage parts trays can be acquired either through our 3D printing and thermoforming capabilities. For DIY customers, purchase one of our 3D Platform or BCN3D printers and create your own custom trays!
The ASRS works by assisting a robot in longer parts runs. Without the ASRS, a robot will stop running as soon as it finishes that one tray of parts. With the ASRS in place, the robot system is capable of unmanned, continuous production. As the cobot finishes each set of parts on the tray, the tray loader slides the finished parts tray to its predetermined position, and then pulls the next one onto the shelf. Once the tray is pulled into position, the cobot is alerted and automatically resumes its project tasks. Depending on the parts, a project can operate unaided overnight, making each one a potential lights-out automation run. Built-in motor encoders provide highly accurate motion, maintaining the tight tolerances that cobots require.
All together, these features provide reliable and safe load-handling for any part type or size. The ASRS can easily be implemented to automate most CNC lathes, Mills, and many other types of robotic-aided manufacturing for long-running, unattended operation.
ASRS is offered as a package deal with an attached cobot, or as a single component.
Flexibility in Automation
As customers begin to request more custom components, shorter part runs, and cheaper costs, there is an increasing demand for flexibility on the shop floor. The Automated Storage and Retrieval System from Applied Cobotics, in tandem with many types of robots, provides project managers and operators that flexibility. While Applied Cobotics offers the ASRS and cobot as a package deal, the ASRS can be purchased on its own, providing an essential asset to existing automation systems. It offers its own adaptive features such as: » Compatibility with any cobot/robot with I/O ports » Compatibility with any cobot-suited application » Multiple parts programming options within one job run » Production of an entire cart of trays in conjunction with robots » Pallet jack accessible design for portability » Mobile tray rack that can be moved from station-tostation and locks easily into place
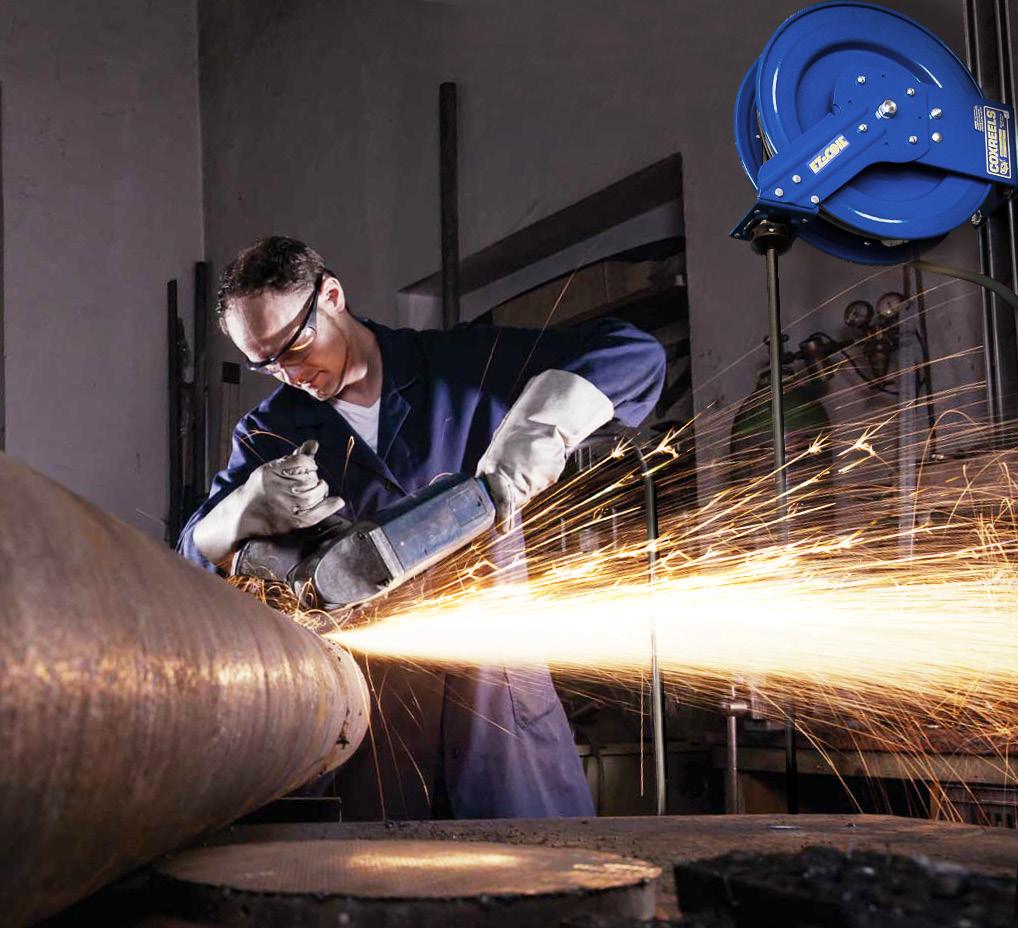
Easy to Use and Install
The ASRS from Applied Cobotics is easy to use, and does not require any extensive programming knowledge. For CNC milling machines, our experience has proven that the time investment is less than one day to fully implement the ASRS/cobot package. Other ease-of-use features include: » HMI touch screen display for easy control » Software Interface that can be programmed in a few simple steps » Removable cart for station-to-station mobility » Optional camera and monitor screen allows operators convenient production viewing
Additionally, the safety characteristics of cobots have been applied to the automated material lift system. If a human worker or any object gets too close to the ASRS, a floor sensor will alert the ASRS to pause its motion until the area is clear again. Use any of the links below to find out how Applied Cobotics is making automation easy for SMEs.
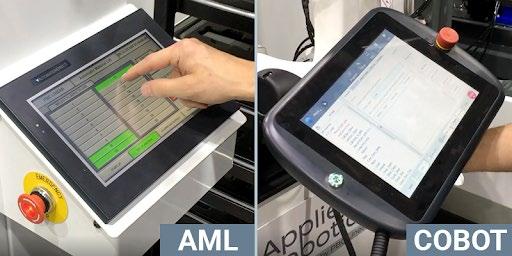
For more information, visit www.pbclinear.com.
quality matters.
every time.
PRO GRADE HOSE, CORD, & CABLE
REELS
SOLUTIONS FOR: AIR / WATER | HYDRAULIC | PNEUMATIC | VACUUM | WELDING | POWER