
7 minute read
Satellite constellation engineering: Blending legacy systems with modern manufacturing principles
As the number of active satellites in orbit continues to grow at a rapid rate, heritage components evolve to bridge the gap between cost, mass production, and performance.
Brian Ippolitto, Senior Director, Business Development of Space Business Unit, Marotta Controls, Inc.
Propulsion systems onboard space vehicles are not typically characterized by high-volume, low-cost development, engineering, and production. Built for specialized missions, these high-reliability systems are manufactured in very small numbers, typically dozens at a time, or less. While that was once the nature of space itself – a vast frontier with relatively few pioneers blazing new trails – today the landscape is much different. The proliferation of Low Earth Orbit (LEO) satellite constellations represents a new opportunity, both commercial and military, featuring hundreds or thousands of satellites per constellation. Working together, these systems solve remote sensing challenges, gather and transmit data, monitor weather and climate patterns, provide affordable internet services to rural areas, and enable fast and reliable global communications.
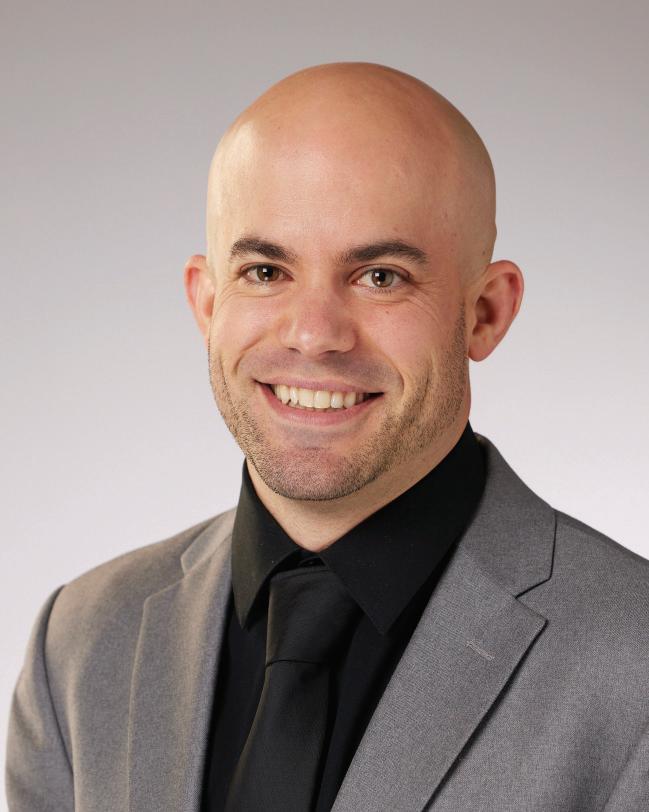
Constellations are recognized for low latency, with swarms of small units (<500kg) designed to be cheaper and faster to deploy. Propulsion systems, once designed for production of one, five, ten, or one hundred, now need to be manufactured by the thousands in certain cases. This demands an entirely new design and development model, one that must leverage existing systems, components, and expertise proven for spaceflight. As illustrated in Figure 1, NewSpace customers are willing to sacrifice some mission capability in order to prioritize cost and schedule. With planned constellations now routinely consisting of many hundreds or thousands of satellites, as opposed to a dozen or less on a legacy program, operational success can be achieved while minimizing the impact of single-unit failures.
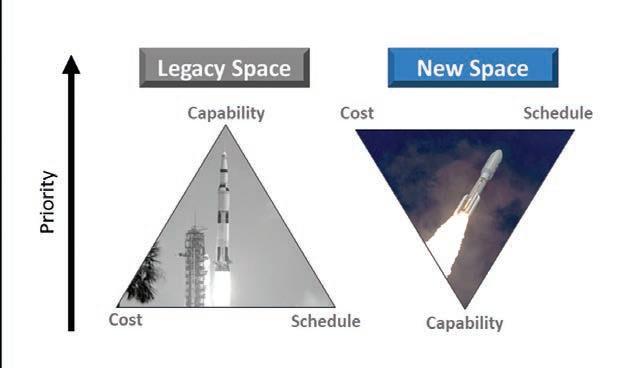
Industry options are slowly evolving to address this challenge. Modular designs tap into the heritage of proven components, now supported by Design for Manufacturing (DFM) principles that balance quality against costs and scalable production.
MAKING TRADES TO BALANCE QUALITY, COST, AND PERFORMANCE
Traditional space heritage technologies are exceptional in every way – but their extremely low volume production, extended development timelines, and high costs do not meet the mission needs for new space innovators working to beat the odds with successful mega-constellation development. At the other end of the spectrum are inkjet printer companies or hobby rocketry firms, providing lowcost, low-quality materials. Neither approach meets the need for quickly and competitively delivering massive numbers of space-proven components optimized for LEO constellation development.
