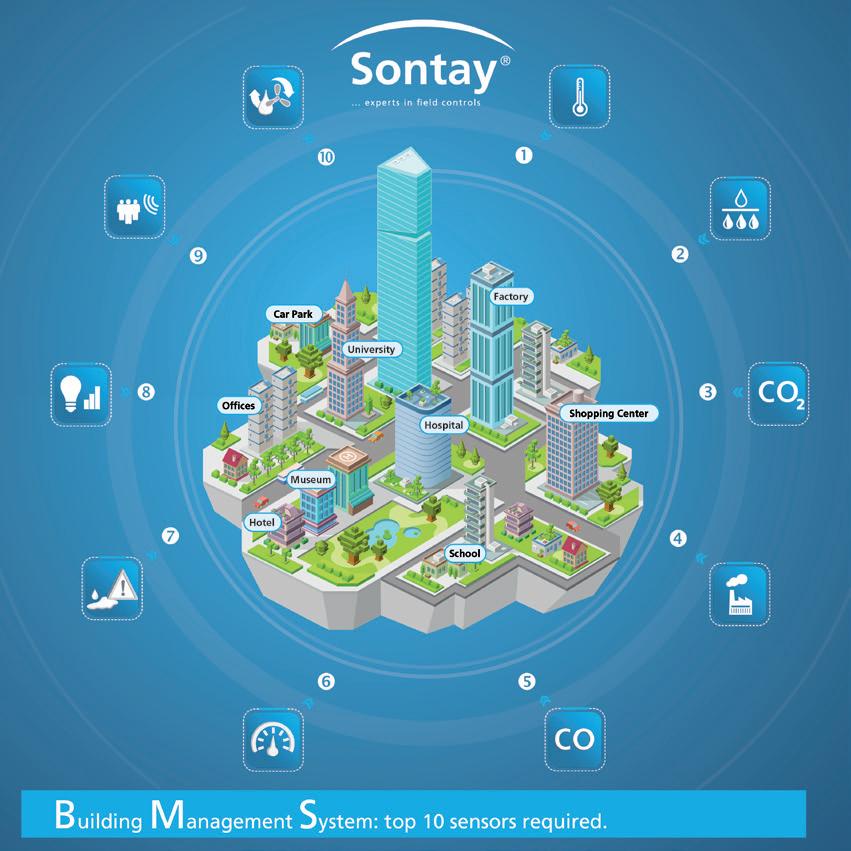
14 minute read
Intelligent Buildings
A sixth sense
From temperature to building occupancy, water to air quality, and gas to lighting usage; sensors are having an increasing effect on a building’s operational performance. Stacey Lucas, commercial and marketing director at Sontay, explains the role each sensor plays in achieving this interior idyll.
Advertisement
s people return to their workplaces following the government’s A lockdown measures imposed as a result of the Covid-19 pandemic, there will be unprecedented focus on ensuring the offices, factories and warehouses employees reoccupy hereafter are as bio-secure as it is possible to be. Building sensors, installed as part of an efficient central management system, offer an ingeniously smart and effective way of remotely monitoring elements such as temperature, air quality and ventilation to help maintain a healthy indoor climate for the occupiers’ comfort and peace of mind.
Sensors also give property owners more control over energy usage; a benefit that not only helps reduce heating and lighting costs, but also facilitates a significant reduction in a building’s carbon footprint. Their usage could therefore be crucial in driving environmental initiatives, such as the UK government’s pledge for carbon-neutral status by 2050. The following is a guide to the ‘must-have’ sensors for a healthier, safer, energy-efficient building.
Temperature sensor Historically, temperature has been viewed as crucial to occupancy comfort in buildings. In the workplace, such contentment results in improved productivity and fewer sick days. Sensors can help maintain the ideal indoors temperature, which for an office environment, is found to be around 22°C.
Humidity sensor Relative humidity can have a negative effect on indoor temperature settings. If not controlled, it can make a room feel hotter or colder than the actual temperature reading. In order to maintain the desired indoor climate, the humidity reading should be around 50%. A humidity sensor will help achieve this.
CO2 sensor The Covid-19 pandemic has focused a lot of attention on the amount of indoor space people should be allowed to share in order to maintain distance and prevent viral spread. A CO2 sensor provides a clear visual indication of when a workplace requires ventilation due to deterioration in the indoor air quality.
