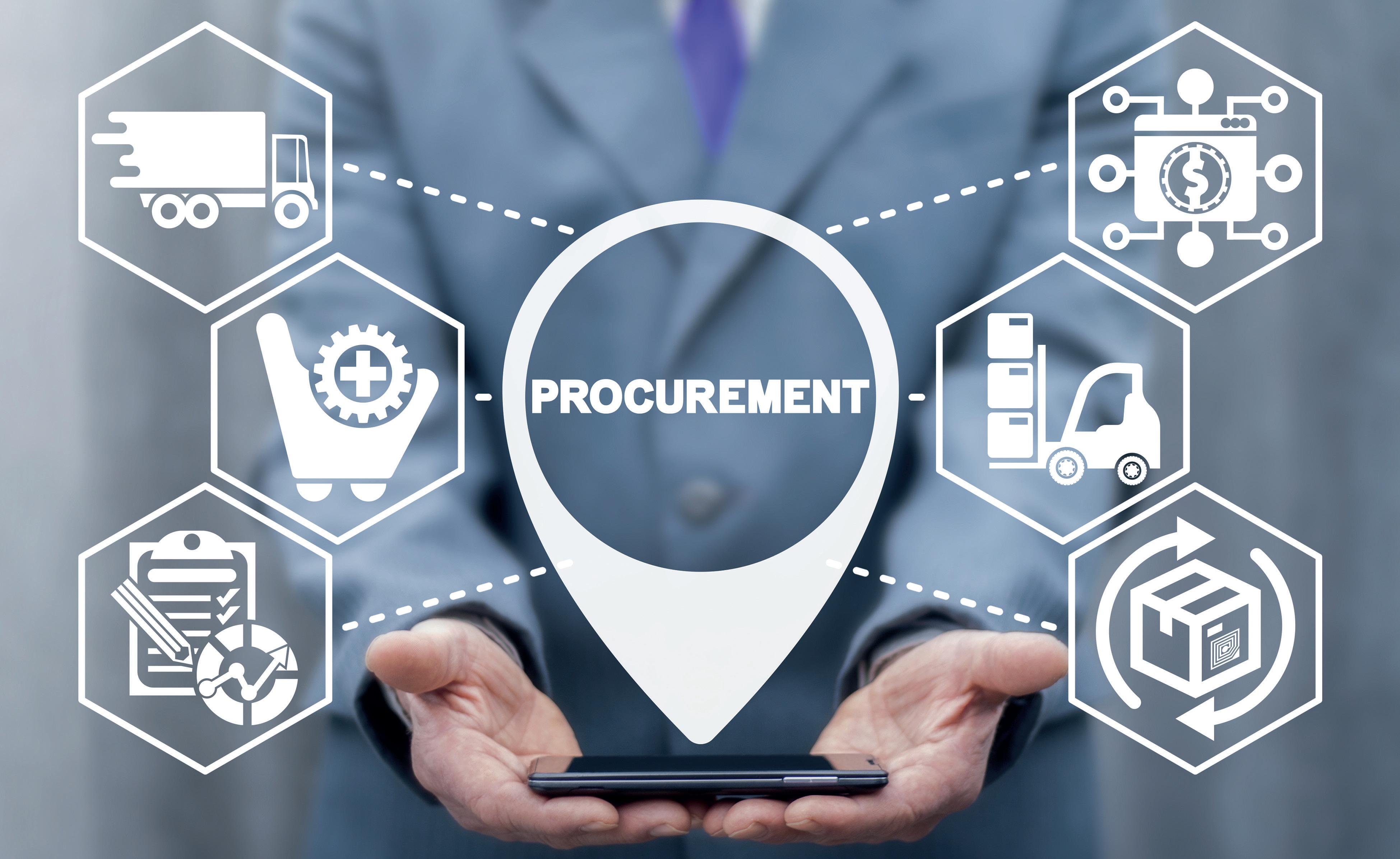
131 minute read
PROCUREMENT
A key role
How connected preconstruction can fuel construction’s move from damage limitation to recovery in 2021. By Mike Pettinella
The start of 2021 has been far from easy. Construction owners and businesses in the UK are facing renewed national lockdowns, with sites remaining open under strict conditions. But there’s hope that, even if it’s some time away, the end may finally be in sight – and with it the recovery of the economy and the sector.
The government is putting the construction industry at the centre of plans to build back better. The Construction Playbook has recently been released, aiming to reform the delivery of public sector projects and help to create an industry that’s more productive, sustainable Mike Pettinella and profitable. Construction organisations are also beginning to move from damage limitation to rebuilding and even growing, as recent research underlined.
However, preconstruction – and particularly procurement – is highlighted as a blocker to productivity and new initiatives. Incorporating technology in the earliest processes of each project will be critical for helping organisations move from crisis to strategy in the year ahead.
Constructive plans
Many businesses were adept at finding ways to respond to the pandemic. A third of owners and 28 per cent of subcontractors reported exploring new sectors during 2020. But increasingly, firms are also looking at innovative ways to improve how they work in the longer term.
For example, using prefabricated elements can increase both productivity and safety – and is also recommended by the Construction Playbook. Interestingly, 43 per cent of owners and 24 per cent of main contractors are considering moving to off-site manufacturing methods as part of their plans for the future.
Implementing greener construction methods is another long-term goal for many businesses. Four in five owners are focused on adopting new sustainable construction designs
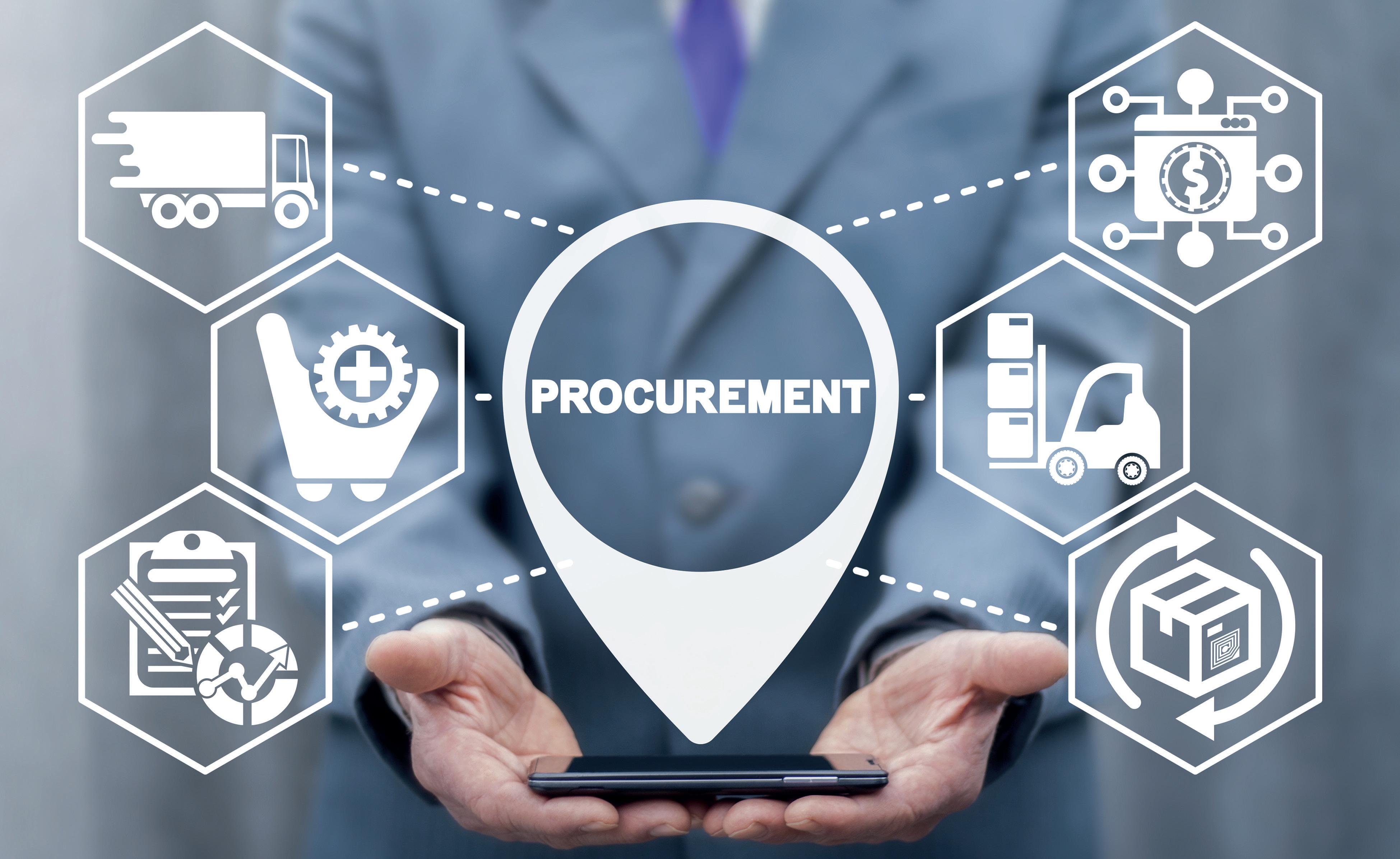
or methodologies – and 41 per cent are incorporating sustainable construction requirements into tender invitations.
Making greater use of technology is a priority for many organisations, with 47 per cent of main contractors scaling up remote working and off-site technology. But use of technology during the preconstruction phase is still limited, creating challenges on current projects and potentially hindering plans for the future.
The preconstruction roadblock
Manual, paper-based processes are still common during preconstruction. Only around half of owners and main contractors use technology to find new collaborators (57 per cent and 52 per cent) or tender comparison (57 per cent and 50 per cent). Organisations often use a combination of email, file-sharing tools, Excel sheets and paper documents.
This has a significant impact on setting up and completing projects. Just 24 per cent of owners and 19 per cent of main contractors say that it’s easy to find qualified subcontractors for projects. Importantly, it’s easy to make mistakes; 86 per cent of main contractors and 78 per cent of subcontractors admit that errors are routinely made during tendering that impact the project down the line.
The limitations of these processes may also hinder businesses’ plans to adopt new methods. A quarter of subcontractors report that owners’ internal procurement processes are a roadblock to adopting innovative construction methods like off-site manufacturing – and 26 per cent of owners agree. Organisations need efficient, flexible and datadriven preconstruction processes, and this is where technology can play a key role.
What digitalised procurement can do
Technology designed for the construction industry can improve preconstruction processes, delivering greater accuracy and efficiency and helping owners, contractors and subcontractors to make more informed decisions.
When it comes to selecting subcontractors, networks of construction professionals like BuildingConnected can help businesses to find qualified collaborators with a proven track record. This can enable organisations to enter new sectors or incorporate new methods, while mitigating the risk of working with unknown companies.
During tendering, digital platforms can centralise bids in one place and facilitate clearer tender comparison. Data analytics can help to highlight errors in proposals, so that mistakes are picked up at an early stage rather than during construction. Equally, with digital preconstruction tools, teams can undertake more accurate scheduling and costing, to help projects stay on time and on budget.
Importantly, by using tools that link data across the project phases, collaborators can ensure that nothing is lost – and stakeholders from design through to facilities management can benefit from the project data.
Moving to recovery
Construction businesses continue to show incredible resilience by adapting to the new challenges of the Covid-19 pandemic. As we gradually approach the end of this episode, the construction industry will also play a key role in the national recovery – and it’s really encouraging that businesses are already considering innovative ways to build that are more productive, sustainable and profitable.
Technology will play a key role in this transformation, and it’s especially important not to overlook the planning phase. Implementing digital preconstruction tools will be key for owners, contractors and subcontractors to realise their plans for the future, and support the move from crisis to strategy.
Mike Pettinella is Director of EMEA Sales,
Autodesk Construction Cloud. Autodesk makes software for people who make things, leading the market in 3D design, engineering and entertainment software. Since its introduction of AutoCAD software in 1982, Autodesk continues to develop the broadest portfolio of 3D software for global markets.
For more information, please see www.autodesk.co.uk
Fig 1
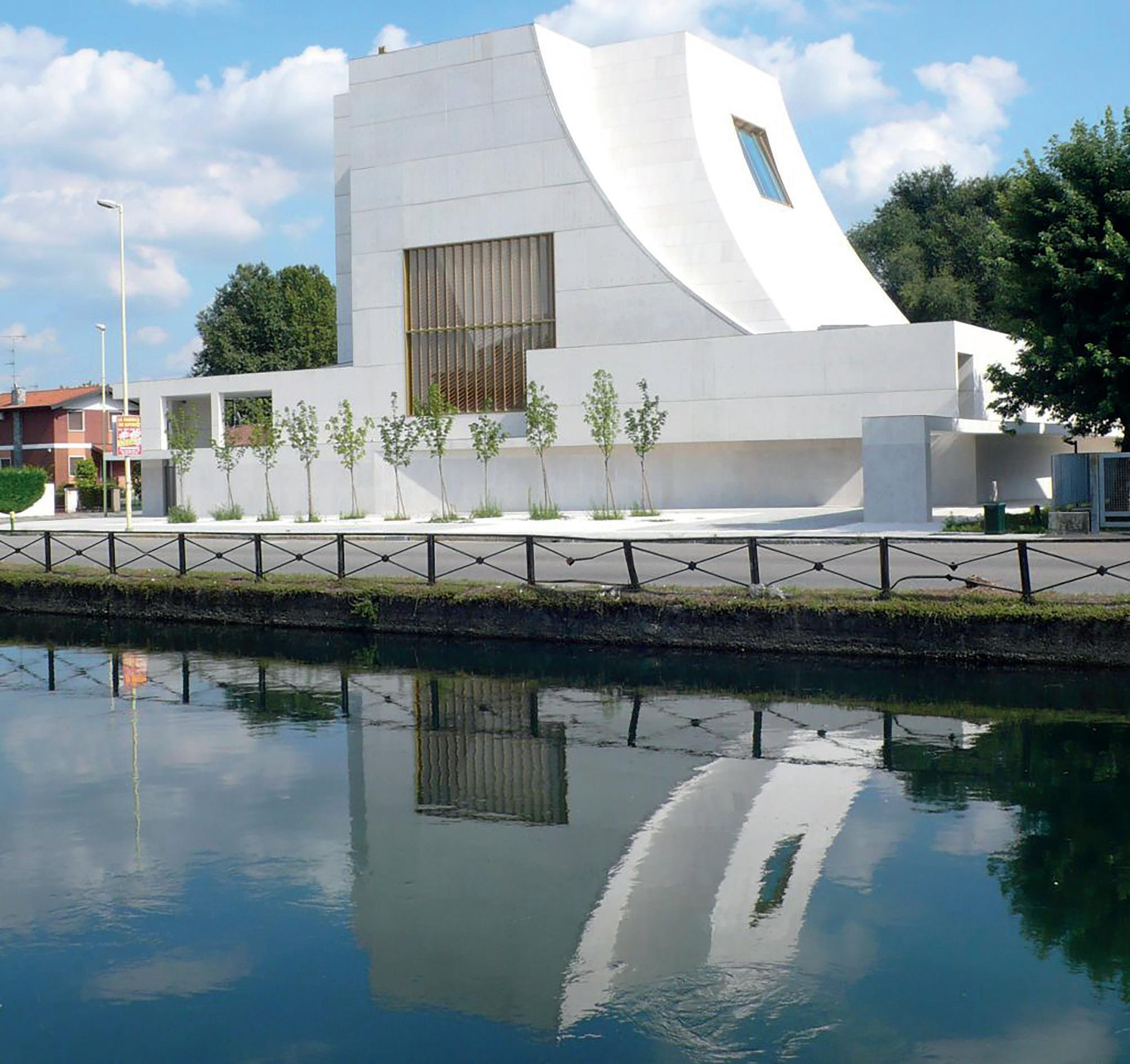
Thinking out-of-the-box
Roberto Garziera, a leader in construction design and engineering for over 20 years and the founder of Wenlock, a small engineering firm based in the West Midlands, has created solutions to CAD construction design problems for years and his innovative ideas are still solving problems today
Looking at the market today, and you can find a range of construction design CAD packages available, many of which present features dedicated to improving performance and lowering the possibility of errors. Roberto Garziera
In the domain of steel construction in particular, some CAD packages allow the designer to easily position a component - for example a universal I beam type - within an assembly drawing. Connections at either ends of the components can be chosen from a library or designed. Once the components have been added to the assembly model and their end connections defined, the CAD system can export the model and drawing of each component with the right length and connection details at both ends.
That is very helpful, but it still requires the user to define a full
assembly and handle each of its components manually, before the system can export their geometry and create drawings. When a project involves thousands of components, few or none of which are identical to each other, manually adding them to an assembly can still be a challenge, take a long time and increase the risk of making mistakes.
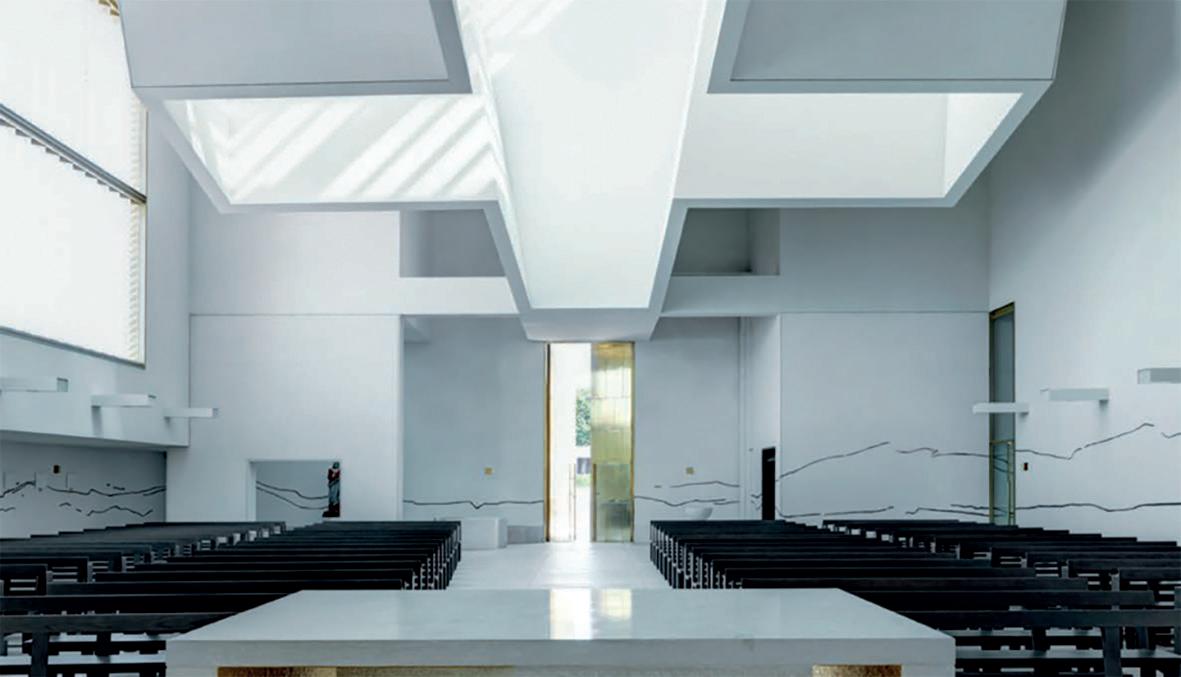
The first solution
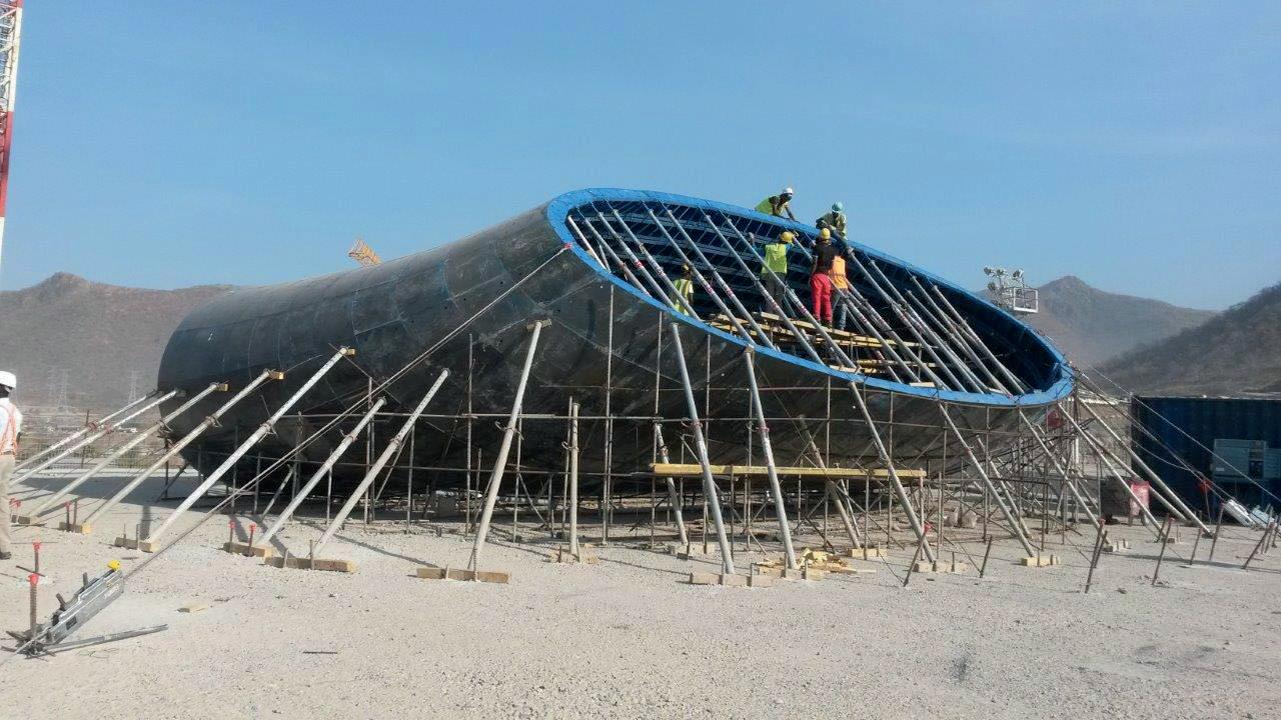
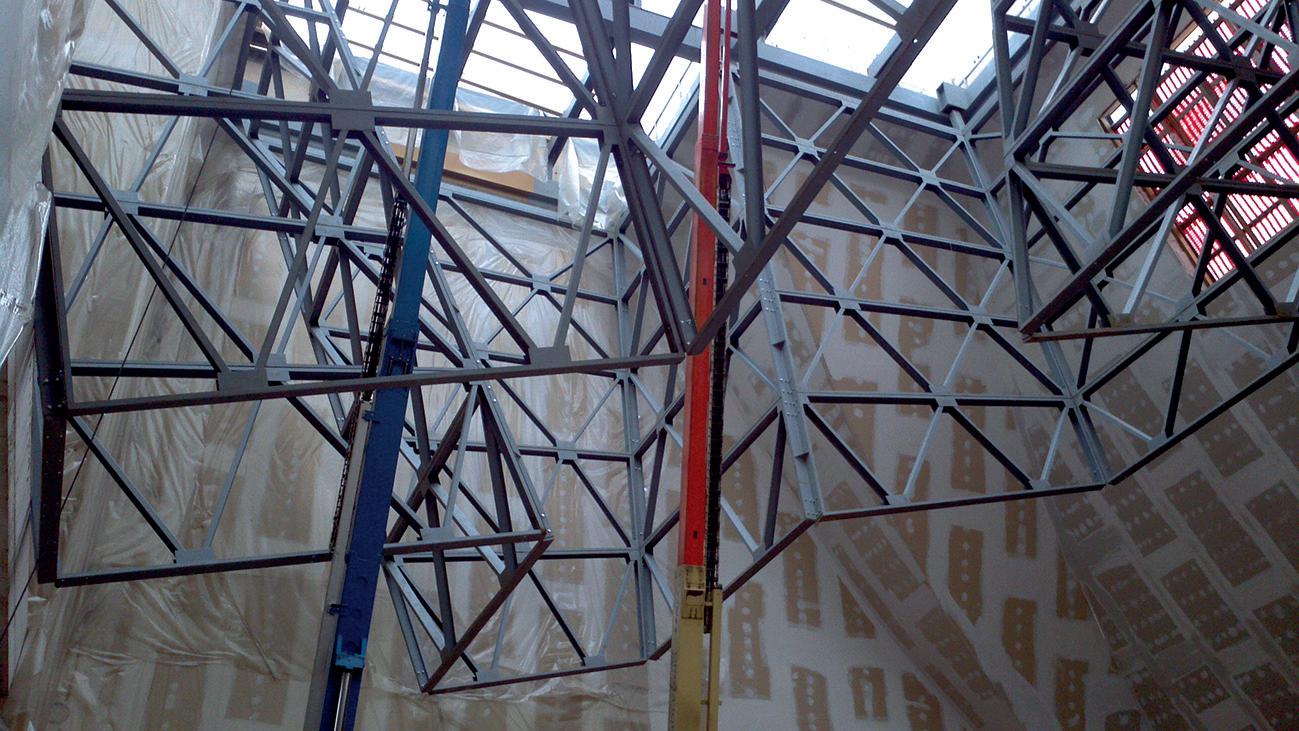
The first project which required Roberto’s CAD innovation involved the design of a 3D spatial cross structure for the new church of San Gianna Beretta Molla, built in Trezzano SN, near Milan, Italy in 2012) [Fig 1].
“The architects had conceived an impressive 3D spatial structure, with the section of a cross, hanging from the ceiling and projecting the light entering through its glass roof onto the believers in church below. The cross structure was to be covered in drywall, therefore it needed to be very strong and rigid (in order to avoid cracks) and extremely light [Fig 2 and Fig 3]. I proposed a truss structure made of very light folded U channels: it would be rigid and strong enough, and it would also present flat, regular faces for applying the drywall, a very welcome bonus [Fig 4],” explained Roberto.
After having been FEM verified, the structure needed to be designed for fabrication and Roberto decided it was time for engineering a much simpler and quicker design approach. Time was of the essence, and manually designing the required components - just over 500 in this instance - would have taken too long.
“Therefore, I divided each of the 12 cross walls into five smaller trusses,” he said. “Once the first truss had been designed, a routine was built into the CAD to automatically place it in the assembly at the right position according to its mark ID. Another routine could generate all the remaining trusses from the first one, by using it as a master model. After positioning each new truss in the assembly, the routine would automatically model it according to its needed size.”
Similarly, once a detailed drawing had been drafted for the first truss and its components, detailed drawings were automatically available for all remaining trusses and their components. In other words: 60 different trusses and more than 500 components automatically modelled and drafted after having modelled and drafted just one truss and a handful of components.
Fig 2
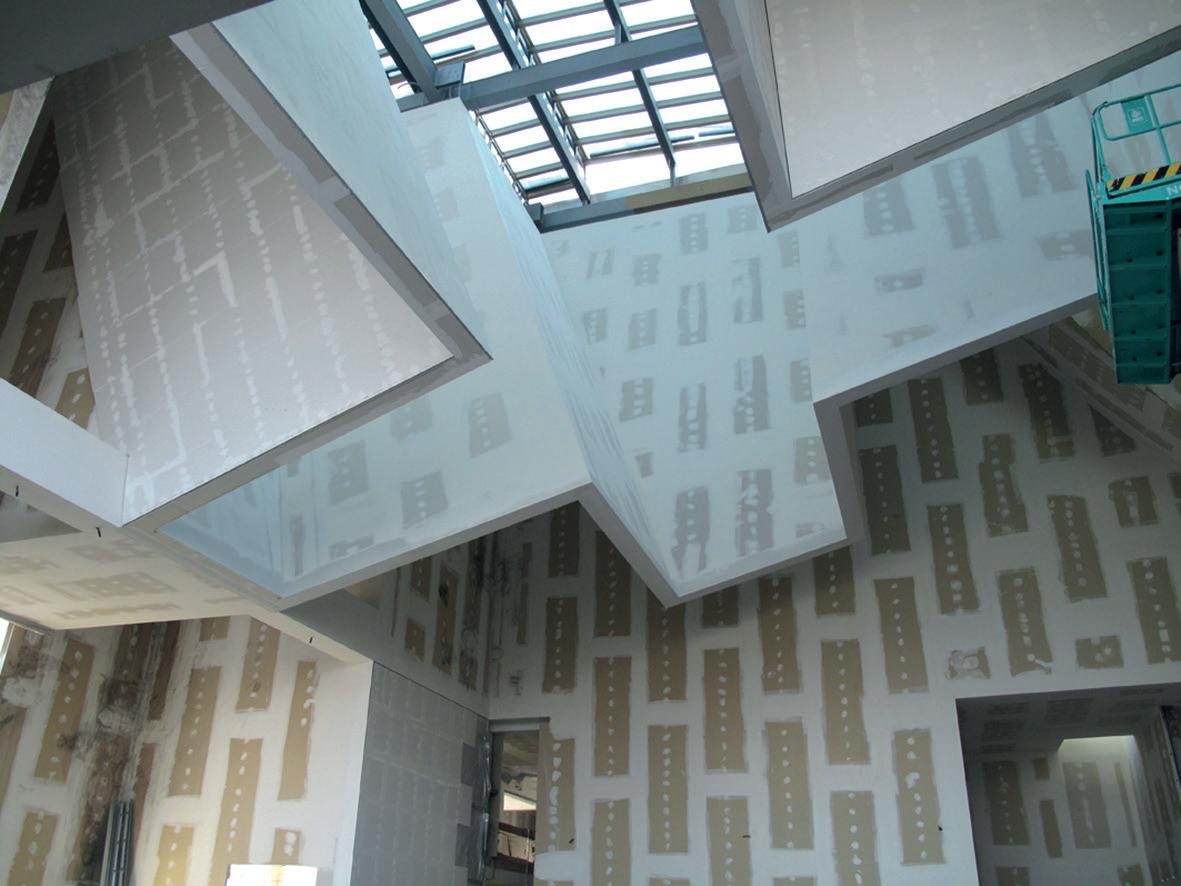
Fig 3
Fig 4
Fig 6
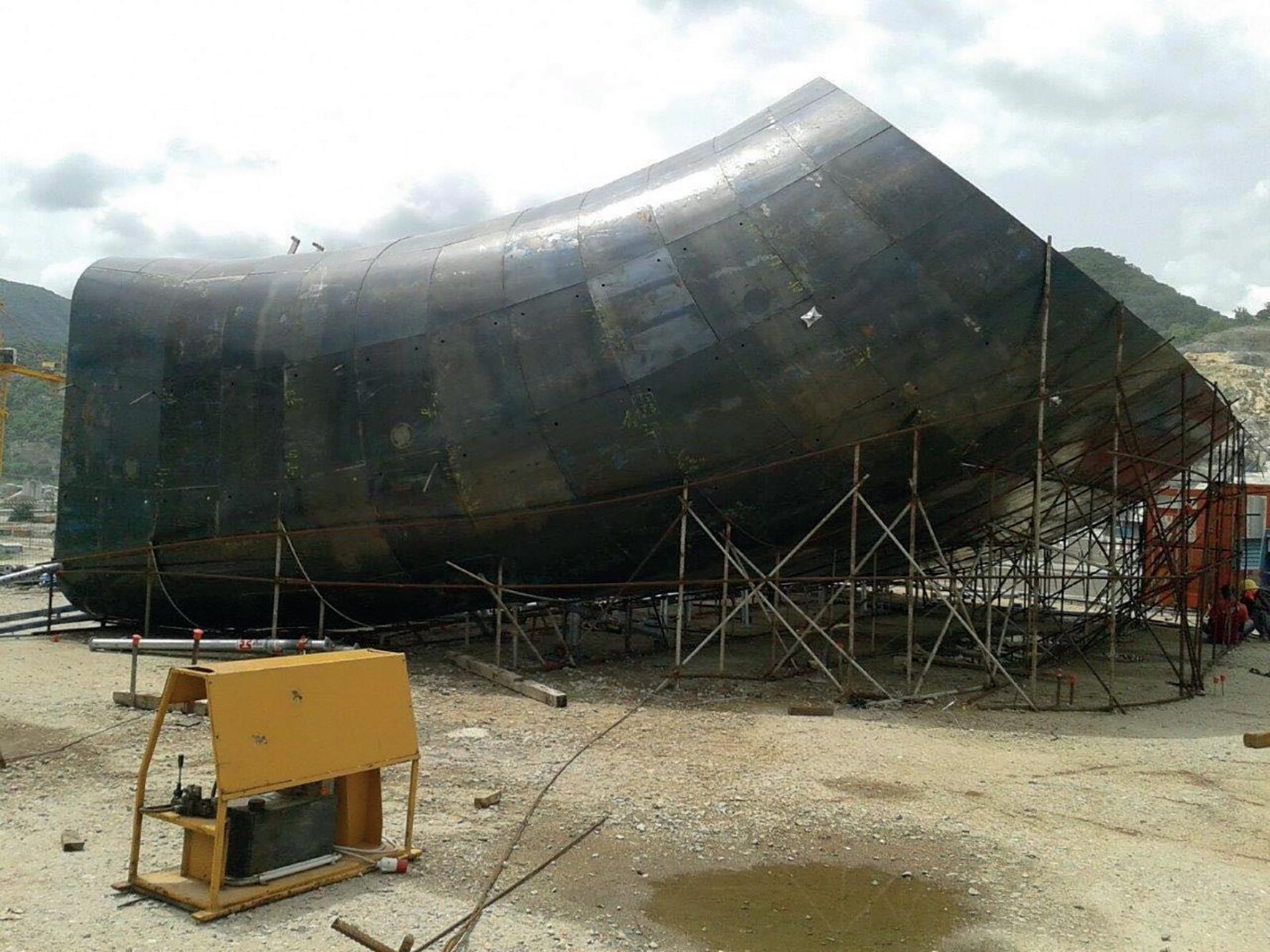
Fig 7
Thanks to the automated process, once the accuracy of the first truss had been double checked, all remaining trusses were generated automatically without possibility of error. The design had been conceived for quick manufacturing as well as simple on site assembling. Consequently, the project was a great success for all parties involved.
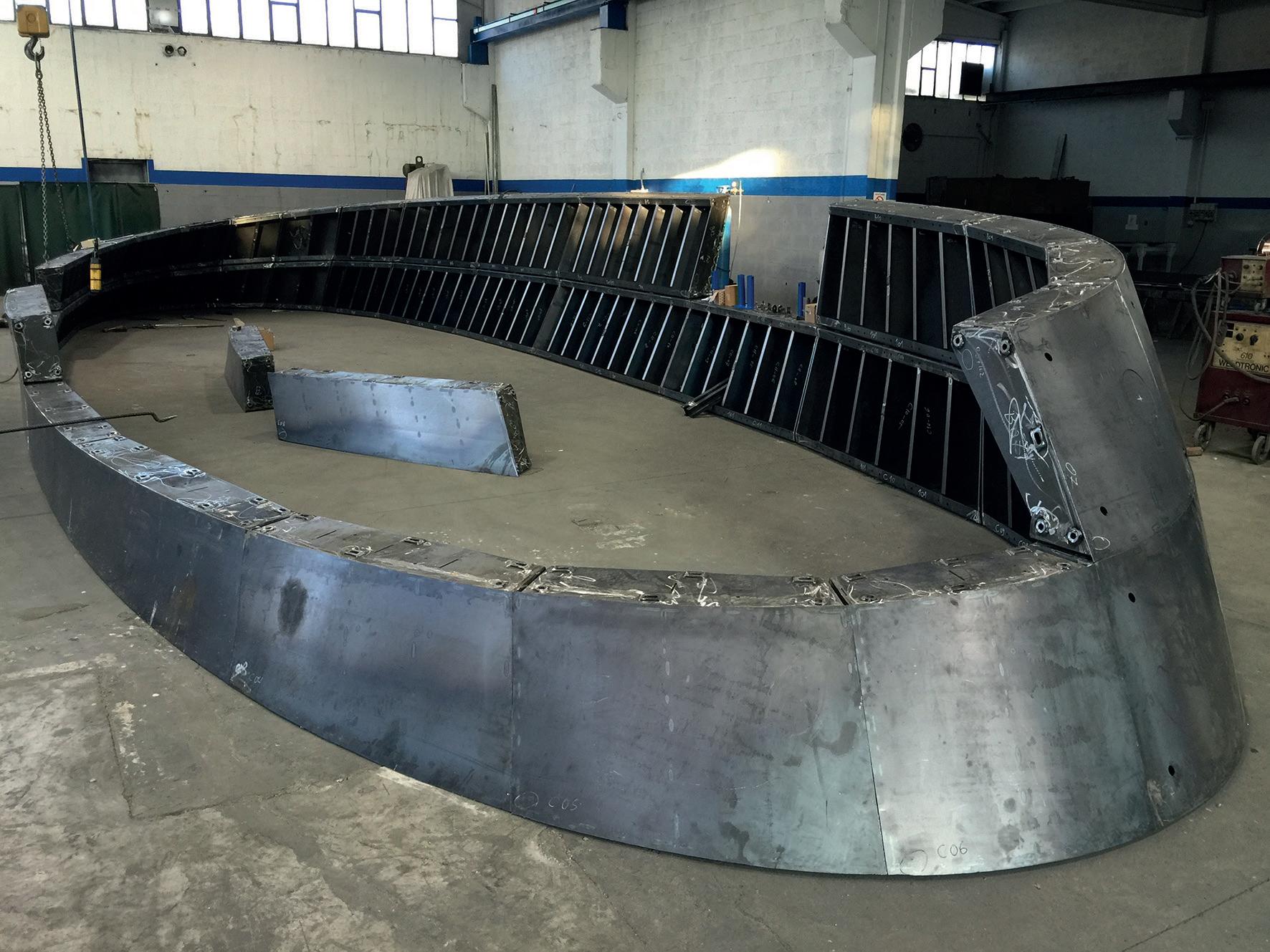
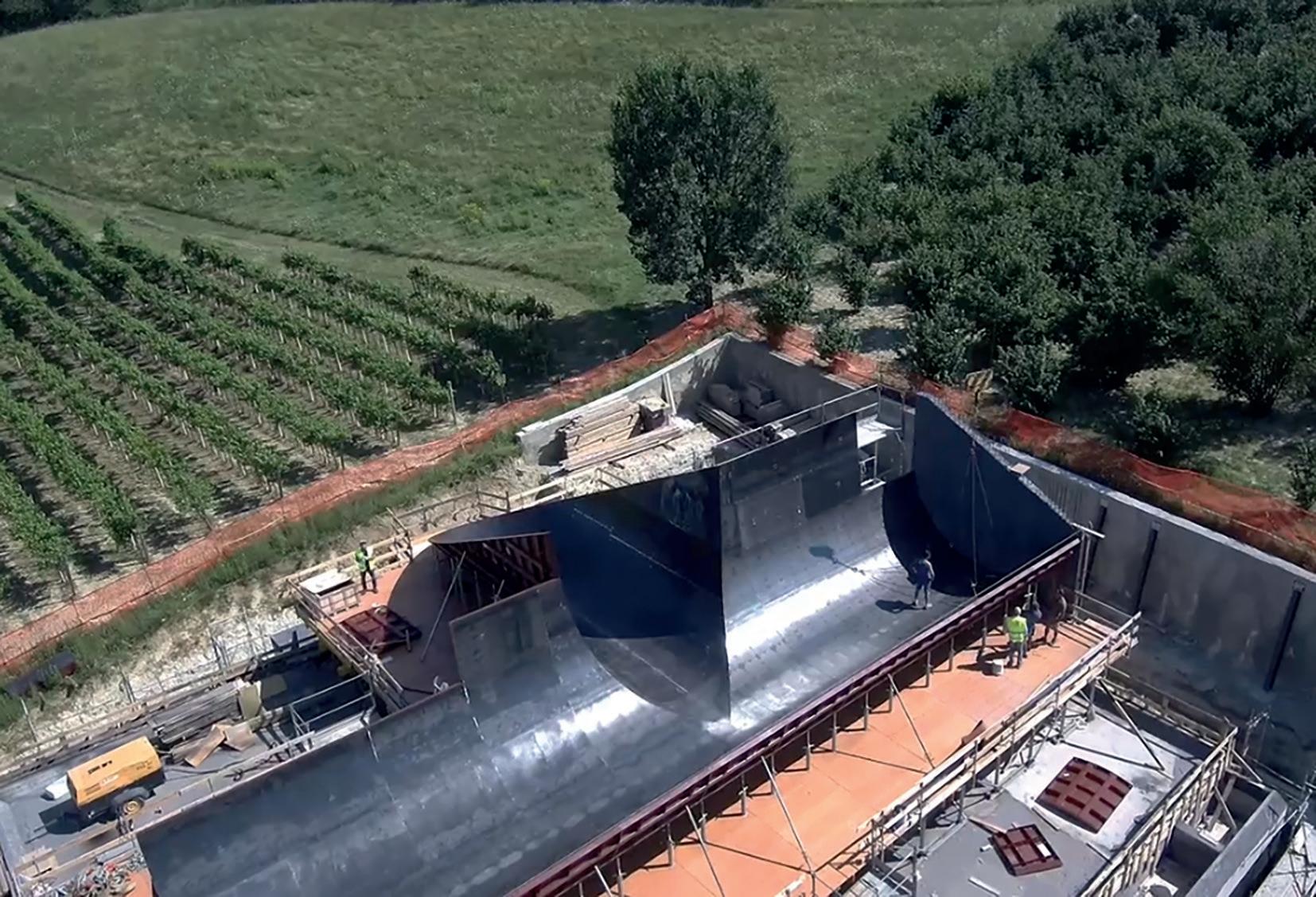
Problem solving
Roberto (who is in the top percentile of his field) then brought this expertise and technology to the UK where he founded Wenlock in 2015. Since then, a lot of Wenlock’s projects have gained considerable benefit from this technology and a few of them would not have been possible without it.
“A good example of this is for a project that involved the design of two different sets of formworks for the draft tubes of the Grand Ethiopian Renaissance Dam (GERD),” added Roberto. “Hydroelectric power plants often have less than five turbines, and hence less than five draft tubes. Consequently, due to cost and to their very irregular shape, draft tube formworks are often build on site with wood, through an approximate and labour intensive operation. For the GERD, it being a large dam with 16 turbines of two different types, the most convenient option was fabricating steel formworks. Using its customised CAD technology, Wenlock divided each draft tube formwork in 22 rings, each comprising 24 blocks: 528 unique blocks [Fig 5, Fig 6 and Fig 7].”
Accounting for about eight to 14 plate components for each block, depending on shape and size, the number of unique plates to be laser cut, folded, and handled was over 5000.
It became immediately obvious that manually handling the design of more than 5000
plates, albeit with the help of 3D CAD systems, was not feasible. By applying Wenlock’s design approach, each block was automatically positioned within the assembly and generated by applying a routine to a single master model. Each block’s component was shaped on the outer (concrete) side by the draft tube surface. “Since each block, being automatically generated, was created relative to the same absolute co-ordinate system, its shaping surface had to be re-positioned, by the automatic routine, according to the linear transformation defined by the actual position of the block in the assembly relative to the absolute coordinates. The result: more than 5000 components and more than 500 assemblies modelled and drafted automatically!” Roberto revealed.
Once the design was accomplished, it was soon clear that fabrication would not be easy. Actually, with each block lacking even two sides orthogonal to each other, fabrication would have been impossible with conventional methods. Wenlock stepped in again, and devised a method for assembling and tack welding the blocks using an industrial robot in a very unconventional way: but that is a story for another day!
Conclusion: thanks to Wenlock’s design technology, a project which was deemed almost impossible turned out to be very successful and profitable.
Wenlock has also worked its magic on another interesting project, this time in Italy. Using the same technology, this featured a 350sqm soffit formwork designed for a winery project in the Cuneo province in Piedmont [Fig 8 and Fig 9].
This massive formwork, having the shape of two intersecting tunnels upside down, albeit less
Fig 10
irregular than the draft tube one, presented the difficulty of having to achieve a perfect match among 540 panels, including the intersection line [Fig 10]. Once again, Wenlock’s design technology enabled it to automatically model and draft more than 6000 components and 540 assemblies after having defined only two master models (one for each tunnel trunk).
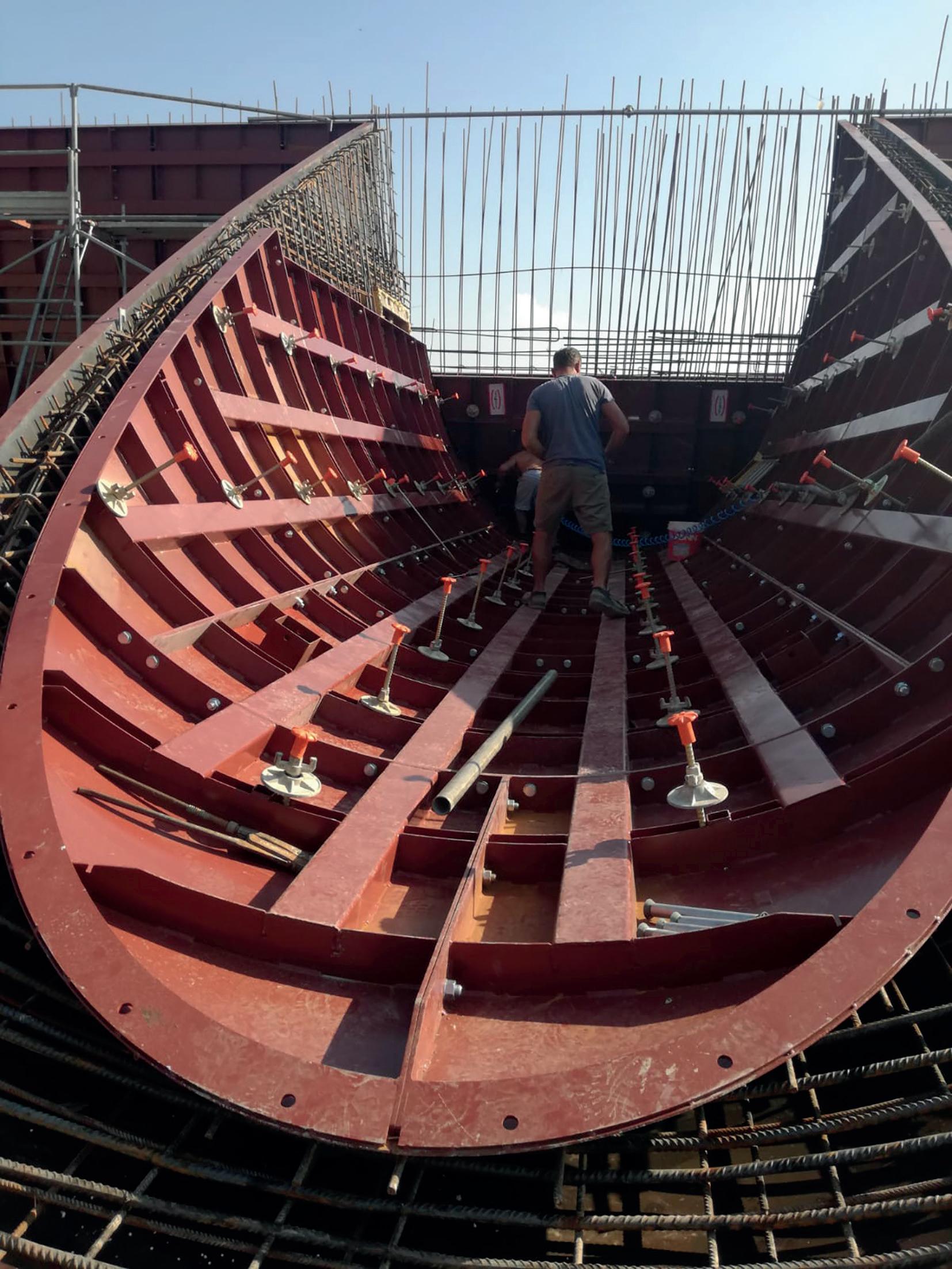
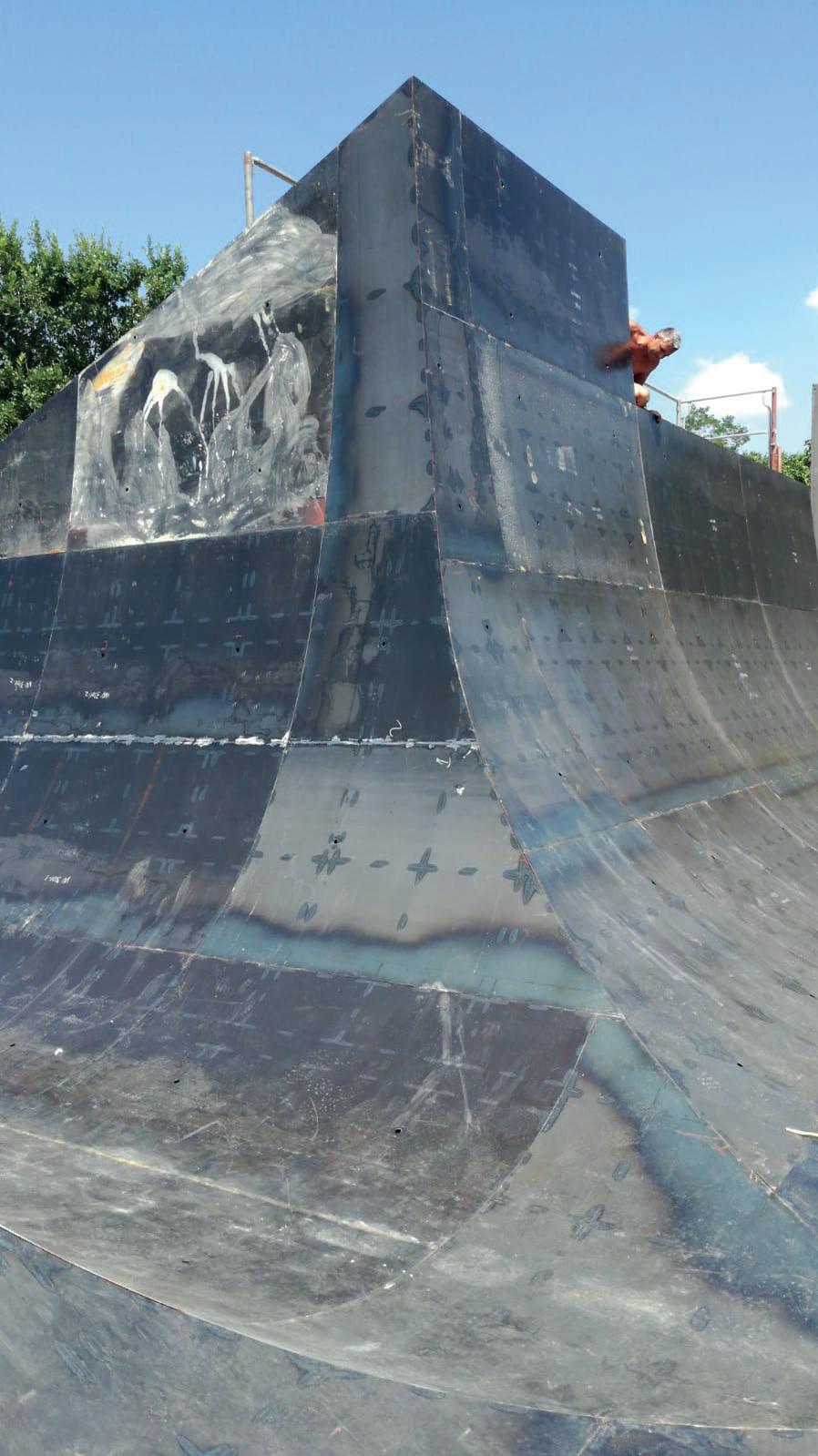
By combining an interest in 3D design
and a knack for innovation, Roberto Garziera and the team at Wenlock continue to address challenging builds around the world. Specialising in the design of bespoke machinery and devices, special equipment, steel constructions, and industrial products, Wenlock’s expertise is increasingly being called upon for challenging and unusual projects.
For more information, please see: https://wenlock.com
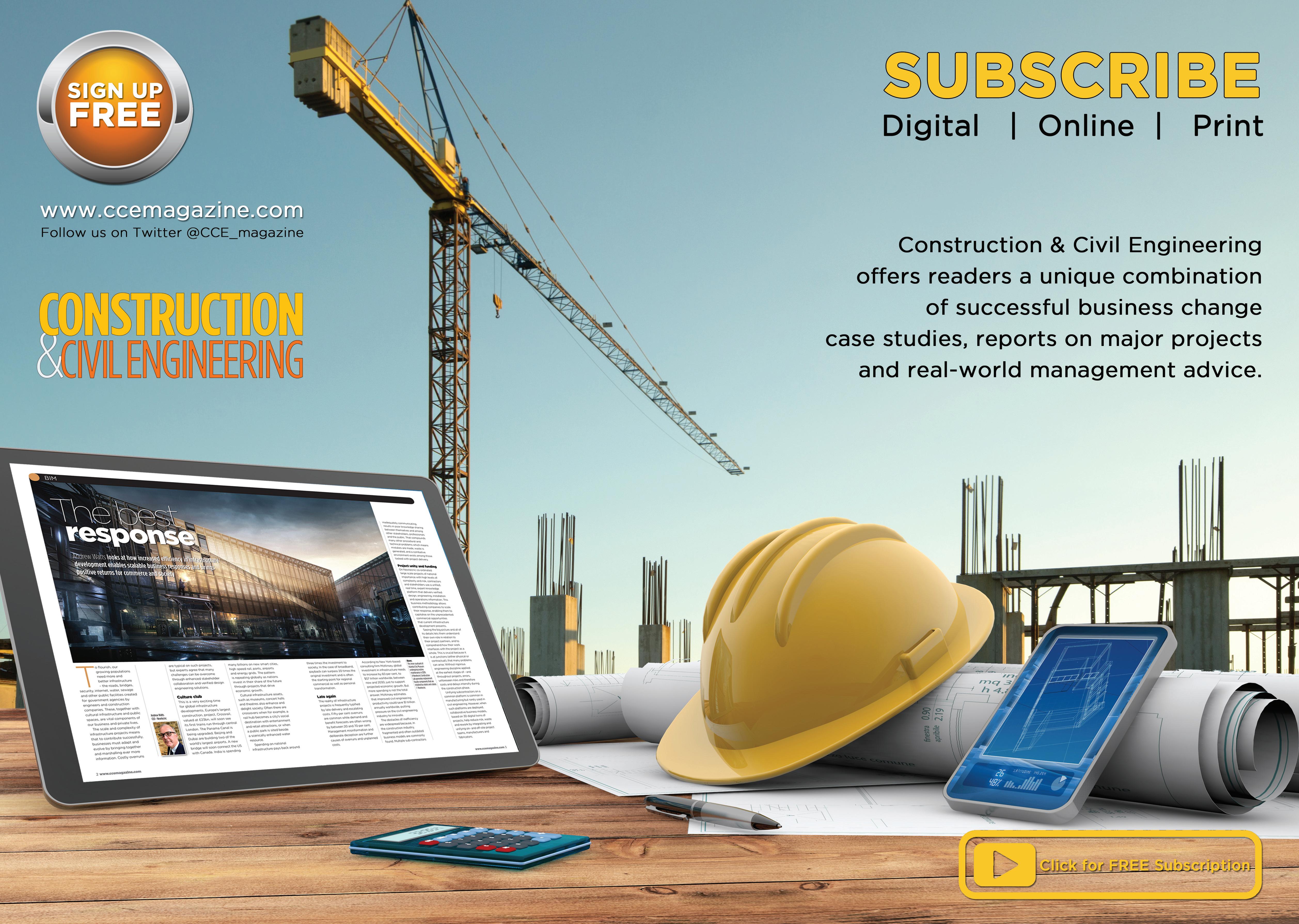
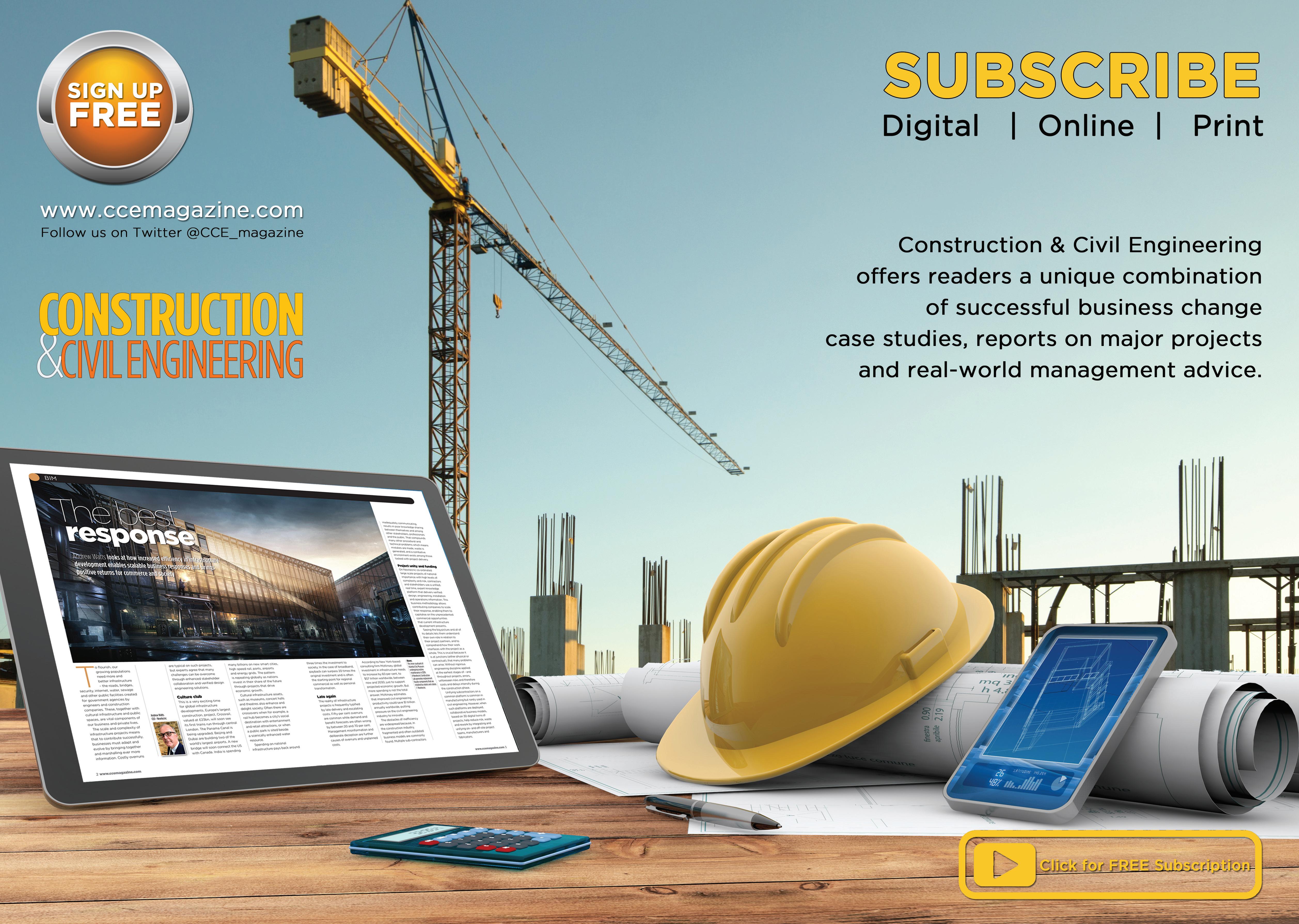
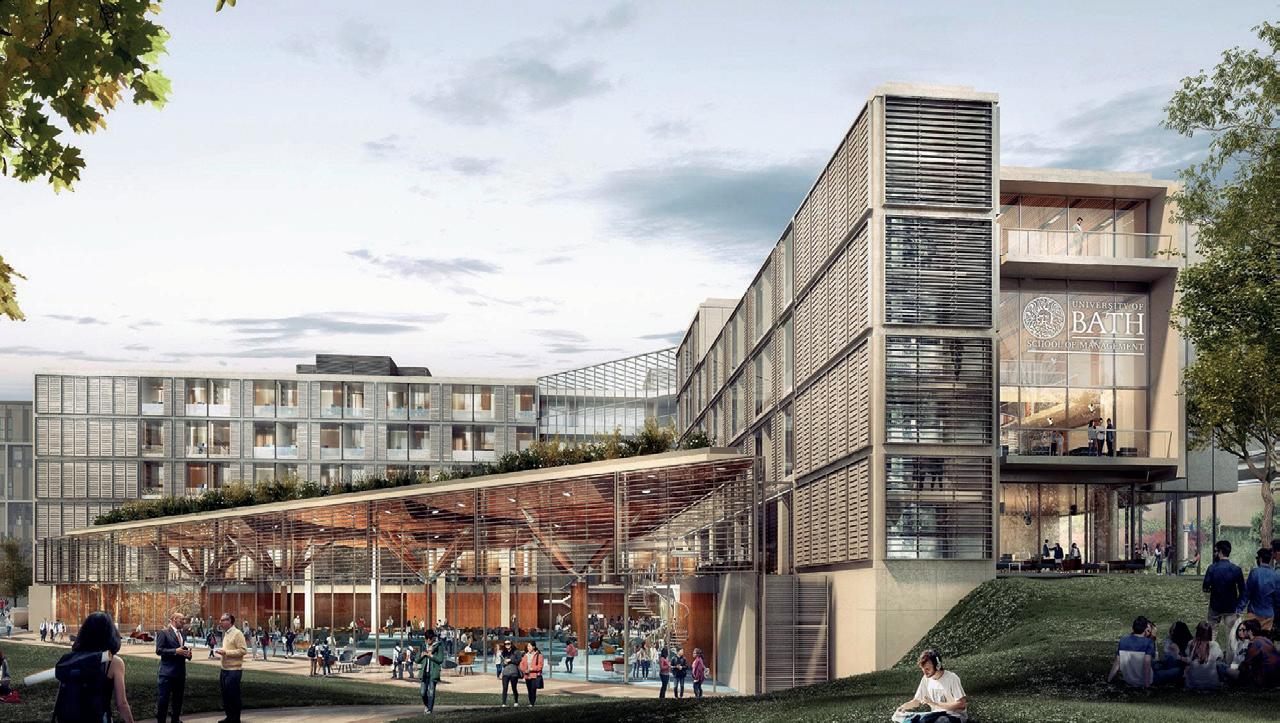
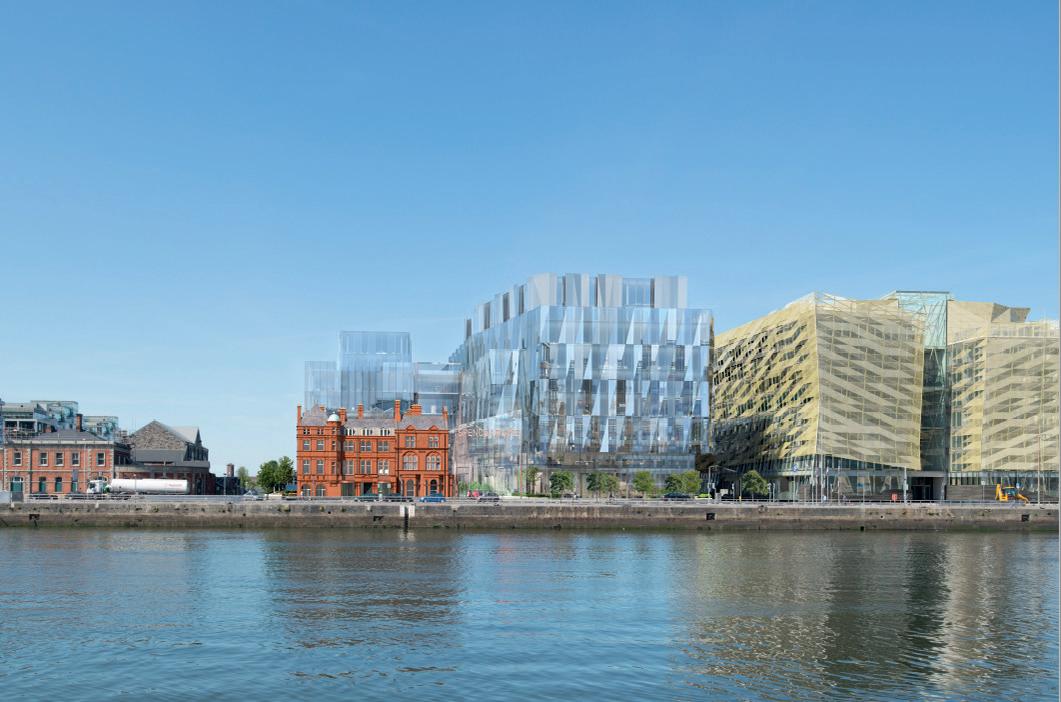
Strength in numbers
The Clarison Group brings together some of the leading names in the UK’s façade industry, creating a new force in the design, manufacture and installation of architectural glazing and façade systems
Formally launched in February 2021, the Clarison Group is made up of four market leading brands in the field of building envelope technologies within the UK and Ireland. These brands – Alucraft UK, Alucraft Ireland, EAG and Williaam Cox – retain their own management teams and collaborate as a group under the leadership of a team led by CEO Mark Oliver, and supported by the private equity group Elaghmore. As a result of the shared knowledge, capability and expertise of its brands, the Group is able to offer full design, fabrication and installation of unitised and stick curtain walling, windows and doors, rainscreen, architectural glass, reinforced concrete, brick slips and more, as a full ‘through the wall’ façade solution.
With the amalgamation of these businesses, the Clarison Group is today able to boast combined annual revenues of close to £100m, 450 employees across six locations, the industry’s largest factory footprint in the UK of 25,000 sqm (plus additional 20,000 sqm of storage space), and the country’s largest domestic production capacity, equating to approximately 430,000 hours.
“There are three main reasons why I was attracted to becoming the CEO of the Clarison Group,” Mark says. “The first is that the UK’s façade industry is large and fragmented, with scope for consolidation and room for some large professional domestic players to emerge. The second is that this is an industry that I and many others see as one that is likely to undergo significant change in the coming years – particularly in the aftermath of the Grenfell Tower enquiry. It is a highly legislated and technical industry, which is having to adapt to changes in these areas. Other changes to be expected are a continued transition to offsite production and the need to meet the 2050 Carbon Net Zero Commitments. With change comes opportunity. Finally, the third reason is that the four companies that have come together to form the Group are already high performing businesses with strong, respected brands.
“The combined companies make the Clarison Group the strongest domestic player in the UK and Irish markets, offering a solution to customers that have – in the past – had to look to continental Europe and Asia for support on larger, more complex projects,” Mark explains. “The structure of the Group allows for the vertical integration of design and fabrication, the ability to share capacity between companies, and to become involved with projects at an earlier, pre-construction phase. The lower carbon footprint achieved by domestic production also results in more sustainable solutions for our clients.”
Much of the Group’s success is derived from the people side of its various businesses. Therefore, ensuring that it has engaged teams is of paramount importance, and is an area where significant investment has been made in recent years. “It is crucial to have a common purpose and associated values that help everyone to feel that they are heading in the same direction,” Mark states. “In this regard, in 2019, Alucraft in Ireland defined ‘Guiding Principles’ for its team through a Continuous Improvement project whose team consisted of senior managers and various employees. The project culminated with the development of eight Guiding Principles, which had broad employee buy-in from the outset due to the collaborative nature in which they were formed.
“The project also highlighted the need for an engagement platform to boost internal communications, which were previously fragmented across the office, factory and site-based teams. Alucraft also recognised the need for a centralised portal to host the new ‘Reward and Recognition’ awards, which had been deployed alongside the rollout of the Guiding Principles.
The rollout of a workplace engagement app was kicked off in early 2020 for the Alucraft and Williaam Cox teams in Ireland, Poland and The Philippines. It has since been embraced for deployment across all of the Clarison Group companies and it will be launched in the UK and Spain in Q2 of this year.”
The tool has amplified the Group’s community spirit, grown a culture of recognition, and bridged communication gaps between senior management and employees. “It has been a valuable resource to our HR department who have utilised the platform to carry out regular pulse surveys to track employee satisfaction – especially useful throughout the past year when remote working became the new norm,” Mark adds.
As a newly formed Group, 2021 will see it developing its Vision, Mission, Goals and Strategy for the next three to five years, as well as ensuring that its business units continue to grow and provide excellent customer service. This will happen alongside continued investment in its different businesses. Recent examples of this include Alucraft UK’s purchase of a 3000 sqm manufacturing facility in Rotherham in February 2020.
“The UK and Ireland market for glazed façades is currently worth over £4bn so, at £100m turnover today, the Clarison Group’s market share is below three per cent. With our investment in Design for Manufacture & Assembly (DFMA) processes, our advanced manufacturing facilities, and the industry-wide need for off-site manufactured solutions, I believe that there is plenty of opportunity to increase our market share and become a £150m Group in the coming years,” Mark concludes. “That is provided we can do so in a controlled, risk managed and profitable manner.”
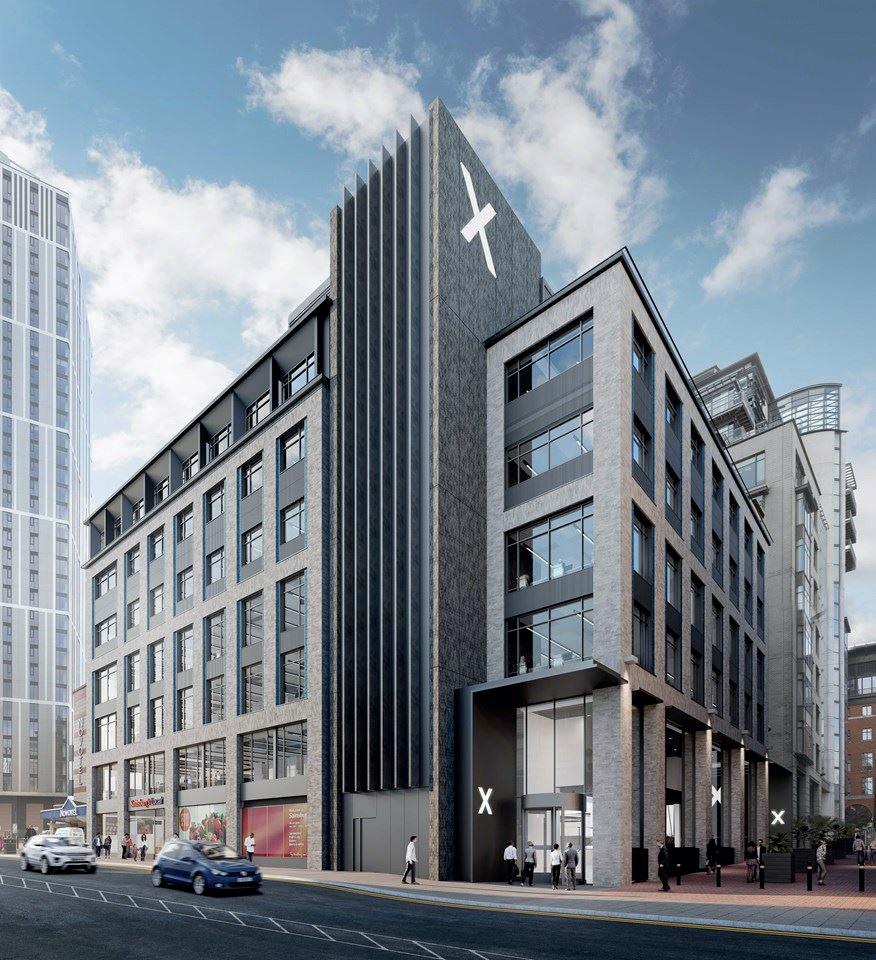
The Clarison Group www.theclarisongroup.com
Services: Building envelope solutions and architectural glazing
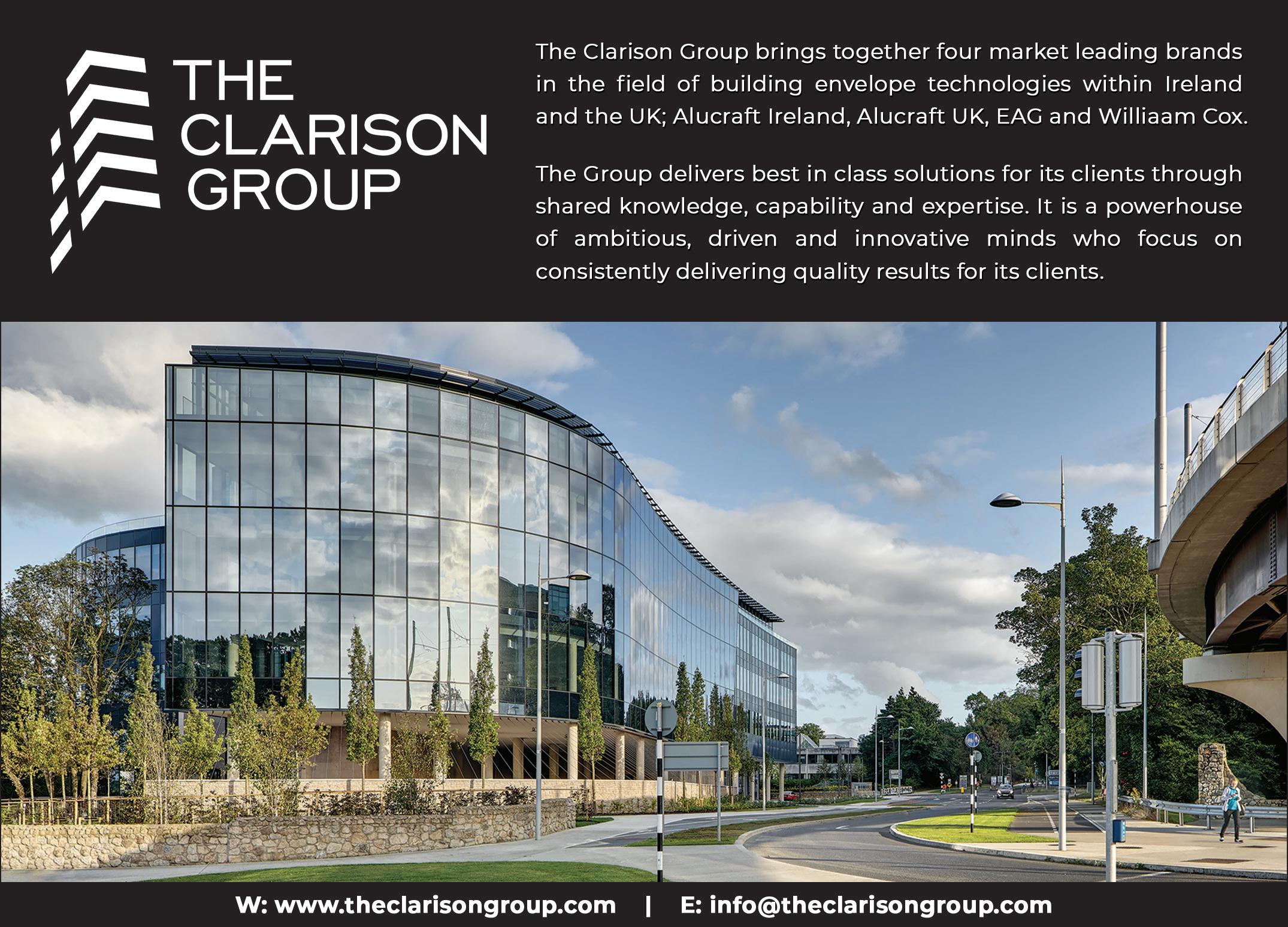
A phoenix on the rise
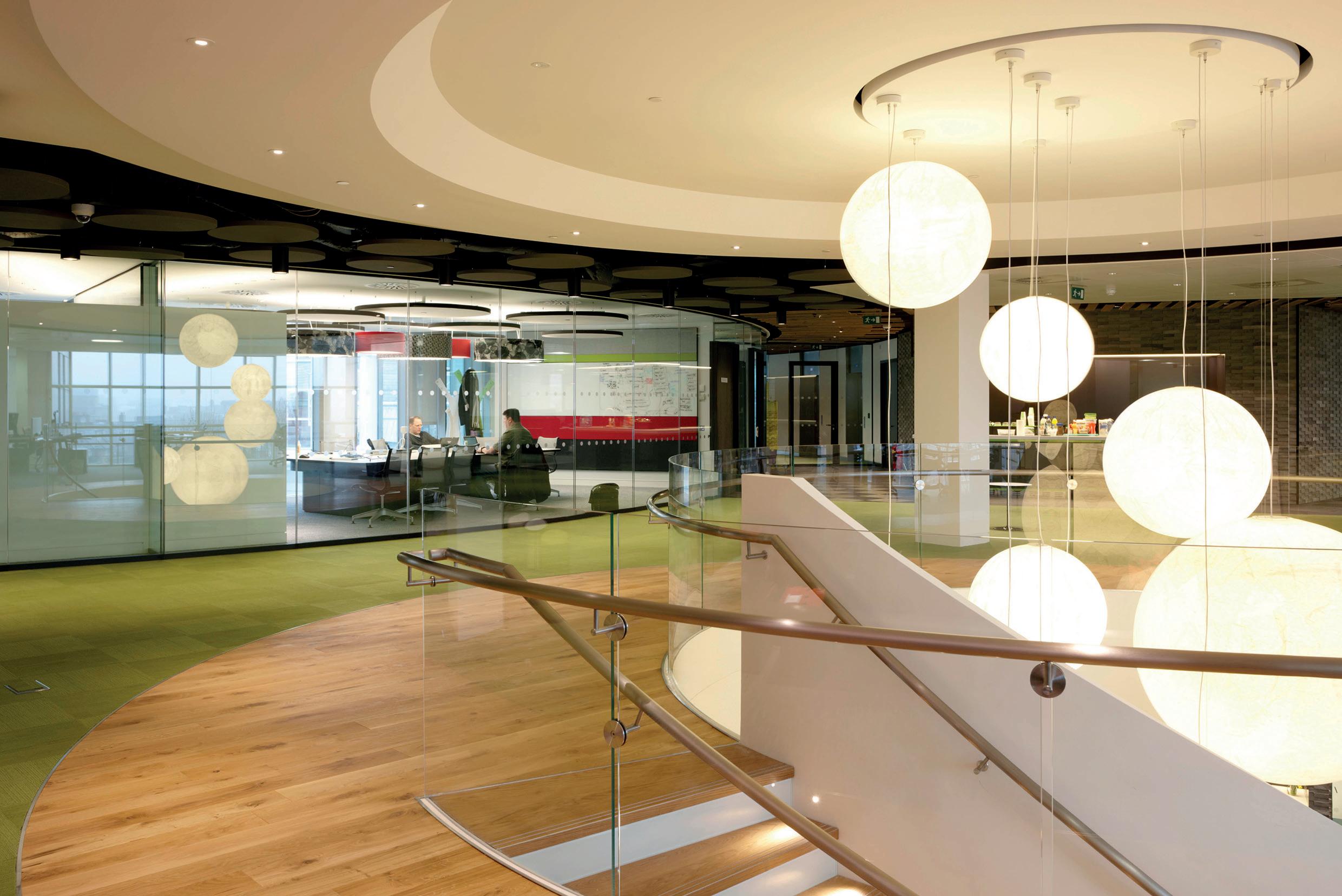
A considerate contractor of considerable experience, Phoenix ME Ltd’s work is underpinned by its values of delivering consistent outstanding performance, maintaining a collaborative, client-focused approach, and having the utmost regard for health and safety
Established in 1931, Phoenix ME Ltd (Phoenix) is today an established market leader, providing the design, installation and commissioning of mechanical and electrical systems to a number of different work sectors. These include, commercial offices, banking establishments, data centres, government buildings, education facilities, residential infrastructure, retail units, and pharmaceutical laboratories. Phoenix’s project experience ranges from £1 million to £50 million in value, and covers the full spectrum of services and distribution systems required for varied building solutions.
Phoenix’s CEO, Lee Compton, first became involved with Phoenix some 15 years ago. “At that time, we were considered a London-based electrical trade contractor, and while we didn’t have what I would call a large customer base, what we did have was a track record for working on some relatively niche projects in and around the city,” Lee begins. “My remit upon joining the business was to grow it, and I had a clear desire to make Phoenix a reputable and respected, multiservice M&E business, that could grow organically.”
This goal would go on to quickly be achieved, with the
business growing year-on-year by anywhere between ten per cent and 20 per cent, taking on more new clients as time passed. “We set ourselves a target on taking on a new client every year, and with each one we looking to cultivate a working relationship that would see us carry out multiple projects, not just the one,” Lee continues. “At the same time as turning ourselves into a relationshipdriven business, we have also picked up an increasing number of larger-scale projects, which has contributed hugely to growth.”
Defying limitations
Within the last decade, the business has also progressively moved into tackling work across Europe, which was a unique venture for a company such
As you can imagine, we are very much going to be focusing our efforts on those markets or sectors that continue to be sources of high growth for Phoenix, such as data centres. We also envision more opportunities for us arising from our work with the likes of AstraZeneca in the pharmaceutical and life sciences worlds. There is clearly an awful lot of investment being made in those sectors at present, and we want to be a key part of the works that will arise from that
Diffusion Group
As long-standing supplier for Phoenix ME Ltd, Diffusion have the privilege of enjoying a close business relationship. It has blossomed from foundations built upon our shared values: trust, collaboration and work ethic. Clear communication and understanding specific needs of each project has been key. Our positive interactions at the tender stage, constructive exchanges during design and construction and full engagement during handover have been pivotal in making each project successful for both parties. As Phoenix continue to grow as a Building Services company, the experience within Diffusion paired with our innovative products makes us the ideal partner to accompany Phoenix on their journey.

as Phoenix, but also a highly successful one, with its projects gradually expanding in size, scale and notability. It has in fact led to the business being named on the Sunday Times HSBC International Track 200 league table of Britain’s mid-market private companies with the fastest-growing international sales.
“Another of my ambitions when beginning my role at Phoenix was to make it as good, if not better than its competitors,” Lee states. “While I believe that we have achieved this, it is an area of focus that continues to drive not only myself, but all of our people, and one that can only be achieved by remaining to be seen as one of the more proactive, easy to work with businesses in our field, and one that defies limitations to carry out any type of job.”
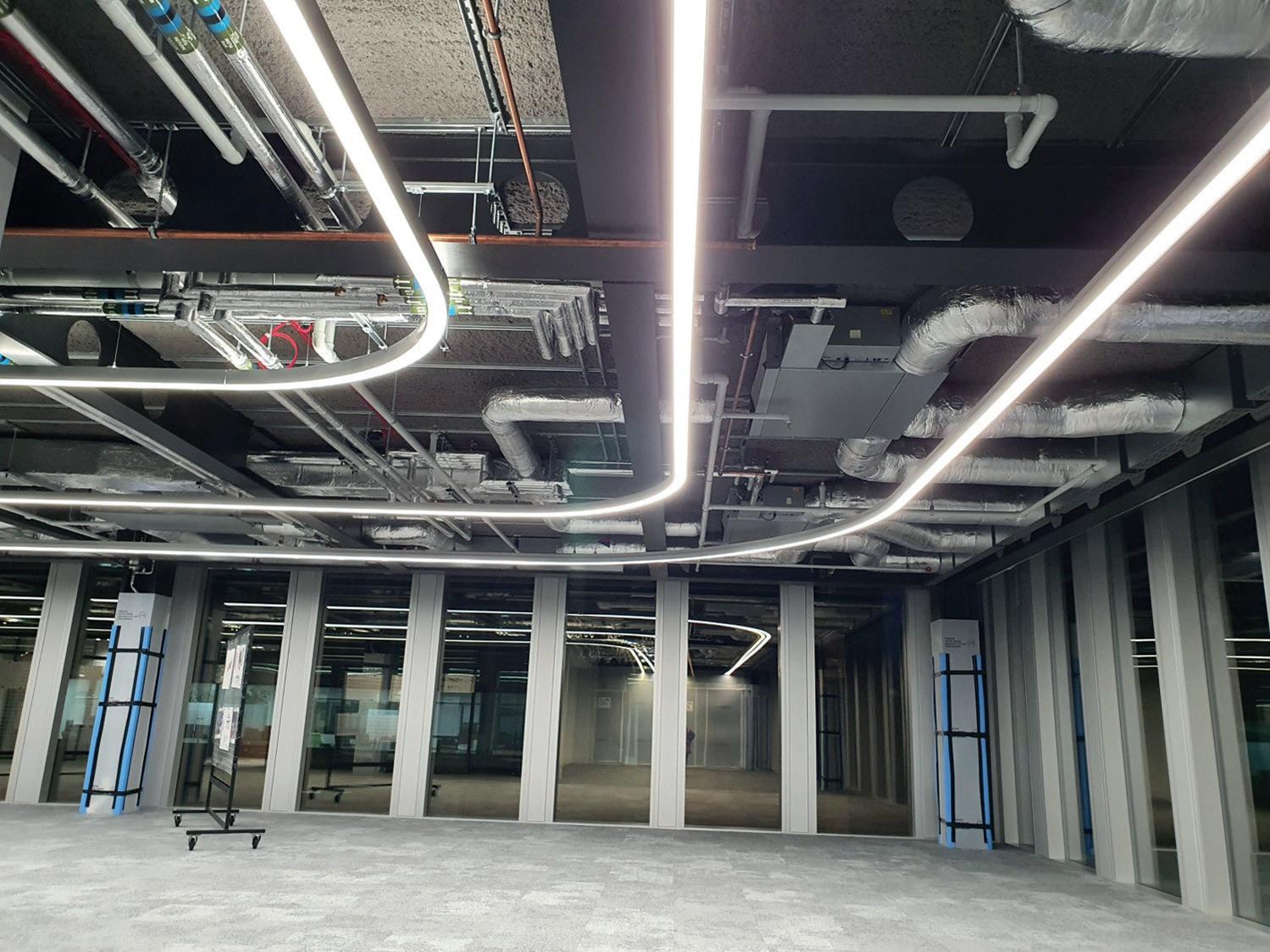
Prestige projects
In terms of projects and the types of market that Phoenix serves, it has endeavoured in recent years to serve a diverse range of sectors. Today, one of the busiest markets that it serves is data centres, while the commercial sector also remains fairly busy and buoyant, and it is making good strides into the pharmaceutical and life sciences industries. Going forward, it is also hoped that key infrastructure works will also increase in frequency in the months to come, which the company very much intends to be involved with.
Taking a look through Phoenix’s website and its showcase of past projects, there are a wealth of incredible examples of the work that it has carried out for all manner of blue-chip clients. These range from projects on behalf of
DAL
During their 35-year association, DAL and Phoenix ME have successfully worked together on many projects. These include an array of building infrastructures in the City of London and Canary Wharf and most recently Google headquarters. Our working relationship continues as we supply a variety of luminaires for the iconic Battersea Power Station and other prestigious developments.
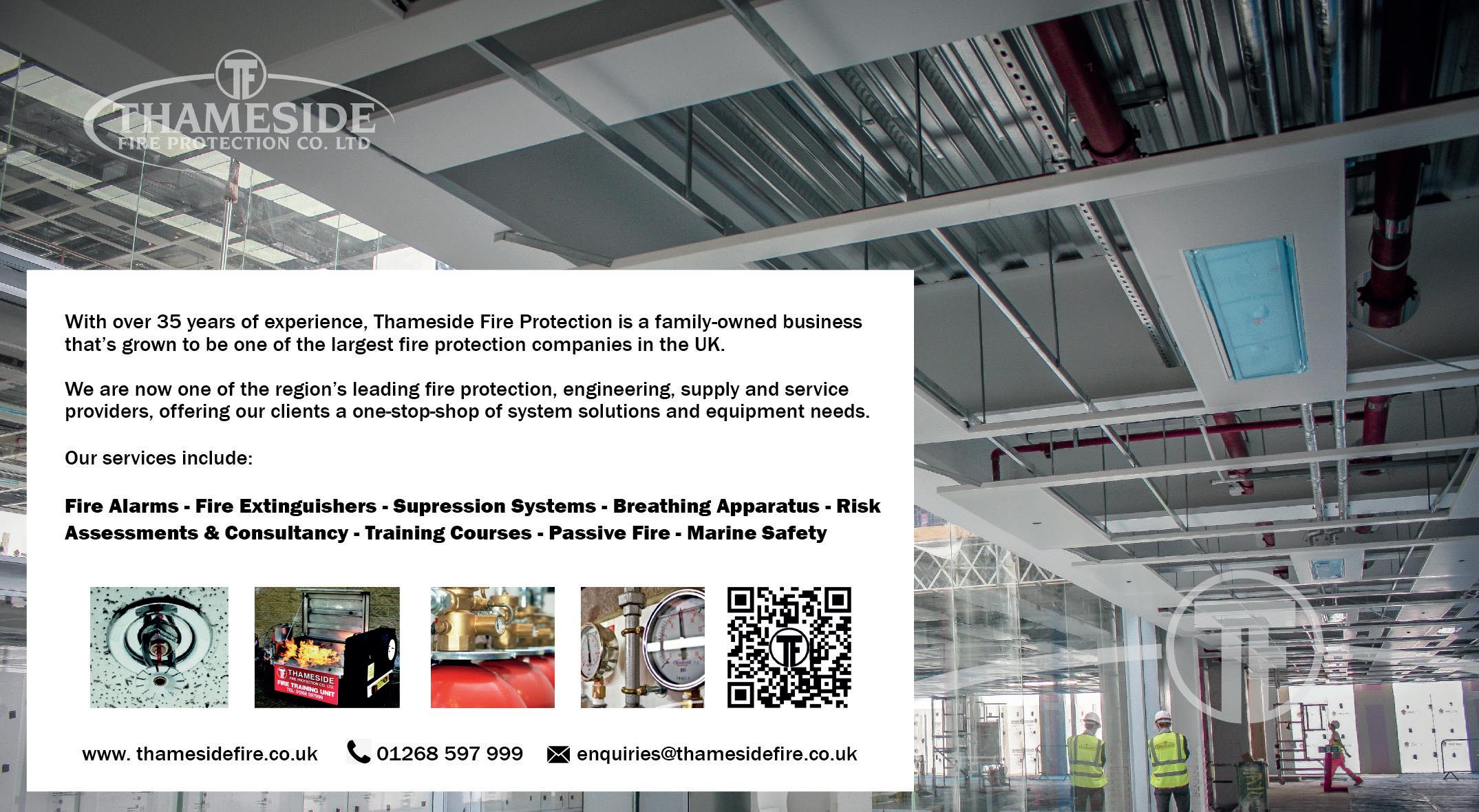
Elizabeth Line Crossrail Station
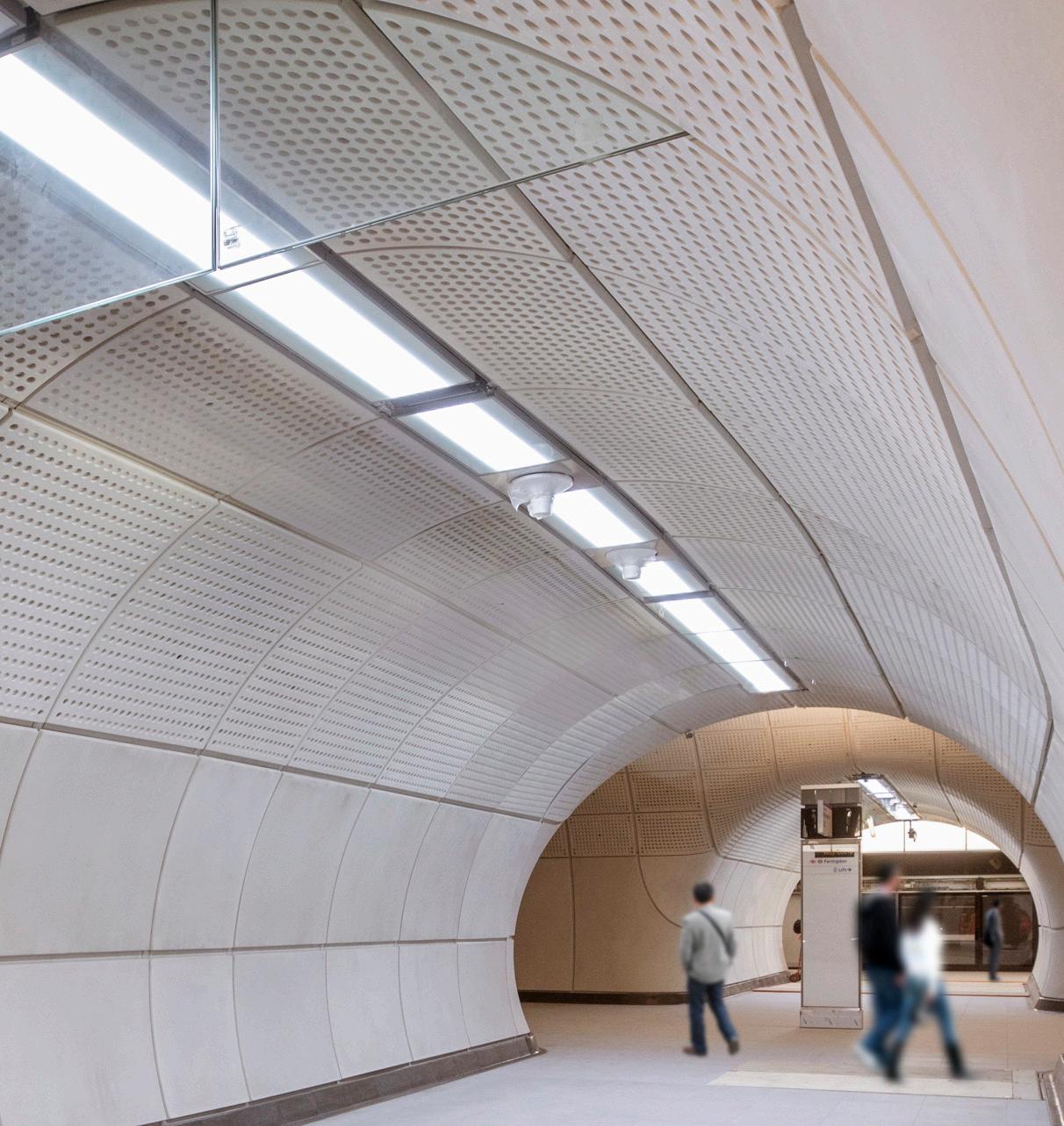
Designed Architectural Lighting the established designers and manufacturers of high-quality luminaires has merged with CP (Compact Products Ltd), a worldwide lighting components manufacturer. As close trading partners for nearly 30 years it is a good match. The new company structure allows direct access to CP’s manufacturing expertise, their state-of-the-art laboratories and production facilities which complement a long-established UK manufacturing base. This ensures DAL’s UK designed products and brand remain competitive. With this new and exciting expansion DAL has relocated to larger premises in Underwood Works, a distinctive former industrial building in Hoxton on the edge of the City of London where they still offer their unique client-oriented work ethic.
