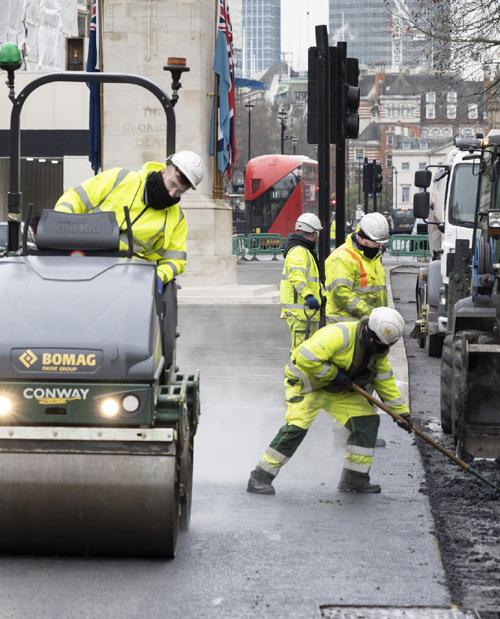
14 minute read
SOUNDING THE DEATH KNELL ON FATAL RISK
FM Conway’s Andrew Cox explains how the organisation will eliminate the 10 biggest fatal risks in the business inside 10 years
Andrew Cox
Safety, Health, Environment and Quality Director
Last year FM Conway launched a health and safety strategy like no other. It was a transformational approach that prioritises the greatest health and safety risks to the business in order to help the company achieve its vision for all people to go home safe each day without life-changing harm. But it was more than that. It was a step change-moving away from the more traditional approach using behavioural safety to something that was going to have an immediate positive impact on improving health, safety and wellbeing at FM Conway.
The strategy has a bold ambition, shaped by an indepth risk analysis of both the business and the industry to identify gaps in any previous health and safety approaches, as well as looking at the tools and measurement controls required to monitor and evaluate the true operational performance of the business and not just the lagging measuring the absence of harm.
Elimination of the risk is the ultimate aim for FM Conway, but where that is not possible, a number of safety critical controls will be put in place for each Big Risk activity, in order to create an environment where people can fail safely and learn rather than pay the ultimate price for a mistake.
It is very important that this new approach is sustainable for the business and that is why it will take full advantage of digital and technological advances to provide a high level of physical, electrical and mechanical protection for the biggest risks.
FM Conway has categorised its Big Ten Risks as the following:
Isolation and Guarding Occupational Health Temporary Works Lifting Operations Traffic and Pedestrian Interface Safe Digging Practices Occupational Road Risk Subcontractor Control Confined Spaces Working at Height
ELIMINATING RISK
THE BIG TEN IN 10 IS FM CONWAY’S TRANSFORMATIONAL APPROACH FOR ELIMINATING THE TEN BIGGEST RISKS THAT CAUSE LIFE-CHANGING HARM.
This unique approach strives for the full elimination of risks removing the reliance on human behaviour, and is designed to be revolutionary for the construction industry.
