
3 minute read
Sector report
the vaccine, at least within commercial environments, 2021 appears to promise another strong performance.
Packaging
2020 was a highly disruptive year for this normally stable sector. Covid-19 saw a significant impact on food-to-go sales, although when cafés were open the recent rise in reusable cups went into reverse. Greater focus on hygiene has presented many opportunities for manufacturers, however, and slowed moves to reduce packaging content (albeit only temporarily). Positive trends include the growth in grocery sales and the growth in ecommerce, with consumers very focused on the condition and shelf-life of what they buy and on-packet branding becoming even more important to the relationship with the end customer.
Building products
The recent Brexit deal has given builders much more clarity on the cost and availability of imported materials such as timber and roofing materials. Loss of skilled labor with the exit from the EU and ongoing delays at UK ports will continue to cause some frustration, but UK housebuilders held up far better than initially expected through 2020. Construction is widely recognized as one of the major industries to contribute towards rebuilding the economy. Indeed, according to recent construction PMI data, only ten per cent of companies in the sector felt it would contract in 2021, versus 50 per cent believing it would grow.
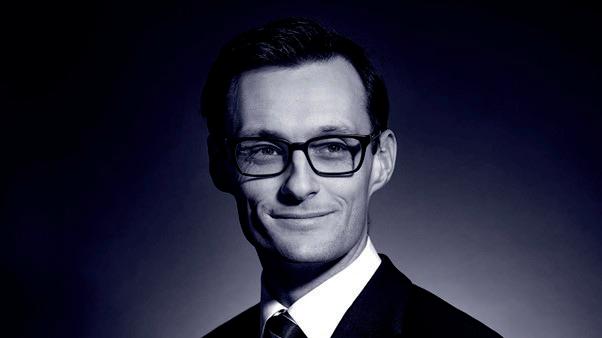
Overall
There are also several other manufacturing sectors, such as capital goods that are set to return from a more difficult year, with deferred business investment from 2020 deployed over the next couple of periods. It will take longer for Automotive and Aerospace to recover, but in the longer-term, population growth, the reopening of the travel sector and legislation-related advances in automotive technology should all contribute to the overall outlook beyond 2021.
The FTSE 350 Industrials index is currently 40 per cent above its March 2020 low, while PMI data reflects confidence within the sector. 2021 will be a vintage year for manufacturing investment both within businesses and through M&A. v
Graham Carberry
Graham Carberry is Managing Director at Arrowpoint Advisory, the dedicated lower midmarket team of Rothschild & Co in the UK. We provide expert M&A, Debt and Special Situations advice to publicly-listed, private and family companies, entrepreneurs, sponsor-backed businesses and management teams, investors and lenders.
arrowpointadvisory.com
Mobility
mindset
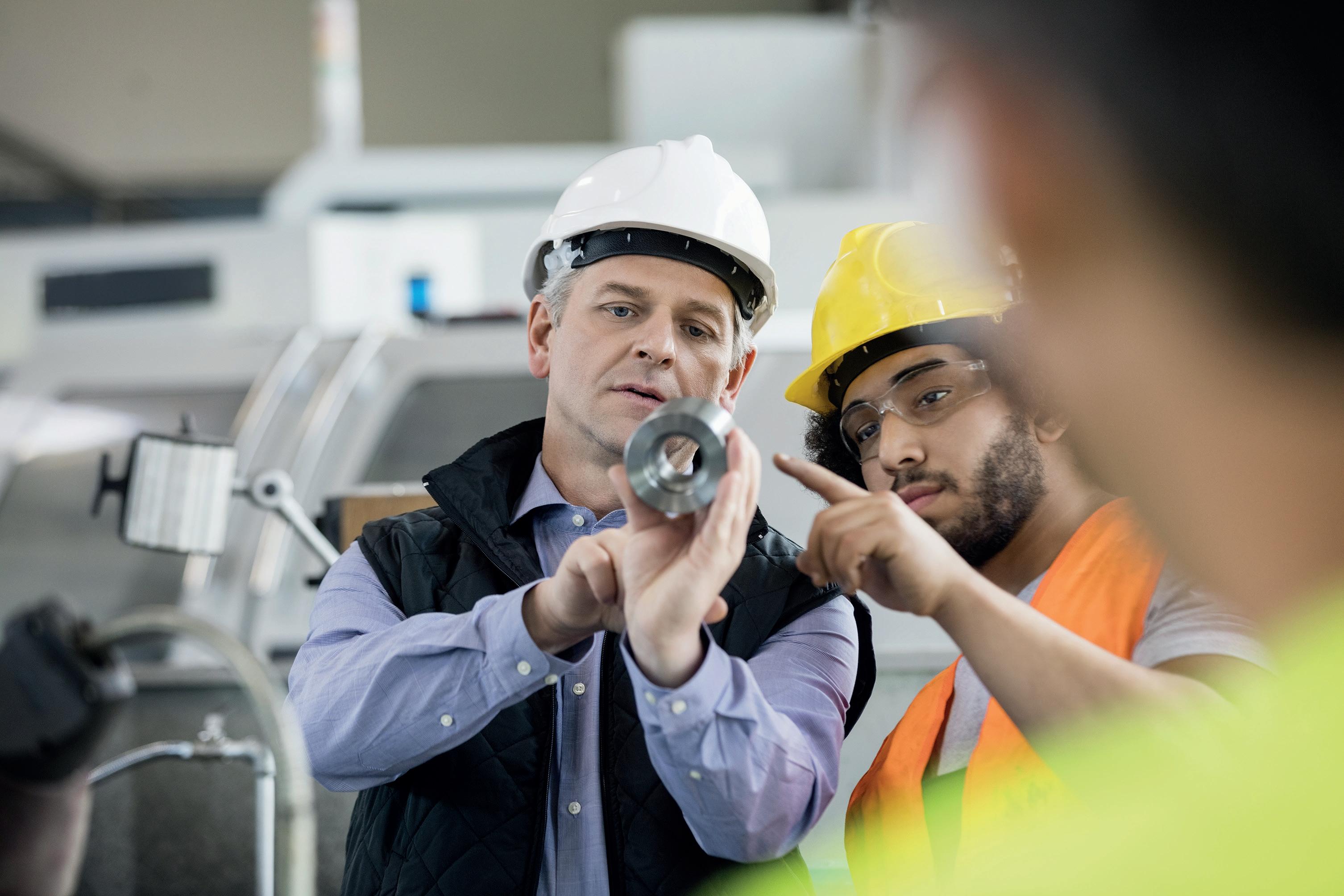