DESIGNED ARCHITECTURAL LIGHTING
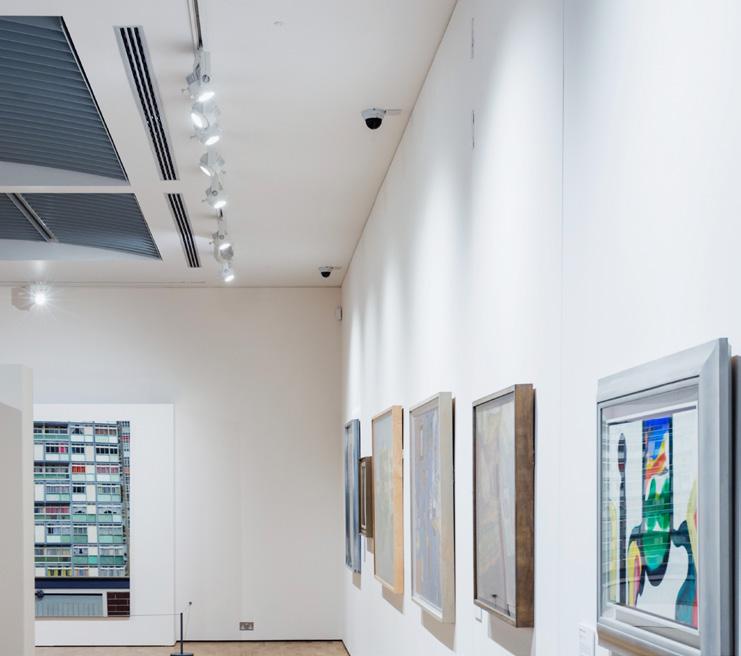
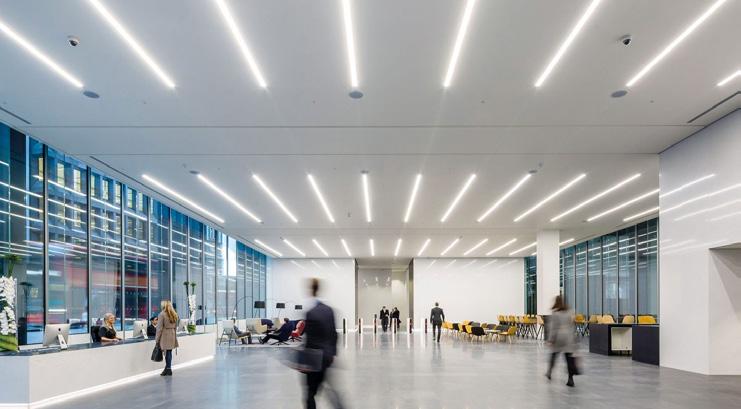
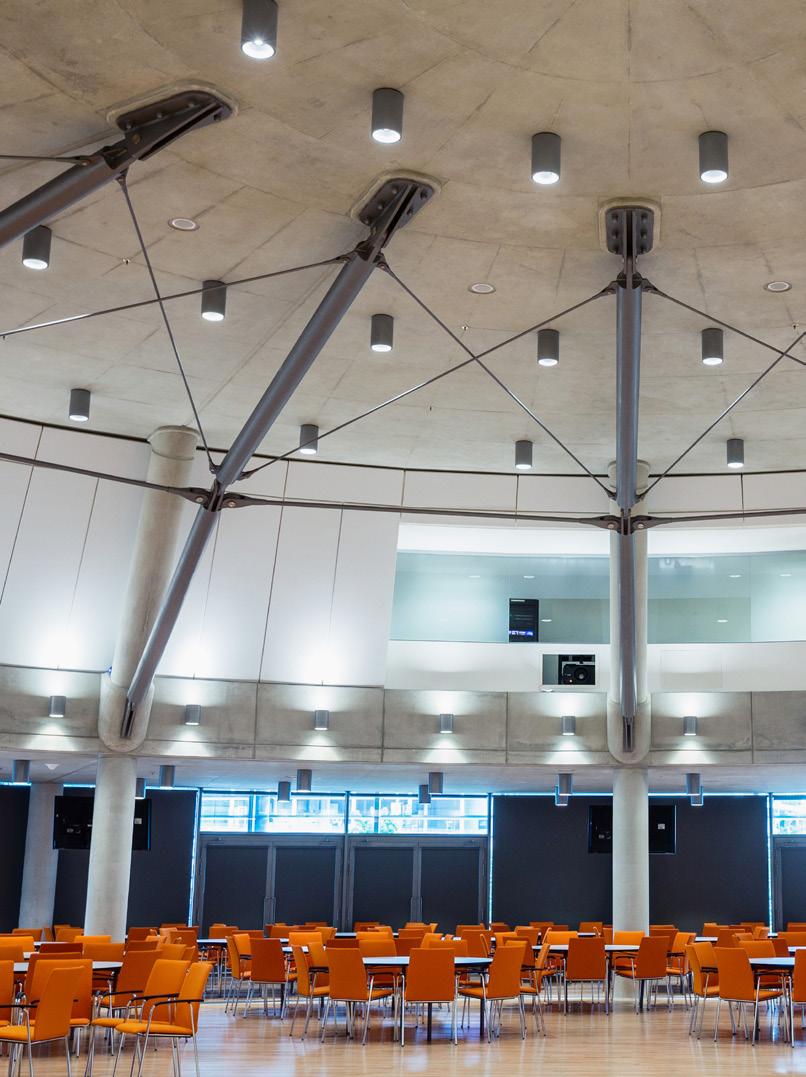
While DAL’s design team is developing new downlighters and linear lighting systems with the most up to date light sources, they are also applying their diverse skills and knowledge to a variety of projects, including Art Deco custom luminaires for the listed Shell Mex House on London’s Strand, integrated cross passage luminaires, for the Elizabeth Line Crossrail stations and exclusive downlighters for the Deutsche Bank Building, Moorfields. International projects continue to be part of the DAL portfolio, supplying a bespoke suite of downlighters to a Palace in Riyadh, Saudi Arabia and the National Museum in the United Arab Emirates.
Designed Architectural Lighting
• Designers and manufacturers of technical, high specification lighting • Established in 1984 • Major suppliers to commercial architectural, infrastructure and transport projects, art galleries and museums, leisure and retail outlets • Primary markets: UK, Europe, Middle East, South East Asia, China • Based in Central London • Designers and manufacturers of downlighters, wall washers, linear lighting and track mounted spotlights
CP
• Established 1983 • Designers and Manufactures of lighting products
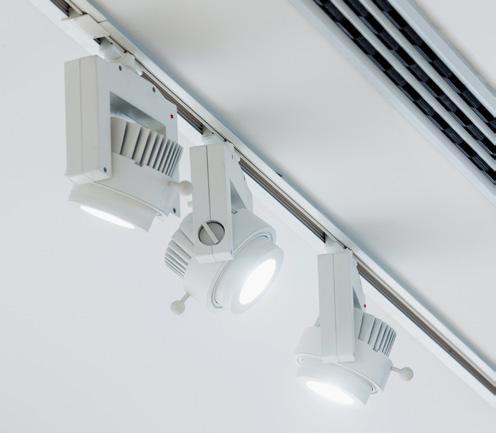
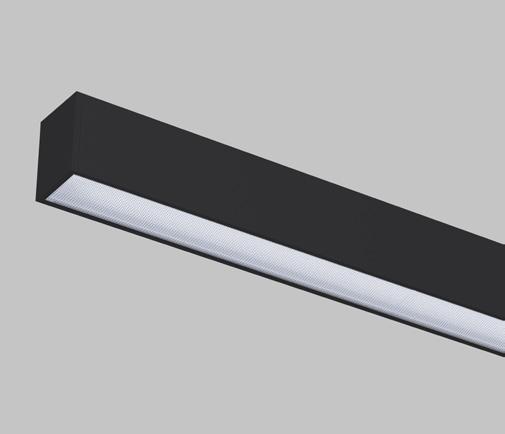
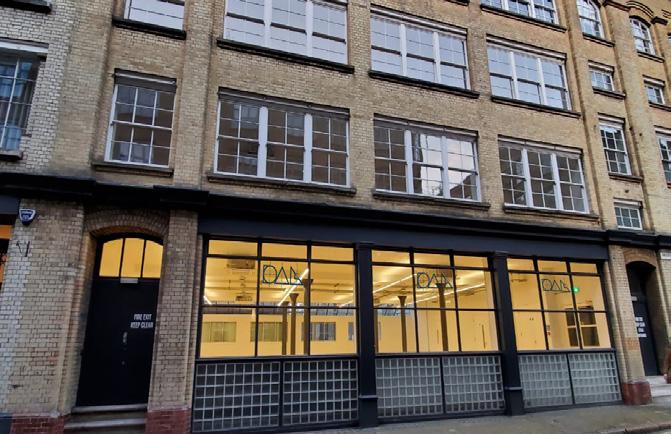
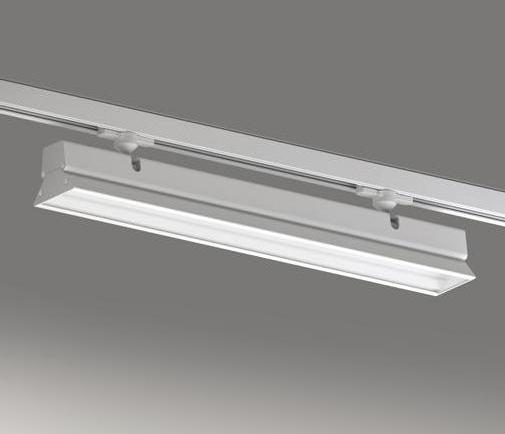
LONDON STUDIO Underwood Works 6-14 Underwood Street London N1 7JQ T +44 (0) 207 490 3998 www.dal-uk.com
the likes of Warner Bros, Wells Fargo, Credit Suisse, Amazon and Google. “Without doubt, we have completed a number of significant projects in recent years,” Lee undertakings – and will continue to focus on this area going forward. Meanwhile, within the commercial space we do like to take on what I like to think of as prestige jobs, with examples of our work present in places such as 100 Liverpool Street, and current work taking place on major developments such as the regeneration of the Battersea area of London.”
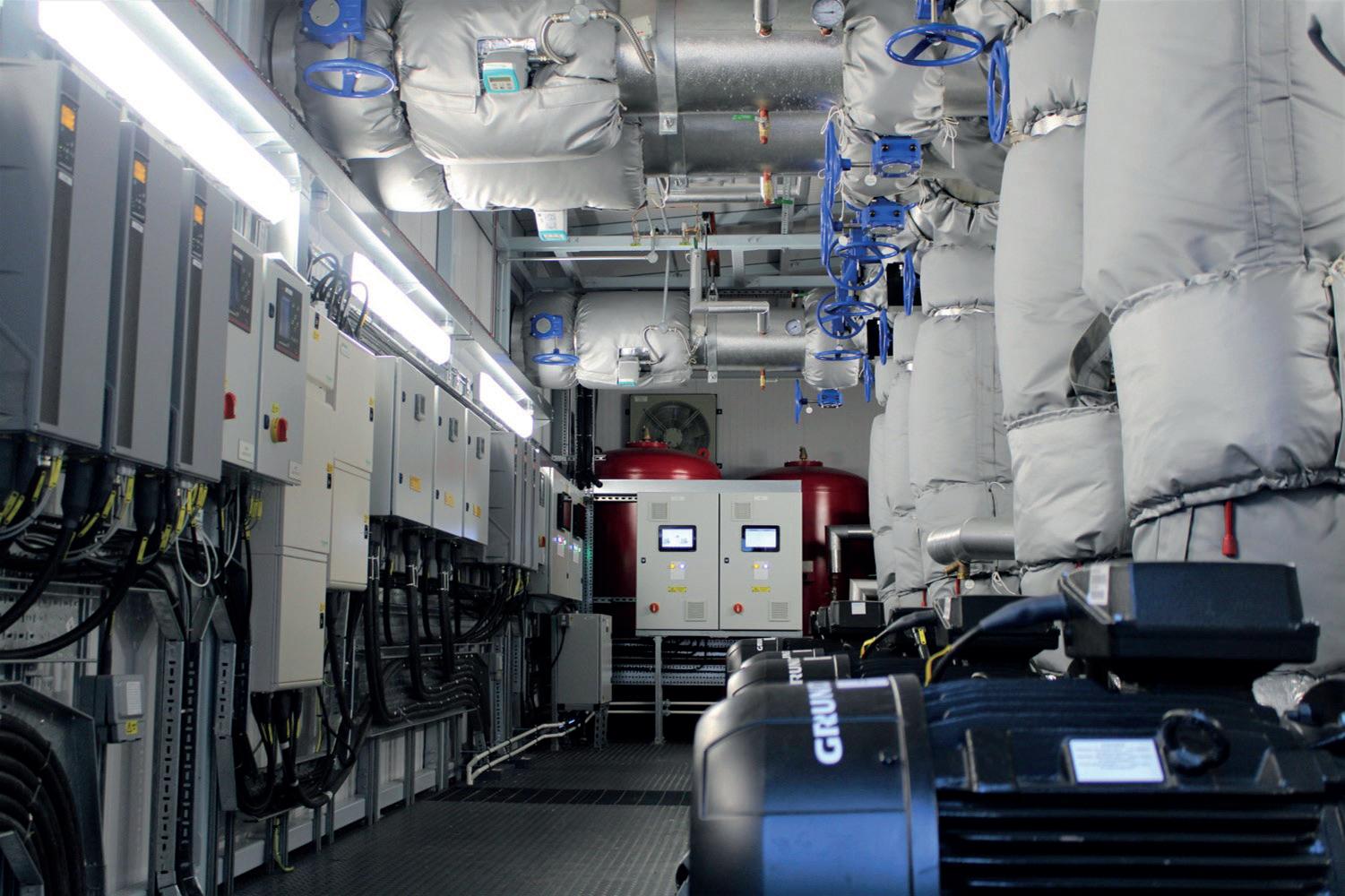
highlights. “We are particularly proud of our work delivering data centres both in the UK and in Europe – the majority of which are especially large, demanding
Simmtronic
Simmtronic have an excellent long-standing working relationship with PME, having worked together on a wide range of projects, from complex CAT B office fitouts and large CAT A commercial building refurbishments, to Shell & Core installations in data centres and industrial type premises. Phoenix excel at managing sub-contractors and suppliers which allows all parties to meet deadlines and fulfil client aspirations, as was the case with a recently completed 12-storey fit-out at 100 Bishopsgate. The lighting installation was complex and included specialist luminaires from multiple suppliers using various control protocols. Phoenix’s Paul McCluskey and Shane Keary smoothly coordinated all project elements. Business culture
Another ongoing project of note sees Phoenix working on Google’s new Head Office facility in King’s Cross. “This flagship undertaking for the company in the UK will result in one the biggest, most expensive and – frankly – sexiest buildings to appear in London for quite some time,” Lee enthuses. “When it comes to such projects, clients
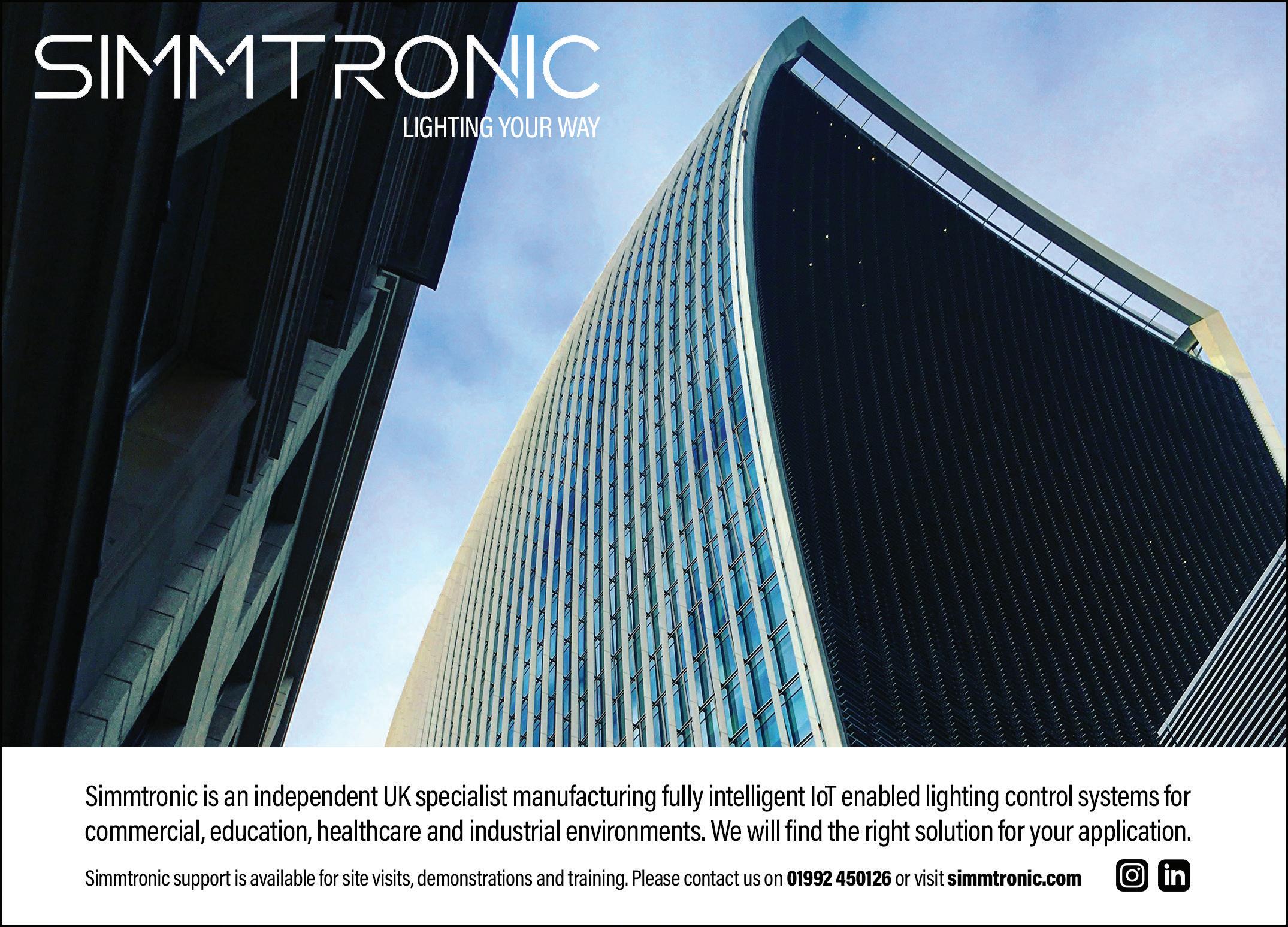
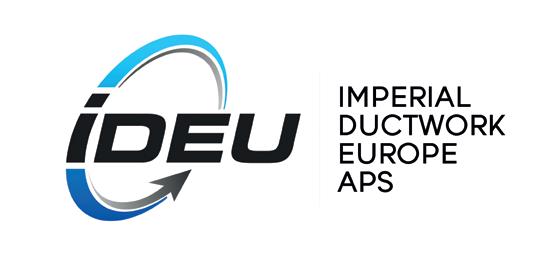
IMPERIAL HYGIENE SOLUTIONS LTD
The ductwork industry’s company of choice for some of the most prestigious buildings in London
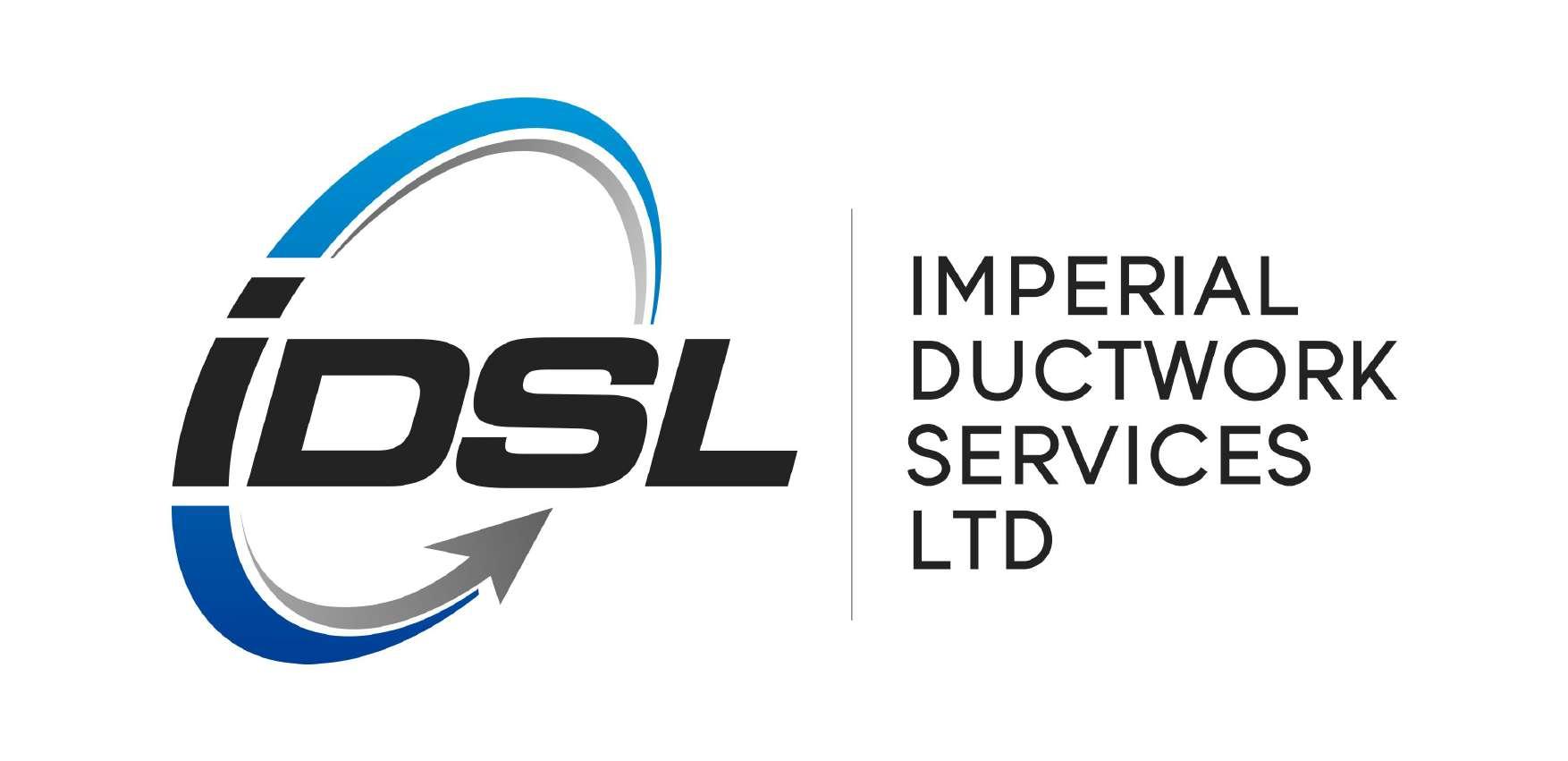
From its foundation in 1997, Imperial Ductwork Services Ltd (IDSL) has grown into one of the industry’s leading companies in the Manufacture and Installation of Ductwork Ventilation Systems. Our head office is based in Sidcup, Kent providing easy connections to the centre of London and the M25. We have a manufacturing facility located in Dartford, Kent including further overspill facilities located across London and South-East area. This provides us with flexibility to meet our clients’ needs and ensure we continually satisfy the demands of our daily operations. IDSL have the capabilities to provide services ranging from Full Airside turnkey installations, to more traditional sub-contract ductwork Supply and Install only packages. We have a wealth of experience working throughout the sectors providing shell and core, to fit-out installation within the commercial, residential, educational and pharmaceutical industries and Data Centres. We are proud to be able to work efficiently across the whole of the UK and Europe with offices based in Central London, Sidcup Kent, Milton Keynes, Chelmsford and Denmark. With further plans to open offices across Europe. Our engineering departments are fully supported by our own in-house CAD resources, offering full 3D/BIM modelling, as well as a dedicated Health, Safety and Environment department. Quality is paramount to our business as we strive to deliver exempla projects consistently. We are fully accredited to ISO standards 9001, 14001 and 45001. In addition to this we are pleased to have been awarded the RoSPA Gold Award for the last 10 years, in recognition of our commitment to Health & Safety. We also hold the LPS1531 Fire Rated Installation Accreditation, covering both Fire Rated Ductwork and Fire Damper Install, that none of our current competitors offer. Along with many other H&S Accreditations achieved. IDSL have their own Air Conditioning Department – As accredited Daikin D1+ Premium partner, Mitsubishi Electric Diamond Quality partner and fully qualified and conversant with all major manufacturers’ equipment, Imperial AC has built an enviable Portfolio of Blue Chip Clients. Imperial AC offer a variety of services – please check out our website to find out more. IDSL have their own Fire Department – Imperial Fire Solutions (IFS). Imperial Fire Solutions are a Risk & Development department that have at its core a thorough understanding of the requirements of these often critically systems within the built environment. IFS offers an impartial commentary on how these systems can be delivered and guidance on the relevant standards applicable to ventilation, smoke control ducts and kitchen extract systems. IDSL have a sister company – Imperial Hygiene Solutions Limited (IHSL) IHSL offer a specialist cleaning and testing facility and would welcome the opportunity to undertake any of the works listed below: l Ventilation Ductwork Cleaning l Kitchen Extract Degreasing l Fire Damper Maintenance l Pre & Post Vacuum Tests l Microbiological Sampling Surveys l Pre-Commissioning Cleans l Air Hygiene Risk Assessments l COVID 19 Cleaning l Digital Camera & CCTV Surveys of Ventilation
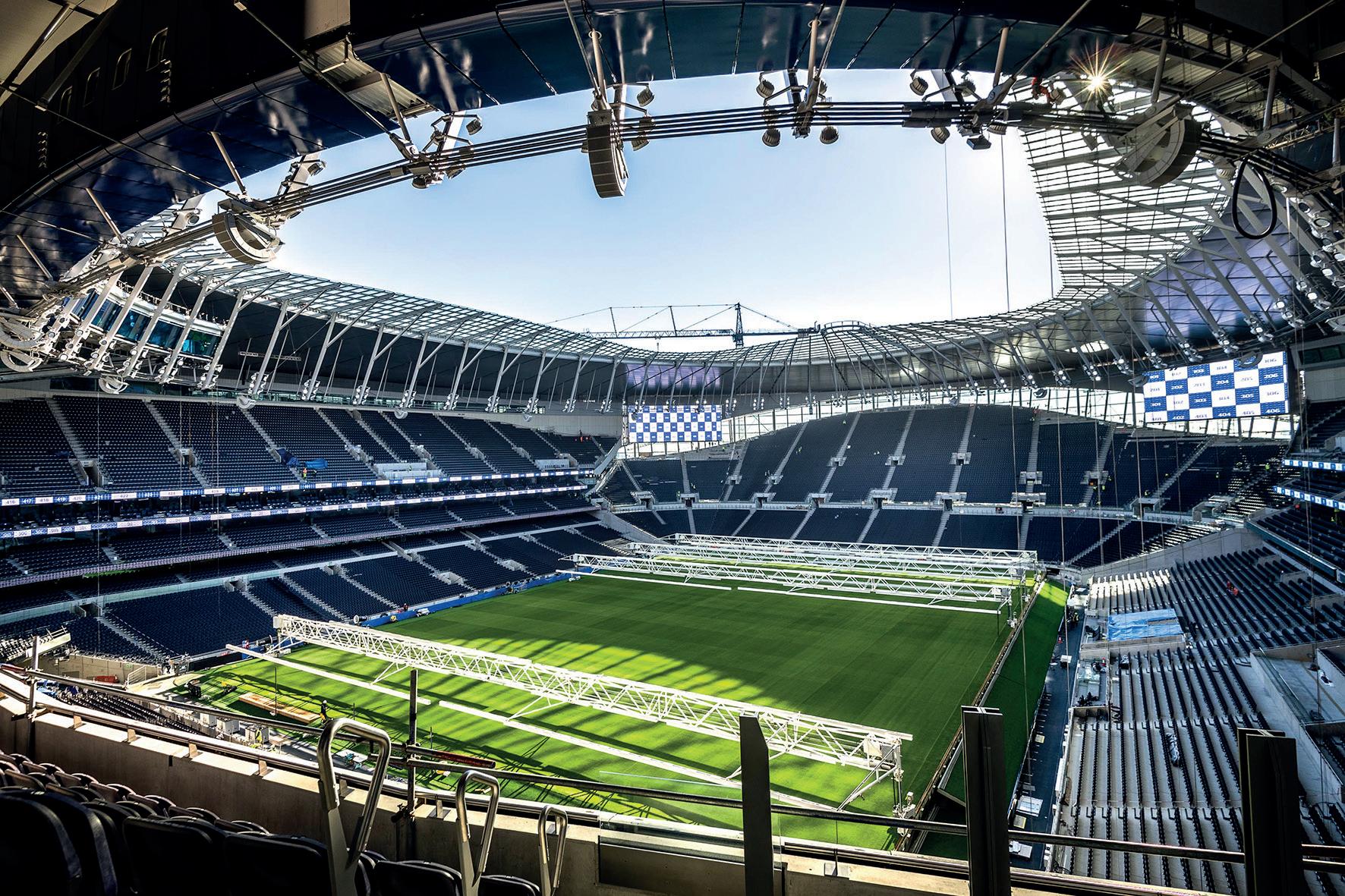
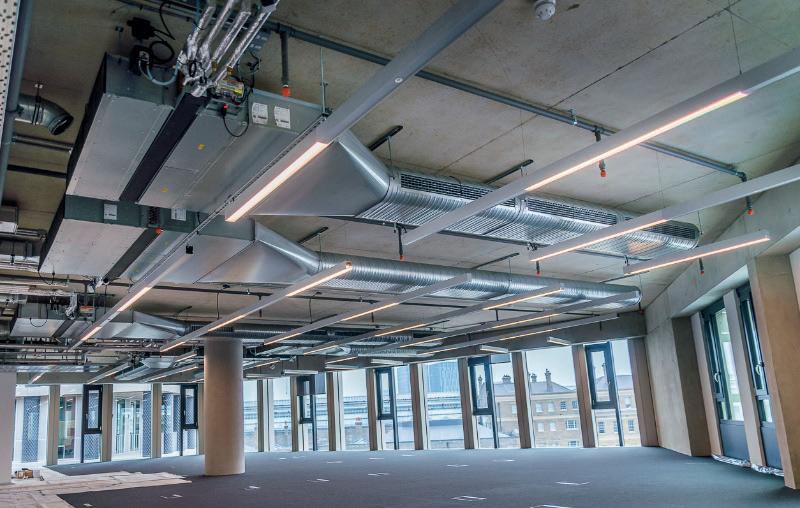
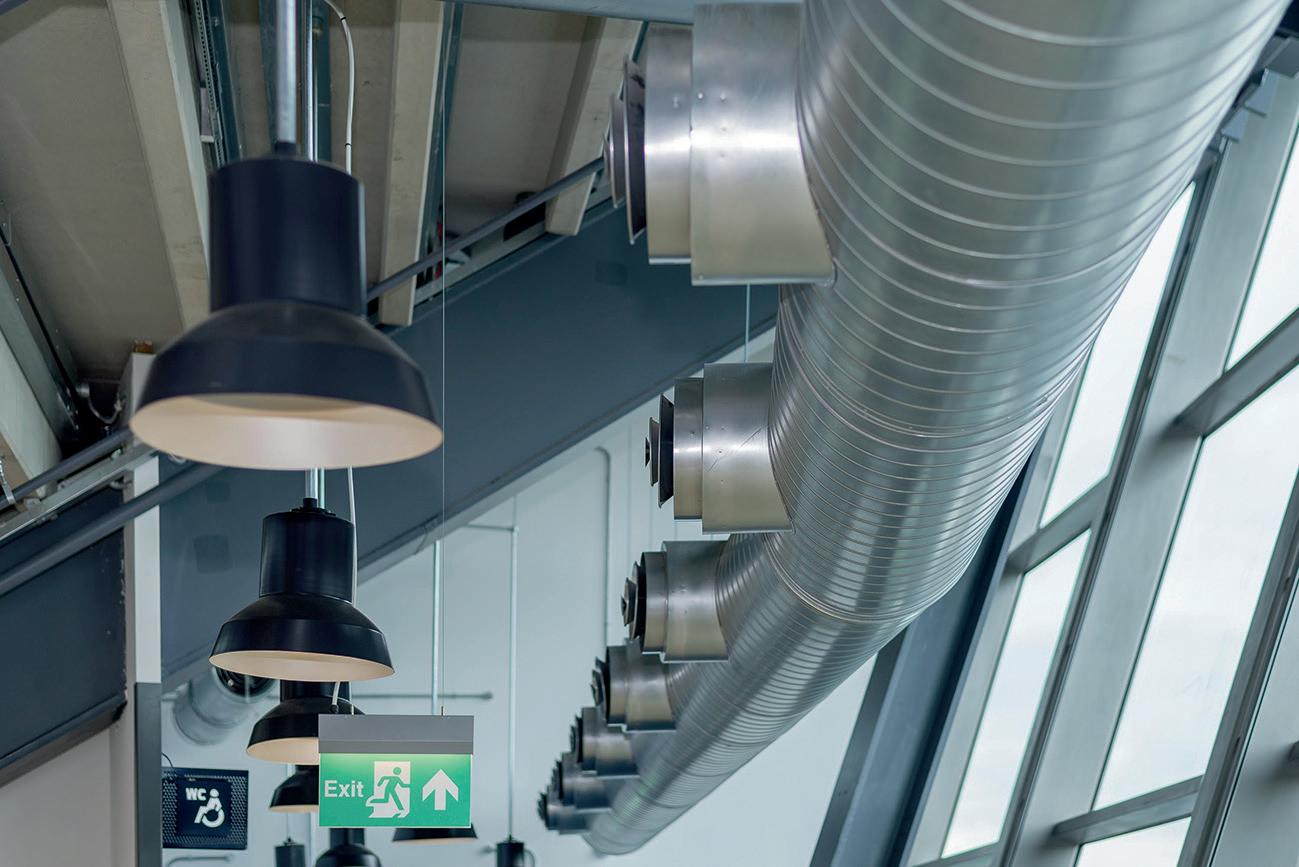
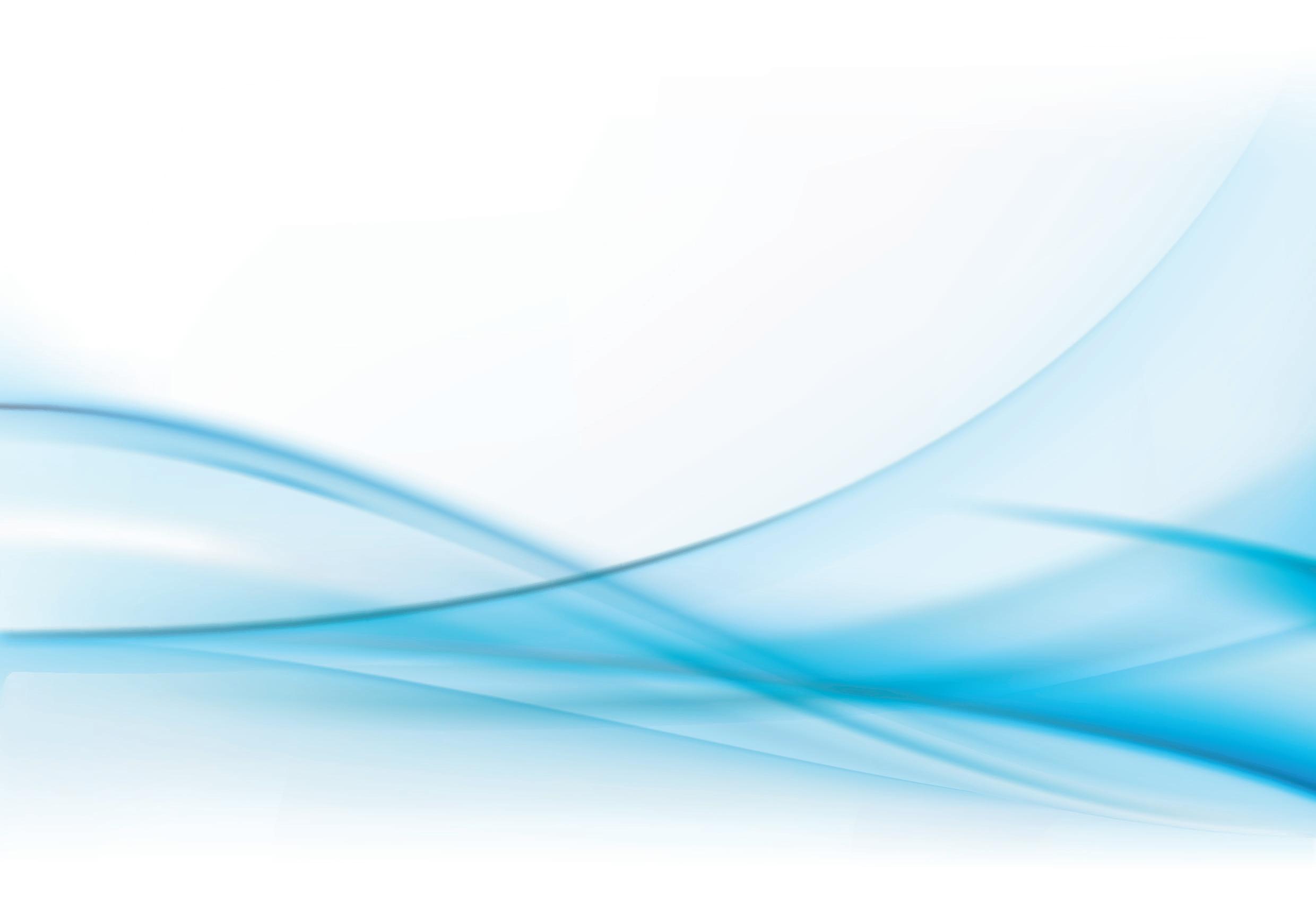
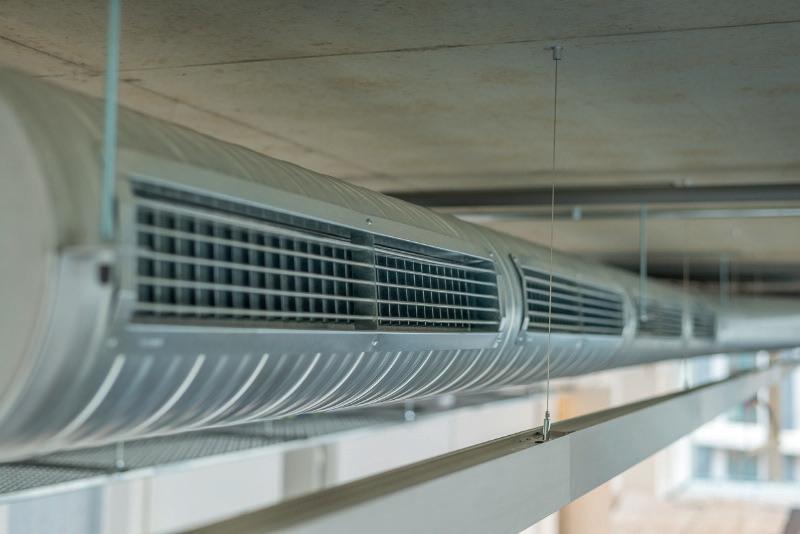
Our philosophy has always been to deliver our contracts to the highest level of quality and service; on time and snag-free. All our employees “ work closely with our clients to fulfil, in full, all of their requirements in the preparation, implementation and completion of each project“
like Google and many of the others that we have worked with understandably want to have the very best contractors on-board, and there is an extensive process that one has to go through to win this work. In this instance, we had to put a great deal of and embrace new technology wherever possible, and I firmly believe that is what we have shown to be more than capable of on countless occasions to date.”
With the healthcare and life sciences sectors being significant areas of growth for Phoenix in the past year, it can also be found working on several high profile, high quality projects, including one on behalf of AstraZeneca. “This project involves the construction of a global R&D facility located in Cambridge,” Lee imparts. “Operating alongside Mace Group, we are working extremely hard to deliver this important facility, which will ultimately be marketleading in a number of respects.”
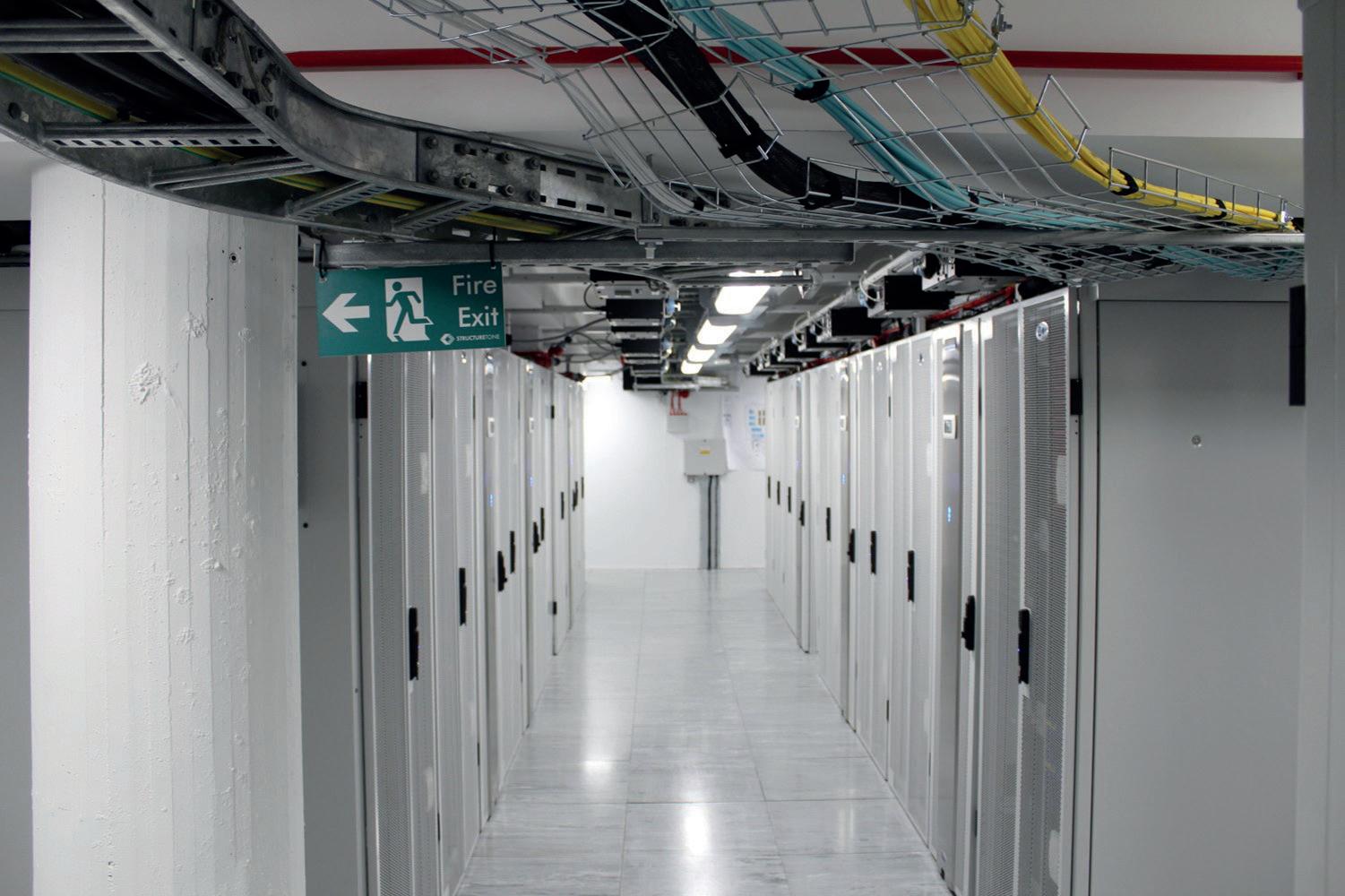
time and effort into proving that our culture as a business aligned with that of Google. On their part, they are looking to us for collaboration, for examples of out-of-the-box thinking, and for us to bring ideas to the party for how we can engineer things better Team effort
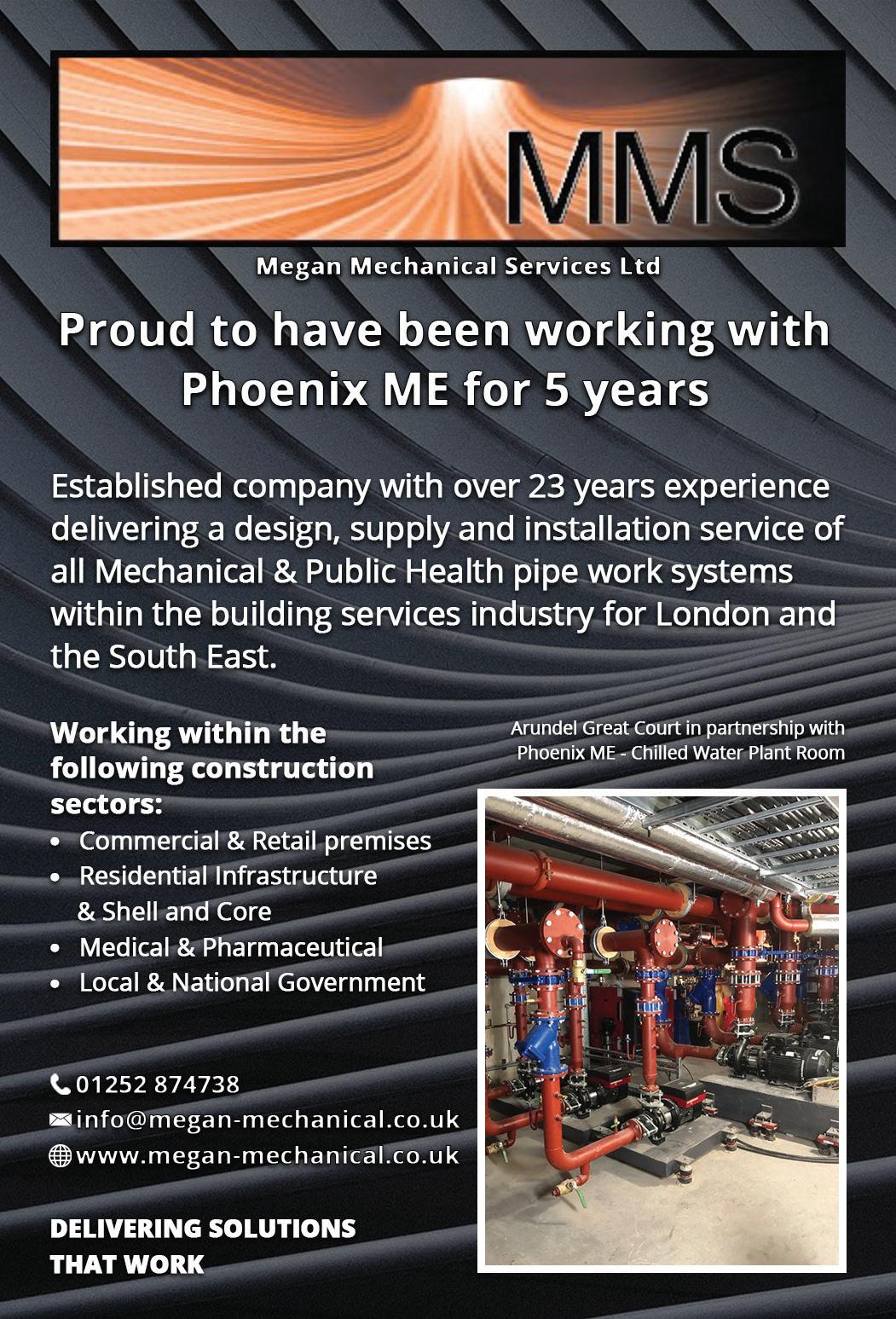
AstraZeneca is, of course, one of the leading names in the development, manufacture and distribution of vaccinations against the Covid-19 virus. Reflecting upon Phoenix’s own performance during the time of the pandemic, Lee reveals how it has worked
E+I Engineering
E+I Engineering are a global leader in the power distribution industry with four manufacturing facilities in Donegal, Ireland, Derry, N. Ireland, South Carolina, USA and Ras Al-Khaimah, UAE. From our European headquarters, E+I Engineering have been built on providing quality and innovative solutions for all our customers worldwide. E+I Engineering manufacture full power distribution systems including a MV and LV switchgear, busbar trunking, energy management systems and modular power solutions. This fully integrated power distribution system allows customers to deal with one expert supplier throughout their project. E+I Engineering have a highly experienced team of engineers to manage every aspect of a project, from concept design, through to manufacture, delivery, installation, testing, commissioning and after sales services. E+I Engineering have a proven capability of consistently delivering projects to the highest of standards. We boast a varied portfolio of successfully delivered projects across the globe including iconic buildings in major cities.
to overcome the barriers that have been presented. “When Covid-19 really took hold here in the UK back in March 2020, we – like everyone else – were initially speculating on what that meant for both the immediate and long-term future,” he says. “With construction being deemed to be an essential
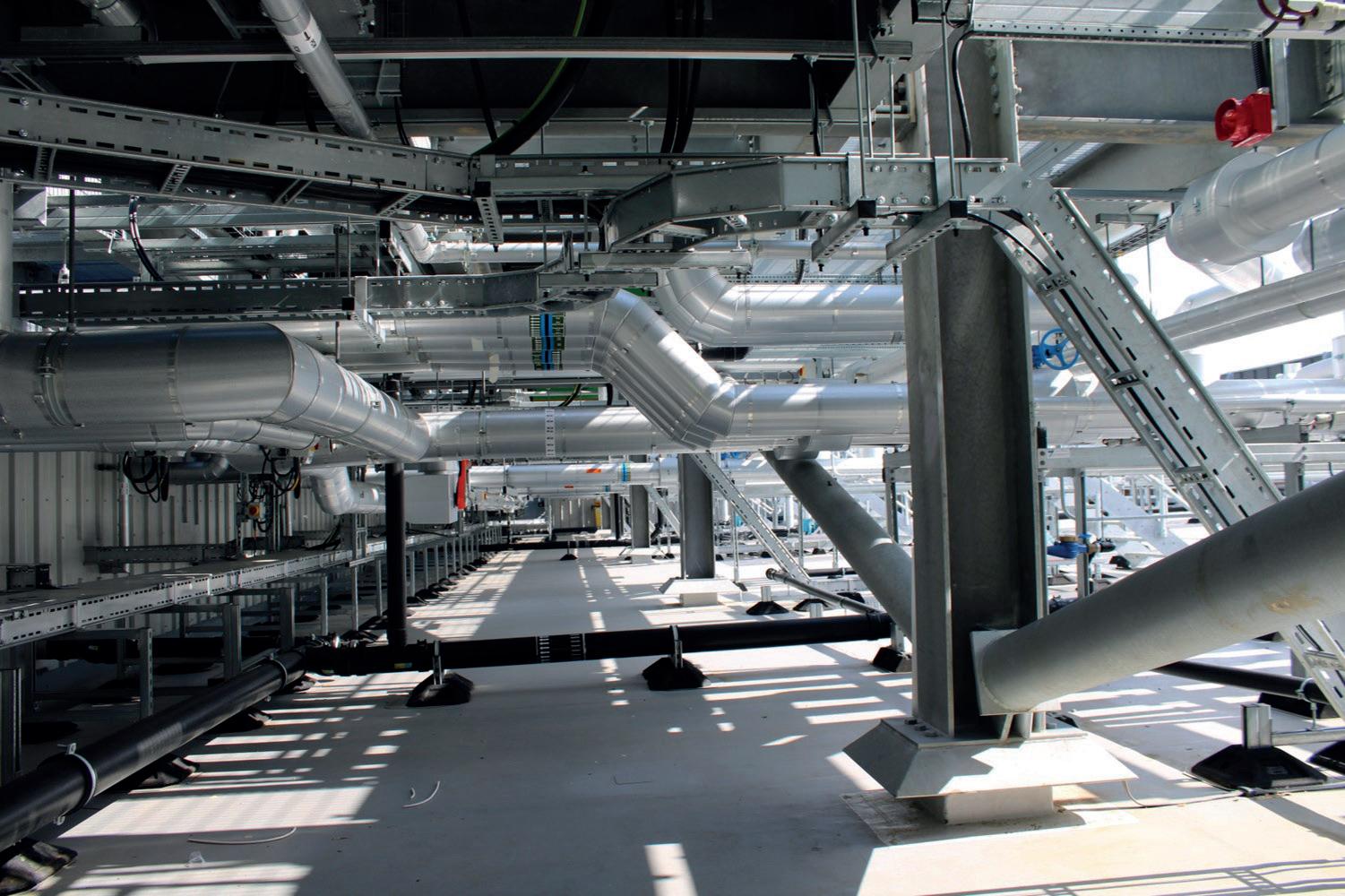
SEC Group
Since becoming a key part of Phoenix ME’s supply chain, SEC Group have worked on some very prestigious projects including Goldman Sacs, KGX1, credit Suisse and Battersea. Phoenix ME offer full support to their sub-contractors throughout the project duration, which in turn has assisted SEC Group’s growth over the past five years. SEC Group are looking forward to building further on our relationship with PME, with an exciting and prosperous future ahead.
industry, we quickly turned our focus towards overcoming the barriers to working under strict safety conditions, so doing things like providing the correct PPE for our people to use on site or modifying our transport arrangements to get people to and from site without taking unnecessary risks.
“I can truly say that we made it our business as a management team to drive the business forward through the embracing of new, safe ways of doing things, whether that be adapting greater flexibility in working hours or considering a larger degree of offsite assembly work in a socially-distanced environment. The result of our team’s efforts was that our turnover for 2020 actually increased year-on-year, rather than decreased which was
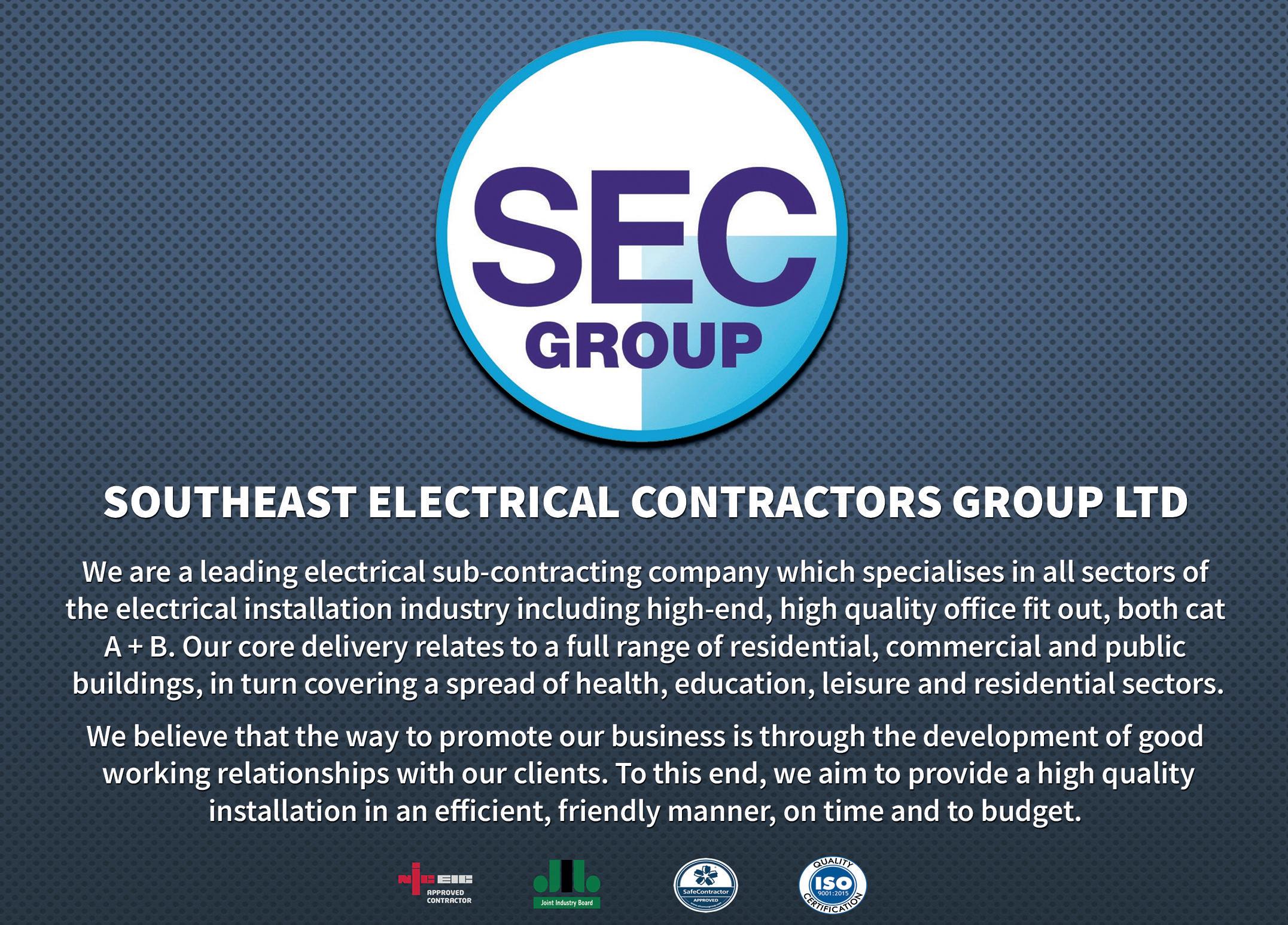
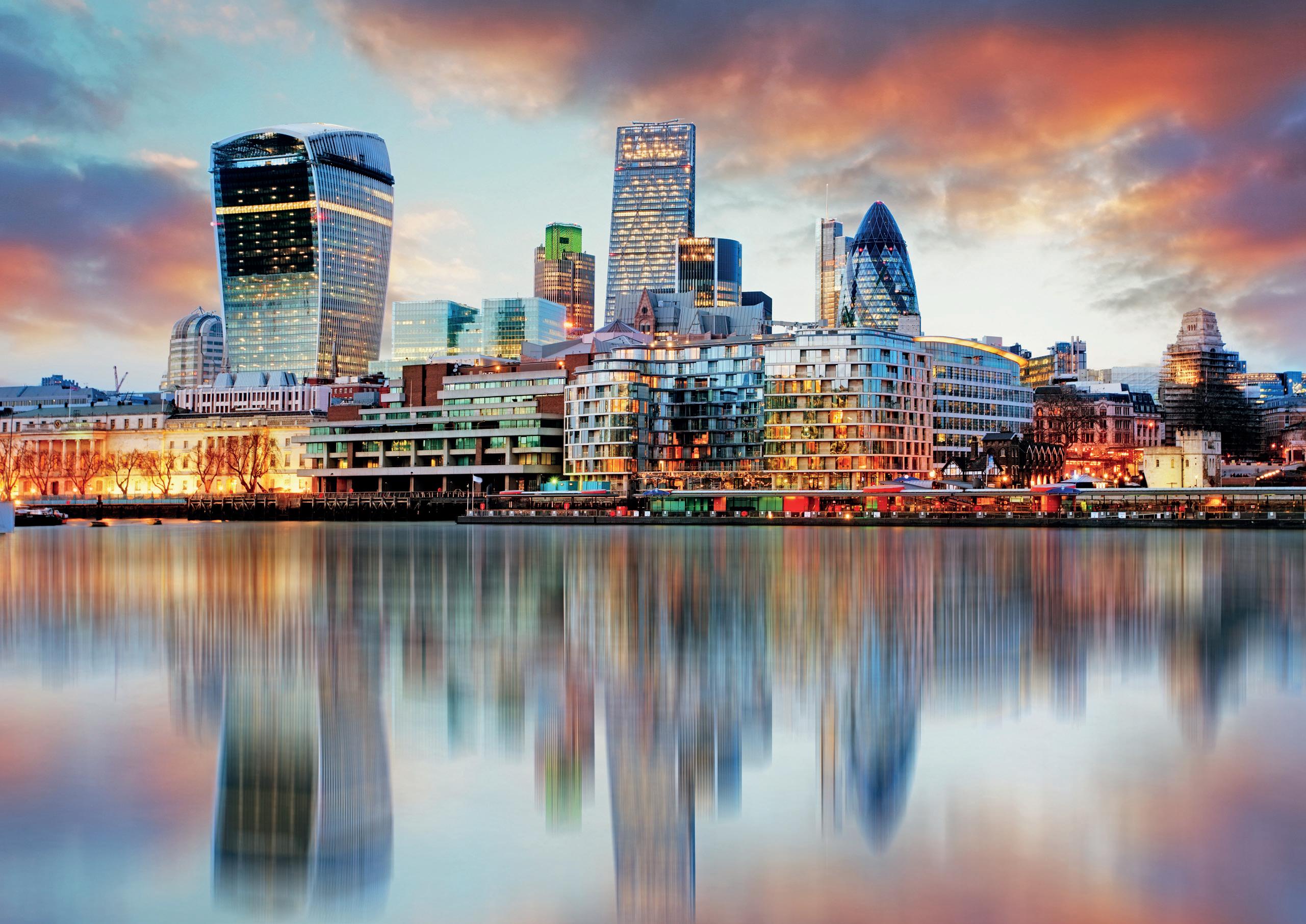
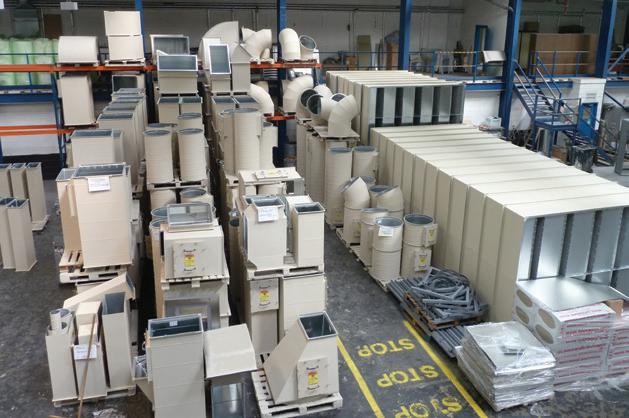
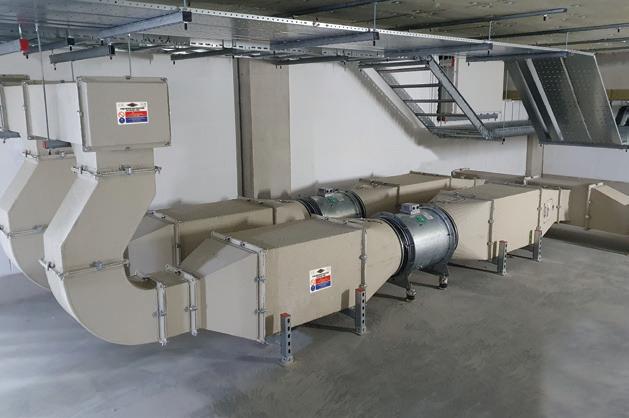
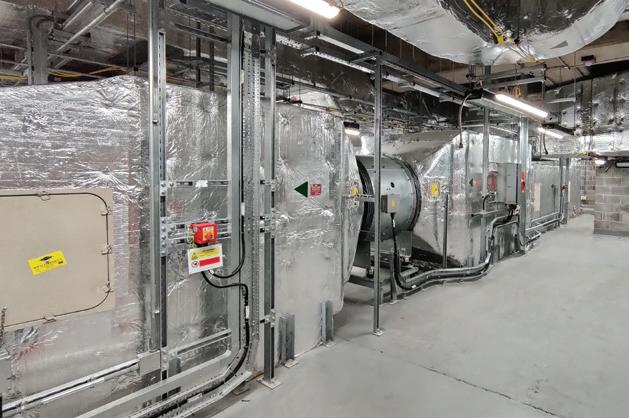
the case for a lot of other players in our field, and that says a lot about our company and the way we always strive to deliver for our clients.”
Growing family
With those results in mind, the company has an optimistic outlook for what the months ahead in 2021 have in store for it. “As you can imagine, we are very much going to be focusing our efforts on those markets or sectors that continue to be sources of high growth for Phoenix, such as data centres,” Lee states. “We also envision more opportunities for us arising from our work with the likes of AstraZeneca in the pharmaceutical and life sciences worlds. There is clearly an awful lot of investment being made in those sectors at present, and we want to be a key part of the works that will arise from that.
“We are also going to focus on doing more work across Europe in a number of different countries. We have worked successfully to date in places such as Finland and Belgium, and we want to take our experience in these countries and bring them to other locations across the continent. That will be
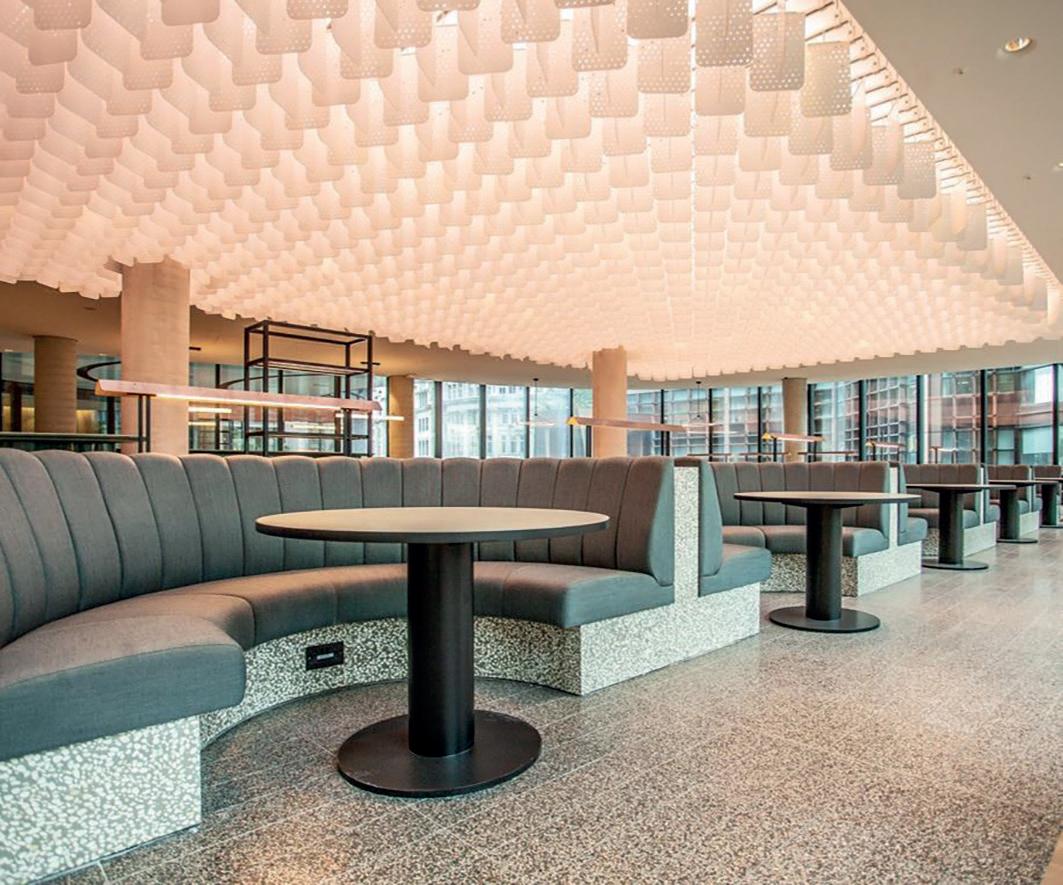
Mafi Mushkila Ltd
We’ve worked with PhoenixME for the past four years on many projects. As with most of our customers, every project is different. We have supplied a variety of solutions from simple floor standing heaters to more complex solutions using server emulators and real time, remote monitoring solutions. Projects include trading floors, office, IT equipment rooms to hyperscale data centers with multiple data halls. The key to our great working relationship with Phoenix is communication and partnership. We are grateful for the many years we have worked together and look forward to our future partnership.
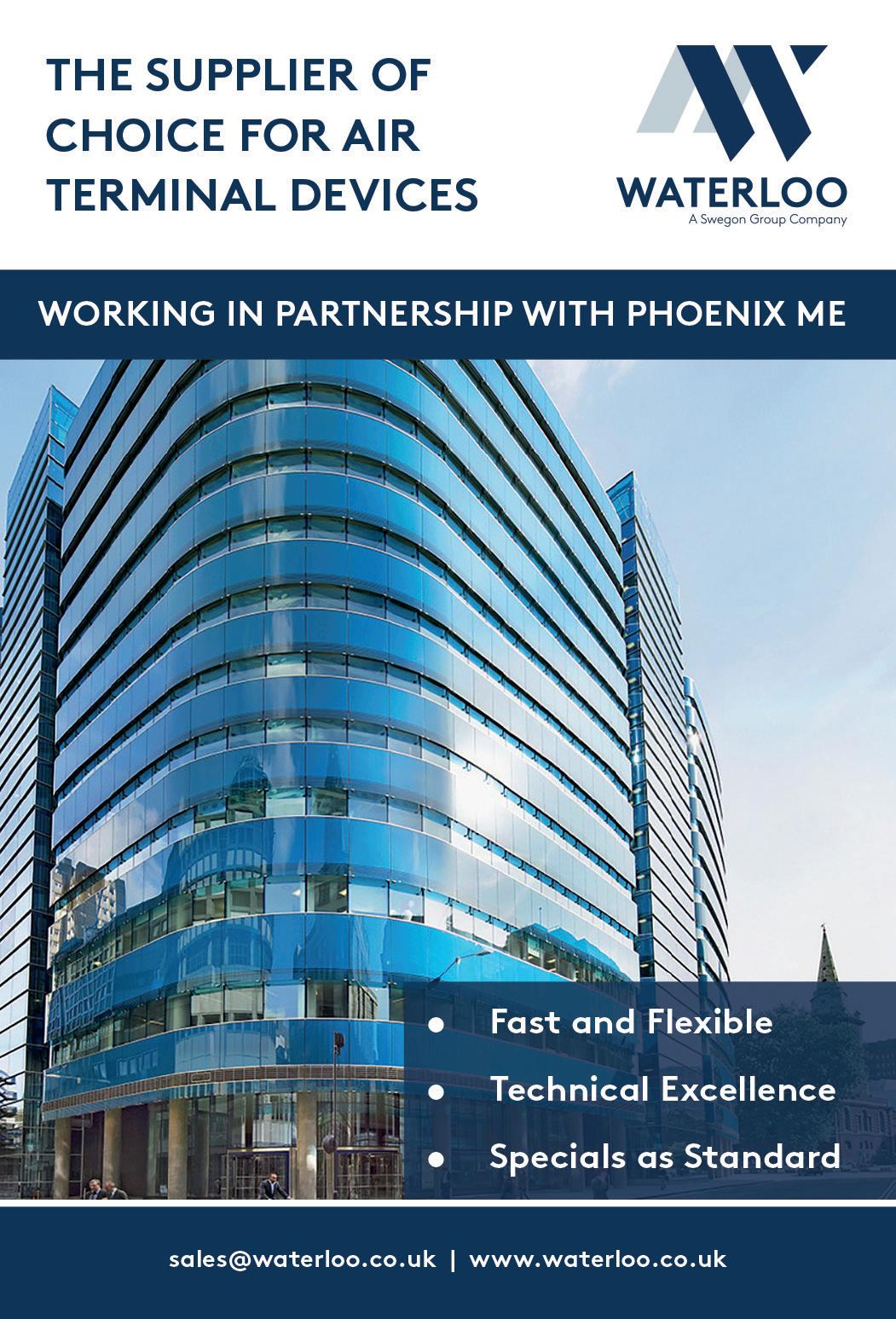
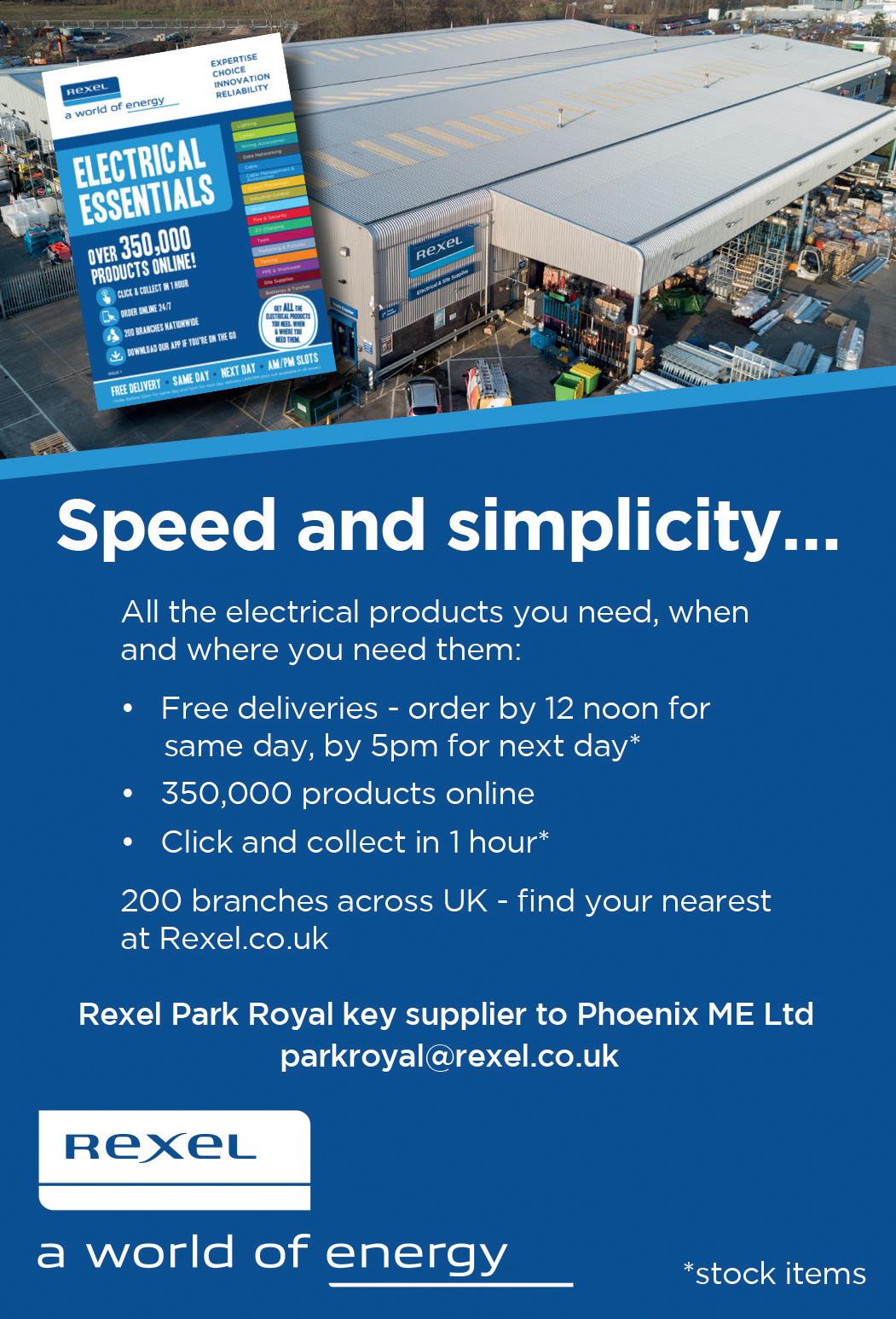
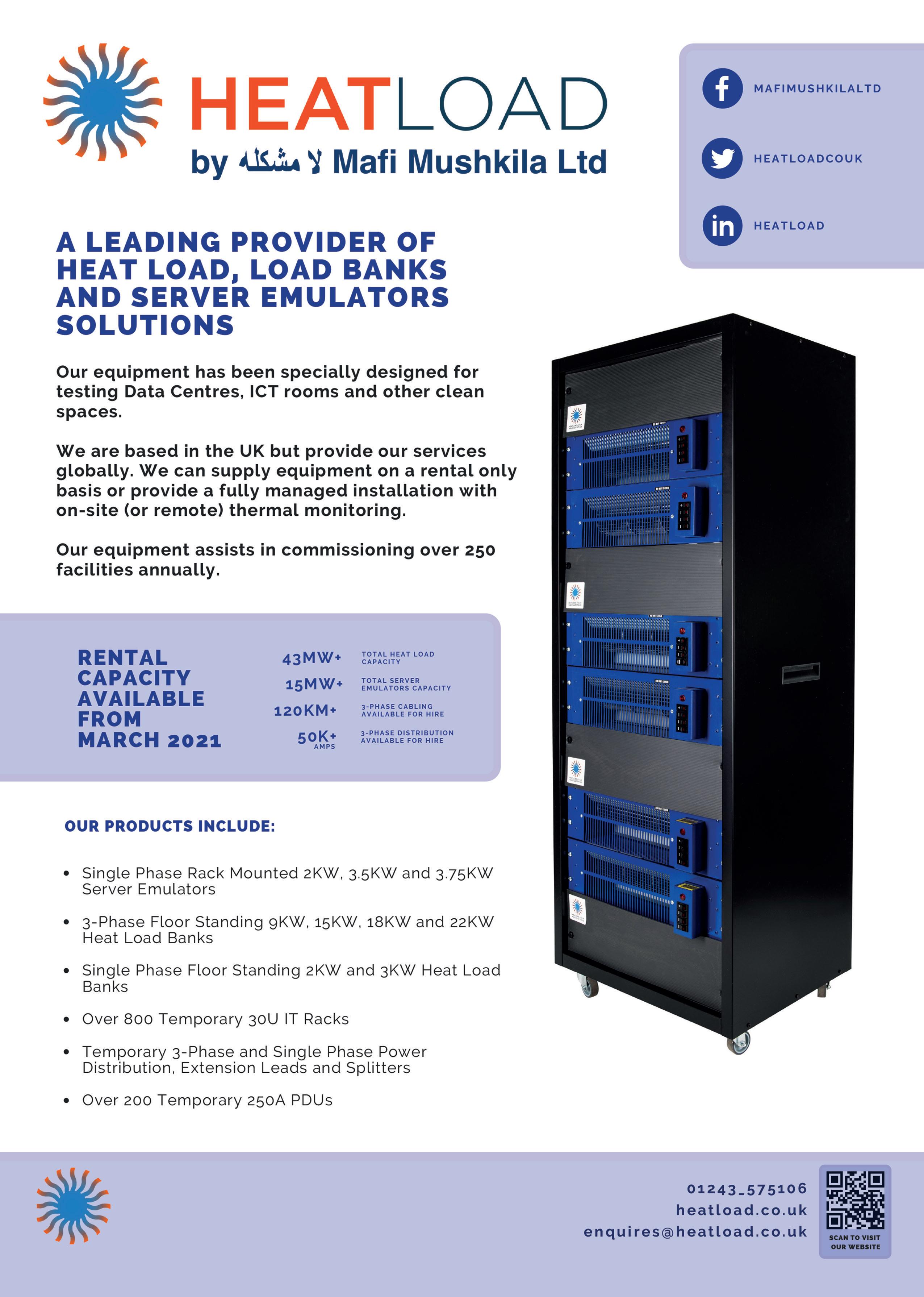
BMSL

BMSL are proud to have partnered with Phoenix ME since 2001 on numerous prestigious projects offering flexibility through either electrical sub-contract packages or the supply of agency labour. Both services are JIB, ECA CHAS and ISO 9001 & 14001 accredited. We look forward to continuing our successful relationship for many years to come.
a big driver for us in the years to come.”
Having come through 2020 extremely well – and growing in the process – Phoenix can now see an ever-more competitive marketplace ahead of it, one which will be influenced by the decisions and moves taken by companies to survive the pandemic. “I think companies have definitely taken a more proactive view of tightening up on costs in order to be more competitive in bidding for work,” Lee confirms. “When it comes to Phoenix, what we have done is
CBL Cable Contractors
CBL Cable Contractors have partnered alongside PME for 25 years on numerous prestigious projects in both the UK and Europe which include Commercial Buildings, Data Centres and Office Blocks. CBL are proud to be a part of their preferred sub-contractor group and look forward to being involved in the future success of PME.