Designing with a lower-priced, non-heritage component and working to increase its quality is a risky approach for constellation developers. Alternatively, the strategic ideal is to access proven quality but identify other opportunities to reduce costs. To achieve this, system developers and their component providers must be willing to work in close partnership – evaluating potential design trades early in the development cycle. How will the system really be used? Can design trades accommodate a minor percentage drop in performance parameters? The smallest adjustments can make all the difference in balancing cost and manufacturability, with limited impact on overall performance. The same close cooperation can also help aerospace suppliers and their manufacturing partners redefine production techniques, reducing costs and enabling manufacturing at scale.
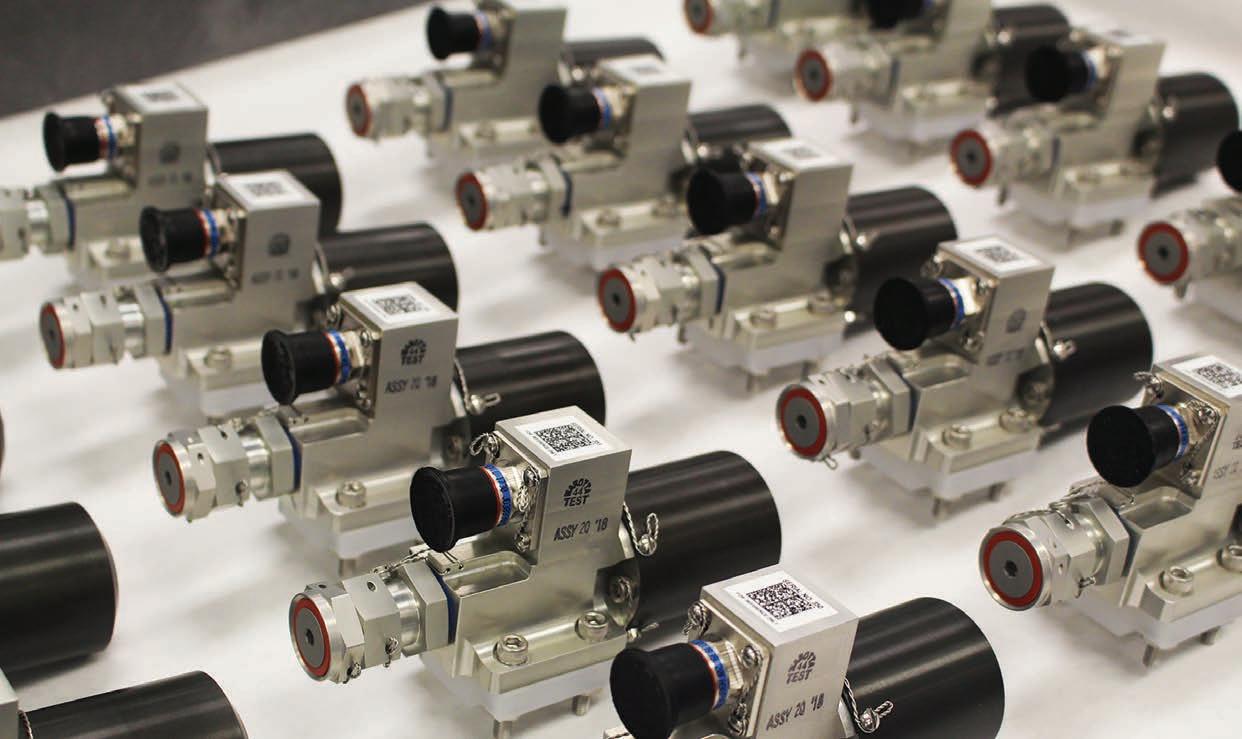
APPLYING DFM STRATEGIES TO HERITAGE TECHNOLOGIES
Heritage components often demand more complex machining operations, with multiple steps and tool paths increasing complexity and cost. Collaboration and new technology are helping to streamline manufacturing, often allowing components to be created using a single machine. Heritage developers must work closely with a new set of suppliers, refining and retooling machine operations for the most cost-effective solution. This simplicity, coupled with the ability to produce large numbers of a certain part already proven in a spaceflight system, creates immediate economies of scale. Parts can be generated much more effectively and used in a variety of building block designs, enabling a streamlined, modular approach to developing propulsion subsystems.
PICKING UP SPEED WITH MODULAR SUBSYSTEMS BASED ON EXISTING HERITAGE PRODUCTS
This is demonstrated in the manifolded configuration of an electric propulsion system recently developed by Marotta Controls for use in a LEO constellation application. In contrast to chemical propulsion, electric propulsion is typically fueled by a noble gas such as krypton or xenon with very low flow rates. Such systems are used for minor adjustments and station keeping, controlling flow through tiny, pinhole-sized openings. Using existing Marotta components, the system required only minor design modifications to meet overall performance criteria. The company drew from its extensive catalog of spaceflightqualified components, designing the assembly in accordance with component capabilities using heritage data. Subcontractor-designed components selected are all commercial-off-the-shelf items with no significant changes.