The three key principles to unlocking front-line innovation and productivity through
staff mobility. By Philipp B. Cornelius, Bilal Gokpinar and Fabian J. Sting
Front-line workers are the people that are living and breathing their company’s products and processes every day. They are the ones who literally handle the nuts and bolts of the operation. They know what is working and what is sub-optimal from the product and process perspective. But inviting their creativity and effectively capturing their input is a big challenge for any manufacturing company - How do you help to unlock what they know? How do you operationalise their feedback? How do you share knowledge effectively between teams in different factories? As the sector considers its recovery from the incredibly challenging events of 2020, answering these three questions could deliver a step change in how your organisation works, by tapping into and prizing the knowledge of one of your key assets - your employees.
To unpick the answers to these questions, we were particularly interested in looking at the effect of mobilising employees to foster innovation in manufacturing. We conducted a large-scale study where we systematically analysed innovative ideas submitted by the workers and their economic impact in a multinational, multi-billion euro car parts manufacturer over the course of four years. Key to our analysis was matching mobile front-line employees to similar colleagues who did not travel to other plants. This allowed us to precisely estimate the contributions originating from their mobility. Over the course of our research, more than 21,000 ideas were submitted by around 2,500 workers.
There were two key discoveries that stood out from our study:
• Significant productivity gains could be traced back to non-R&D employees: Shop floor and front-line employees frequently possess a wealth of hands-on production knowledge at a level of detail that far exceeds what is covered in manuals or is known to engineers. • Staff mobility is central to unlocking innovation and organisational learning. Our study showed for the first time how strategically implementing front-line mobility (the short, focused, and purposeful exchange of staff members between different company sites) can substantially boost these employees’ contributions to innovation in manufacturing companies because it stimulates learning. As staff observe how different setups of similar manufacturing processes are linked to various performance outcomes, they acquire a more fundamental understanding of both how and importantly why these processes work.