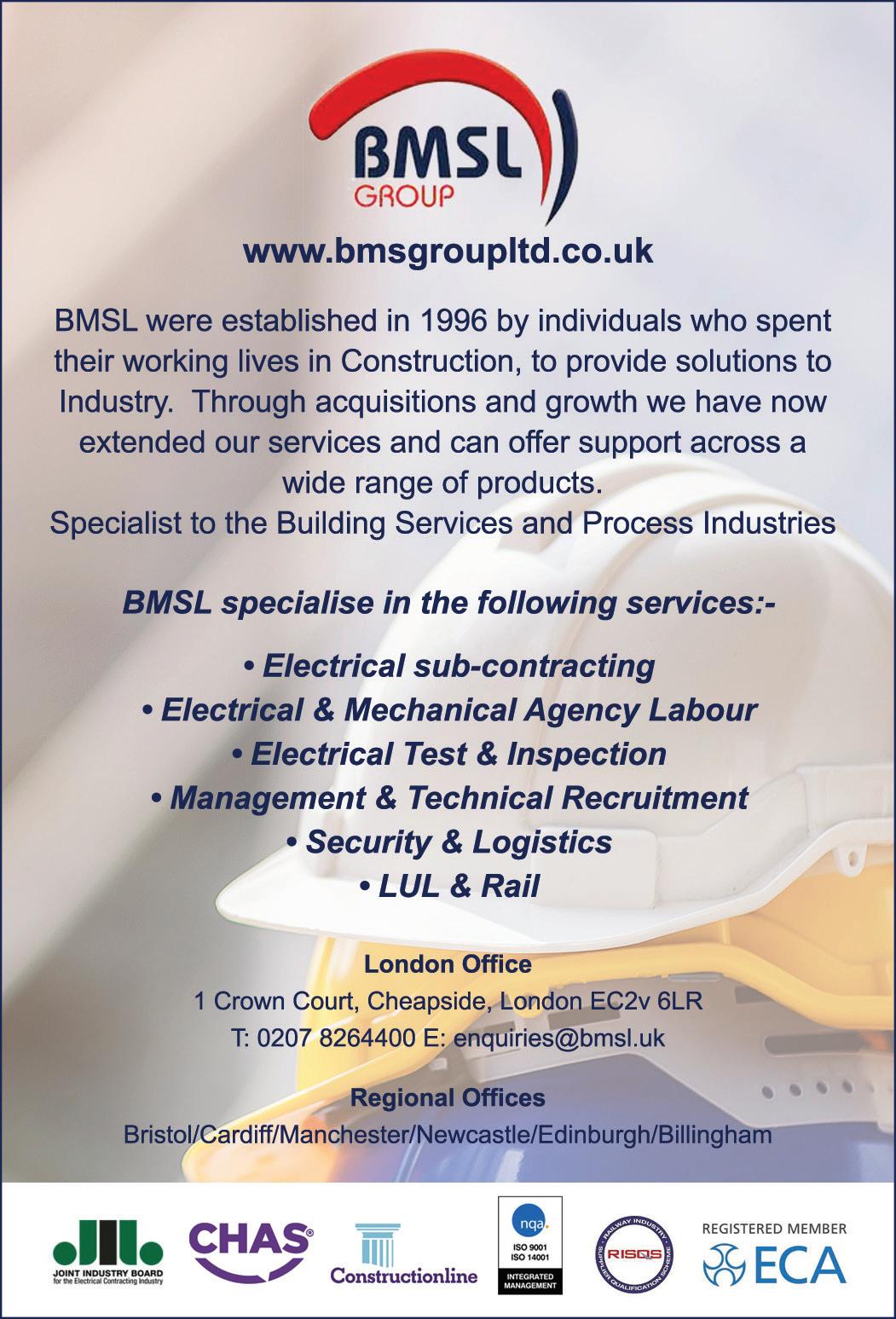

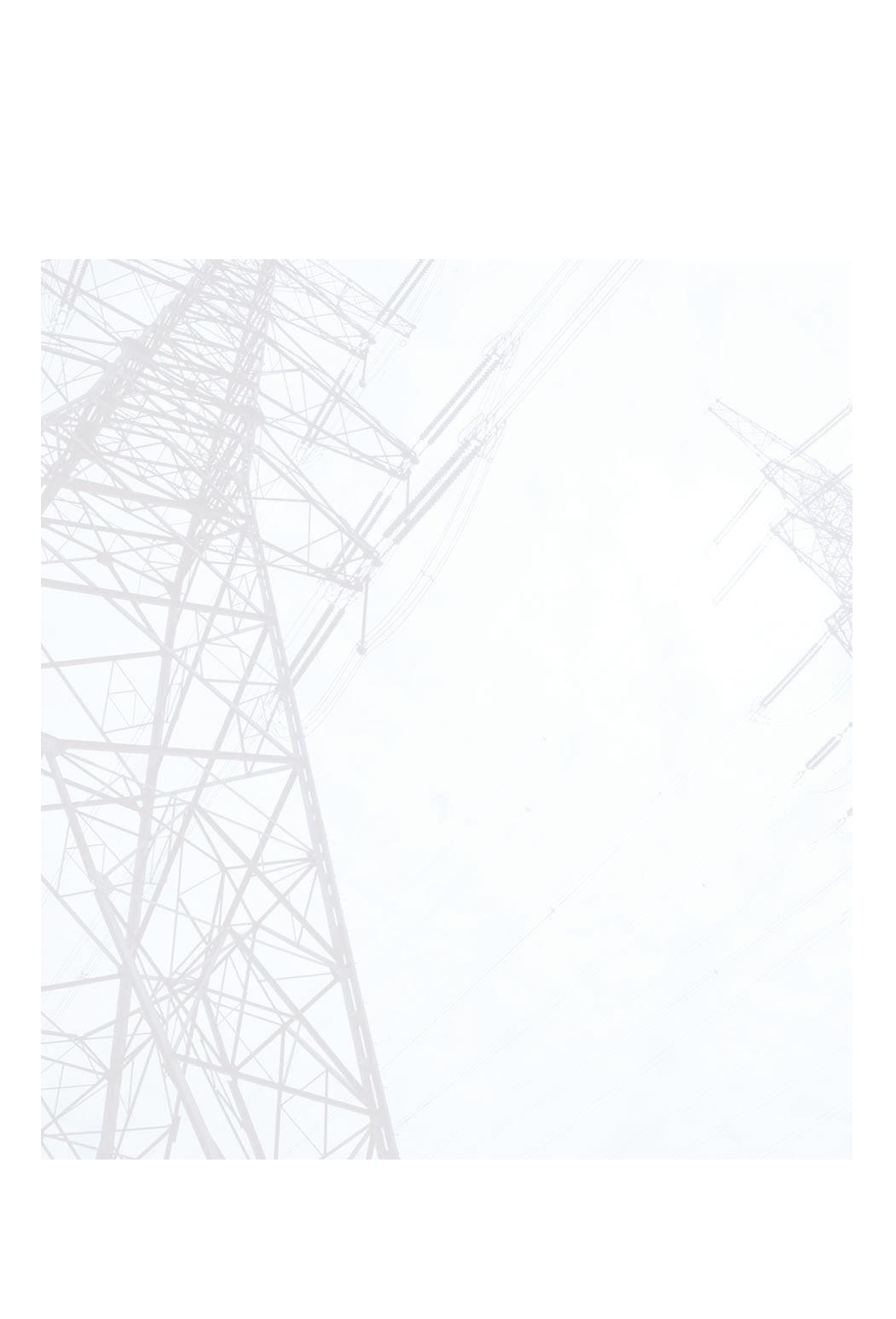
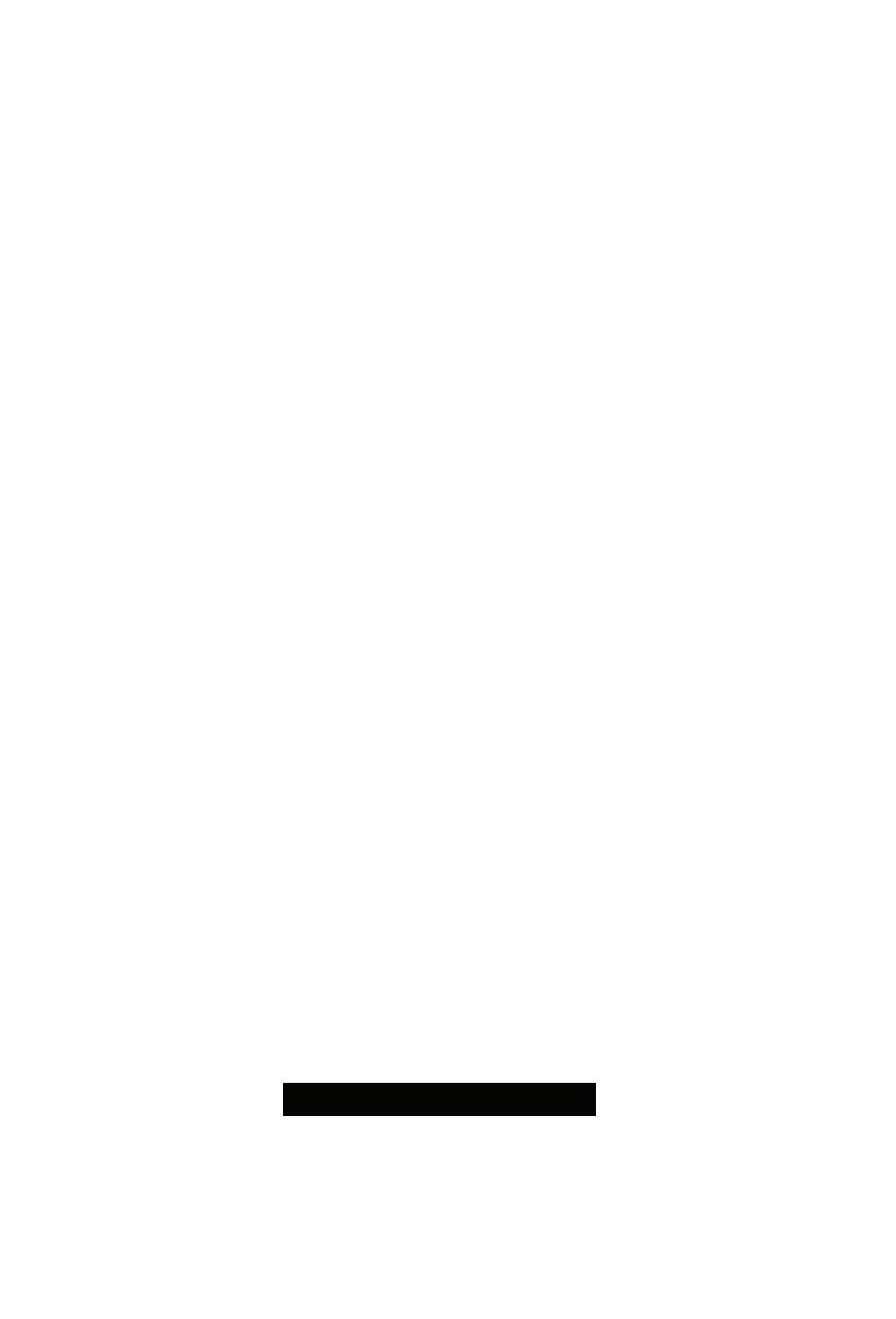
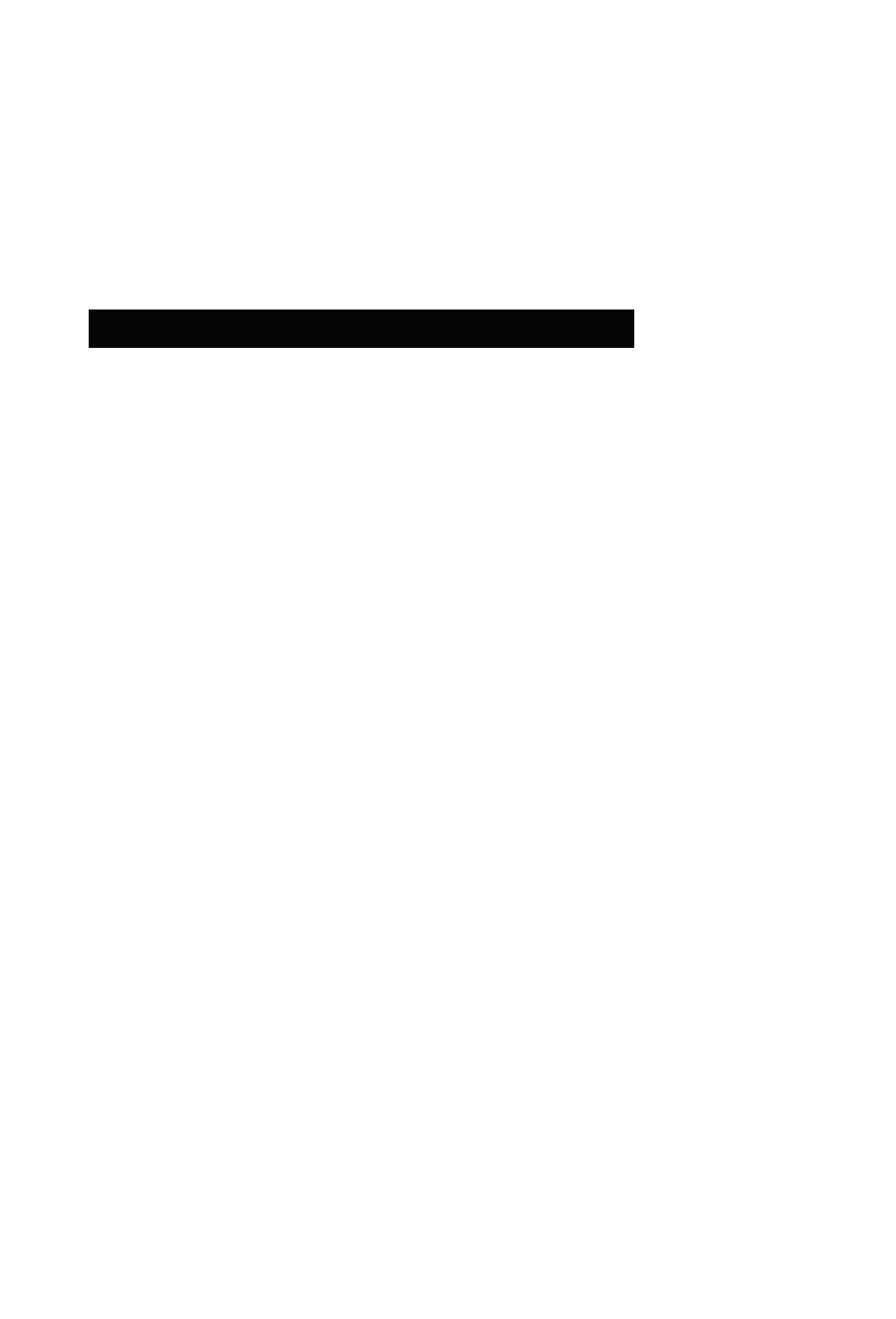
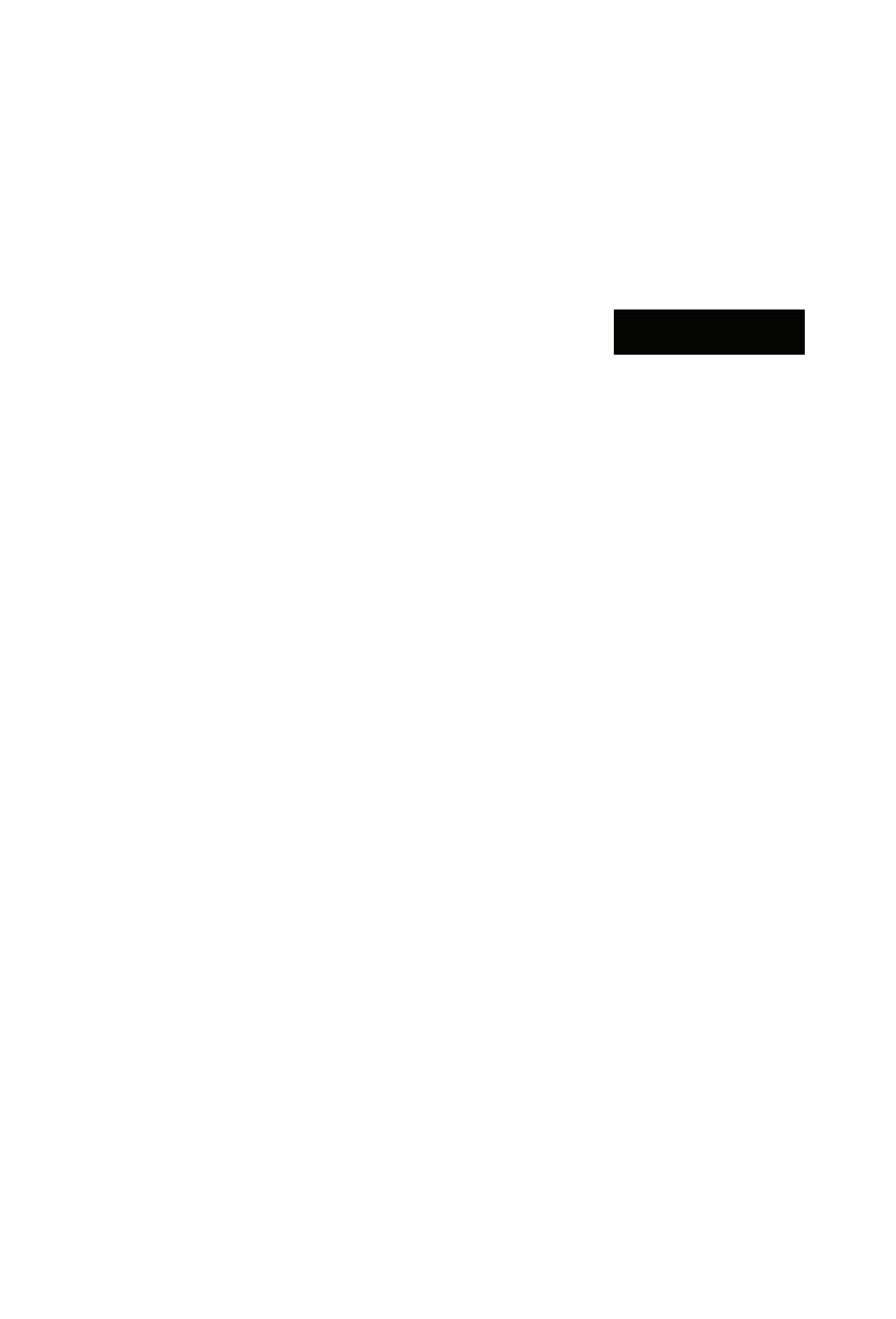
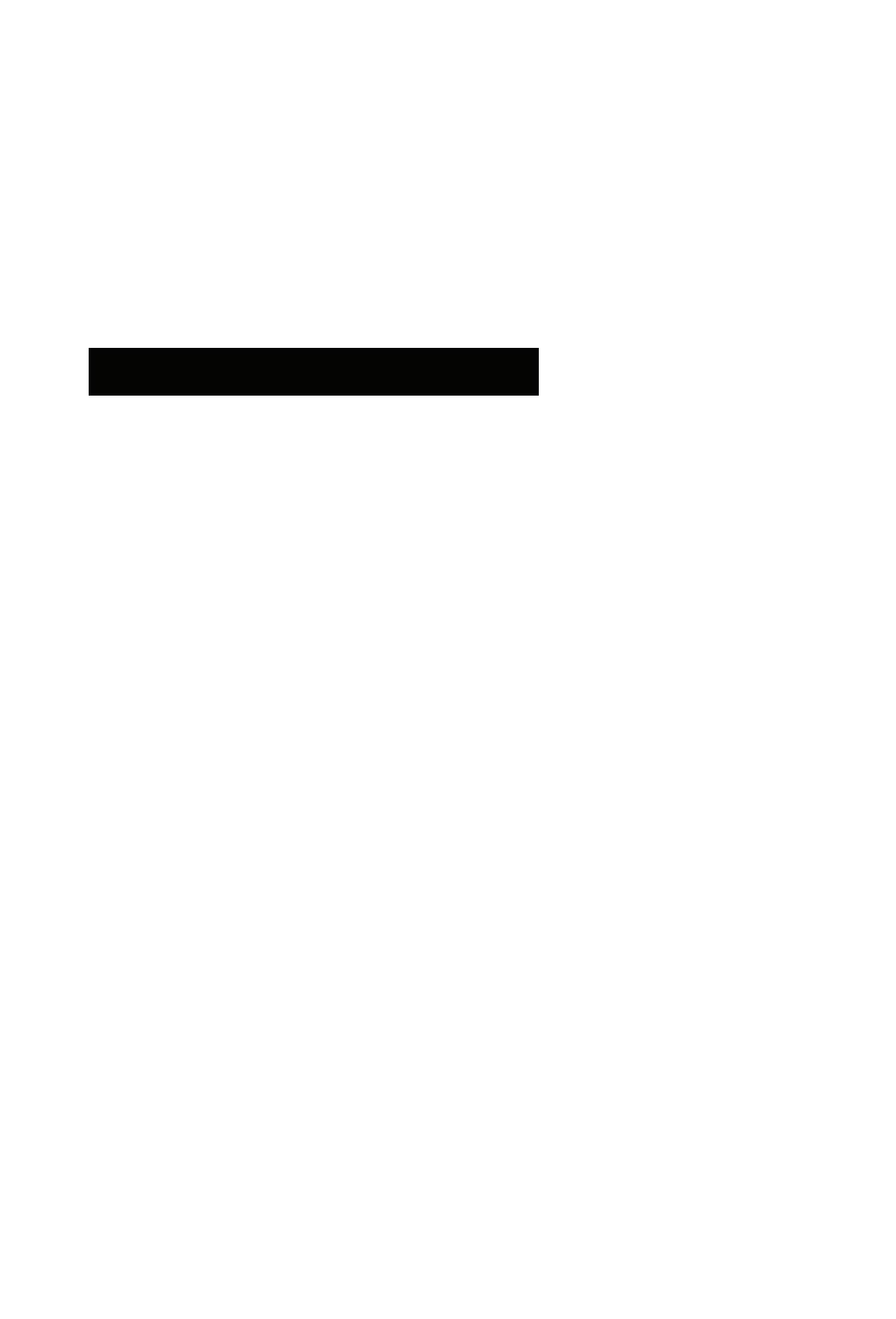
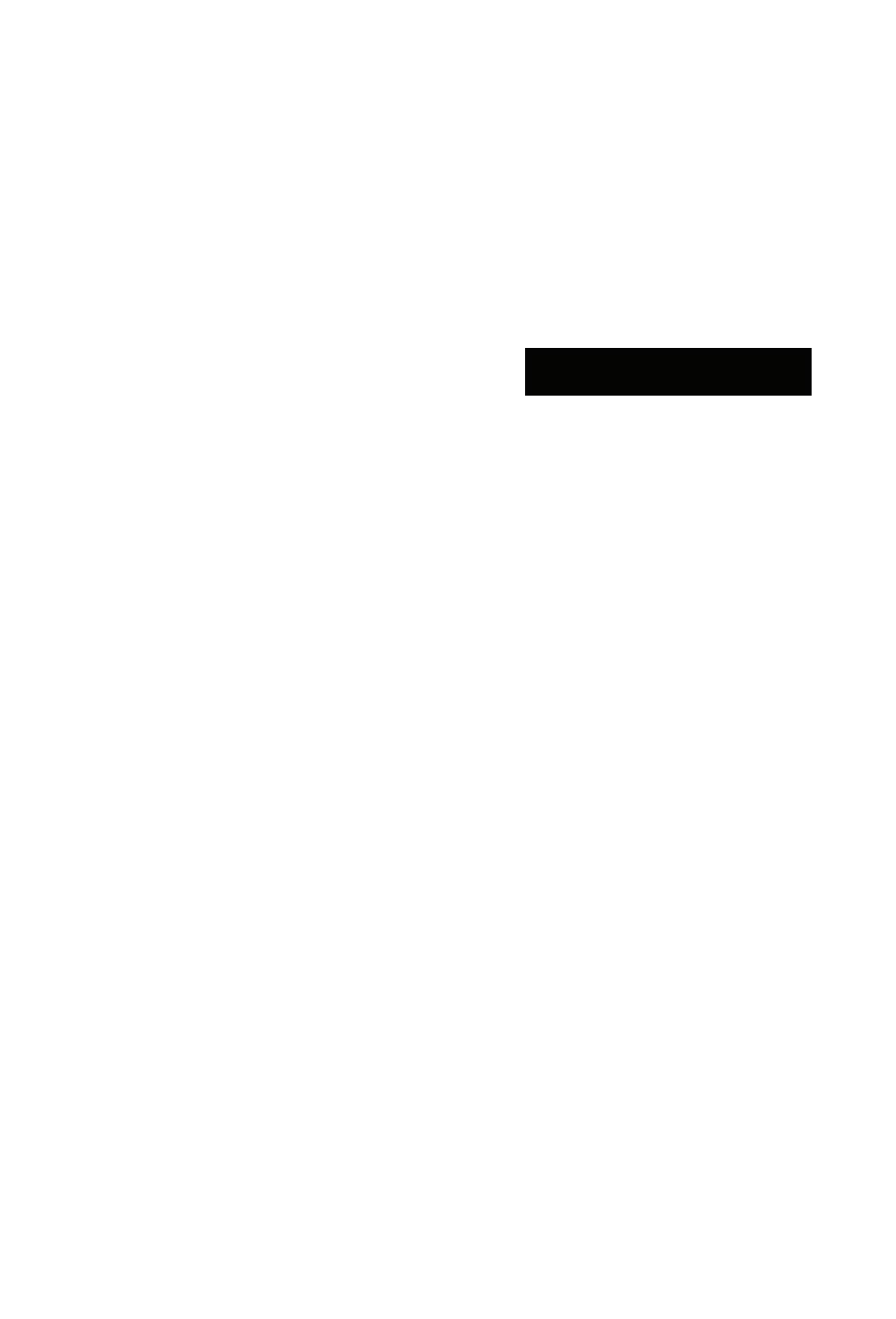
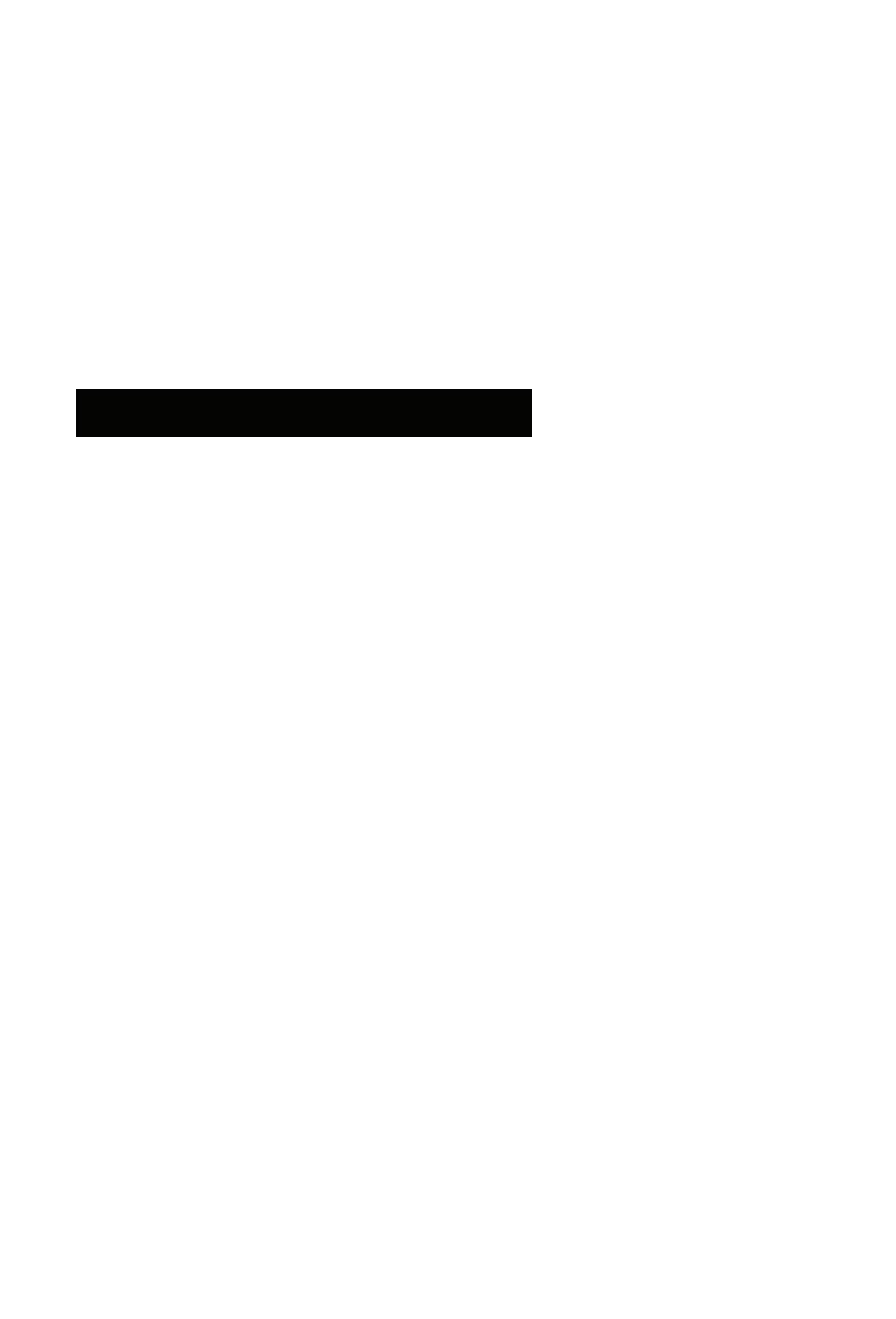
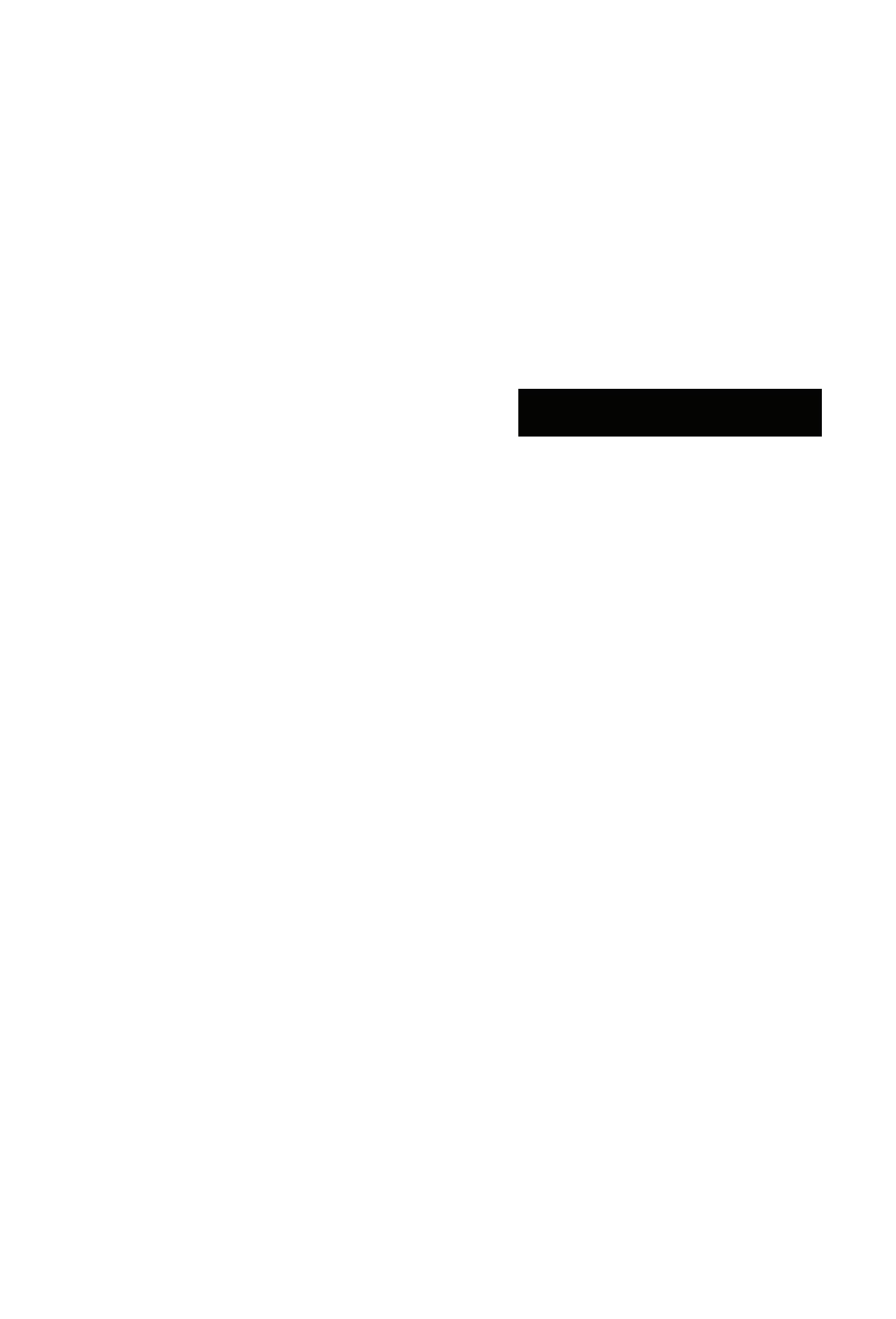
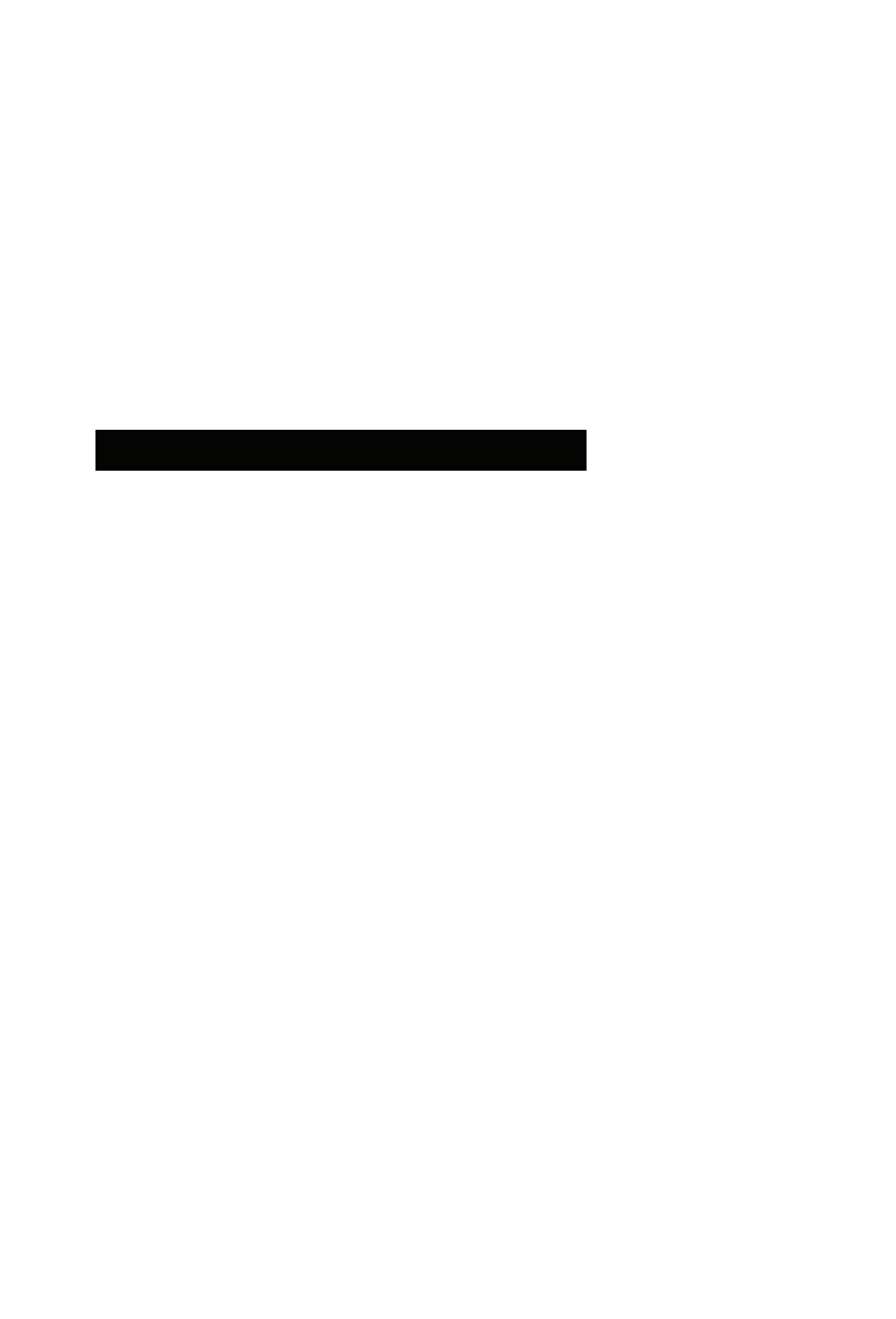
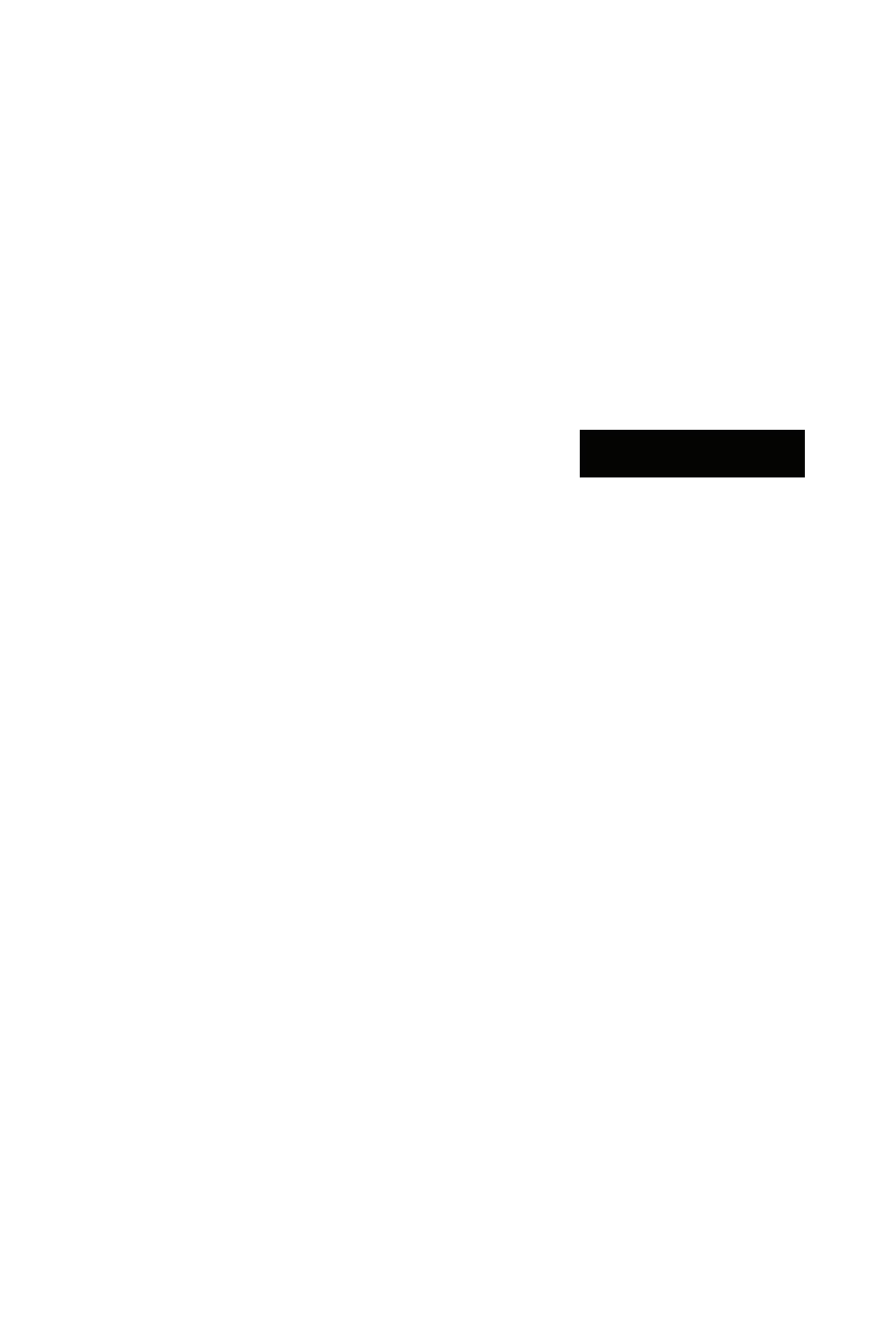
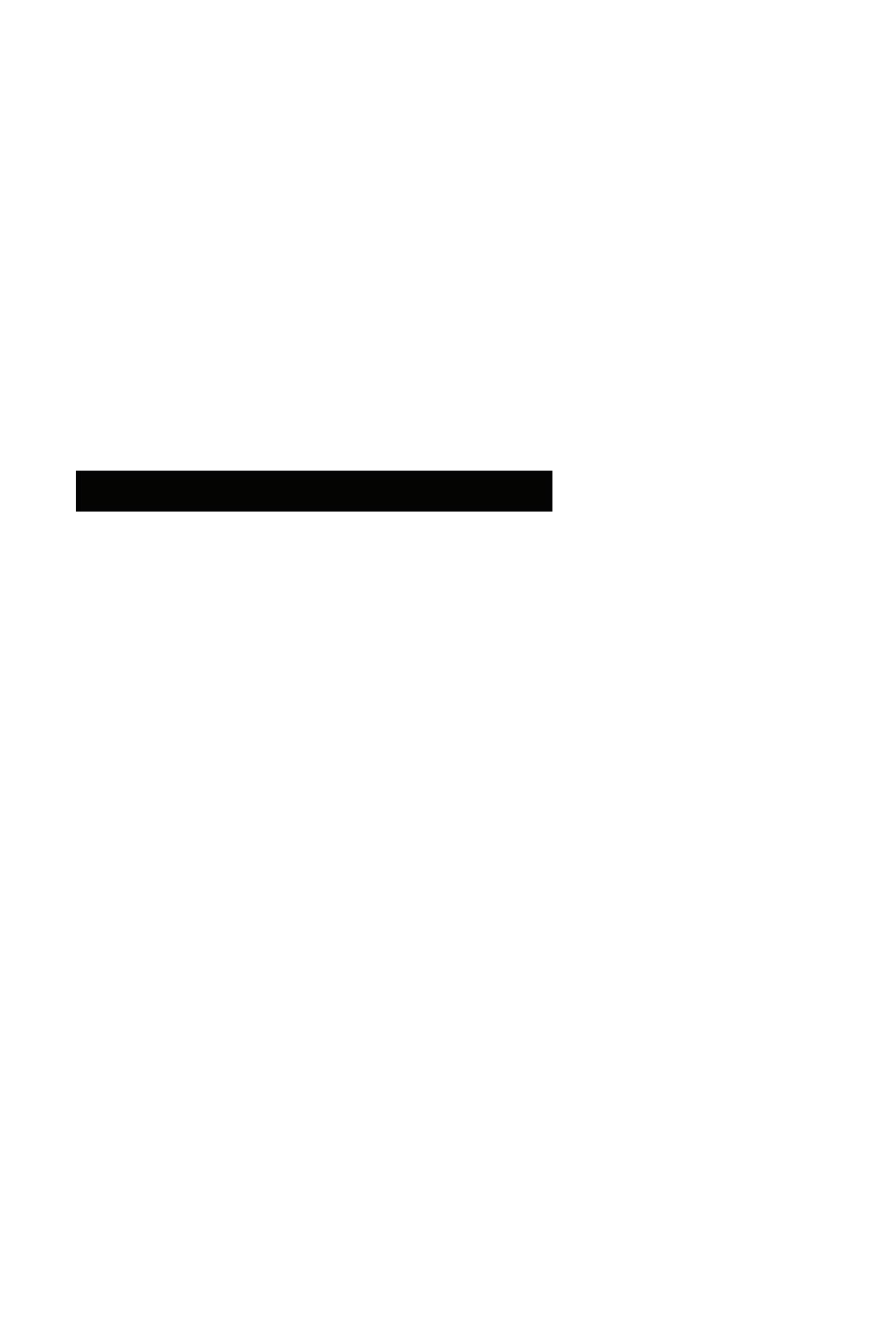
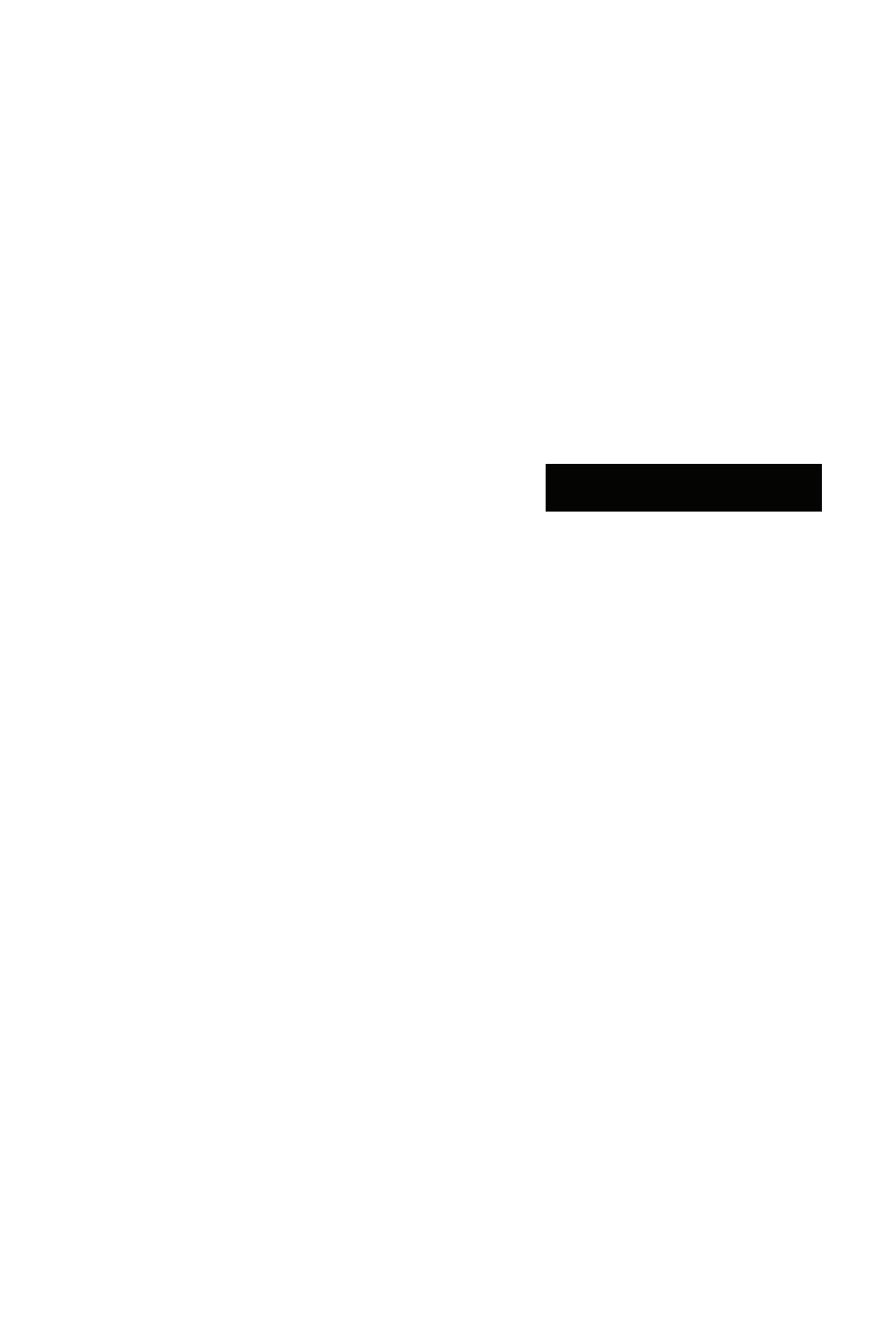
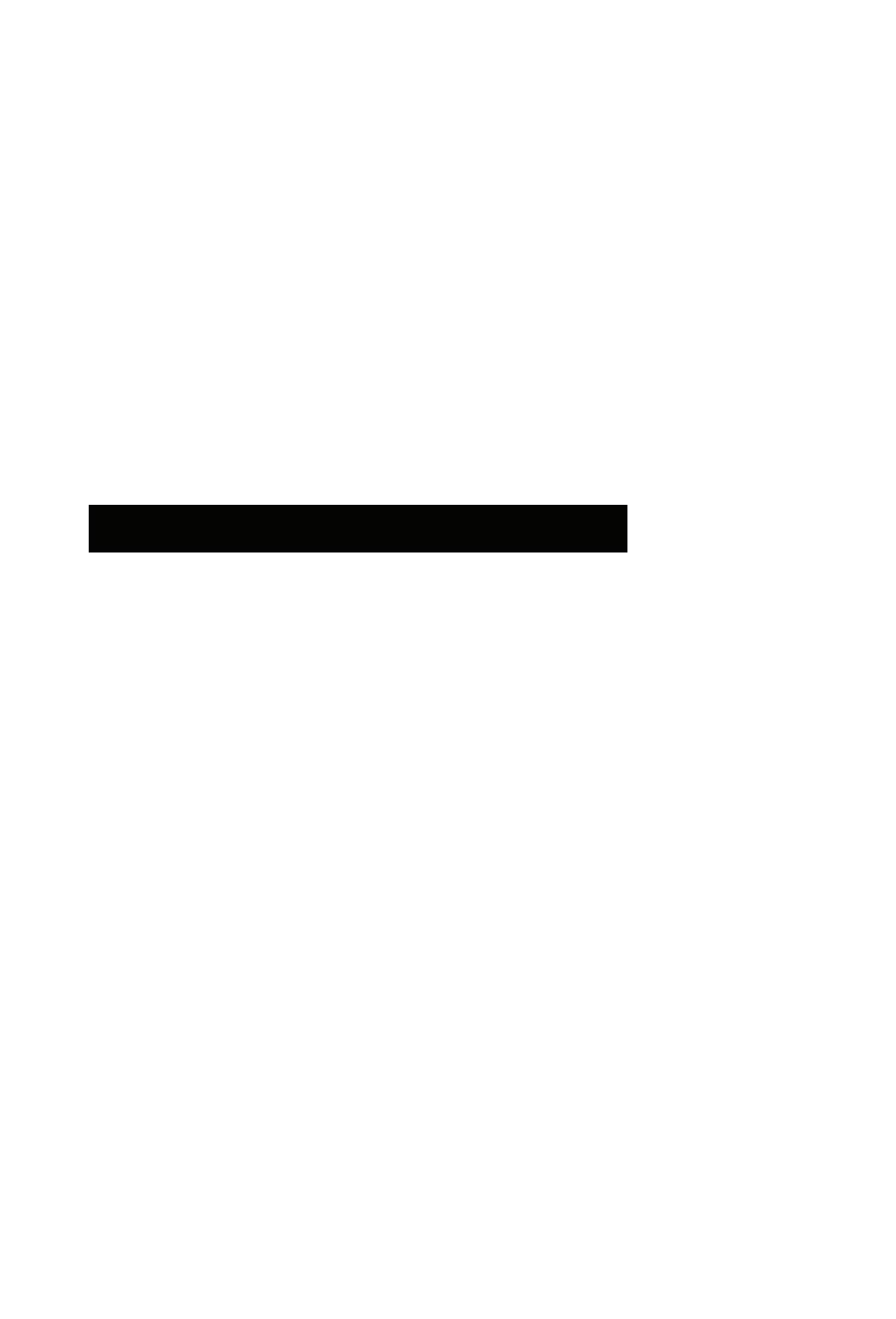
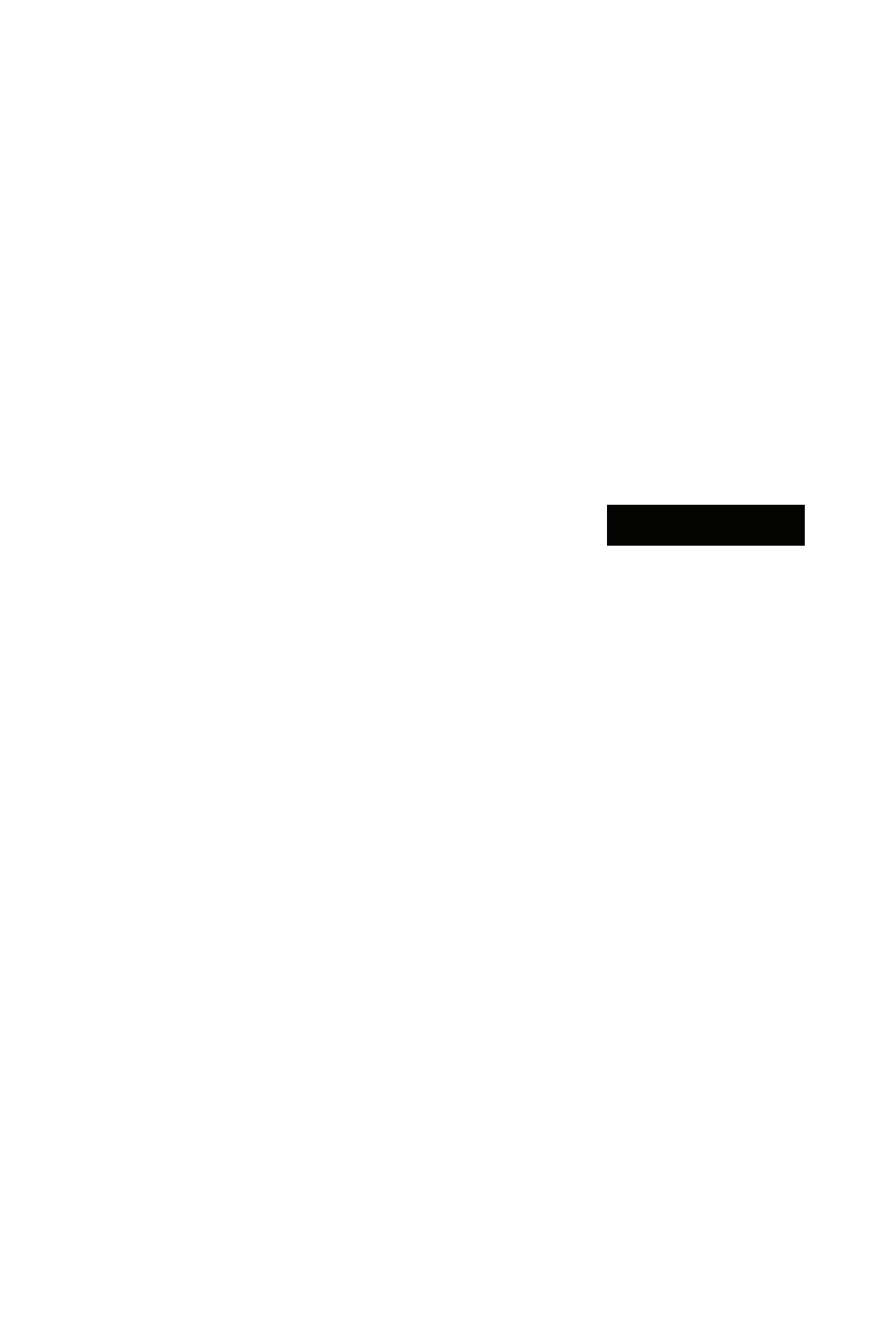
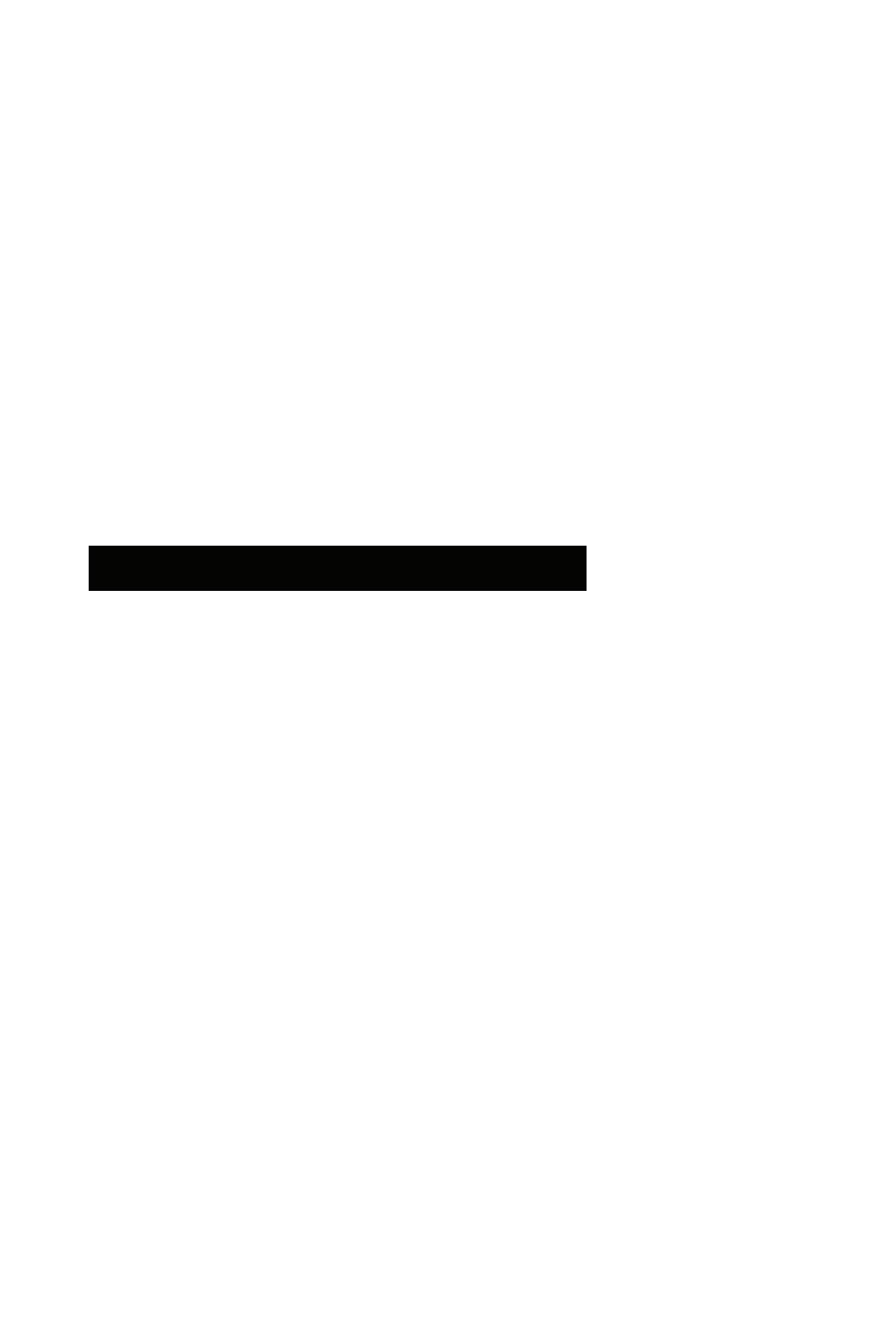
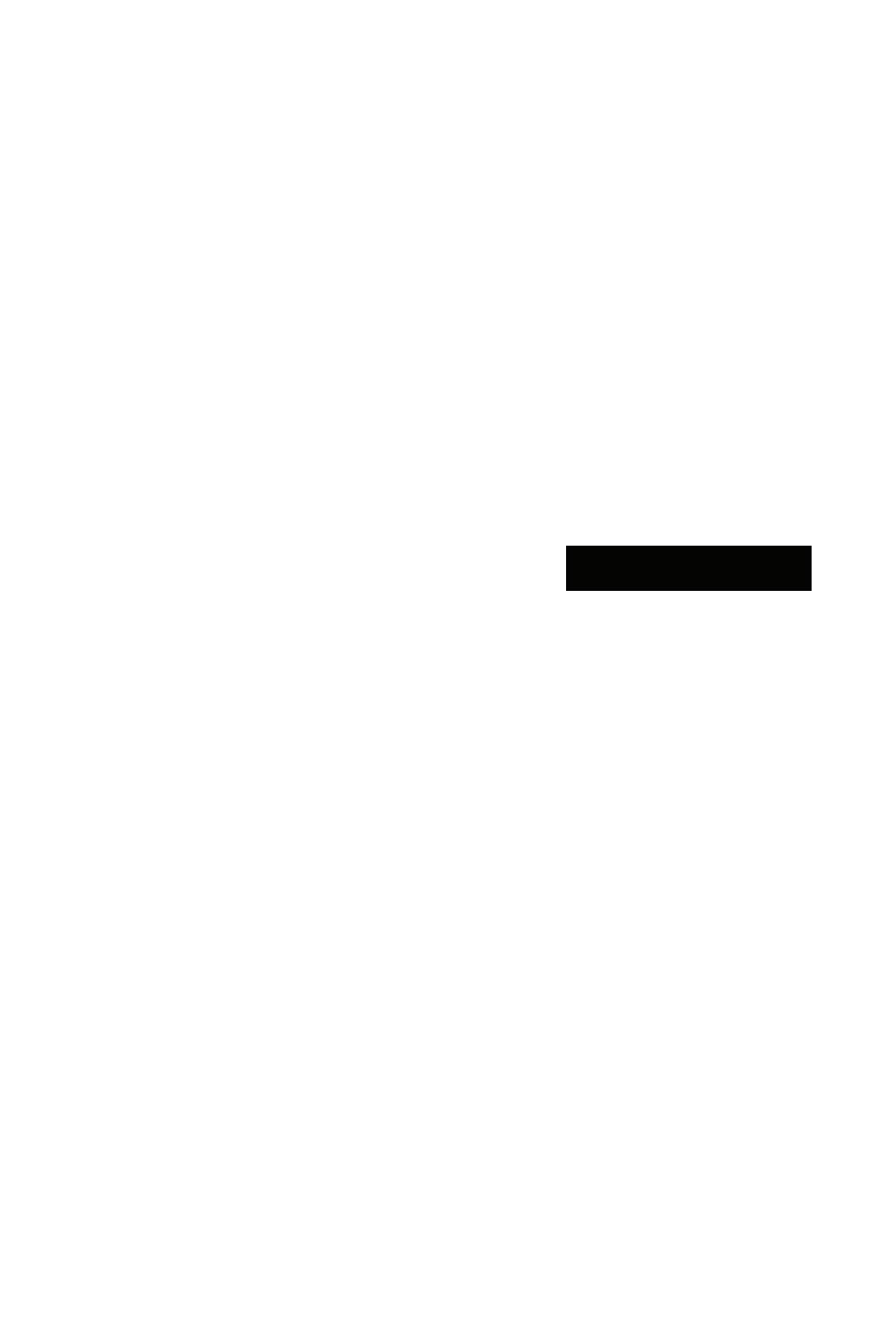
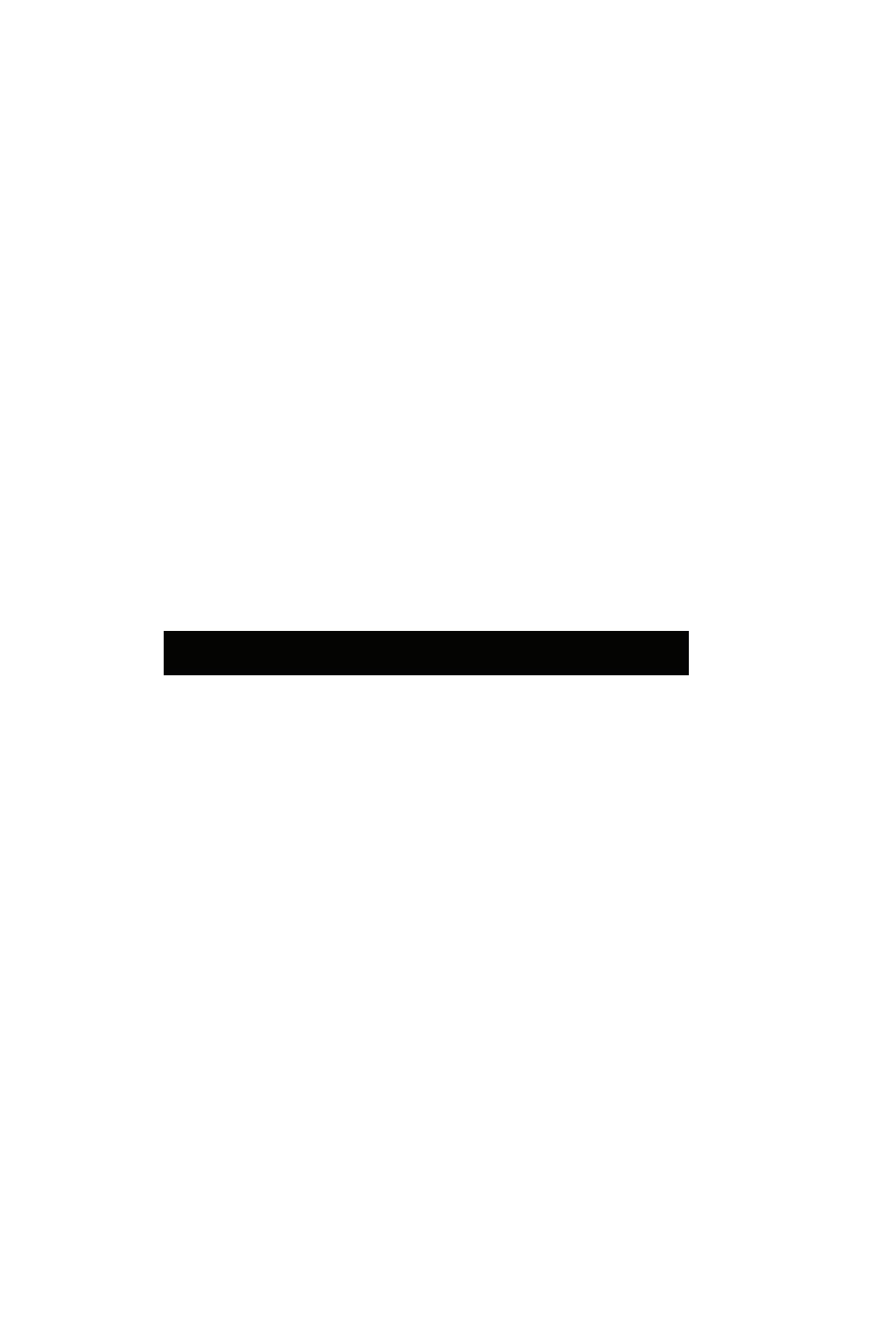
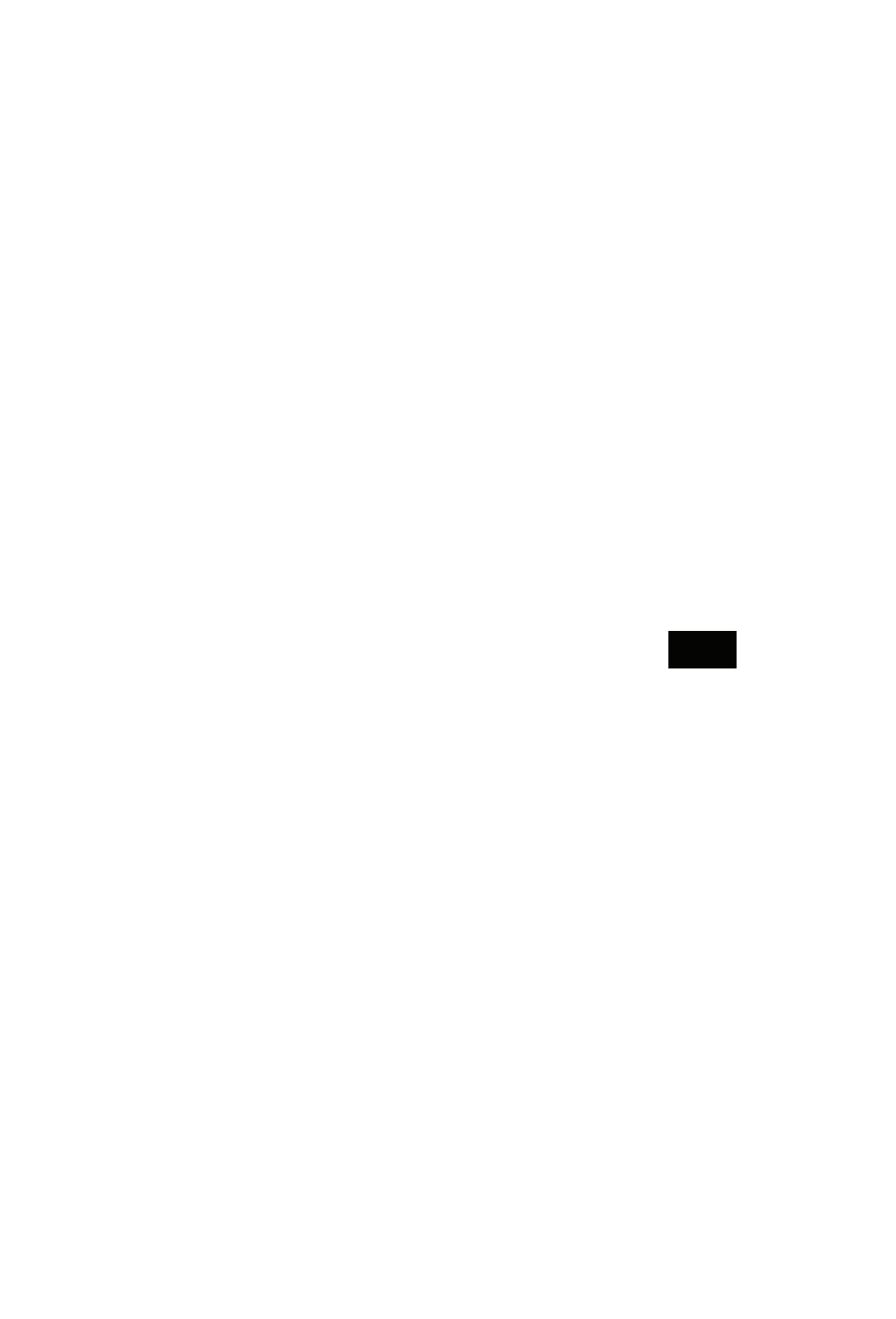
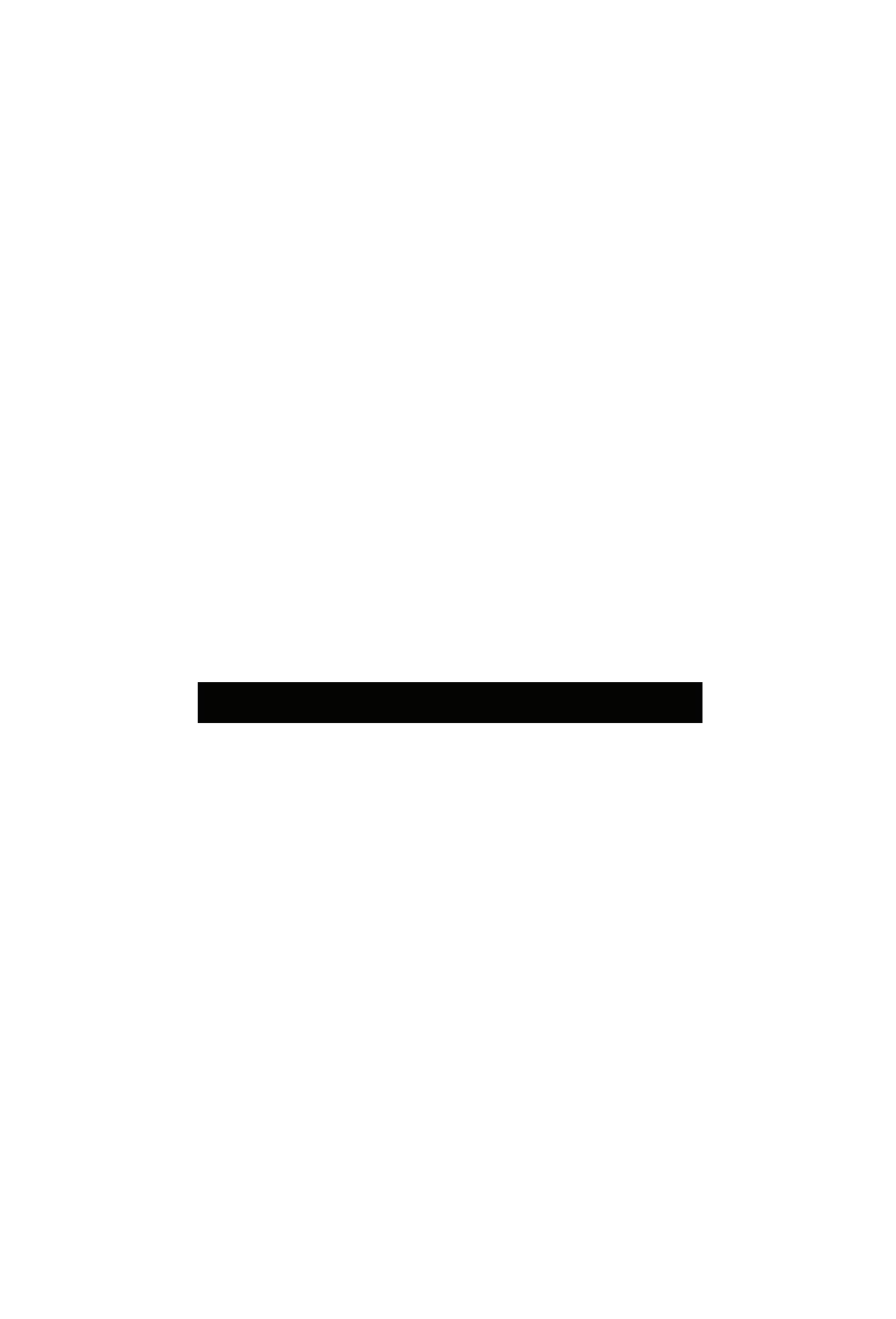
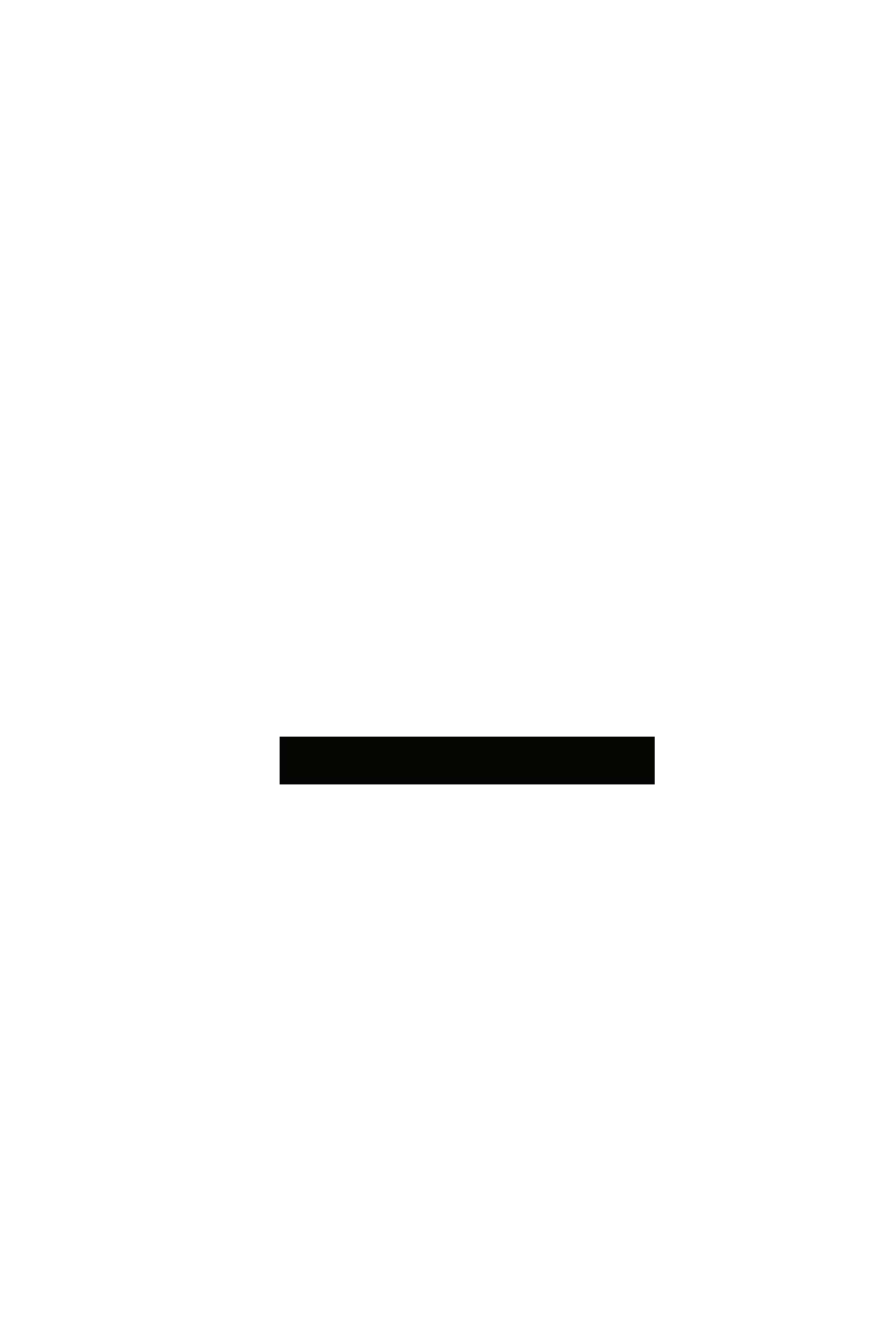
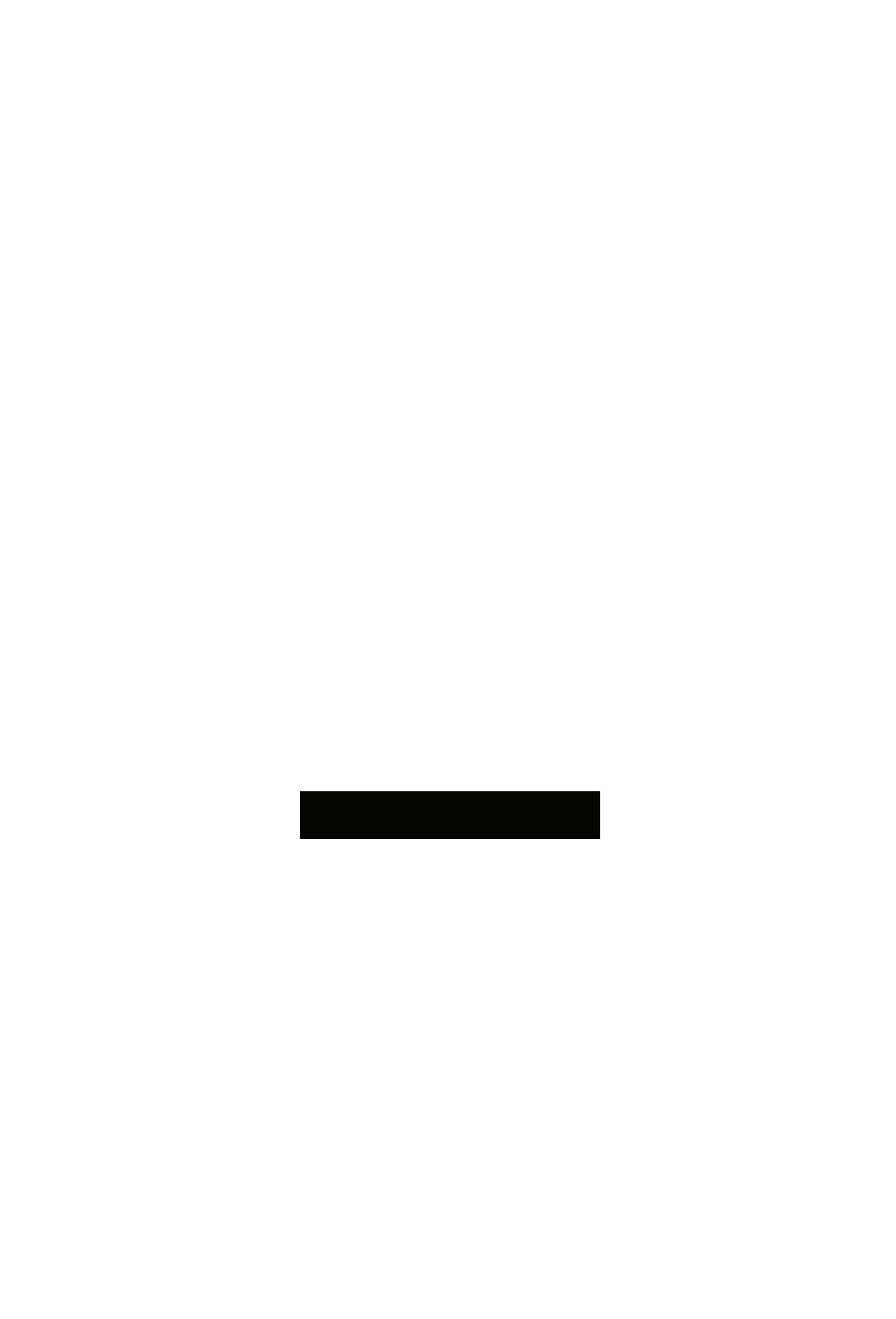
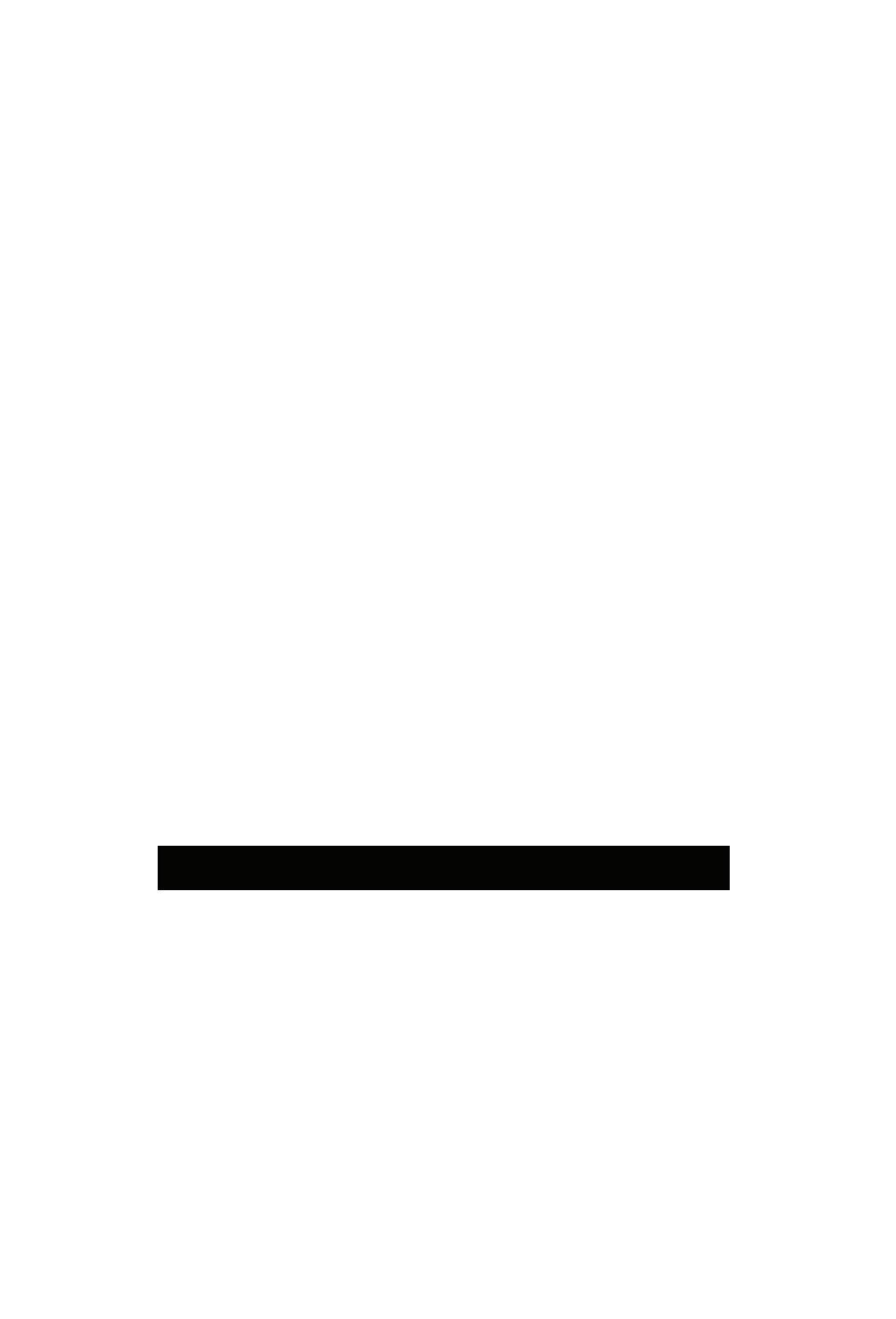
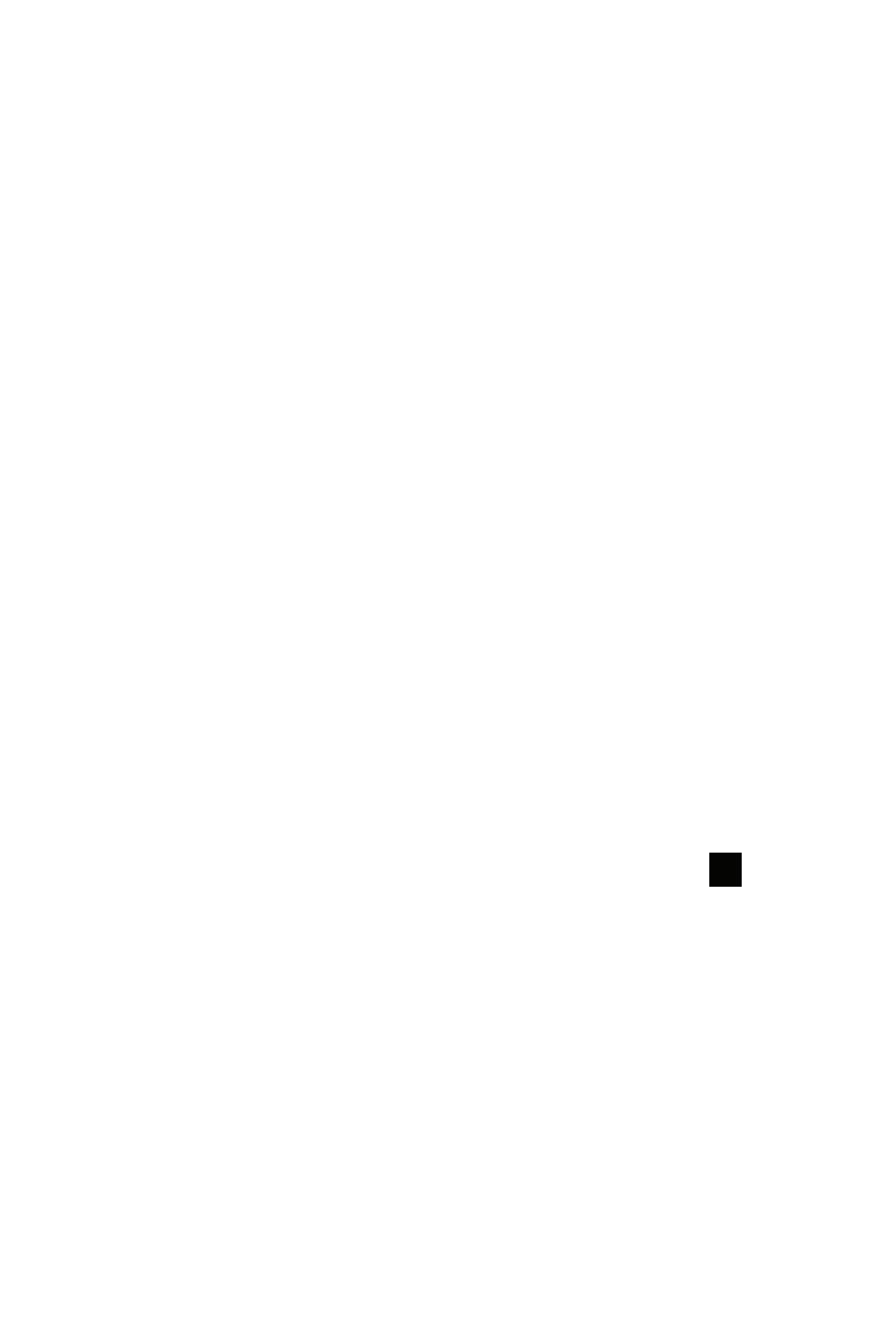
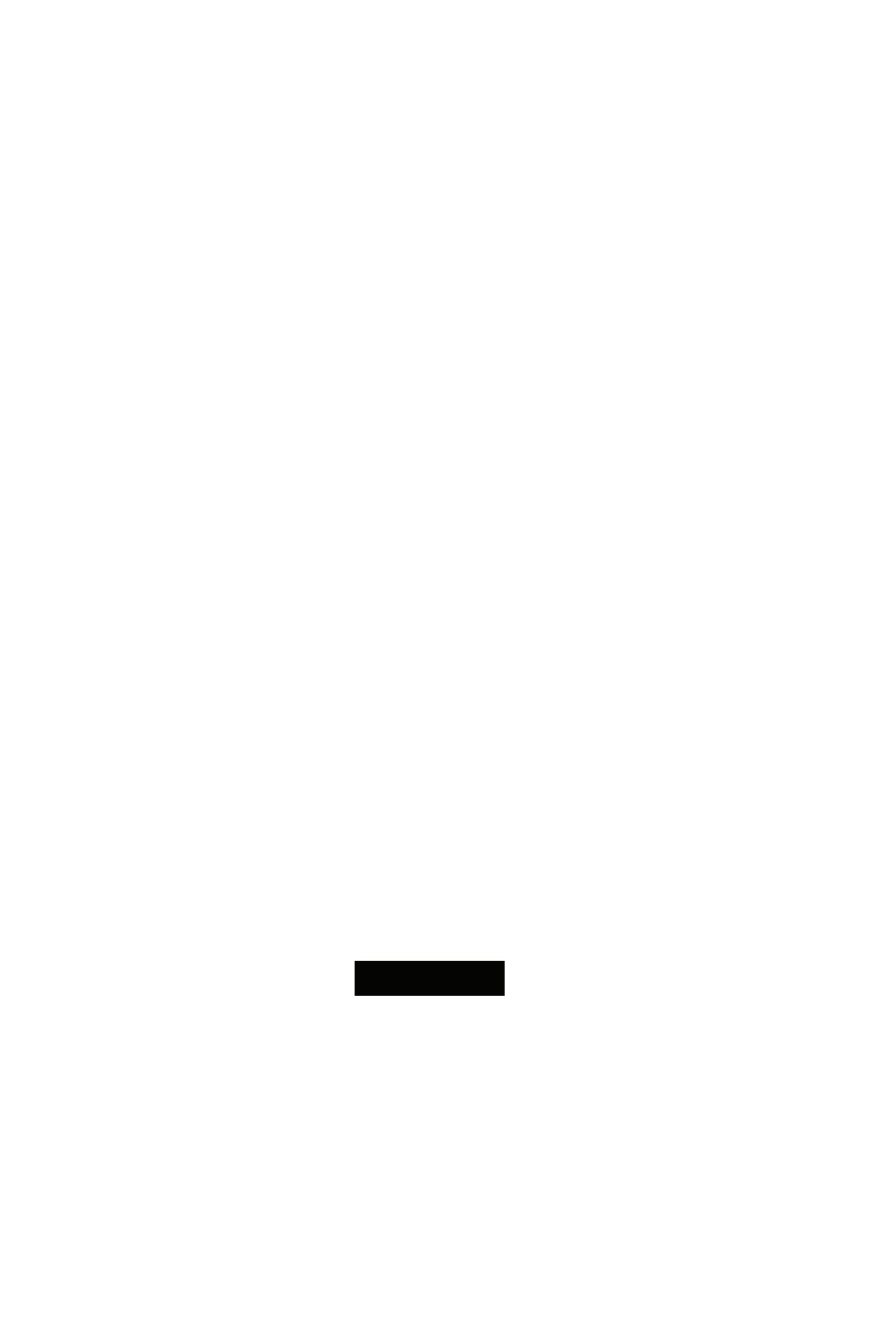
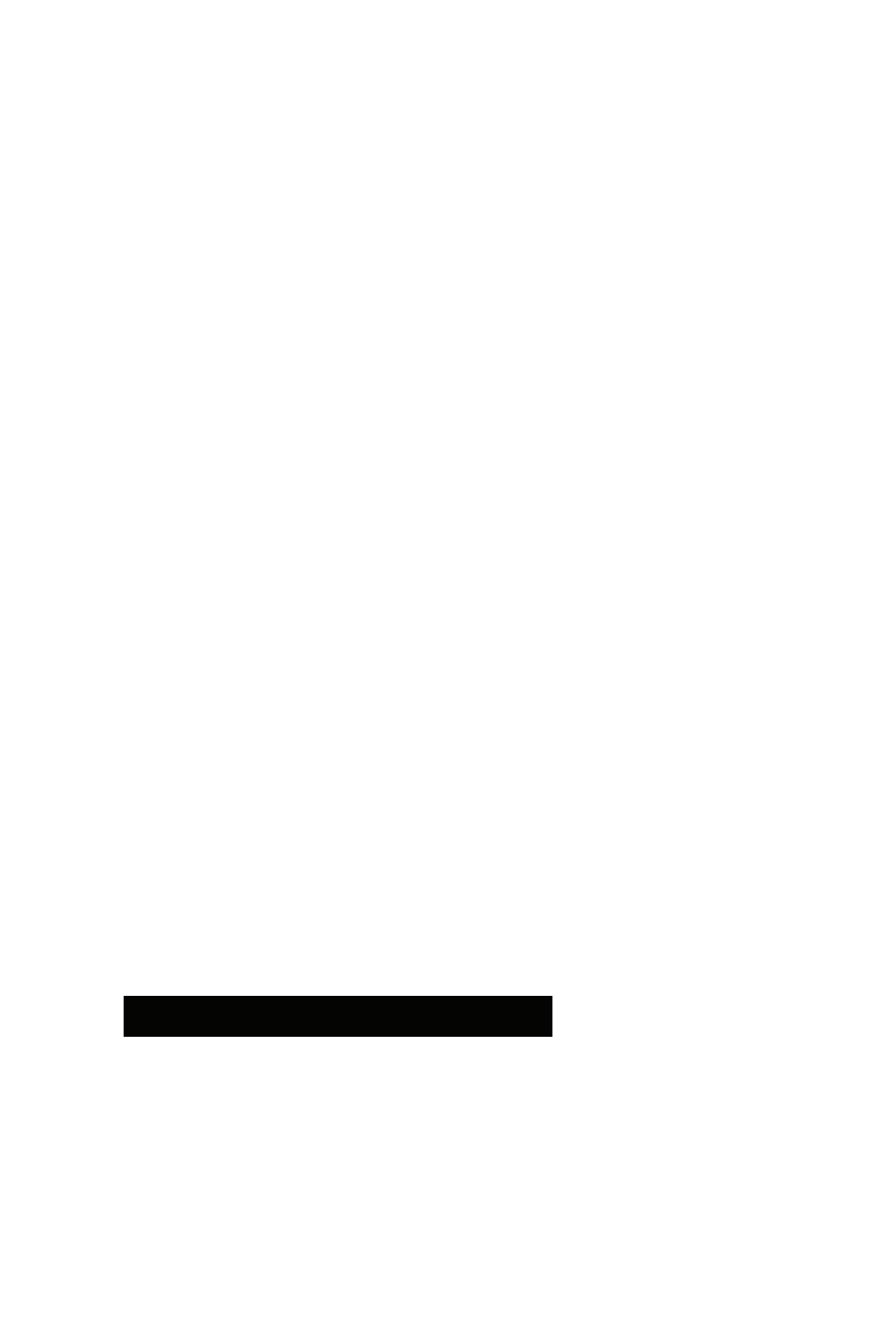
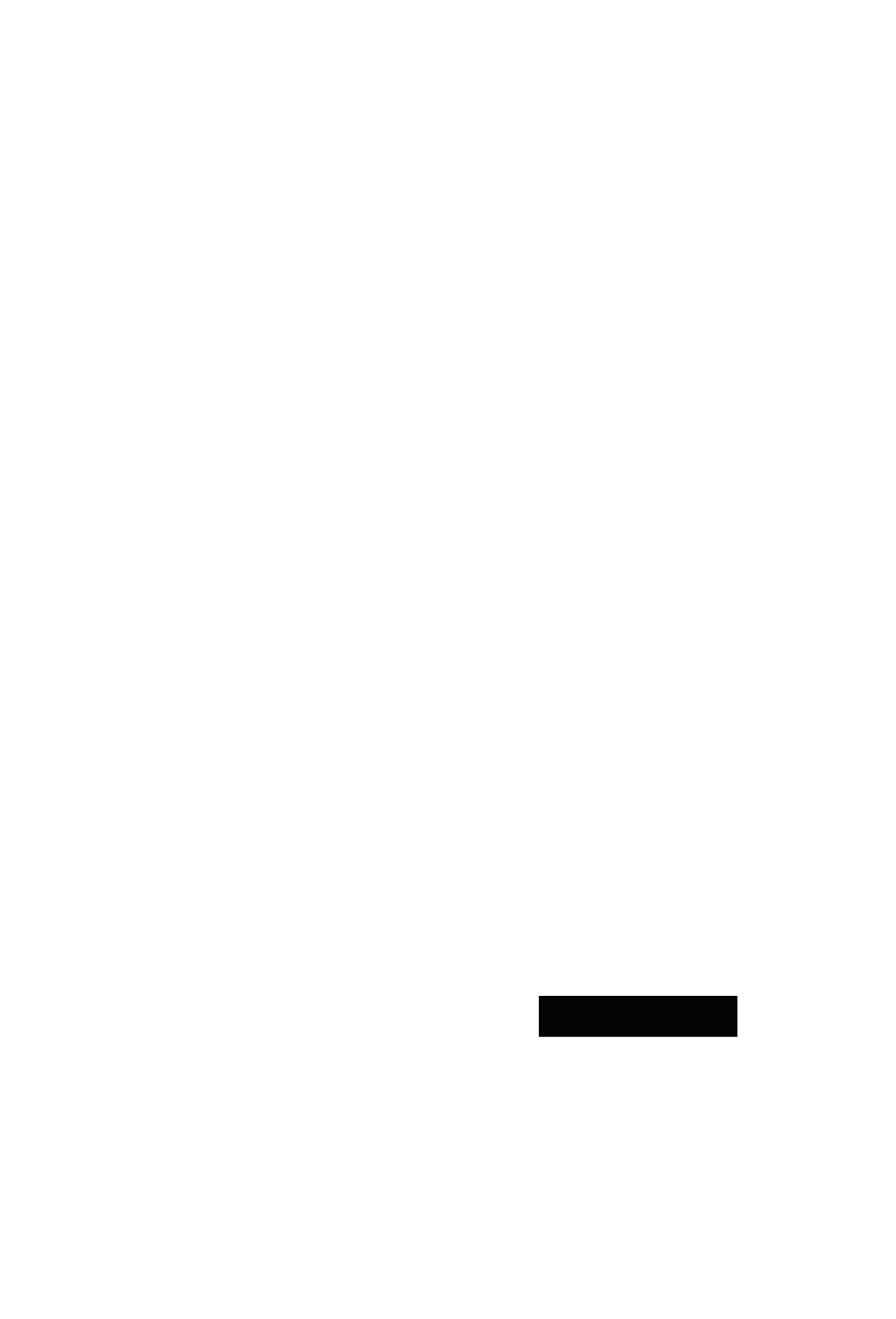
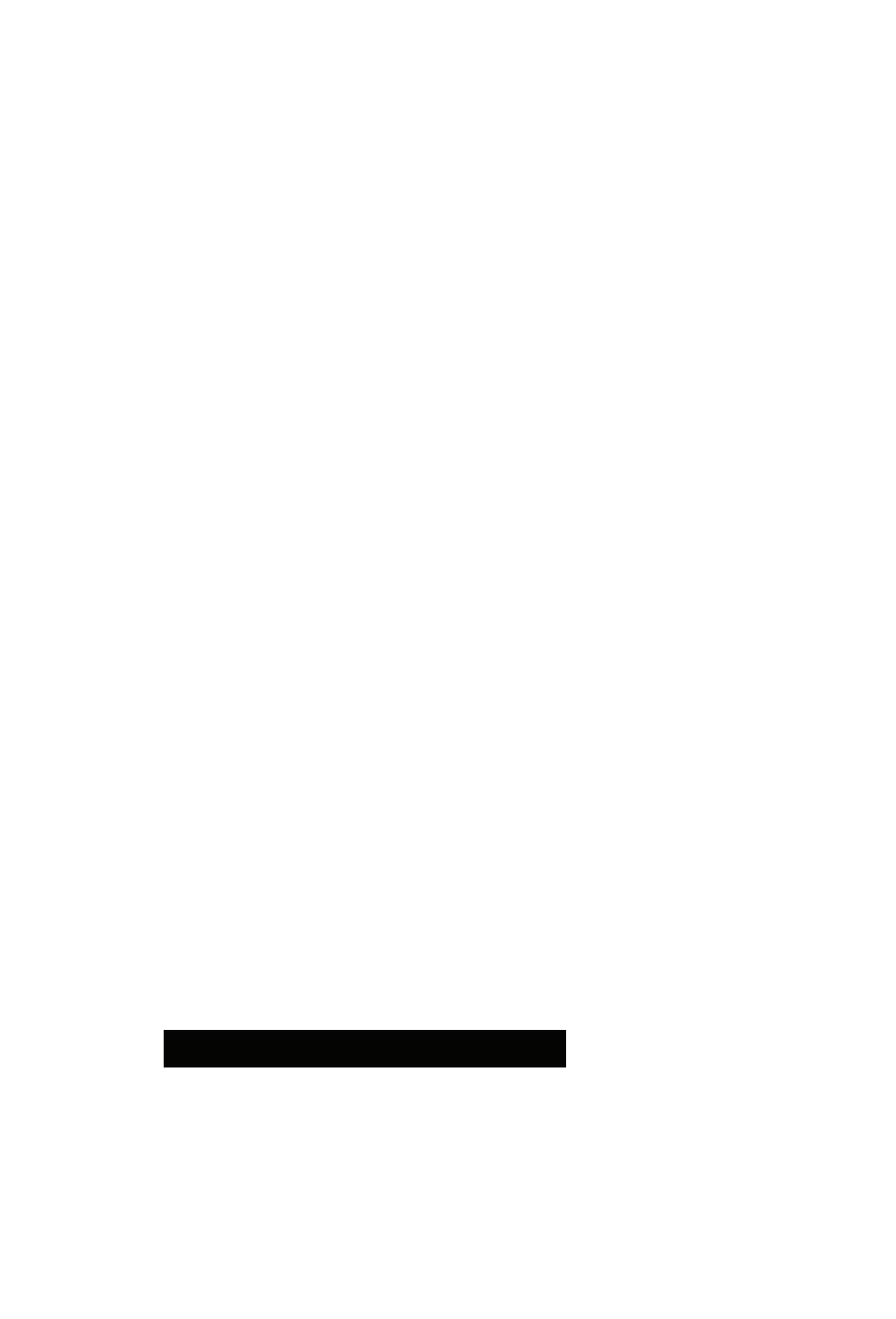
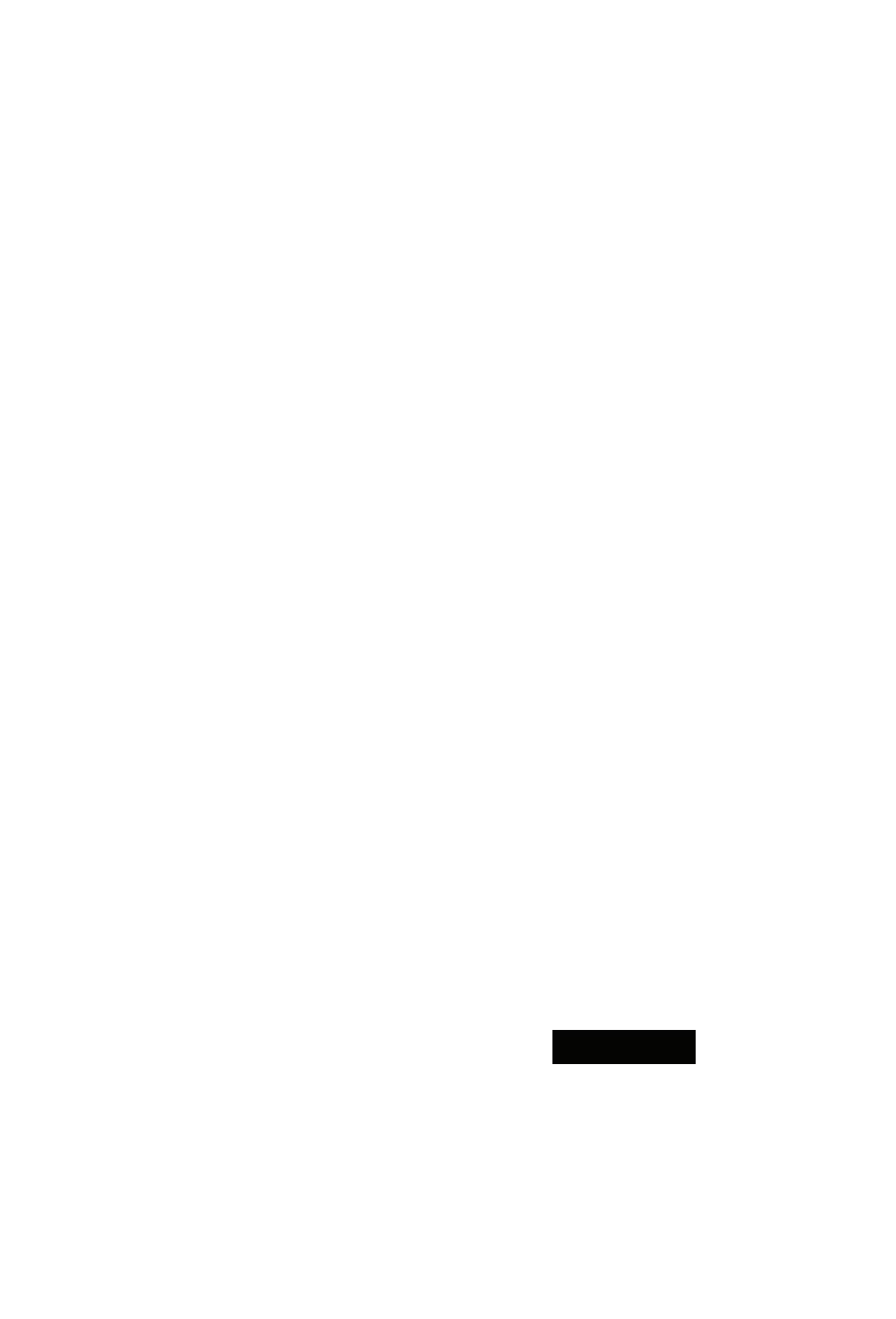
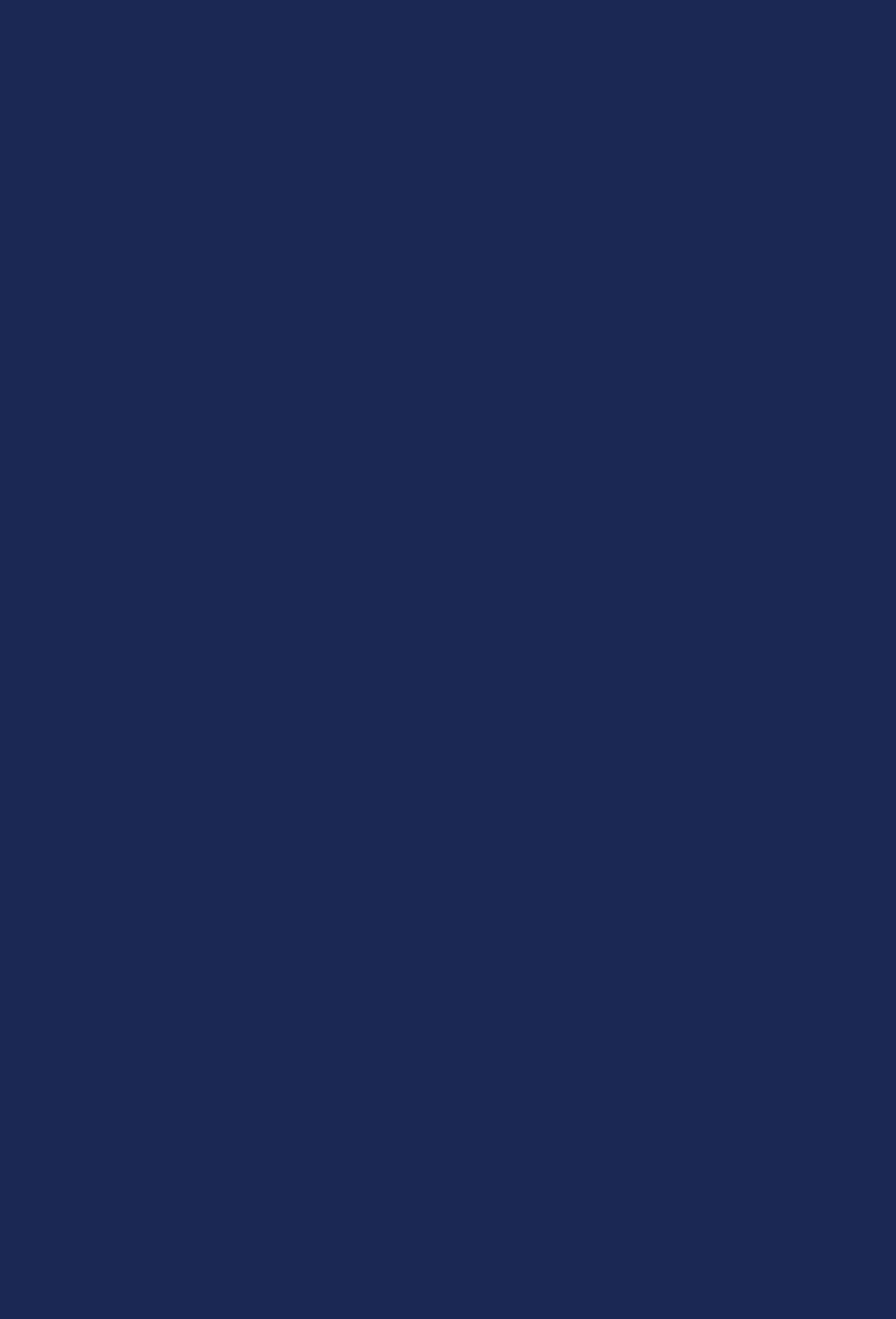
focus in on efficiencies across the business in order to improve on not only our effectiveness on site, but also our own profitability.