A manifold arrangement was selected to minimize assembly time and complexity. The manifold design also offers modularity such that the system can be configured as mechanically regulated or bang-bang pulse-controlled. Subassemblies are assembled and tested prior to integration. The manifold is manufactured from a single piece of aluminum, all flow paths and connections are directly machined into the body. The manifold is similar to other Marotta valve bodies and can be manufactured at high production rates with ease. Consideration was given to machining optimization and producibility during the design.
In the use case presented above, low cost and high performance were achieved with component simplicity, and system architecture is largely focused on design for manufacturability. Common components are utilized wherever possible. Piece part count is kept to a minimum, and assembly complexity is considered and optimized. The regulator described contains just seven machined parts and is designed for a manifolded assembly interface. It features an adjustable setpoint and a high turn-down ratio in a compact, lightweight, and low-cost package. The solenoid valve contains just five machined parts and features an integrated filter and latching option.
HERITAGE EXPERTISE AND DESIGNS CREATE IMPACT ON CONSTELLATION STRATEGIES
The maturity of launch vehicle design is 60 years in the making, while the constellation business has progressed over the last handful of years and is only beginning to take shape. Here, new space stands on the shoulders of legacy space flight innovation. The same advancements that took mankind to the Moon and beyond are critical in constellation strategies – they just can’t be developed and delivered in the same way. Modular concepts leverage existing capabilities to develop or springboard propulsion systems. Development is accelerated overall and furthered with a DFM focus that features simplicity at the heart of the manufacturing process.
Even as cost is a consideration in a new space market focused on constellations and their associated volume production, systems must perform in space. System providers must understand the unique impact of physical rigors such as lack of gravity, extreme temperatures, and environmental contaminants.
Heritage expertise and product data allow providers to leverage this expertise and take a critical eye to component design. As NewSpace evolves, quality must remain the design starting point as industry players determine new ways to proliferate LEO systems affordably and quickly.
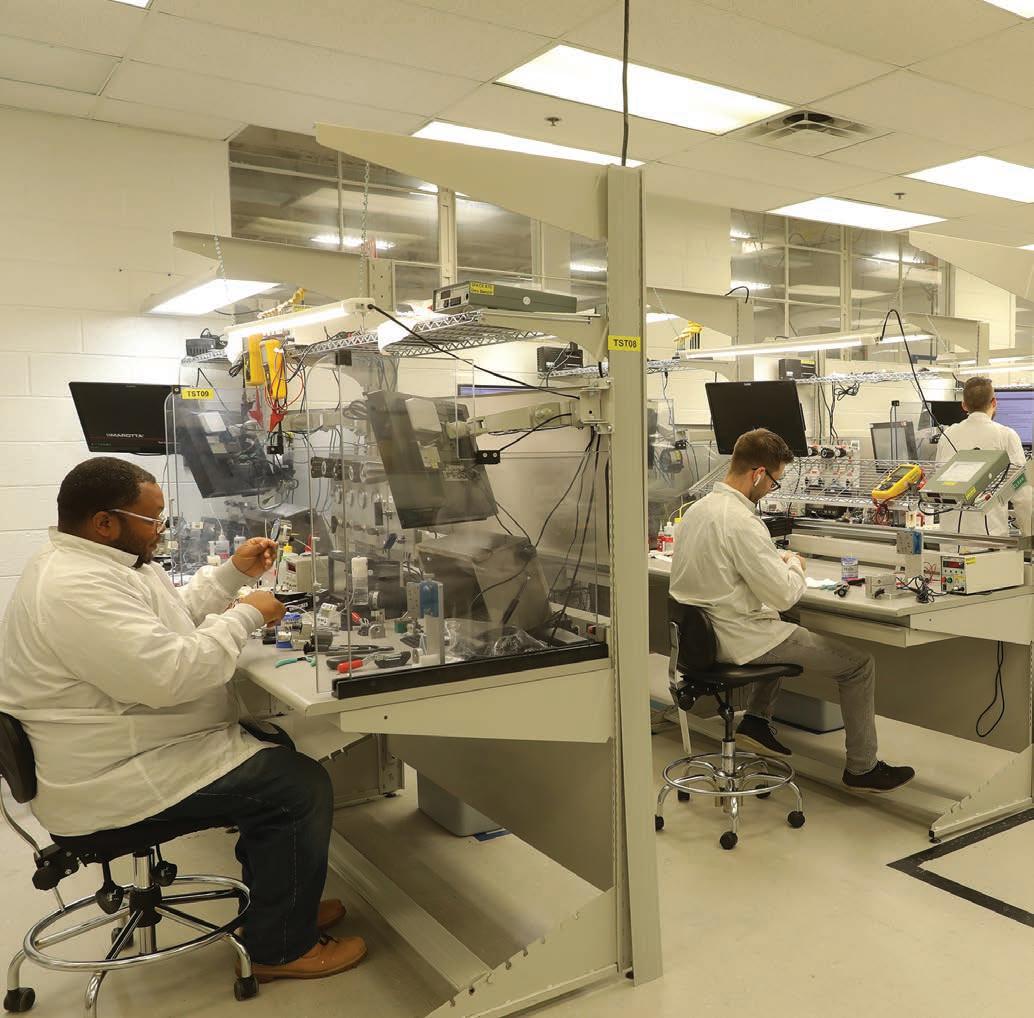
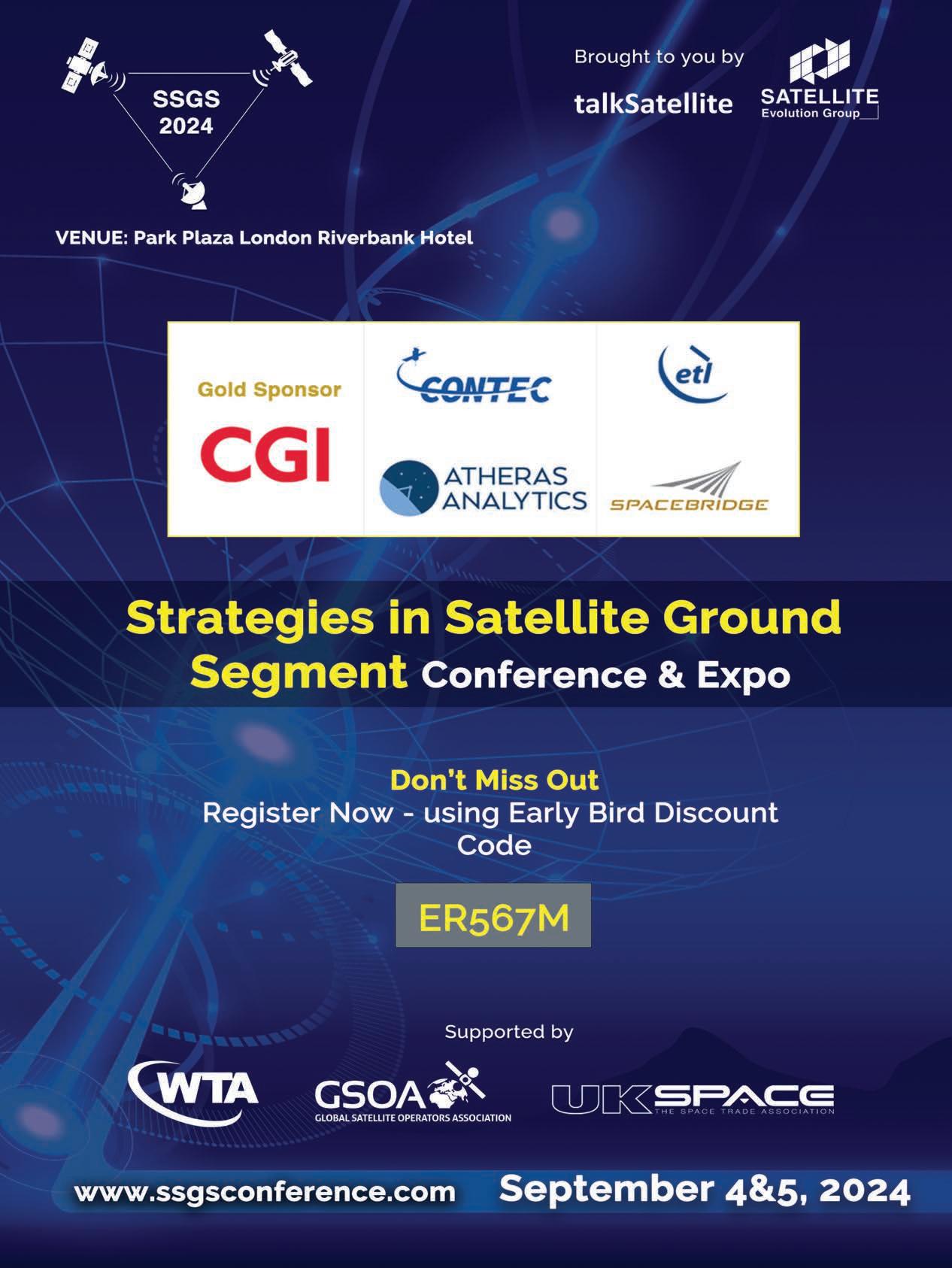