When we exhale, we emit CO2, which if left unchecked in a busy office environment for example, can lead to headaches due to increased discomfort levels. A CO2 sensor with an LED traffic light-style display can help alleviate this issue. When showing green, for instance, the sensor is indicating that a room isn’t over-occupied and the risk to air quality is low.
Should the sensor show amber, it’s a sign that windows require opening or fewer people need to be in the room to maintain the same healthy indoor environment. When the sensor turns red it is a call to action, as it indicates there is not enough ventilation in the room. At these last two stages, if a sensor is connected to a building management system, it will activate the relevant vents.
Air quality sensor This monitors levels of airborne volatile organic compounds (VOC), pollutants which are found in paints and other building materials. This sensor has particular relevance to the current climate, with the increased use of hand sanitisers, aggressive cleaning products and detergents potentially adding to the release of harmful VOCs into the interior atmosphere.
CO sensor In a domestic or workplace setting, high levels of carbon monoxide can be life-threatening. A lot of CO sensors are installed within indoor car parks where there is high retail footfall. In these environments, the sensor will trigger ventilation systems into use when safe pollution levels are exceeded due to car exhaust fumes.
Water detection sensor This is what we call a behind-the-scenes sensor, which has come into its own during the recent coronavirus crisis. With many people recently forced to work from home via PCs, tablets and other digital devices, data centres have been vital to maintaining remote operations and ensuring staff retain contact with colleagues and their employers.
A water detection sensor takes the form of a strip of tape. This is placed in a floor cavity beneath the data centre in order to detect any presence of water. Should this situation arise, the sensor will short circuit the server and trigger a response from a connected building management system, which will decide whether to shut down the server or notify the relevant maintenance team.
Pressure sensor Behind-the-scenes in a building management system application, liquid or air pressure sensors are used in either pipe or ductwork. These indicate a drop in liquid or air pressure, which usually means in relation to air pressure, a fan has stopped working. This can have a debilitating effect on a building’s ventilation, therefore a sensor will alert a fault to a management system and the incident can be investigated accordingly.
Light level sensors Again, this is relevant to the recent nationwide lockdown, when many offices in towns and cities remained empty, whilst within the buildings themselves lights and other energy sources continued to burn unmon
itored. An estimated 40% of a building’s energy costs are attributed to light usage, therefore installing a sensor which operates lighting based on a building’s occupancy and interior light levels has financial and environmental benefits.
Occupancy sensors Although considered an effective security item to alert the presence of intruders in a building, our selling-point for occupancy sensors is their ability to detect ‘people presence’ in order to regulate temperature control or air conditioning usage. Such services can be smartly switched on or off depending on how well occupied a building is. This can lead to huge gains in terms of cost-savings and enhancing a property’s sustainable credentials.
Air velocity sensor This is often used in cleanroom applications such as hospital operating theatres. Outside or polluted air is prevented from getting into these hygiene-critical areas in a process that involves over-pressurising the rooms. An air velocity sensor, along with a pressure sensor, indicates when a room is at the required velocity pressure and acts as a warning device if levels begin to drop.
Though relatively small in size, building sensors can have a huge part to play in ensuring properties, particularly workspaces, are managed safely, sustainably and profitably. Like a friend we never knew we had, these smart little devices look out for us when we’re in the office, and look out for the office when we’re at home. They are becoming ever more vital to the way we work today, and in the future.