“We have always valued the contributions of our people, whose opinions matter hugely to us, and so we have made certain that we have worked closely with them throughout the past year to ensure that they are happy with the conditions under which they work. We look after them to the best level possible, so whatever efficiencies or changes we make
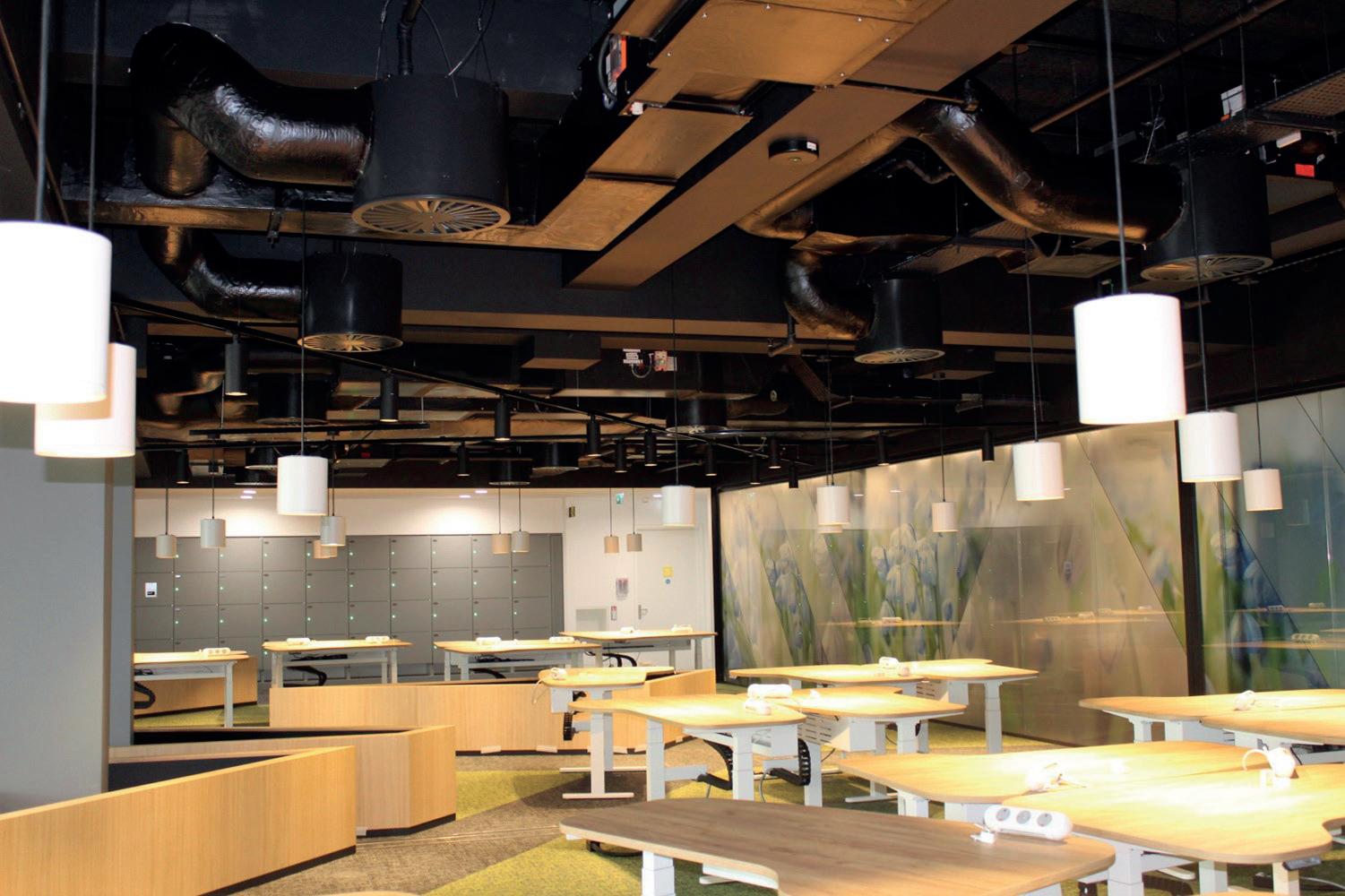
Denflow Ltd
Our Relationship with Phoenix ME Ltd started around ten years ago; in that time, we have built a tremendous working relationship, built on trust and workmanship that has delivered some great projects. We at Denflow Ltd feel we are a company that doesn’t need to be micro managed by our client, something Phoenix ME Ltd find appealing. Phoenix are a large company with a family atmosphere, something not seen often in today’s market. All Directors are very approachable and easy to deal with should any issues arise, and we move into 2021 with knowledge that we have a solid relationship based on trust.
to the way we operate are done so with their wellbeing at their very core.”
As Lee goes on to conclude, those same employees should also soon see additional faces joining their ranks, as the company ramps up its efforts as more of the economy emerges from the pandemic. “We are actually in the process of recruiting staff as we speak. We have been on a bit of a drive to identify new talent that we can bring into the business in recent months, and we look forward to welcoming these men and women into what is a growing family here at Phoenix.”
Phoenix ME Ltd www.phoenixme.co.uk Products:
Mechanical and electrical systems
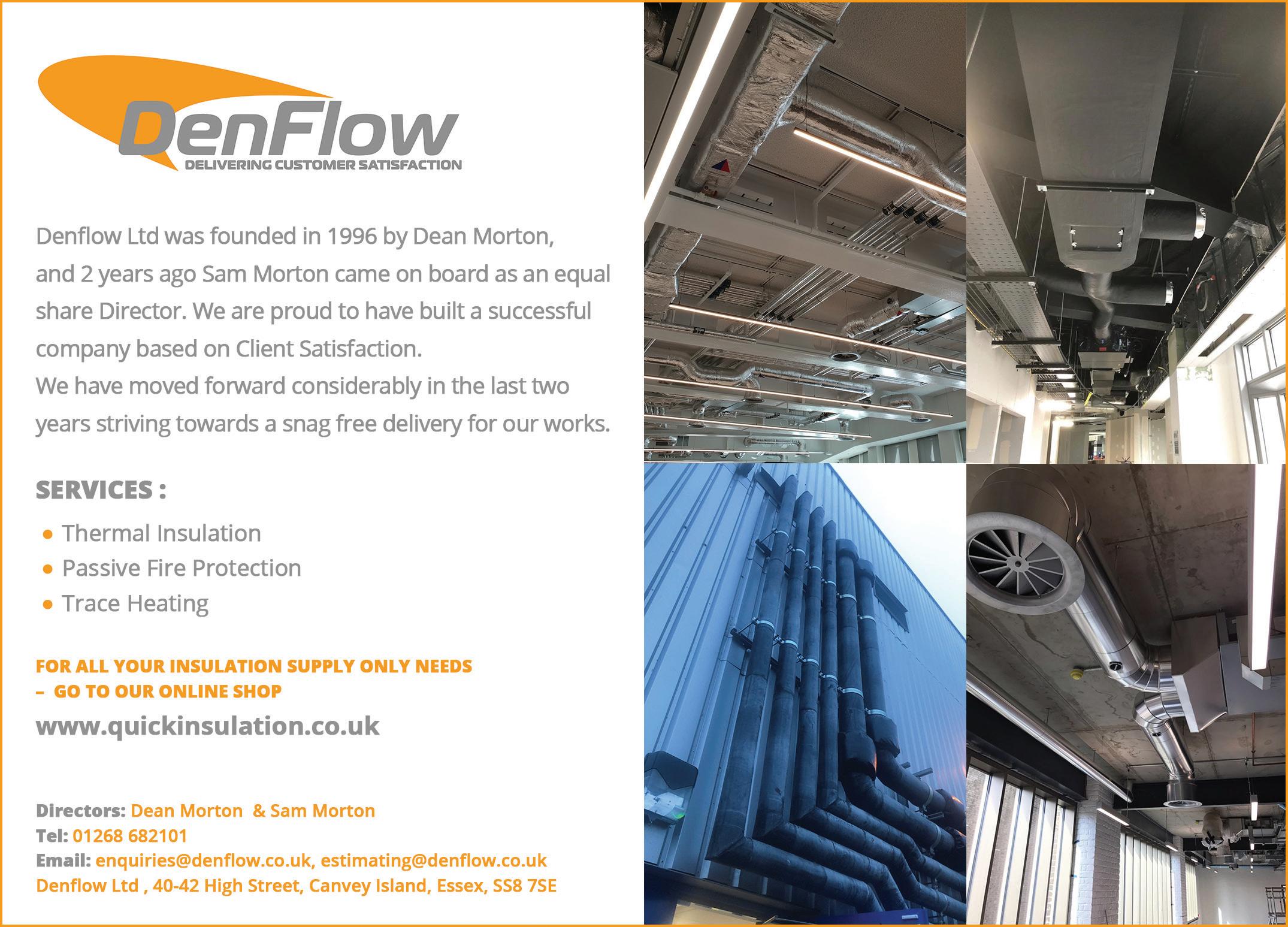
Investing for the future
With its network of strategically located distribution centres, Belgrade Insulation & Drylining has emerged from 2020 with its sights firmly set on continued expansion in the rapidly evolving structural and technical insulation markets
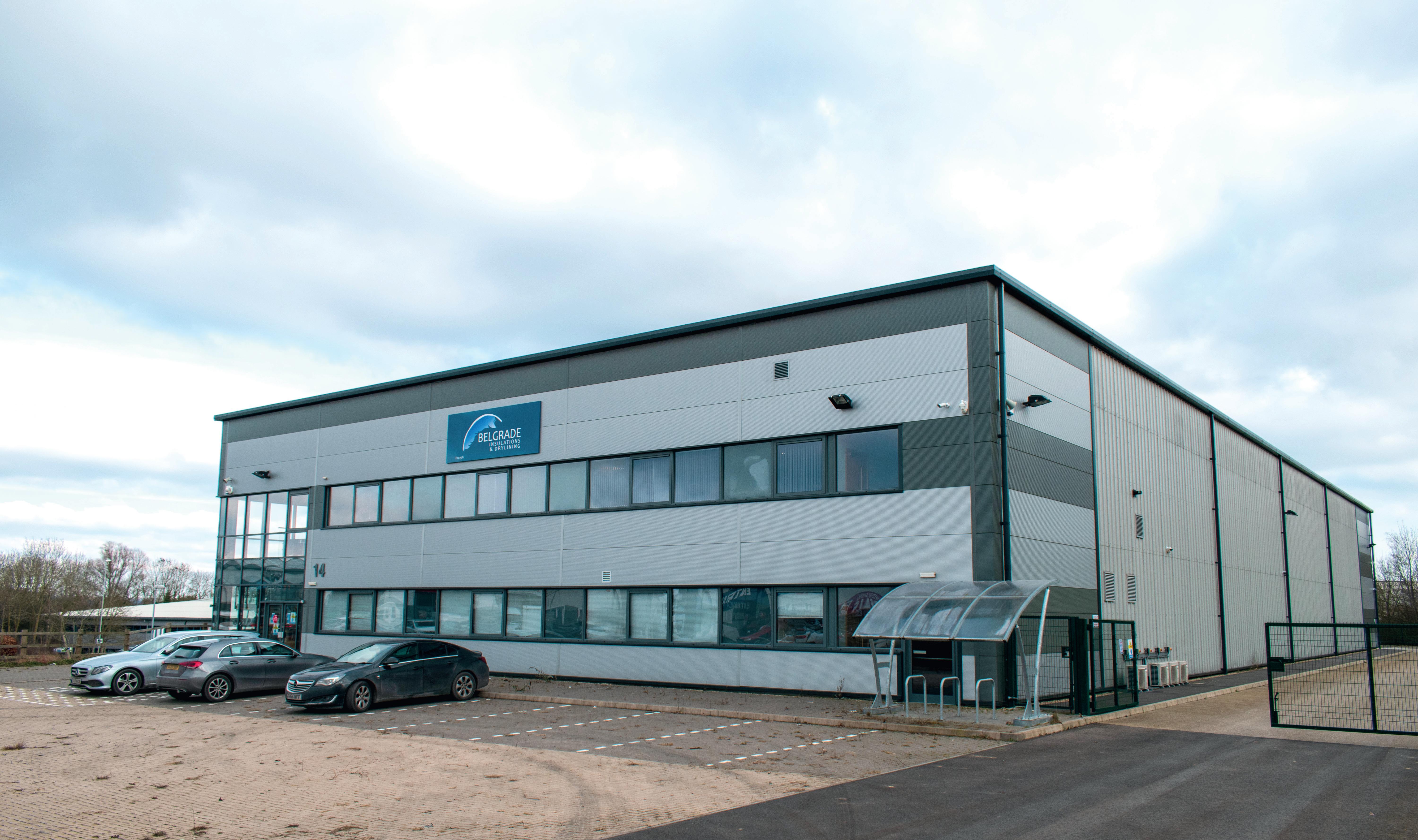
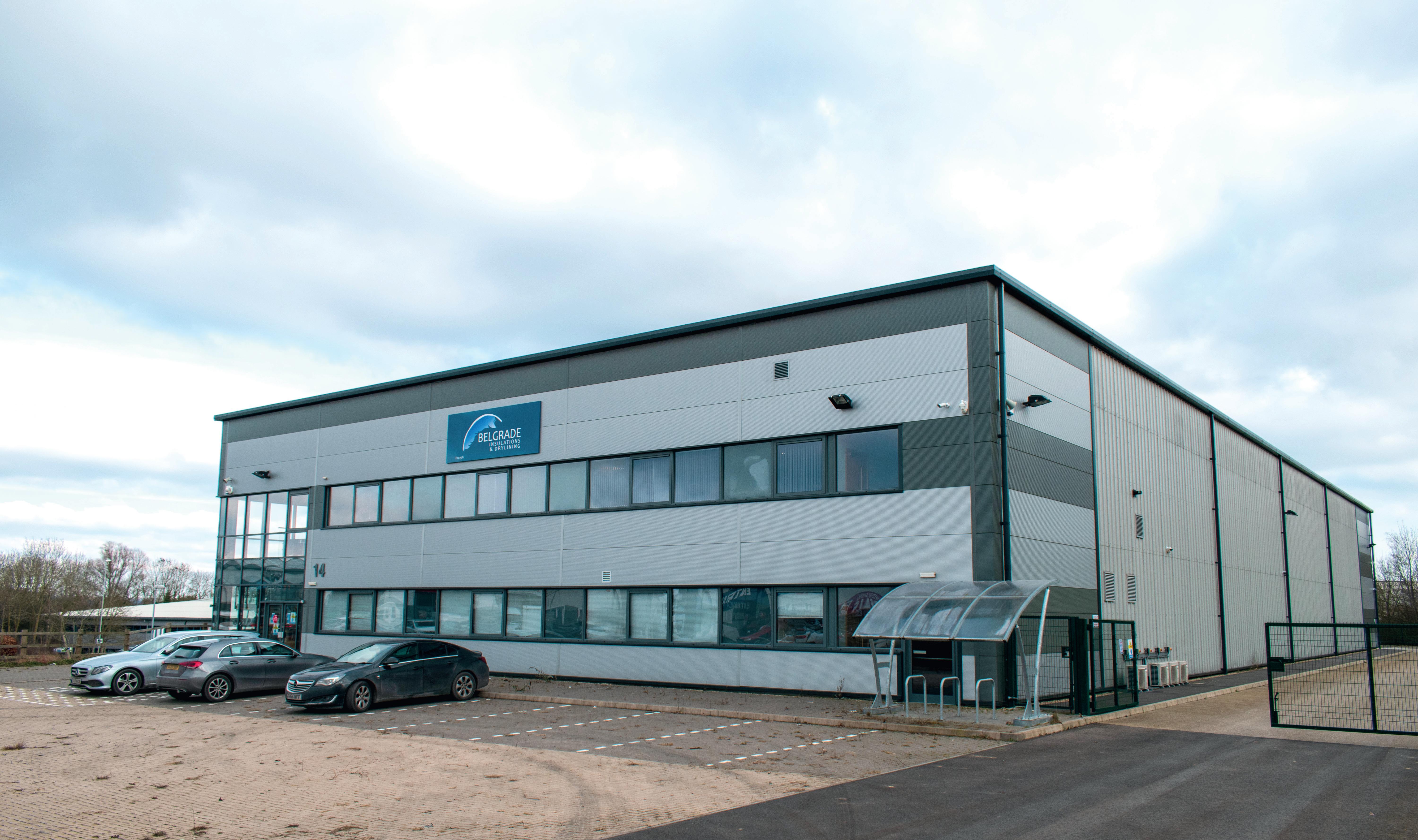

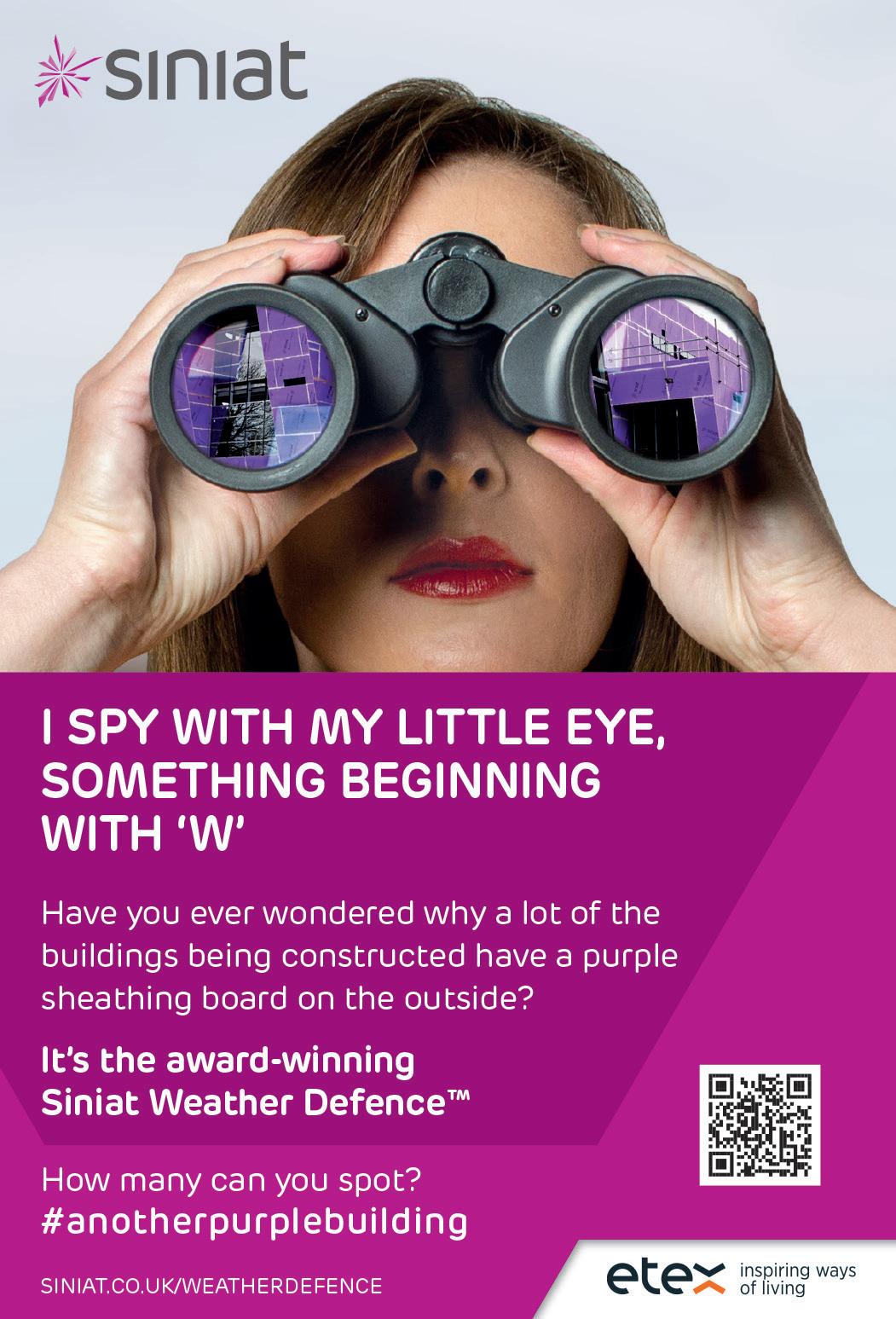
Alex Belgrade
First established in Northamptonshire in 1976, Belgrade Insulation and Drylining (Belgrade) is today a respected, recognised specialist distributor of Insulation and Drywall systems. In 2010, a management team lead by Managing Director Alex Khan acquired the business from its previous owners. In the time since, Belgrade has been the beneficiary of significant investment, not only in the development of its original trading site in Wellingborough, but also through the opening of five new distribution centres, located in London, Leeds, Birmingham, Portsmouth and Glasgow. Together, these sites allow the business to service both the Building and Technical Insulation markets.
The company has specific expertise in the Technical Insulation (HEVAC), Fire Protection and Fire Stopping, and Building Envelope sectors. These cover applications across the building market including roofing, flooring, and brickwork in traditional construction together with modular and offsite construction.
There has been rapid growth in the use of gypsum boards for a variety of applications and Belgrade has supply agreements with the major UK manufacturers that ensures specification compliance. To service this market, all branches have vehicles with mechanical offload capability. “When we acquired the business in 2010, we did so with the belief and confidence that gaining access to a network of well-established suppliers would enable us to develop a comprehensive and farreaching distribution business,” Alex begins. “In March 2011, we opened up our Leeds branch – where our head office was relocated – before opening sites
in Birmingham in 2012, Glasgow in 2014, London in 2017, and Portsmouth in 2019. In that time, we have taken a business turning over approximately £2 million in distribution from a single site, to one that achieved turnover of over £52 million in 2020 from six sites.”
Impressive growth
Today, the company excels in what Alex refers to as ‘specialist market sectors’, while Belgrade’s Business Development Director, Phil Proom, notes that the company’s activities can broadly be broken down into two categories, these being structural insulation and technical insulation. “In the case of the latter,” Phil continues, “we are talking about insulation to pipework and ductwork, the fire ...we will continue to invest in our people, developing them through training courses with the goal being to promote them up into more senior roles as time goes by. For some time now, we have recognised the need to grow talent from within the business, and we are starting to see the benefit of that approach in the advancement of our people
Saint-Gobain Insulation UK
Saint-Gobain Insulation UK are proud to supply Belgrade Insulation & Drylining with ISOVER’s wide range of HVAC solutions. Whether it’s a school, hospital, factory, office or residential building, ISOVER’s HVAC range will provide efficient insulation solutions for pipes and ductwork to provide thermal, acoustic and ventilation comfort in buildings. Our dedicated sales and technical support teams are available to assist and support you on your building projects.
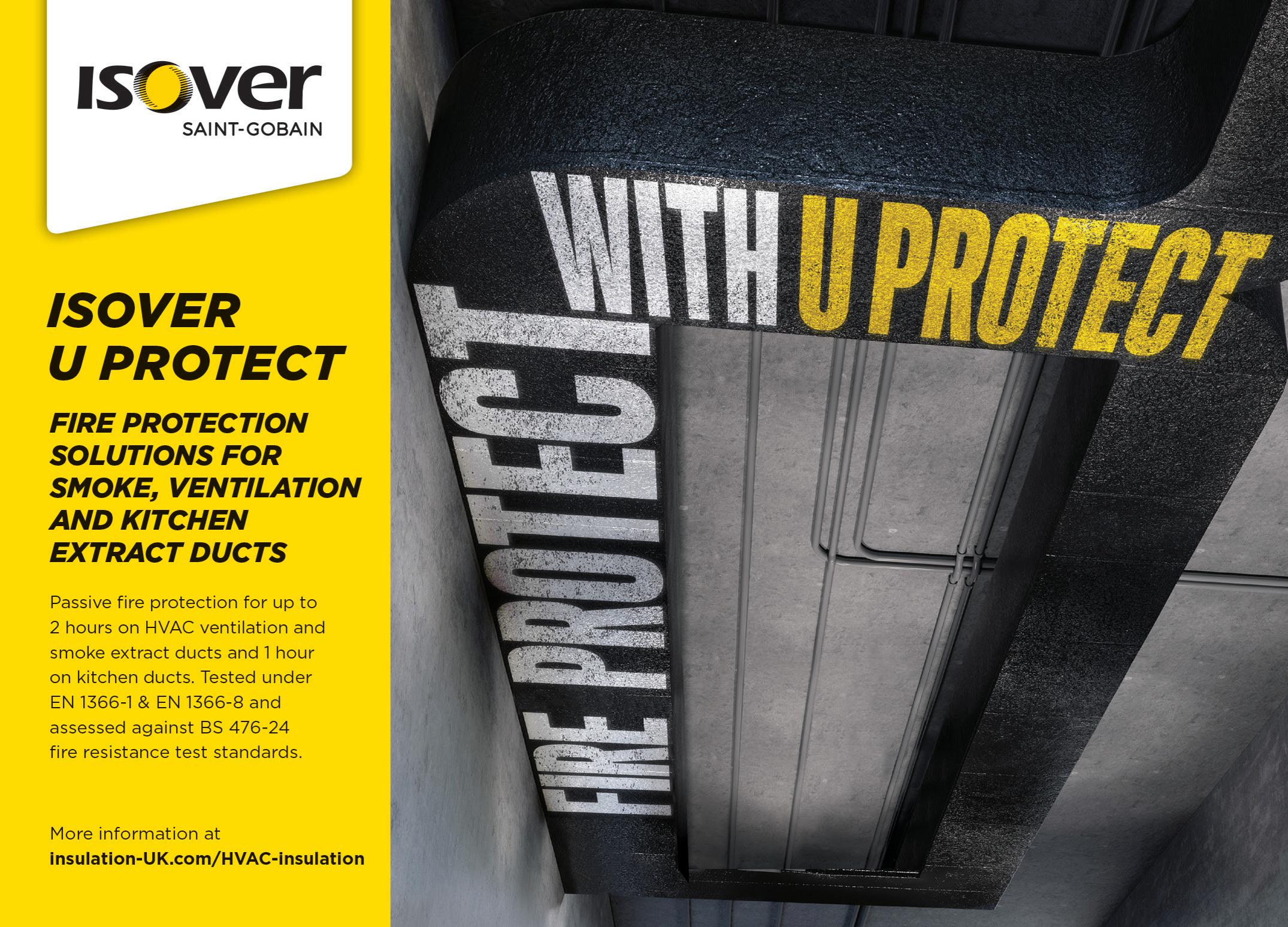
protection of those systems, together with fire stopping of penetrations.
“Our membership of industry trade associations ensures our sales teams are aware of latest products, their application and regulatory compliance across all the sectors in which we operate. Belgrade are members of bodies including, ASFP, BMF, FIS, NFRC, and TICA.”
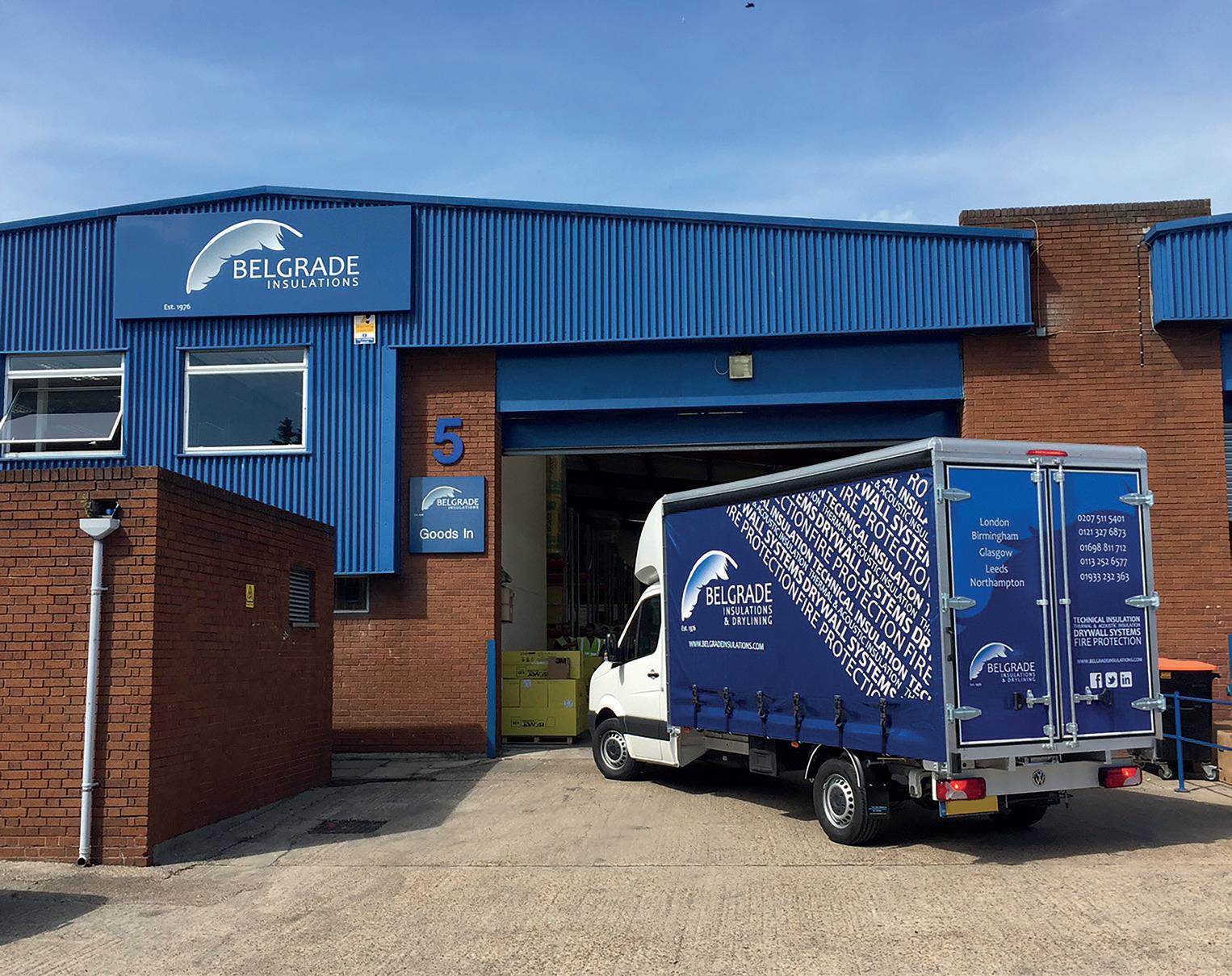
London branch
It is Phil who goes on to offer an important insight into what has helped Belgrade to achieve such impressive levels of growth and success in a relatively short space of time. “For me, it has to do with several factors, including the nature of the relationships that we build with our suppliers, customers, and the consistent quality of our service,” he details. “Said relationships are built upon providing our customers with what they want, when they want, by always delivering on-time and infull. Furthermore, as you will know, the construction industry is very much a people-centric industry, and we take incredible pleasure in being able to rely upon the quality, commitment and passion of our teams throughout the UK.”
Looking at the recent performance of the company,
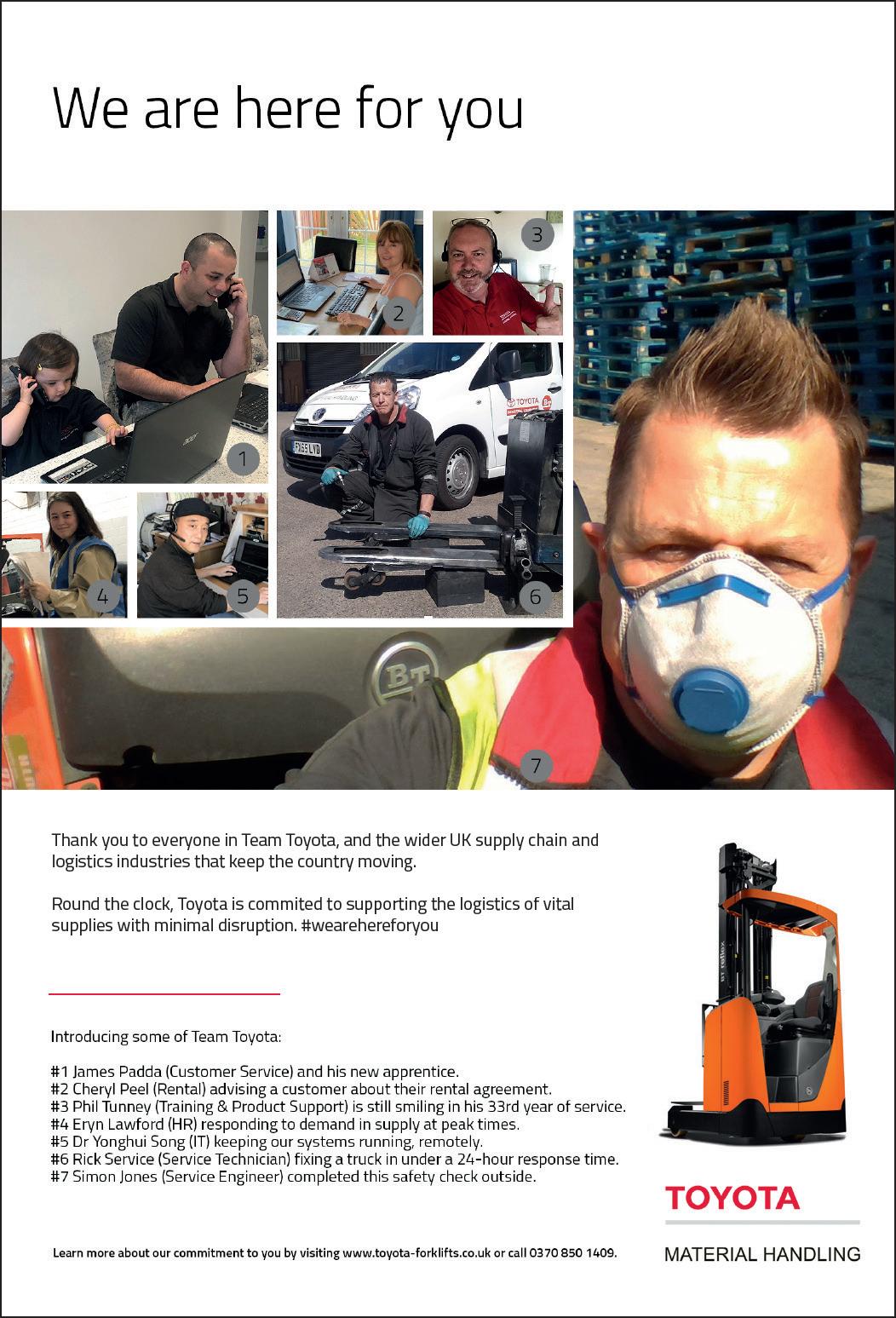
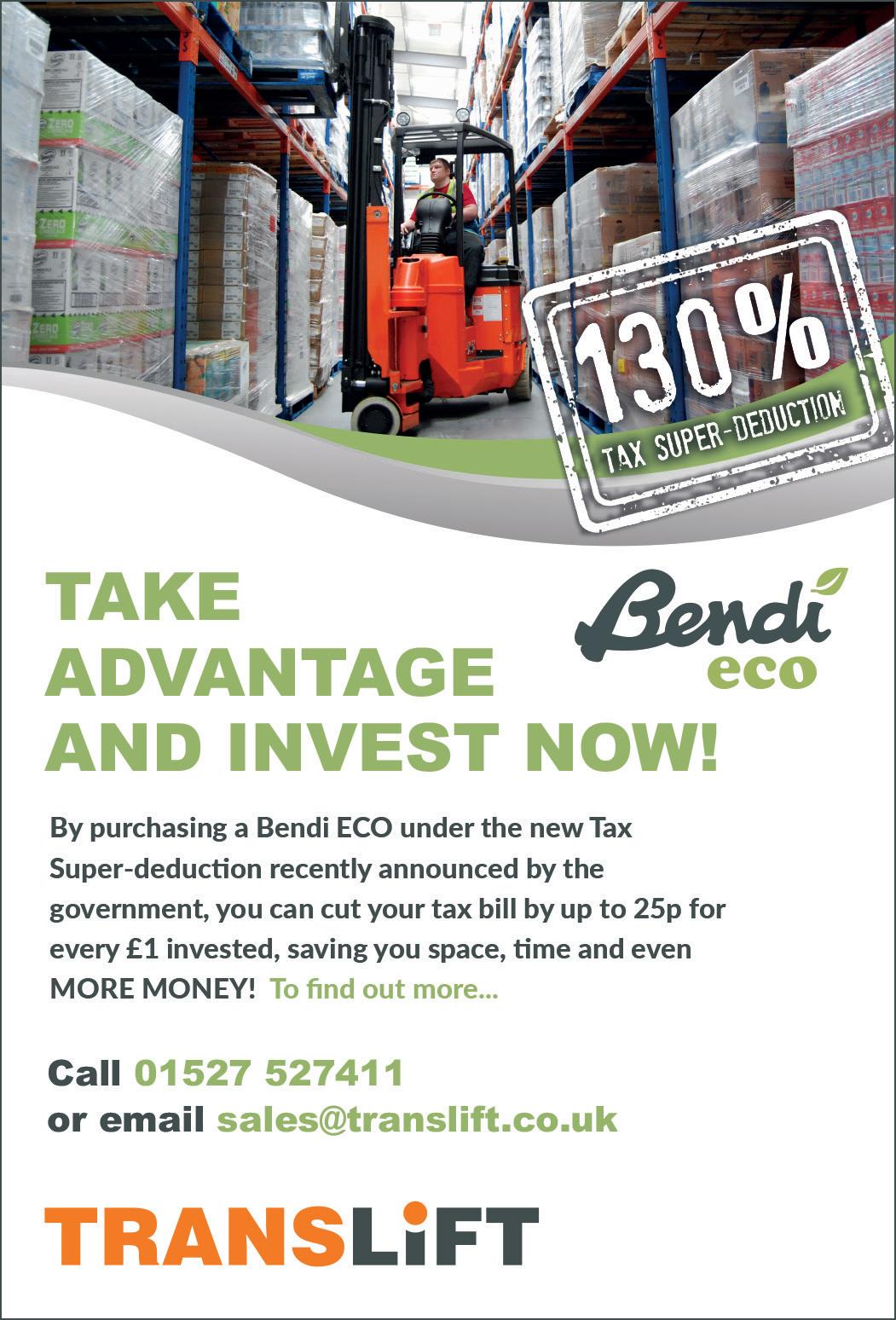
particularly during 2020 and the height of the Covid-19 pandemic, both Alex and Phil are humble enough to note that they – like many of us – have been pleasantly surprised by how strong the recovery in a number of sectors has been since those initial months of lockdown in the spring of last year. “With construction being designated a key industry in those early weeks of the pandemic, we worked tirelessly with not only our own teams, but also our customers to ensure that whatever we were doing as a business, that it was being conducted in a safe environment,” Alex stresses. “We initiated procedures, systems and equipment to make our branches Covid-19 secure and safe for our colleagues. Where it was possible and practical a number of our teams worked from home. We did make use of the furlough scheme for a few weeks, but soon brought these people back and have come through the last year in spite of some incredibly unique challenges.”
New space
Indeed, in spite of the pandemic, Belgrade was also able to move forward with its ongoing investment in its facilities, including acquiring additional space for its Birmingham site in November 2020.
In February 2021, it also announced the relocation of its Wellingborough branch to the Brackmills Trade Park in Northampton. The enhanced stock holding covers products for Building and Technical insulation, together with Drywall Systems and Passive Fire Protection. The fully Covid-19 compliant branch also boasts expertise in building envelope insulation and associated fire stopping solutions.
Another key feature of the branch is that it holds the
Mannok
Mannok is a leading manufacturer of a diverse range of premium building materials, including bulk and bagged Cement, top quality concrete Roof Tiles, high performance PIR and EPS insulation, Aircrete blocks and bespoke designed Precast concrete products. The company has been working in partnership with Belgrade Insulations & Drylining for many years as a supplier of insulation products. Key to their long-standing, close relationship is a shared focus on delivering excellence to their customers. Mannok’s award-winning products and service combined with its focus on sustainability and innovation has earned it a reputation as one of the UK’s preferred building materials brands.
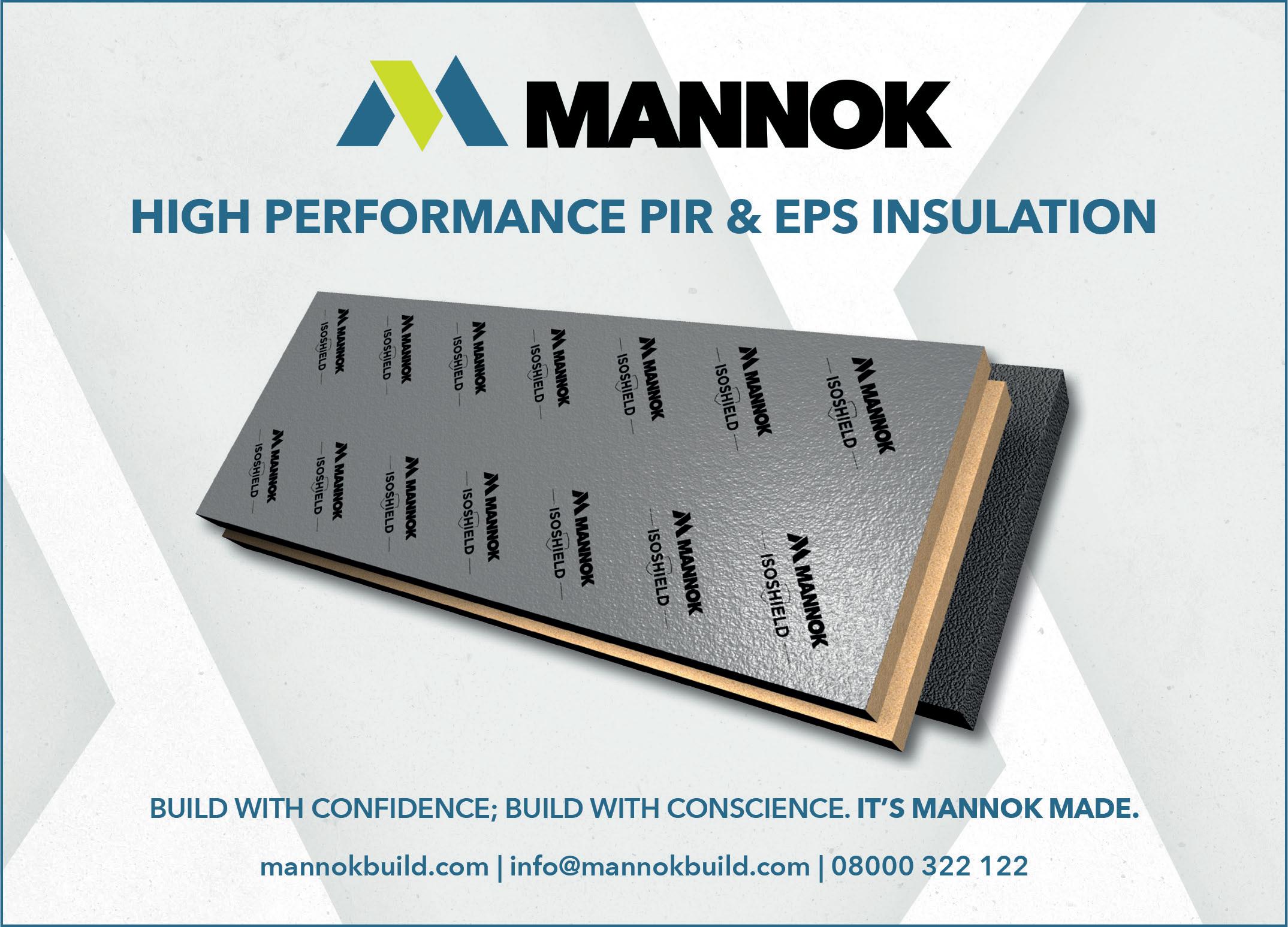
Merlin Park

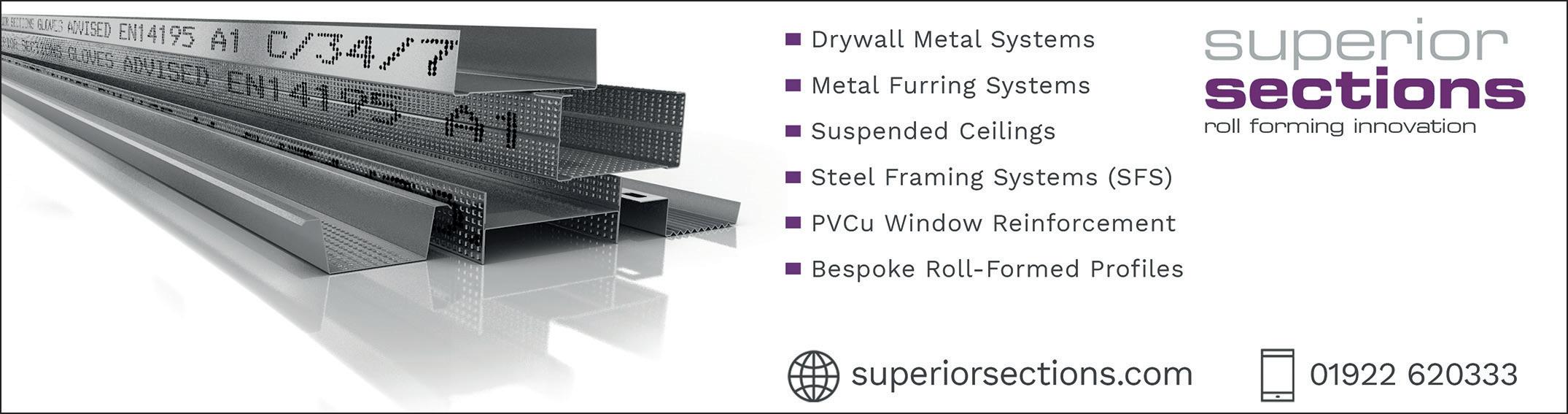
latest storage and mechanical handling equipment to fully utilise floor and height space. It is complemented as well by secure external storage and a dedicated material handling area. “The biggest cost to the business is arguably warehousing, so it is imperative that we get as much use out of this space as we can,” Phil notes.
Positive outlook
In the coming months of 2021, Belgrade will also be moving forward with a planned relocation of its Leeds facility. “At the same time,” Phil notes, “we will continue to invest in our people, developing them through training courses with the goal being to promote them up into more senior roles as time goes by. For some time now, we have sales, improving its margins, and cultivating talent within its employ wherever possible. “The outlook for the industry is very positive, and while crystal balls are in somewhat short supply at the moment, the general consensus is that the UK will see increased investment going forward in things like hospitals, schools and other key infrastructure areas,” Phil affirms.
“So, with that in mind, we anticipate a future for Belgrade that looks very promising indeed.”
Leeds branch
recognised the need to grow talent from within the business, and we are starting to see the benefit of that approach in the advancement of our people.”
From a more longer-term perspective, Alex and Phil believe that the future hopes and goals for Belgrade rest on it continuing to deliver what it has done so consistently for the last decade, namely increasing its volume of
Products: Specialist distributor of insulation and drywall systems
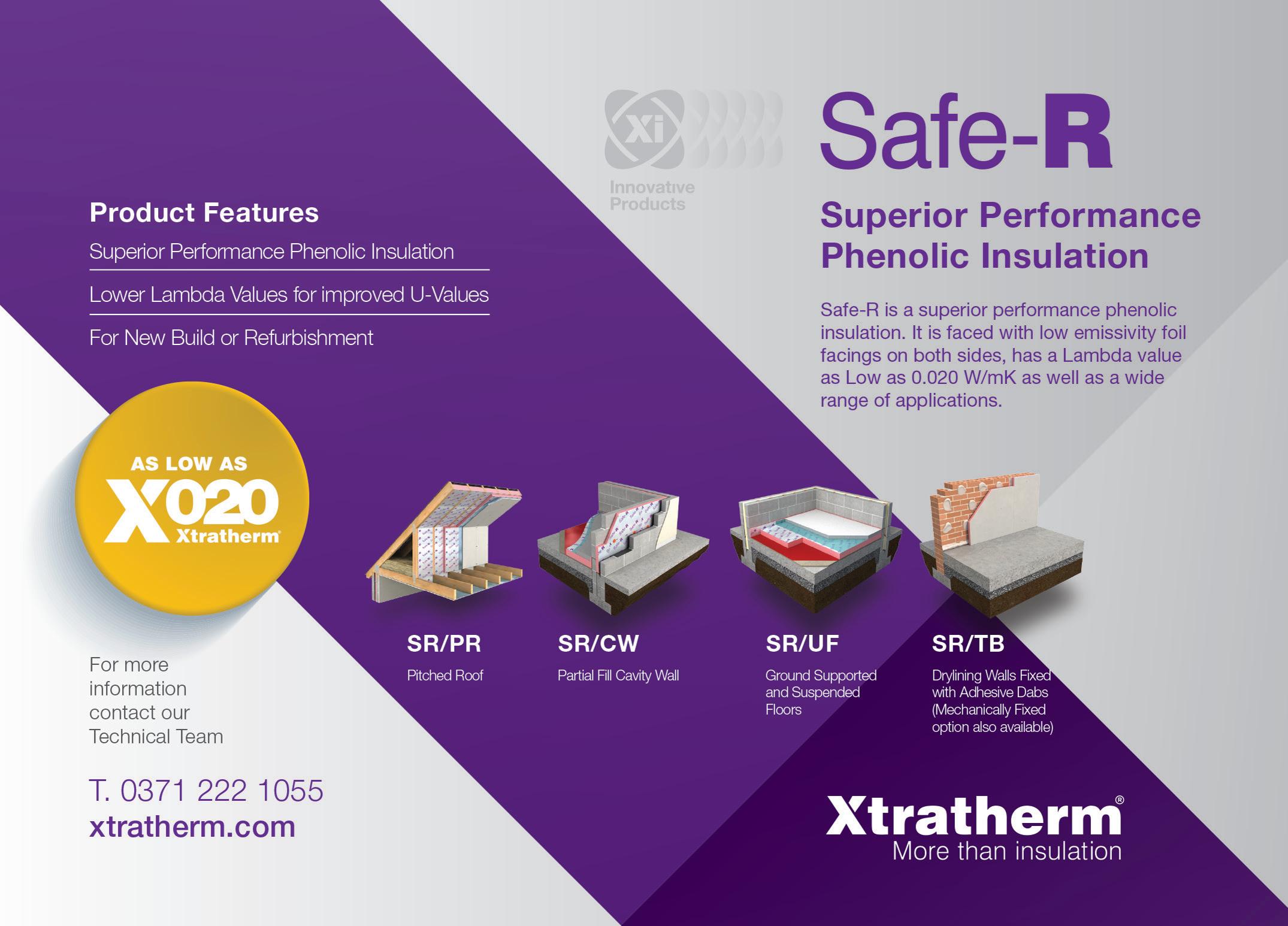
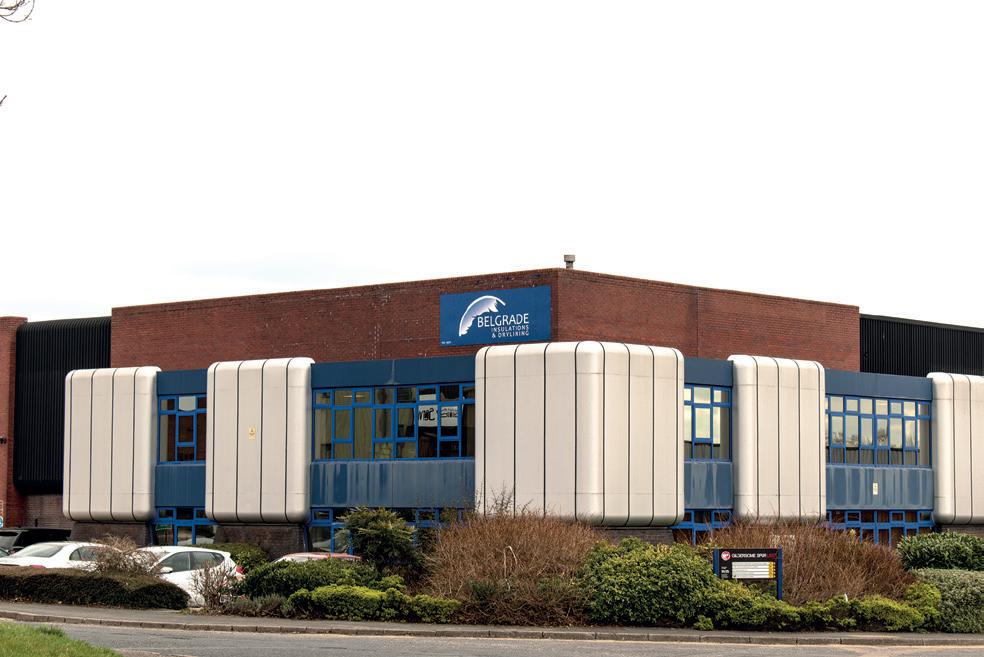
Clad with confidence
As a successful contractor, Colmore Tang Construction is determined to pioneer an industry in which its services provide clients with the peace-of-mind to live and work safely
Following the Grenfell Tower disaster in 2017, it is expected that the Government will enforce legislature to make cladding remediation mandatory by the end of 2021. This is as a result of report findings that around 2,000 residential buildings are still swathed in high-risk combustible cladding, which include many high-rise buildings across the UK such as hotels, student accommodation and residential
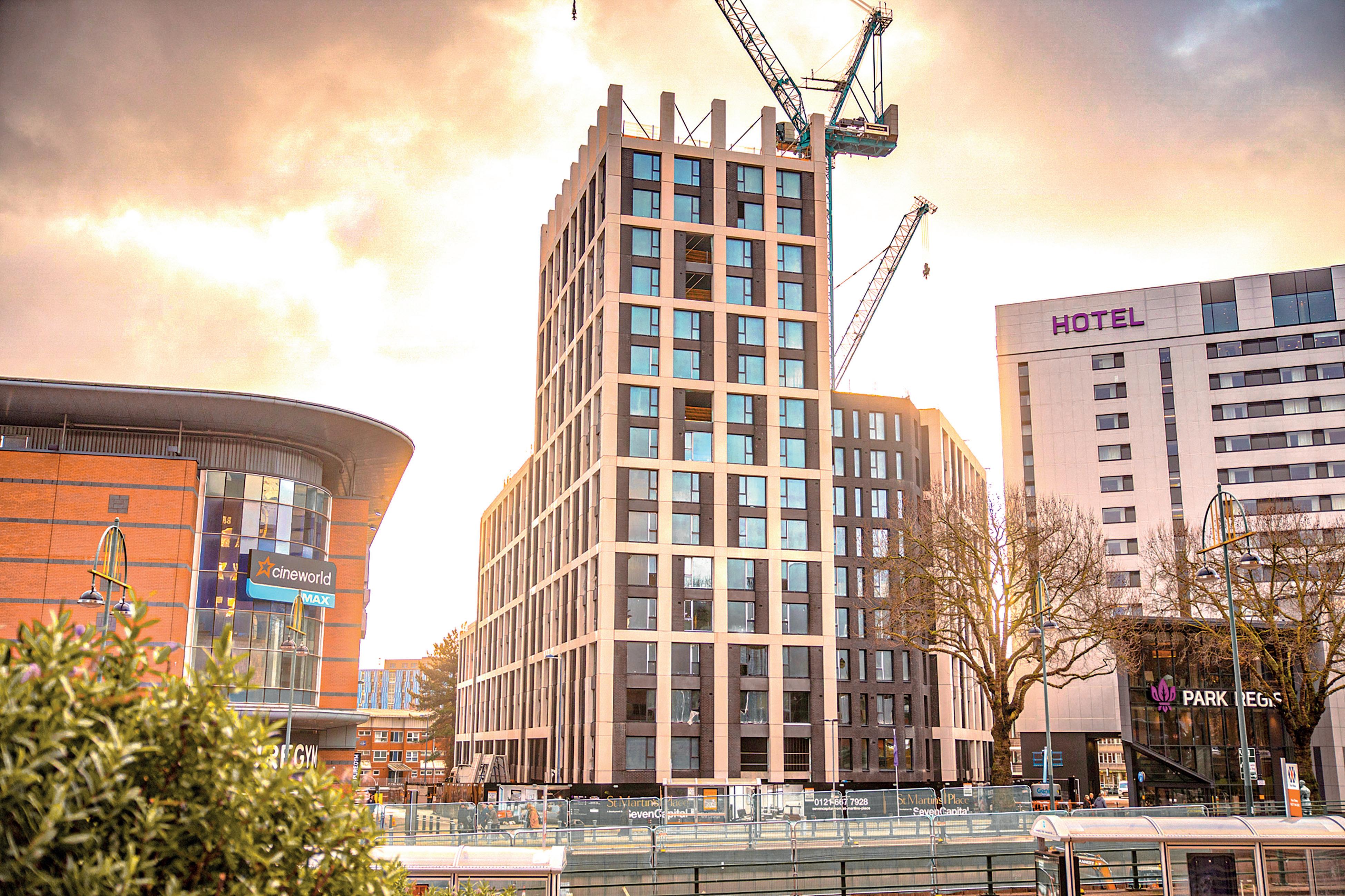
care homes that have been built using unsafe cladding systems.
This is why Colmore Tang Construction is using its expertise in development and supply chain management to offer complete and insurable cladding remediation and provide comfort and trust for its occupiers, building owners and agents. Having delivered over 3,700 new apartments since its inception in 2013, Colmore Tang is one of the UK’s fastest-growing contractors. It specialises in tall, high-density residential buildings, operating across the Midlands, with a wealth of over 450 years of combined experience in constructing new buildings. The Birminghambased contractor understands the design complexities, supply chain requirements and risk management in delivering cladding remediation with EWS1 compliant properties.
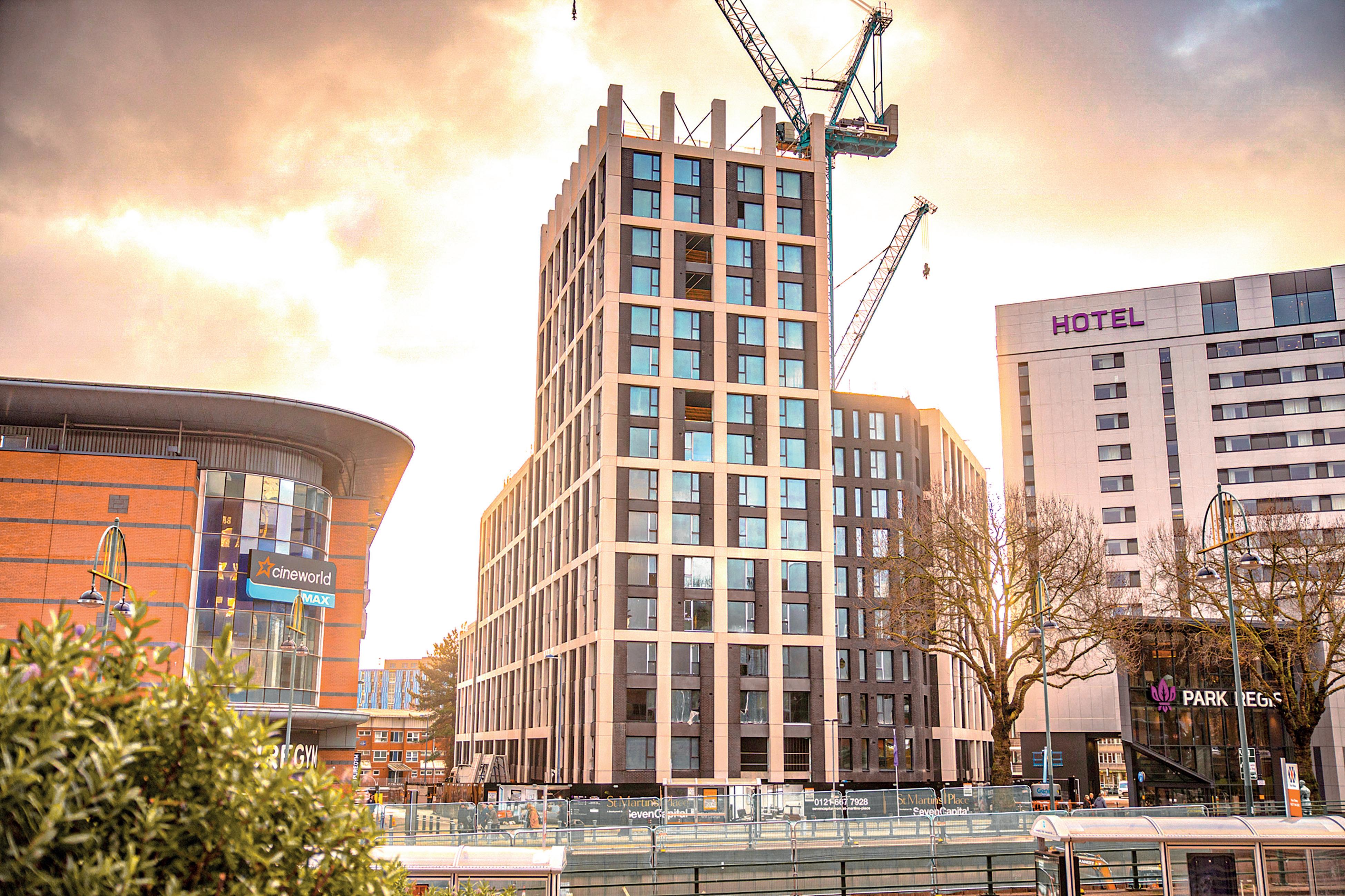
Harnessing expertise
Since 2016 – when Colmore Tang was last featured in the magazine – the company has continued to successfully tally a list of highlights. According to the Chief Operating Officer Steve Underwood, the company is proud that it has maintained its progress on live projects during 2020, despite the challenges presented by the pandemic. “We have additionally built a core business of highly competent and dedicated individuals while providing a class leading solution for multi-finished concrete structures,” Steve informs.
Maintaining this pace has meant that that life in the business has been nothing short of a rollercoaster ride. “We have been driven by demands made by our market. We had to cope with a peak in 2019 with a dozen projects on site generating an annual revenue of around £100 million while employing over 100 staff from a standing start. This level of activity would represent a challenge for an established medium sized business, however with the support of our clients and staff, we have succeeded,” says Steve.
After the Grenfell disaster, one of the most debated market demands has been the need for safer, robust cladding and Colmore Tang has responded
accordingly. In January 2021, its passion for safety led the company to launch an end-toend cladding remediation service to harness the expertise gained through working closely with its clients, particularly in dealing with means that it is also able to advise owners who would like to access the Government’s Building Safety Fund.
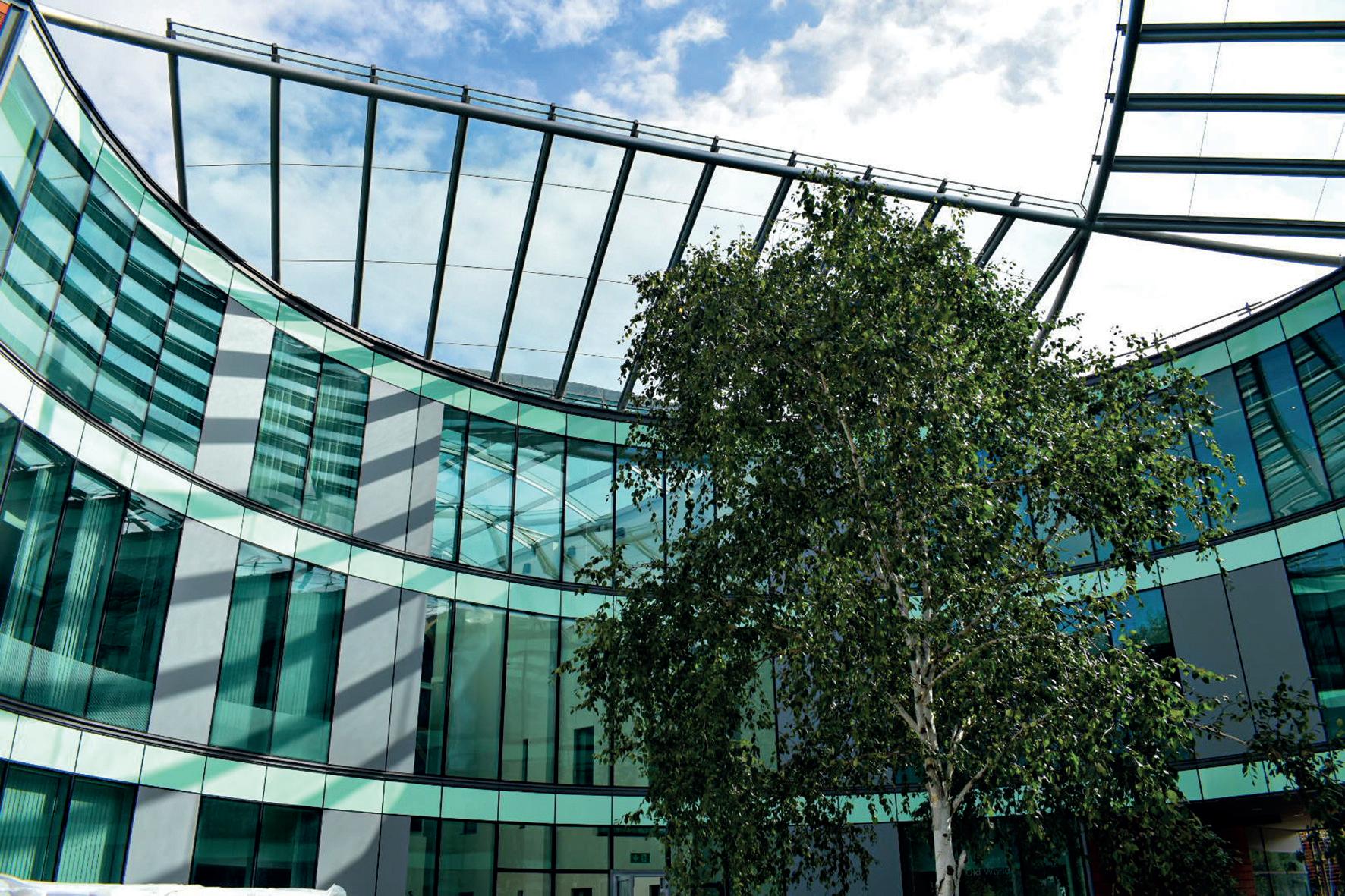
the demands of the end user. By drawing on its established supply chain, Colmore Tang provides the full remediation process from initial fire assessment and design, to project management, tax advice and delivery. This Methodical approach
This diversification in its services allows Colmore Tang to pride itself on being a complete solution for building owners, managing agents and surveyors seeking to replace dangerous, non-compliant cladding. “Not only do we draw on our own experience of delivering high-rise residential homes, but furthermore we have developed a comprehensive approach to cladding remediation and passive fire protection that enables a fully audited, designed and delivered service with compliance, cost and quality assurance,” Steve further elaborates.
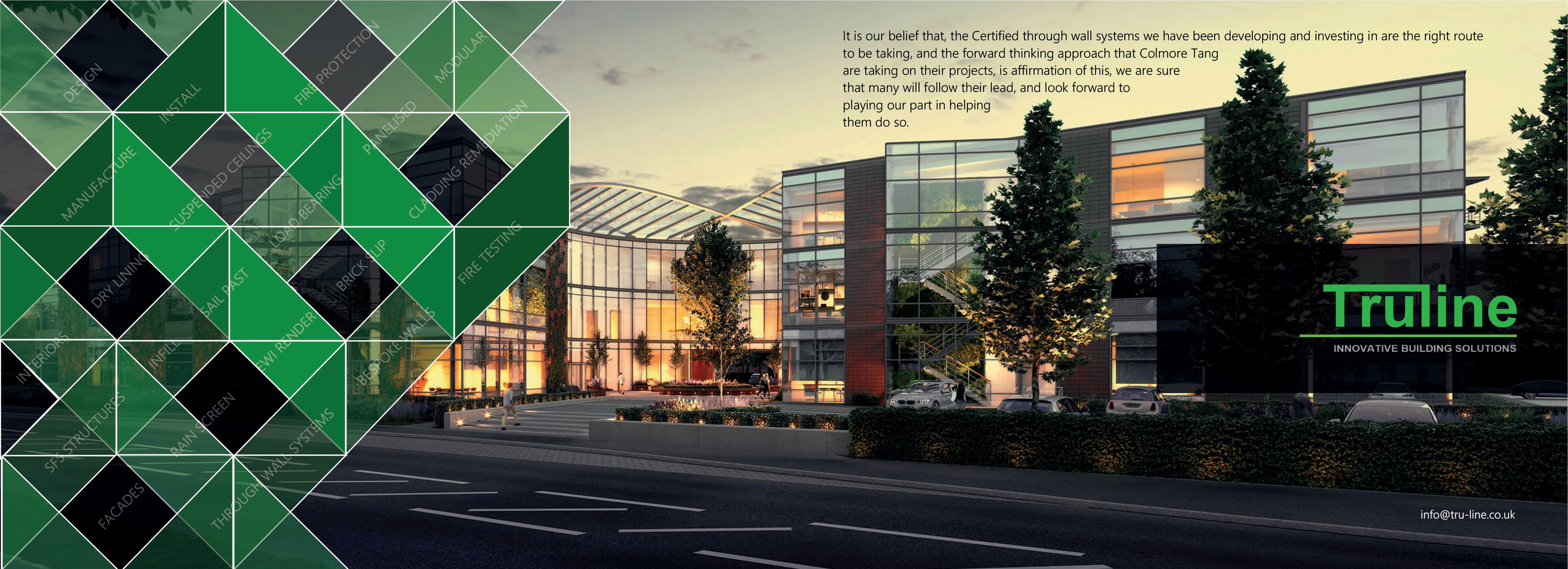
According to him, cladding is fairly similar to all construction and if you are able to get the basics right before starting on site, the rest of the project flows fairly smoothly. If not, these basics can amount to some of the challenges and hurdles associated with cladding remediation works in the UK. To guarantee that these obstacles are avoided, Colmore Tang ensures that before each project there is a clarity of requirements between the team and the client, an acknowledgement of the true scope of works, adequacy of program, sources of funds, design and labour resources, material and planning to ensure that the job is completed as efficiently as possible.
Such a methodical and careful approach to each project has clinched an impressive portfolio of outstanding developments completed by Colmore Tang in the last several years. Two noteworthy constructions that
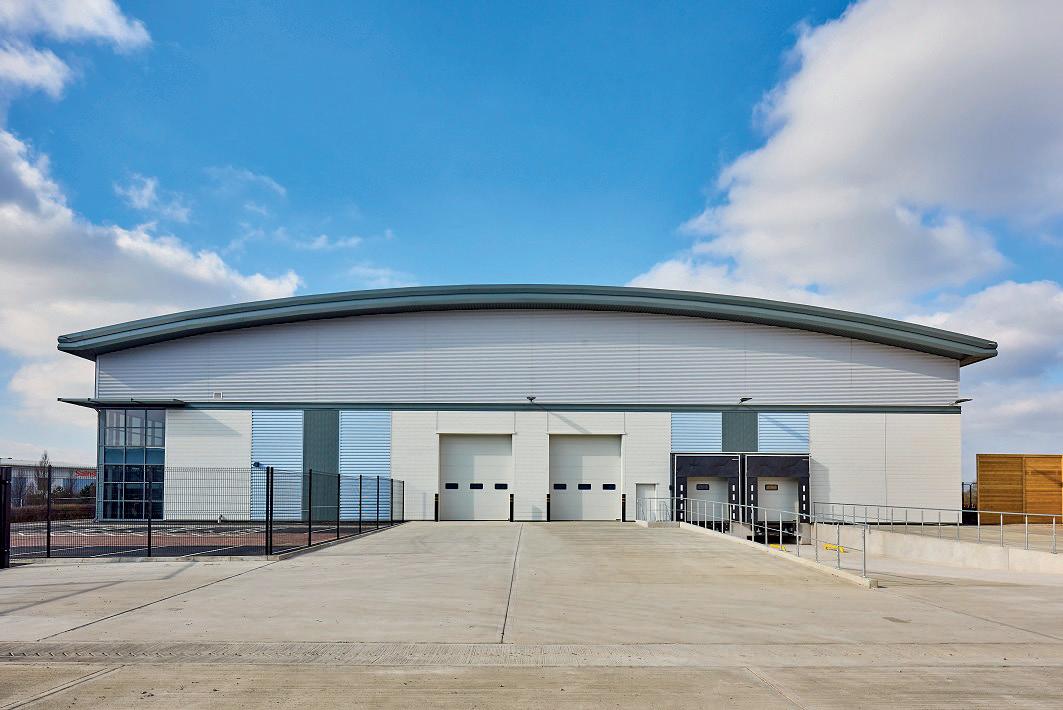
Truline
The clarity of Colmore Tang’s message to their supply chain is clear and positive: ‘Change the culture of the industry to one that strives to do it right!’ An Ethos that is not only commendable but is an affirmation of Truline’s own beliefs.
The commitment to the use of technology and innovation in their management processes, especially those of compliance and quality control along with the early involvement of their supply chain and the expertise they bring, works well for all, providing the right product for each element of the build.
The end to end approach to the cladding remediation sector and their view that this is not simply a matter of ‘a strip out and replace’ contract, but is more about understanding the whole process, this leads us to think that they will become a leading light in this sector of the industry and we look forward to being part of their solution.
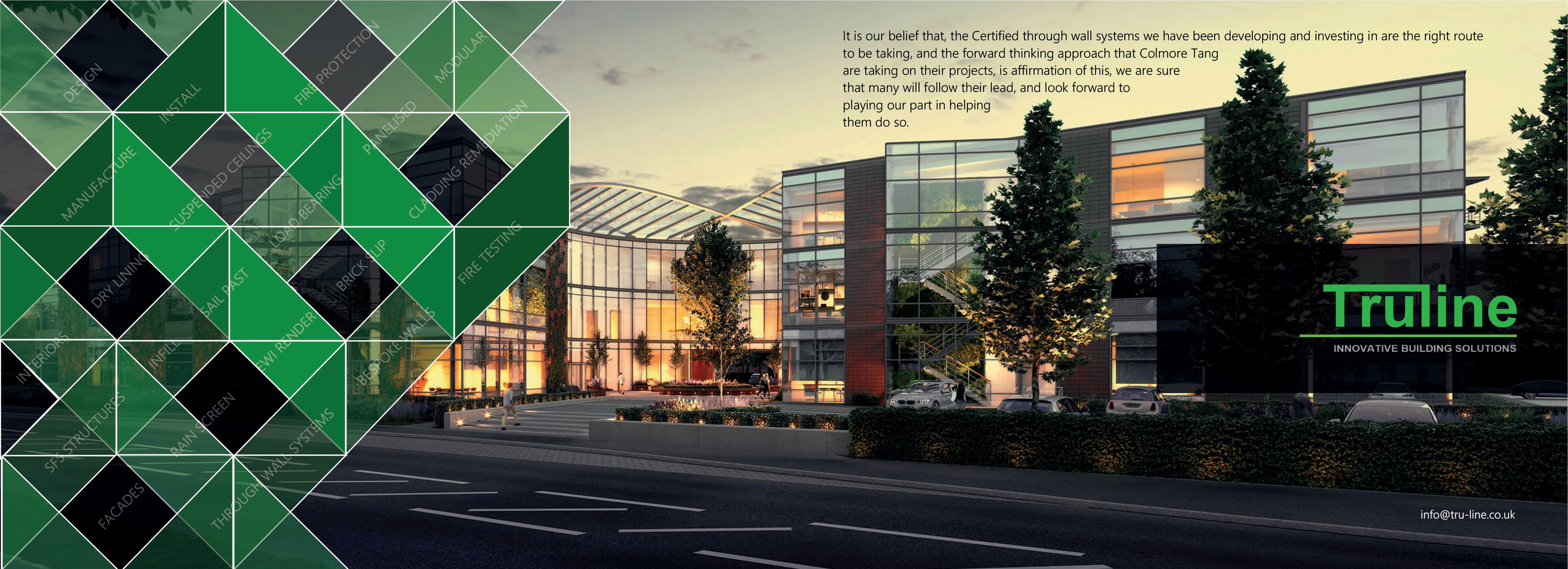
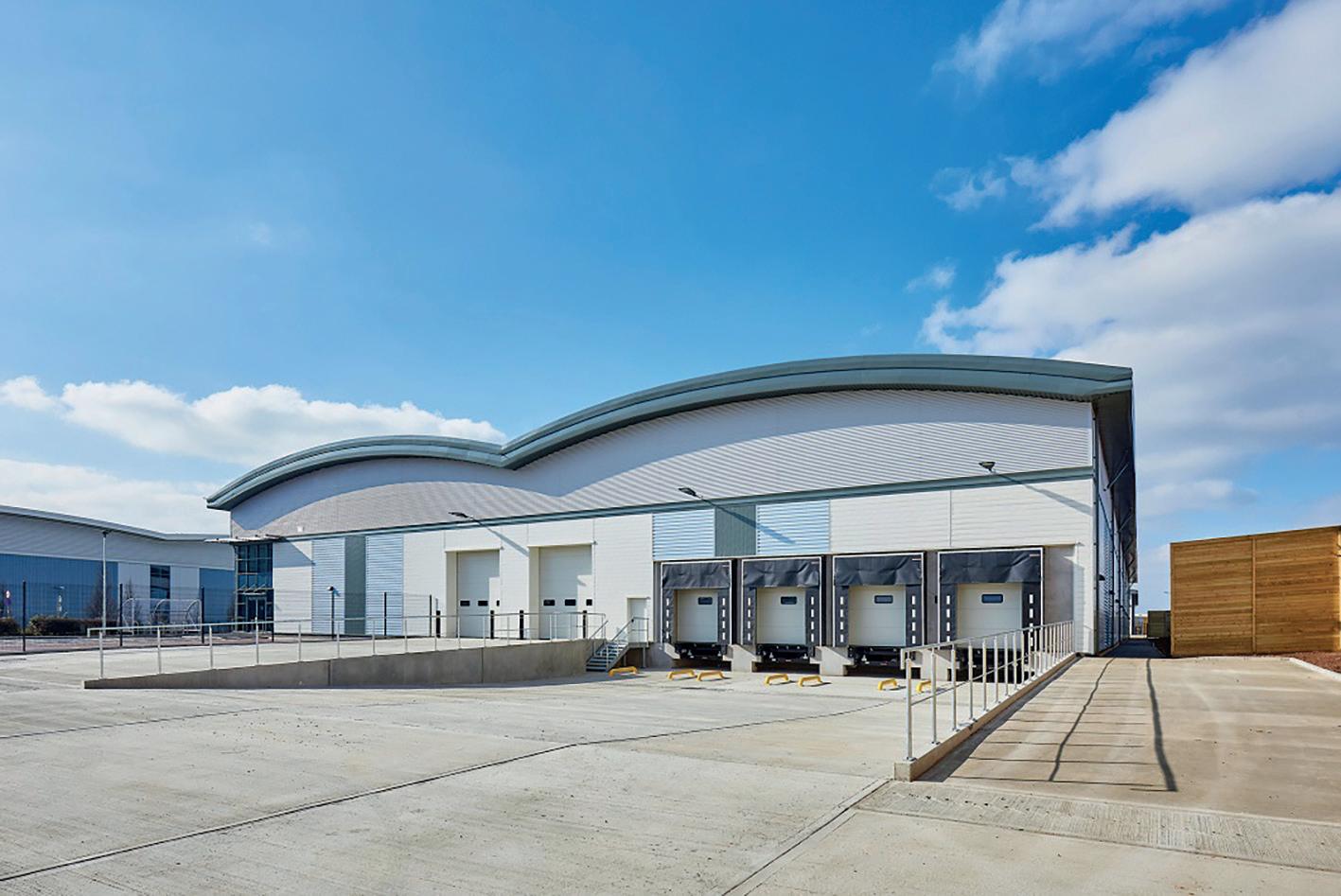
the business is particularly proud of are One Thames Valley and St Martins Place. The Thames Valley development involved the transformation of a high-tech office building into a location of luxury living accommodation. “On this project, the team was faced with the challenge of renovating a building in which the design was far from ideal. However, with meticulous planning and dedicated work ethic, we constructed the Thames Valley skyline’s new focal point,” explains Steve. With floor-toceiling windows centred around an expansive atrium and two residential lounge wings equipped with open-plan seating, the building’s atmosphere encourages community by bringing the outside in. space and 120,000 square feet of distribution warehousing.
On top of its vast range of services, Colmore Tang’s concern for the built environment extends into tending to the needs of its community. In February 2021, the company announced that it will be donating refurbished highend laptops and tablets to pupils at Birmingham’s City Academy. Following a recent system upgrade, Colmore Tang identified a number of devices that could be repurposed to support home learning. The contractor worked with a close IT partner to ensure these devices would be fit for home schooling assistance for disadvantaged students who have not had access to IT equipment suitable for remote learning during lockdown. “With construction projects across the city, it’s important to us that we support our local communities; City Academy is a fantastic school, less than a mile from our office, I know that this donation will make a major impact on its young learners,” Steve notes.
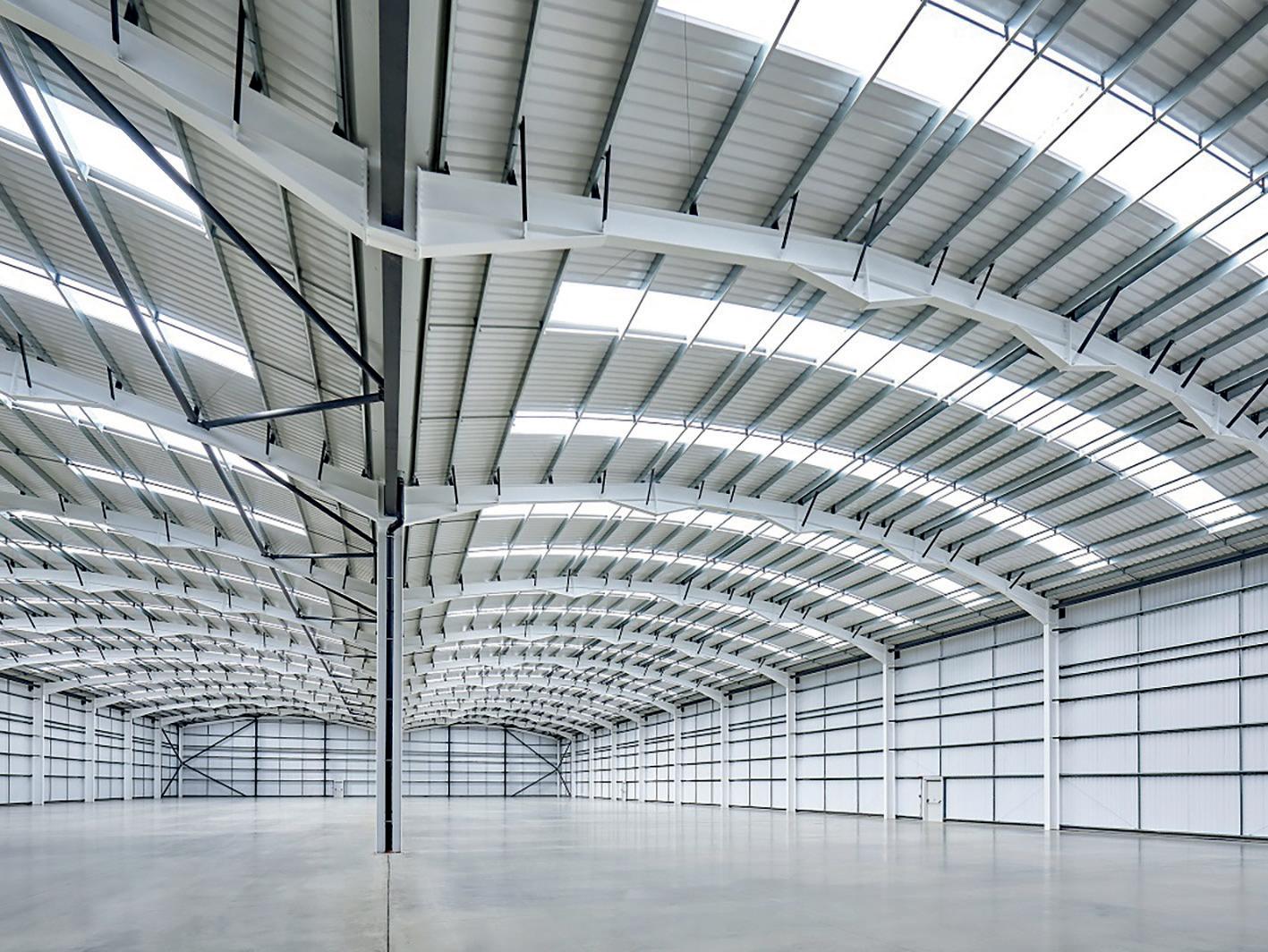
Then, moving out from London and back to Birmingham, the St Martins Place project required a panelised solution for an upmarket residential tower with integral parking. Located just minutes from Birmingham’s main business district, the premium development features 228 spacious, luxury one, two and three-bedroom apartments, as well as residential amenities which include a private gym, cinema, Wi-Fi, café and 24-hour concierge. Steve also adds here that the site was adjacent to a four-star hotel in which the guests did not suffer from any disruptions or disturbances. In addition to these striking constructions, Colmore Tang has also delivered a 253-bedroom four-star hotel, 180,000 square feet of retail Stand out features
It goes without saying that for some companies, the pandemic has been a detrimental knock to business, but for ColmoreTang, as we have seen, there were many highlights in spite of the international crisis. According to Steve, the company was able to maintain progress on live projects during 2020 and consequently, was able to build a core business of highly competent and dedicated individuals to provide a class leading solution for multifinished concrete structures. This sort of determination for growth comes down to two stand out features that the company believes in continuously refining. “Firstly, coupled with a degree of buoyancy in the high density residential market, we strive to meet and exceed our clients’ demands and secondly, we have
an ability to bend our business to meet those in-coming demands,” explains Steve.
Now, as it emerges out of the pandemic, the company is determined to focus on providing full façade and cladding remediation for the buildings in the Birmingham and Liverpool Manchester and Leeds corridor. “We also have plans to continue developing opportunities with partner businesses and to repurpose existing buildings for safe residential use,” highlights Steve, “Of course, looking towards the next three-to-five years, we wish to remain a niche organisation that can provide a tailored service to our clients and pioneer the façade remediation industry,” he continues.