Isolation and Guarding
Occupational Health
Temporary Works
Lifting Operations
Traffic and Pedestrian Interface
Safe Digging Practices
Occupational Road Risk
Subcontractor Control
Confined Spaces
Working at Height
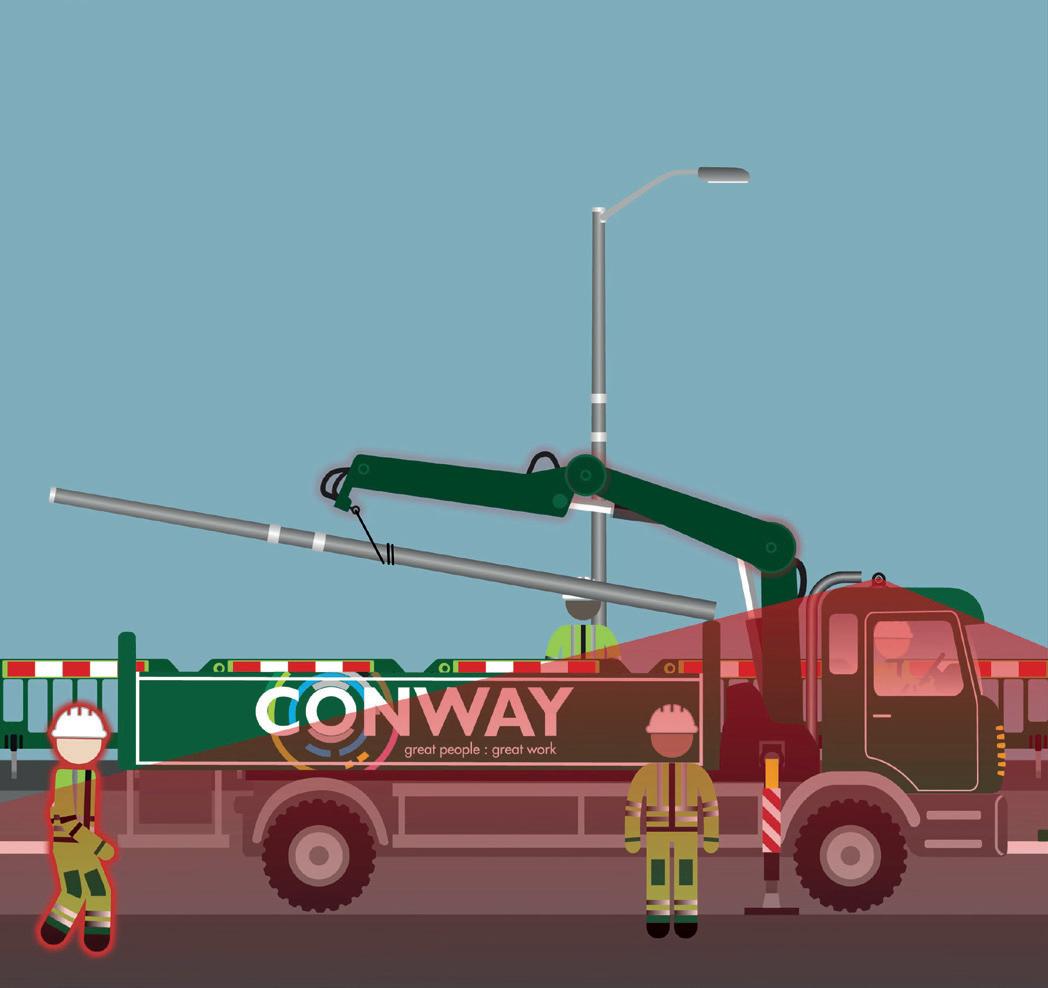
To find out more
Please call 01732 600 700 visit: www.fmconway.co.uk email: enquiries@fmconway.co.uk
The project is being spearheaded by Andrew Cox, FM Conway’s Safety, Health, Environment and Quality Director. Joining FM Conway and embracing its self-delivery was a new way of working for Andrew and that was also the catalyst for the business to start understanding what its risks were and how best to deal with them.
“Statistically speaking we were having one of the best periods of performance as a company with all the traditional lagging indicators such as lost time accident rates and RIDDOR Rates at historic lows. But even with these historic lows our traditional reports and approach wasn’t explaining why certain things were going wrong, including, tragically one fatality. That’s when we realised we needed to do something different.”
FM Conway began to think big risk. “This frustration made us change our overall philosophy. Every single year people have been dying the same way and as an industry, we have spent a huge amount of time and resource focusing on individual behaviour and not fixing the problem. We are relying on the fact of hoping people follow the rules and don’t make mistakes and the reality is that we are all human and we will make mistakes, and that is ok. We needed to create a workplace where people can make mistakes and not have to pay the ultimate consequence for their mistake.”
