
6 minute read
Street Department
Director of Engineering: Louis Najar Street Superintendent: Quinton Miller
After the surface improvement of the Hot-inPlace process, the street is covered with a Micro Surface Type III process. This will seal the surface of the asphalt and give a more consistent driving surface. This will be at an investment of $504,923.16. This phase involved 4 city employees and lasted 4 weeks.
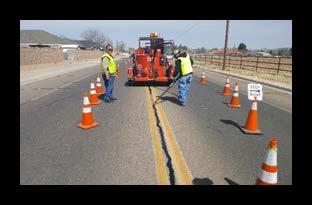
To finish the job once the micro surface is fully cured the street markings are restored. All lane markings, turn arrows, and crosswalks are restored. The cost for the remarking of the streets is covered in the budget under a scheduled striping contract. The Street Department has gotten fired up about fixing our street. The streets we have gotten hot about are South Main Street, West Alameda St, and North Sycamore Ave. Sections of these streets have had a major facelift this year. With the help of Dustrol, a contracted hot recycle company. Asphalt is heated in place, remixed, laid back down, and then compacted. You may have noticed the heater trucks leading a parade of other equipment during this process. The Dustrol process on these streets is an investment of $715,972.30 for the 1st phase of the work. This phase involved 4 city employees and lasted 6 weeks.
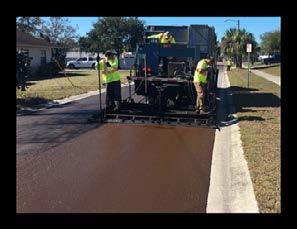
The work shown here is performed by contracted companies with specialized equipment doing one part of each project. Not all streets require the extensive work described above to improve and protect the street for longer life. A good number of streets in the North East areas and part of South Park Cemetery underwent a Slurry Seal process as part of the street maintenance plan. This in part was contracted work at an investment of $1,192,463.33. This project involved 7 employees and lasted 3 weeks.
The work begins with the street department along with the engineering department selecting the best value for the money available. Project measurements are made to ensure the scope of work will be within the budget allotted. Street department crews start preparing the street by repairing potholes and filling cracks. If necessary ruts of displaced asphalt can be milled down with a skid steer milling attachment. Street repair crews work almost year-round with the favorable weather at Roswell. Online Fix-it forms and call-in requests take priority to be fixed. The crack seal crew has used over twentyfour tons of material this year filling cracks in our streets.
Asphalt injection is another approach used to stop small defects in the roadway. The truck and trailer-mounted system use rock chips from the truck mixed with oil stored on the trailer and forced into small defects in the street to seal the street and prevent the defect from getting any larger. Estimated 6,480 gals of HFE 90 are used each year with an equal amount of rock chips from the city crusher. With repairs of larger diameter valves, the larger hole will require subgrade work. The repair to the street will be contracted out utilizing the Annual Maintenance Contract.
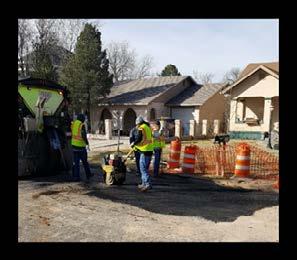

Part of the responsibility of the department is maintaining the alleys and right of way areas for weeds or other obstructions. Each part of the city has a dedicated mower equipped tractor to mow the alley and right of way where possible. The areas where the mowers are not suited are sprayed. The herbicide crew is required to maintain training and be licensed. 14000 gallons of herbicide were used this year. This is usually a 2 man crew working year-round.
The larger potholes, water line cuts, fiber optic cuts or some other damage to the street are repaired with the patch truck. The department has used 600 tons of patch material this year. This is usually a 3 man crew working year-round.

The Street Department maintains the alleys, to insure trash pickup, sewer service and access for utility companies. The crew consists of a maintainer blade, water truck and dump truck. The crew has used 4792 tons of gravel and 922 tons of road base this year. This crew also maintains the drainage ditches, gravel parking
Street Department
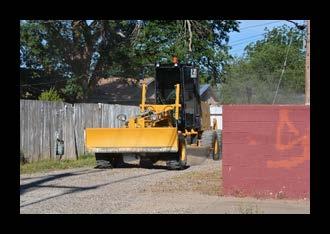
lots in the city and the preparation work for the larger contracted projects. This material was provided by the department rock crusher operation. This is usually a 3 man crew.
Director of Engineering: Louis Najar Street Superintendent: Quinton Miller

how much material was picked up, but we do have numbers on how much was hauled to the landfill. From the haul records, 4117 tons of trash material was taken from the streets. This is a three-man crew working year-round.
The city maintains a rock crusher operation to provide gravel and road base. Mine Safety Health Act training is a requirement that must be maintained for personnel working at the crusher site. The crusher operation is not a full-time operation, it operates based on the needs of the City and weather permitting the safe operation. One of the overlooked maintenance jobs is that of the sign shop. Each day some signs are replaced for a variety of reasons. Some are just faded out, but most fall victim to vandalism or traffic accident. The sign shop crew replaced over 100 signs, most required an 811 call for clearance. The cost of materials $10,158.70 and 105 man-hours. The sign shop plays a key role in the support of special events. Set up and recovery the programmable message boards and other equipment as required. On larger events, the entire street department might get involved in the process. This is a 2 man crew supported by the entire department if needed for special events. Fall is the time of year the street sweeper is working very hard to clear the street from all the falling leaves. The department has two late-model mechanical sweepers and one older vacuum type unit. The sweeper does not record Work continued at South Park Cemetery and Cielo Grande to improve the roads in these areas. The weeds in parking areas were cut, the roads were leveled off and 24000 gallons of PEP oil applied to both locations. Once the oil was cured, the area was slurry sealed.
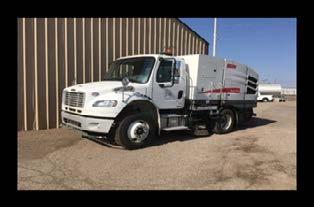
The Street Department is headed by Quin B. Miller as the Street Superintendent and Frank Rincon as the Street Supervisor. With 22 additional employees working in small crews or if needed combining crews to get the larger jobs finished. The crews cross-train to get the maximum value of the workday if others are missing due to vacation or illness. Helping other departments with equipment or manpower is something we will do very often. Supporting special events, demolition of old buildings or just moving clay at the museum we try to help whenever possible.