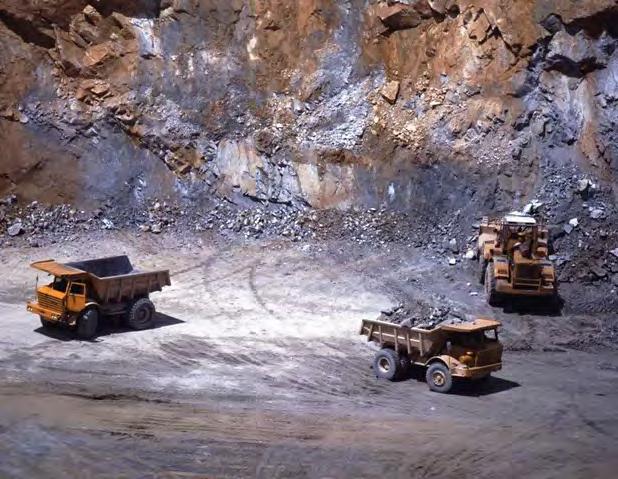
4 minute read
US Steel Iron Ore Could Bring New Boom
SURFACE MINING
US Steel Iron Ore Could Bring New Boom
us sTeel is seT To produce TaconiTe pelleTs ThaT could poTentially save the iron ore mining industry and create more job opportunities. For almost a century, Minnesota mines have produced iron ore not just for US Steel mills but also for other major corporations. These mills then turn ore, coal, and limestone into cast iron and eventually steel.
ROBEL RAMOS
However, this process is becoming obsolete as cheaper and more energyefficient plants utilizing electricity and scrap metal become the new norm. Furthermore, as governments increasingly call for greener and cleaner alternatives, traditional steelmaking’s future is beginning to look a bit uncertain. The Pittsburgh-based company is set to put in $150 million in its Keewatin plant. This plant produces high-grade iron ore to power electric furnaces or mini-mills. These mini mills create high-quality steel and need high-quality iron to supplement scrap metal.
“The biggest advance in modern iron ore processing technology is what’s happening right now in the Iron Range,” said Kevin Kangas, Director of the Natural Resources Research Institute at Coleraine, part of the University of Minnesota. Duluth. “This is a huge step forward for Minnesota’s iron ore industry,” he added.
Cleveland-Cliffs, the most significant player on the Iron Range, is already producing highgrade iron ore pellets.
The future of the Iron range depends on whether these two major players, which have been associated with blast furnace steelmaking, make it or not in this new industry. It is important to note that the mines found in this region have always been in the hands of their steelmakers.
“We are on Pins and Needles on the Rail Belt as the Steel Industry Turns Around [electric furnaces]. Are we going to be part of the long-term future of the steel industry? That worries me,” said John Arbogast. Arbogast is the 11th district representative for the United Steelworkers of America, which represents workers at all but one of the state’s six taconite operations.
Minnesota’s taconite industry is still a pillar of the Iron Range economy despite having diminished from its prime.
In its heyday, this industry contributed about five thousand jobs. This figure may have dwindled to four thousand jobs but, on a positive note, has remained steady for the last two decades. The mining industry provides one of the highest-paying jobs in the country and the industry forms the Iron Range’s tax base.
Keewatin mayor Mike LaBean said, “Mining is still the straw that stirs the drink.” LaBean was a miner until he lost his job in the early 1980s. Keetac, a site near Keewatin City Hall, is one of the many taconite sites in the area. It was built between the mid-50s and mid-70s and is the smaller of the two Iron Range mining and processing opera-
tions owned by US Steel. Keetac has 400 workers and will continue producing traditional seeds. Taconite is about 30% iron and is mined from the Keetac site and then fed into a large crusher. The iron is culled from the pulverized ore using magnets. It is then molded with clay into smaller pellets containing approximately 66% iron.
In August, US Steel started expanding to take this process one step further. If Keetac’s new wing begins operating by 2024, the facility will still produce new pellets with 68% to 69% iron. They will also have less silica as compared to traditional pellets thereby making them more suitable for use in electric furnaces.
Mike Bakk, director of operational readiness at the iron ore factory in Minnesota said, “This is probably the most exciting thing that has happened in the Iron Range in 50 years.”
Electric furnaces are increasingly gaining a foothold in the industry. In the 1980s, electric furnaces gained traction - especially in the US where scrap metal is abundant. First, they produce low-grade steel products like rebar for reinforced concrete. However, the influx of newer technology prompted small-scale mills to enter the premium steel market. By 2021, 71% of US steel production comes from electric furnaces - a 47% increase from 20 years ago. These figures come from Carnegie Mellon University’s Iron and Steel Research Center in Pittsburgh.
Traditional steelmaking’s share in the market has plummeted and the number of blast furnaces in the country has dipped from 60 in 1990 to 21 in 2021. Small-scale mills employ electrodes in order to melt scrap metal, together with pig iron and DRI or direct reduced iron, both of which are critical in making high-quality steel.