Through his work, FM Conway adopted a philosophy of preventing accidents in the first place and in particular fatalities. To achieve this, the first step was to bring together and analyse a raft of data to help identify and prioritise activities most likely to cause life-changing harm. And then to deliver solutions for them based on the reverse triangle with an unrelenting focus on elimination, substitution and engineering control.
New dashboards and risk barometers were then created to help actively manage the Big Risks by demonstrating if they were rising within the business. This provided an opportunity to respond to where the potential harm could be rather than relying on traditional measures such as an LTI rate, which we know do not tell you where your next big incident could be.
The second part of the project was about putting the safe systems in place in the business to further manage the risk. “That is when the ‘Big Ten in 10’ was first born,” says Andrew. “After that, our plan was to consider where we could remove people from the equation or if that wasn’t possible, put safety critical controls in place.”
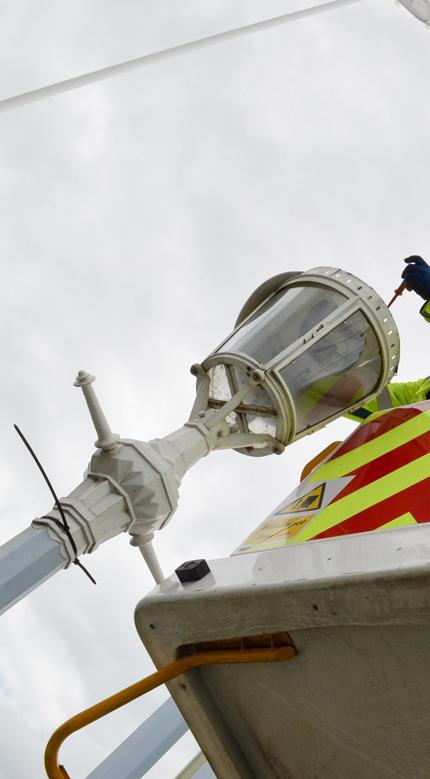
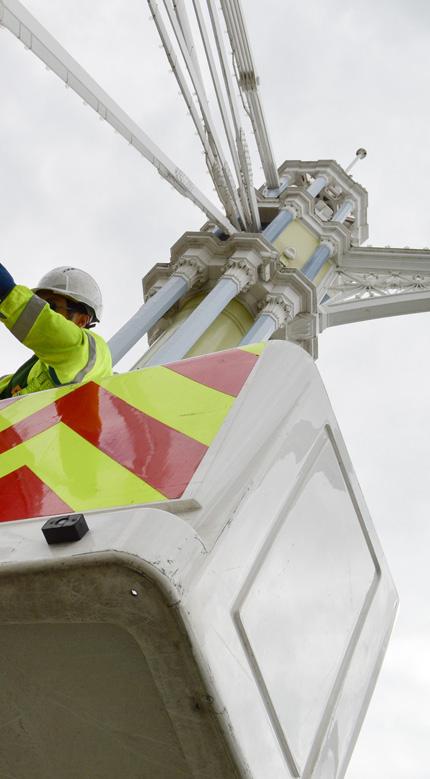
One example of how a safety critical control was achieved, was the automation of road sweepers. FM Conway’s data demonstrated that sweepers, which spend 50% of their time in reverse while on site, making over 30,000 reversal movements on projects every year and present a risk to workers and MOP’s behind them. The automation includes a proximity radar that detects when a person is within a certain distance of the machine and then applies the brakes.
“It is just one example of the many safety critical controls we have been able to put in place as a result of identifying the risk in this new way of working,” says Andrew. Other examples include making confined spaces safer after it was realised that FM Conway workers are in and out of manholes over 40,000 times a year. A HD scanning camera now surveys the manhole automatically without the need for anyone to have to climb in one at all. The need for ladders has also been removed from many sites after it was found that working in height with ladders resulted in a number of fatal accidents across industry every year. The business has removed of over 111,000 activities of work from ladders with these changes. “As a result of all this work, we have managed to already achieve over five million risk reductions across the business. It is a massive step forward. If we can see where the risk is, we can reduce it at source and make a change for better. These leading indicators are the measures of success that the business now monitors and not that we have gone 300 days without a RIDDOR accident. We are moving forward with answering the question ‘are we safe or are we lucky’? And we can now say that with actual improvements in elimination, substitution and engineering controls we are definitely getting safer and enabling people to go home safe each day.”