Last year, the UK Government announced that £5 billion would be allocated to the Building Safety Fund to support the remediation of unsafe residential buildings that are 18 metres and higher. This means that pressure is mounting on building
Bennetts Cranes
Bennetts Cranes is a leading specialist tower crane provider in the UK, with an extensive fleet of luffing jib, saddle jib and remote-controlled cranes. Bennetts is proud to be a supplier to Colmore Tang, and recently completed work on its St Martin’s Place development in Birmingham. Bennetts purchased two brand-new 24 tonne capacity cranes for the project, due to the large lifting capacity required for the pre-cast panels that were used to build the luxury apartments. Edward Seager, Managing Director of Bennetts Cranes, said: “We were delighted to work with Colmore Tang. Using these two cranes enabled the site to lift heavy panels that were manufactured off-site, which in turn resulted in an efficient build process.”
owners and managing agents to provide safe and secure living environments on behalf of their leaseholders. On this issue, Steve conclusively comments that nobody should have to live in an unsafe building. “Through conversations we have had with building owners, managing agents and even cladding manufacturers, it’s clear that the complexities in cladding remediation are slowing down the ability to get this vital work done,” he ends. Colmore Tang Construction is determined and dedicated to fulfil a mission in which all occupiers of the UK’s high-rise built environment can live and work confidently.
Colmore Tang Construction www.colmoretang.com
Services: Construction contracting
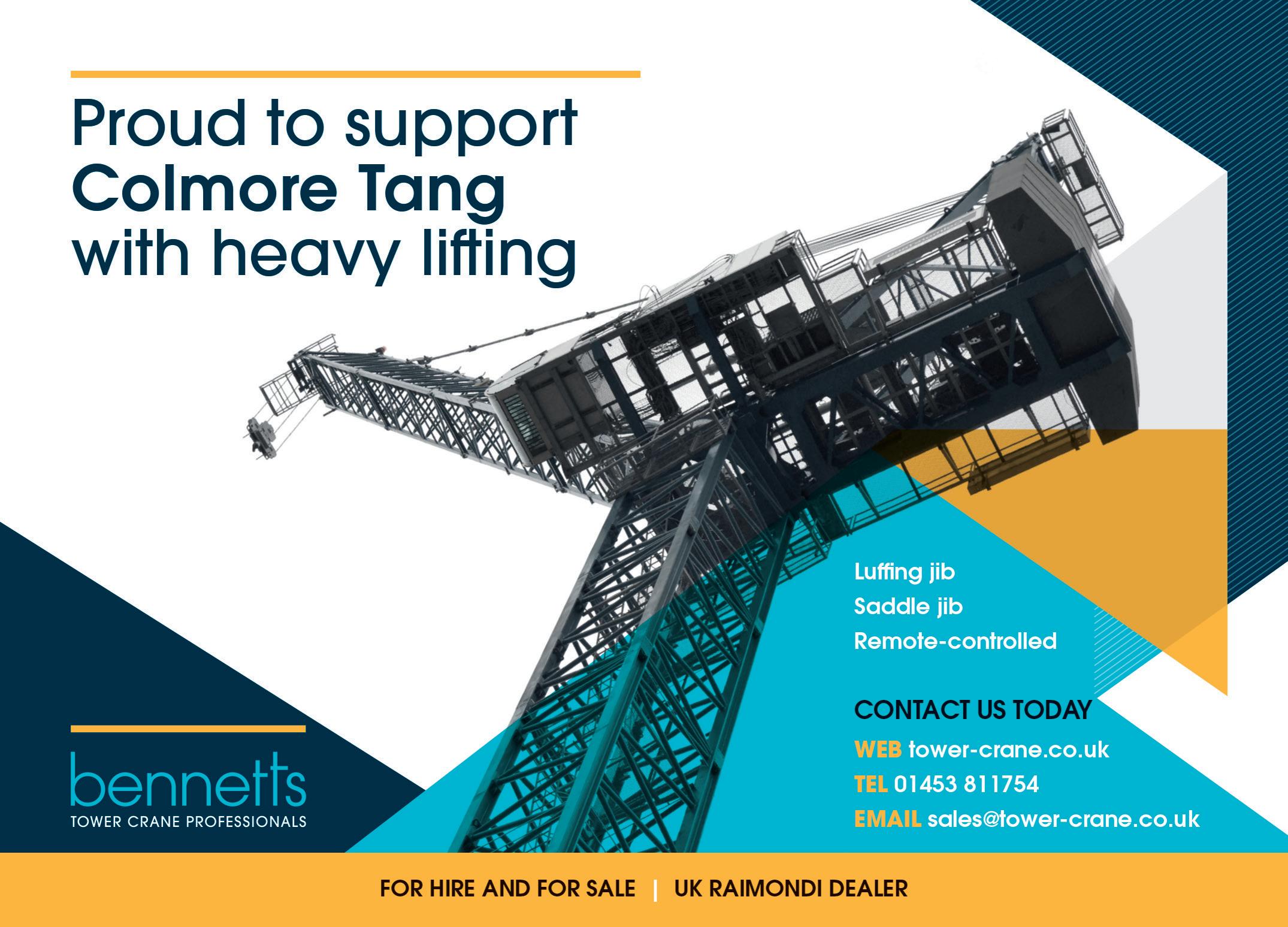
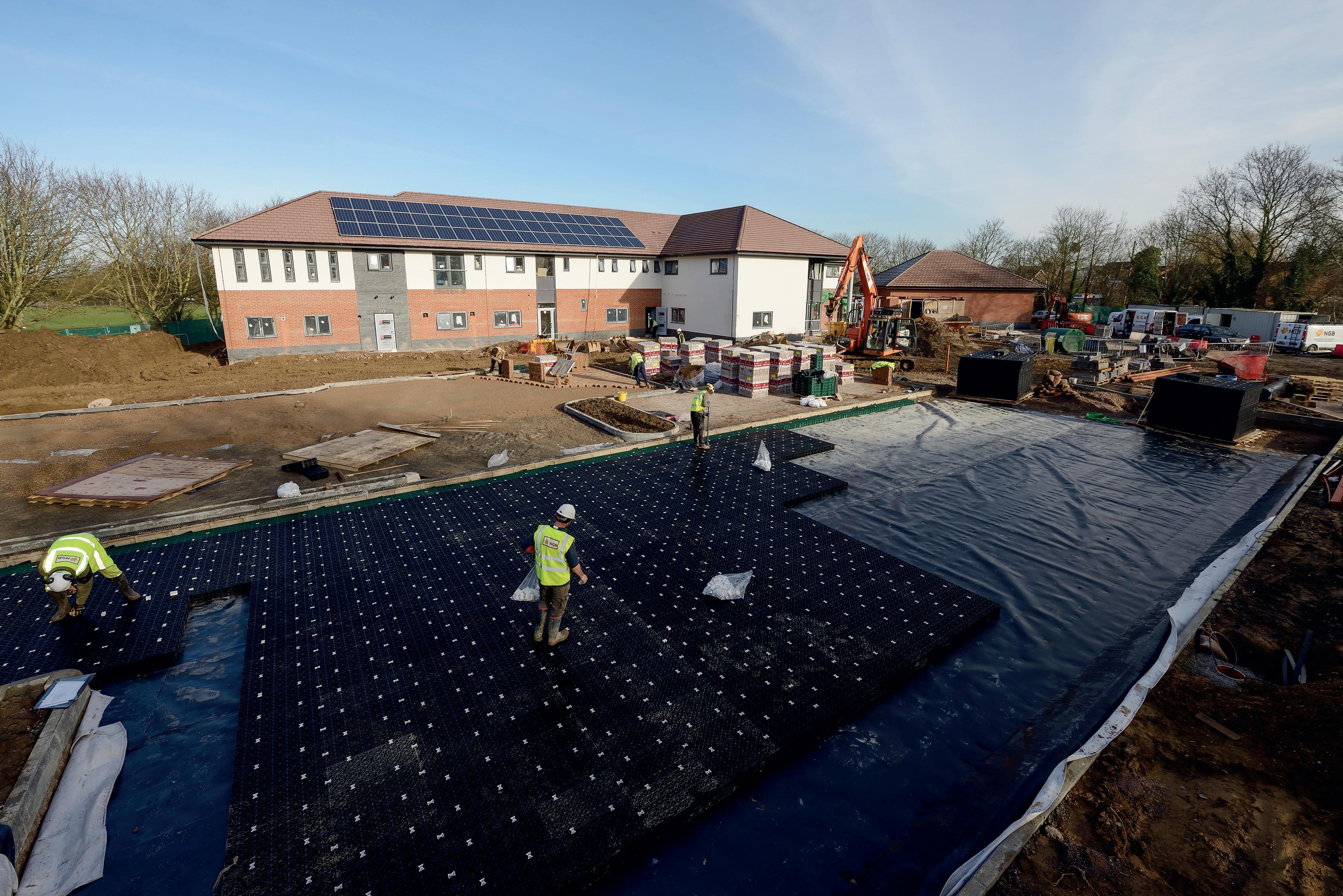
Genuine ingenuity
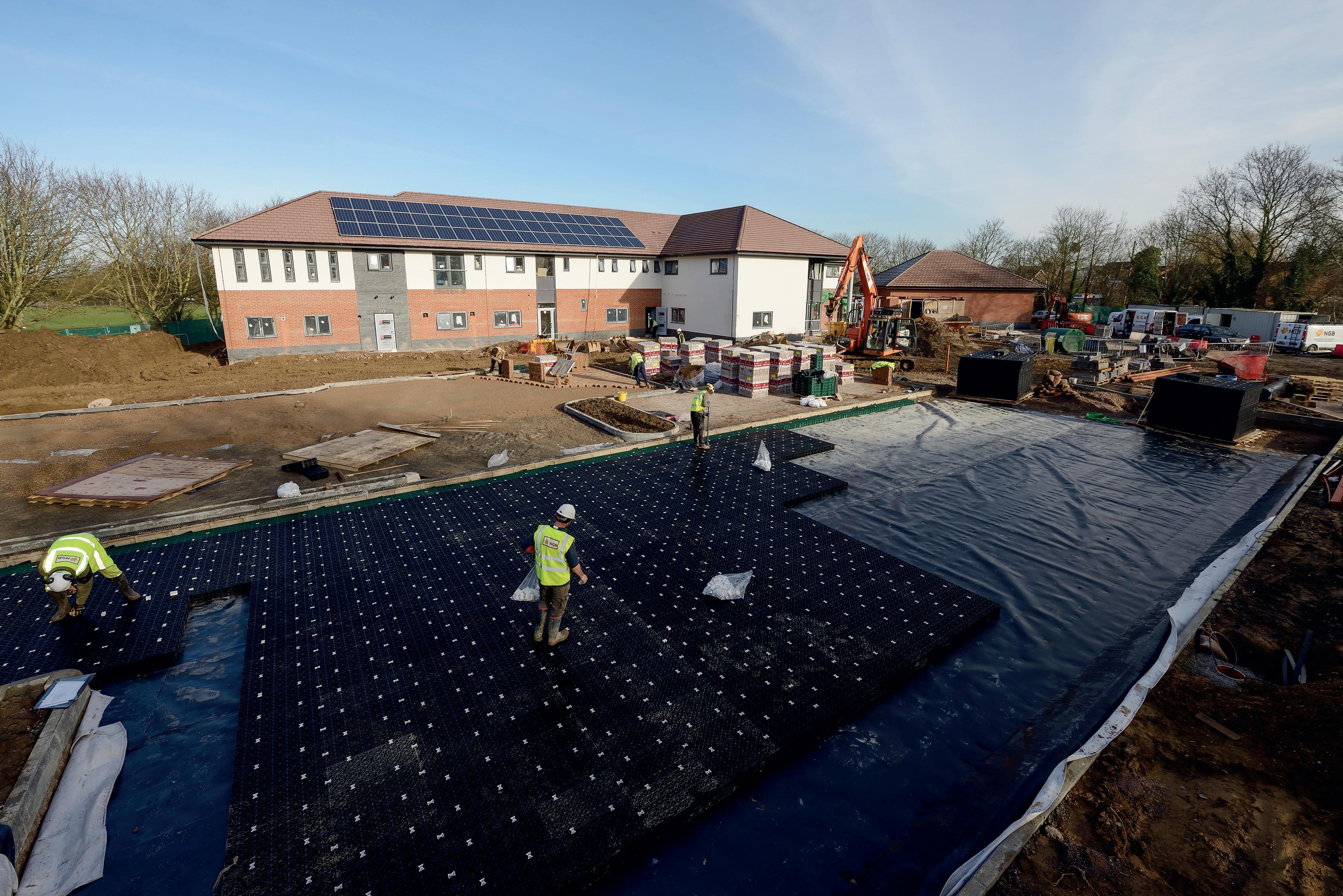
Offering 20,000 product lines, Polypipe, the UK’s largest manufacturer of solutions for heating, plumbing, drainage and ventilation, is diversifying its range and developing its sustainability credentials as it is re-branded as Genuit Group. The strong brands, including Nuaire, Alderburgh, Permavoid and of course Polypipe itself, will continue to be used as commercial brands as well as the names of some of the Group’s businesses
One of Europe’s most successful manufacturers of piping systems for the residential, commercial, civil and infrastructure sectors, Polypipe has built a tremendous reputation over the years for its market-leading sustainable water and climate management solutions. Launched in 1980s Doncaster, the business overcame humble beginnings as a manufacturer of simple drainage equipment, growing quickly into a major producer of plumbing products and an assortment of plastic goods. After a short period on the stock market, Polypipe solidified its focus on the product range it retains today – plumbing and drainage systems, building materials, underfloor heating, and, following the purchase of Nuaire in 2015, ventilation.
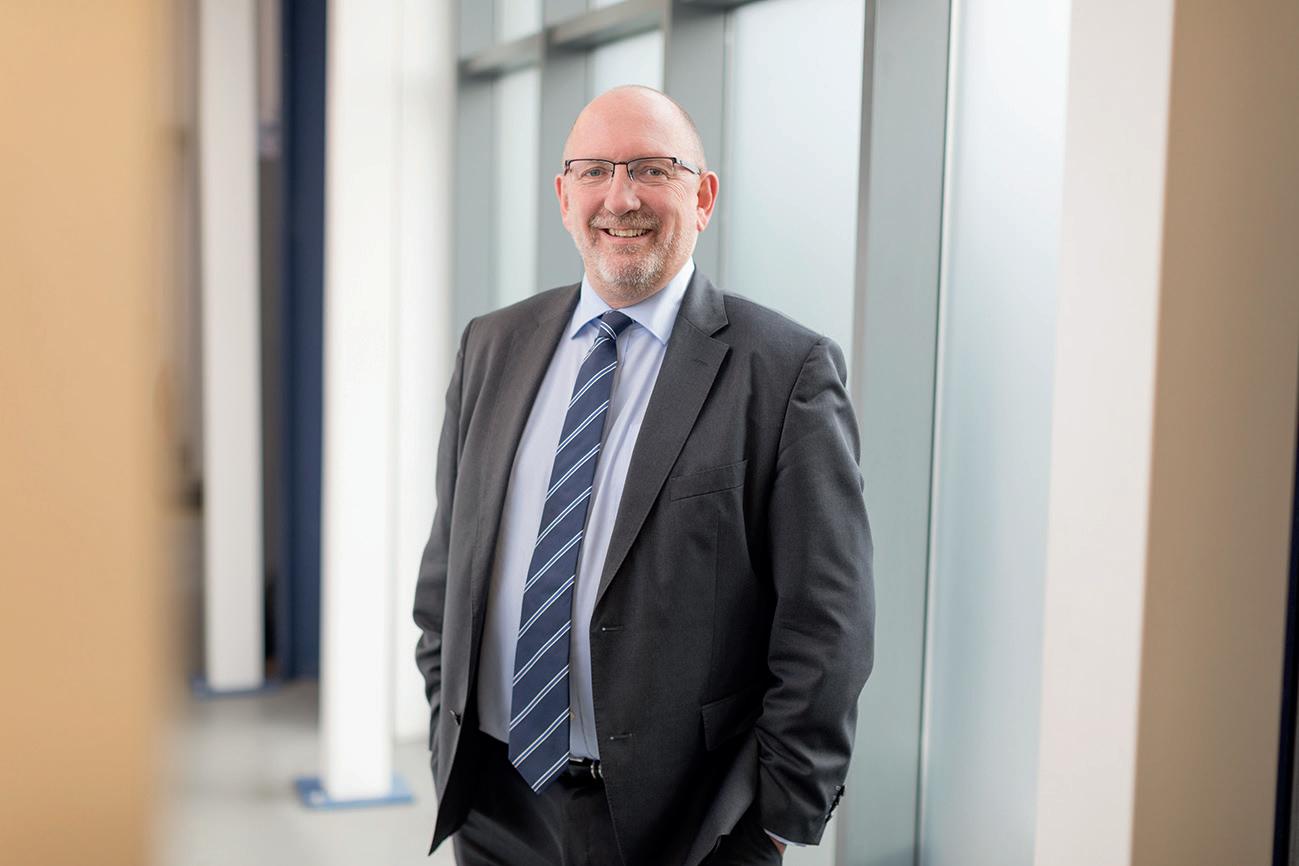
Martin Payne - CEO of Genuit Group
Martin Payne, Genuit Group’s CEO, joined the business in 2016 and has been clarifying and refreshing its growth strategy ever since. Speaking to Construction & Civil Engineering, Martin explains that good customer relationships, innovative solutions and, most importantly, strong sustainability credentials continue to drive the company forward.
“In the Group, we are, of course, involved in underfloor heating, plumbing and drainage, but if you look at the key drivers behind the business, we are trying to solve environmental issues within the water and climate management space, such as resilient drainage and flood resilience,” Martin says. “The whole concept is centred around making our built environment a greener and better place to live, so we have a whole range of solutions to help developers to do that.”
Recently, an industry-wide push for zero carbon heating in construction has resulted in an increase in activity for the Group’s ventilation business. Transmission systems that work in line with new low-carbon, low-energy heat sources are becoming more popular in the sector and Polypipe is well-positioned to deliver relevant solutions to serve the burgeoning demand.
“Even beyond the environmental factors fuelling our growth, regulatory changes within the
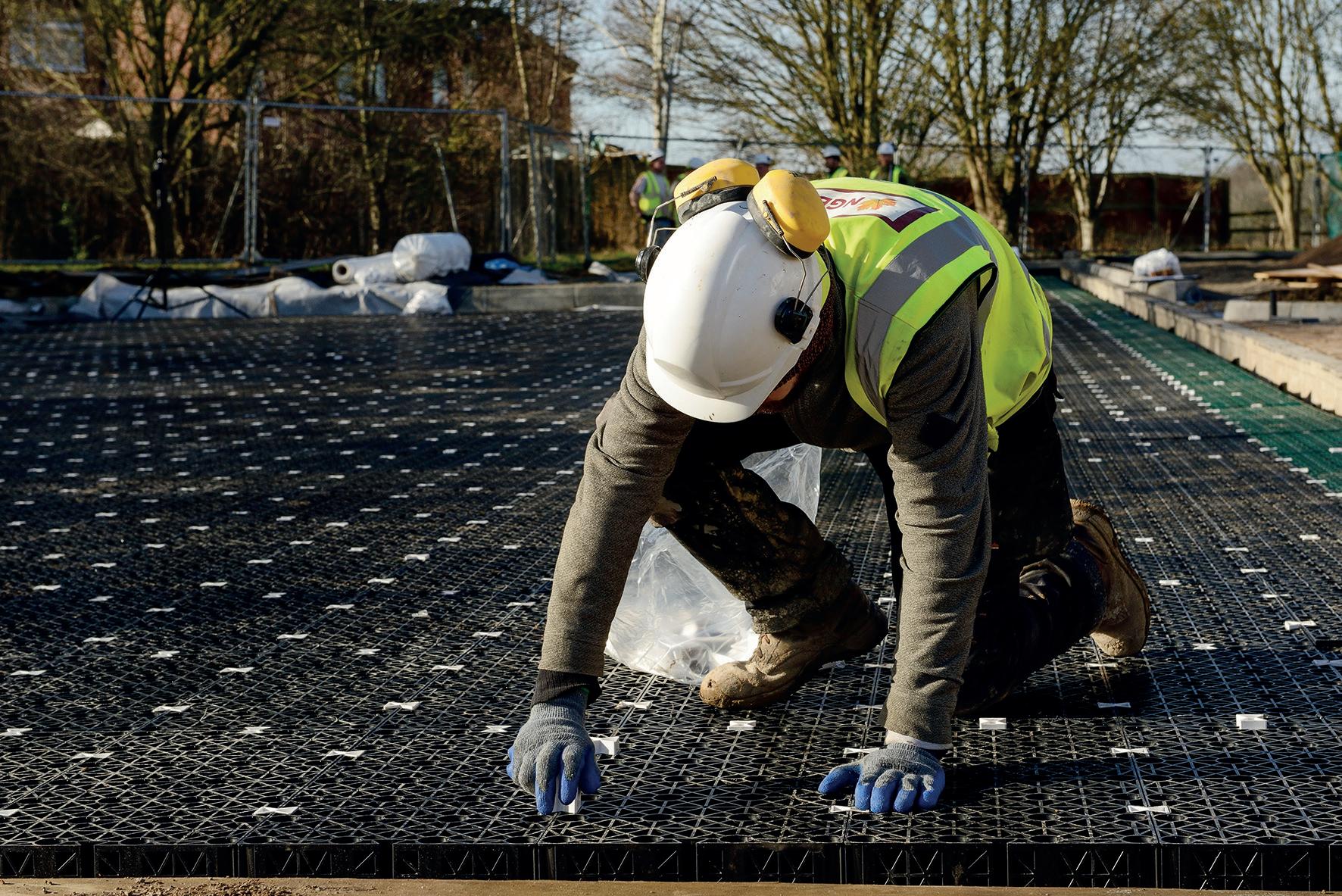
building sector are driving us forward as companies look to meet targets in terms of air quality and low carbon emissions,” Martin reports. “Technical expertise and excellence in the field make us an ideal partner in this area.”
Innovative products
One of Polypipe’s latest major projects involved the boosting of flood defences at a £2.7 million medical centre in Churchdown, Gloucestershire – an area prone to flooding. Serving 20,000 patients from the local community, the 1191 square-metre site includes and most recently, at the end of 2020, the company launched Haven. Designed to meet the specific IAQ needs of clients, while creating healthy, comfortable indoor environments, Haven ventilation products are best suited to projects with specific or demanding air quality requirements. Later this year, Martin expects the Group to add its latest Haven model to the range – SafeHaven.
“We’ve been working on SafeHaven with our ventilation business group for two or three years now,” Martin reveals.
consulting rooms, nurse treatment areas, training rooms and a large car park. Working in conjunction with EPG and NGB Cheltenham, Polypipe Civils & Green Urbanisation assessed the existing water table in the car park, which offered limited storage, and implemented solutions to ensure the sewer and drainage systems at the medical centre would not be overwhelmed, even if the area experienced high rainfall.
In terms of the company’s broader product range, Polypipe regularly introduces new and innovative solutions to its line
Impact Handling
For decades we have worked extremely close with Polypipe to fully understand their operational needs and challenges. By doing so we have been able to respond with uniquely flexible contracts and proactive solutions that support their operations where it really matters. We currently supply them with a range of Cat Lift Trucks and specialised equipment designed specifically for their application and support them with onsite engineers who proactively maintain their fleet, which means they are able to get the maximum from each truck.
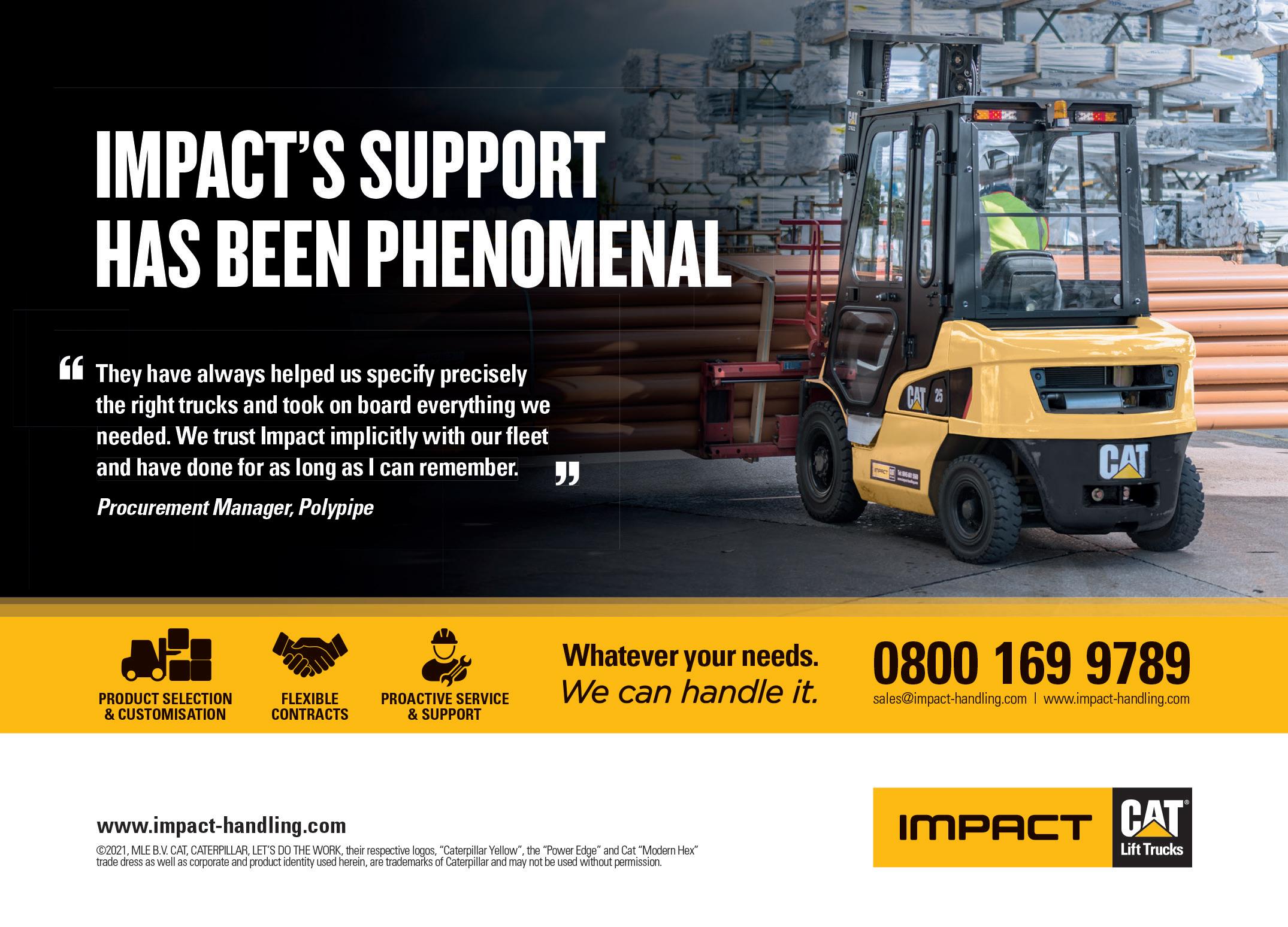
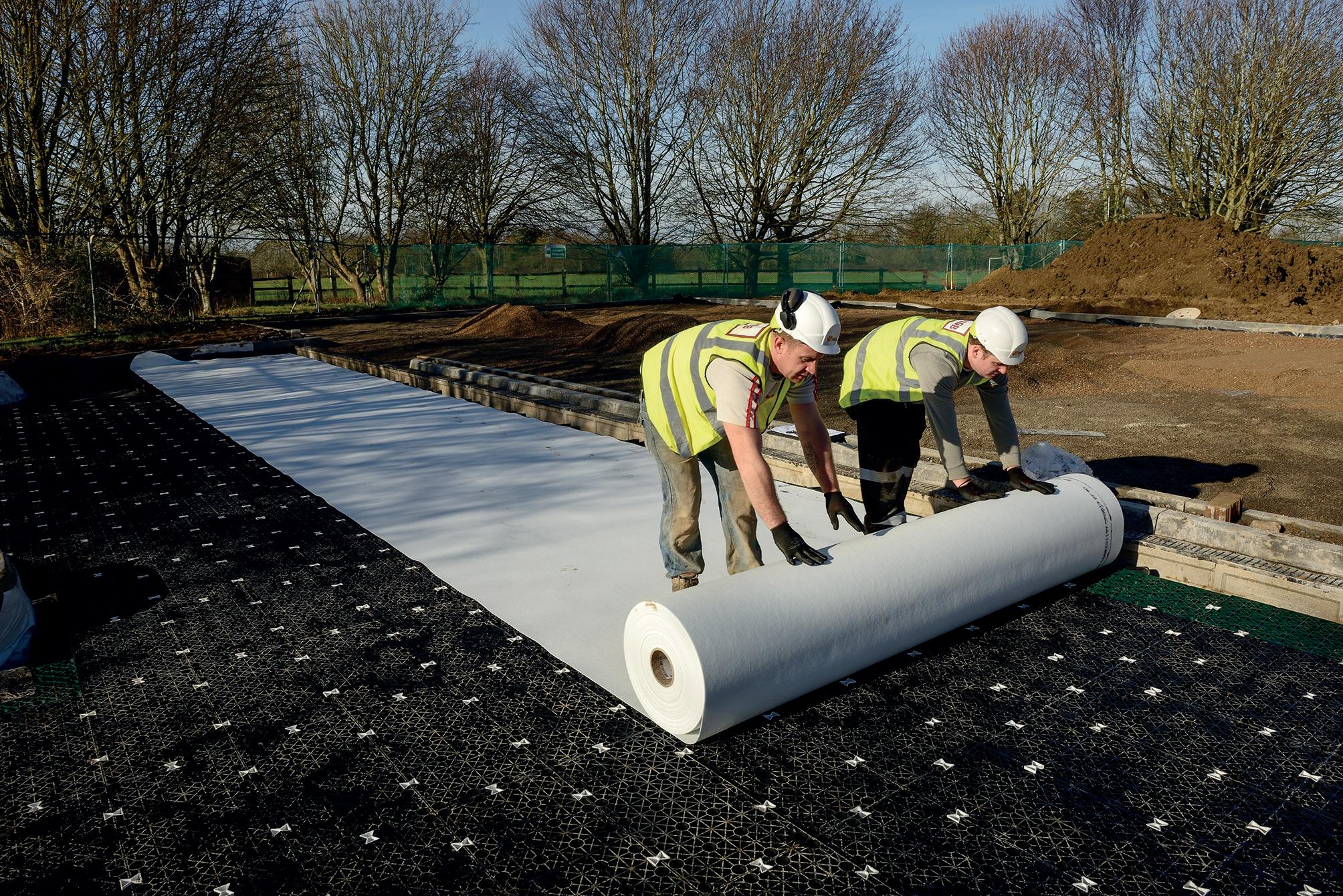
“Intended for the ventilation of high occupancy offices, schools, care facilities and NHS properties, SafeHaven protects against viruses like Covid-19 by bringing clean air into a building and then extracting it at floor level to ensure ventilation is executed from top to bottom. A lot of air conditioning units and air cleaning systems circulate air around a space, but in a Covid-19 environment that is not what you want. For safety, our system has an ultraviolet filter that can kill 95 per cent of airborne viruses, making it a very popular product with employers, education authorities and health services worried about the quality of air coming into a building.”
Critical activities
As Martin suggests, the Covid-19 pandemic has been shaping the nature of Genuit’s work of late. The virus has had an equally sizable impact on the way the business operates internally, forcing the firm’s workforce to adapt to changes and overcome numerous obstacles.
“People are the most important part of this business and so our primary objective at the onset of the Covid-19 crisis was to make sure they were safe and well. Our employees repaid our dedication by leading us to a very successful year,” Martin declares. “In 2020, we performed critical activities, such as supplying and maintaining the Nightingale Hospitals, NHS facilities, and the care sector. Whilst we did have to reduce activities in our factories, we still kept serving clients throughout the pandemic, as well as manufacturing visors for local communities in a very safe way.”
Operating from 15 manufacturing sites in the UK and a single location in Italy, Genuit has long been ahead of the curve in terms of production efficiency. Although the company has been pleased with the results of recent investment in automation and assembly improvements across its network of facilities, Martin is most proud of the Polypipe recycling plant in Horncastle, Lincolnshire.
“At Horncastle, we take 17,000 tonnes of consumer milk bottles and bleach bottles and put them through a ten-stage process, which turns them into material we can use to make sewer pipes and drainage products,” Martin states. “Over 46 per cent of
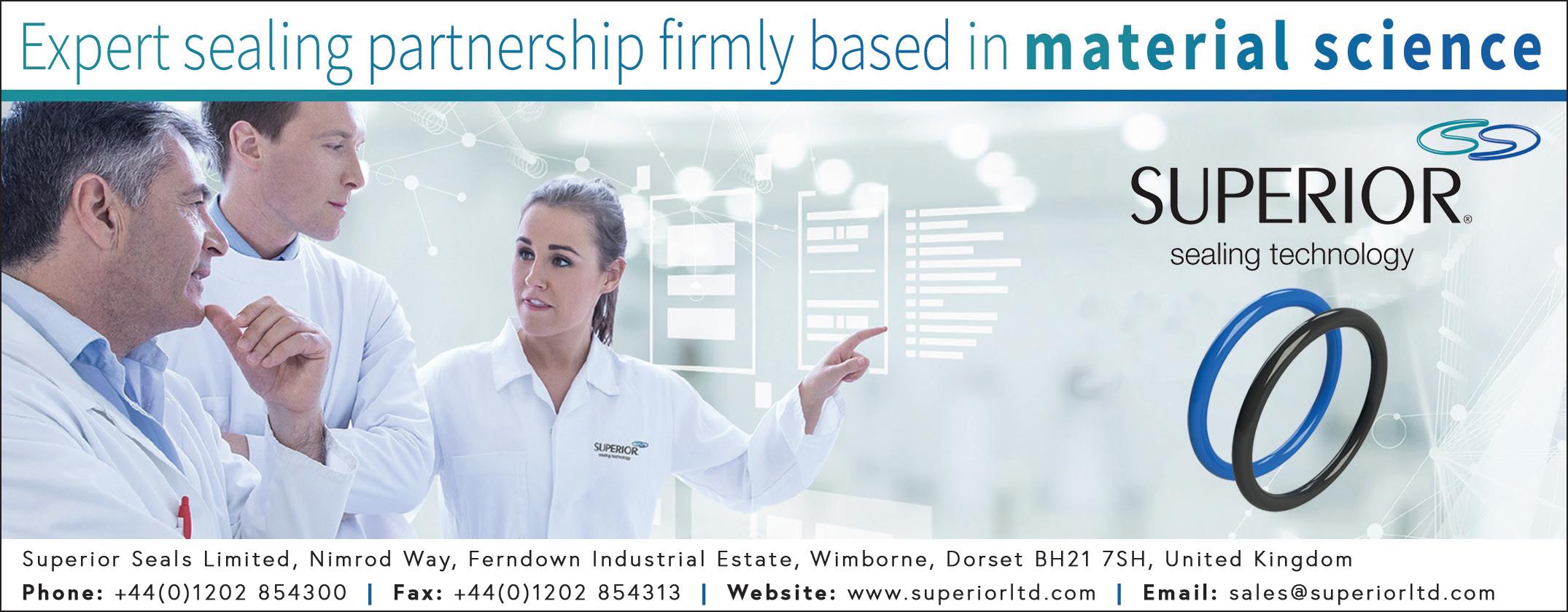
our plastic usage comes from recycled materials, which puts us way ahead of the competition. I don’t think there is another site of Horncastle’s scale doing recycling in the way that we are.
“Sustainability means an awful lot to all the stakeholders in our business - from employees to shareholders to customers. Not only is it about doing the right thing, but we are increasingly seeing a competitive advantage thanks to our recycling credentials.”
Genuit Group’s commitment to sustainable practices has seen the company sign up to the Race to Zero emission reduction scheme and the firm is joining many of its clients in driving progress across Scopes 1, 2 and 3. The focus on emission reduction sits alongside similar recycling, innovation and workforce-related targets. For example, regarding the latter, Martin would like to see five per cent of Polypipe’s workforce in education, whether through apprenticeships, graduate schemes or on-the-job learning.
In 2021, the Group is a very different, and far more varied, organisation than when it opened its doors as Polypipe in 1980. No longer a simple
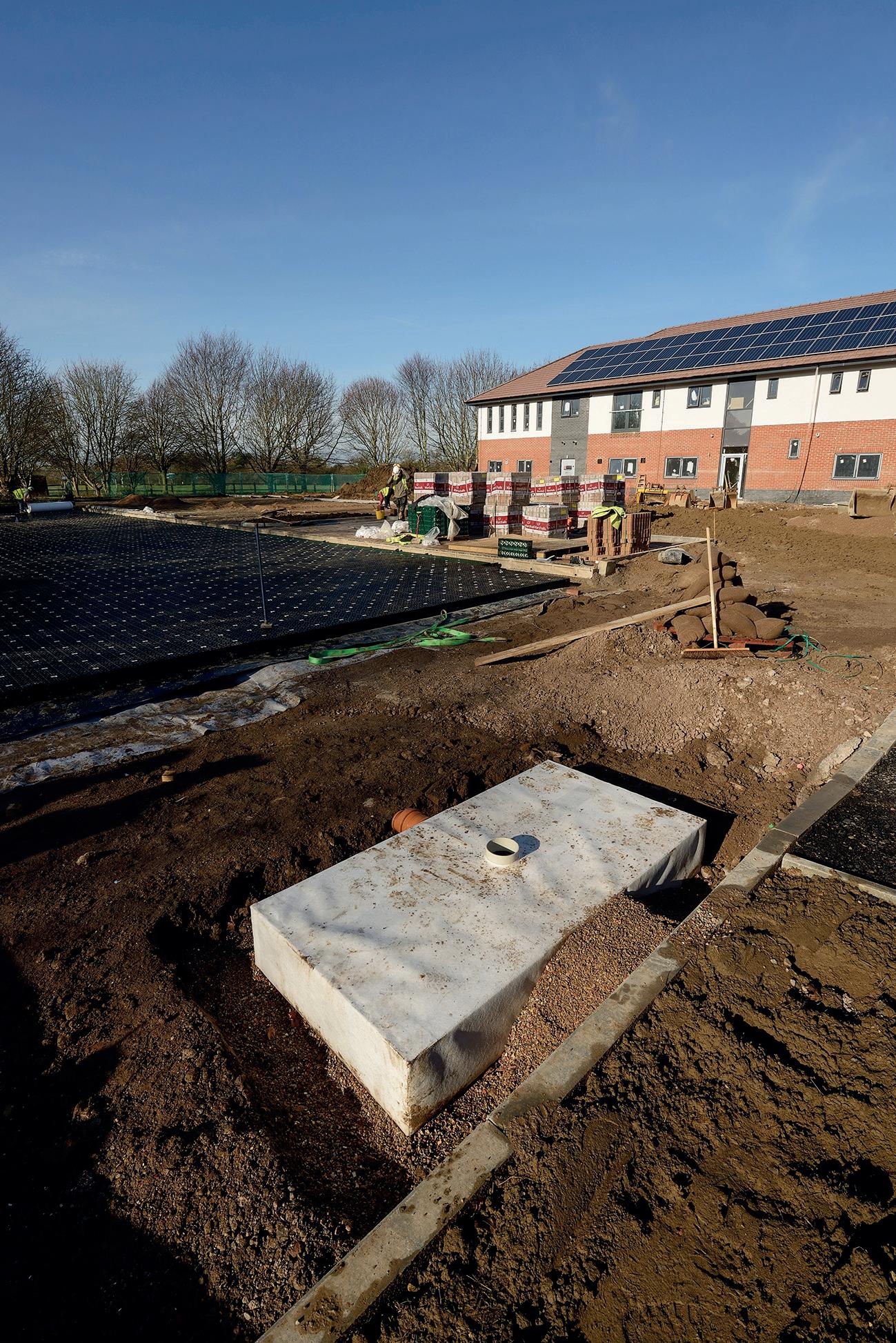
Veolia
Veolia are a world leader in environmental solutions. We have over 50 years of experience and expertise in manufacturing high quality recycled polypropylene (rPP) and have been supplying Polypipe for over ten years. Our versatile and sustainable compounds are engineered to last a lifetime. They naturally find their place in the green urbanization offering of Polypipe contributing to deliver sustainable management of surface water. Through continuous innovation and improvement processes, together with our customers, we co-develop solutions which help them reduce their carbon footprint.
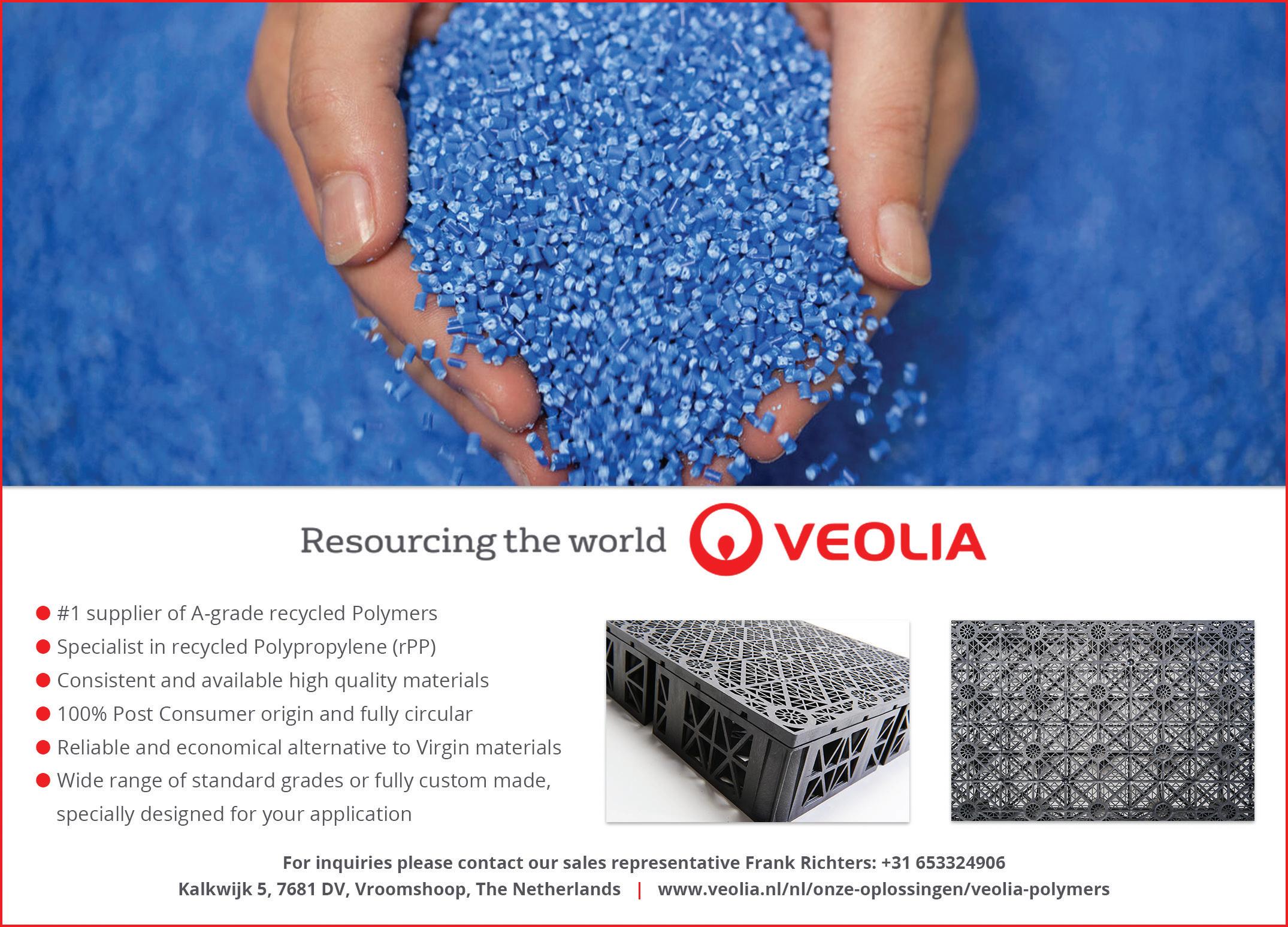
manufacturer for the plumbing and drainage industry, the company has developed into a leading solution provider for real world environmental issues, with the ability to deliver specialist products as varied as integrated heat pumps and magnetic to feel part of the group, while maintaining an affinity to our customer base and brand,” Martin remarks. “We asked our workforce what they thought best described the culture at Polypipe and the word ‘ingenuity’ came up over and over again. It sums up our approach to problem solving and solution development, and that’s why we decided on ‘Genuit’, as a variation of ‘ingenuity’.
“To be clear, the customerfacing Polypipe brand itself will not change, but our new acquisitions will join Polypipe under the Genuit Group umbrella,” Martin adds. “We have had six acquisitions in the last three years, and we now have a portfolio of very strong brands in their own right. Nuaire is the number one light commercial ventilation business in the UK, ADEY is the number one magnetic filtration and chemical treatment firm for water-based transmission systems and heating, and they sit alongside a whole range of complementary companies.”
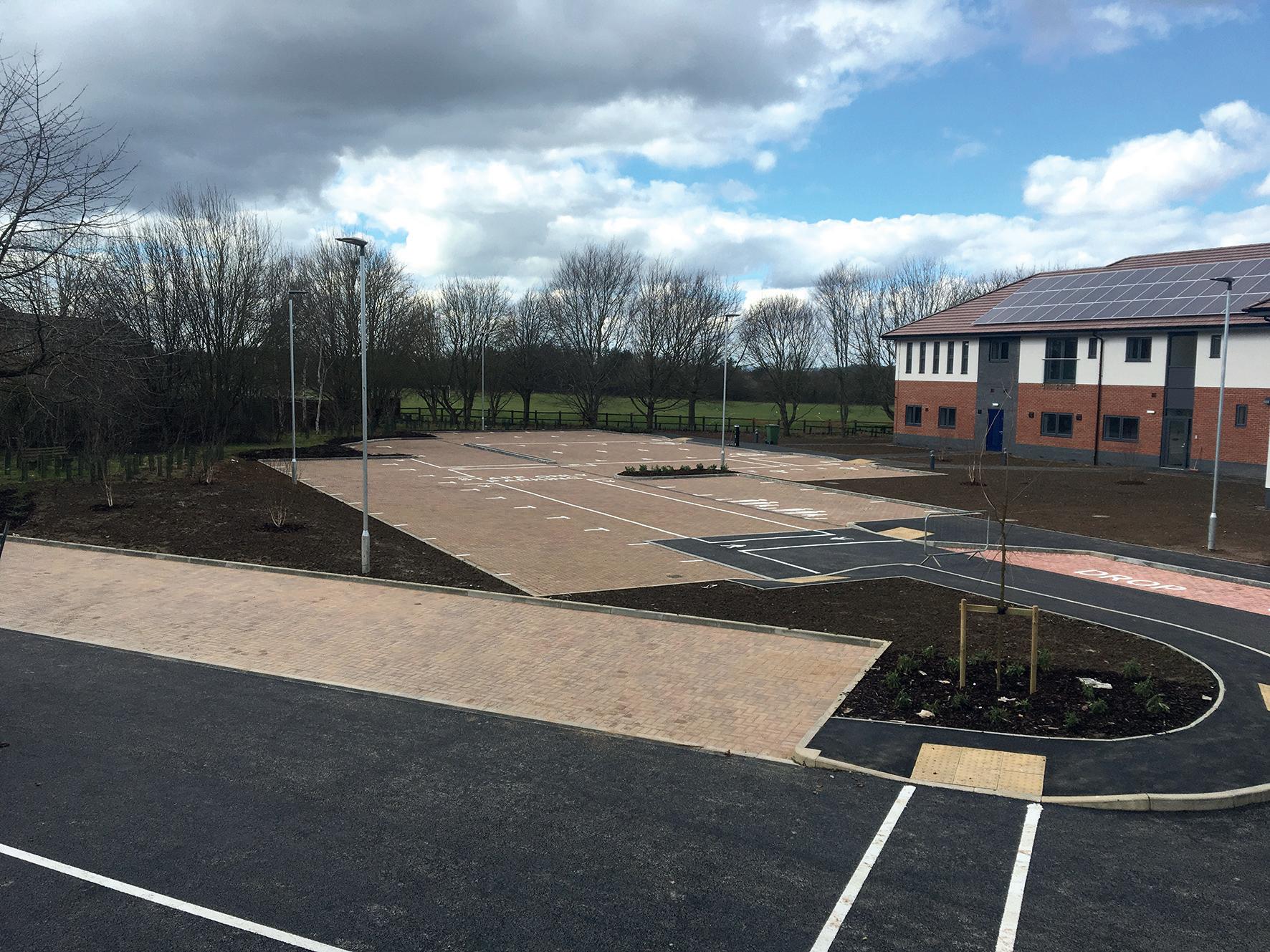
filtration. To reflect this growing sophistication and increasingly diverse offering, as of April 6th 2021, Polypipe’s parent company, the Polypipe Group, will now be known as the Genuit Group.
“We were looking for a name that allowed all our employees
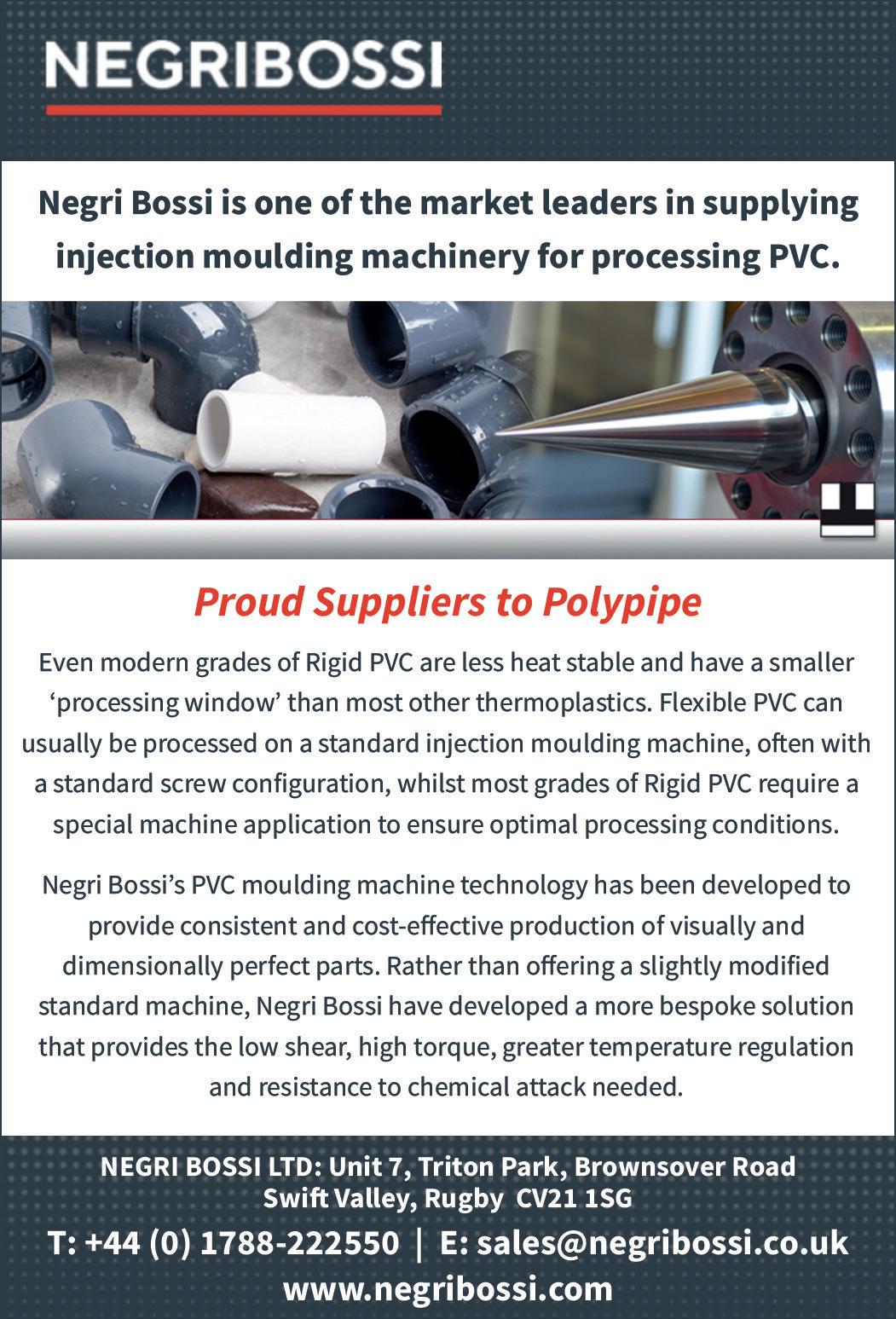
Key drivers
As the number one plumbing and drainage company in the UK, Polypipe will continue to receive substantial investment from the Genuit Group in 2021. The company will also be joined in the group by Genuit’s latest acquisitions, which include Plura and Nu-Heat. With Covid-19 vaccination programs starting to prove successful around the world, Martin and his team at Polypipe finally feel as though they can start focusing on the company’s long-term future.
“Resilient drainage, green urbanisation, healthy air and zero carbon heating within the residential and commercial sector are going to be key drivers for us in the months and years ahead. We are very lucky to be operating in some really strong markets at the moment,” Martin points out. “Our post-Covid-19 world is
likely to have a structural housing shortage, which bodes well for the group, and I would like to see the business continue to grow both organically and through acquisition.
“Despite the challenges of Covid-19, we were able to invest in new products in 2020 and we expect to see that pipeline come to fruition over the next few years, which is very exciting. As a business, we will continue to align ourselves with environmental and regulatory drivers, whilst operating
Baerlocher UK
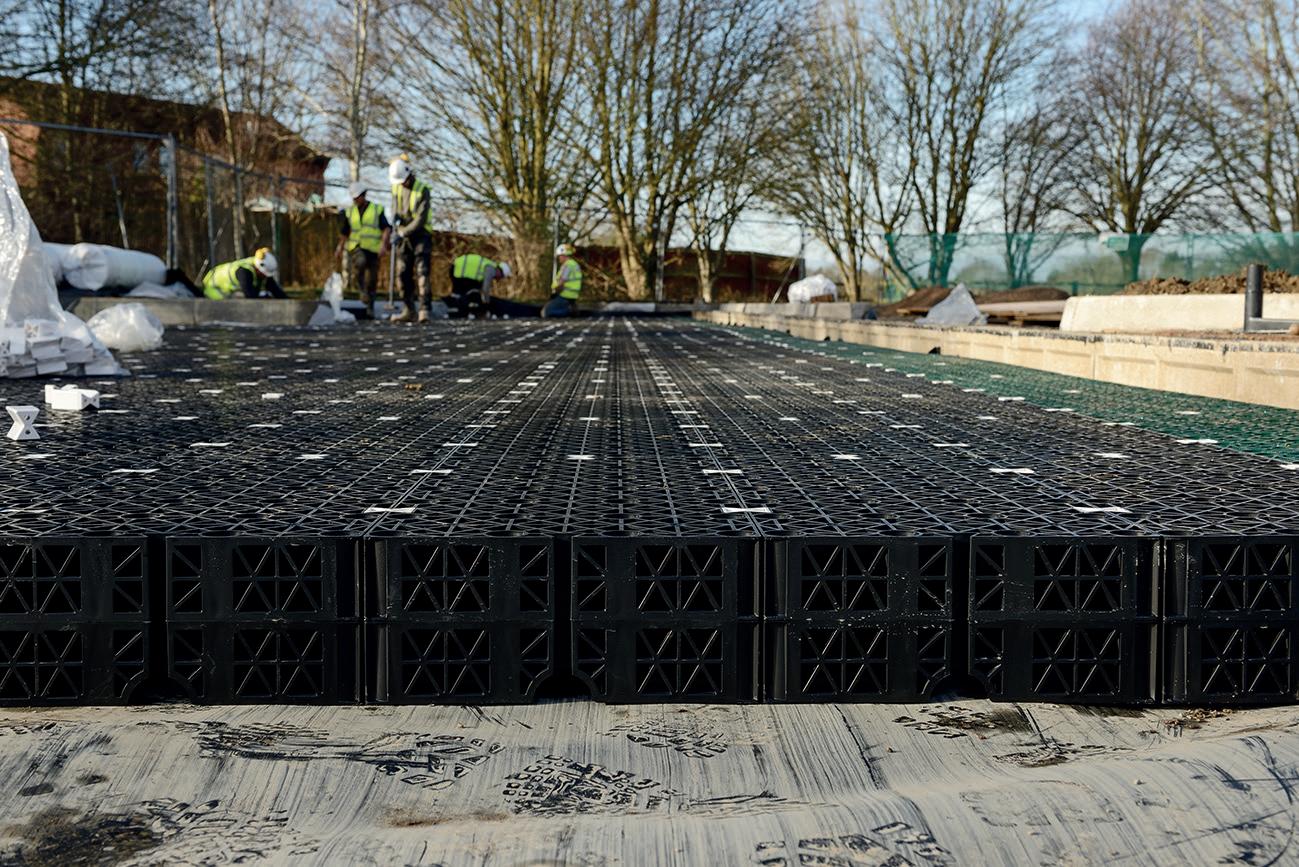
as a sustainable business ourselves in line with targets we laid out in November 2020 regarding carbon reduction, plastic recycling, digital innovation and the development of people.”
Baerlocher UK are proud to be the major supplier of PVC stabiliser solutions to the Polypipe group. Our longstanding co-operation has been invaluable to the development of improvements in cost performance, processing, output, and product design. Our close working relationship over decades has resulted in a partnership where development ideas from both companies can be brought through the trial phases and on to full production smoothly and quickly. Baerlocher are the world’s leading PVC additive supplier and we pride ourselves on our service and delivery performance in challenging technical markets, forging partnerships up and down the supply chain to generate state-of-the-art formulation solutions to the industry.
Polypipe www.genuitgroup.com
Services: Piping systems and commercial building services
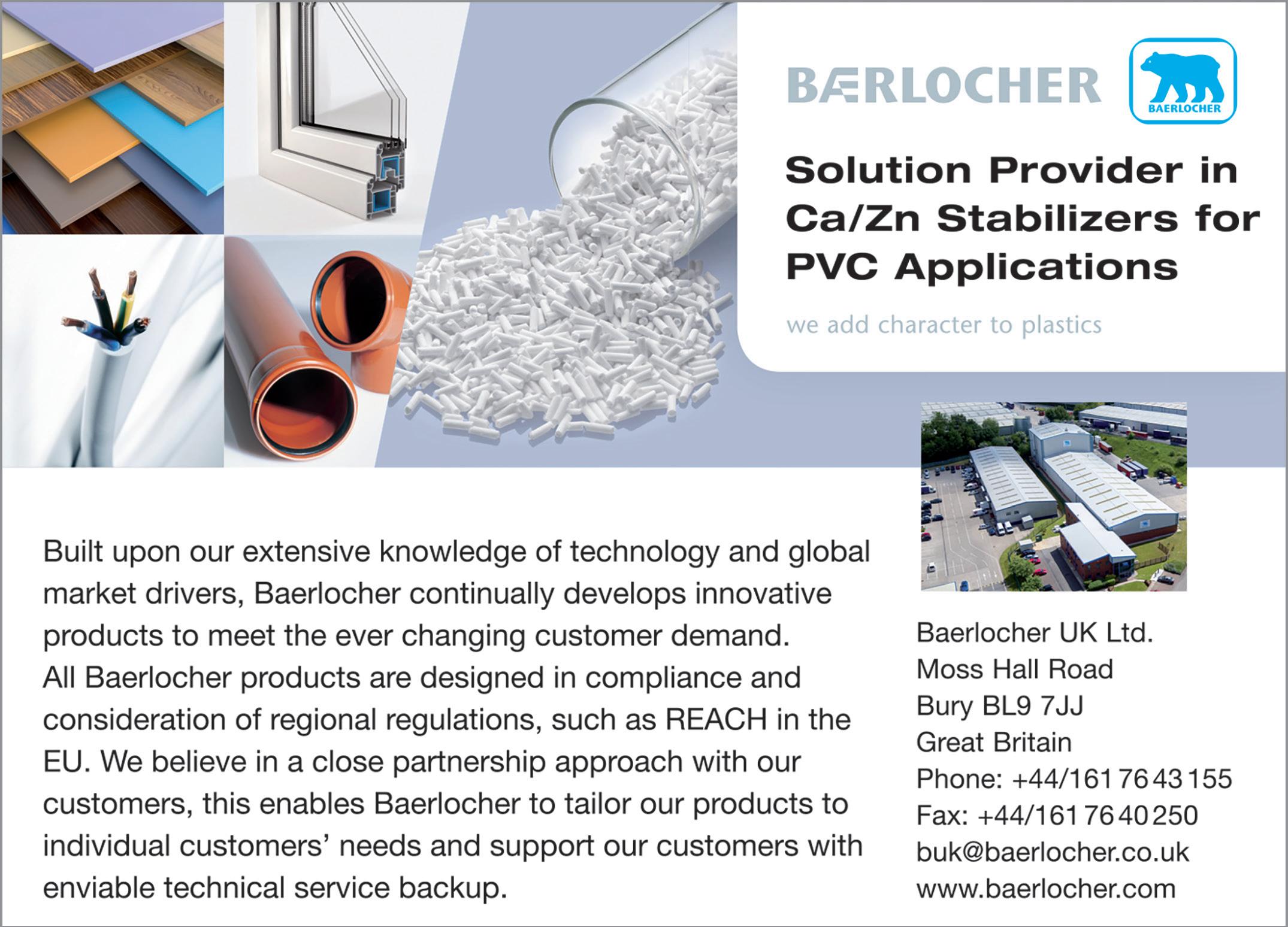
Incorporated in July 2002, Traditional Brick & Stone (TBS) is a privately owned independent company, proud of its commitment to providing its customers with a quality product and excellent levels of service. Headquartered in Rugeley, Staffordshire, and with distribution centers located in Tilbury, Harwich, Hull and Belfast, the company is owned by Daniel Sims and Trevor Robinson.
“At the time leading up to us forming TBS, we were actually
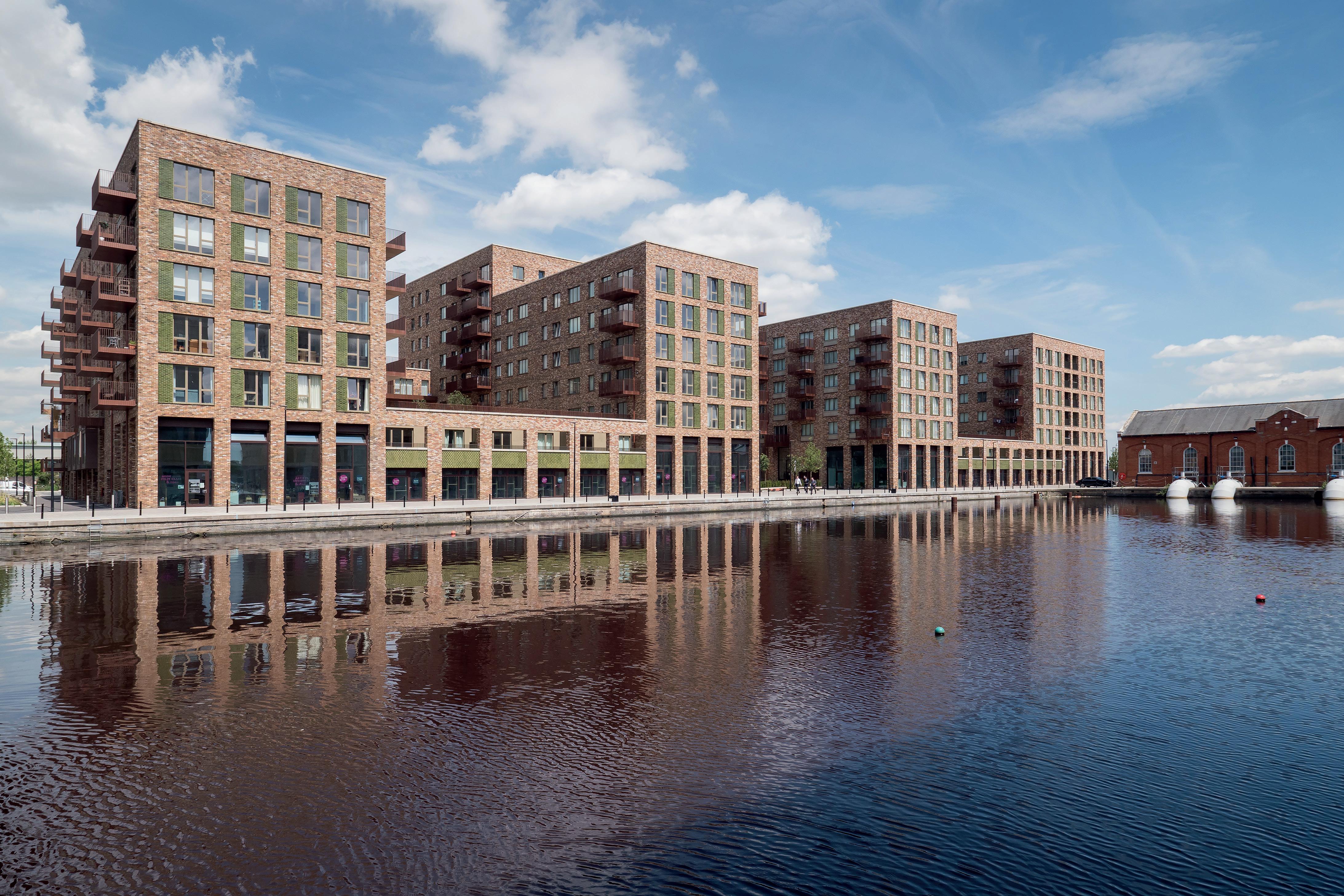
Blocks of success
With an extensive, unique product portfolio, and a national network of sales representatives, Traditional Brick & Stone (TBS) provides a service that its customers know that they can trust
working for what is now a competitor of ours in the brick importing sector,” Daniel – Joint Founder and Director of TBS – explains. “It was our opinion that this particular company was sticking far too rigidly to its existing product portfolio and approach, and lacked the vision and willingness to listen or to see
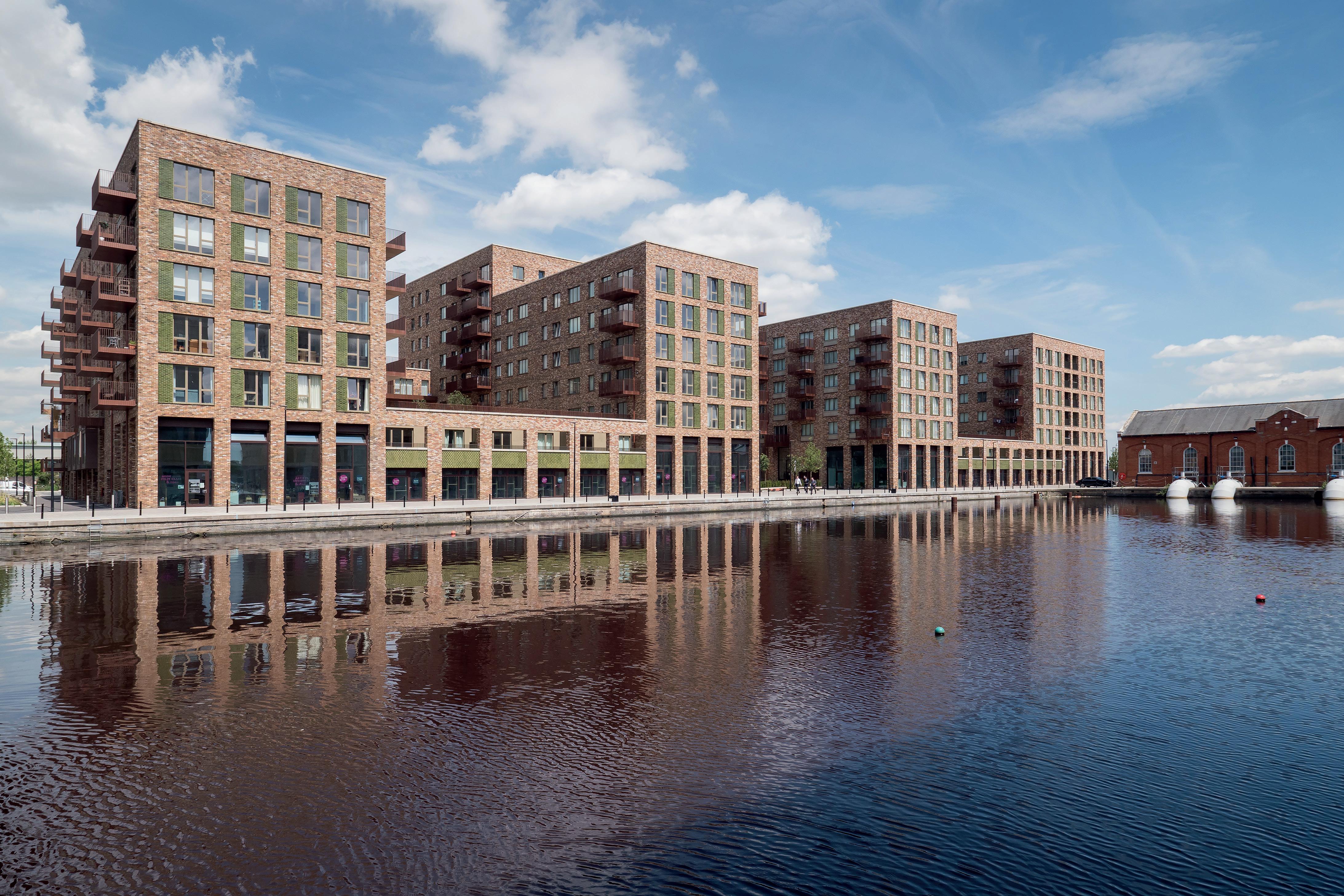
Photography by Alex Upton
where new market trends were heading. Indeed, we felt that there was much more that a business could offer UK specifiers and designers, and so we decided
Photography by Robert Greshoff

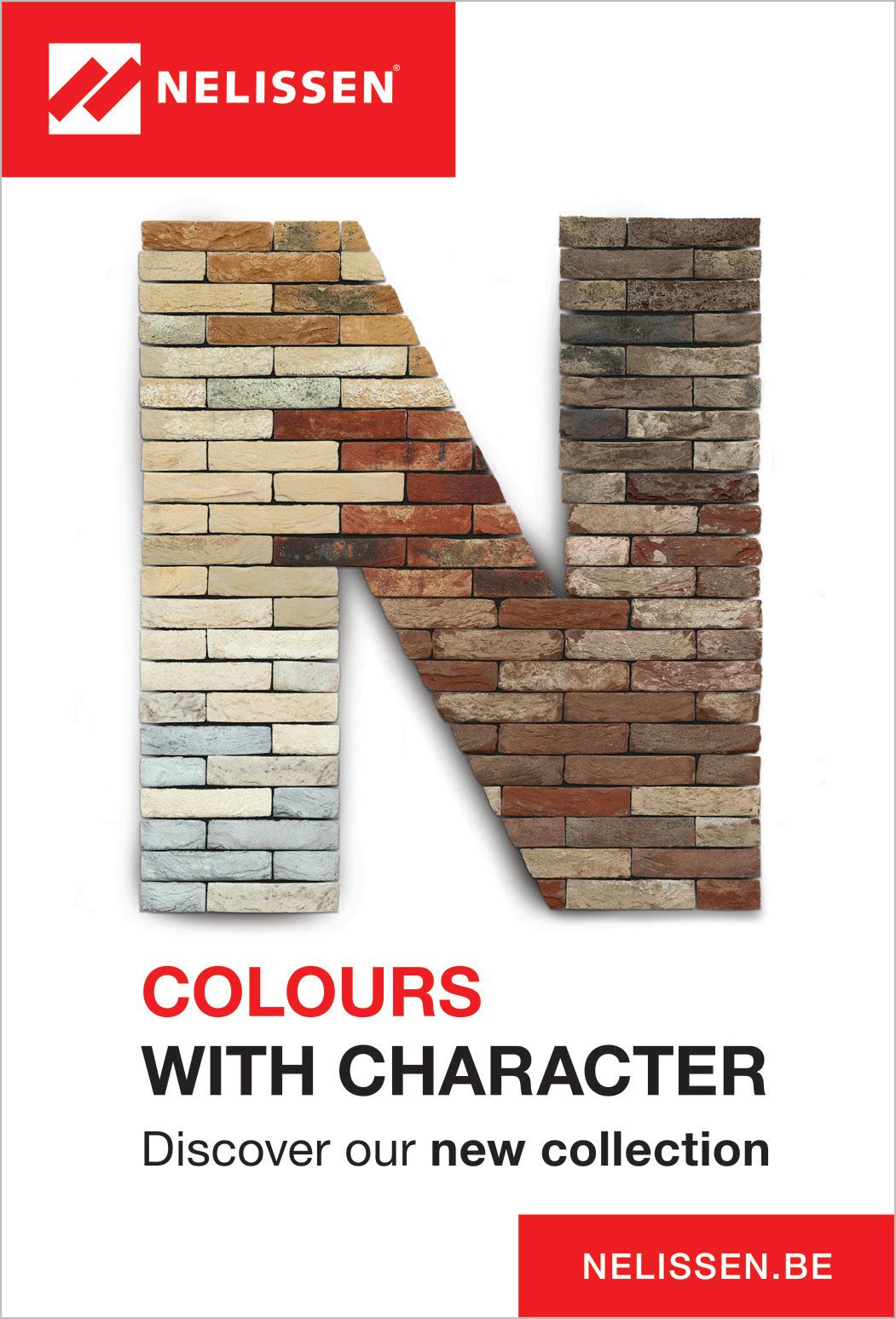
to start TBS and began to put together our own portfolio of brick and stone products, which we could add to or modify as time and trends dictated.”
Customer choice
TBS’ main product lines can be split into three categories – bricks, pavers and cast stone – but it is arguably best known for its range of quality facing bricks of varying textures. The company has even gone so far as to create an inhouse facility to pre-blend bespoke mixtures to customer orders. “One thing that you hear us repeating on numerous occasions is that we pride ourselves in our ability to listen to what the market and our customers want,” Daniel continues, “and what specifiers want today is the ability to create something unique with their brickwork. By providing bespoke blends made up of different textures, colours and sizes, we are doing what the majority of our peers do not, and that is offering our customers a choice.”
The TBS team has always believed that the most effective strategy for achieving long-term success is to impress the customer at every opportunity, an ethos that Daniel expands upon. “This can encompass everything from the quality of our products and services, to the ability of our people to respond to individual needs or queries. Graham Boyd – our Sales Director – runs our business strategy as it relates to the sale of our products and/ or services, and he has given our people the ability and trust to be decision makers in their own right, which helps the customer to arrive at a solution to their requirements quickly and effectively.”
Graham joined TBS in October 2018, and what immediately appealed to him was how open and transparent the company is in the way it operates, the impressive range of products on offer, and the positive attitude of its people.
“One of the things I would say we pride ourselves on being is what I like to call a ‘large-small business’, by which I mean, while we boast an impressively large product range, we still retain a high degree of flexibility and speed of response, which is fundamentally due to the fact that we empower our colleagues to make quick decisions and encourage them to be entrepreneurial at every opportunity,” Graham adds.
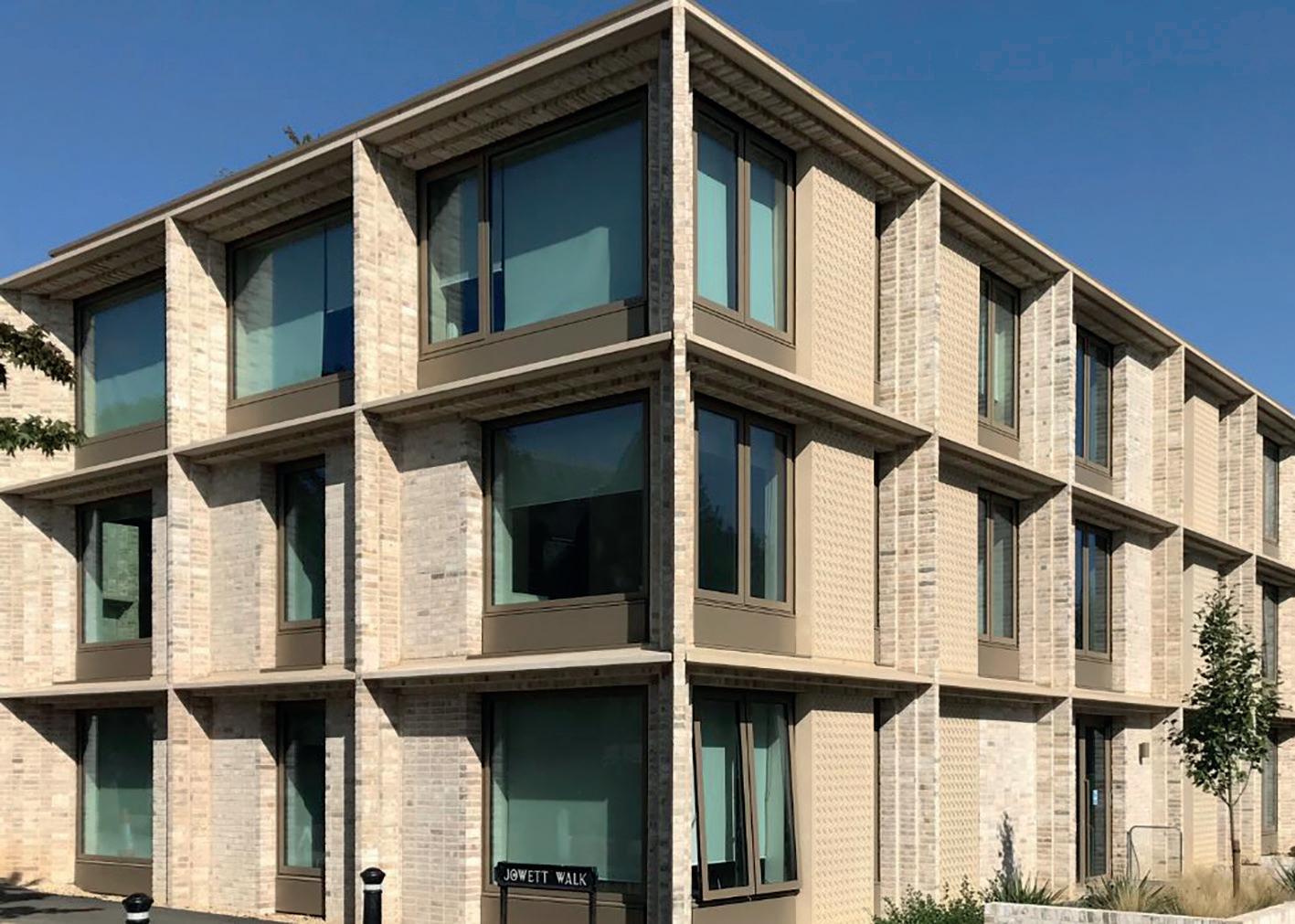
Quality & consistency
Selling through its distribution partners, TBS’ products are valued by all manner of customers, from architects, engineers and specifiers, to house and high-rise builders in some of the UK’s major cities. In recent times, the company has found itself increasingly working
Steenfabriek Klinkers
From the cradle to a fullgrown business and respectful partnership Steenfabriek Klinkers has been a partner of Traditional Brick & Stone (TBS) since the start of their company. Together we have managed this partnership to grow and have completed a lot of beautiful projects and family houses in the UK. The TBS team works with their clients and architects and is continuously searching for new blends or tailor-made solutions to an existing build. This approach is a perfect match for us and we aim to continue this relationship with the TBS team and its founders for a long time.
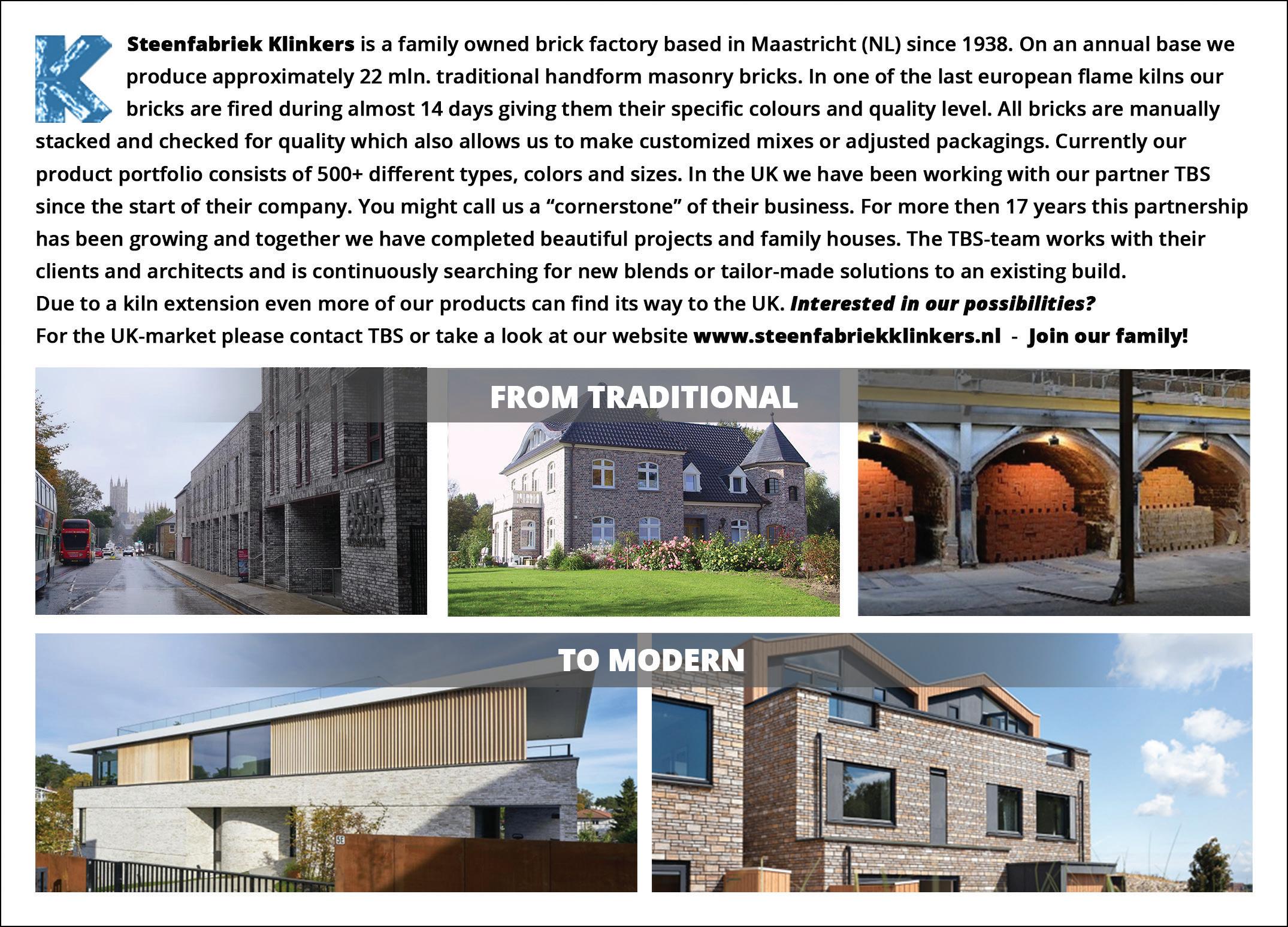
with customers specialising in areas such as precast, offsite construction, and individual highspec projects. Said customers are among the many beneficiaries of the fact that TBS will produce as many as 600,000 bricks in a single firing, whereas many of its contemporaries in the industry will take two-to-three runs to produce a similar amount.
“Making so many bricks in one firing helps us to ensure consistency of quality when it comes to our production processes,” Graham continues. “We also now have a dedicated specialist fabrication facility where we carry our activities such as brick cutting, and we also ensure that we pre-blend our slips and pistols for precasting, to avoid any potential issues such as colour changes. We are also very much into linear products today as well. TBS offers a range of 40mm and 50mm linear bricks in a 240mm format, and these are very much in demand amongst architects these days, especially those looking to do innovative things with bricks such as stack bonding or creating particularly unique patterns.”
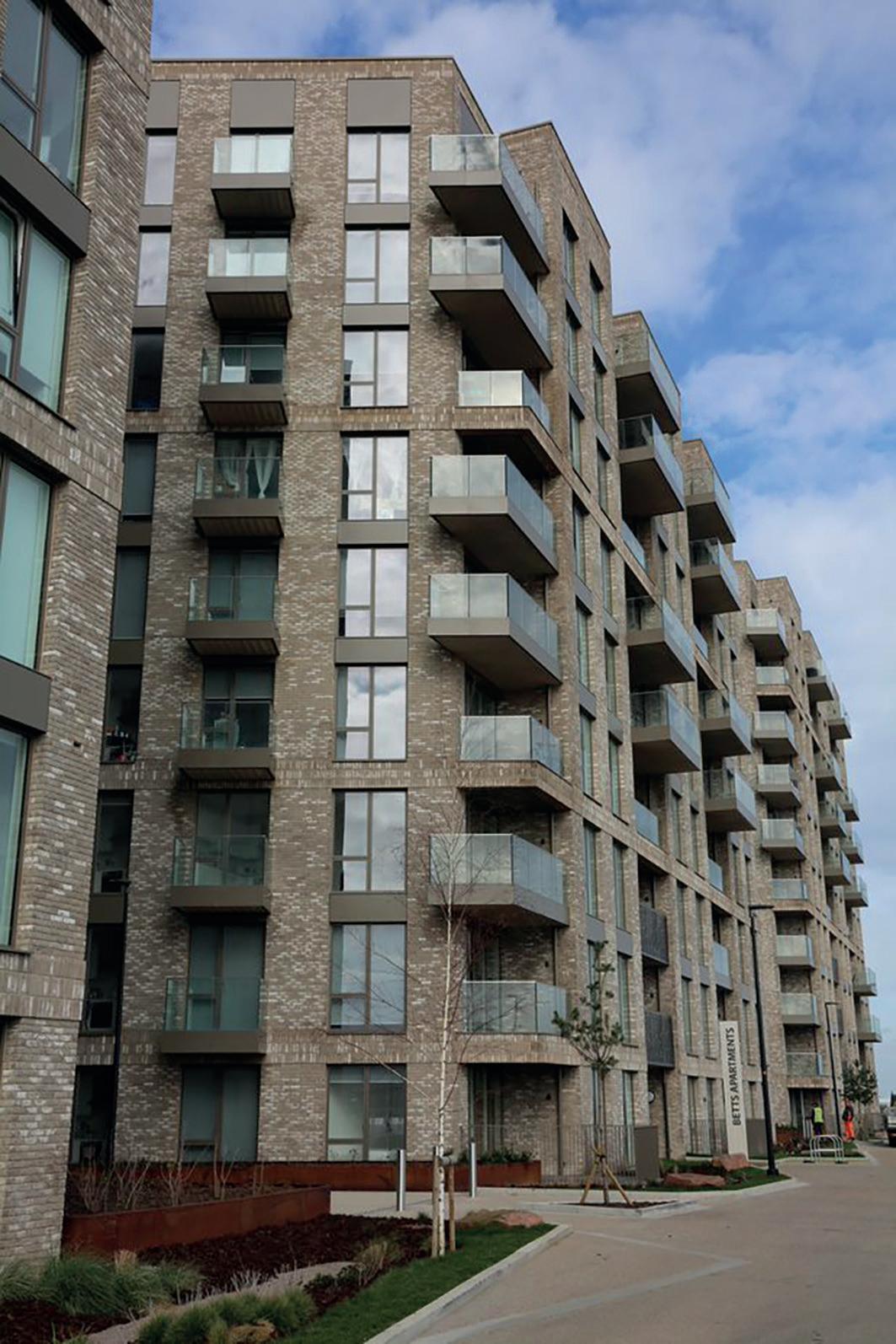
Photography by Robert Greshoff
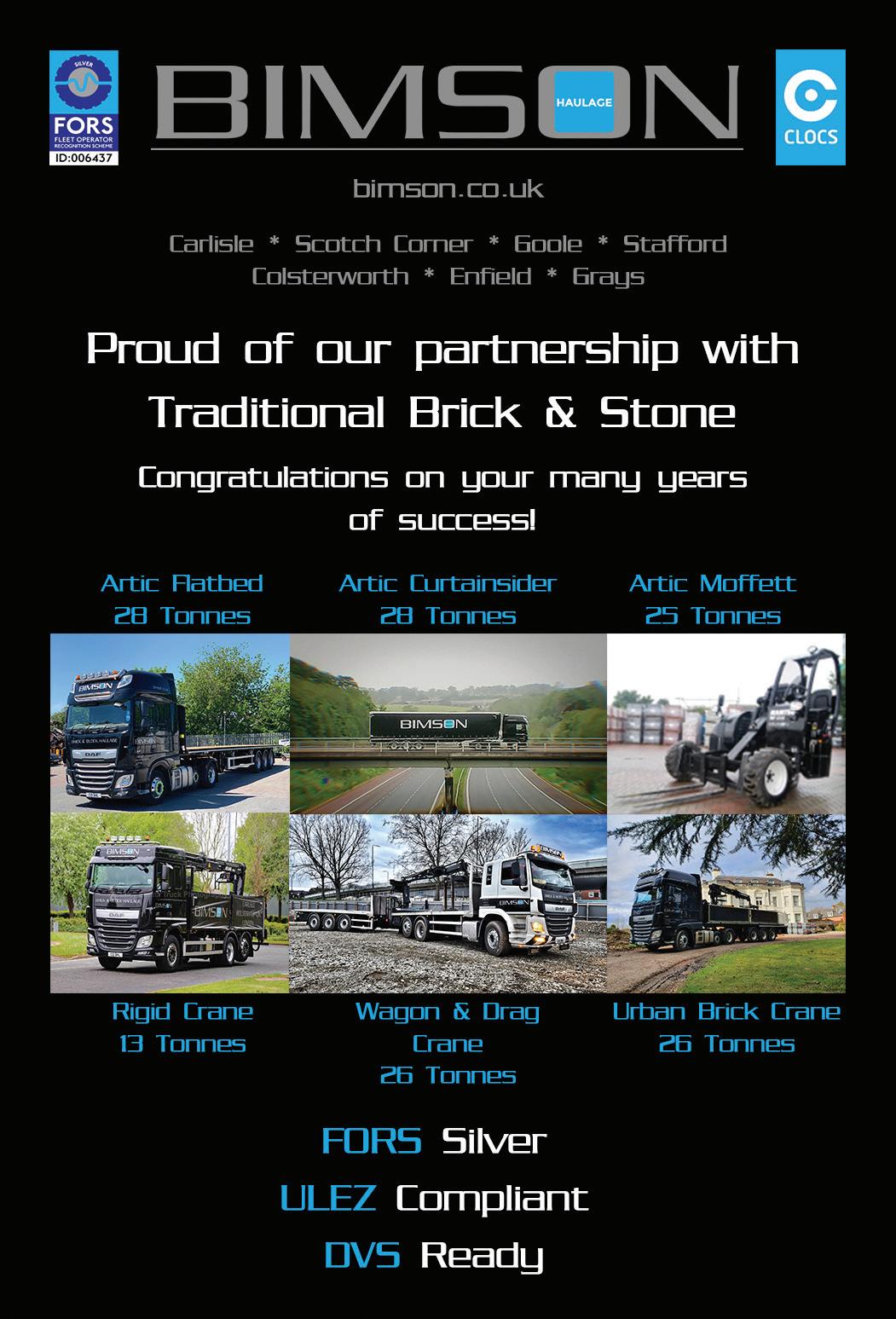
New offerings
Another area that the business is making further inroads into concerns smoked bricks. “We have recently been linked with a supplier that has a new method of smoking the bricks so that it takes the oxygen out of the kiln, creating a very different appearance altogether,” Dan states. “Smoked bricks are very much a niche market – which makes up a small percentage of our overall business – but it is something that specifiers and architects are becoming more and more interested in, and servicing the wants, needs and requirements of our customer network is what we are all about!”
TBS is also in a unique position in that virtually everything that it offers it imports into the UK. This naturally posed a potentially significant challenge when Brexit was taking center stage and the UK was negotiating its leaving of the European Union. Thankfully, as a result of a tremendous amount of planning and work, disruption has been kept to a minimum since the UK’s transition period ended at the turn of the year. “Due to the amount of time, energy and preparation work that has gone into the last couple of years, we have emerged into a post-Brexit world with our eyes firmly fixed on the future and the growth opportunities that we anticipate coming our way,” Graham enthuses.
“Among the different things that we are focusing on in the coming months is working with the RIBA Providers Network to present technical presentations to architects and specifiers and drive the agenda of unique bond
patterns and sizes,” Graham reveals. “We want to be a part of the movement that explains to the UK market that it does not just have to rely on the use of the standard, traditional bricks, and that there are indeed a whole range of colour combinations and sizes at one’s disposal. As part of our efforts to do this, we are starting to gain momentum when it comes to marketing TBS and its past successes, and to the way we present our products. We know from experience that architects and other customers are looking for ways that they can deliver exciting new designs with their brick buildings, and we are working hard to be at the forefront of facilitating that change in 2021.”