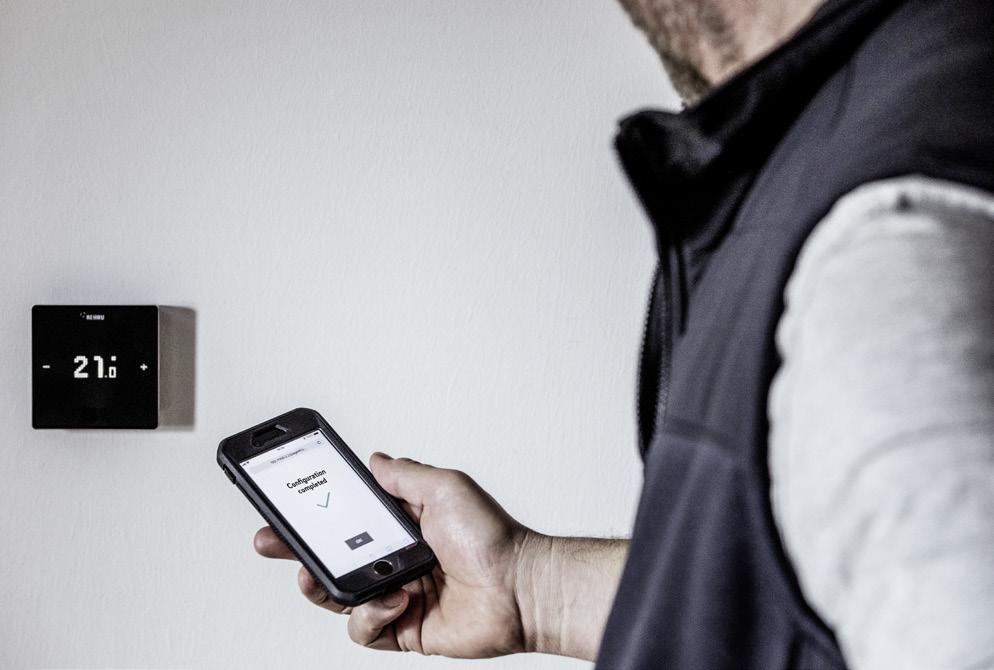
Getting smart with underfloor heating
Franz Huelle, head of technical at Rehau Building Solutions, explores how electrical contractors can use under floor heating (UFH) together with smart controls to deliver more efficient and intelligent buildings for end-users.
How the nation’s buildings are heated has changed dramatically over time and, as industry becomes more sustainable, so too must heating innovations. In order to drive efficiency and adaptability in a variety of buildings, many are increasingly opting for UFH technology. To regulate and optimise such systems, building professionals are also starting to implement smart controls into these solutions.
For any building project, whether new-build or refurbishment, choosing an efficient, future-proof heating solution is important to developers or contractors. Once thought of as an expensive, high-end solution, UFH is fast becoming an efficient space heating solution in any development. More flexible and scalable than traditional central heating, a building can benefit from the adaptability of underfloor heating throughout its working life, as layouts and occupant habits change.
As the world works to become more environmentally-friendly, the nation’s building stock must also be constructed with sustainability in mind. Lower flow temperatures in UFH systems compared to their more traditional radiator counterparts distinguish them as a more sustainable, high-performing option. Specifically, according to research by the British Electrotechnical and Allied Manufacturers Association (BEAMA), warm water UFH installations are 25% more efficient than radiators when paired with a modern condensing boiler, and 40% more cost-effective with a heat pump.
On top of this, growing use of technology, such as smart controls, drives further efficiency by optimising and regulating space heating throughout a building using data learned from occupant habits over time. As consumer demand for this technology grows, so too will the expectation that energy efficient heating solutions and smart controls will be present in all modern buildings.
Smart controls are growing In recent years, smart home technology has grown in popularity and use at an exceptional rate in homes across the world. Continued development of our national 5G infrastructure, along with sector growth, demonstrates the UK’s own smart home market, already worth over £900 million in 2017, will see enormous expansion.
Yet though smart controls can optimise a multitude of building functions, when integrated with technologies such as UFH, they can start to deliver savings on energy bills over time while keeping occupants in optimal comfort. However, end-user requirements can vary, and, with this in mind, it is important that an electrical contractor knows their customers’ distinct needs when they are installing a system.
Understanding end-user requirements How we use buildings, both residential and commercial, is changing constantly. Whether through growing numbers of multigenerational households, or office spaces becoming flexible coworking spaces; occupant requirements and overall trends vary greatly across the nation’s building stock. This is even more the case for mixed-use developments, where the blend of commercial and residential property presents an even more complex assortment of end-user needs.
When it comes to providing building services, such as heating for these diverse uses, it helps to have a level of flexibility from a system. Smart controls can alleviate complications associated with these varying heating requirements. With an efficient means of space heating, such as UFH, every room can be heated to each occupant’s exacting requirements, whatever time of the day that is required.
For many end-users, a heating system must be energy efficient to keep costs to a minimum, whilst providing a comfortable level of warmth. Smart controls offer an excellent way to do this, gleaning information from occupant habits and times of peak demand to efficiently adjust the system’s overall energy consumption. By doing so, valuable savings can be passed onto the end-user.