While behavioural safety isn’t the focus anymore, there is still an emphasis placed on what the individual workers are doing as well. “Everyone from management through to operations has five lifesaving rules they follow when considering a big risk activity which is important whilst we work towards building safety critical controls for each risk over the next ten years,” says Andrew.
But the work doesn’t stop there. Technology to support advances in safety critical control is advancing at a pace. Some of this work is centred around using sensors to enhance safety. An example is sensors that will form part of an intelligent side guard that will fit on the side of maintenance vehicle to inform the driver when cyclists are within a certain distance. “This is a really exciting use of Artificial Intelligence and other technology to make further meaningful risk reductions.”
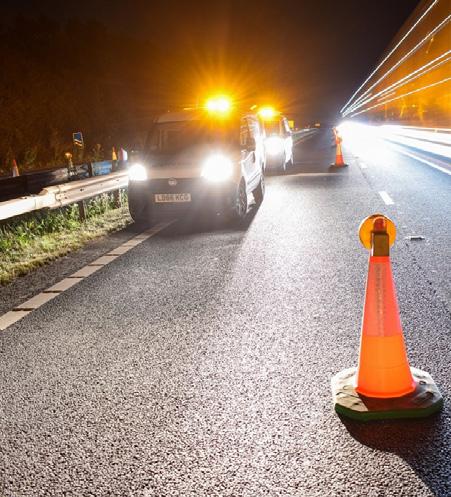
Partnering with specialist glove manufacturer STALSEN and using a glove originally designed for the automotive industry, J.M. McCann successfully introduced new-to-the-market hand protection for the workforce on the M27 project with the support of Bam Morgan Sindall Infrastructure Joint Venture (bmJV).
This new glove has replaced standard issue work gloves in order to reduce the risk of hand injury, improve hand health, reduce environmental waste and improve operative satisfaction and uptake.
The product has been in use since January 2021 and as a result of its strong performance, seen the M27 project presented with a Highways England Blue Star Award for safety innovation – an accolade awarded to projects which demonstrate “exceptional performance or new initiatives not widely used on other sites.”
An evolution in the approach to hand health is overdue for the UK’s civil engineering sector in the view of our Project Health and Safety Manager Dave McPherson, and he sees STALSEN’s product as a great way to solve common problems for site operatives across the country.
“Occupational health can be overlooked in our industry and when observing the levels of hand protection already available, standard-issue gloves are, more often than not, seen as disposable items rather than a technical piece of equipment. We felt that this mindset needed to change to better protect workers and minimise waste. The way we see the industry achieving this is by moving away from low cost gloves to a higher end product in order to reduce stock turnover rates and evolve and improve levels of protection,”
For Dave, addressing the underlying reasons why operatives might not wear the correct hand protection for each task is paramount. Involving the workforce in the innovation has helped to create a solution that not only improves the provision of safety equipment, but helps to challenge perceptions and attitudes towards wearing Personal Protective Equipment.