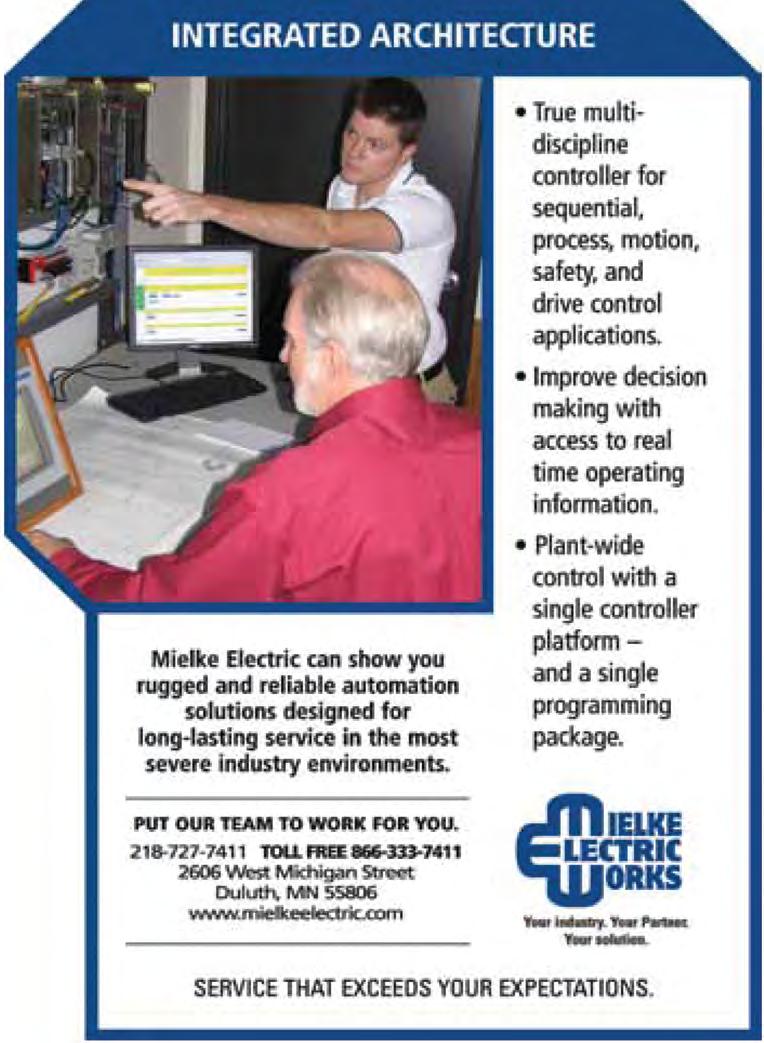
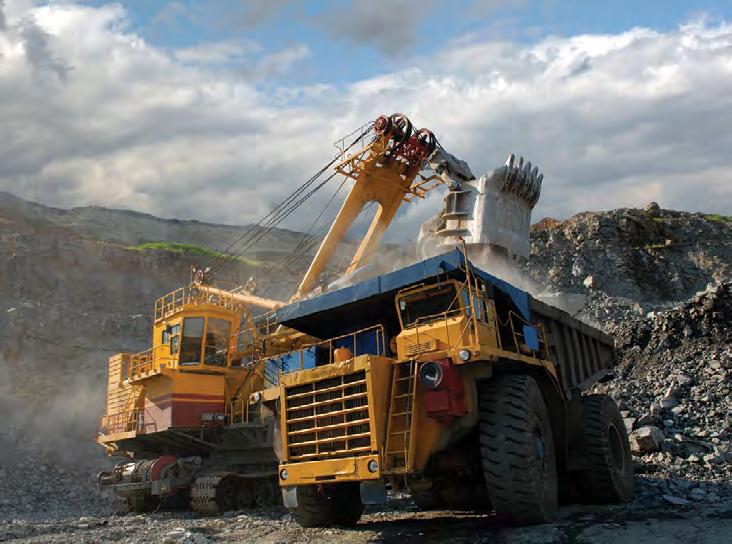
Proud to be your reliable partner.
19260
We have long supported the region’s mining industry by providing safe, reliable and competitively priced electricity. In 2021, half of the energy we provide to all of our customers will come from renewable sources. Together, we power northeastern Minnesota’s economy.
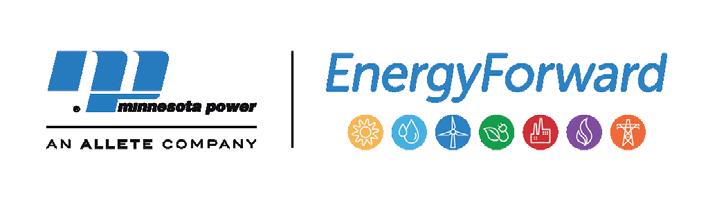