It is clear end-users across many building types have varying heating requirements, yet ensuring a property remains future-proofed and cost-effective is a common concern. In this respect, it is key for electrical contractors to get ahead of the smart control curve.
Getting smart For electrical contractors fitting these systems, it is important to know what smart controls can deliver in order to provide the best results for customers. In order to deliver solutions across developments and projects, systems must also be quick and easy to install and set up so contractors can meet tight deadlines.
Connected smart devices use data from sensors, the internet and information learned over time from a building’s efficiency and occupant habits to optimise the heating of a space. With other technologies like geofencing, which determines the location of a building’s occupants and heats their rooms accordingly, these solutions can work with UFH systems to continually optimise a home’s space heating.
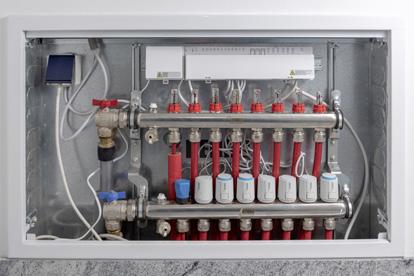
Often working from an internet-connected base station, smart controls can cover a wide array of underfloor heating zones within a property. Depending on the technology available, these singular zones can be divided up into subgroups that can be programmed individually to fit the building’s needs. With this kind of functionality, electrical contractors can easily separate spaces in-line with end-user requirements. For instance, separate floors belonging to different organisations in an office building can be regulated distinctly, or apartments in a block can benefit from their own separate system.
Initially, programming smart technology can seem a daunting and complicated prospect. However, most systems provide electrical contractors with easy installation and are designed with flexibility and adaptability in mind. Indeed, the most up-to-date systems often feature a simple tool-free set-up with an intuitive commissioning wizard for more complex systems, guiding contractors through process and system checks.
The internet connectivity of these smart devices also provides contractors with a host of other possibilities, including remote access to installed systems for servicing. With end-user permission, system data is now capable of being accessed through dedicated apps, delivering more intuitive maintenance, while saving time and increasing customer satisfaction.
As technology’s progress continues to march on, these smart control systems will also continue to develop, offering a multitude of temperature control functions, such as air conditioning and ventilation. Such innovations will be viable to electrical contractors as they seek solutions in a world where sustainability is an increasing priority. With that in mind, smart controls represent a technology that can help key stakeholders keep up with rapidly changing end-user demands, while also improving overall energy efficiency and future-proofing buildings for years to come.
Protecting our energy infrastructure
In days gone by, activists sawed down pylons to forcibly isolate smaller areas from the energy grid. Nowadays it is hackers, whose motives range from political to purely financial, who are attempting to use digital means to remotely access our critical infrastructure. Here, OMICRON explores the role of cyber security monitoring systems (IDS) for substations.
he protection engineering and SCADA technology or the station T automation system (SAS) belong to the critical infrastructure of utilities. They make an essential contribution to maintaining the energy supply. These infrastructures must, therefore, be protected against unauthorised access or illogical switching actions that cause disruptions to the energy supply or the destruction of equipment.
Andreas Klien, product manager responsible for cybersecurity products at OMICRON, explains the challenges facing substation operators today, “To get a better handle on this, we look at the possible attack vectors that might be utilised against the station control and protection technology: How could a hacker or malware get into the substation?