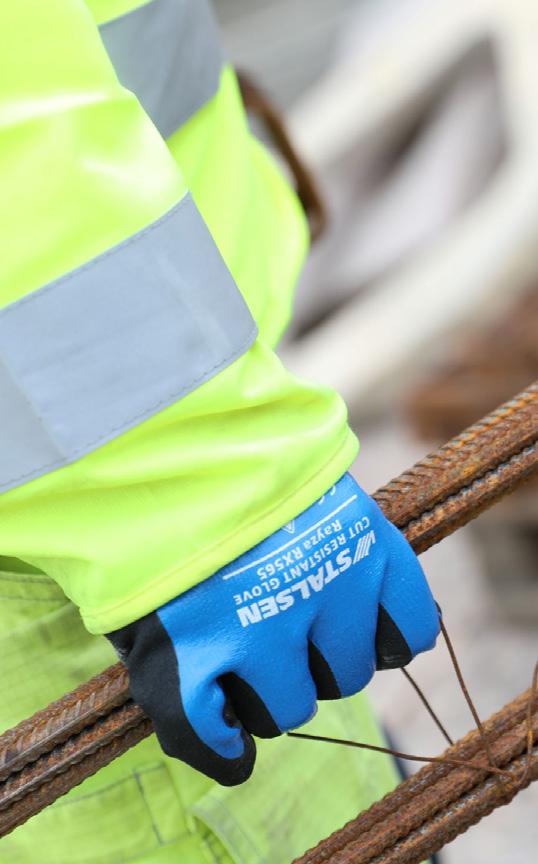
RECOGNISED FOR NEW SAFETY INITIATIVE AS M27 MOTORWAY UPGRADE PROJECT IS PRESENTED WITH HIGHWAYS ENGLAND BLUE STAR AWARD
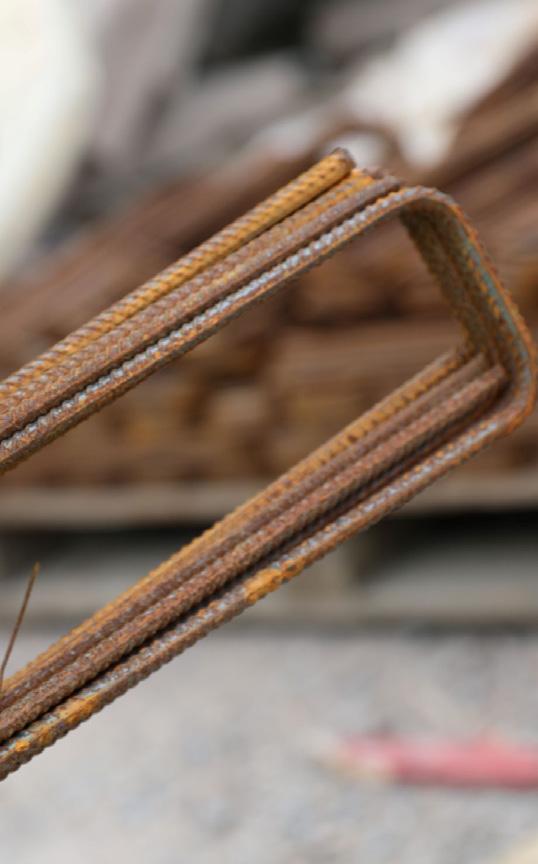
After McCann introduced an industry-defining safety initiative on the M27 motorway upgrade scheme between J4 – J11, we’re delighted to announce that the project was recently awarded a Blue Star Award by Highways England for safety innovation.
“We consulted our workforce and much of the feedback we received suggested that no single glove offered the right levels of comfort and dexterity for multiple jobs. This means that operatives frequently change their gloves throughout the working day, often multiple times per hour – creating barriers around practicality and convenience. This can create a vicious circle because if products are not popular with operatives and they don’t like wearing them or they wear the wrong glove for a given task, we can end up with a higher probability of accidents. All of this makes it harder to achieve high levels of compliance – creating an ongoing challenge around ways of thinking about hand safety,”
He continues, “If adequate protection isn’t used, then common injuries such as cuts and grazes can occur far more easily. There’s also a significantly increased risk of developing serious long-term health problems associated with uncontrolled exposure to concrete or other hazardous materials including sensitization to chemicals and occupational dermatitis – causing hands to crack, itch and bleed. These health problems can take root without any sign and it is this lack of immediate signals which means that often no action is taken in the short-term to prevent them. What we want to do is make hand protection more convenient in order to lower these risks.”
