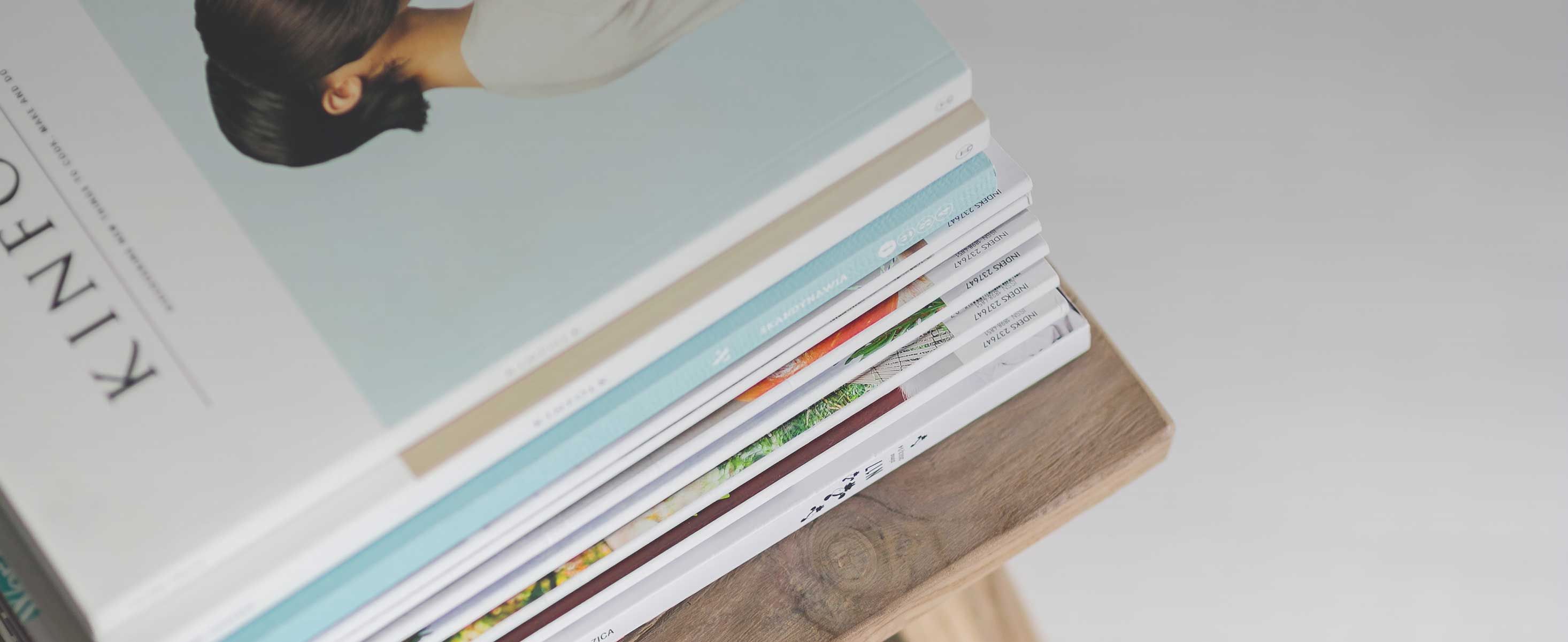
19 minute read
Concepts in Enterprise Resource Planning 4th
Edition Monk
Full download link at: Test bank: https://testbankpack.com/p/test-bank-for-concepts-inenterprise-resource-planning-4th-edition-by-monk-wagner-isbn1111820392-9781111820398/
Advertisement
Solution Manual: https://testbankpack.com/p/solution-manualfor-concepts-in-enterprise-resource-planning-4th-edition-bymonk-wagner-isbn-1111820392-9781111820398/
TRUE/FALSE
1. An ERP system is a good tool for developing and executing production plans because it integrates the functions of production planning, purchasing, materials management/warehousing, quality management, sales, and accounting.
ANS: T
This is an accurate description of an ERP system.
PTS: 1 REF: 78
2. Production planners aggregate products into product groups to make forecasts and plans more accurate.
ANS: F
Aggregate production plans help to simplify the planning process
PTS: 1 REF: 82
3. The Sales and Operations Planning process is used to combine the sales forecast with capacity information to determine a production plan for finished goods.
ANS: T
Sales and operations planning (SOP) is the next step in the production planning process. The input to this step is the sales forecast provided by Marketing and Sales. The output is a production plan designed to balance demand with production capacity.
PTS: 1 REF: 85
4. Demand Management is the process where sales forecasts are adjusted to incorporate the impact of marketing initiatives.
ANS: F
In the Demand Management step, the production plan is broken down into smaller time units, such as weekly or even daily production figures, to meet demand for individual products.
PTS: 1 REF: 84
5. The MRP process determines the schedule of finished goods production.
ANS: F
The Materials Requirements Planning (MRP) process determines the amount and timing of raw material orders.
PTS: 1 REF: 84
6. The term supply chain describes all the activities required to move raw material from inventory to manufacturing for the purpose of producing a product.
ANS: F
The term supply chain describes all the activities that occur between the growing or mining of raw materials and the appearance of finished products on the store shelf.
PTS: 1 REF: 109
7. In a traditional supply chain, demand information is transmitted rapidly to all members of the supply chain.
ANS: F
In a traditional supply chain, information is passed through the supply chain reactively, as participants change their product orders.
Because of the time lags, it might take weeks or even months for information about increased needs for raw materials to reach suppliers. Raw material suppliers might require time to increase their production to meet larger orders, resulting in temporary shortages for the supplier.