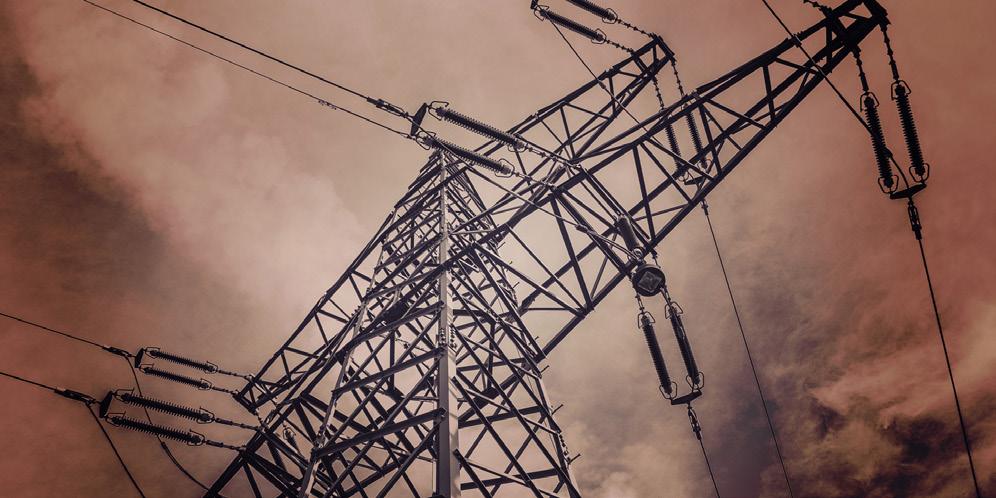
Where is the path of least resistance as far as a potential hacker is concerned, what would make their job as easy as possible? This is the first thing an operator has to consider.”
OMICRON’s IDS (Intrusion Detection System) StationGuard protects these critical infrastructures against almost all conceivable cyberattacks or unauthorised actions. It contains the accumulated know-how from many decades of worldwide engineering work in switchgear, as well as research on IEC 61850 network analysis.
With its unique approach, a combination of cybersecurity threat monitoring and functional monitoring, StationGuard not only detects unauthorised activity on the substation network, but also identifies problems
StationGuard is based on cyber secure hardware and is controlled and monitored by the easy-to-use software running on it.
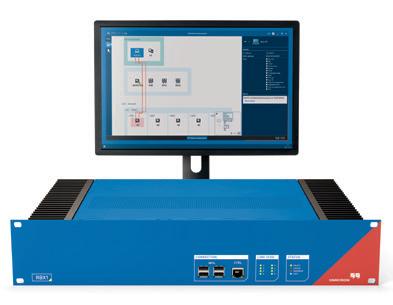
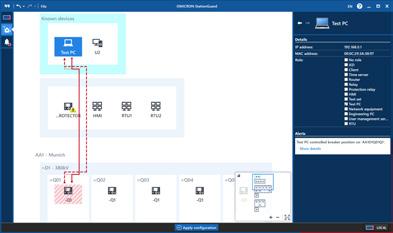
StationGuard is easy to use and presents each event in a clear and comprehensive presentation of the station.
in the IEC 61850 communication, enabling it to detect different types of malfunctions in the substation to allow a quick response.
To achieve this, StationGuard imports the SCL (Substation Configuration Language) file of the substation to create a complete system model of the automation system and the substation. It then compares each in
dividual network packet with the live system model. This process works without a learning phase and independently through the SCL description with just a few additional manual inputs.
An essential feature of StationGuard is its ease of use. Its user interface is adapted to the diagrams and terminology in substations and does not use special IT terminology. Therefore, all information is easily understood by protection and control engineers.
Because verification of the network traffic contains such a high level of detail, not only are illegal packet encoding and unauthorised control commands detected, but also errors in the sequence numbers and more complex measurements, such as message transmission times or critical states of the IEC 61850 quality bits. StationGuard emits very few false alarms because it knows the typical maintenance operations and considers them in a specialised maintenance mode.
The IDS itself is protected by a secure measured boot chain (via a crypto chip), encryption of data and communication, and a specially hardened Linux operating system. In addition, OMICRON’s StationGuard experts assist users with questions about alarms reported by the IDS. To do this, they can analyse the network recordings of StationGuard to assess whether a potential threat situation exists.
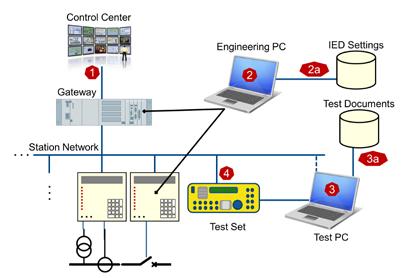
There are multiple attack vectors to a typical substation, each marked with a number
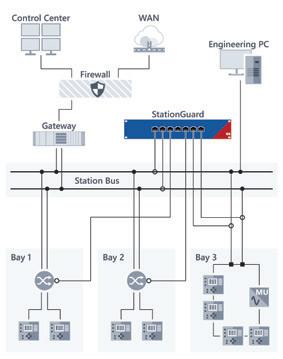