A recent report by the Health and Safety Executive showed that the construction industry has seen an estimated 60,000 Musculoskeletal lost time injuries per year in the last decade – of which roughly 20% are hand injuries. As a result, workers are twice as likely to develop dermatitis when compared to other industries. For Dave and our team, reading these figures made everyone realise that an industrywide change was long overdue.
Dave made contact with specialist glove manufacturer STALSEN after seeing their Rayza RX565 product online – a glove commonly used in automotive manufacturing. This model of glove, most notably adopted by a large automotive manufacturer, offers uncompromised levels of dexterity while offering water resistance, high levels of grip and protecting hands against cuts and chemicals.
It was clear that by utilising STALSEN’s expertise in glove innovation, a longterm solution could be found that would revolutionise hand safety for site operatives in the civil engineering industry – as STALSEN’s Director Patrick Tydeman goes on to explain.
“We approach all hand-based problems in the same way,” says Patrick. “We’re about more than just the glove and always go above and beyond to find the right answer for each and every customer,”
“Our mission is to make hand injuries history through tailor made solutions, which can only be achieved by listening to the customer and applying our many years of knowledge and experience – as we did when we were approached by Dave and the team at McCann,”
Patrick continues, “The beauty of the RX565 is the story of innovation that formed it’s three-layered design. The first layer is a lightweight lining offering high levels of cut resistance and comfort. This is then covered with a nitrile blue coating which provides an effective liquid resistant barrier before a final black textured nitrile coating to enhance the grip and oil resistance,”
“Crucially, all of this protection is achieved without sacrificing dexterity – which is vital, so that the protection nor the comfort inhibits the functionality of the glove. Using gloves which are too cumbersome makes handling objects or performing tasks incredibly difficult. The RX565 is an 18-gauge liner so it’s very lightweight, allowing wearers to feel what they’re working with while knowing they have the protection they need.”
Following on from the success of an initial 4-week trial, the product was not only commissioned for use for all operatives on the M27 – delivered by bmJV – but has now been adopted by us as our standard issue hand protection across all of our concreting operations across the UK.
“We’re delighted to have introduced a new level of safety to the industry through McCann. This really is a game changer for civil engineering and construction and for me, seeing the product recognised by Highways England is testament to our team’s ability to innovate and think outside of the box.” adds Patrick.
Dave is delighted with the results achieved to-date – with STALSEN’s product making an instant impact on both site safety and attitudes towards adopting hand protection.
“Since introducing the new glove, the project has reduced glove consumption by over 60% and reduced non-compliance with hand protection requirements to zero. This is fantastic to see,” says Dave.
“Partnering with STALSEN has enabled us to achieve our goal of improving hand health standards not just for this project, but for future projects as well, and we’re delighted to see the M27 scheme awarded the Highways England Blue Star Award in recognition of this innovation. Maintaining good hand health is vital for the industry as a whole both in the short and long-term, and we look forward to seeing this glove adopted by further McCann and bmJV projects in future.”
Victor Johnson, Highways England’s Project Manager for the M27 motorway upgrade scheme, said: “We are extremely proud that the M27 is associated with this brilliant innovation which fully complies with Personal Protective Equipment (Enforcement) Regulations 2018. The glove’s adaptability has proved to be a major benefit as it is multi-operational while also being waterproof, cut resistant, light and supportive of dexterity. It is even known to be resistant to lean concrete. The glove is more efficient by eliminating the need to replace it for various tasks undertaken by the same workforce and has been a huge asset in our working practices.”
Nigel Fullam, project director for bmJV on the M27 motorway upgrade scheme, said: “Enabling and supporting our supply chain to bring innovations to life is a key part of our approach. We’re delighted to have supported the trial and subsequent adoption of these gloves on our M27 project,”
“The safety and wellbeing of everyone involved in delivering our schemes are of paramount importance to us, and by working with McCann we have reduced the potential for hand injuries on our M27 scheme, we’re also making our operations and the industry a safer and more productive environment.”