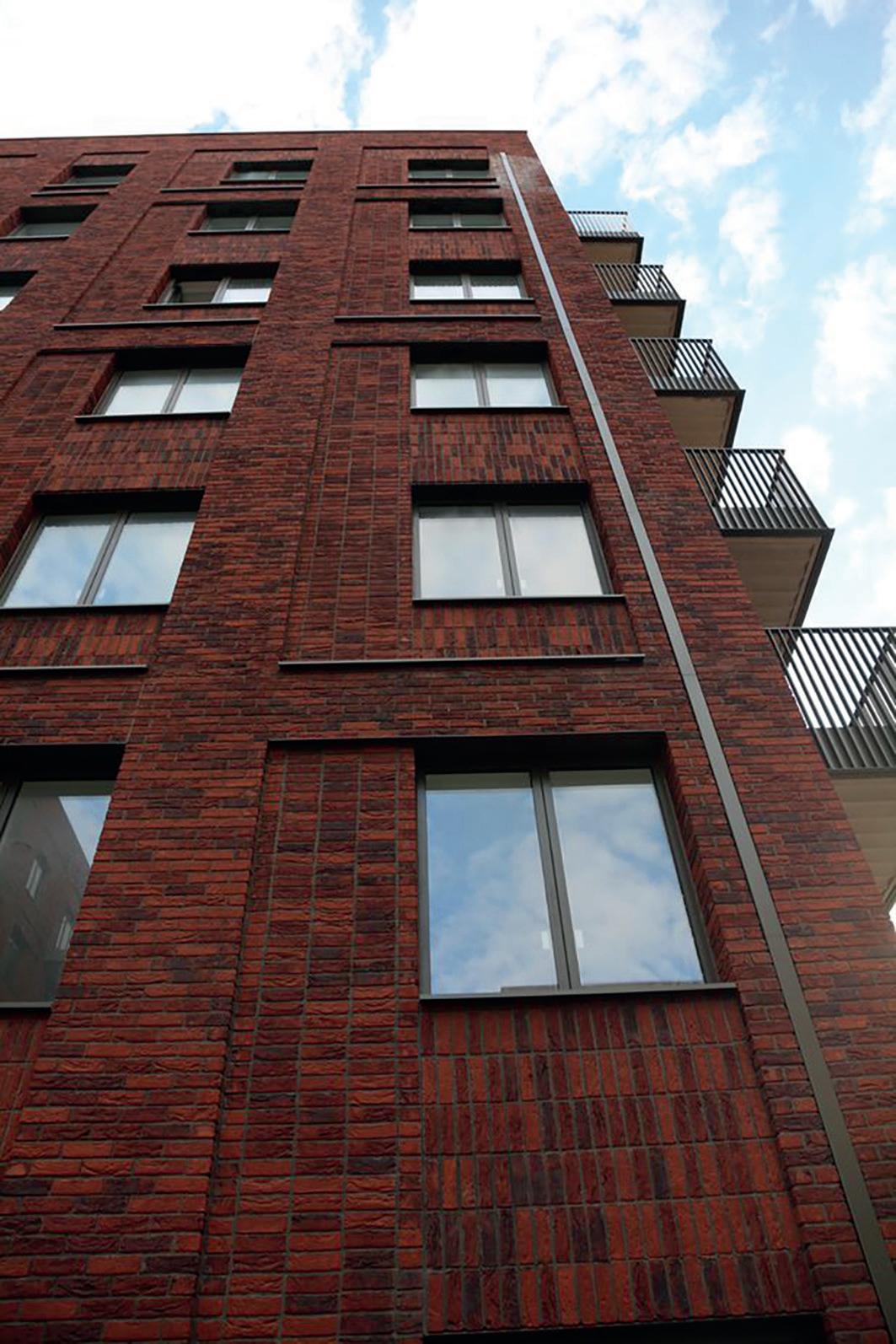
Product innovation
Looking a little further ahead, Dan reveals some of TBS’ goals for the coming three-to-five years. “Today, we are moving approximately 50 million to 60 million bricks per year, and in the next few years I would expect to see that comfortably move to between 60 million and 70 million,” he says. “We certainly have the capacity to achieve this, and we also have further investments in the pipeline with suppliers to develop more volume and bring even more products through over time. We also have plans to expand further upon our existing facilities and capabilities to offer additional cut specials, as well as more products to assist in the sale of precast goods as well.”
Graham then goes on to conclude: “At the same time, we need to continue to do what we do so well, which is to listen carefully to our customers in order to identify what they require from us, and to lead the way in terms of innovation. I know that bricks are essentially a lump of clay, which is dried and then fired through a kiln, but there is a high degree of specialisation present in that process. We need to take full advantage of any innovative new products that we can develop with our manufacturing partners, and this makes us very excited about what can be achieved in the future with our customers.”
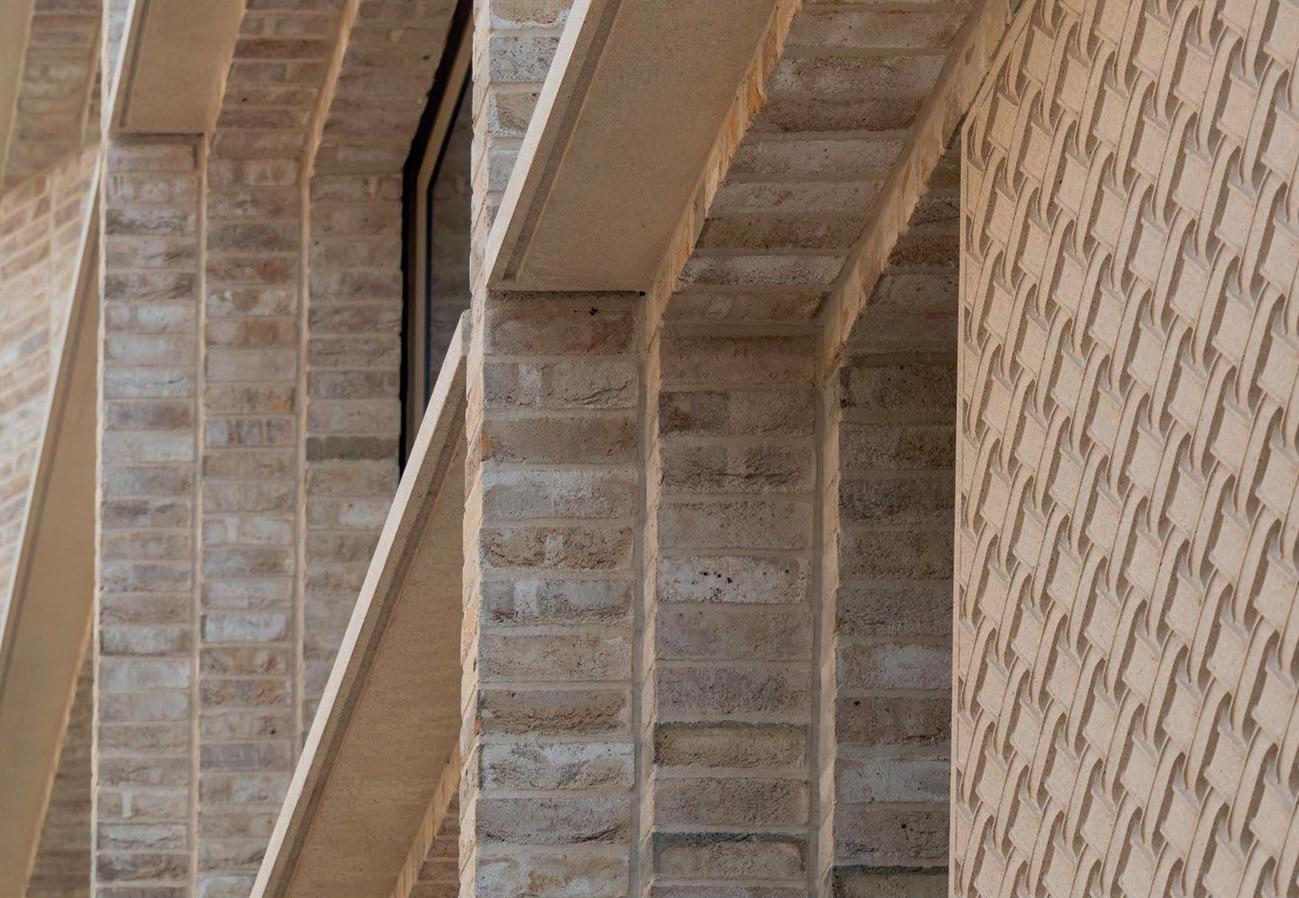
Photography by Robert Greshoff
Products: Bricks, pavers and cast stone
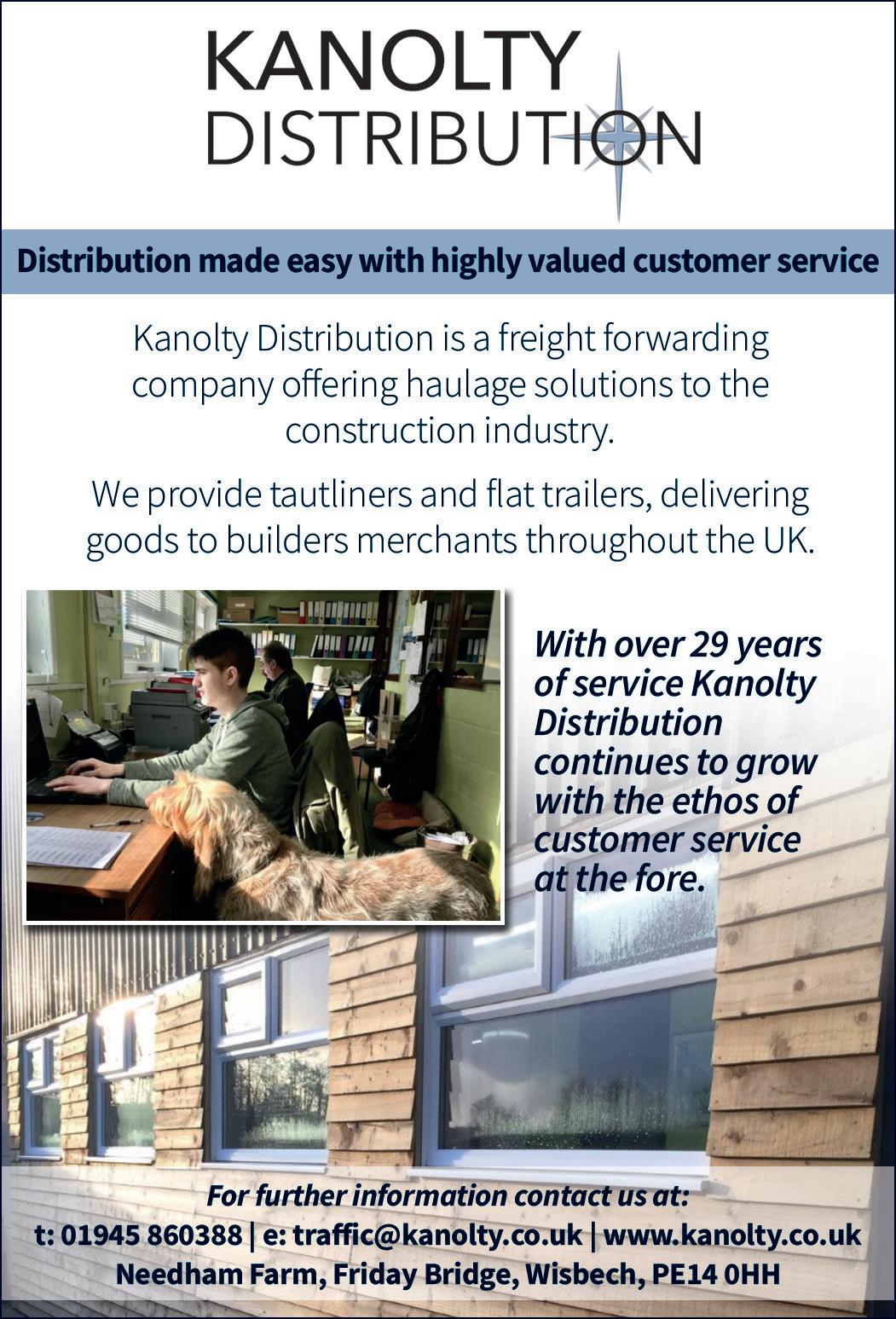
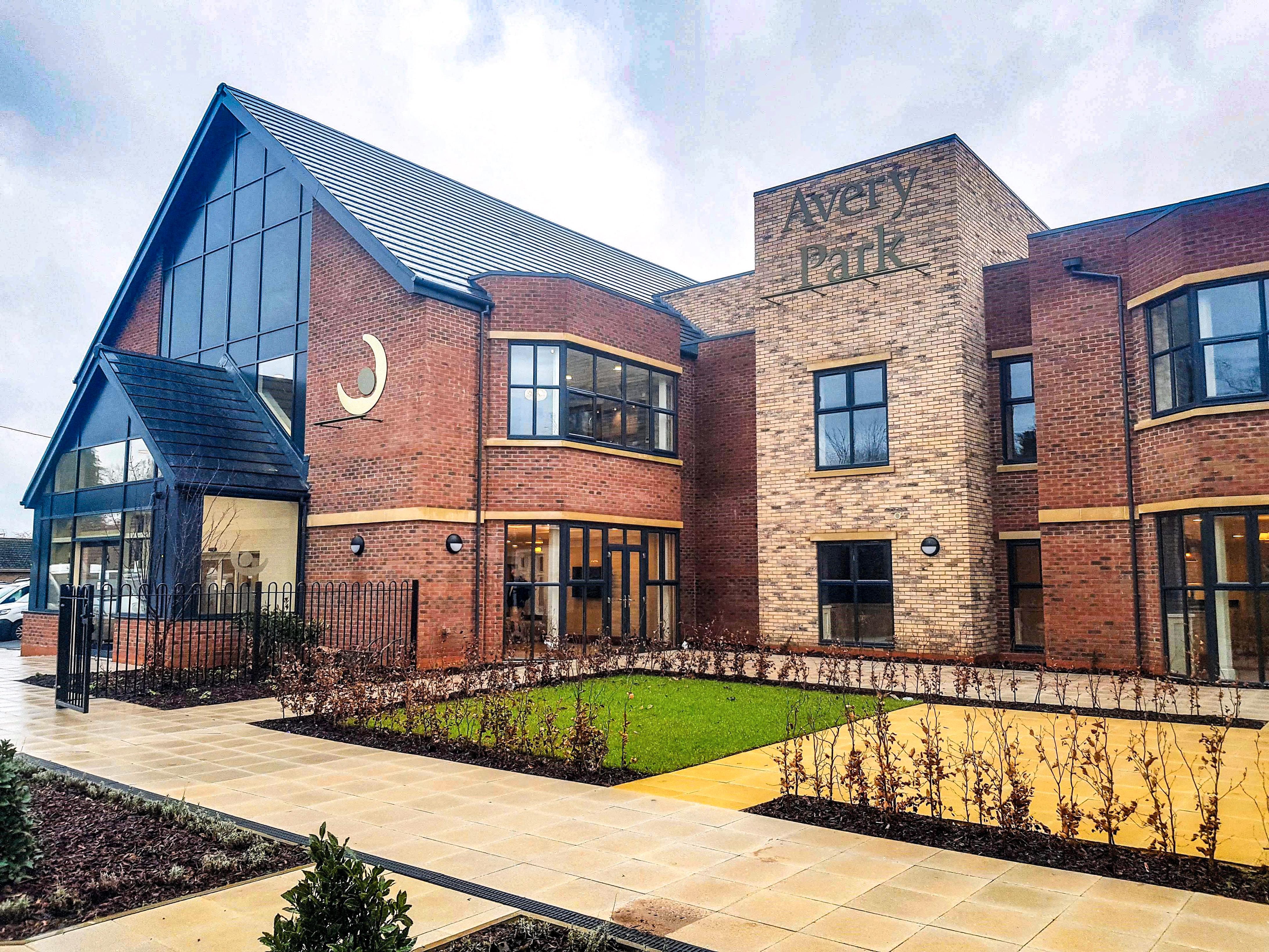
Family first
The strong family ethos that formed the foundation of Natta Building Company continues to serve as the source of its success
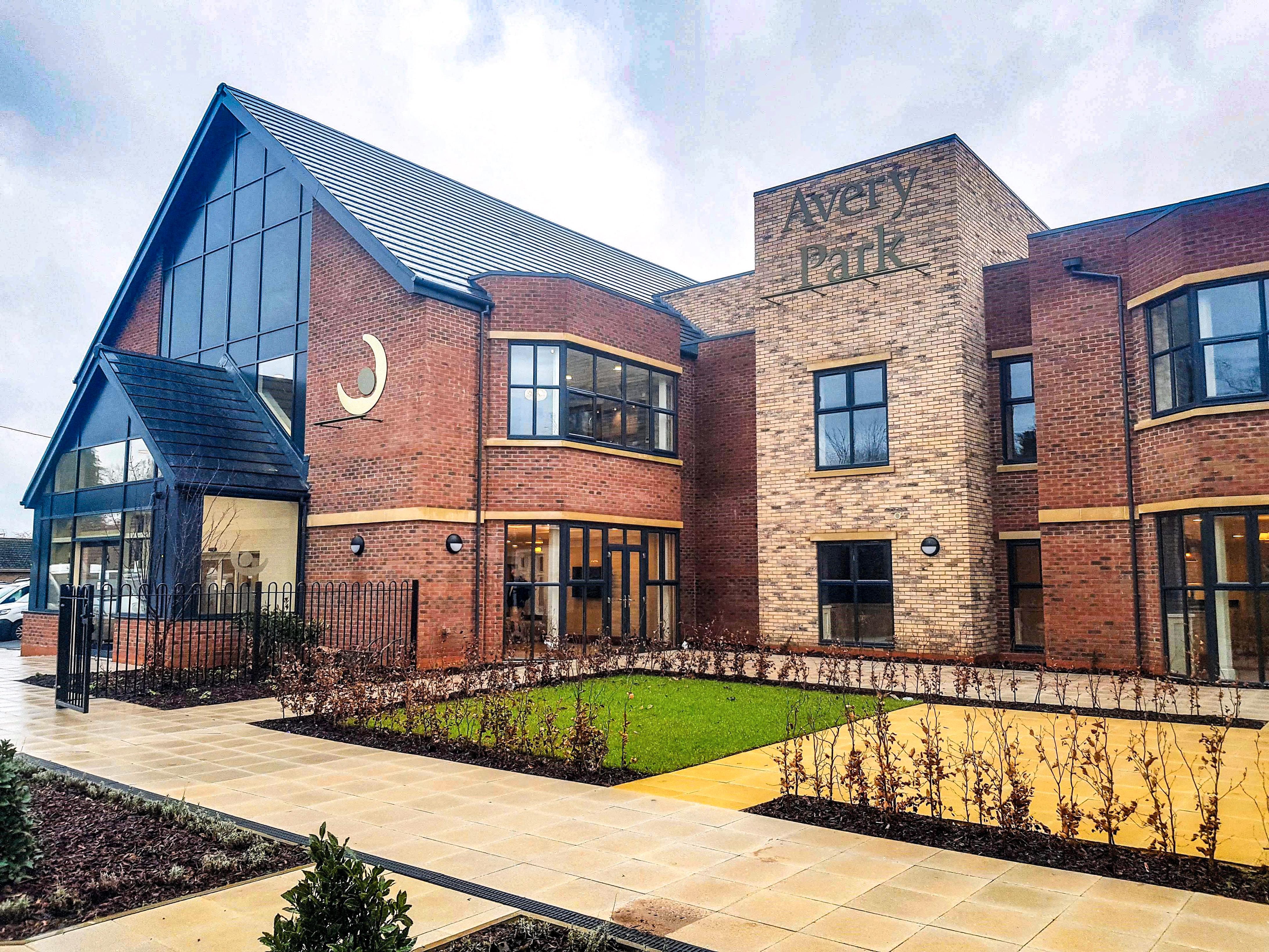
With nothing more than a shovel and fork, John J Whelan established Natta Building Company Ltd as the sole owner, in 1972. He built his company from the ground up as a pipeJohn E Whelan refined his trade and worked his way to the top to take over from his father as Managing Director in 2007.
Now, as one of South England’s leading multi-disciplined construction and civil contractors, the Natta Group has covered projects from London and the South East to Bristol, Swindon and Milton Keynes. When it began as a specialist in infrastructure installation, Natta was able to excel in its project completions, allowing it to diversify to offer more turnkey services to its clients such as site investigations and reporting, site clearance and geo-environmental solutions such as dealing with contamination, remediation and recycling. One of the newest expansions for the company has been the creation of its inhouse specialist division: Natta Utilities. The scope of this division includes gas, electric and water services installations providing full package construction for both on and off site installations. It is primarily focused on the construction and commissioning of new infrastructure on new development sites.
This at the start of the project, and together with Natta’s geoenvironmental experience, is where Natta believes it is at its most effective in saving the client on lead times and costs, providing a full service from the inception of the project through to the project completion.
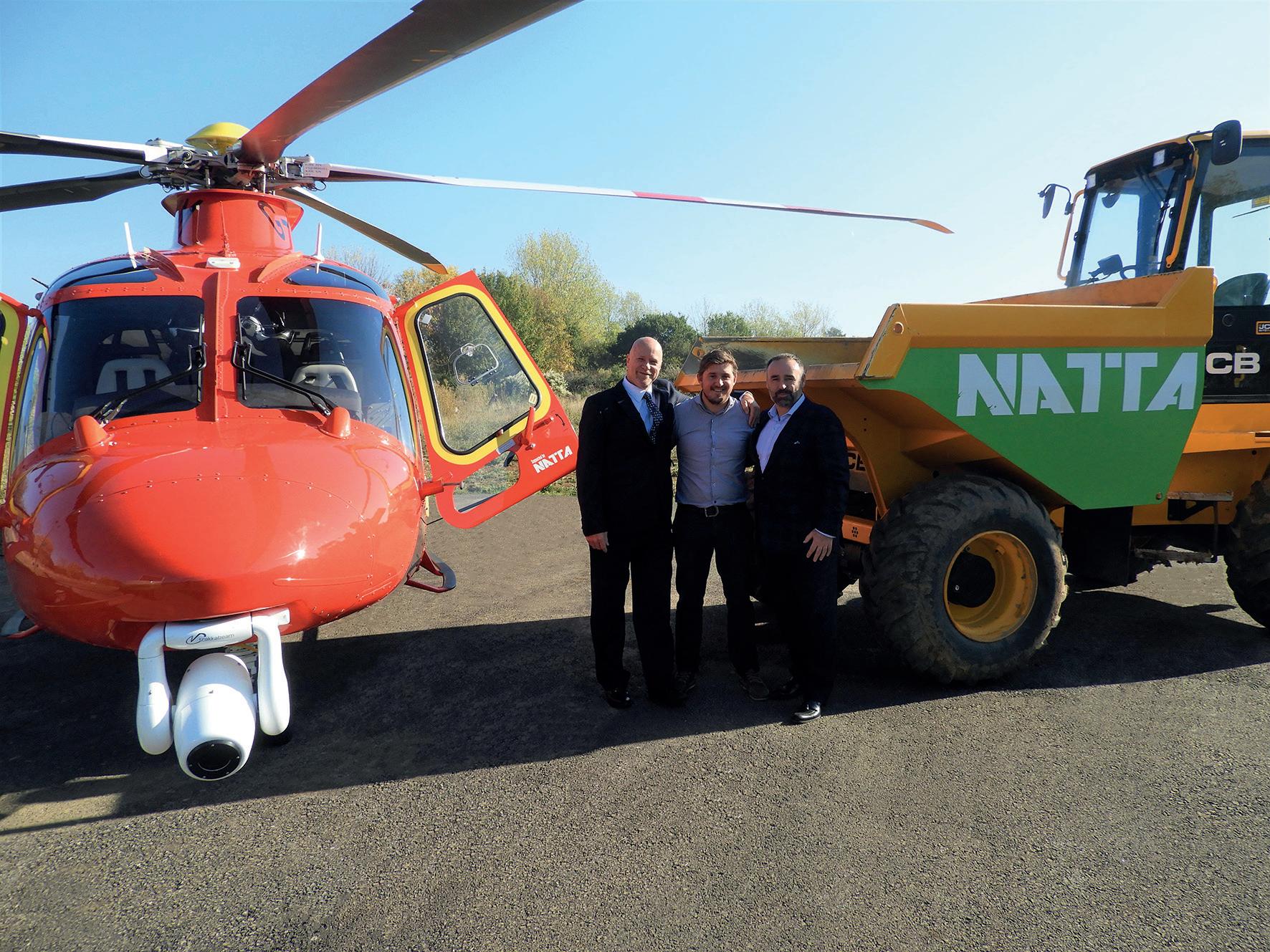
layer and groundworker before his tools were traded in for his first excavator. Following in his father’s footsteps, John E Whelan brought to the company his own freshly learned skills from a BSC Hons in Building Management and a Post Graduate in Construction Management. Just like his father,
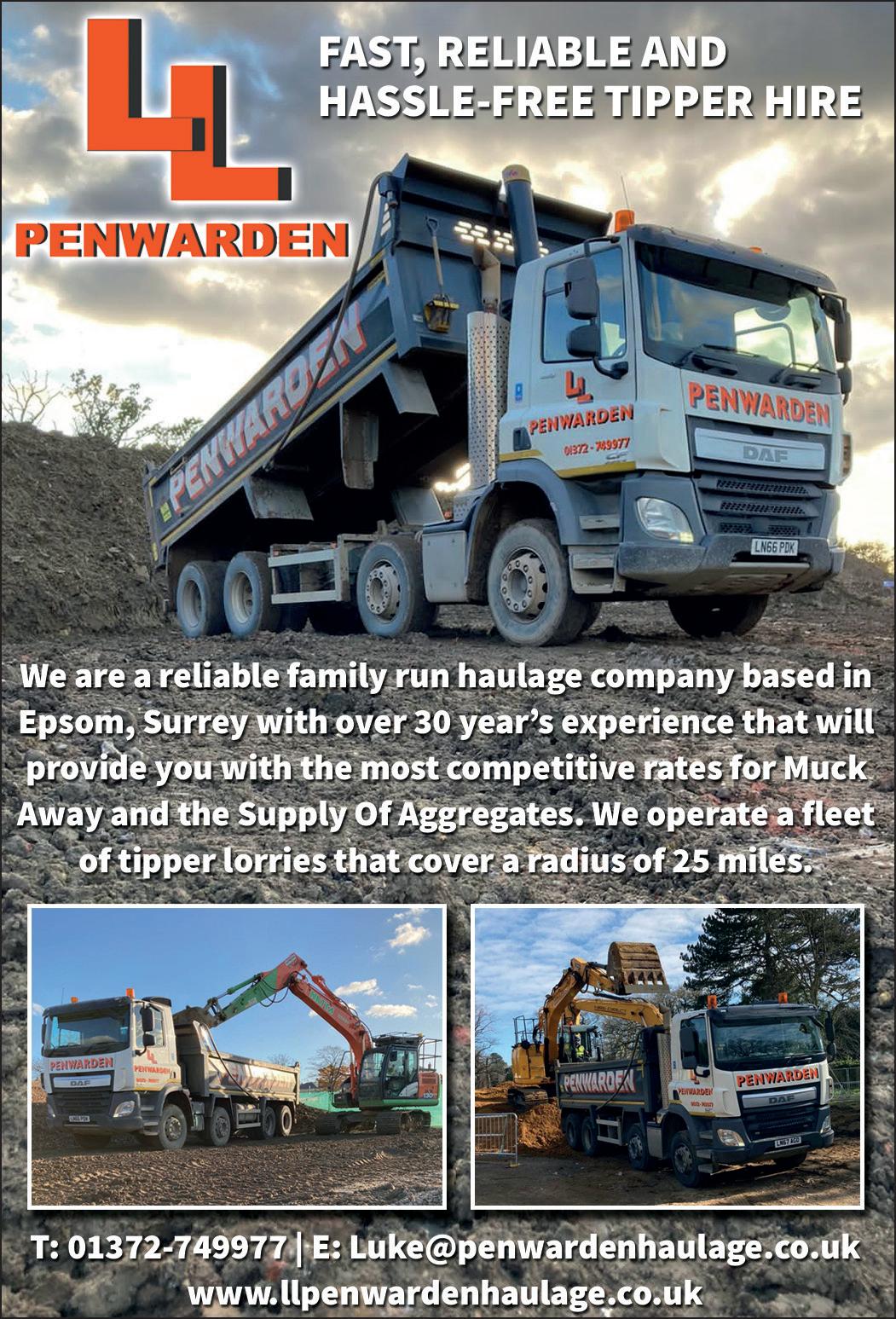
One-stop solution
This, according to a comment by Jo Whelan, the Marketing and ICT Manager, is what sets Natta apart from its competitors. “With our cohesive offering and approach, we can be a one-stop solution for the needs of our clients,” she said.
In fact, when it comes to thorough services, Natta strongly believes that training is vital to fulfilling construction contracts with a work ethic that can be trusted. This led Natta to set up
its own training company CISTC and is one of the key facets that give Natta its stand-out quality for project completions. Because it is all at once a training group, construction employer, and a training provider, it can provide the highest level of safety regulations and quality construction for its clients.
Intertwined with Natta’s nature to care for its employees is its ethos to care for the built and natural environment. So, when in 2017 the business opened its own Training and Wellbeing Centre to host apprenticeship programmes and CISTC’s training courses, it was natural that it had sought a greener way to construct this. The resulting zero carbon building featured structural insulated panels, the building is heated by a 200 KW wood chip biomass boiler and electricity generated by a 46KW PV array.
Additional methods that the company undertakes in its pursuit of environmental sustainability have led it to receive multiple awards for its construction site care. In the Construction Material Recycling category, Natta was awarded the Green Apple Award for the ‘Built Environment and Architectural Heritage’ and in 2019, it received another Green Apple Built Award for Reducing Plant Emissions. In the pipeline are also enquiries into electrical vehicles for its fleet.
Meticulous safety
It is well known that the construction sector can be a dangerous place to work. However, some measures can be implemented to safeguard
AJN Steelstock Ltd
AJN Steelstock Ltd is proud to be working in partnership with Natta Building Company, providing processed steel to site, whenever and wherever it needs it. Our huge product range, fleet of own vehicles and 24-hour working pattern means we are able to meet even the most demanding of schedules. But we don’t just deliver steel; we also deliver it how it’s needed. From in-house sawing to shot-blasting and painting, from state-of-the-art CNC drilling to plasma and laser cutting, we offer a comprehensive range of rapid processing and finishing services.
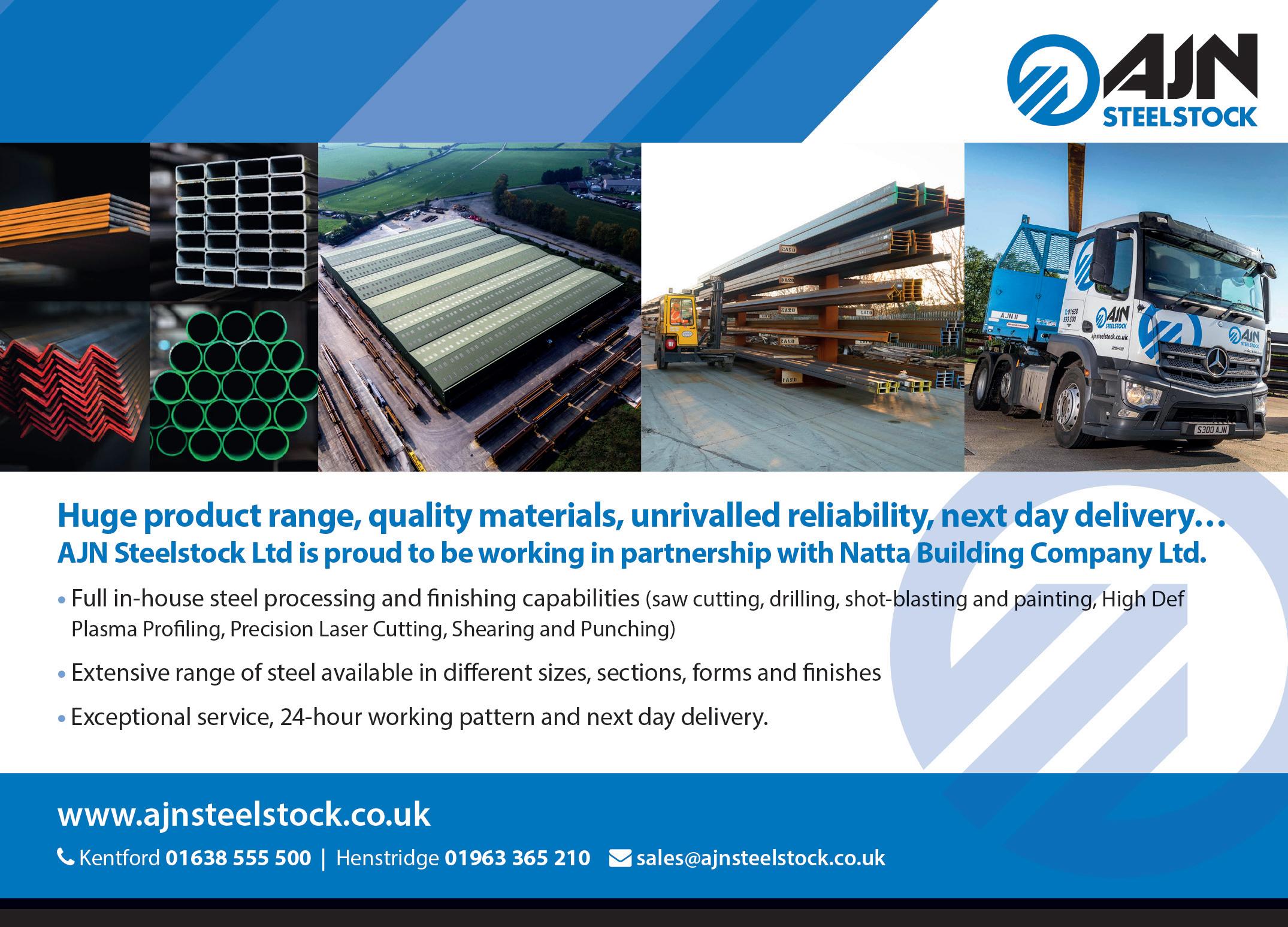
against accidents to clients and employees and these measures are highly prioritised by Natta. Illustrating the success of its approach, Natta recently celebrated the achievement of working 4.3 million hours without any reportable accidents. The success of such regulatory measures has to be maintained at management level and Natta ensures that the company abides by the highest level of corporate responsibility and governance. To implement this, it is an Achilles’ BuildingConfidence member; a certification that recognises the highest construction standard in safety schemes, a member of CHAS, a leading accredited risk manager, and Constructionline. and was greatly appreciated by West Sussex County Council.
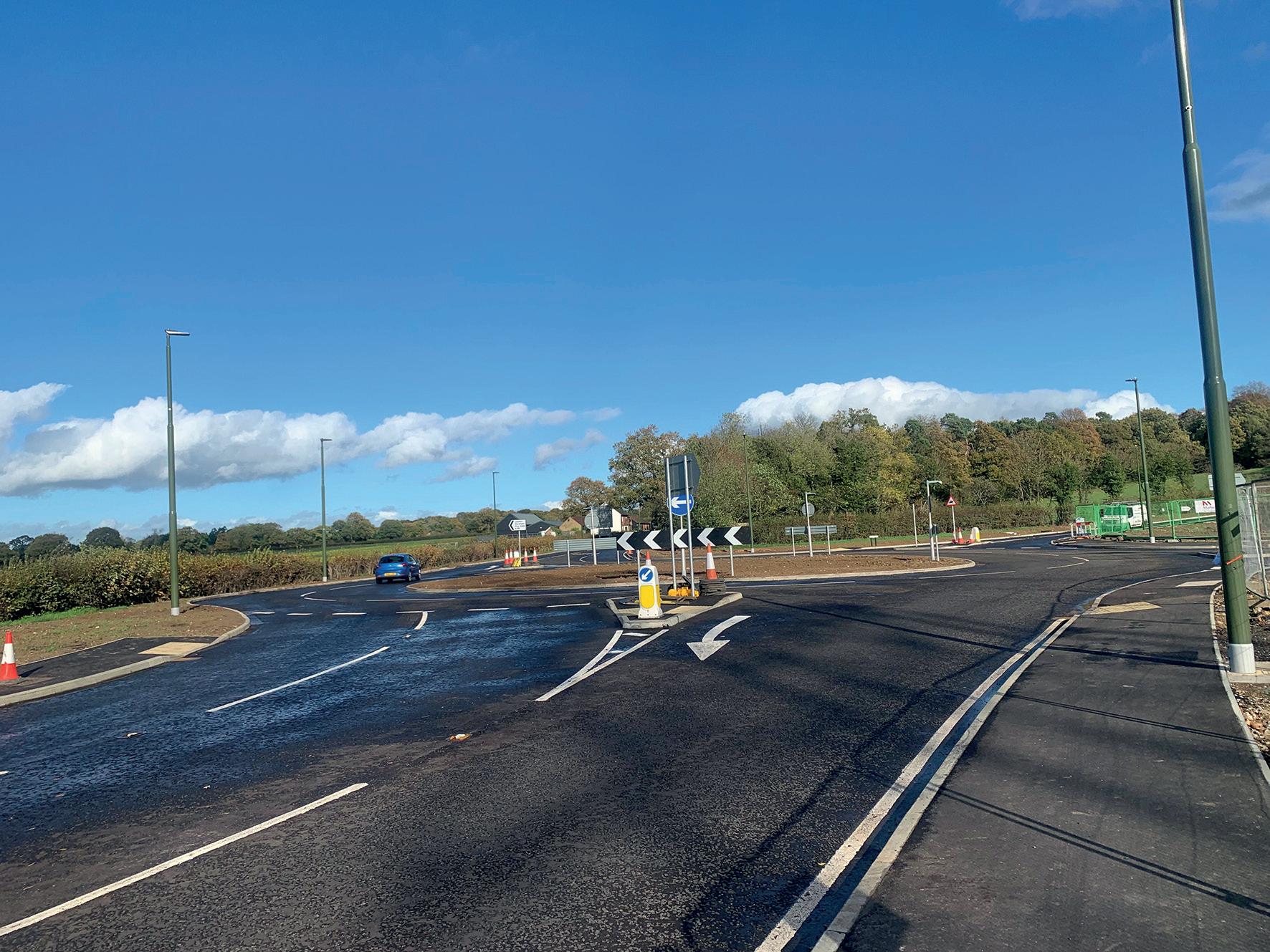
Undertaking such intensive and meticulous safety regulations means that Natta’s project portfolio is both expansive and impressive. In Copthorne, Natta was contracted to develop a new roundabout and access road for a 500-unit housing scheme. In an area that had been previously used as an inactive material tip, the problematic soil conditions required the company to negotiate a substantial amount of earthworks cut and fill. The project also included a new bridge, prefabricated portal sections, and installation of a large 2.10m diameter attenuation pipe and drainage. The entirety of the project encouraged the full use of Natta’s engineering expertise Billingshurst Clever initiatives
Another project sent Natta to Kettering where it received a contract to demolish and remediate a former industrial testing laboratory, and create a site for a new 120-bed residential care home. The site was found to be historically contaminated by ground materials of coal and asphalt, as well as bedrock clay and ironstone formations which had naturally increased the soil arsenic levels. This made the area unsuitable for community settlements. The project in Kettering required extensive work by Natta’s Geo-Environmental division, ensuring the site would be safe and secure for the long-term.
A recent completion was in Billingshurst for the Dunmoore Group. As the main contractor, Natta worked to build a roundabout and access road to a new industrial park. This project involved extensive resurfacing of the existing carriageway and the installation of street lighting and water mains. An adoptable drainage diversion and storm attenuation tank were built on site as well as potable water main and BT diversions.
Natta is also a charitable company that believes in giving
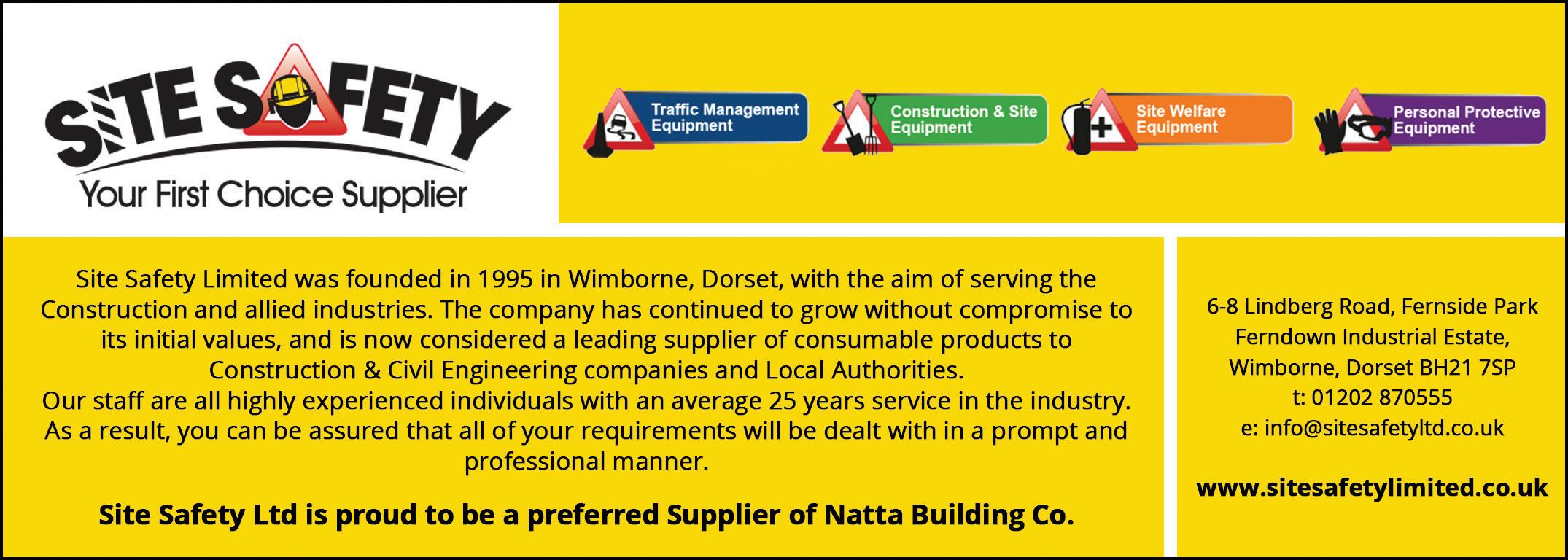
back to its community by donating time and energy to some projects. In 2018, it constructed a new helipad for EHAAT and Basildon and Thurrock University Hospital at no charge. In 2019, in support of Woking and Sam Beare Hospice, Natta completed the build of a new ‘Wildlife Garden’ for the residents and staff there.
As a company with innovative solutions that thrives on complex challenges, not even the pandemic has proven to be an impossible obstacle for Natta. It still successfully secured several new groundworks contracts, a new care home in Wrotham, and its first in-house property development in Cuddesdon near Oxford. When completed, the development, called Dove House Park, will be comprised of nine unique properties; five units in a new build block, three barn conversions, and the conversion of a huge tithe barn into a modern grand luxurious home. This new adventure into the realms of property development is an exciting step for Natta Building.
Of course, that is not to say that Covid-19 has been smooth sailing. In situations regarding site building, sourcing building supplies from other companies has made completing projects according to schedule a challenge. However, Natta has introduced several clever initiatives to manage supply chain efficiency for 2021, and on the civil engineering side, the usual challenges of working on highways and schools have actually been easier and more flexible than usual. It is these adaptations that make Natta hopeful about its evolution despite the restrictions of the pandemic.
It is clear that Natta continues to strive for greater heights to ensure the success of its name. What began as a family-owned business almost 50 years ago still upholds the same family ethos instilled by John J Whelan. Heading into its third generation, Matt Sainty, the Commercial Director, is one of the cornerstone employees in the senior management team and has served more than 30 years with the company. Although Matt is not family, he noted that the family dynamic is one of Natta’s strengths. “We see ourselves as custodians. Everything we do is for a long-term time frame,” he said. It seems that Natta is here for the long-term too.
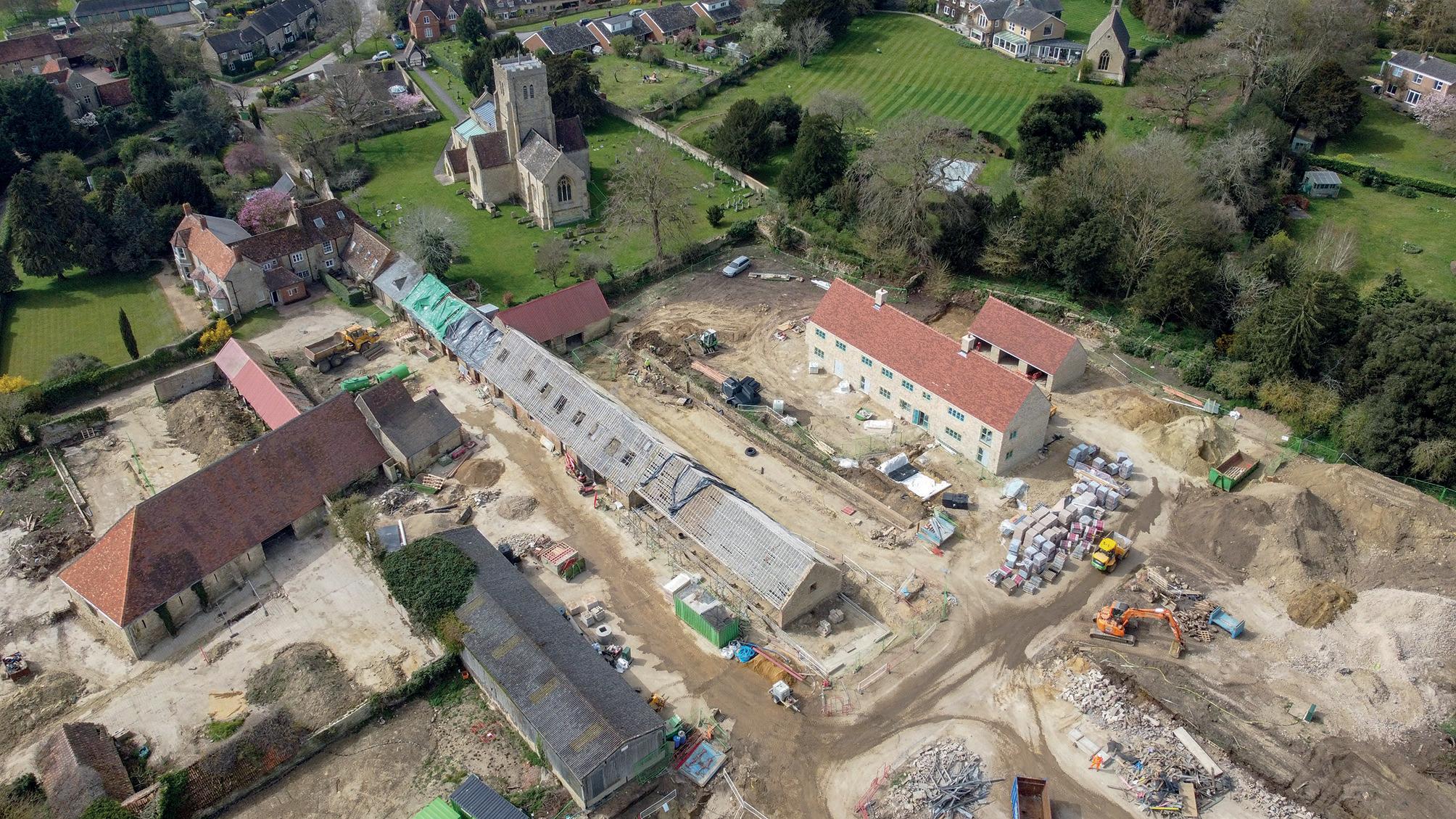
Construction and civils contractors
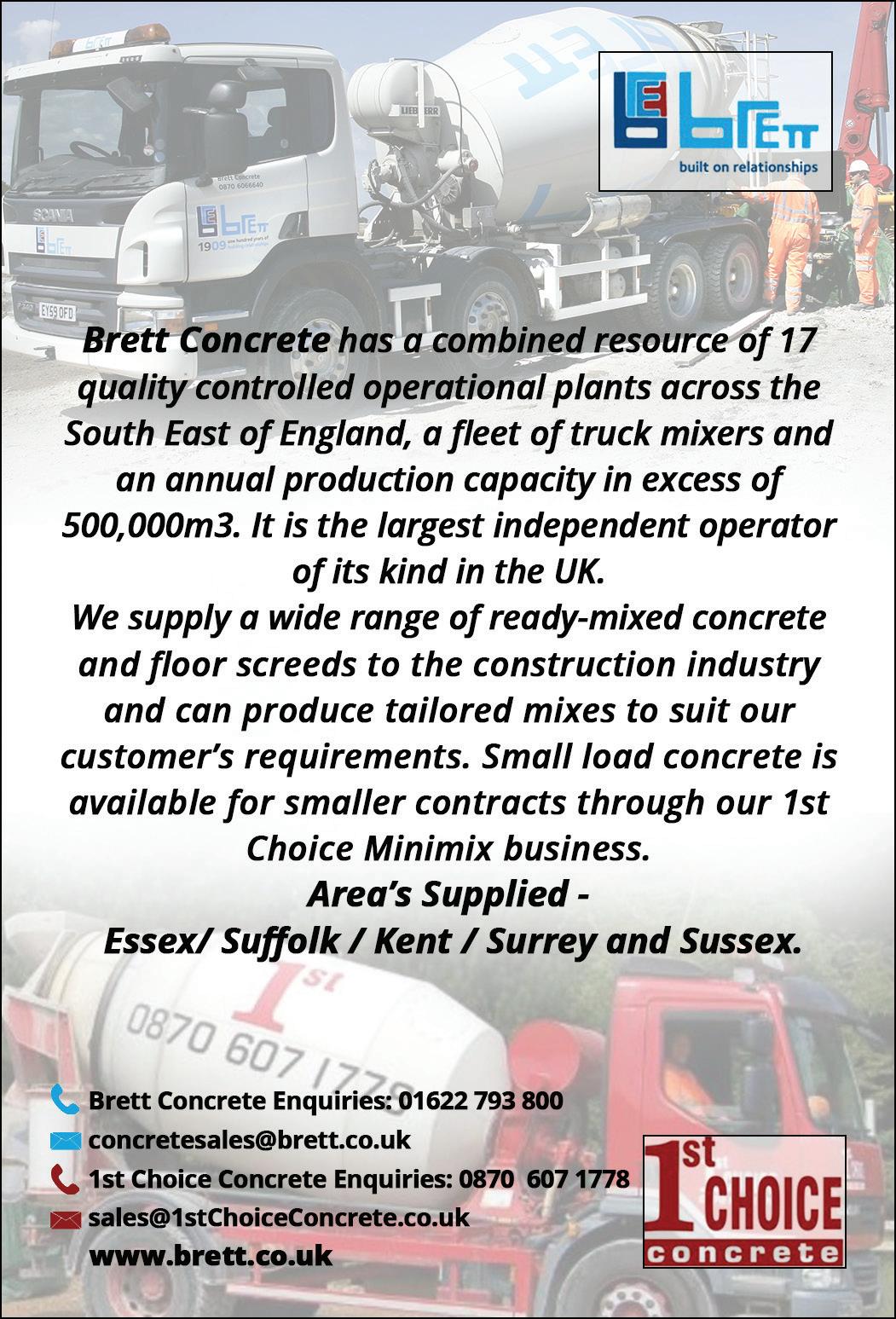
When Kind & Co turned 70 years old in 2015, it invited all its employees and long-term business partners to define what they believed to be the company’s key values. The exercise resulted in the ‘The Kind Effect’, a collection of 11 principles that drive the business and translate into everything the company does. Among the phrases chosen to summarise Kind & Co by those that know the business best were: neighbourly, polite, respectful, caring, safe, professional, and considerate. Speaking to Construction & Civil Engineering Magazine, Kind & Co’s Joint Managing Director, Bill Bassenger, asserts that the values are way more than just words.
“From the outset, in 1945,
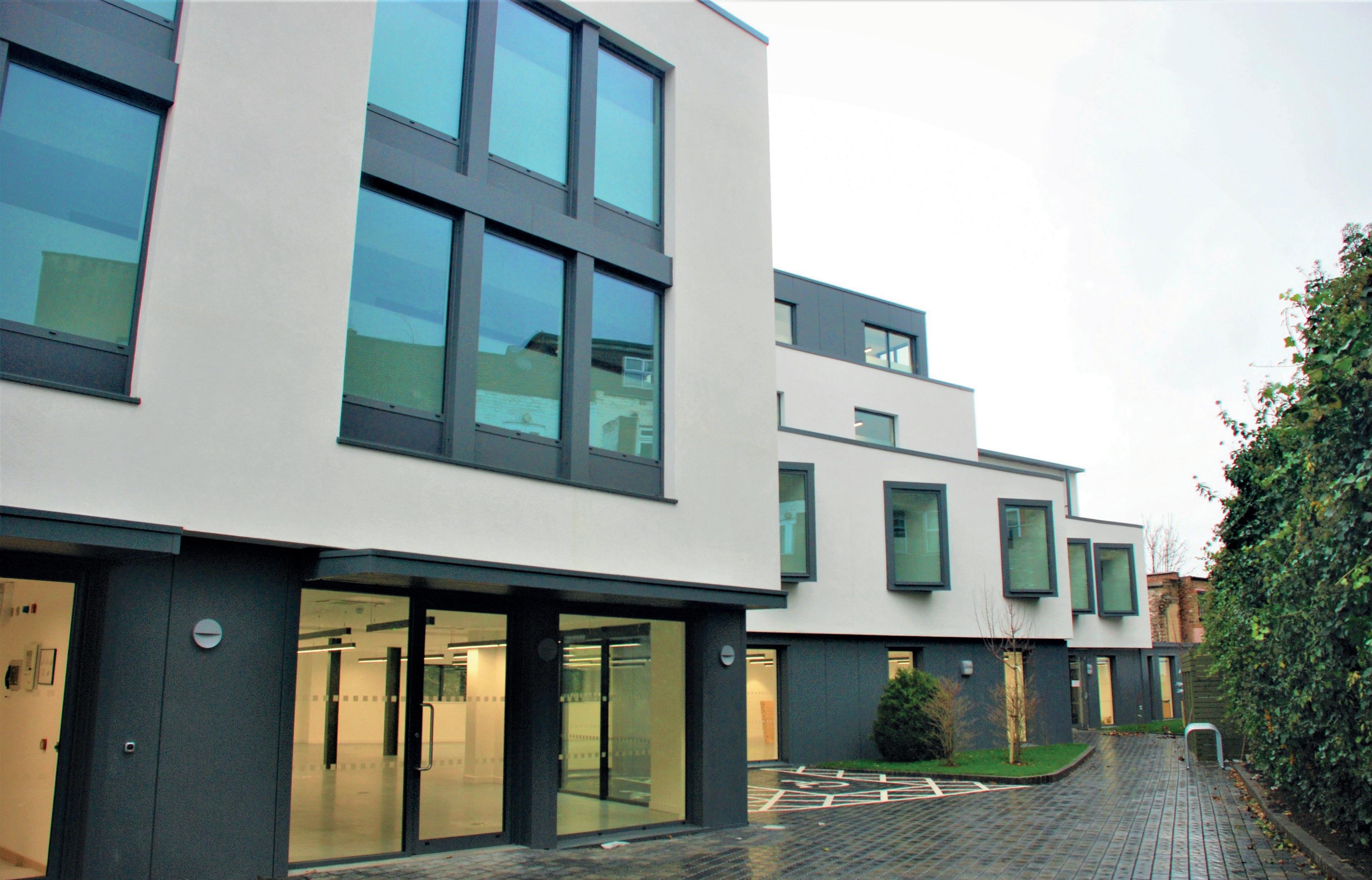
One of a kind
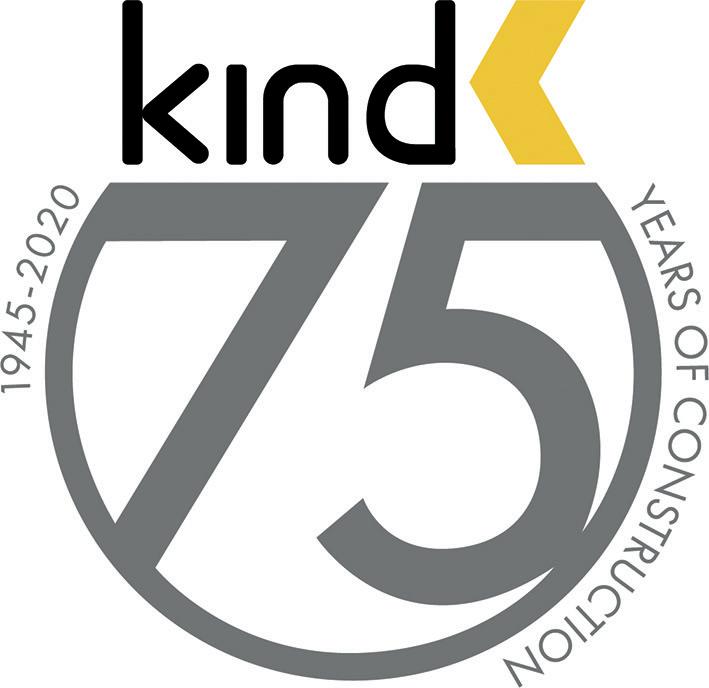
Celebrating its 75th anniversary in 2020, Kind & Co is a fast-growing, employee-focused construction company with a modern, values-based approach to business
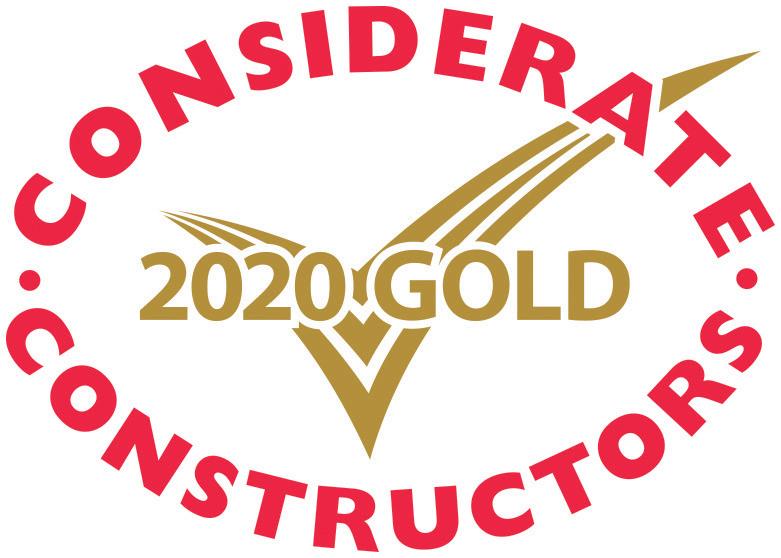
Kind & Co was involved with war damage repairs and regeneration work,” Bill reveals. “Following this, it continued to deliver much needed housing for post-war London. In the late 1950s, Kind & Co acquired a major client: Greater London Council. This unlocked many opportunities for the company in an array of sectors including schools, council housing, arts projects, sports and medical centres, setting it on a path to the future.
“Things have changed a lot since then, but our values are the same. Onsite, we have a determination to make use of local labour where possible and communicate clearly and openly with our neighbours, maximising understanding and minimising inconvenience. This has resulted in close liaison with schools, charities and local support groups, and we are a major sponsor of the first London Borough of Culture 2019 (Waltham Forest) where our support created a 1000-volunteer programme that has provided experience and training to a wide cross-section of local people and facilitated the safe presentation of many events.”
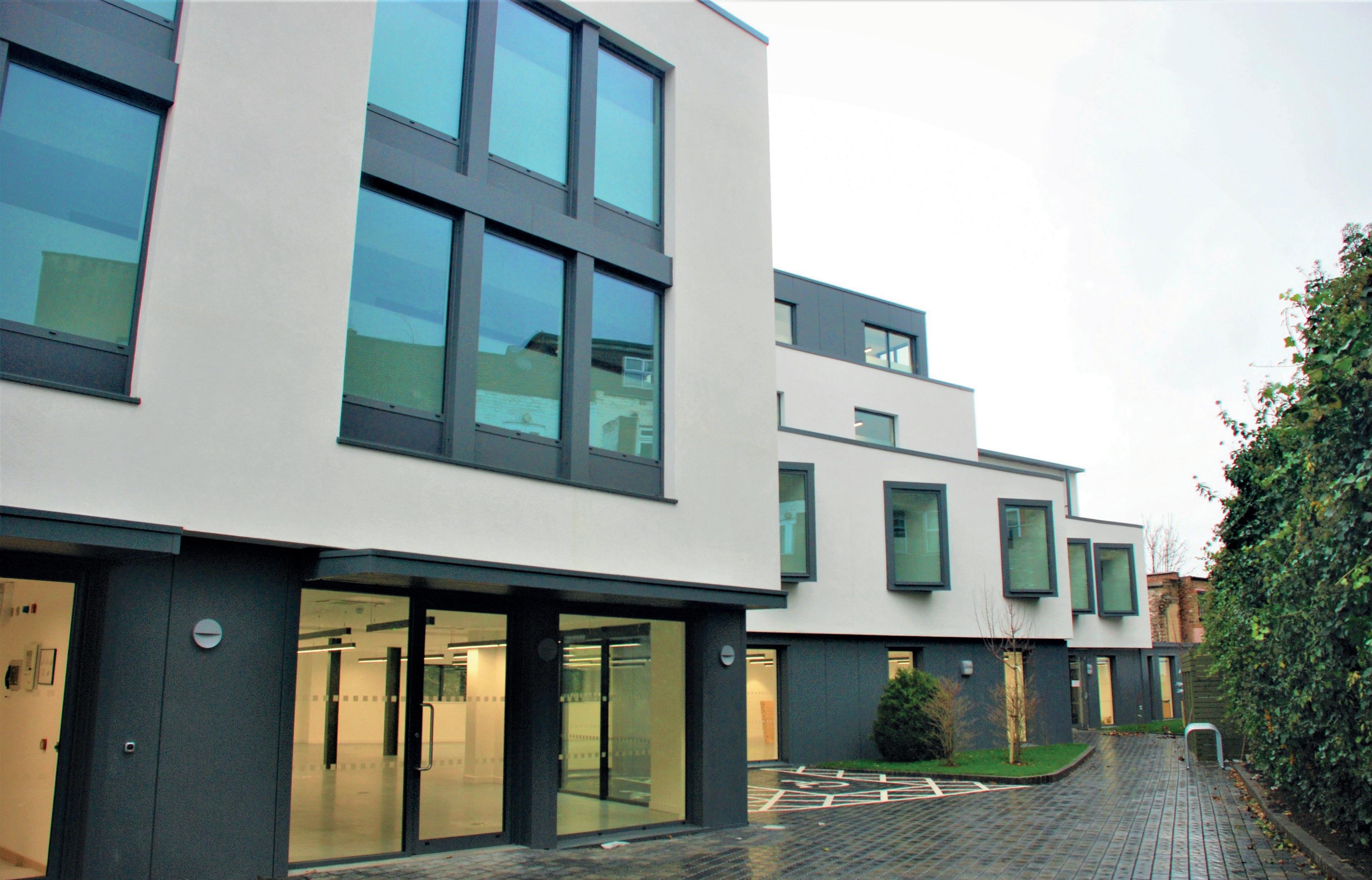
Award winners
Three quarters of a century after it first started building houses in London, Kind & Co continues to deliver high quality modern construction projects. Today, the company’s Head Office is based in Leytonstone, where it has operated since 1985. In 2017, after securing its largest contract to date - a £28 million residential scheme for the London Borough of Sutton - and in recognition of the value of a presence in South London and the southern M25 corridor, Kind & Co added a regional office in Airport House, Croydon. Taking on both new build and refurbishment work,
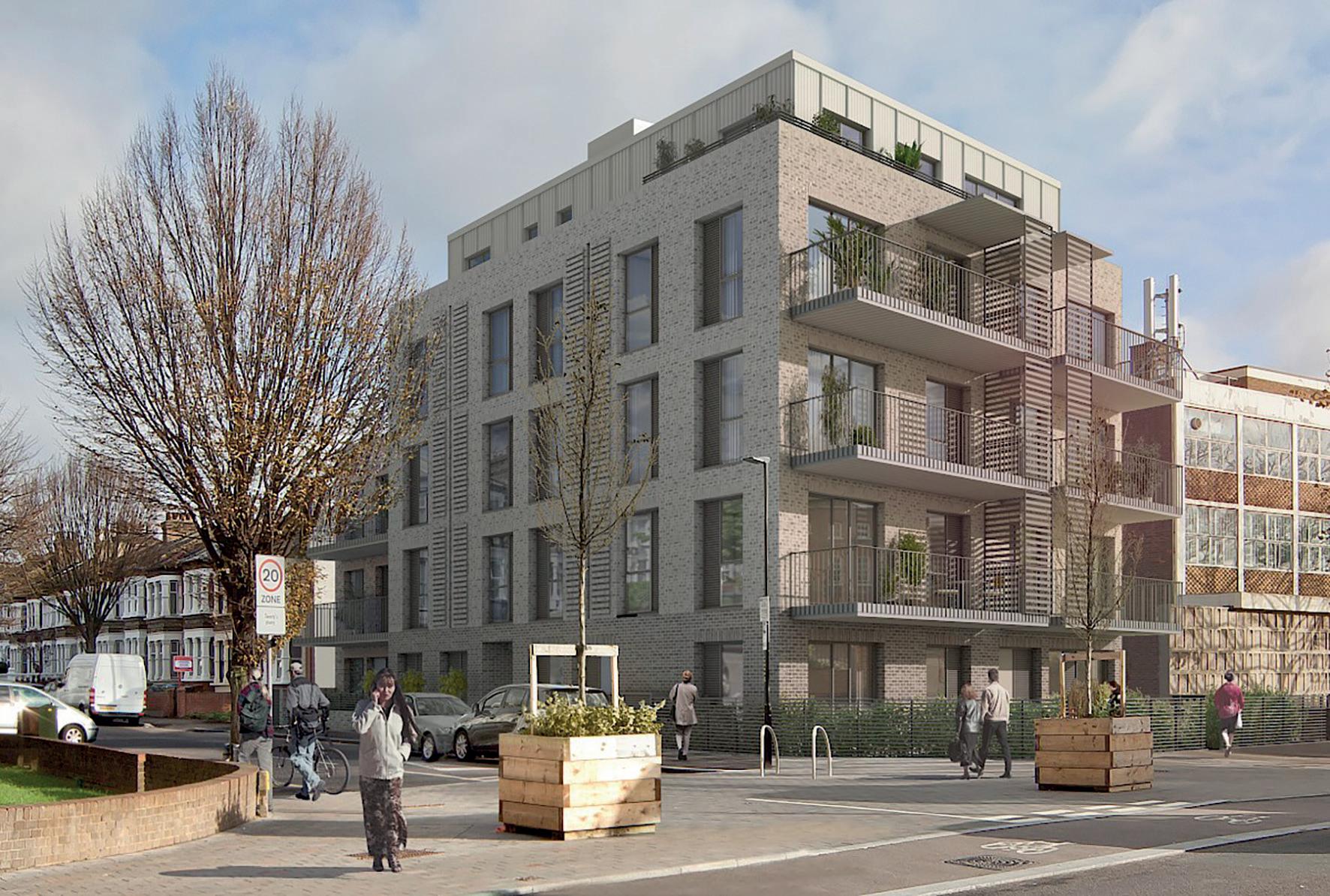
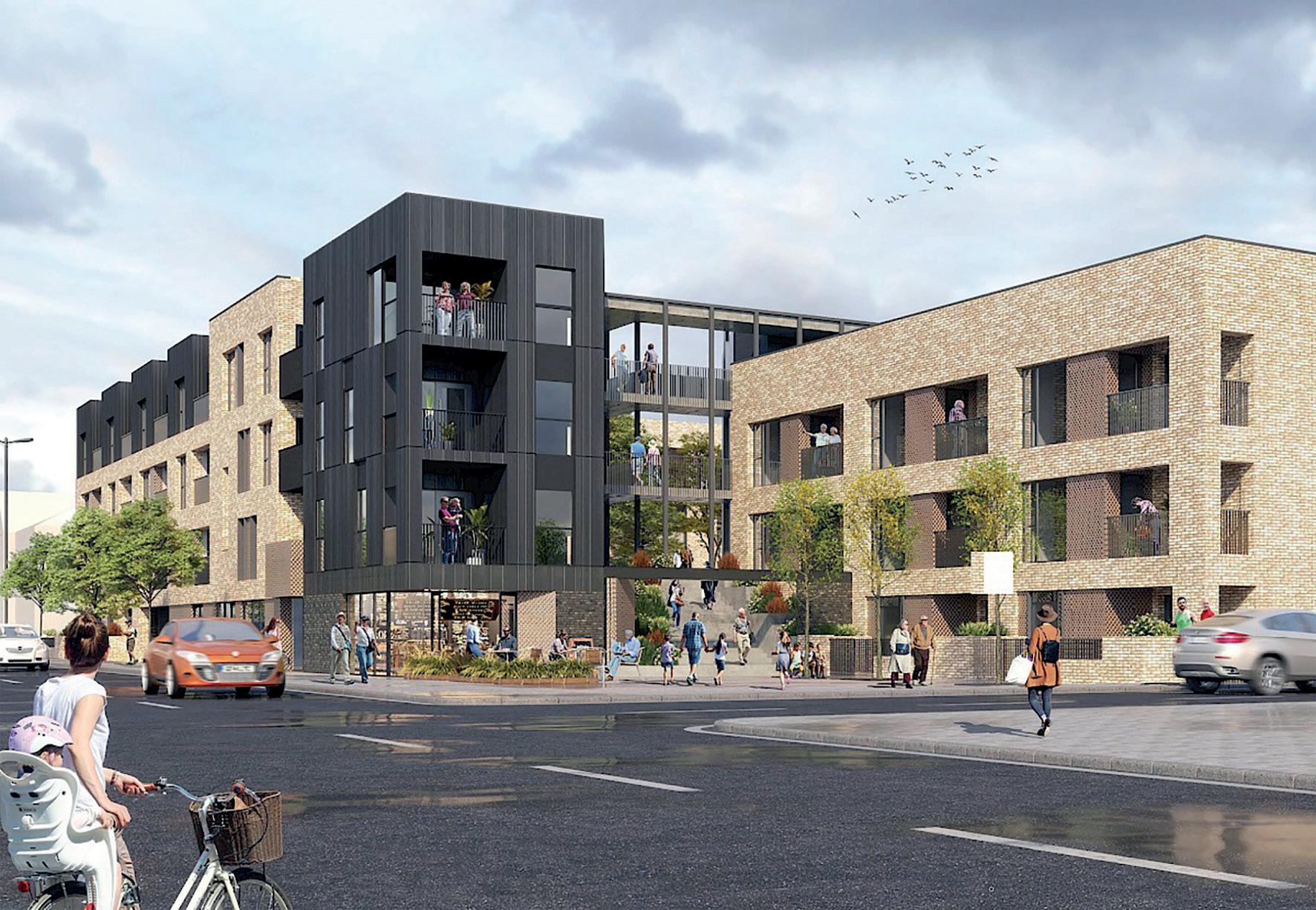
the company operates across five main sectors in the South East: Residential, Care, Commercial, Education and Health.
“Prior to the commencement of each contract, we assess the viability and buildability of a project,” Bill says. “The company’s design team then helps to develop project designs through the RIBA stages, before handing over to our project managers, site managers, surveyors and tradespeople who manage the daily logistics and practicalities of delivering a high-quality product. We have longstanding expertise in the construction sector and
Winner of the Considerate Constructors Gold National Site Award, Kind & Co’s work at Ingate Place was recognised for the company’s ‘exceptional approach to considerate practice’, ‘brilliant work within the local community’ and ‘respect for safety and the environment.’ Carried out for CWC-Group, the project itself consisted of the spacious refurbishment of an existing two-storey building, as well as a major extension, adding two additional storeys to a high-end, open plan office building, which included large glass elevations to enhance natural light. As Ingate Place is situated very close to neighbouring residents, local businesses and a busy rail line, careful planning within the local and wider communities was an essential contributing factor to the project’s successful delivery.
are able to contribute to a wide range of industries. We believe this helps to set us apart from our competition.”
Over the last few years, Kind & Co has completed a number of significant projects, including a residential refurbishment and roof top extension in St John Street and Friend Street, as well as a commercial nine-storey office and retail project in Berners Street, Fitzrovia and are well advanced in building a new residential scheme in Calcutta Road, Tilbury, However, the company’s most celebrated recent project took place at 4 Ingate Place, Battersea. New frameworks
Owing to the positive reception of Kind & Co projects like Ingate Place, the company continued to win further business in 2020. In that year alone, Kind & Co has successfully secured a place on three new frameworks - Hyde Housing, Connected Partnership Framework and LB Tower Hamlets DPS. These three frameworks run from 2020 through to 2024 and 2030 covering projects in Housing, Education and related works.
Tony Battle, Kind & Co’s other JMD explains more: “These three new frameworks are a welcome addition to our established frameworks and loyal client base for whom we have been successfully delivering projects in all of our sectors for many years.”
Capeford
Capeford have been proud to be in a close working relationship with Kind & Co for the past 15 years. We have worked together on many projects all over London, taking on the Groundworks, Concrete Superstructure and External Work elements of many of their fantastic projects. In this time, we have found Kind & Co to be an excellent company to work with. They have helped us grow and pushed us to do better in all aspects of our work including Health & Safety, Program Commitment and Quality of Workmanship, to list just a few of their many assets. They have been forward thinking in their approach to every project using all the latest innovative products and design techniques. They have very highly skilled site management teams who work through problems and resolve them fast and efficiently. We look forward to remaining involved in future Kind & Co projects and continuing to grow together.

2020 was always going to be a big year for Kind & Co, with the company celebrating a milestone 75 years in business. As the company has developed and evolved over the decades, one element has remained the same – a dedicated core of reliable and diligent employees. To recognise the commitment shown by its workforce, in 2020, Kind & Co took the major decision to launch an Employee Ownership Trust. “We are committed to our staff and in turn we have extremely hardworking and loyal employees. As well as offering quality training programmes to help staff develop their skills, we are always looking for ways to keep them happy and motivated, as this has a direct result on productivity, which in turn secures longevity and success for the business,” Bill declares.
“One of the best ways we believed we could do this was by including our staff directly in an Employee Ownership Trust. It means that all employees, providing they have worked for Kind & Co for 12 months, will be entered into the scheme and will share in the future prosperity and profits generated by the business. Employees will not be shareholders, but instead 75 per cent of shares in Kind Management Ltd have been transferred into the Employee Ownership Trust, which is then managed by a team of independent trustees. We feel that it is a fantastic opportunity to share all the benefits and results of the great work each individual employee has brought to Kind & Co. It demonstrates our trust in our workforce and will
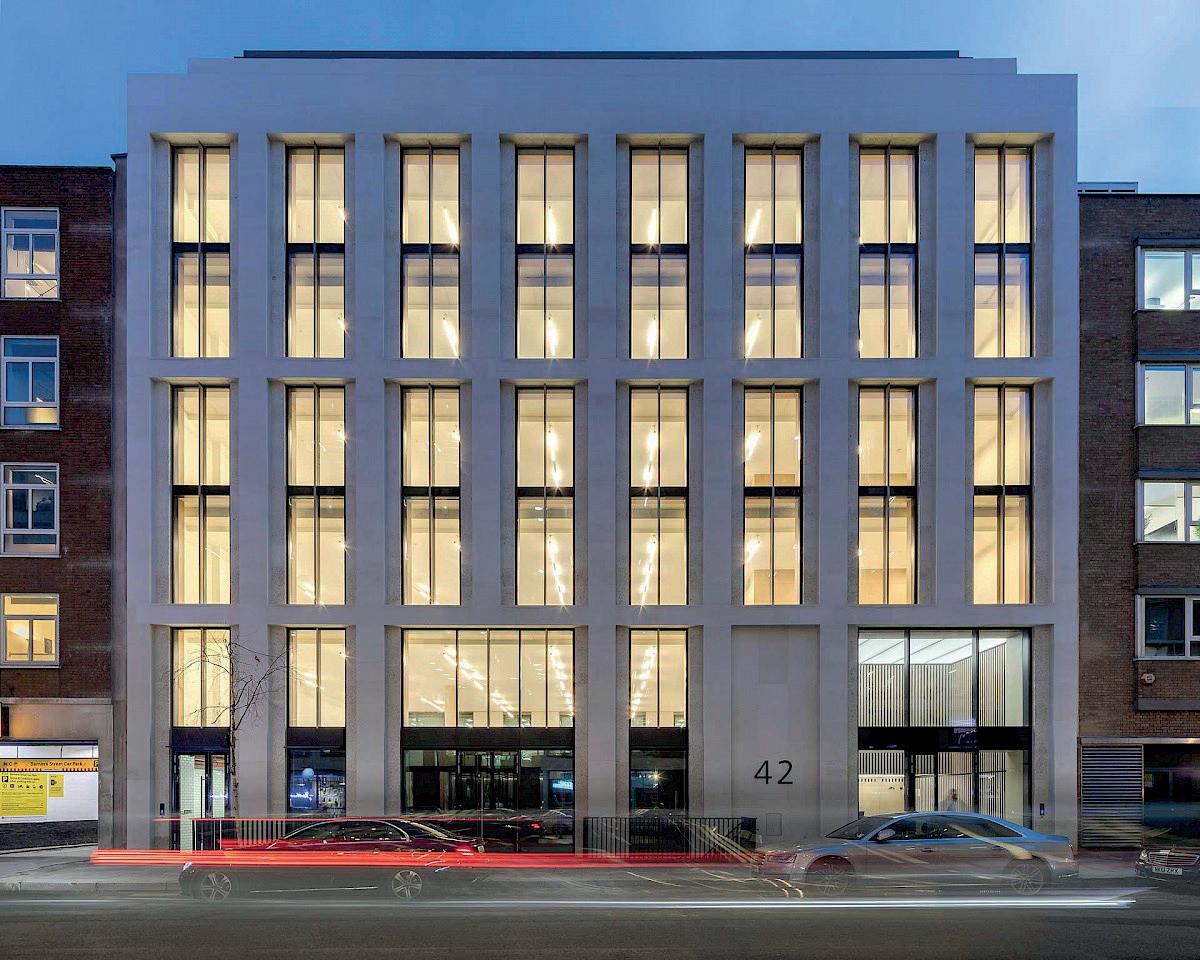
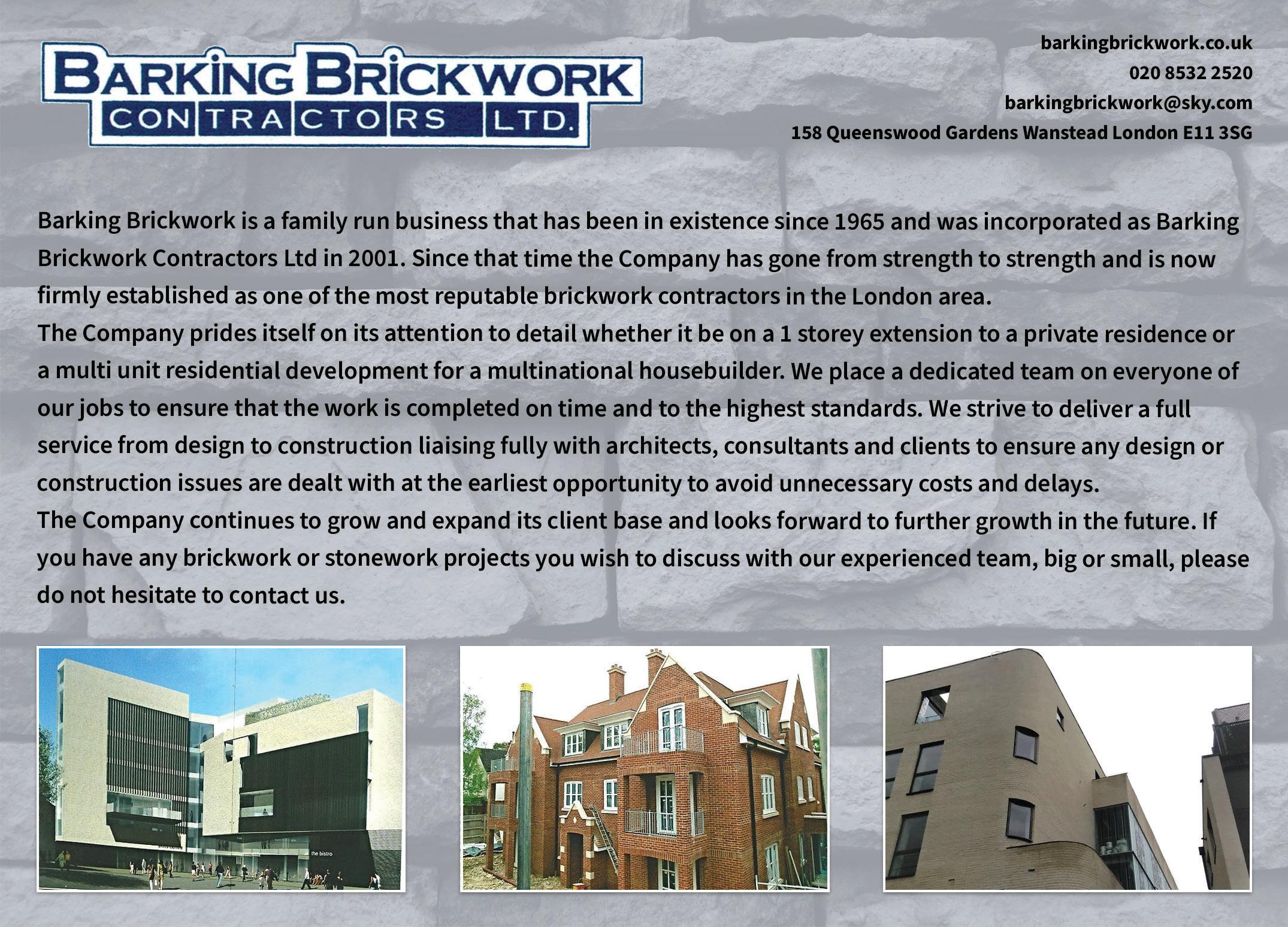
only strengthen the future of the business.”
Future growth
Of course, 2020 did not afford Kind & Co too much time to reminisce on its longevity and success. Like all businesses, the company was impacted by the Covid-19 pandemic, which required it to showcase a great deal of resilience and adaptability. As a company that has always valued safety above all else, Kind & Co was already in a strong position to protect its employees knowledge and service will be key drivers as the company moves into the future.
“With London and the South East requiring extensive residential development to meet demand, our experience and focus in this significant sector provides considerable opportunities for the future of the organisation,” Tony notes. “It also places us in a perfect position to contribute to the Care, Education, Commercial and Health sectors that support the communities being built. Most importantly, we will continue to deliver over and above to our valued clients and remain committed to our truly dedicated staff.”
when the virus hit, and for much of the year, team members worked on a rota basis, both from home where they can and the office, as part of a phased return in strict accordance with government guidelines and a robust office operating procedure which continues to evolve.
Despite the challenges, Kind & Co remains in a position to grow in 2021, building on its experience and the firm foundation of its heritage. As well as investing in developing its sustainable and strategic growth; quality,
Perega
Perega has been working with Kind & Co for over 15 years. Together we have delivered many projects in and around London including Richmond Green, Century House and Ludlow Lodge, a series of residential projects for the London Borough of Sutton, Marylebone Town Hall and Wallington Public Hall, as well as new build care homes, schools and commercial projects. This longstanding partnership has a collaborative, solution-focused approach, made possible through an open and honest working relationship gained through years of shared experience. We look forward to continuing our partnership with Kind & Co in the years to come.
Kind & Co www.kind-build.com
Services: Construction contractor
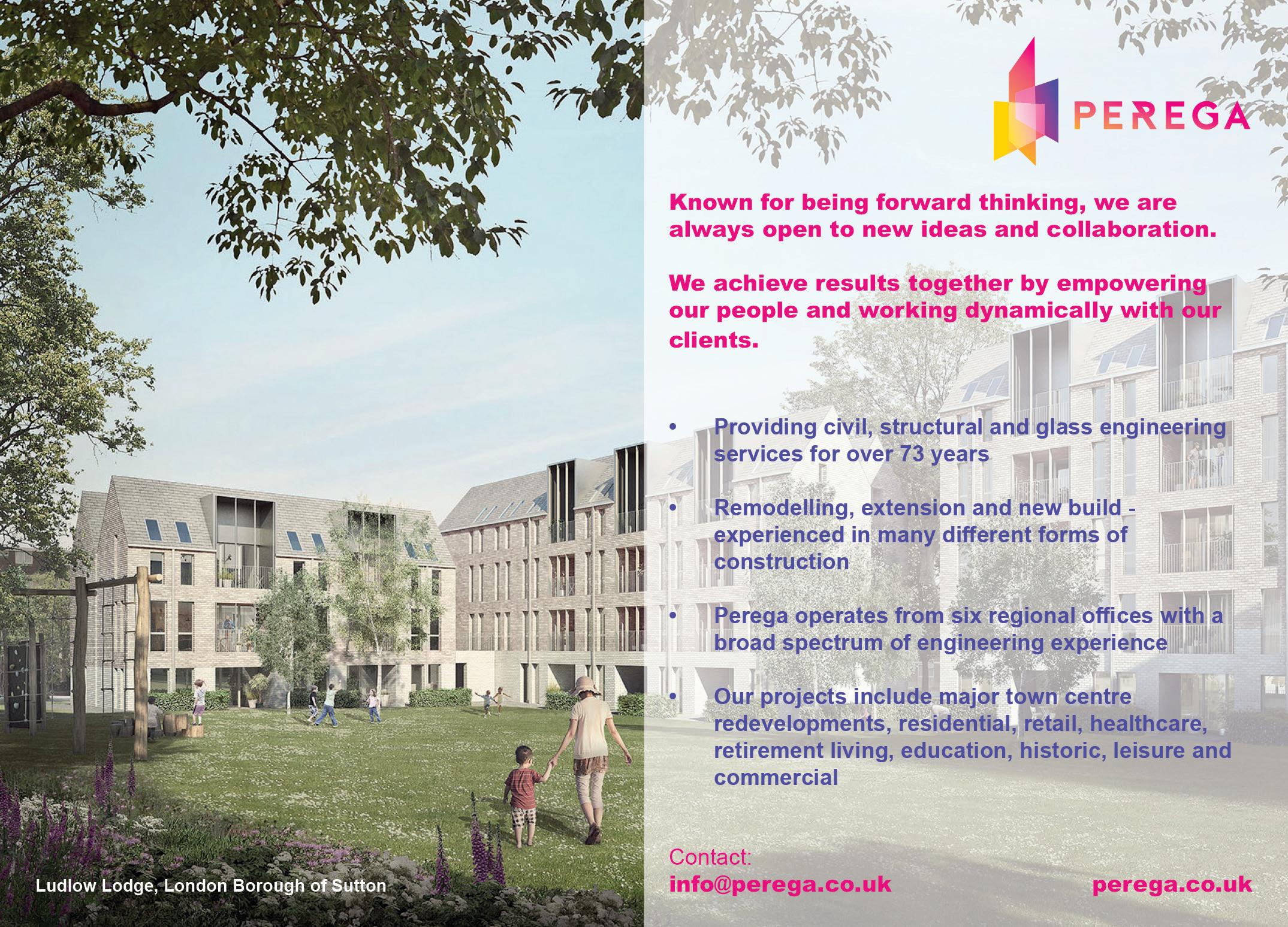
Fast and flexible housing
Operating for over six decades, Dutch modular housebuilder Jan Snel produces highly sustainable modular housing and apartment buildings based on circular economy principles
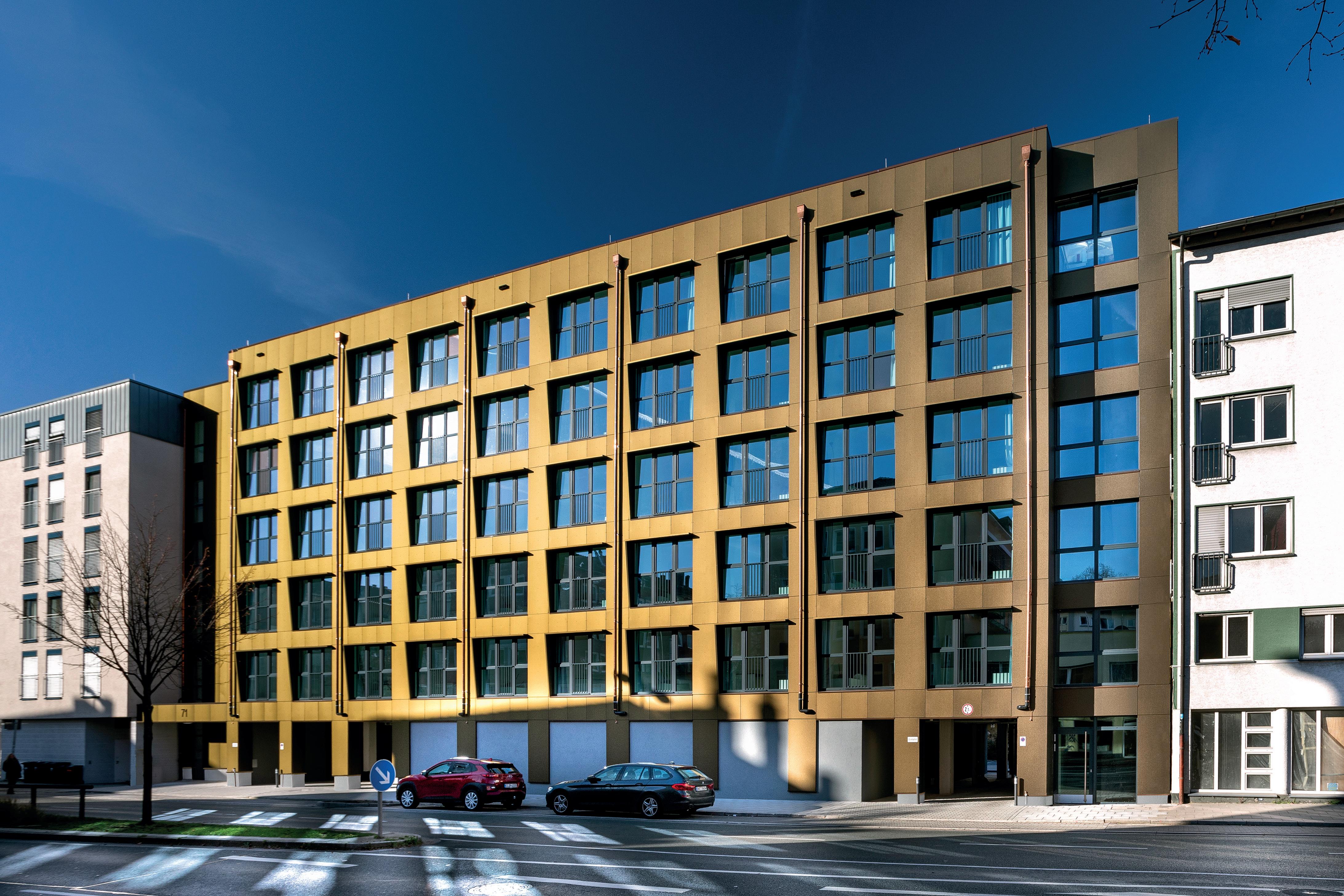
Campus 71, Essen (Germany). Jan Snel’s first major project in Germany where it delivered 106 flats in 12 weeks
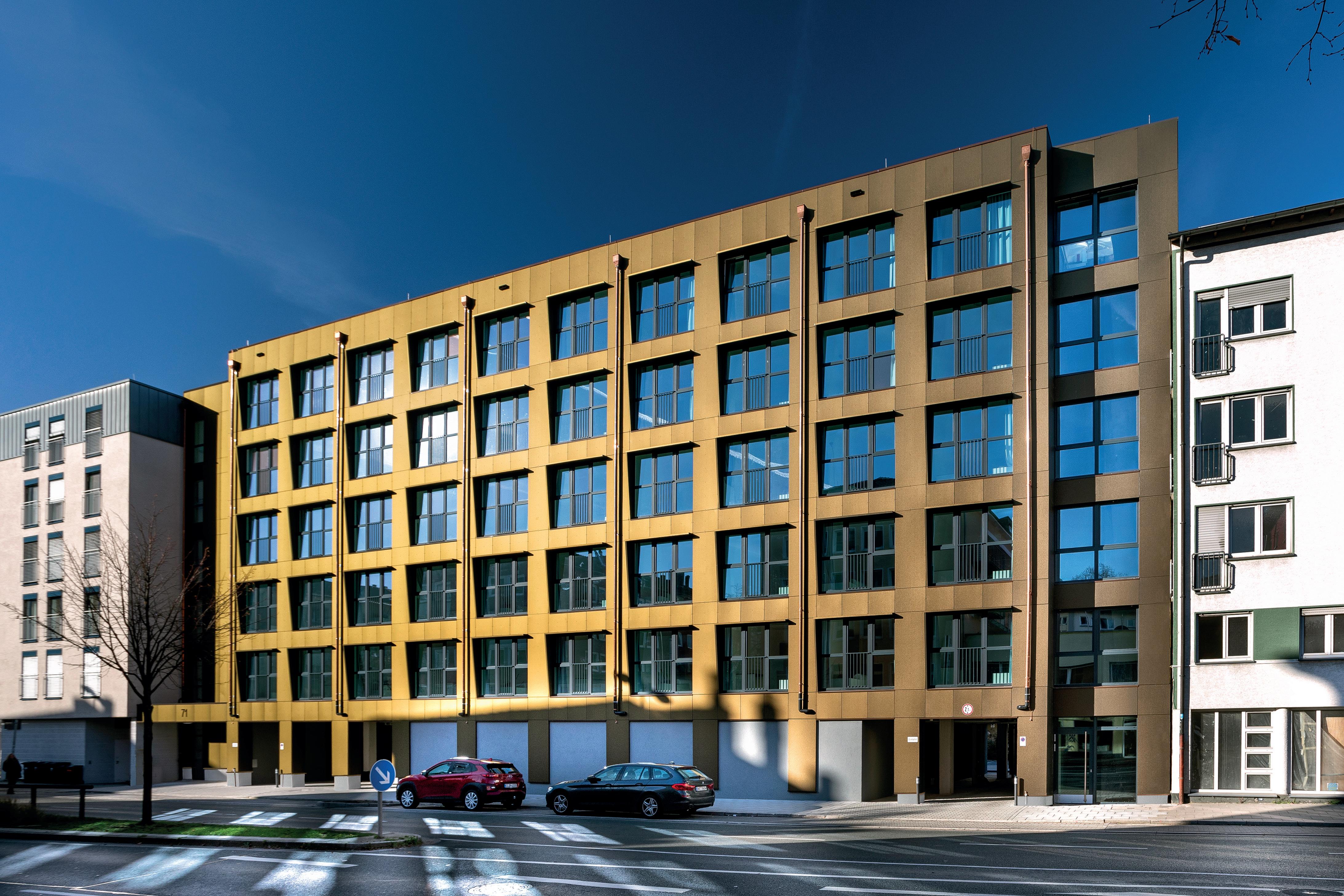
Keramus, Utrecht. Here Jan Snel built 232 student houses in 10 months
Established in 1960, Jan Snel Flexible Building (Jan Snel) actually began life as a business delivering milk churns in the municipality of Montfoort in the Netherlands, before extending into unit construction in the following years, and later becoming a fullyfledged modular construction company. Now, 60 years on, this €170 million turnover business is a leading, internationally operating company, boasting more than half a century of experience in flexible construction and specialised transport. With more than 550 employees, the company today has branches in the Dutch towns of Montfoort, Hulst and Eemshaven, as well as in SintNiklaas in Belgium, and Bochum in Germany, and Swansea in the UK.
