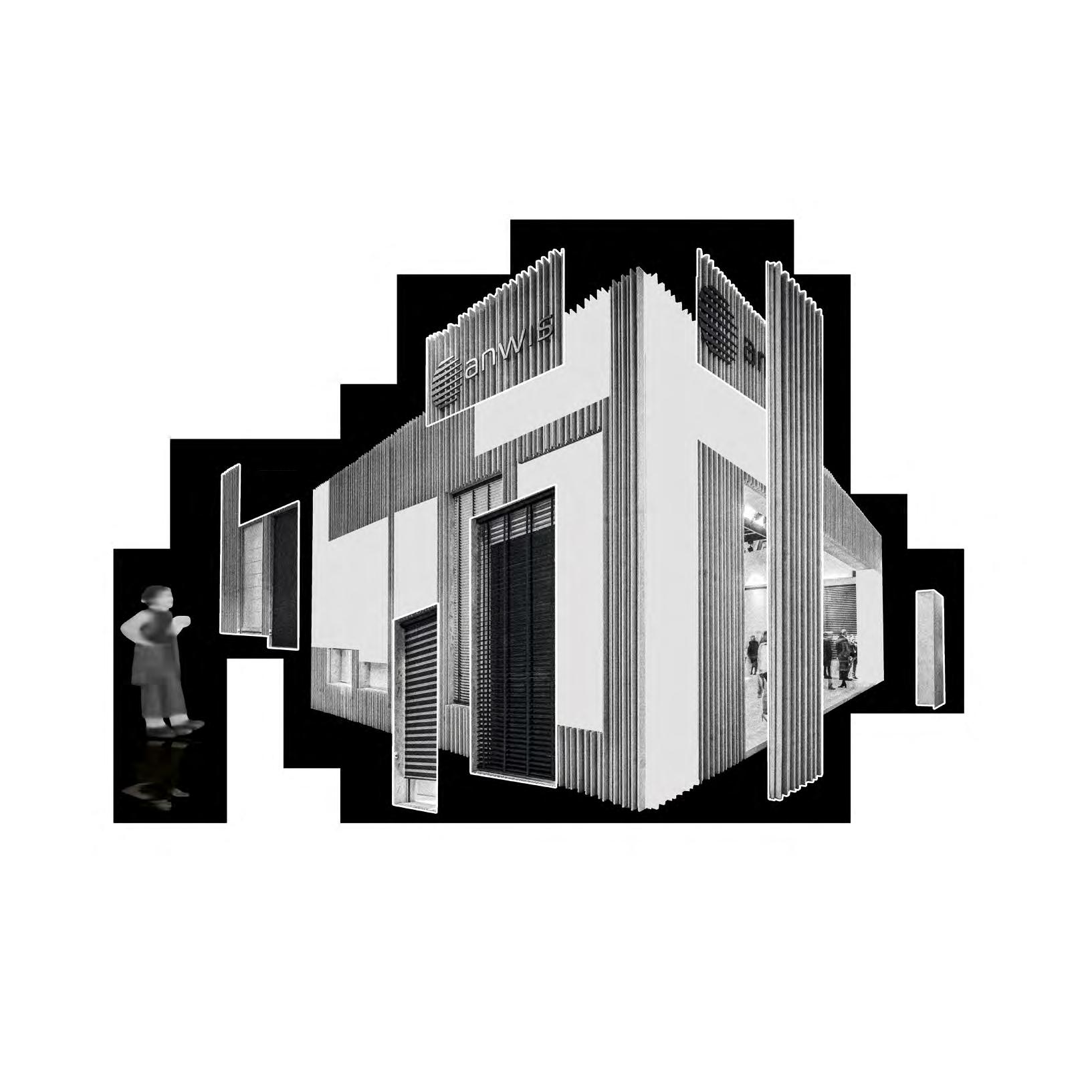
6 minute read
THE ASSEMBLY OF A STAND AND ITS PRODUCTION - A PRACTICAL GUIDE
Achieving success, which partly results from being able to expect the unexpected, largely depends on how carefully and painstakingly prepared the elements of the stand are before they can be assembled.

Advertisement
An exhibition stand comprises many elements and it is the adequate preparation of those elements that can guarantee a professional and problem-free assembly of a stand during the exhibition show. The number of elements and their level of complexity depend on the sophistication of the project that a client approves. In order to provide our clients with stress-free solutions, we have described every single stage of the process of creating an exhibition stand in detail.