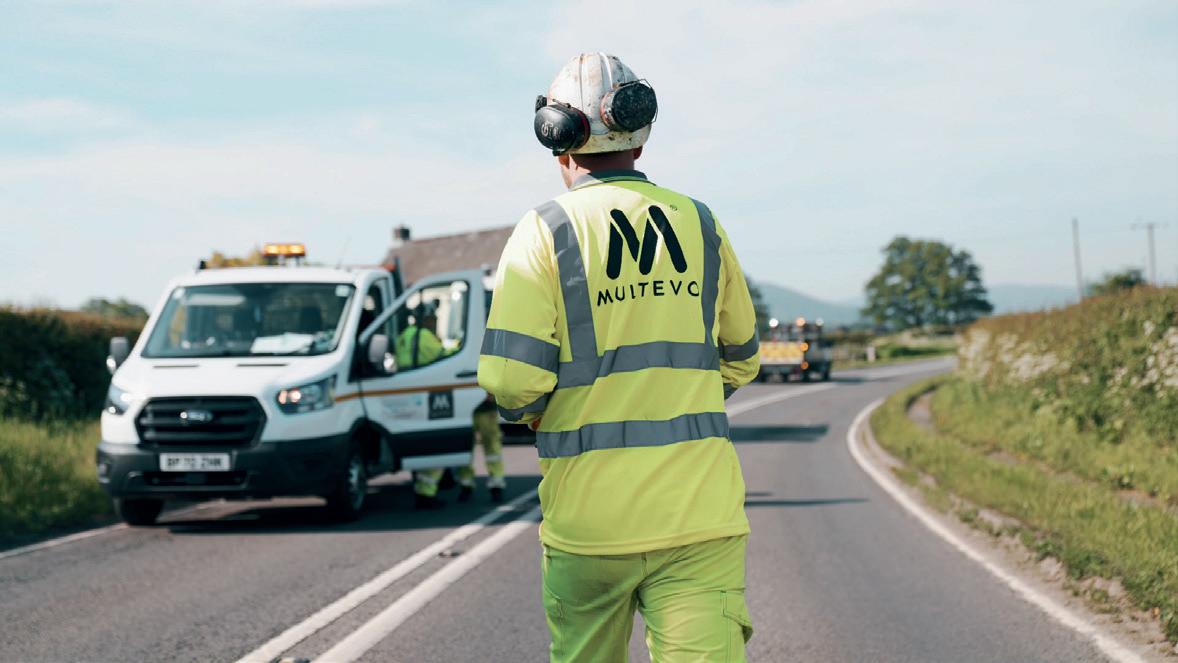
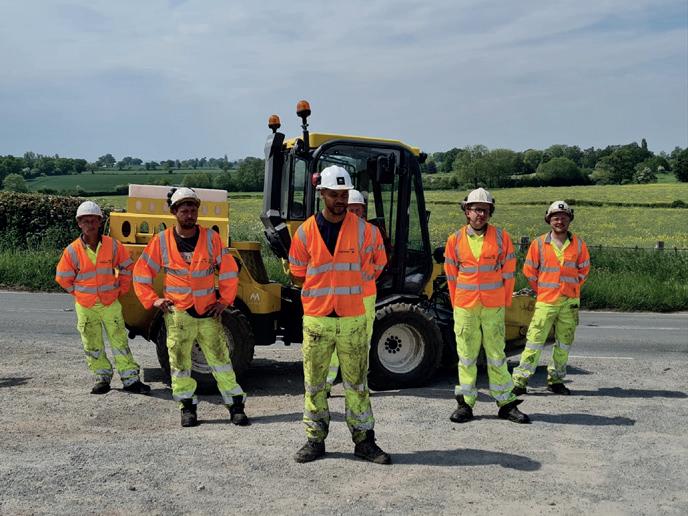