“What we do here at Jan Snel is specialise in swift, modular and circular construction, which we carry out for several key market segments, most prominently the residential and healthcare sectors,” explains Richard Brinkman, Jan Snel’s Chief Financial Officer. “Our modules are put together within our own facilities, where around 85-to-90 per cent of the work is carried out, before being transported to their desired locations, where the remaining work is completed. Not only does our methodology result in lower build costs, but it also means that we possess a speed of work that is hard to match.”
In more recent times, the company has taken the decision to go a step further by constructing completely circularly as well. “This was not necessarily a massive leap for us, as our modules have
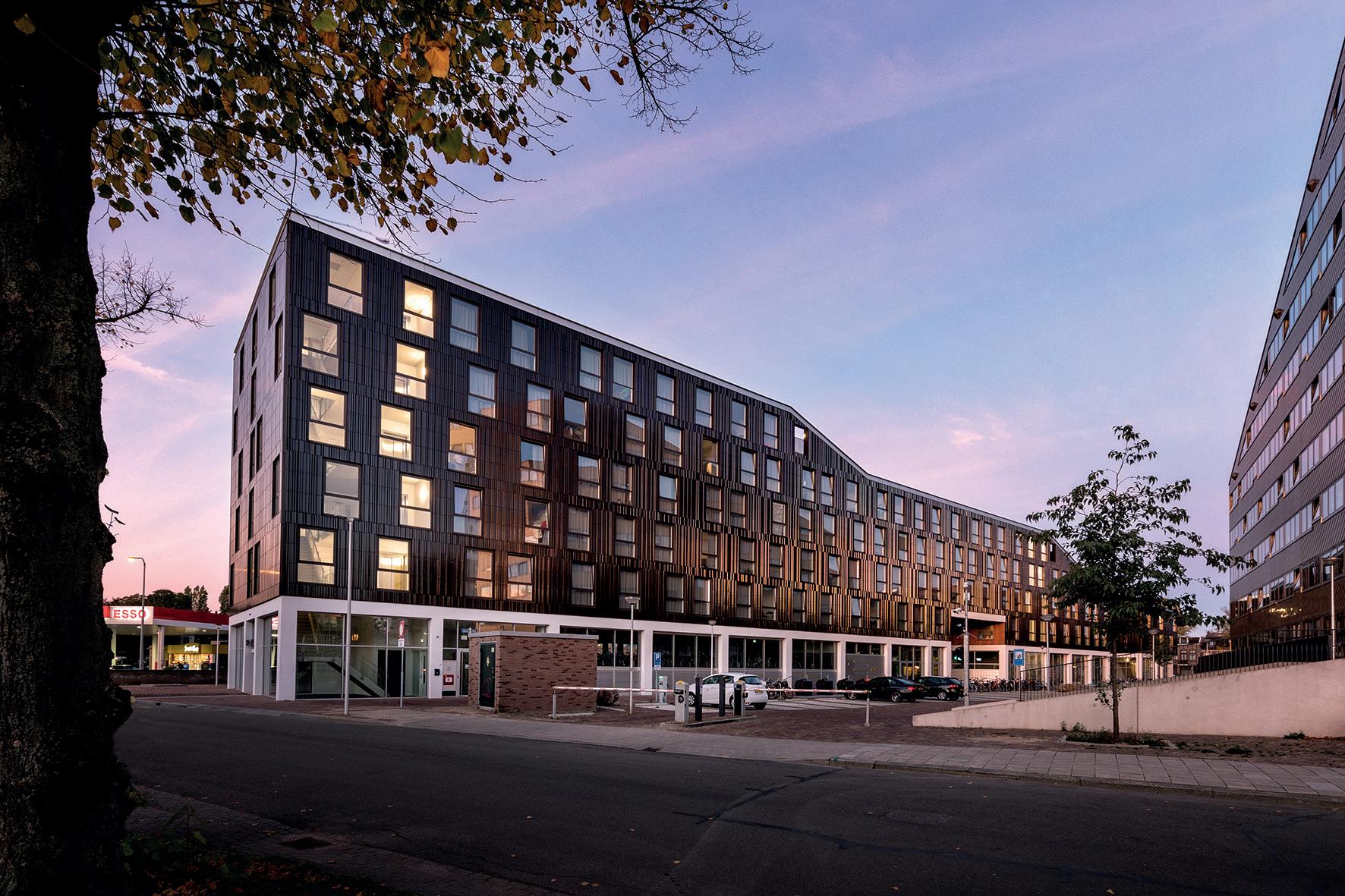
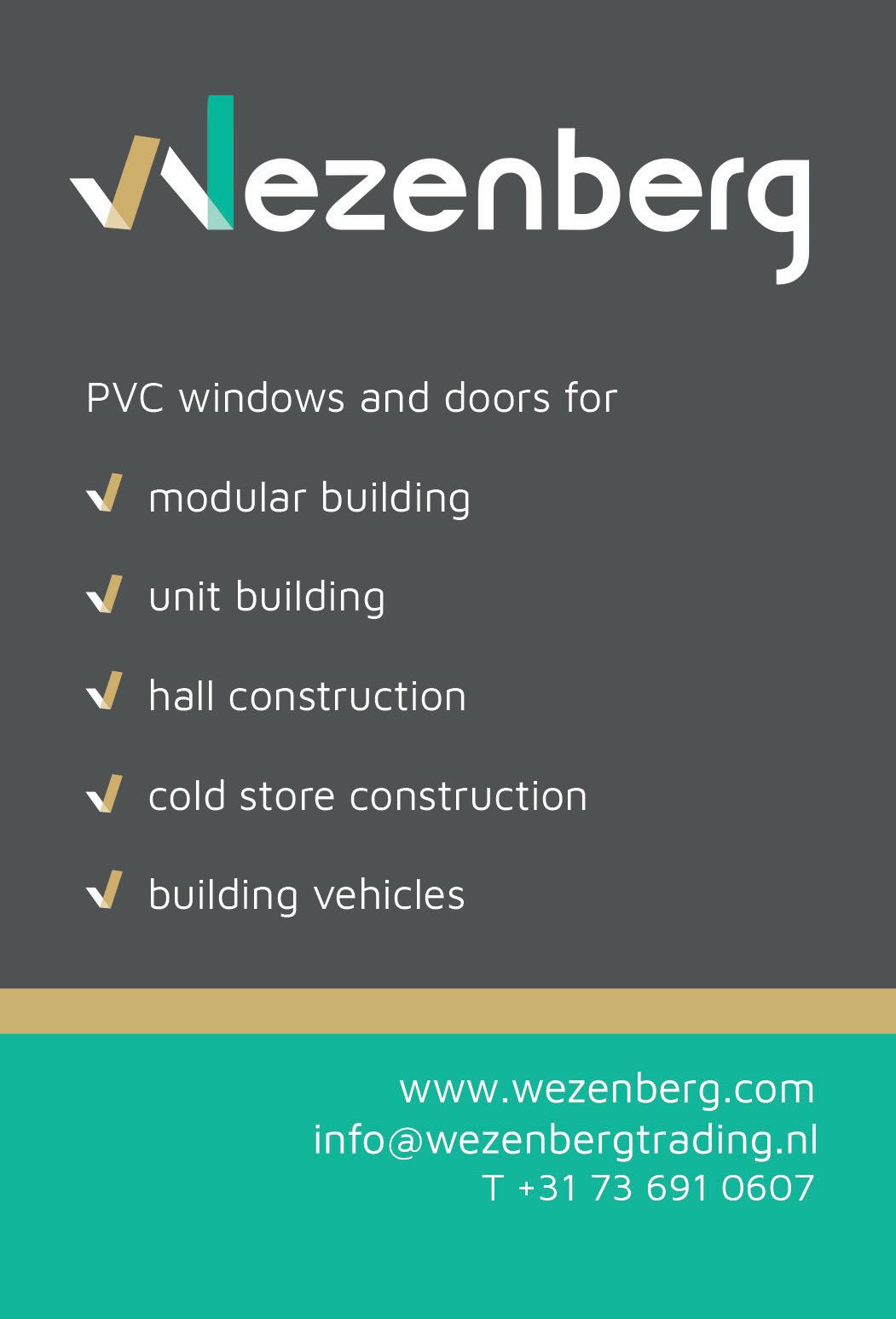
Wezenberg Trading
Wezenberg Trading have been the proud supplier of PVC windows and doors to Jan Snel in the Netherlands and Belgium for many years. The short communication lines, the no-nonsense mentality and the professional attitude in doing business characterize this constructive collaboration. We congratulate Jan Snel on its further international growth towards Great Britain.
been designed to be disassembled and reused after use, but it is one that is very important from a sustainability and environmental point of view, as it helps us to limit our footprint on the ground, especially when compared with that of traditional builders,” Richard continues.
Utilising its years of experience, Jan Snel prides itself on being able to realise flexible building that is seamlessly linked to its clients’ respective identity and unique user requirements. The result is a modular construction system that offers quality, fast and efficient housing solutions – whether they are temporary or permanent – as well solutions for markets such as the commercial sector, sports and events, building and industry, or educational settings. “Regardless of whether we are tasked with building a multi-storey apartment complex or a hospital operating theatre, we always apply the highest of standards to our work in order to ensure that we deliver the product to our client on time, and as agreed,” Richard states. “Not just meeting, but exceeding our clients’ expectations is without question one of our greatest strengths as a company, and has helped us massively in gaining the share of the market that we have to this day.”
The company’s website provides a number of fascinating case studies of its work in recent years, and Richard is happy to point out a few that stand out to him as well. “One example would be our work on the Ravel Residence project in Amsterdam, which involved the commissioning of 800 student flats, which we constructed in partnership with Student Experience,” he details. “It represents one of the first really large building projects that we undertook, with the first pile being driven in early April 2014, and completion realised in February 2015.
“More recently, we have finished the building of a block of 106
RVV Airconditioning
RVV Airconditioning has had a good relationship with Jan Snel for well over ten years.
RVV Airconditioning is proud to have a solid collaborative working relationship with Jan Snel, delivering many temporary schools, offices and care centres across The Netherlands. The relationship is built on the ability to communicate and work together effectively. It is a pleasure working with a company who are experts in their field.

For over 15 years RVV Airconditioning has supplied practical quality solutions in the field of indoor climate of offices, schools, hotels and temporary constructions. We continue to welcome new customers while serving our loyal customer base. RVV Airconditioning has got a good relationship for well over ten years with Jan Snel.
We offer highly competitive prices, lead times and have a dedicated team to handle each project. We are specialized in cooling, heating and ventilation. We use o.a. heat pumps, airconditioning, VRF, heat recovery.
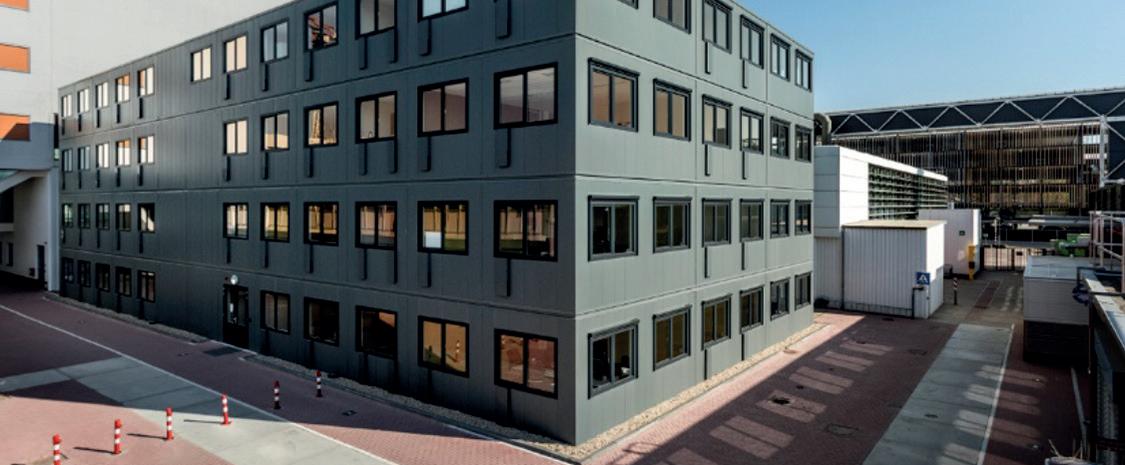
Tel: (+31) 085 070 31 07 | www.rvvairco.nl | info@rvvairco.nl
The construction of another big project in Bochum (Germany) where 700 student residences are currently being built in buildings of 10 and 12 floors high
apartments in Essen, Germany, in the centre of the city, which showcases our ability to deliver our product into congested locations. We are also currently busy delivering a 12-storey high student accommodation complex in the German town of Bochum, while in the health sector we are in the process of building a number of theatre rooms for different clients, which is a particular area of expertise that we are extremely proud to be able to deliver.”
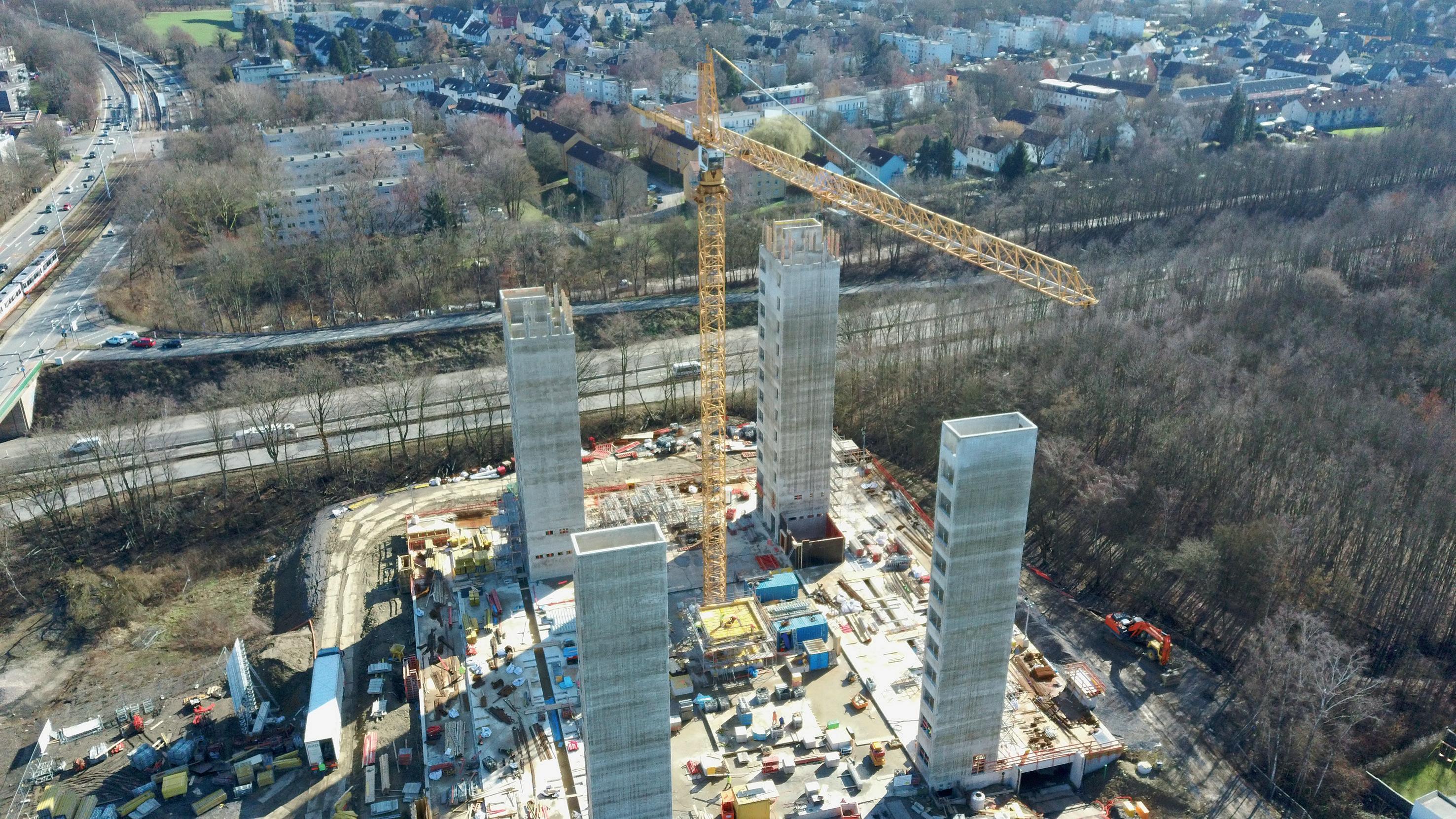
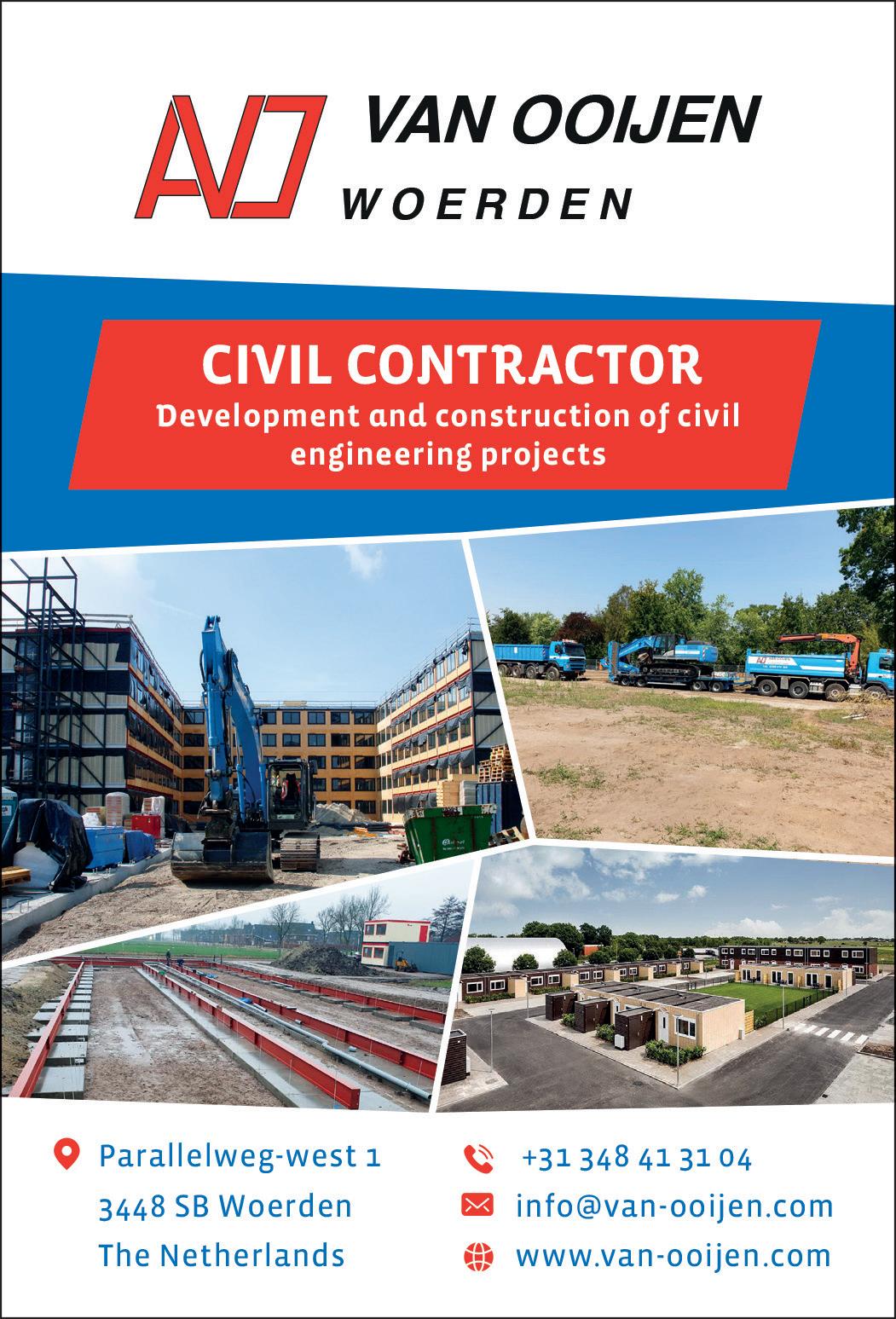
Combined expertise
Away from its work on the ground, one of the biggest recent developments to involve the company was officially announced in December 2020, when it was revealed that it had become a subsidiary of the publically traded Daiwa House Group (Daiwa House). Both Jan Snel and Daiwa House are forerunners in industrialised and modular building, with the latter being active already in Asia, North America and Australia. Together, the two intend to further expand their respect modular building businesses within the European market by combining global knowledge, manpower and solutions.
“In Daiwa House, we have gained a powerful partner, whose own resources and expertise in industrial building will help us to grow and move closer towards where we want to be, which is the clear market leader in our field in Europe,” Richard enthuses. For Daiwa House, this partnership represents its first footsteps into Europe, and opens up a number of exciting potential markets, including the Benelux, Germany, the UK, the Nordic countries, and eventually Eastern and Southern Europe. “By combining our solutions and expertise with the strength of Daiwa House, we believe that we are laying the foundations for a strong, prosperous future!”
The above development brought to a close what was overall a good year for Jan Snel, with Richard estimating it to have achieved year-on-year growth of around 30 per cent. It is hoped that now, through a combination of increased demand for temporary housing solutions across the continent, a rise in government investment in housing – particularly that which is achieved through more sustainable means – in its core markets, and its partnership with Daiwa House, that a similar figure will be achieved in 2021.
“For the next few months of 2021, it is important that we facilitate and achieve good integration alongside Daiwa House,” Richard says. “From our negotiations and time spent with one another already, both parties already have a clear understanding of each other, but we want that to get even stronger as we start to learn more about our respective capabilities, and share concepts and ideas on a range of different things, from the development of materials to robotisation in the manufacturing process.”
At the same time, the company believes it is important for its future to continue to expand in what it sees as being important markets, such as Germany and the UK. It is in the latter where Jan Snel has recently opened offices in Swansea, Wales. From here, it aims to service the housing sector’s urgent need for highquality accommodation that can be delivered quickly. With modular construction being an ideal solution to this problem, establishing a UK office will allow the company to meet said need expediently. Jan Snel is already working on an exciting project with developer Abode Waterstone and housing association Coastal Housing Group to provide affordable homes on the former oil refinery site in the Coed Darcy urban village in South Wales.
Ravel, Amsterdam (Netherlands). This was the first major housing project in the Netherlands where Jan Snel built 800 student dwellings in only 11 months
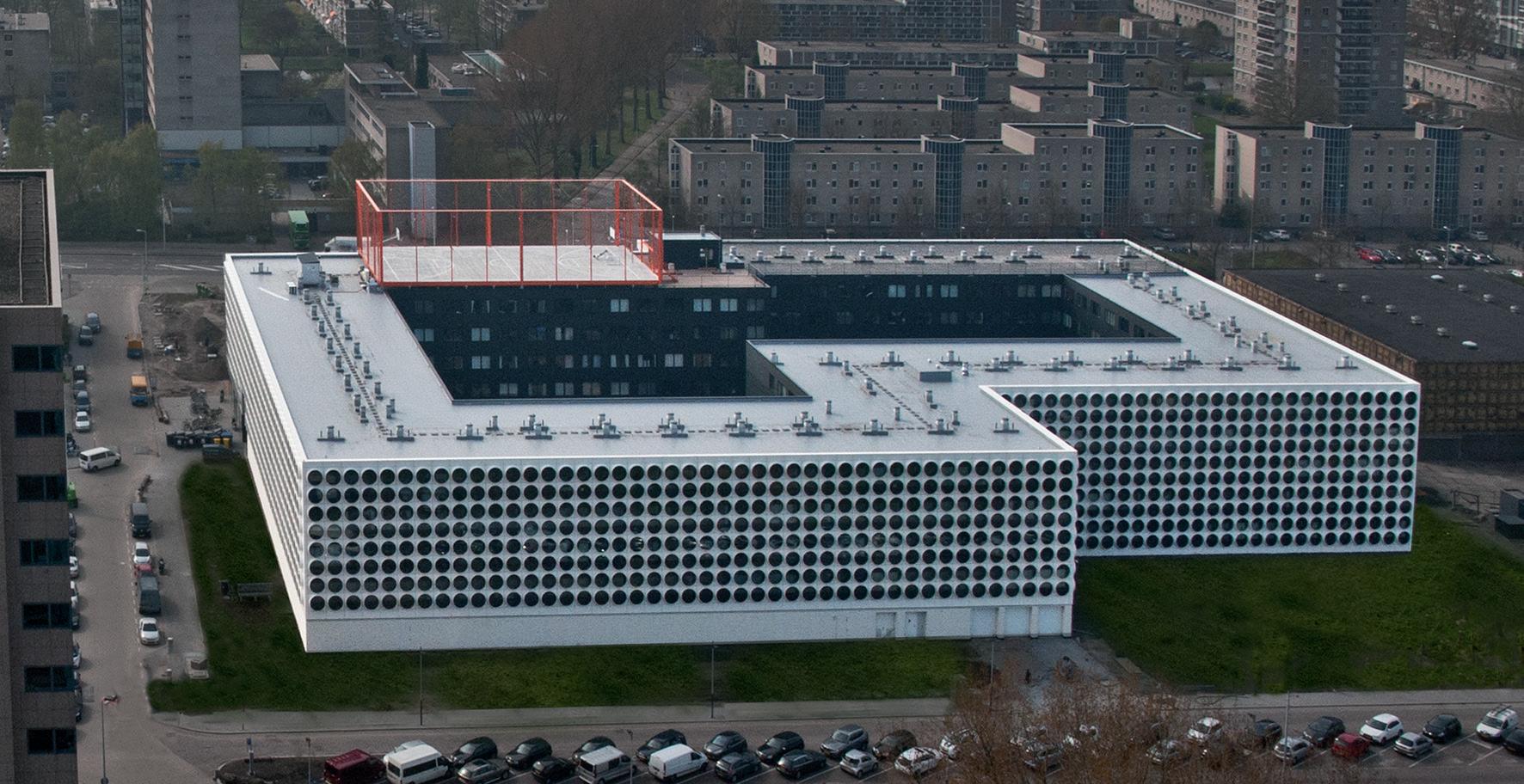
The natural next step on from this will be to look at opening new factories in markets such as the UK, and the company is already in early stage discussions about this possibility with representatives of the Welsh Government. “The establishing of a factory in somewhere such as Wales will only help to accelerate the growth of the business, while also allowing us to bring more jobs to the local area and contributing even more so to the local economy,” Richard adds. “This is a development that we hope to press forward with in the coming months, with the longer-term view of having assets operating in 2022, not just in the UK but in other countries such as Germany also.”
Services: Modular and circular construction
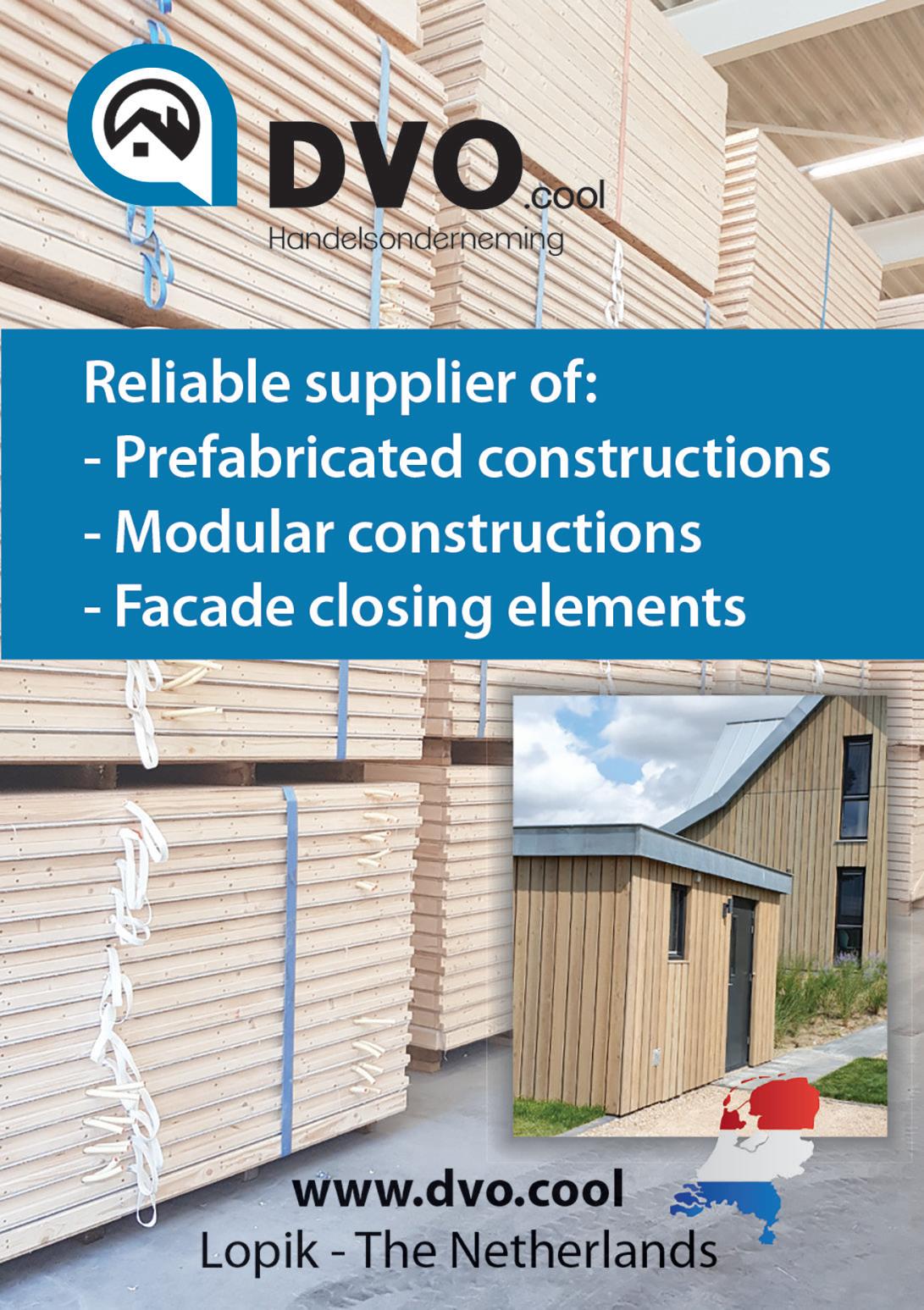
Lite-ing the way
For over 20 years, Litecast has been recognized as being a leading manufacturer of precast concrete floor beams in the UK, and a new purpose-built production facility stands to take the company to a whole new level
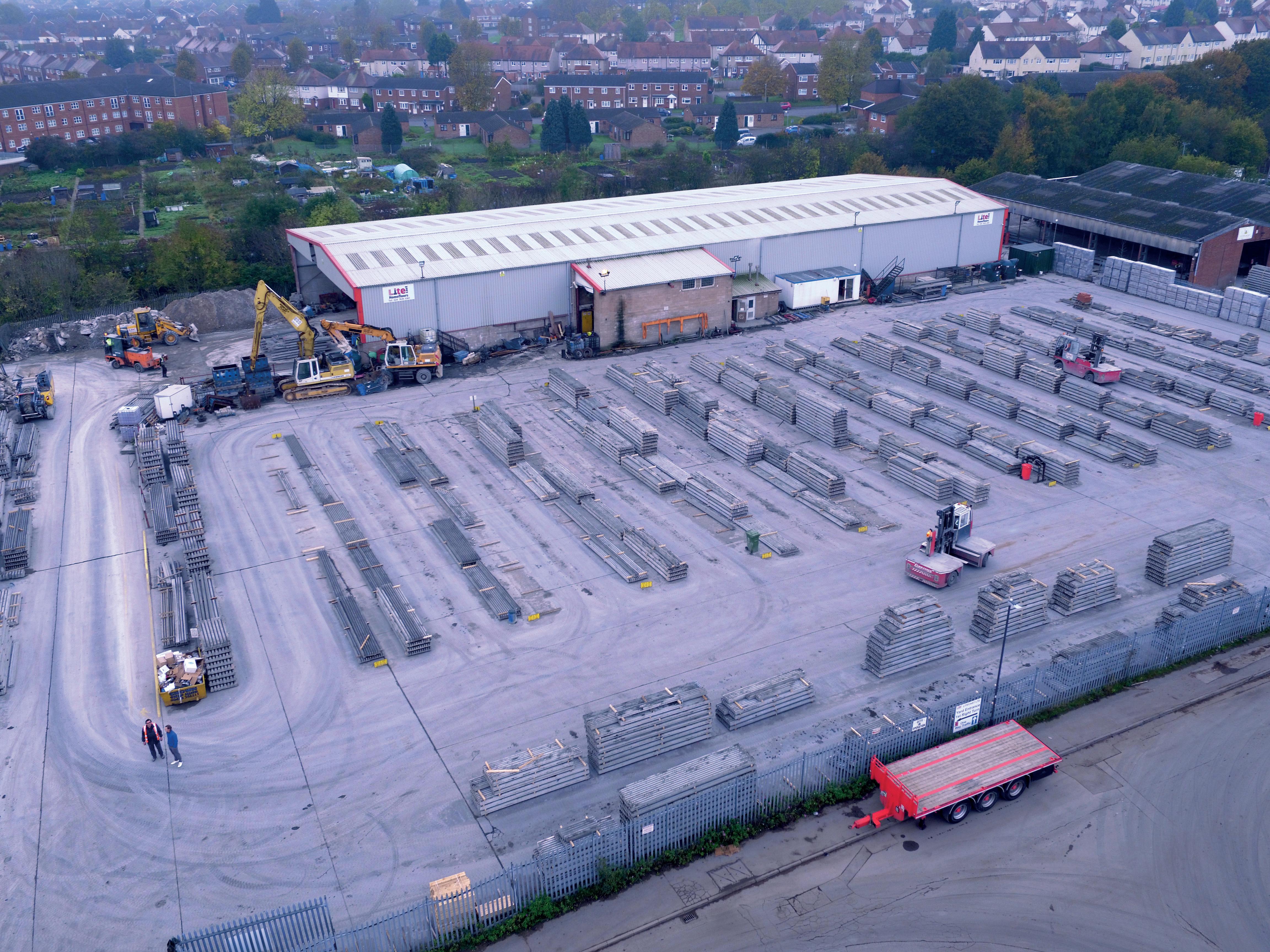
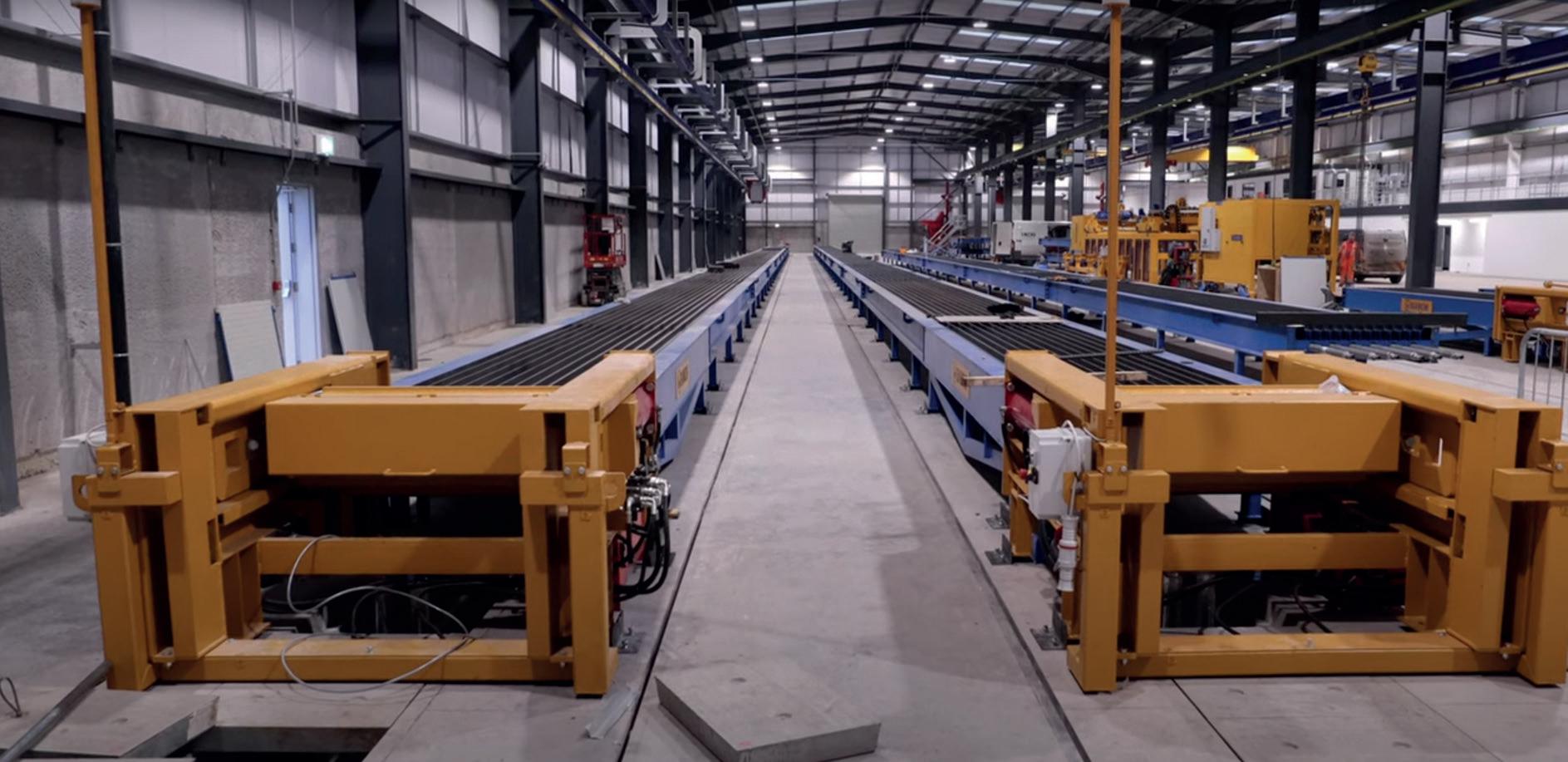
The formation of Litecast – a precast concrete business, based in Nuneaton, Warwickshire, and specialising in the manufacture of concrete floor beams – came about in somewhat unique circumstances. It was brought to life by four individuals who had previously worked together at a company by the name of Earthspan, but who were collectively made redundant following its acquisition by Tarmac.
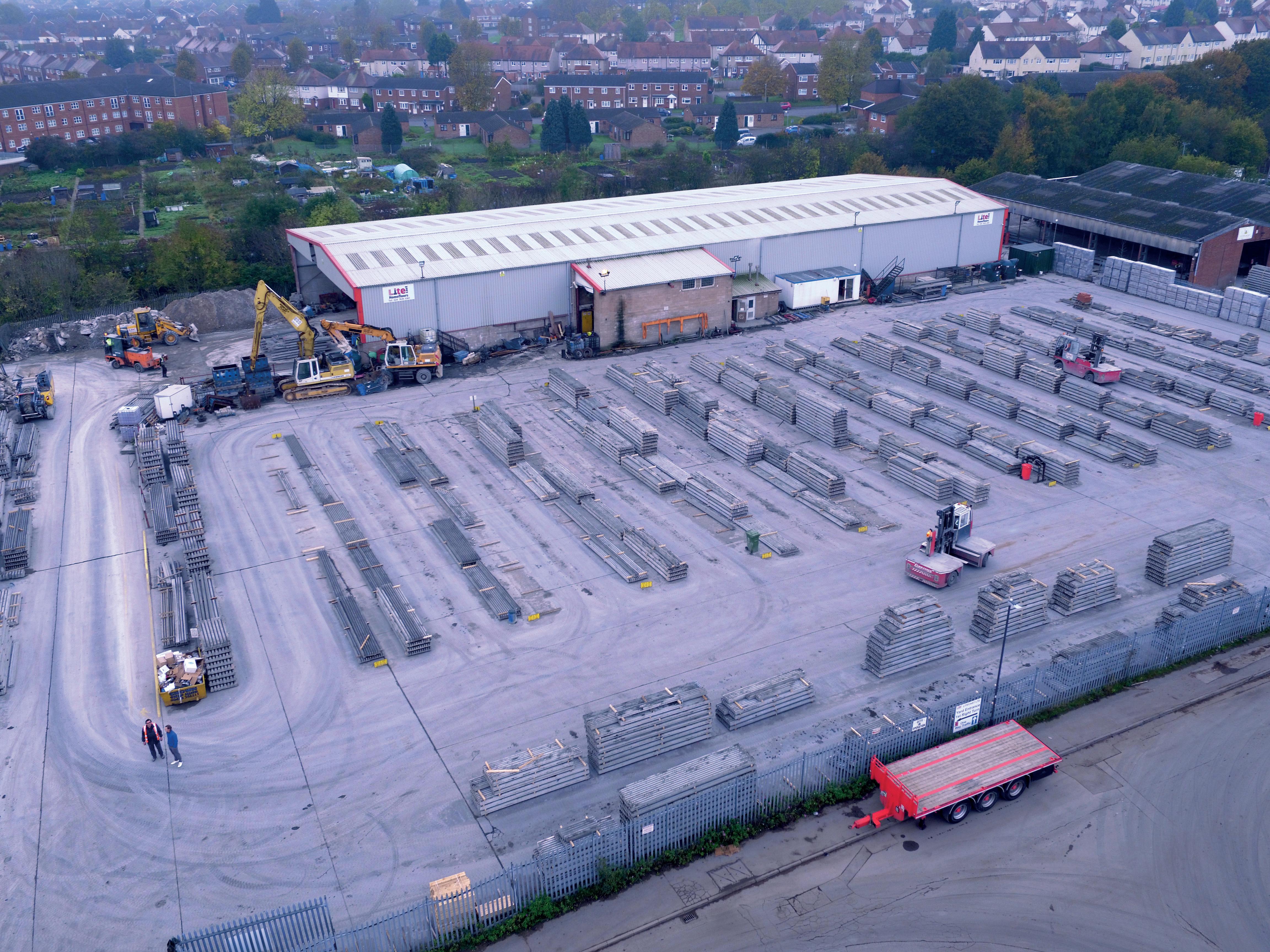
The ground source heat system ground loop being installed in the field adjacent to the site of the new factory
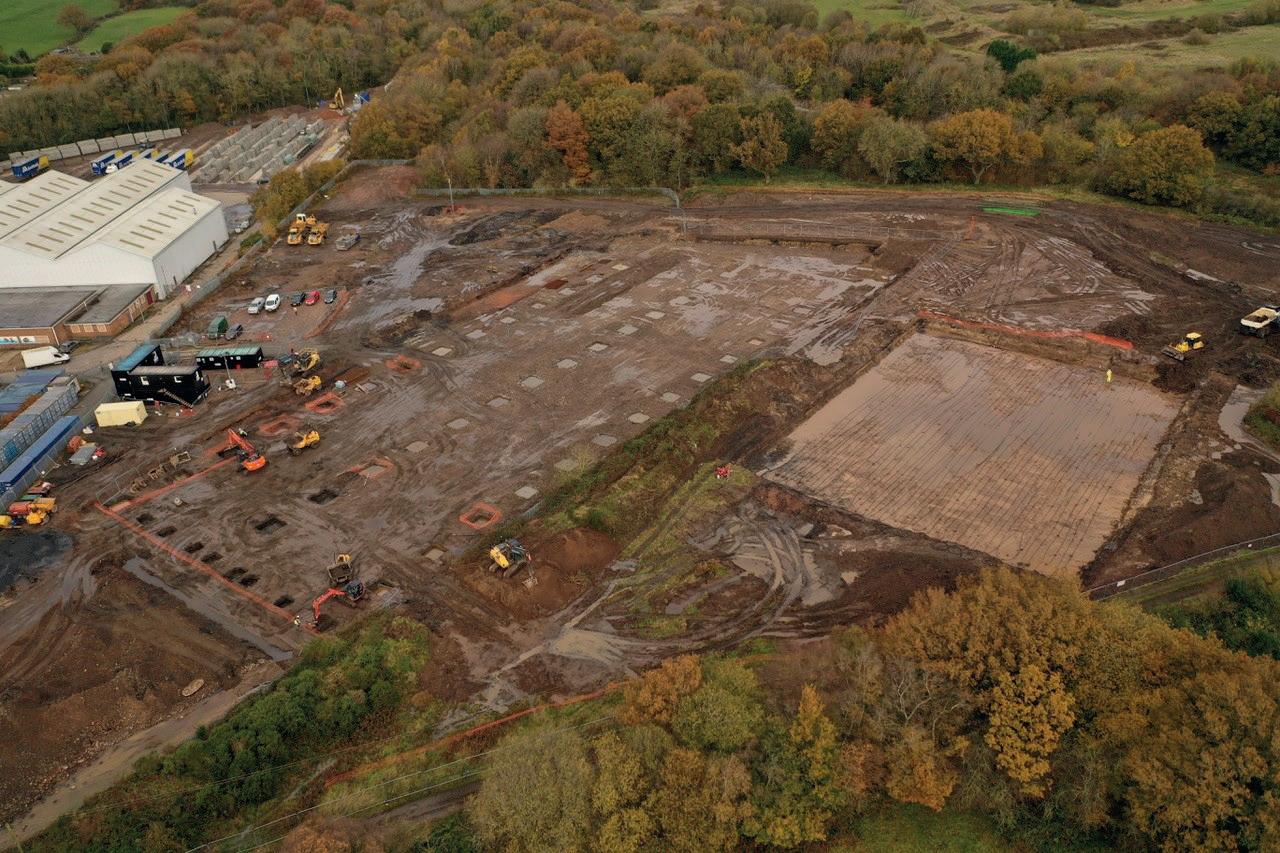
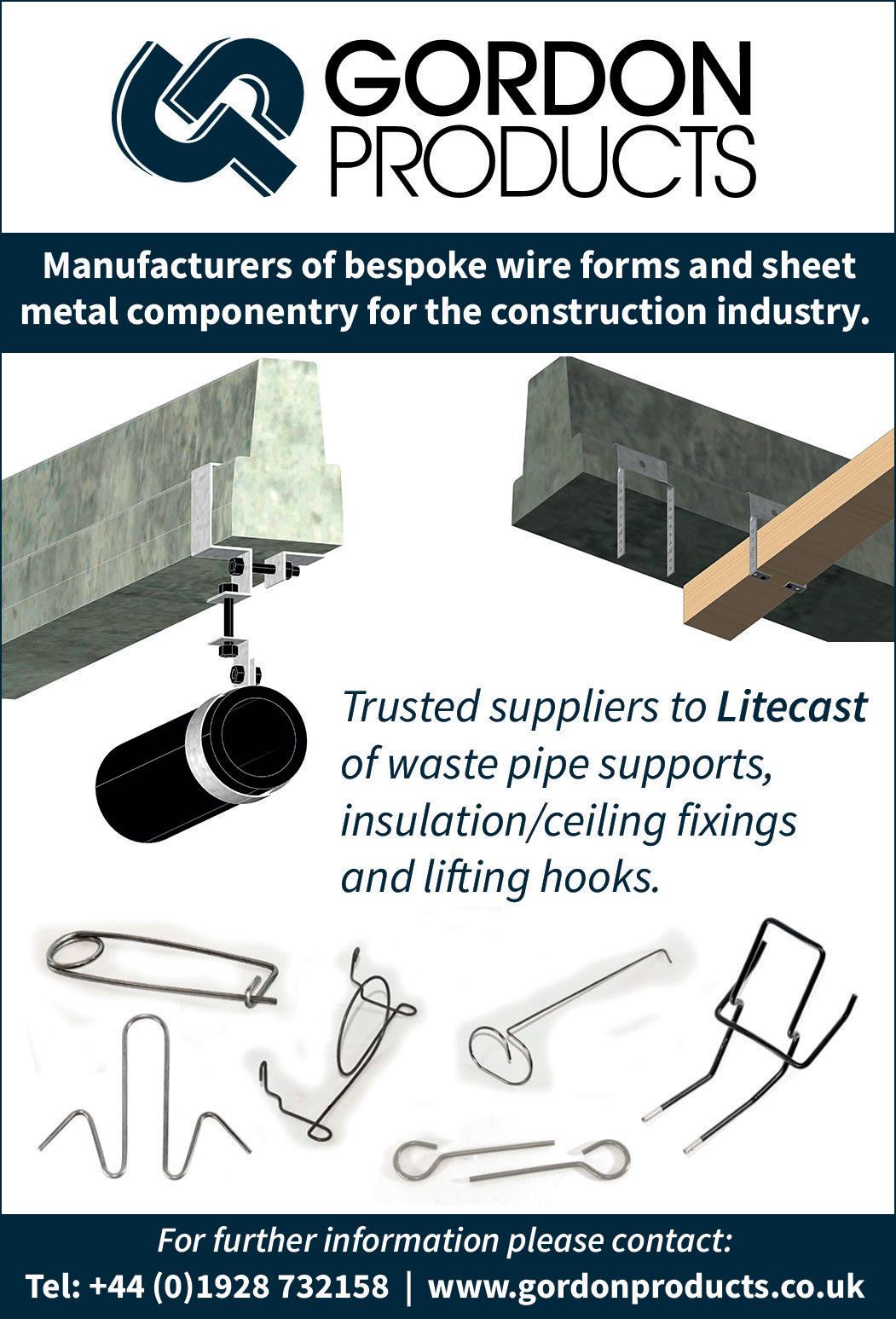
With their redundancy money, the group set about creating Litecast, which made a similar, but vastly improved, lightweight T-beam for the residential building sector.
Digital transformation
In the years that followed, Litecast quickly established itself as a leading supplier of construction materials, and an integral part of the UK construction industry’s supply chain, manufacturing in excess of 42,000 linear metres of concrete beams each week. In 2016, the company would purchase the Purely Chase Industrial Estate in Ansley Common, Nuneaton – once the home of Earthspan – with a view to erecting a purpose-built production facility that would enable Litecast to become landlord-free for the first time.
“Today, Litecast predominantly manufactures pre-stressed, pre-cast 150mm deep T-beams for domestic/residential purposes,” explains Managing Director, Jonny Leroux. “We also manufacture a 225mm deep beam for commercial use, but this constitutes less than five per cent of our revenue. More recently, we have begun manufacture of precast Insulated Wall Panels and interlocking/castellated blocks, initially for our own use within the new factory, but ultimately to take to market.”
The growth of the business is clear for anyone to see, but what is it that Jonny feels sets Litecast apart from others within its space? “For one, it is our service levels,” he declares. “Also, in the last five years especially, we have undergone a significant, £1 million digital transformation. This has created an environment in which we have been a paperless organization for over two years now, with our entire office being operated from a bespoke system called ‘ELSIE’. This system processes every aspect of the business, from receipt of
enquiry to invoicing, and includes all design, quotation, order placement, production planning and transport scheduling. ELSIE has ensured our lead-times have remained un-hindered for three years now at three-to-five working days, and has meant that even throughout the Covid-19 pandemic and its associated lockdowns, we haven’t needed to extend our lead-times beyond five working days.
“Approximately 89 per cent of enquiries that we receive are quoted (with detailed design drawings, which include thermal calculations for our EPS floors) within 48 hours. Providing designs with quotation ensures our lead-time upon receipt of order is unrivalled in the industry. Additionally, it means we don’t have to provide estimates, the prices we are quoted are accurate to the penny and based on a detailed bill of materials taken from the design.”
Record months
One of the many other unique features of ELSIE is its ‘transport bolt-on’ feature, which allows the company to automatically inform customers if a truck is in their area with spare capacity. The customer is offered a discount if they can take the beams on that date, and Litecast benefits from improved efficiency as well as reducing its impact on the environment by maximizing the weight of beams on every truck movement.
While most of Litecast’s competitors opted to close in the early days of the first lockdown back in March 2020, the fact that it was already a paperless company allowed its offices to function normally with just two of its usual 23 employees in attendance. “We initially furloughed most of the workforce, but it quickly became apparent that we were the only beam manufacturer in the country who were still operating, so we soon reversed that decision,”
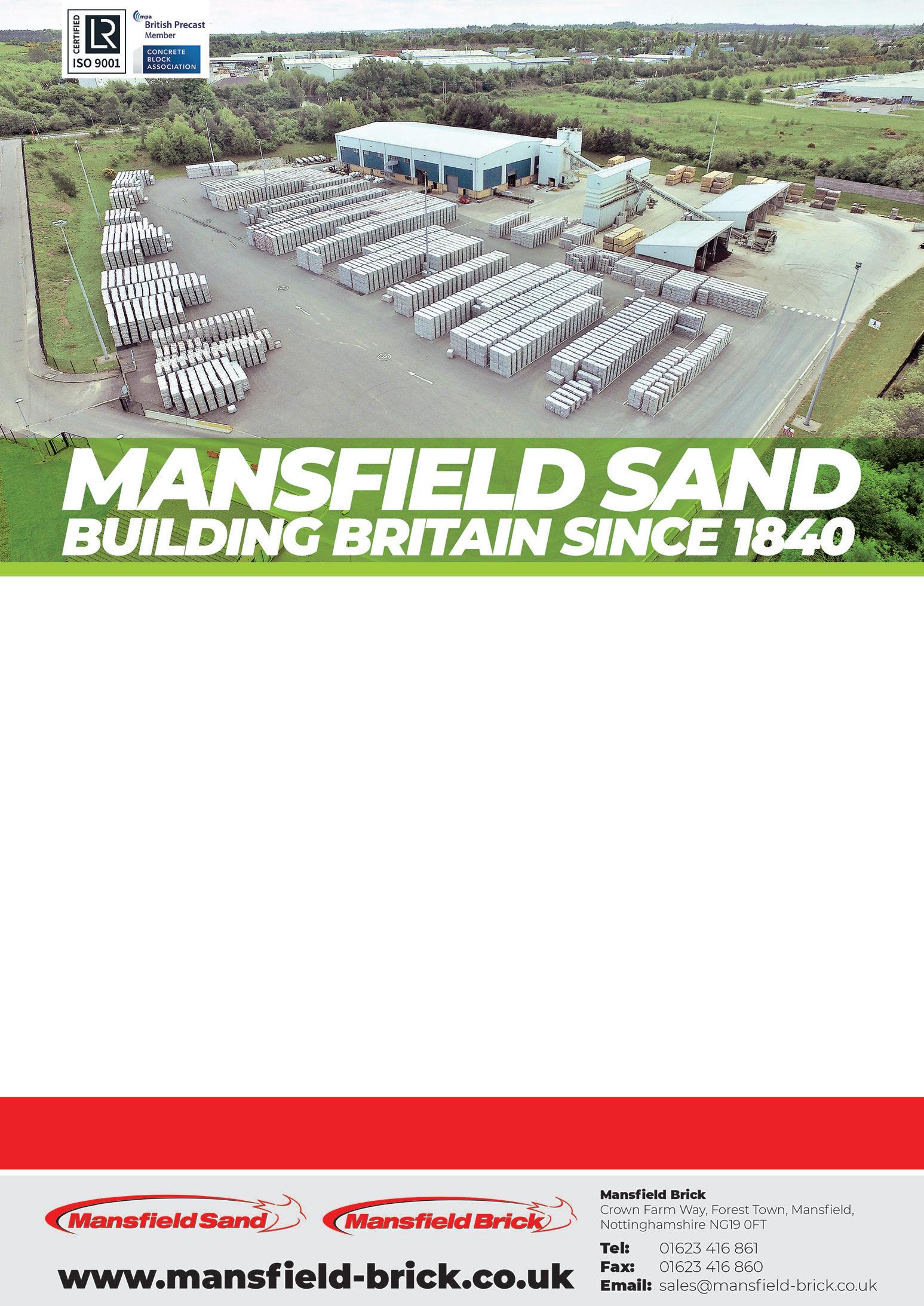
Mansfield Brick
The relationship between Litecast and Mansfield Brick is longstanding, spanning almost two decades and predating the current board of Directors at both organisations. The companies share the same ethos of providing high levels of service and quality products at competitive rates; the reason that Litecast use Mansfield Brick exclusively for the supply of their masonry ancillary items. It is this ethos that has been the driving force behind the success of the two organisations, seeing them through both the peaks and troughs of construction and the housing market and the recession of 2008.
Mansfield Sand Company has pioneered the development and production of premium quality silica sand-based products for over 170 years.
Our core silica sand products include:
t AwiderangeofmaterialsforIndustrialapplicationsincluding pavior/kilndriedsands We t alsosupplyspecialistmaterialsforequestriansurfaces, construction/renovationofgolfcoursesandfootballpitches, forbothmainstadiumandtraininggrounds. Supplyingmajorbuildersmerchants,buyinggroupsandfloorbeammanufacturerswhilstofferingover20 differentconcretebrickandbespokeproductstomeettheneedsoftheconstructionindustryforareassuchas: t ClosureBlocksandTrayTiles CoursingBricksandCommons SlipsandInfills
Mansfield Sand’s Brick Division produce over 30 million concrete brick products ranging from concrete commons and coursings to brick slips and closure blocks.
t t
Mansfield Brick supply all closure blocks and brick slips that are utilised within Litecast’s Precast Flooring Solutions
Jonny adds. “During the course of April, May and June 2020, we picked up over 200 new clients, many of whom have stuck with Litecast even though their previous supplier has since reopened. Other than an initial lull in April/May, when the building
Previously, we noted the company’s plans for its purposebuilt production facility, and Jonny is happy to provide more detail as to what Litecast has in mind for it. “Our new facility takes our production capacity from 42,000 linear up to 72,000 metres per week,” he reveals. “Total investment is calculated at over £10 million, and the project has taken over five years from start to finish.”
sites were mostly closed, we’ve been having record months for the last six months or so. Enquiries remain at record levels, and our conversion rate from enquiry to order is higher than ever at 47 per cent as we sit here in February 2021.”
The concrete bullet skip delivery system filling one of the beds
The bandsaw machine cutting the wires between the beams – negating the need for staff to stand on the beds which had been highlighted as a H&S concern
Green ambitions
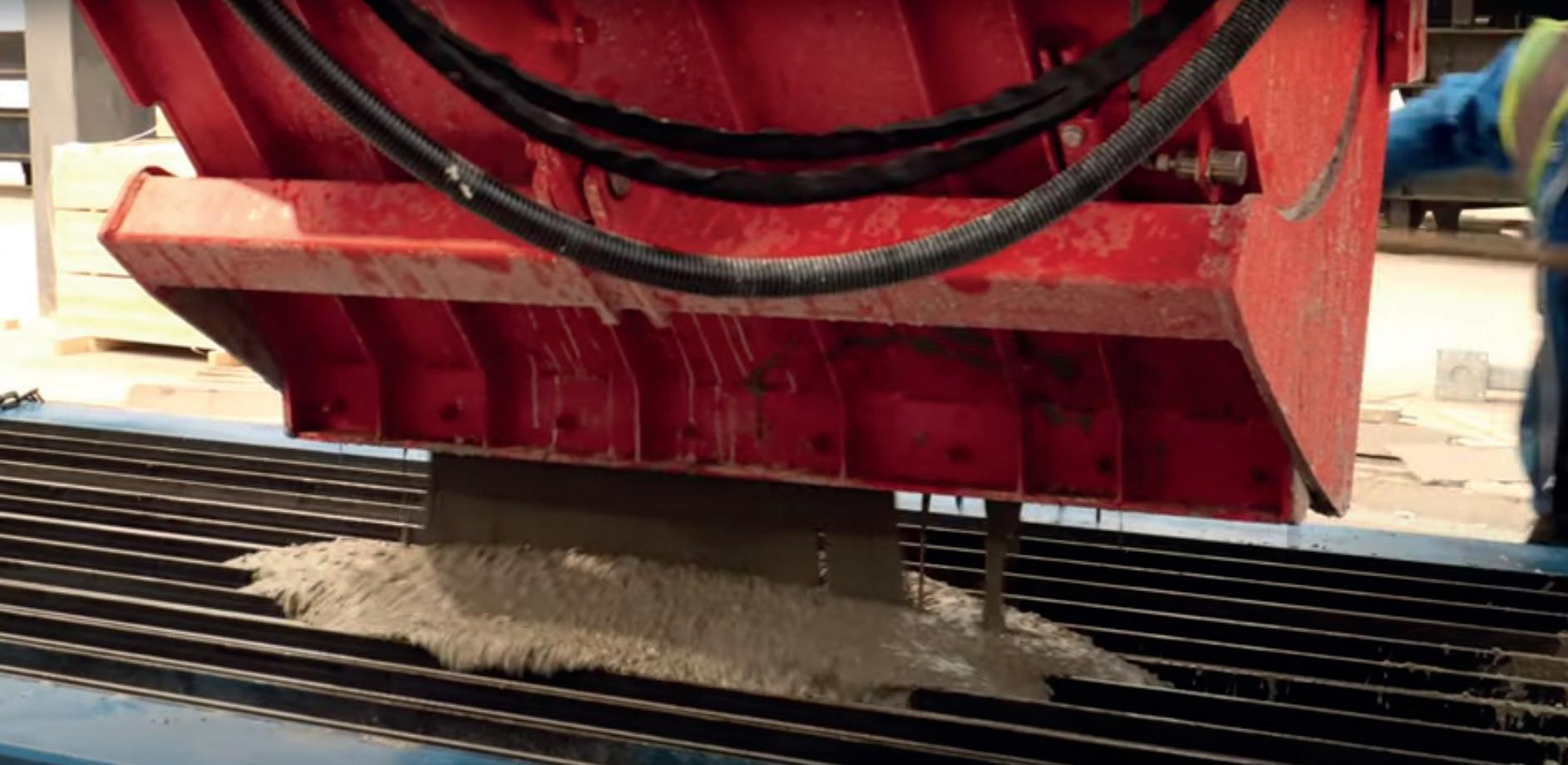
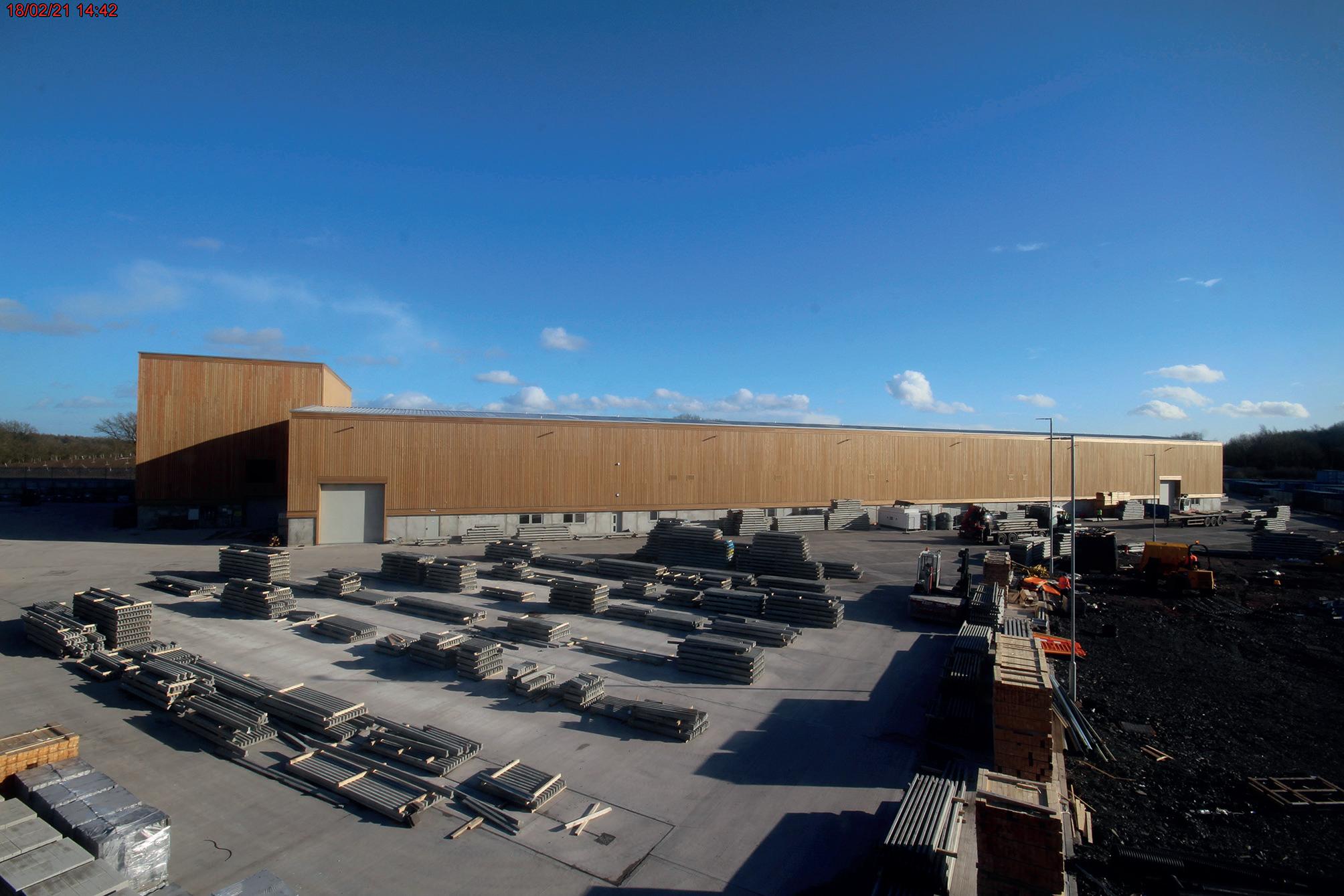
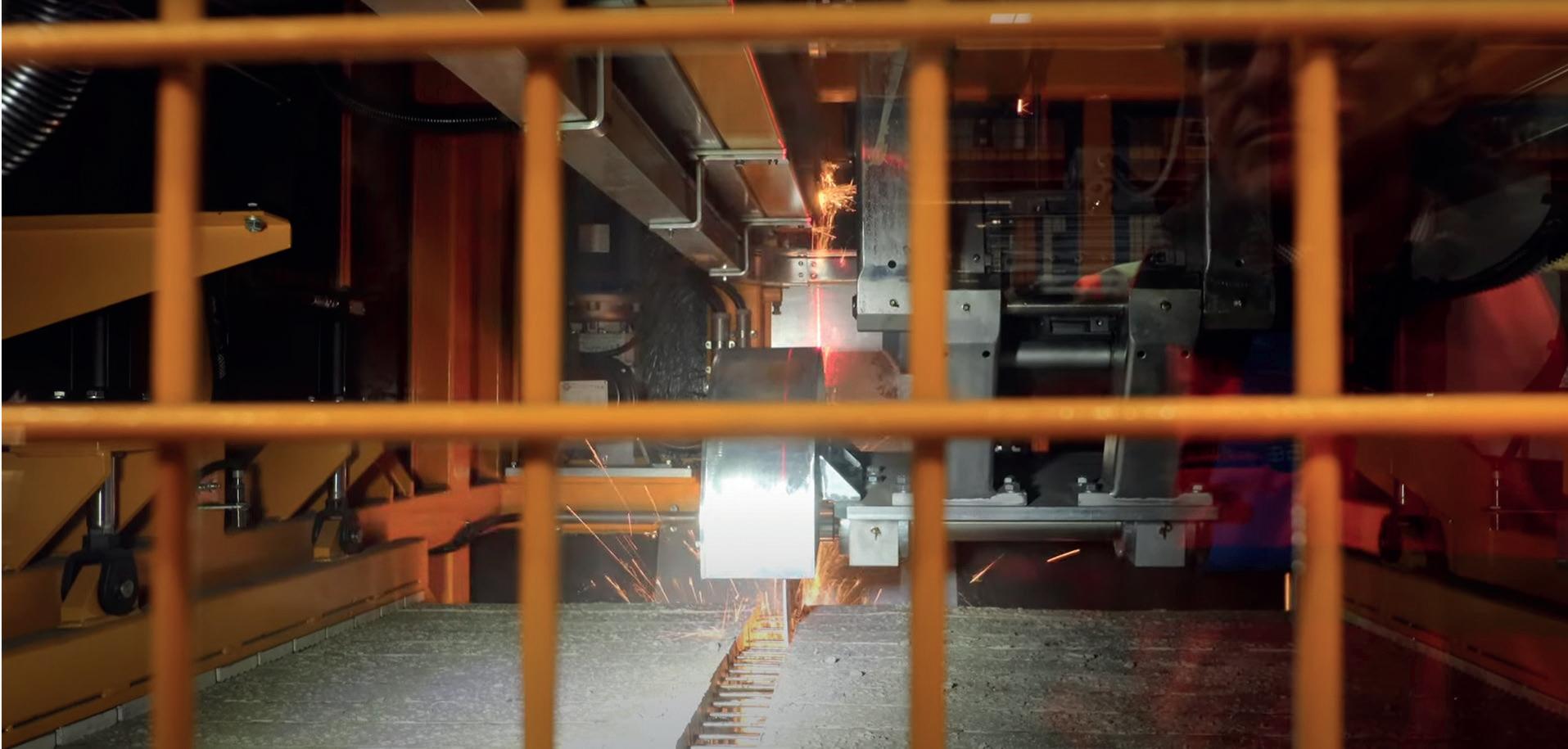
The new facility incorporates both bespoke and brand new machinery that the company believes will revolutionize its industry. “These machines have been designed by ourselves, and through the combined efforts of individuals such as our Works Director, Andrew Hall, and our Maintenance Manager, Steve Smith, we have come up with three machines that massively reduce the labour involved, as well as improving safety, reducing noise and cutting waste,” Jonny enthuses. “Firstly, there is a machine that sweeps the beds, oils the beds and pulls the wires down the length of the bed all at that same time, operated by one man with a remote. Secondly, there is a machine that lifts the beams from the beds and rotates the beams to stack them, and thirdly, there is a band saw that cuts the wires between the beams. We have proven all three machines in a laboratory environment, but are currently commissioning them in the real world.”
Jonny goes on to state how the ultimate vision for the new facility is for it to be Carbon Neutral. “We aim to achieve this through a combination of sustainable energy and significant investment in insulation. The heat for the concrete moulds comes from an extensive ground source array which feeds four heat pumps. Additionally, the ground source heat system is used to heat the water that is used in the concrete mix, which
reduces the required cement content levels, further reducing our carbon consumption. We have also installed a massive PV (solar panel) array on the roof of the factory, and are hoping to get the majority of our electricity from this.
“There is no gas to site, mains or tank, and the entire building is well insulated, including the batching plant and aggregate bins. This ensures that we are able to cast all year round regardless of external weather conditions. Improvements have also been made to employee welfare, in that the new facility is warmer, safer, quieter and cleaner than the old factory, and there are number of health and safety benefits, too.”
With the ground source heat pumps now operational, the plan for the next six months or so, is to get the new facility up to 100 per cent capacity, and then to begin double-casting to meet increasing demand. The insulated building, efficient heat to the insulated beds and heated concrete mix were all factors considered by the
JW Morley
“Having started working alongside Litecast Homefloors a year after the company began in 1998, I have seen immense changes as they have developed. They have always supported me and the growth of Morley’s Transport into the successful business it has become today. “Originally I started as an owner driver with a 7.5t Flatbed and now we operate 7 x 32t Hiab Euro 6 trucks on a daily basis with them. Plus, a further 5 larger Hiabs with a maximum reach of 26m. “The new state-of-the-art facility is great news for us as a principal supplier and Morley’s wish Litecast all the very best for the future and our continued relationship.” James Morley, Founder, JW Morley
company when aiming to doublecast in its new factory.
Looking further ahead, however, Jonny envisions more investment and advances for the business to come. “Litecast is exceptionally well located, being just a few miles from the geographic centre of England, however, there are logistical issues when we try and delivery to the more remote corners of the country. Therefore, an obvious progression for us would be to invest in additional facilities (initially just for stocking beams, but ultimately for production as well) in the South West and/or South East of England,” he concludes.
Litecast www.litecast.co.uk
Products: Pre-cast concrete beams
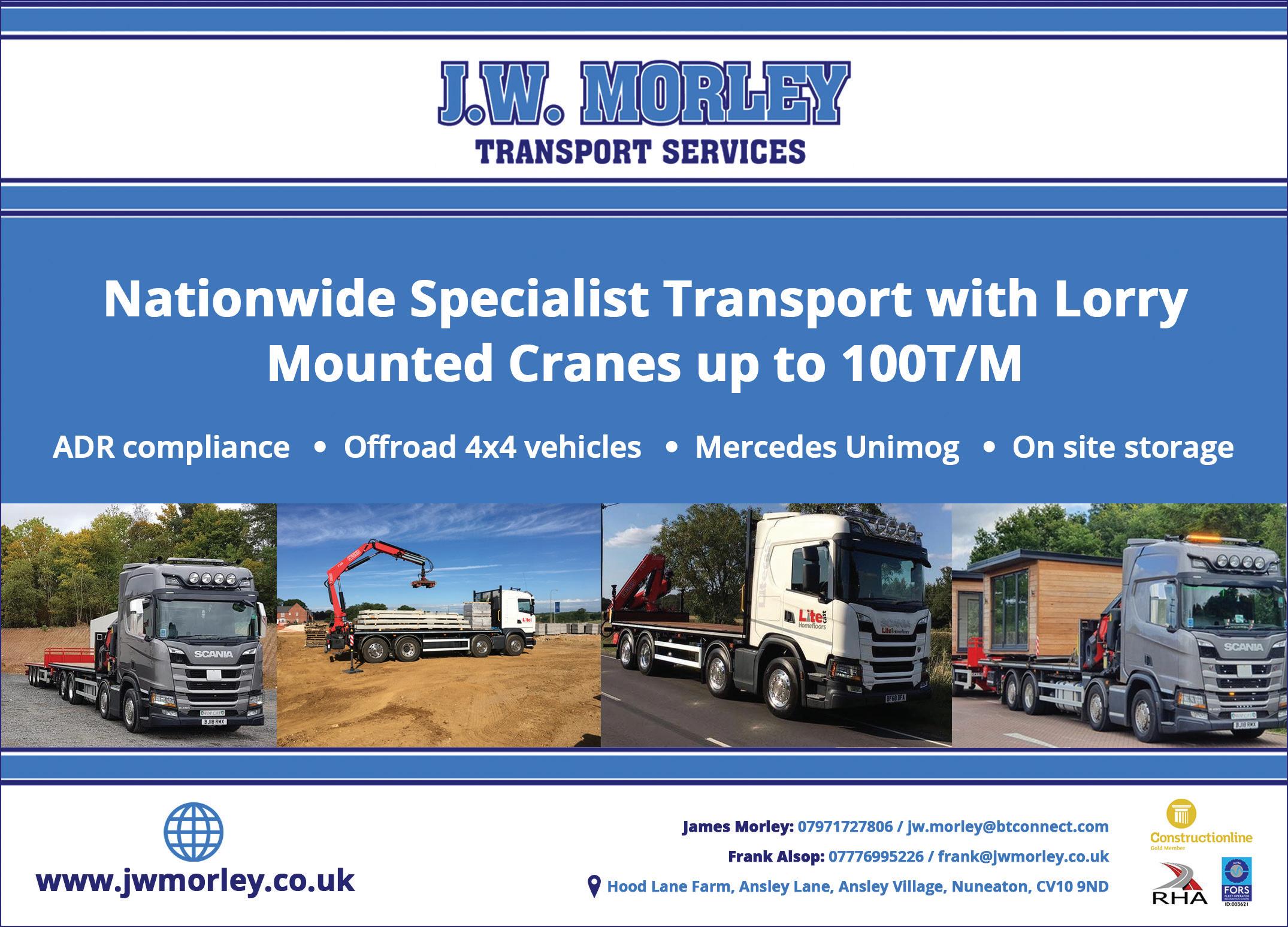
A solid position
Proud to state that it has been ‘building the face of Britain for over 200 years’ Ibstock plc has navigated the Covid-19 pandemic and is now well-positioned to address the industry’s needs of the future
Amarket leading manufacturer and supplier of clay and concrete building solutions to the UK construction industry, specialising in products and systems for the building envelope and infrastructure, Ibstock plc is a very familiar name to not just readers of Construction & Civil Engineering magazine but to the wider construction sector across the UK.
With over 75 million tonnes of consented clay reserves and resources at its disposal, Ibstock is the number one UK brick manufacturer by volume of bricks sold, and operates from 36 manufacturing sites, employing over 2000 people across the group. The business is both modern in its approach and traditional in its ethos of customer service, and it still operates its headquarters from the village of Ibstock in the East Midlands, where its predecessor entity, Ibstock Collieries Ltd, was founded
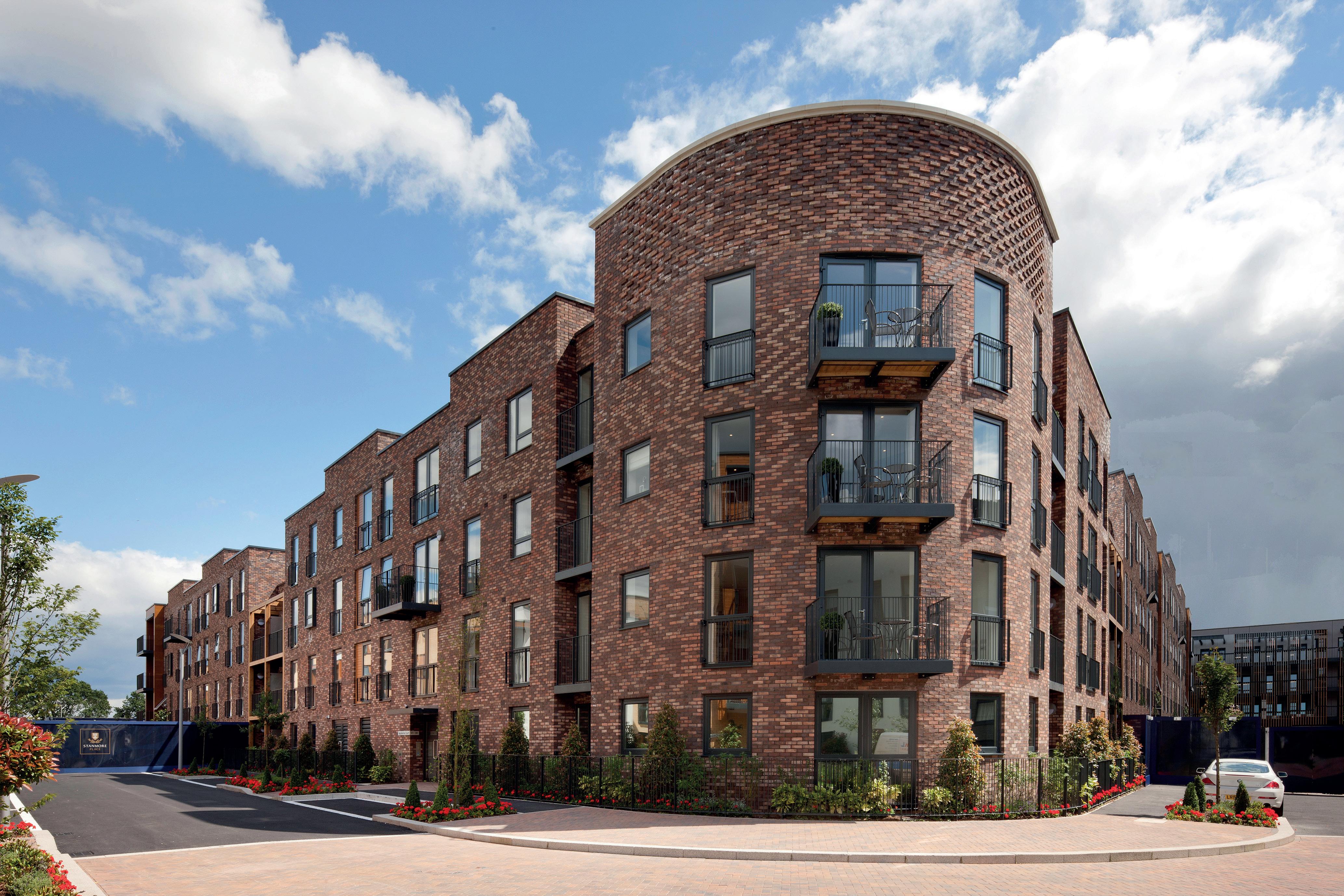
nearly two centuries ago.
The last time that Ibstock was featured in the magazine was in 2019 and as Michael McGowan, Group Sustainability Manager at Ibstock PLC noted, a lot has happened in the months between then and now. “People and businesses across the world have had to deal with a huge number of unforeseen challenges because of the Covid-19 pandemic,” he began. “As a business, Ibstock adapted really well and quickly responded to the immediate challenges we faced but, also, worked hard to ensure we would be well placed to continue to grow our marketleading position as we come out of the pandemic.”
The first national lock-down back in March 2020 had a major impact on the construction industry as building sites closed, alongside companies within the supply chain such as builder’s merchants. “As the health, safety and wellbeing of our people is of paramount importance to us, we also took the decision to suspend production and temporarily close our factories and offices,” continued Michael. “As government advice became clearer and the construction sector started to re-open, we commenced a phased reopening of our operations.”
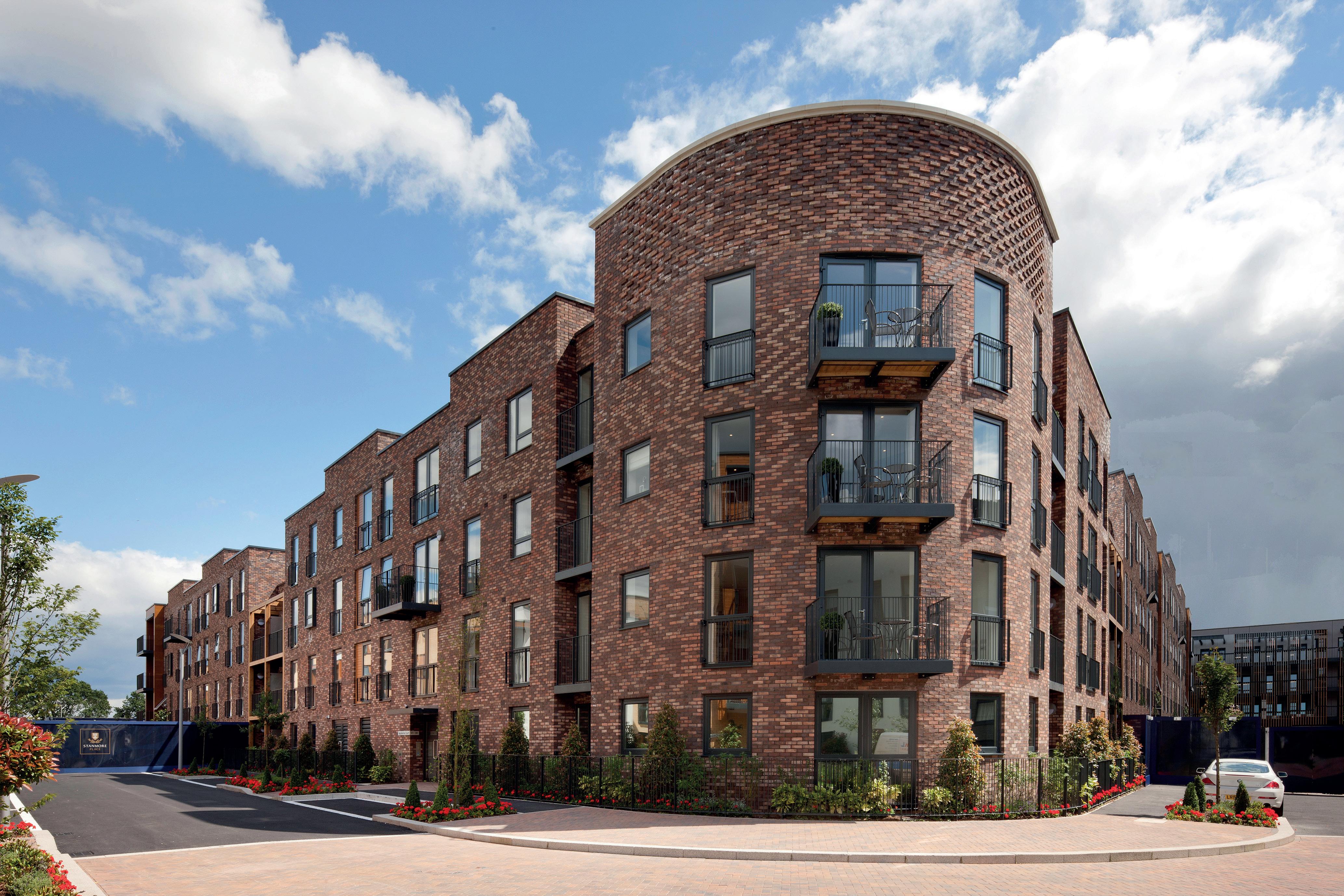
Continued investment
As part of its phased reopening, Ibstock put a lot of focus and investment into ensuring its colleagues could return to work safely, introducing a wide range of enhanced protocols to confirm compliance with social distancing, hygiene and Government guidelines. “These included temperature-screening technology at the entrances of each site, designated sanitation stations and changes to workspaces and shift patterns. We also invested in technology to support remote working for our staff and to digitise our processes to reduce the need for the transfer of paper and minimise the amount of contact needed on site for collections and deliveries. We held ‘Safe Start’ sessions to assist our people as they returned to work. These sessions involved workshops for every employee on their first day back and covered the enhanced safety protocols implemented to protect against the spread of Covid-19. In addition, the sessions provided an opportunity to go through existing health and safety procedures, reinforcing our commitment to excellence and zero-harm philosophy. Delivered by a member of the site management or from the Health & Safety team
Cambridge University Assessment Centre
The future for Ibstock is very exciting. We will be focusing on our strategy – sustain, innovate, grow – with health, safety and wellbeing, development of our people, a focus on providing a leading service to our customers, new product development and progressing further along our sustainability roadmap all as core goals for us to achieve
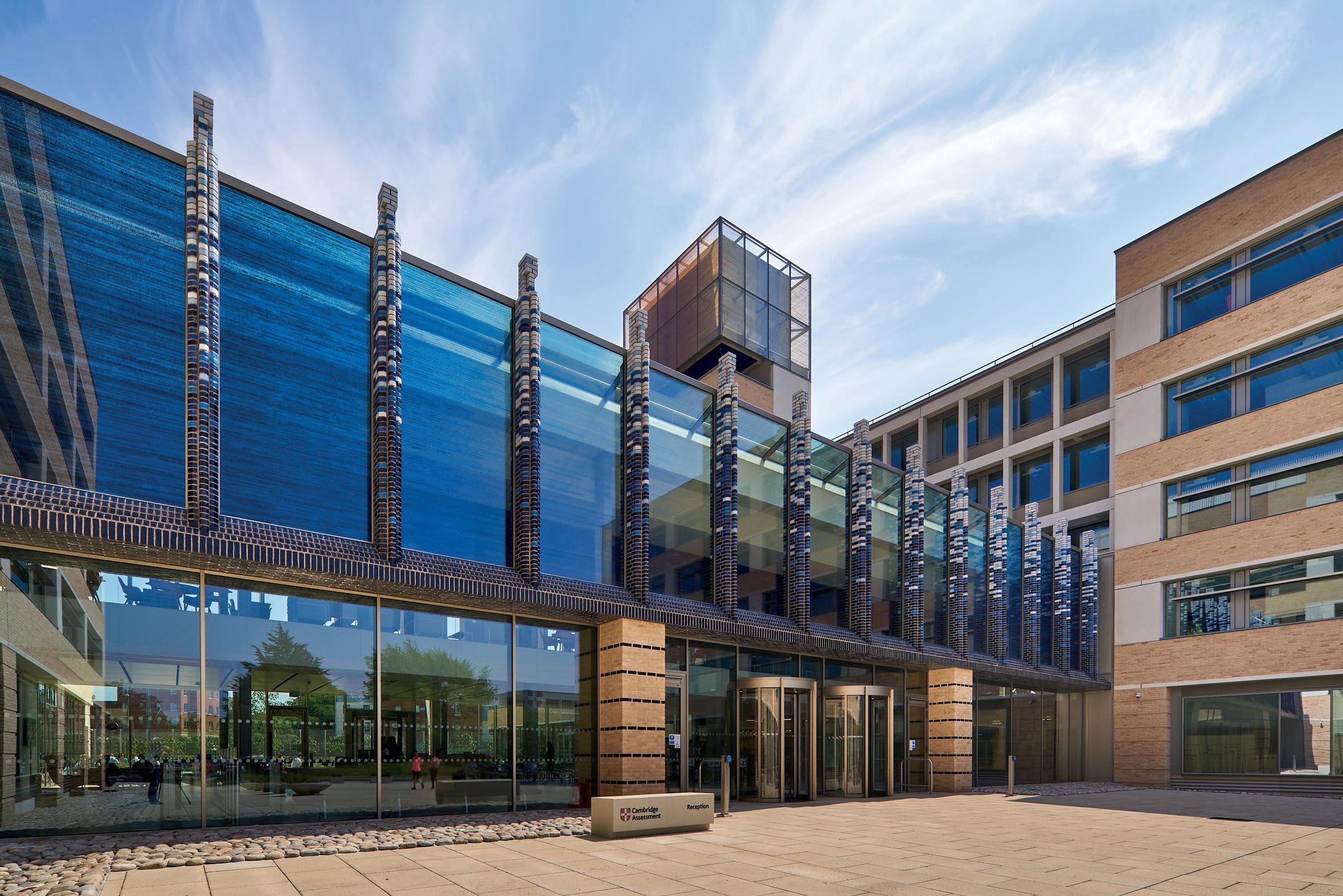
‘Safe Start’ also presented an opportunity for employees to share concerns and ideas with management. All of our colleagues reported feeling very safe and reassured by the measures we had taken to ensure their safety, security and wellbeing,” Michael explained.
In fact, such was the quality of Ibstock’s efforts in this area, that it was recognized by the British Ceramic Confederation (BCC) who awarded the business a Pledge Award of Excellence for its strong leadership and impressive response to the Covid-19 crisis.
As Michael stated, while Ibstock focused on making sure that it was operating safely during the pandemic, it also had to safeguard that once the business emerged from the virus period, it was ready to continue along its strategic path of growth and development. The Group is keen to return to full operational strength, and having invested significantly in new capacity over the past 15 years, it is ideally positioned to hit the ground running as soon as the market allows. “Ibstock remains committed to continued investment in British manufacturing, technology and people, to continue to provide customers with high quality products supported by excellent service,” said Michael. “We have spent over £50m on our Eclipse facility, to develop the most energy efficient factory in Europe. A further, recent example is the multi-million-pound investment we made in our Laybrook factory, which included replacing a hydroseal kiln with a sand-seal kiln. This investment enabled us to increase capacity, improve production efficiencies and reduce energy, carbon and water consumption.”
He added: “This investment commitment goes right across our business. In our Concrete Division, we are approaching the end of a two-year project to reduce process waste and water usage at our Supreme Concrete facility in Sittingbourne, Kent.”