9 EXPERT OPINION
THE STAGES OF CREATING A STAND BY SMART DESIGN EXPO
The preparation works consist of many stages and the following departments of our company are involved in them:
- the technical managers - the assembly department - the carpentry workshop - the main warehouse - the warehouse for electrical equipment - the supply department - the logistics department
stage 1
The indispensable technical documentation
This stage is all about the preparation of the technical and production documentation in line with the requirements of the design folder. All construction elements as well as the furnishings of a given stand such as the furniture, counters and lighting system are included in this folder. Preparing the design folder in an adequate way is a crucial part of the production of the stand as it affects the entire endeavor, especially when it comes to the precision and timeliness. That’s why we hire technical managers together with the designers who are known for their meticulous attention to detail and the high quality of their work. Thanks to that, the production department always has precise instructions that do not require any clarification or reconsideration.
stage 3
A face-to-face meeting - discussing the technical documentation
When the design folder is ready we arrange a meeting of the design department or the technical managers with the assembly foreman who is in charge of the stand. The head of the carpentry workshop takes part in it too. This stage is all about the technical details and clearing up any doubts that appear. We discuss a wide variety of issues such as the structure of the walls, ceilings, floors as well as the steel, aluminum or wooden elements, including the pieces of furniture which are to be manufactured both in our in-house workshop and by different subcontractors providing for example paint shop, upholstery services or iron - worker.
stage 4
The stand planned down to the last detail - from boards to screws - preparing the orders
Then either a designer or a technical manager (depending on whether we create a stand designed by our designers or our Partner provides us with a design) inputs the data into the CRM system, which is a great tool that enables communication between different departments and allows us to order various components of the stand. An individual ID number is assigned to every single element and it used to identify the given item throughout the whole process from the CRM phase to the production and supply phase to the unloading phase, which takes place on the fairgrounds. Orders - ready, steady, go!
The baton is passed to the supply department and the warehouse department, which is responsible for placing orders for the elements of the stand or renting them. In order to offer a truly comprehensive service, all the following departments are involved in this stage: electric systems, carpentry workshop, supply department, logistics department, truck drivers, CNC, assembly team, furniture warehouse, warehouse of constructions and consumables as well as graphic department. Since we want to guarantee the highest quality of our work, as many as 8 different employees are responsible for placing orders for a given stand. Each of them specializes in the sophisticated niche trade fair industry.
stage 5
Producing as many elements as possible
The material used for creating the elements of the furniture or the construction is delivered to our company and it is stored in the warehouse. Then the carpentry warehouse, the assembly team or the construction department get the go-ahead to issue the production orders so that the exact calculation of the man-hours and the costs of the materials can be prepared for every single stand. Each production order has its own ID number, which is assigned by the CRM system. The key principle which we apply in our company is to get as much work done in the in-house workshop as possible so as to facilitate and improve the assembly process on site. The team which prepares a given stand almost always takes part in its assembly. This practice of ours eliminates the mistakes along with the unexpected events on site and it saves a lot of time. What is more, the team assigned to the assembly of the stand knows exactly what to do so that the works can proceed without any problems. It is crucial for us since every single minute of a delay or uncertainty may potentially lead to unpleasant consequences - it directly translates into the risk of missing the deadline. That is the reason why we try to prepare all elements of the furniture, friezes, partition walls, shelves, racks, display cabinets in our production facilities as these prefabricated components, just like Lego bricks, can easily be put together on site.
stage 6
Double-check, that is to say quality control
The elements that we create undergo quality control, which consists of two parts. It means that every element is vetted for quality twice - first by the person who creates it and then by the quality control inspector, who using strict criteria decides whether it is fit for leaving the production facilities. The quality control inspector signs the production order and hands the approved order over to the warehouse. Then the element is secured against damage during the transportation and it is transferred to the main warehouse by the department of internal logistics. The calculation of the costs of the materials used to create the given element is prepared too.
stage 7 The final touch - lighting system, decorative elements, graphics
This is when the lighting system, decorative elements, furniture and graphics come into play. These final touches are equally important as the walls or the floor since without them the vibe and the atmosphere of a stand are not convincing enough to build trust in the client’s brand.
stage 8
Packing and loading the stand onto a truck
The components of the stand which are ready to be loaded onto a truck can be found in the so-called accumulation bin. One more complete check is run in order to be sure that no element is missing. The number of trucks is also reconsidered to make sure there is enough room for everything. Then the transport is organized and the loading process is planned. The stand is ready to leave the company. The rest is in the hands of our assembly workers!
As you can see, creating a stand requires many employees to be involved at many different stages of the production process. Due to the human factor and the high risk of human error, trade fair industry demands great concentration, remarkable organizational skills and an exceptional degree of professionalism, especially when it comes to the stunning and sophisticated stands.
WE BUILD STANDS ALL OVER THE WORLD!
the USA 4 stands
Heimtextil, Domotex, IMM, Maison&Objet, Orgatec, IFA, MWC, WTM, Cersaie, Innotrans, ICE Totally Gaming, ITB, In-cosmetics, Euroshop, Interpack, BAU, Eurosatory, Automechanika, Medica, Ambiente, Light+Building, Buchmesse, Kind&Jugend, Spielwarenmesse, Frontale. Expo Real, SIBOS, SAIE, Batimat, IAA, Embedded World, Achema, Intersolar, KBIS, Salone del Mobile, Ebace, Electronica, ISPO, R+T, Eular, Paperworld, Budma, Interzum, Bauma
14 Birmingham 23 stands