A theme among the investments referenced by Michael was efficiency. “As we make investments in our
factories, efficiency and also sustainability are two of the key elements we consider when preparing the investment case, particularly in relation to energy usage, carbon reduction, and resource efficiencies such a water usage and waste reduction,” he confirmed. “We also have many projects taking place within the business focusing on incremental improvements in efficiencies such as heat recovery projects to maximise efficiencies in kiln processes, an LED lighting rollout, a motors and drives strategy to replace them with the latest, most energy efficient versions and the rollout of electric mobile plant fleet.”
Sustainability aims
Having given the details on the efficiency side, Michael continued with the sustainability side, which has been a major focus for the business of late. With Michael being named as Energy Manager of the Year for the UK at the edie Sustainability Leaders Awards in 2020, this is a topic that is very close to his heart, and is also regarded as one of Ibstocks three ‘strategic pillars’, alongside innovation and growth. “Sustainability is a major consideration in everything we do and we have an ambition to be the most sustainable manufacturer of clay and concrete products in
SEW Eurodrive
SEW Eurodrive is a long term working partner and preferred supplier to the Ibstock Group. We work with all Ibstock sites across every product discipline we supply including geared motors, industrial gears, electronic controls including AC Drives and servo drives, and of course providing service and repair. Ibstock prefers SEW because of the level of support that we have consistently given them throughout the years and because of our market leading product range that’s second to none. In addition, by helping to identify and replace old inefficient products we are proud to help Ibstock on its Net Zero Sustainability journey.
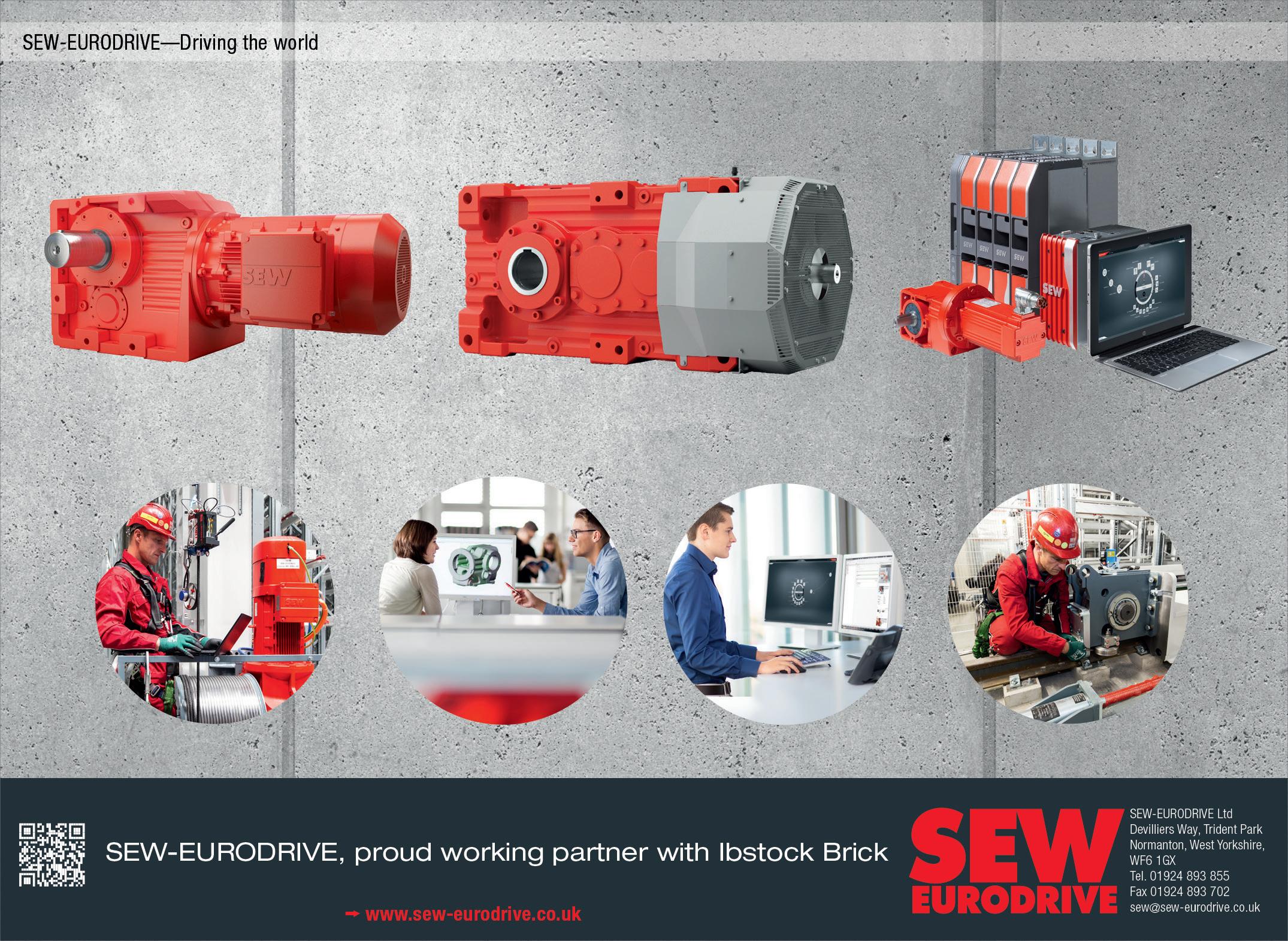
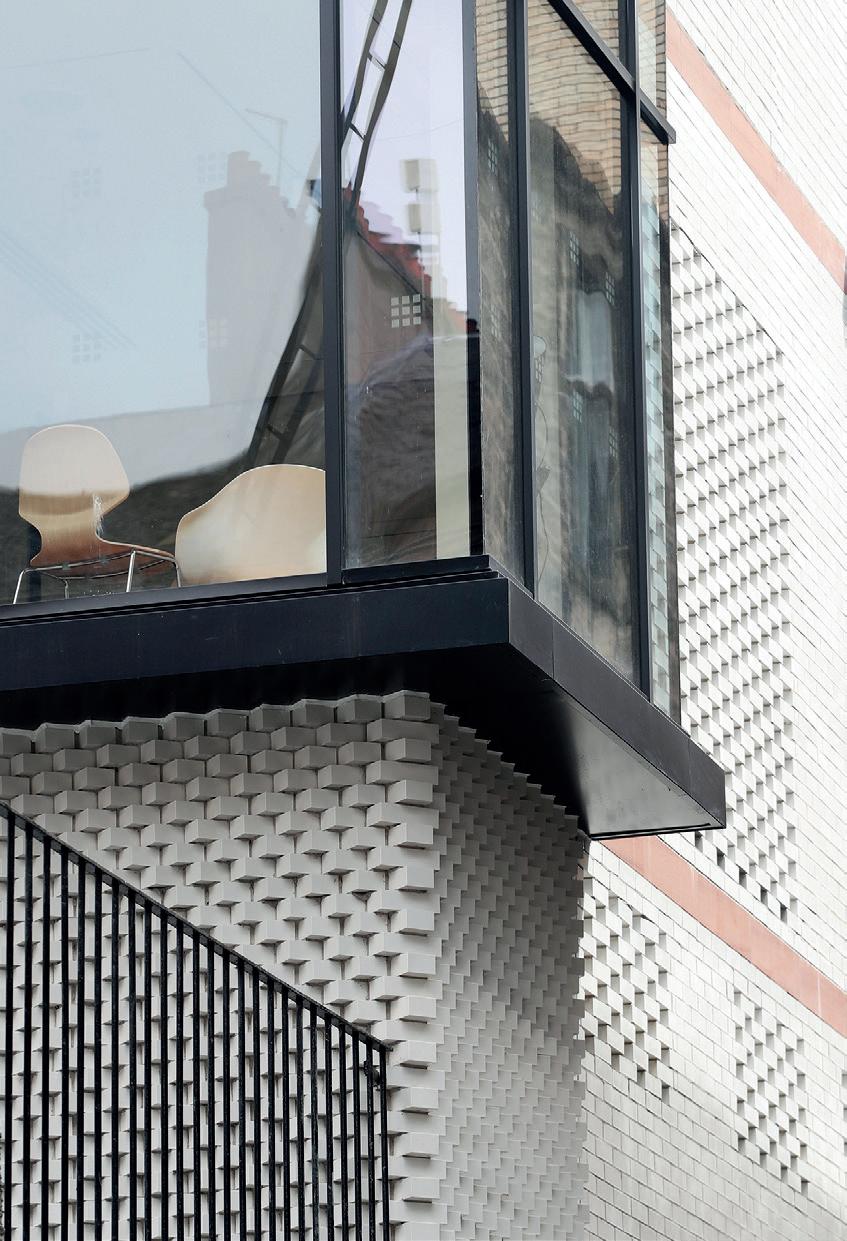
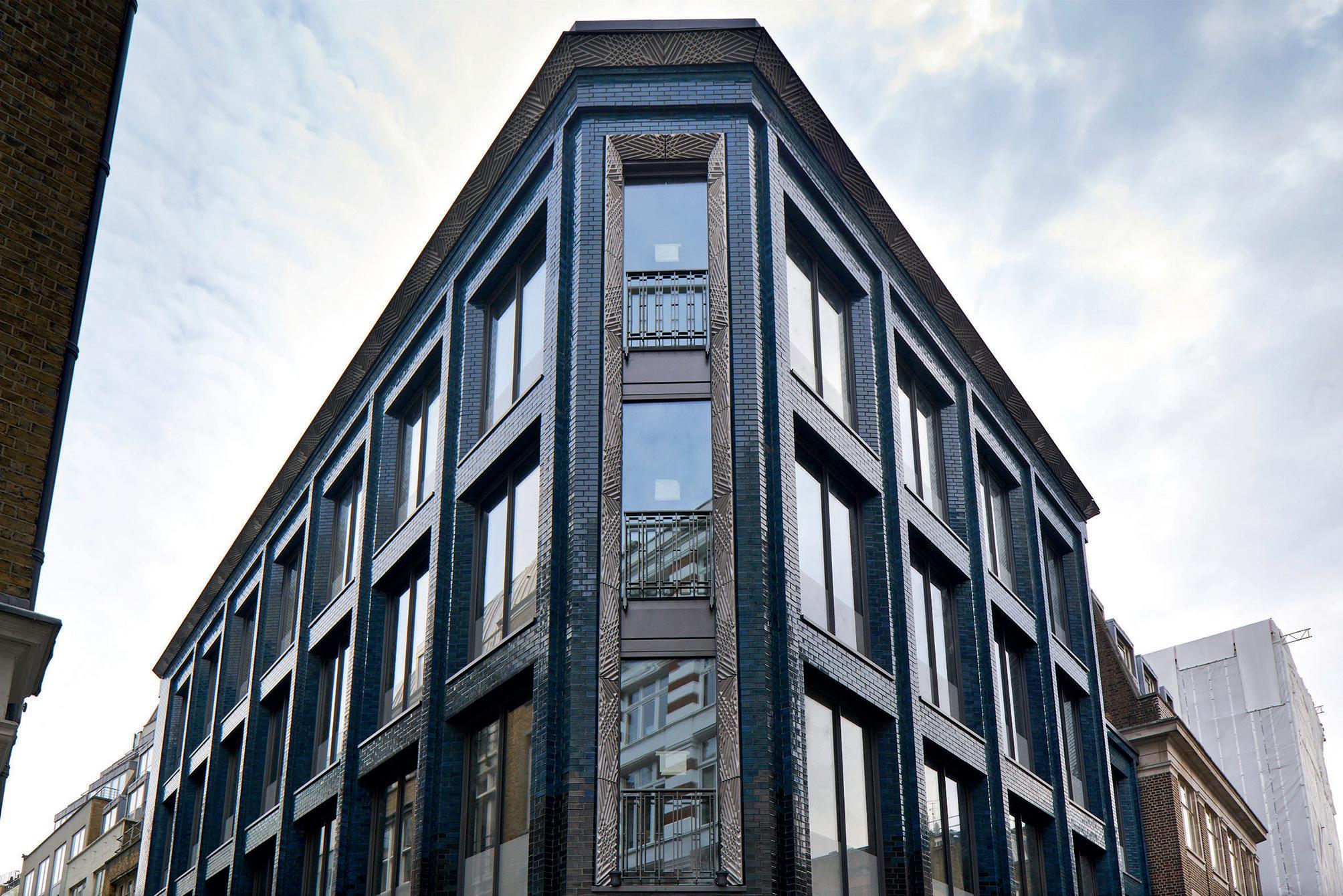
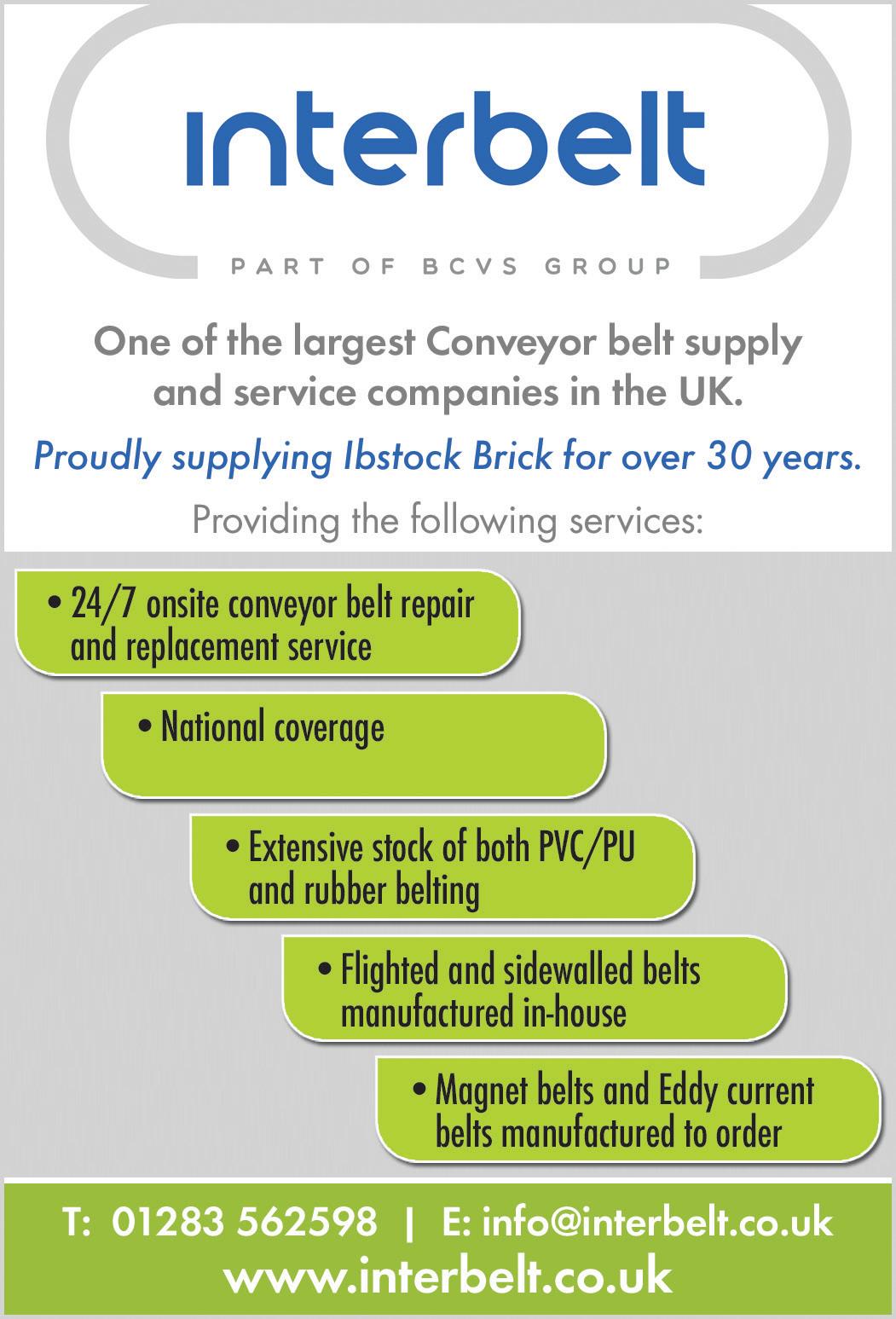
Beak Street
the UK,” he revealed. “We have a Sustainability Board, chaired by one of our Independent NonExecutive Directors, to ensure Sustainability is always at the heart of our strategic decisions and how we operate our business.
“Our most recent example of our focus on sustainability is our switch to sourcing 100 per cent of our electricity from renewable sources. We are the first UK building products manufacturer to do this, further demonstrating our leadership in the industry. This is one of several decarbonisation projects we have delivered recently. Another is the completion of a solar park at our head office in Leicestershire that supplies a quarter of the power requirement on site, another industry first.
“We also have a partnership with Shelter, the housing and homelessness charity that helps millions of people every year struggling with bad housing or homelessness through providing advice, support, and legal services. We have so far raised over £70k for them by conducting various fundraising activities.
“Finally, we are also focusing on the delivery of our Sustainability Roadmap 2025, which includes initiatives such as KPI’s around carbon, water and waste, a packaging target of a 40 per cent reduction in preventable plastics, dematerialisation with utilisation of secondary and recycled materials, and further investment in partnerships on alternative fuels.”
New product development
Having described Sustainability as one of Ibstock’s ‘three strategic pillars’, Michael continued with further information on a second pillar – innovation. “We are committed to achieving our target of 20 per cent of our revenues being generated from new and sustainable products by 2025 – we are currently at 11 per cent,” he divulged. “In order to achieve this, we have a major focus on new
product development and we have a robust product development process in place to capture ideas and manage development projects through the process as quickly and efficiently as possible.
“Changing trends in the market, such as growth in off-site construction and digitalisation for example, provide opportunities and we are keen to explore such opportunities to ensure we can maintain and enhance our leadership position. Our focus on innovation will enable us to develop new solutions for these changing market demands.”
This point brought Michael to one of the company’s newest products, the Nexus XI. This was launched in November 2020, and is a mechanical fix brick-faced soffit and lintel system. “This development was in response to the amendments to Approved document B: Fire Safety to state that all materials used in residential buildings above 18m (11m in Scotland) must be of limited combustibility (rated A1 or A2 under the European Classification system),” he explained. “Our technical and design teams created our innovative mechanical fix system and worked closely with the British Board of Agrèment (BBA) and National House Building Council (NHBC) to conduct the relevant testing and gain the necessary approvals for the use of the system above 18m. We were able to take this development from first concept to BBA approval in only seven months, which is a great achievement. We have received excellent feedback from our customers on Nexus XI resulting in a very strong project pipeline only weeks after launch.
“New product development is at the heart of our growth plans,” he emphasised. “As market leader in bricks and clay building products, we have the broadest range of products and systems available in the UK and we continue to invest to enhance our offer.”
Having highlighted the essential role played by the design team in the creation of Nexus XI, the conversation turned to the people side of Ibstock. Richard Brown, the Marketing Director, Clay Division, Ibstock PLC shared his thoughts on the culture at the company. “I would definitely describe Ibstock as a people-orientated business,” he said. “I joined Ibstock in June 2020 so I am relatively new to the business, but one thing that has become very clear to me over my first few months is how much Ibstock values its people. From how the business invested in a first-class response to dealing with Covid-19 to ensure people were supported in remote working and to feel safe in our offices and factories, to support through the restructuring process that took
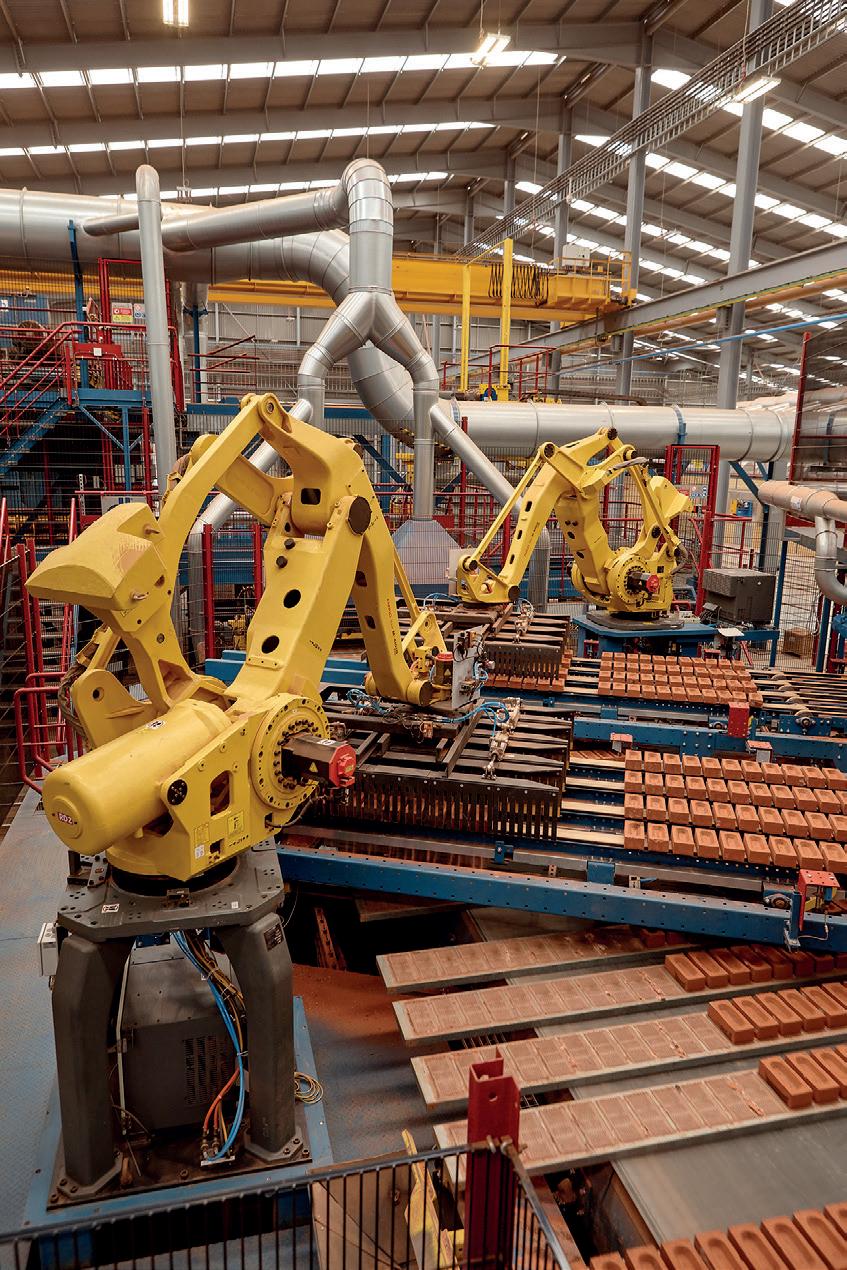
Eclipse Factory
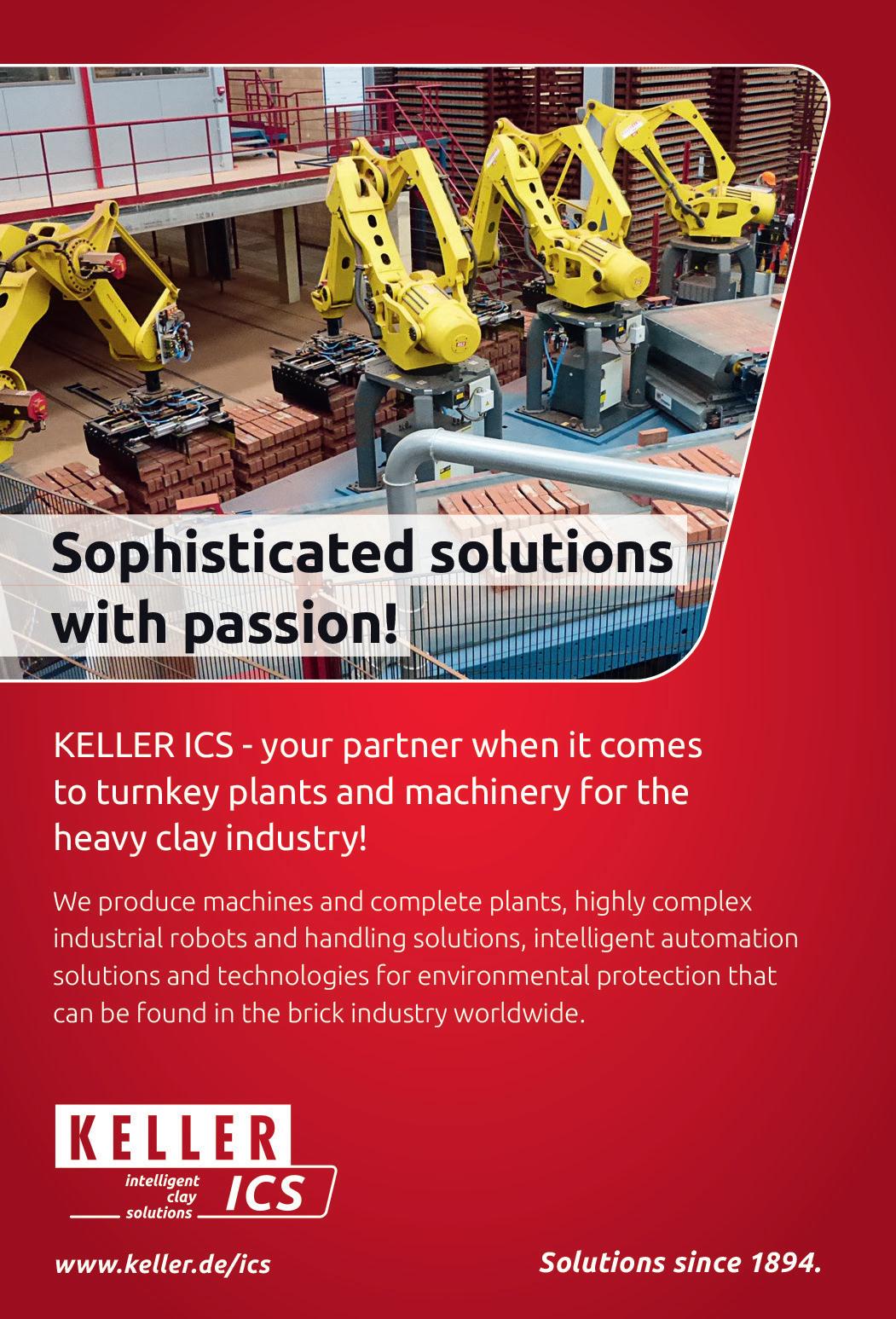
place during the year, to how even though it is a very large business there is a real sense of family among employees. There is a great deal of teamwork and collaboration that takes place throughout the business.”
This focus on staff includes their growth and development, and this is not just of existing staff but also the younger generation, and gone from strength to strength. But for Ibstock, it is not just about training; it is about bringing a new generation into the Ibstock family at the start of their careers, and helping them reach their full potential.
“The company culture is defined by the values of Trust, Care, Teamwork and Courage and I have seen many examples of this since I joined,” added Richard. “This is one of the reasons so many people have worked for the business for a long time. There is a real teamwork mentality and the focus on people goes all the way through the organisation. The key considerations are very much the well-being of the people that work for the business.”
in 2019 Ibstock’s Apprenticeship Scheme was recognised at the Training Journal Awards, where it beat off competition from major brands to win the Gold Award in the Best Apprenticeship Programme category. As Paula Wardle, Group Learning and Development Manager, commented following the award, the Apprentice Scheme has
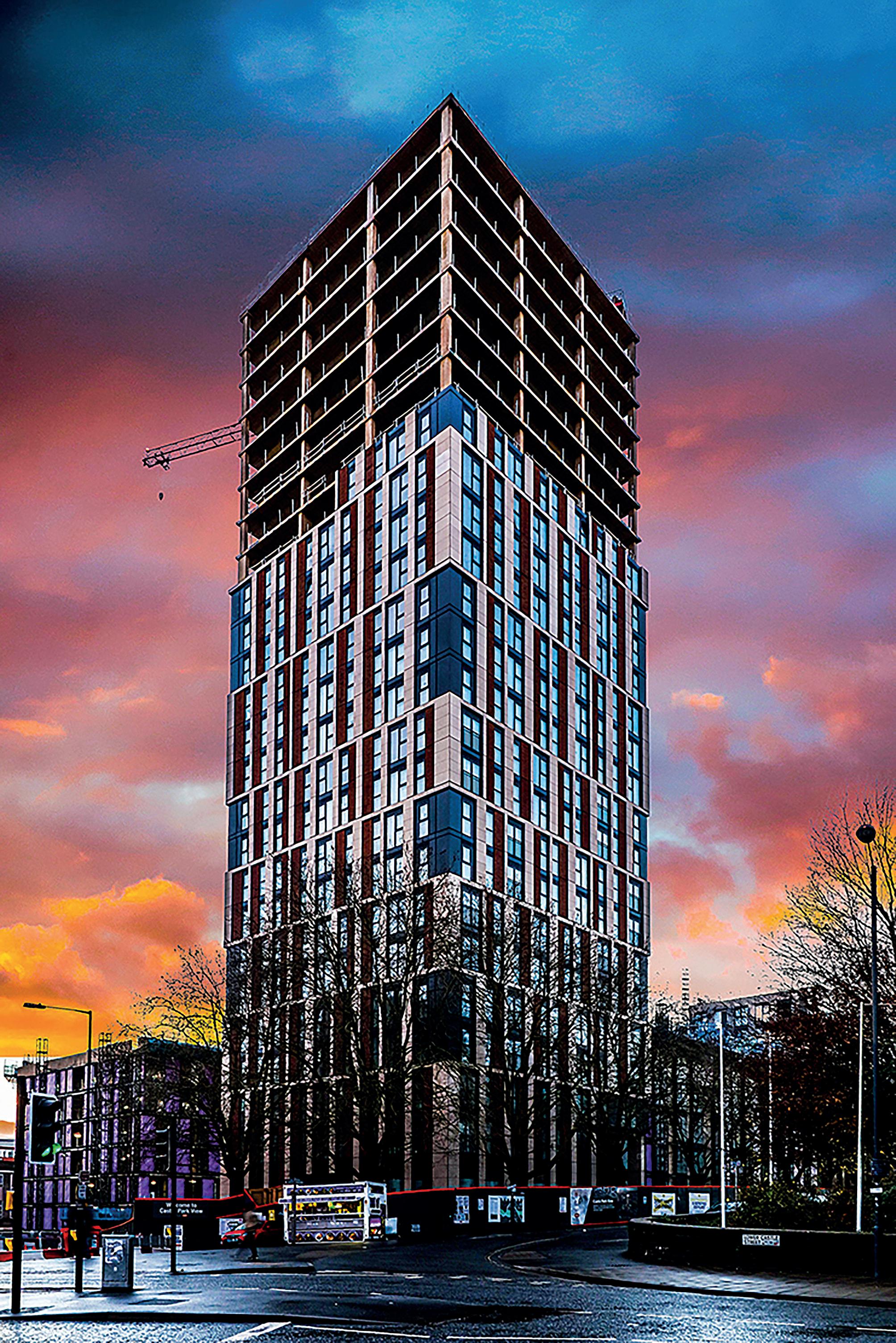
Castle Park
Positive drivers
This focus on well-being that came to the fore in 2020 remains a solid part of Ibstock and will help to support its ambitious plans to continue to grow and strengthen its position over time. “Whether that’s organically or looking at other investments, the appetite is still very much there in terms of how can we move this business forward and continue to grow and develop despite the challenges that the last year presented,” continued Richard. “We made a lot of changes to get through unprecedented times and we are positioned to come out the other side and in a good place to continue in our forward-thinking way.”
With construction set to be a key contributor to the UK’s post-Covid economy, Richard is optimistic about the future of the industry. “We are encouraged by recent market trends in the industry and the resilience of demand from our house builder and merchant customers,” he said. “The UK government has regularly stated that it considers construction a vital sector for economic recovery and has allowed the construction supply chain to continue operating during coronavirus lockdowns. As a result, construction activity has recovered
more quickly than the economy overall.
“Our core business focuses on the residential construction sector and the fundamentals for this sector are positive. The latest forecasts from the Construction Products Association suggest good growth in new build housing and housing RMI in 2021 with further growth in 2022. This coupled with the commitment from Government to build more, much needed, homes and macro trends such as growing population and increases in household formations provide a good foundation for future growth.
“Whilst we, of course, need to be mindful of ongoing uncertainties, including those related to the future impact of Covid-19 and the expected changes in the Help-toBuy and stamp duty rules, these positive drivers and our strong position in these markets mean we are in a good position and have good reasons to be optimistic about the future.”
Having navigated the business through a difficult time, the management team in 2021 is at the helm of a strong business, and one that is aware the pandemic and its challenges won’t last forever. “The future for Ibstock is very exciting,” said Richard. “We will be focusing on our strategy – sustain, innovate, grow – with health, safety and wellbeing, development of our people, a focus on providing a leading service to our customers, new product development and progressing further along our sustainability roadmap all as core goals for us to achieve. We have demonstrated a desire to invest, strengthen and grow over a long period and that ethos will remain very much at the heart of our business.”
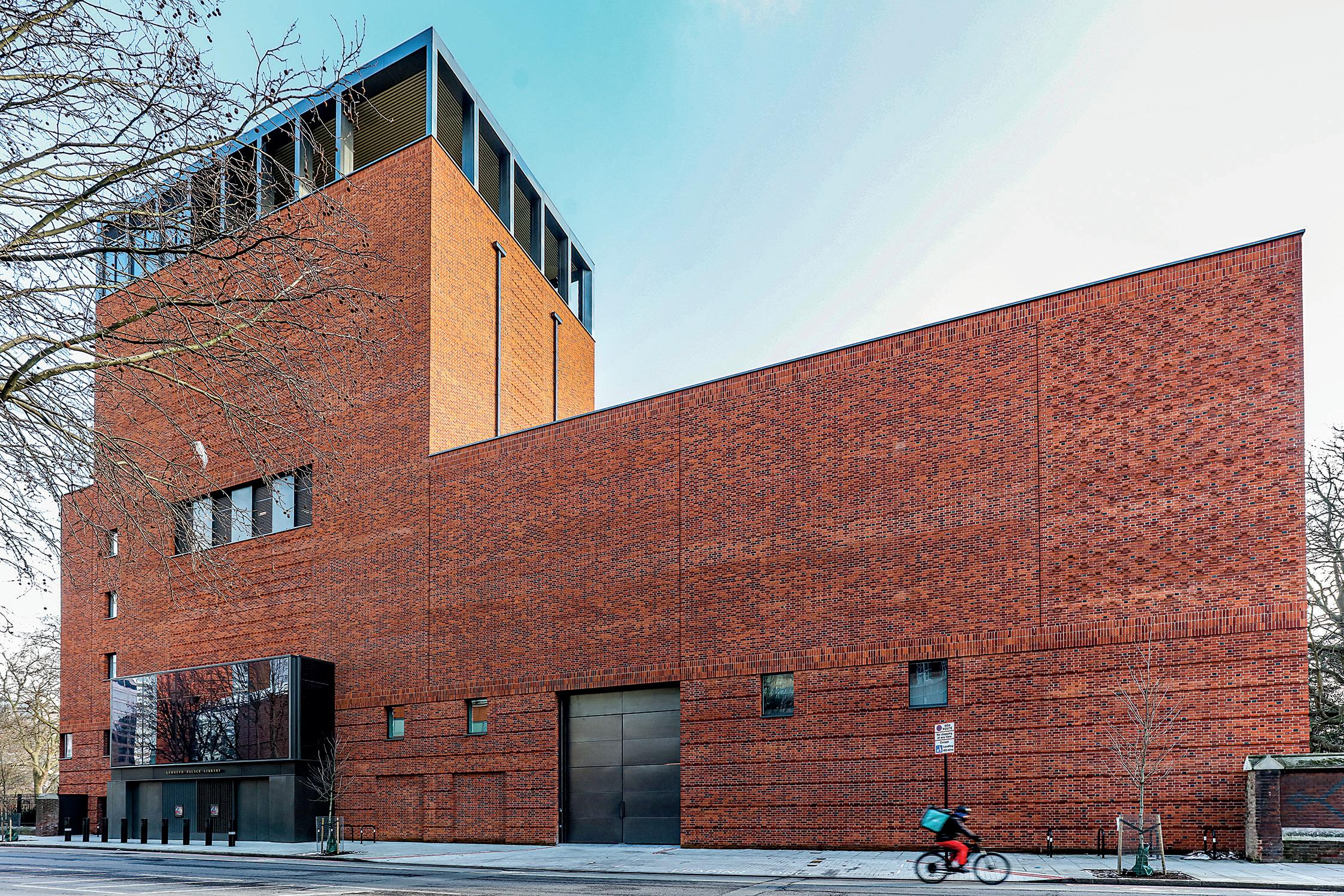
Services: Manufacturer and supplier of clay and concrete building solutions
Lambeth Palace
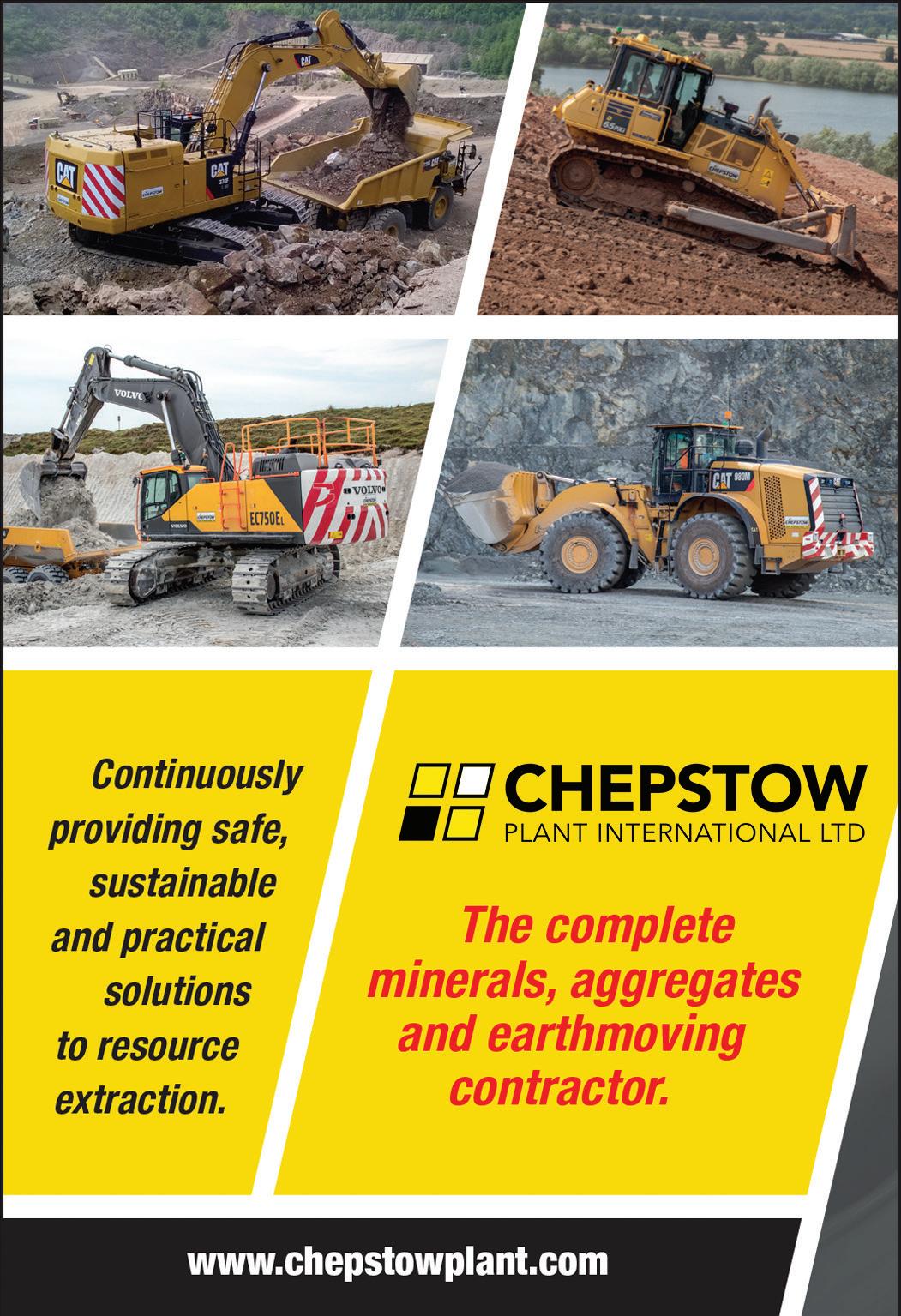
Operating from a number of strategically located centres around the UK, Denholm Industrial Services has developed, over the years, into a true multidisciplinary organisation. Part of Denholm Industrial Group, one of the four divisions of diversified familyowned parent company, J. & J. Denholm, Denholm Industrial Services is a respected provider of scaffolding and access,
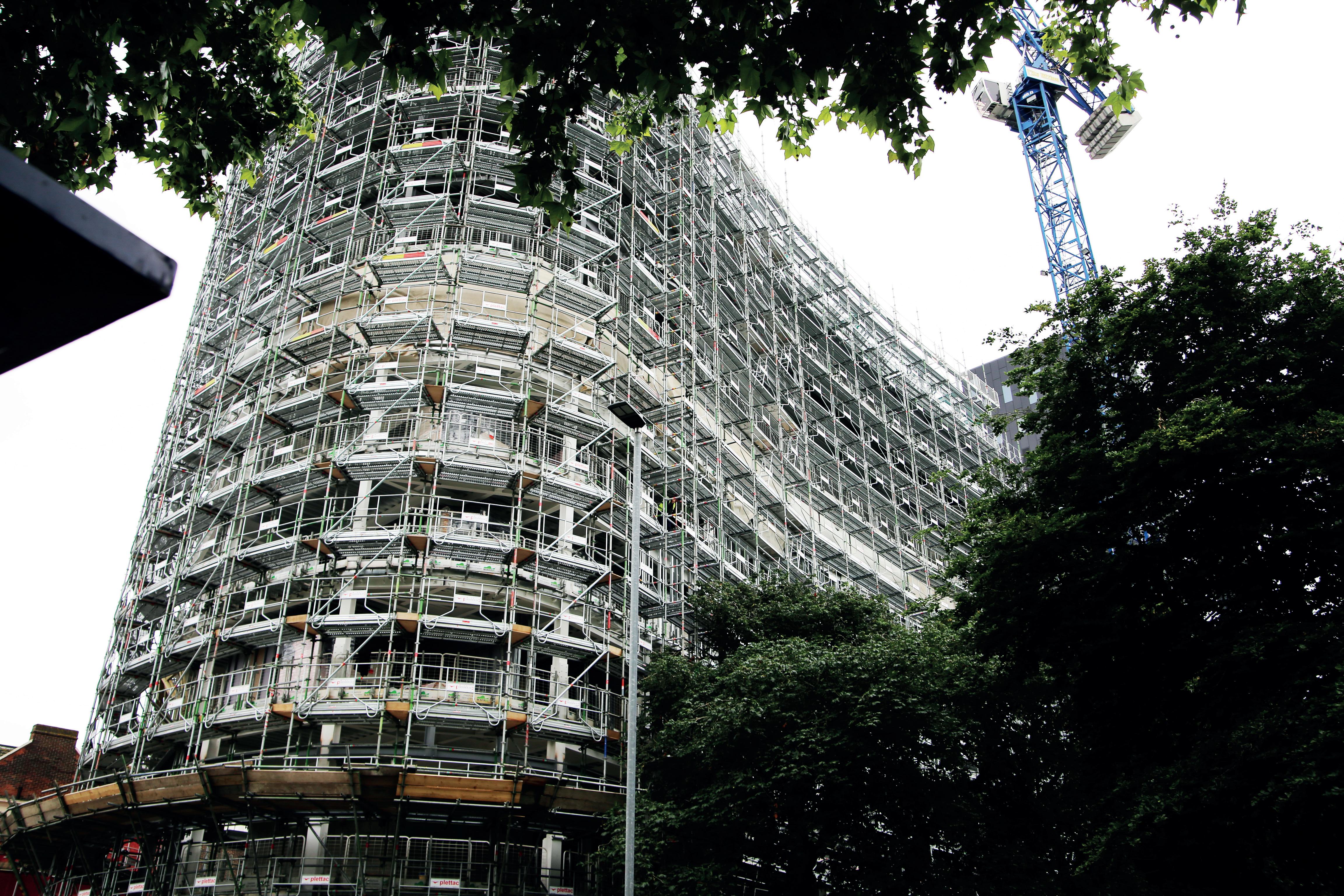
In safe hands
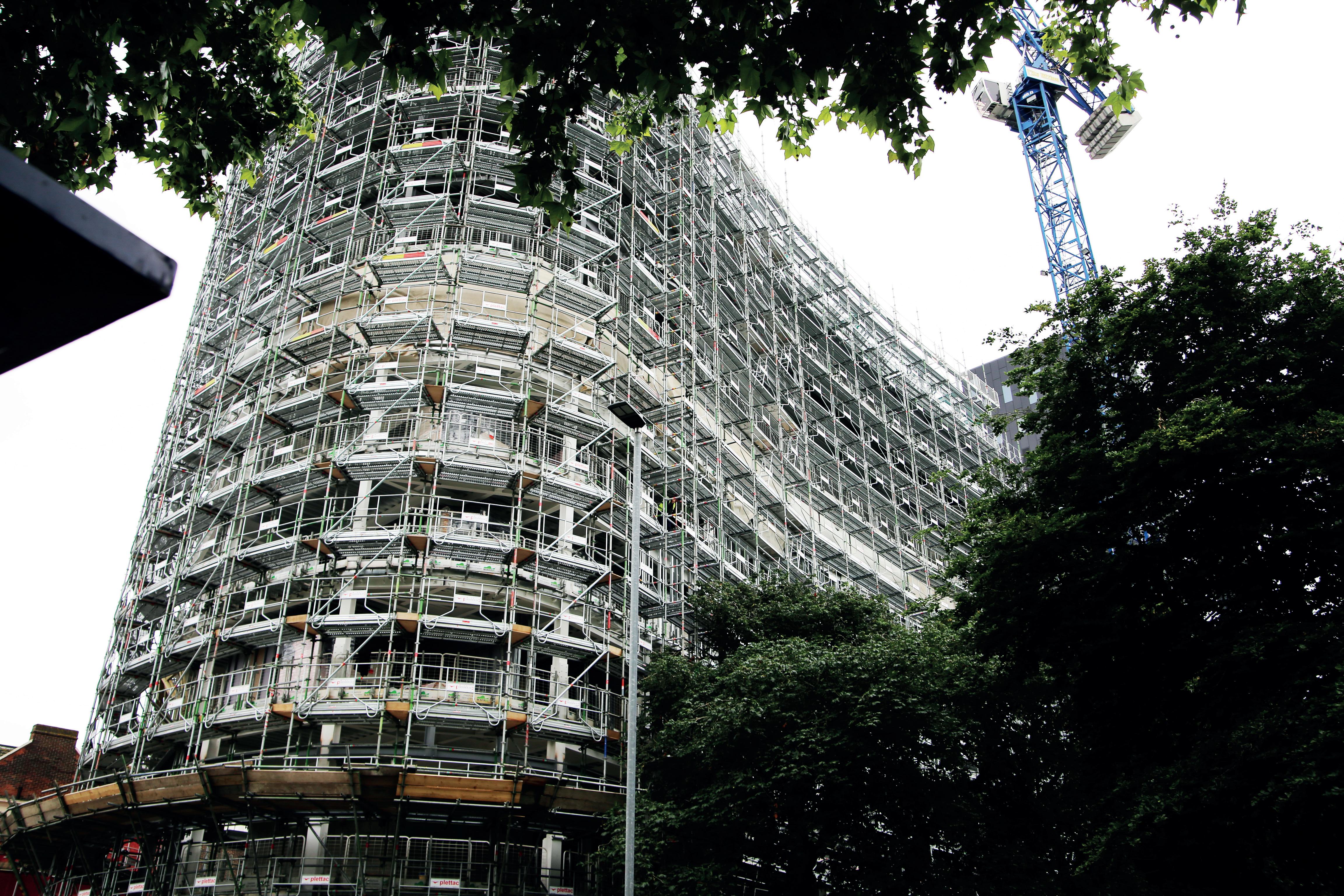
A successful provider of scaffolding, access solutions and protective coatings in the most challenging environments, Denholm Industrial Services is investing in an even brighter, safer future
protective coating, industrial cleaning, containment, and surface preparation services with more than 35 years’ industry experience.
Founded in 1983, Denholm Industrial Services’ roots stretch back to a history of industrial painting and cleaning contracting in the North Sea oil and gas sector. After successfully transferring this experience in tough conditions to land and sea infrastructures, the company now delivers its services across a wide
range of industries, including construction and demolition, defence, energy, historic buildings, nuclear infrastructure and the marine sector.
“At Denholm Industrial Services, we have created a diverse platform that allows us to operate in specialised teams across each sector, giving the sector its specific needs, while sharing information and best practice across industries,” explains Managing Director Steve Hill. “We sometimes come across the opinion that a scaffolder or painter is the same in every sector, but there’s quite a difference between someone working on a building site and a nuclear plant, or an offshore oil and gas installation and a
“Another notable project is the complex engineering we performed at Bidston Moss Viaduct, working with Costain to provide 65,000 square metres of protective coatings and 2,000 tonnes of scaffolding,” Steve says. “We remain a highly collaborative business and we are set up to work in close partnerships. We do that by being honest and transparent and we are strong enough to have difficult and honest conversations if need be. We see the end project goal as being ours, not just the clients, and we work together on that.”
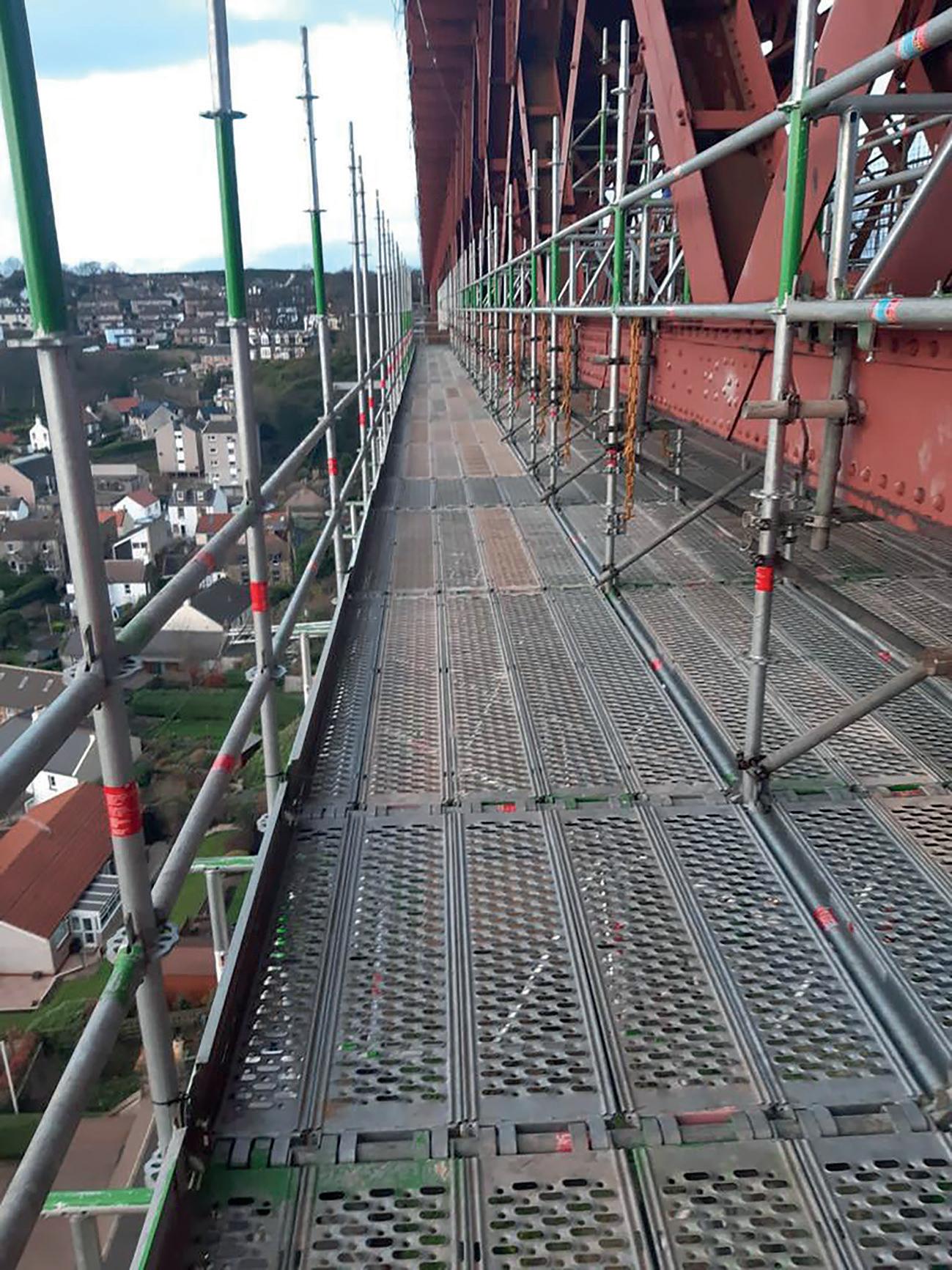
high-rise building. Each setting is unique and requires that element of specialty, which we have fostered within the group.”
Expanding year on year, Denholm’s growth has been fuelled by major long-term projects with clients such as Balfour Beatty, Babcock and BAE Systems. The company received its first shipbuilding contract with the latter in 1997, racking up more than two million multi-discipline man-hours over the course of five years. A more recent milestone contract was a large scaffolding project for Kier Construction at Beckley Court, a 78-metre-tall student accommodation building in Plymouth that marked a departure from Denholm’s more traditional market offering. Focus on safety
At present, Denholm is in the fourth year of a long-term newbuild submarine programme in Barrow-in-Furness and is also working with Cammell Laird. Encompassing extremely complex delivery scopes, the submarine projects are pushing the envelope of modern engineering, to which Denholm is responding by continuously developing its people to deliver these more complex industrial services.
Work also continues for Denholm at the iconic Forth Rail Bridge, where the company is supplying a complex access, containment, blasting and coatings project. A true turnkey package provider, the vastly different contracts Denholm is able to take on is testament to the diverse and multidisciplinary nature of its offering and the strength of its team.
Alongside the ongoing process of diversification, Denholm’s focus on innovation has been ever-present throughout its history and has helped to drive the company forward across the decades. Boasting longestablished experience in the scaffolding industry, Denholm continues to find ways to develop its offering and improve the services it provides. One way the company does this is through
investment - much of which has been geared towards the Plettac Metrix system of late. Acquired in 2018, the Plettac Metrix system replaced an older technology and Denholm now makes use of more than 6000 tonnes of it onsite.
“Investing in Plettac Metrix has resulted in significant productivity gains for our customers, but also, more importantly, the safety features of the system mean that our people and those around us are safer,” Steve reveals. “Plettac Metrix’s advanced guardrail (AGR) system allows the scaffolder to build edge protection on the lift before they get to where work is being carried out, so that the scaffolder is always away from the leading edge and always supported by a guard rail. It allows risk to be engineered out and that is a really important part of our focus – keeping our people safe.”
Another key investment for Denholm has seen the company acquire an ultra-high-pressure (UHP) water blasting machine for its marine activities. One of a kind in the UK, the UHP technology not only delivers significantly faster service for vessels and oil and gas installations, but the equipment also drastically reduces the environmental impact of Denholm’s operation as the machine does not require abrasives that can only be disposed of in specialist landfills. Additionally, the design of the machine removes the need for additional containment associated with blast medium. Crucially, the UHP blasting technology allows operators to work a safe distance away from any high risk zones, illustrating, once again, Denholm’s commitment to investing in apparatus that keep its workforce safe and gives its customers the edge.
SIE Industrial
SIE (specialist industrial equipment) is a key supply partner to Denholm Industrial Services. The two businesses have worked closely together for well over 20 years in a multitude of engineering and construction sectors. SIE helps Denholm deliver exceptionally professional Contract Services year in year out within the Marine, Civil Infrastructure, Nuclear & Defence, Oil & Gas and now the emerging markets of Renewable Energy. Working on headline assets such as the Forth Rail Bridge, Scotland, steel is prepared and re-coated providing long life to one of the UK’s most iconic structures. SIE is a leading company in the supply of shotblasting and coating equipment within all industry sectors, both in-house and on-site. It covers the major industrial hubs of the UK, Europe, the Caspian region, the Middle East and beyond.
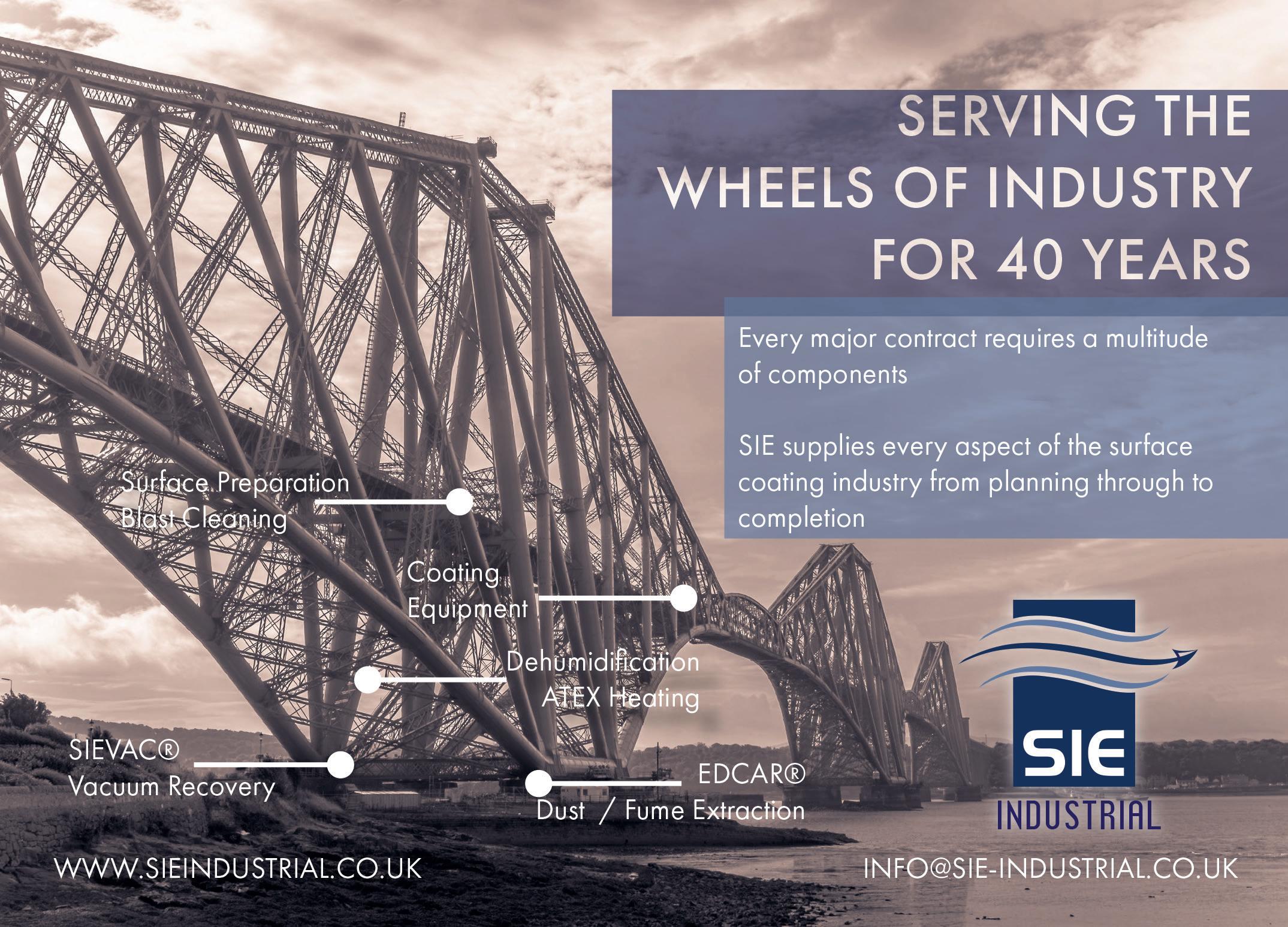
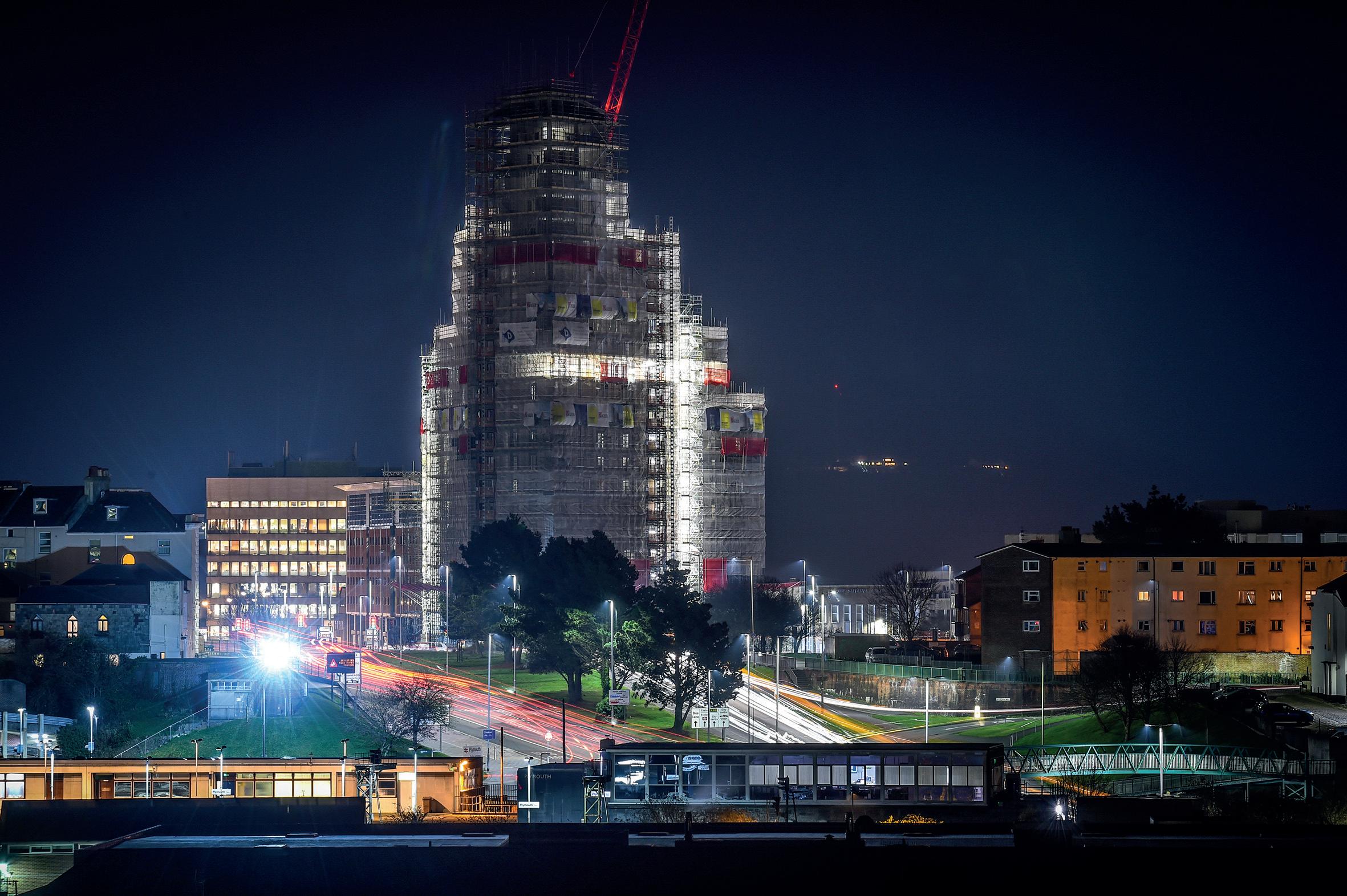
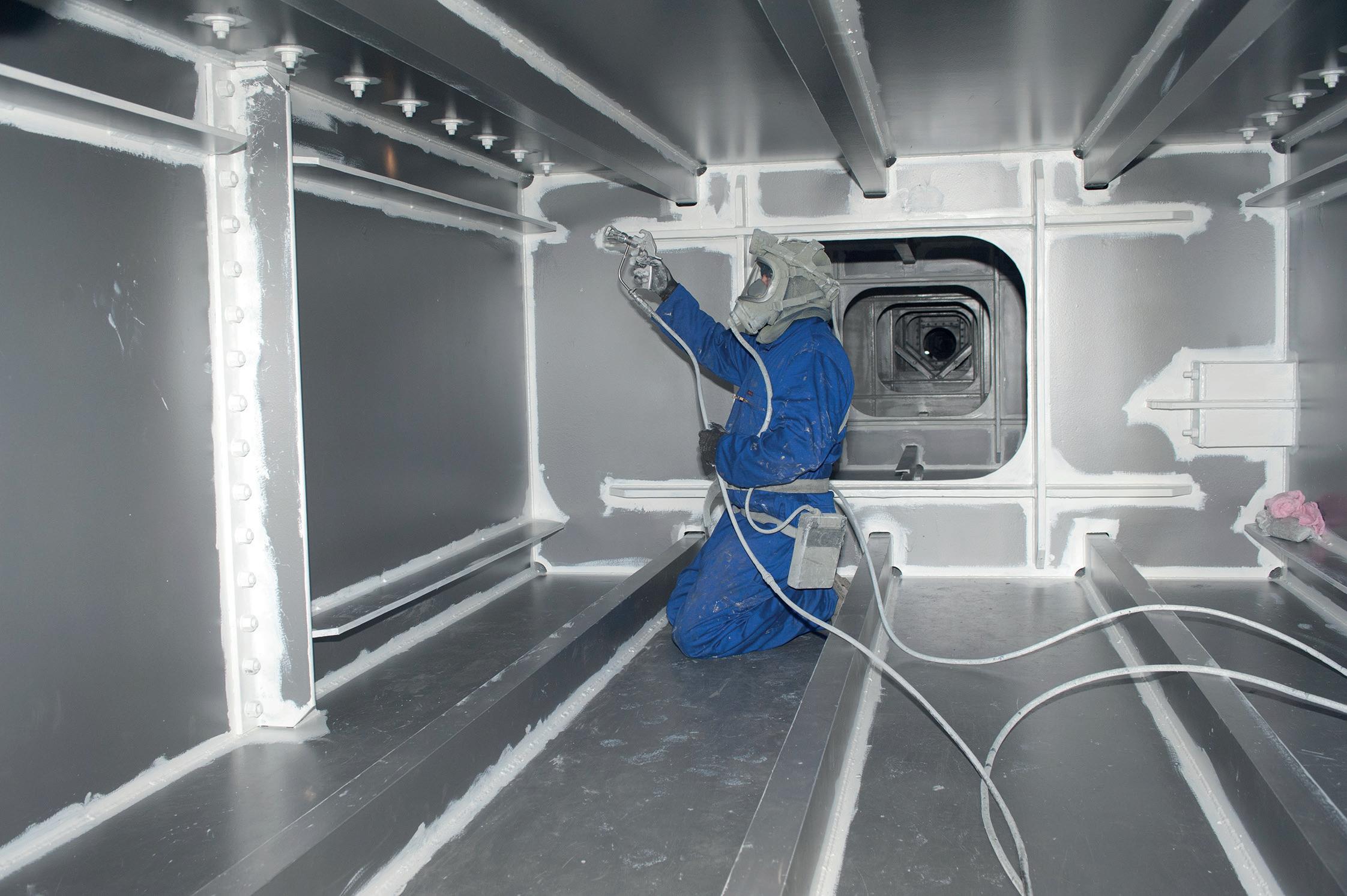
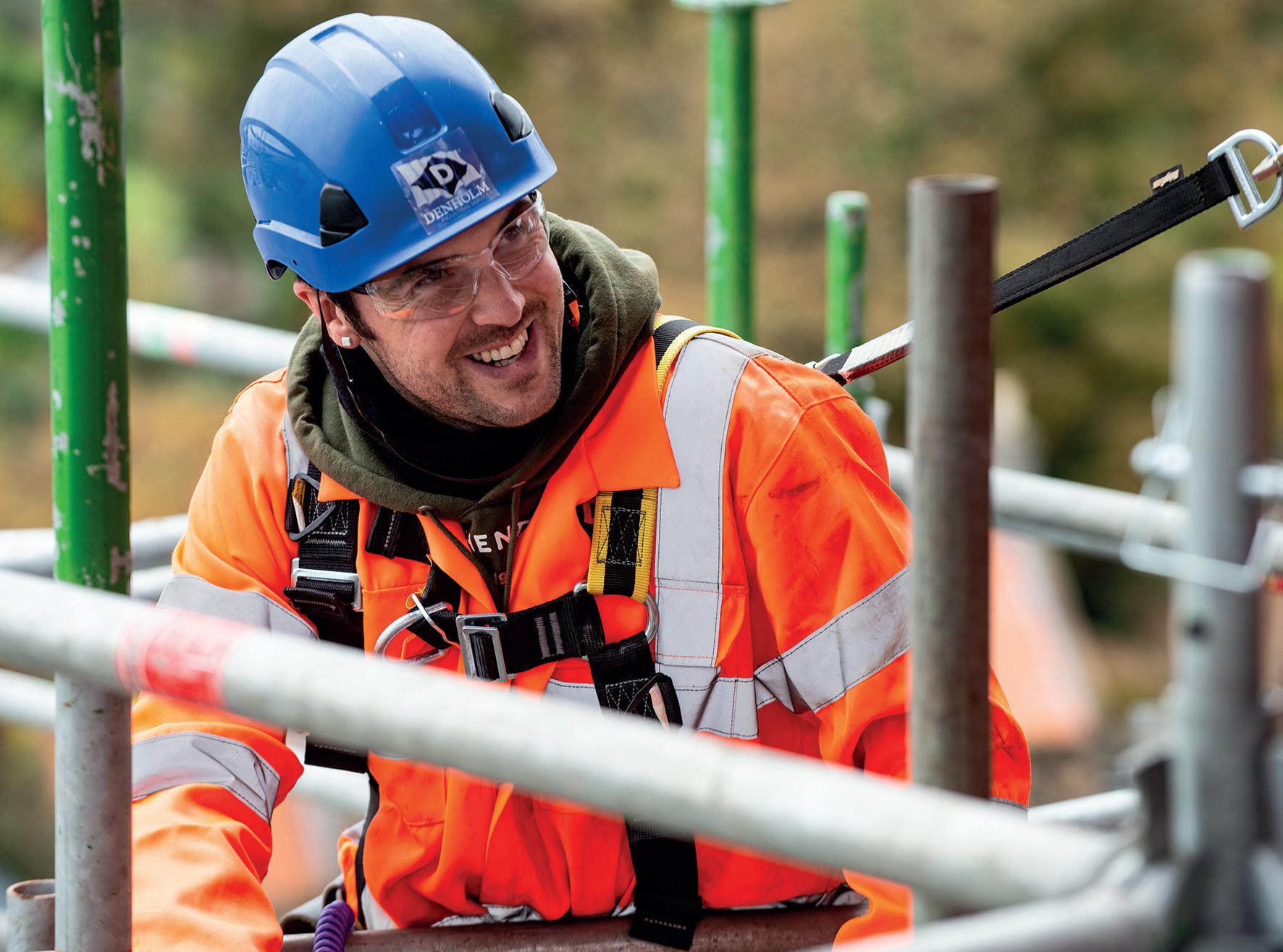
The fact that Denholm’s newest equipment and technologies carry impressive safety credentials is no surprise considering the company recently received the RoSPA President’s Award for achieving its Gold Award ten years running. Denholm’s unwavering emphasis on protecting its employees from harm continued in 2020 when the company achieved an accident frequency rate (AFR) of zero.
“I have to commend our teams for bringing home another award and locking down an AFR of zero in what is a live risk industry and a challenging line of work,” Steve declares. “The goal now is to stay head of the game and to do that we have brought in the DuPont Behavioral-Based Safety System, which is designed to motivate and aid in behavioural changes through discussion, understanding and respect. We run it centrally through a database and through apps and devices, so we are able to collate trending data really quickly and efficiently, which helps to inform discussion and future training. All our people understand why the business cares so much. It’s not about statistics, it’s about keeping them safe.”
2021 vision
In the coming months, Denholm’s valued workforce is set to expand further, with the company increasing investment in the future of its people. Fifteen apprentices are already at work in the business and that number is expected to grow in 2021.
“As our apprentices come in, we have a company-designed career pathway scheme, which supports young and more seasoned workers in their desire to have a long and full career,” Steve states. “As well as offering our apprentices a product-based course, we also have an excellent syllabus delivered in-house, covering life skills like mental health and managing diversity and of key channels. One of these channels involves increasing the company’s service offering, and consequently, Denholm will be looking to its customers and adding core services that best align with client needs, while maintaining the highest safety standards, service levels and operational excellence. “These core services will be generated organically and through more acquisition, so I have no doubt the company is on a growth path,” Steve asserts. “We see our expansion continuing indefinitely and on the same trajectory of the last four years. The process will include bringing on new businesses and moving into new sectors. We are already looking at a couple of potential industries, and are certainly serving our customers in the sectors we are in, so really, the next three to five years are going to be extremely exciting for the entire Denholm Industrial Group.”
inclusion. We get young people in, give them the industry knowledge they need, but also try to develop young adults for the future.”
In many ways, Steve regards the year ahead as an opportunity for Denholm to bounce back following the challenges of the Covid-19 pandemic. As such, he expects to see the company grow across all sectors in 2021, while maintaining high safety standards and operational excellence.
“We will be looking to develop additional longerterm relationships with our key customers throughout the UK over the next 12 months, offering a collaborative approach to national agreements and long-term contracts that give continuity and cost certainty for our clients,” Steve remarks. “The Denholm Group will be 155 years old this year. It’s a highly secure, diverse, financially healthy organisation, so we are in a really safe pair of hands for the future.”
Core services
As part of the company’s longterm strategy, Denholm plans to improve sustainability across all sectors by 2025, and this will take place through a number
Services: Industrial services, including scaffolding, protective coatings and access solutions
Quality over quantity
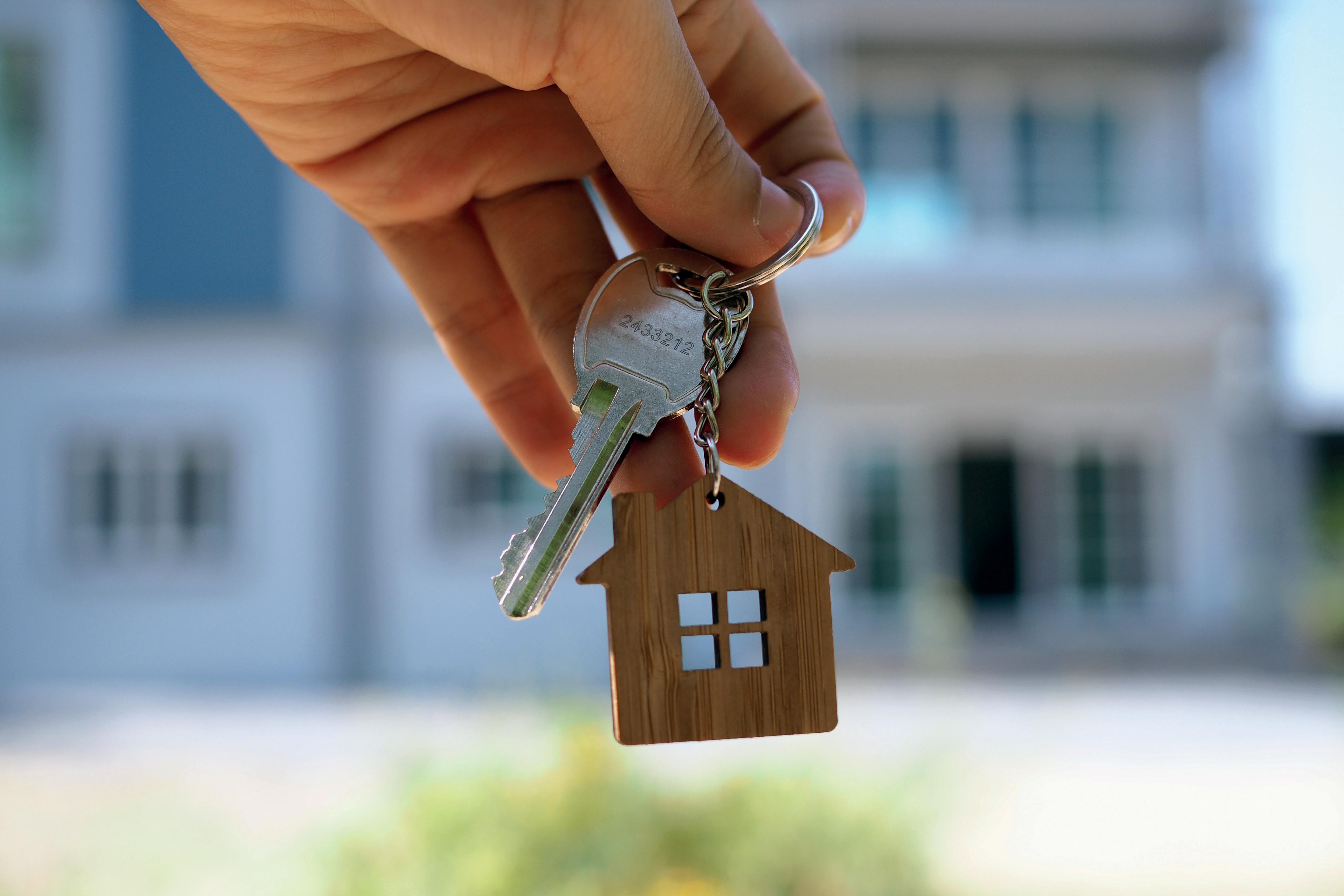
One of the UK’s leading home and commercial developers, Burrington Estates strives to develop high-end living and working spaces that offer a better quality of life to those occupying them
In 2013, Mark Edworthy and Paul Scantlebury, two experts in property, planning, finance and construction, came together in the South of France to combine their 45 years of experience to establish a company that would enshrine community and comfort. Consequently, Burrington Estates was founded. As a commercial property developer, Burrington Estates targets both residential and commercial spaces. On the residential side, it has rooted its reputation in creating unique luxury apartments and homes that encourage a better quality of living, while in the business sector, the company marks mostly mixed-use schemes in the West Country to create innovative and sustainable commercial locations for businesses to establish themselves.
The founders have transformed the company into a thriving business with a turnover of £70m and, in the past five years alone, have completed over 400 homes in the South West. Mark’s qualifications in Chemical Engineering have given him experience in management through the oversight of new fuel station constructions, while Paul brought to the partnership a valuable network of cross-sector contacts. His natural intuition to detect a project’s potential even in the early stages has allowed
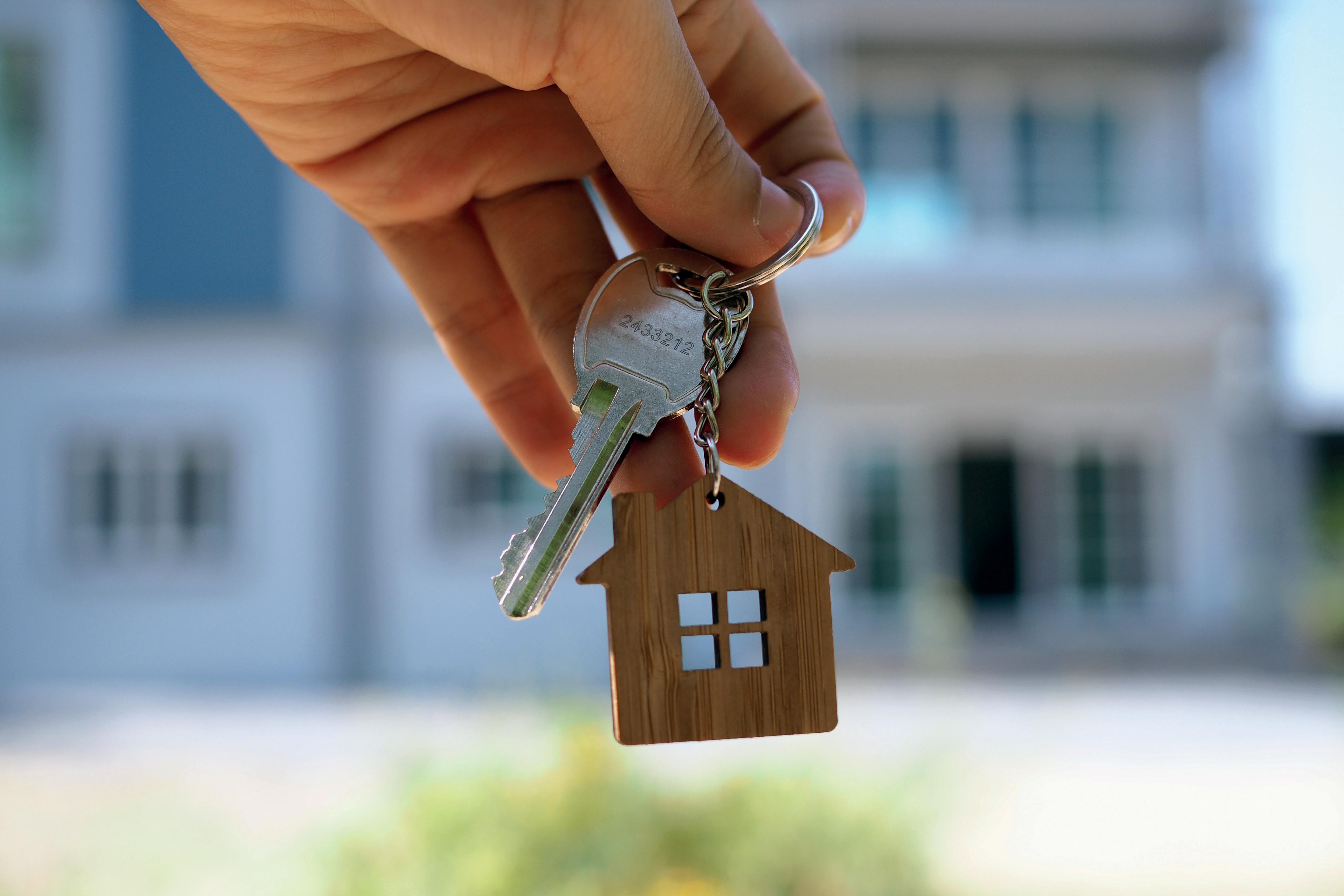
him to undertake major building projects across the UK and Europe. With Paul’s experience in first-time buyer housing, student accommodation, leisure, retail and office facilities, and Mark’s background in excellent development completion and financing skills, the power duo constructed a company that prioritises desirable locations, attention to detail and innovative developments. Mark and Paul were then able to welcome Peter Andrew MBE as Chairman of Burrington Estates. Peter’s 40 years of experience in land and planning has provided him with a refined understanding of the issues affecting house builders.
Overseas opportunities
The first project initiated by the team was an ambitious transformation of a former Grade II hospital in Exeter. The site was developed into a hub of 30 luxury student lofts and apartments with a business centre and restaurant; a development which was inspired by the Georgian elegance of Mayfair. Since then, Burrington Estates has continued to expand its project portfolios with developments that include Eurotech Park, Burrington Business Park and The Ship in Plymouth.
Today, the company has received permission to develop 35 quality business units at Exeter’s SkyPark Development Site, which was purchased in August 2020. With a renewable energy focus, Burrington Estates aims to include Solar PV and EV charging points, insulated panel technology and covered bicycle storage as some of the key features. The units will be built to the BREEAM ‘Excellent’ benchmark and provide flexible spaces from 1000 sq ft. The project is expected to be completed by August 2021. More excitingly, the company is carrying its trade across Europe. In the heart of the French Riviera, Burrington Estates is taking its expertise to a property rental site in high demand, Villa Le Grand Bleu, in the area of Super Cannes, to broaden its overseas opportunities.
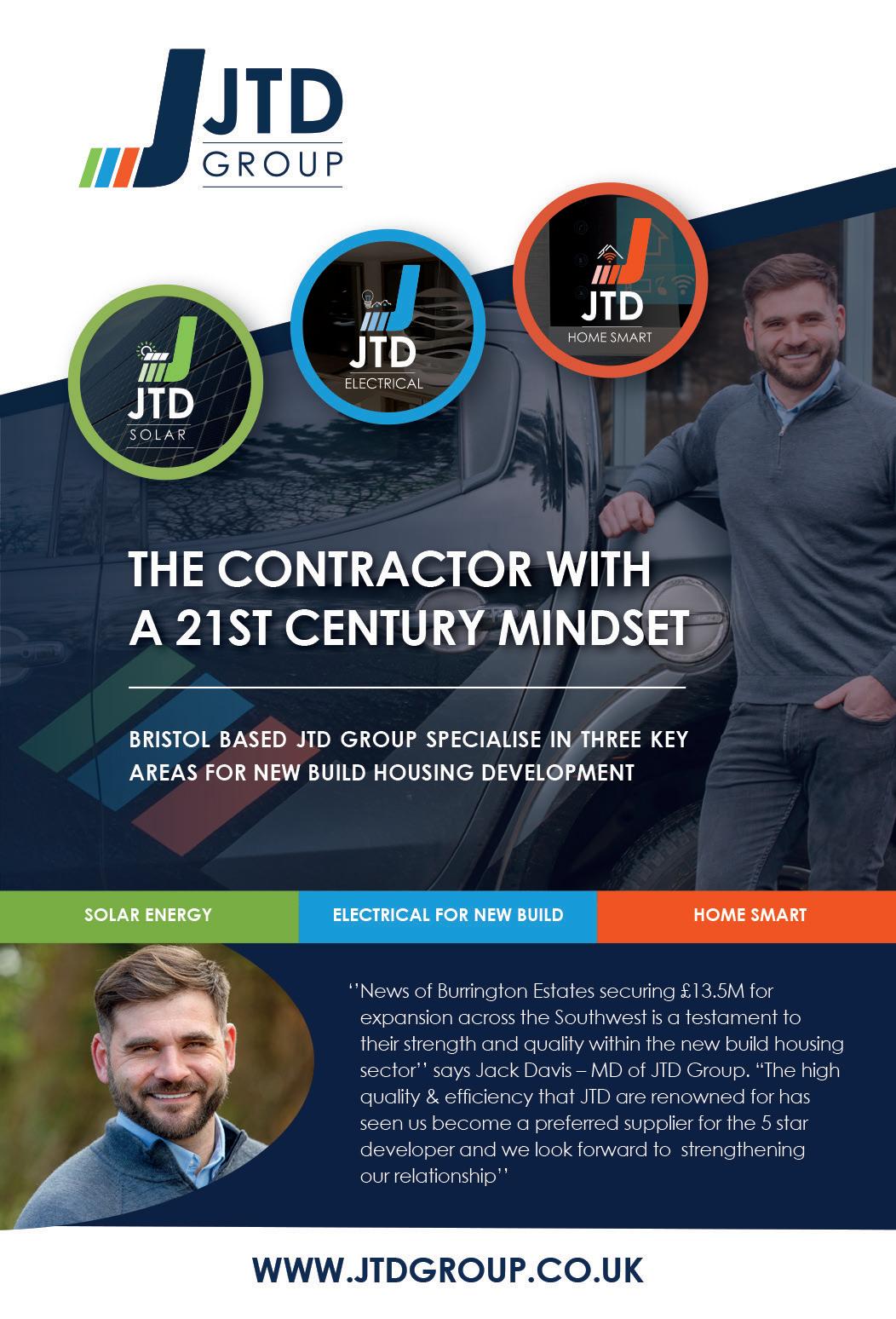
Image for illustration purposes only
Of course, the company’s impressive projects have not gone unnoticed. Since 2017, NHBC has commemorated Burrington Estates’s work with the ‘Pride in the Job’ and ‘Seal of Excellence’ awards for three consecutive years. This competition is highly regarded in the house-building industry and recognises site managers who achieve excellent standards in house building. For Burrington Estates to receive such awards proves its success in management, and acknowledges its dedication to pursuing excellence in delivering prime homes for homeowners in the UK.
Additionally, in 2020 it was awarded the prestigious ‘Housebuilder of the Year’ at the Insider South West Residential Property Awards 2020. Burrington Estates was made a stand out winner for its unrivalled standard of new homes being built across Devon and Cornwall.
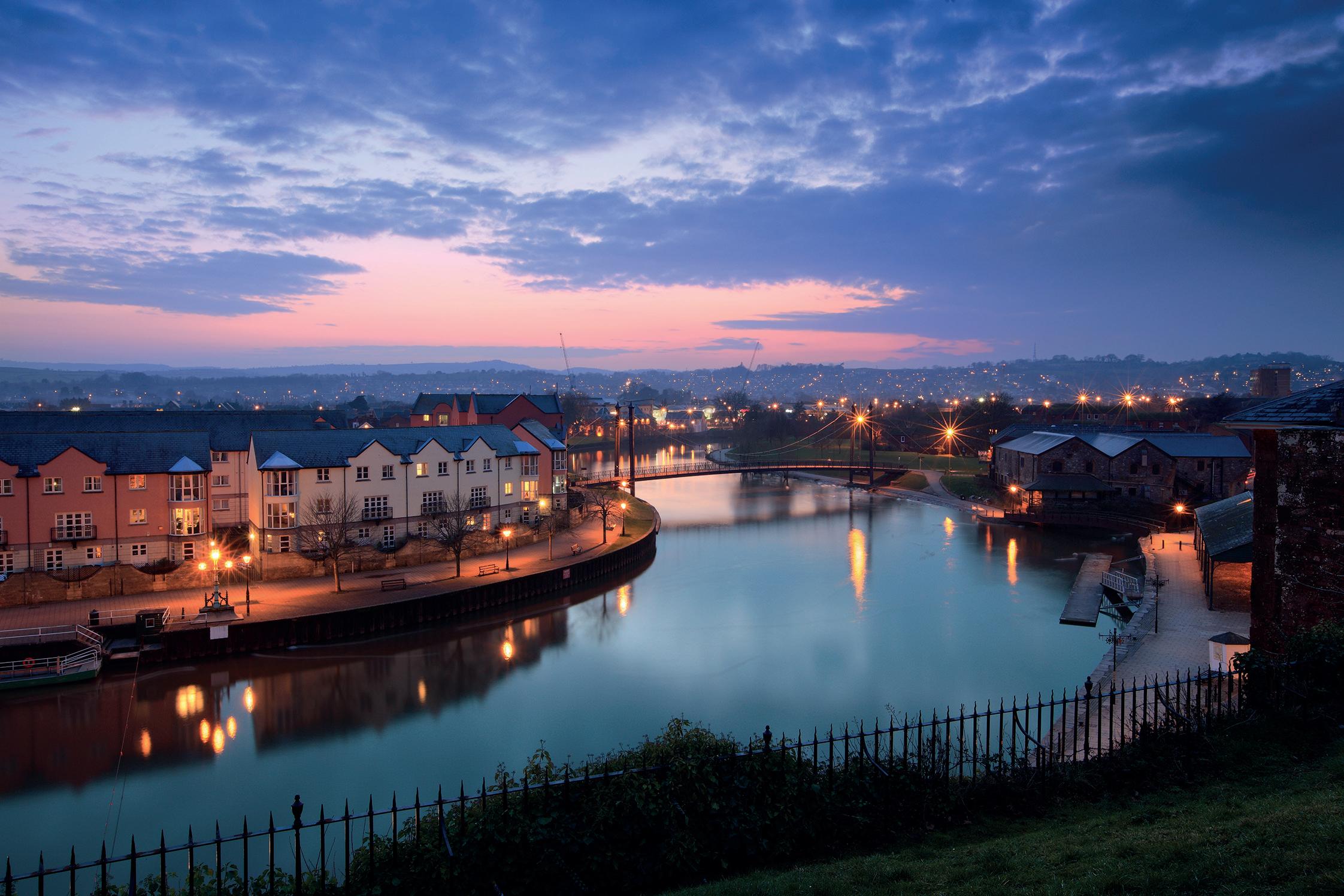
Investment plans
However, despite these already remarkable achievements, Burrington Estates continue to strive for higher goals. By 2026, Mark aims to treble the turnover for the company and so far, the trajectory looks promising. In March of this year, the company announced that BGF, the most active British growth investor which has invested £2.5 billion into nearly 400 companies, pledged a £15.5m investment into Burrington Estates. “We have found real chemistry with the BGF team and look forward to partnering with them in building a flourishing business,” Mark commented.
Of this investment, Mark is funnelling £13.5 billion toward expanding Burrington Estates New Homes across the South West and Midlands, a decision that will stand his turnover goals in good stead. The remaining £2 million will be allocated to Burrington Estates Commercial Development Business, a project to build and sell business parks containing small business units.
The philosophy “do what you love and do it well” is one of the pillars buttressing the success of Burrington Estates, and laying down a legacy of craftsmanship in home and business development is at the fore of its priorities. The company continues to push for properties that equip both homeowners and business people with beautiful spaces in which to thrive.
Home builder and commercial specialists