PTS: 1 REF: 109
8. ERP systems are necessary to implement good supply chain management.
ANS: F
The development of supply chain strategies does not necessarily require an ERP system. Before ERP systems were available, companies could be linked with customers and suppliers through electronic data interchange (EDI) systems.
PTS: 1 REF: 110
9. The percentage of the order that the supplier provides in the first shipment is known as the first-rate.
ANS: F
Initial fill rate is the percentage of an order that the supplier provided in the first shipment.
PTS: 1 REF: 112
10. Make to order items are produced to fill customer’s requests.
ANS: T
Make to order items are produced to fill specific customer orders.
PTS: 1 REF: 78
11. The cost it normally takes to manufacture a product, which is usually derived from historical data and any changes that have occurred since then, is known as a structured cost.
ANS: F
Standard costs are the normal costs of manufacturing a product; standard costs are calculated from historical data, factoring in any changes in manufacturing that have occurred since the collection of the historical data.
PTS: 1 REF: 81
12. Rough-cut planning is a common term in manufacturing for aggregate planning.
ANS: T PTS: 1 REF: 88
13. The production plan for all finished goods is known as the MPS, or the master production schedule.
ANS: T
The output of the demand management process is the master production schedule (MPS), which is the production plan for all finished goods.
PTS: 1 REF: 95
14. Another term for the list of ingredients required to make a product is the bill of materials.
ANS: T
The bill of material (BOM) is a list of the materials (including quantities) needed to make a product.
PTS: 1 REF: 97
15. Lead times and lot sizing help a company determine the transfer of goods to the customer.
ANS: F
The lead time is the cumulative time required for the supplier to receive and process the order, take the material out of stock, package it, load it on a truck, and deliver it to the manufacturer.
Lot sizing refers to the process of determining production quantities (for raw materials produced inhouse) and order quantities (for purchased items).
PTS: 1 REF: 98
16. Because Fitter Snacker uses large quantities of oats, the most cost-effective way to purchase oats is to buy a farm and grown them.
ANS: F
Because Fitter uses large quantities of oats, the most cost-effective way to purchase oats is in bulk hopper-truck quantities, which means that the material must be ordered in 44,000-pound quantities.
PTS: 1 REF: 98
17. After material requirements are entered into the system, the program automatically turns the planned orders into purchase orders without further input from planners.
ANS: F
Planning factors such as lead times are just estimates, so planners must evaluate the planned orders suggested by the materials requirements planning calculation before allowing the program to automatically turn them into purchase orders.
PTS: 1 REF: 100
18. The percentage of the order that the supplier provided in the first shipment is known as the initial order lead time.
ANS: F
Initial fill rate is the percentage of an order that the supplier provided in the first shipment. Another metric is initial order lead time, which is the time needed for the supplier to fill the order.
PTS: 1 REF: 112
19. The initial fill rate measures the time needed for the supplier to fill the order.
ANS: F
The initial order lead time is the time needed for the supplier to fill the order.
PTS: 1 REF: 112
Multiple Choice
1. A make-to-stock production system is where: a. items are made for inventory in anticipation of sales orders. b. items are produced to fill specific customer orders. c. items are assembled for a specific customer order from an inventory of components d. both a and c
ANS: A
Make-to-stock items are made for inventory in anticipation of sales orders: most consumer products are made this way.
PTS: 1 REF: 78
2. An unexpected increase in product demand can lead to: a. a depletion of finished goods inventories b. a depletion of raw materials inventories c. increased overtime and transportation expenses d. all of the above e. both a and b
ANS: D
When Production must meet an unexpected increase in demand, several things happen. First, warehouse inventories are depleted. To compensate, Production must schedule overtime labor, which results in higher production costs for products. Second, because some materials (such as ingredients, wrappers, and display boxes) are custom products purchased from a single vendor, a sudden increase in sales demand can cause shortages or even a stockout of these materials.
PTS: 1 REF: 80 a. 6,628 b. 7,128
The Fitter Snacker company sold 6,435 cases of snack bars in June of the previous year. They are expecting sales to increase by 3% this year. In addition, they are launching a promotional campaign in May, which they expect will increase sales in June by an additional 500 cases.
3. What is the sales forecast for June of this year that Fitter Snacker should use?
ANS: B
6,435 x 1.03 + 500 = 7,128
PTS: 1 REF: 85 c. 6,935 d. 7,143 a. 7,666 b. 9,199
Fitter Snacker can produce 333.3 cases of snack bars per day during the standard 8-hour work week. They can work 2 hours of overtime per weekday, plus 4 hours on Saturday. They are developing an SOP for a month with 23 weekdays and 4 Saturdays.
4. What is the maximum number of cases that Fitter Snacker can produce in the month if they schedule workers for overtime on weekdays only?
ANS: C c. 9,582 d. 10,249
On weekday overtime, they can produce 1.25 times the normal output, or (1.25)(333.3) = 416.6. In 23 days, they can produce (416.6)(23) = 9,581.8 cases, which rounds to 9,582. Adding in Saturdays is equivalent to two additional days of regular production, or (2)(333.3) = 666.6. The total time available is 9,582 + 666 = 10,248.6, which rounds to 10,249.
PTS: 1 REF: 96 a. 7,666 b. 9,199
5. What is the maximum number of cases they can product in the month if they schedule workers for overtime on weekdays and Saturdays?
ANS: D c. 9,582 d. 10,249
On weekday overtime, they can produce 1.25 times the normal output, or (1.25)(333.3) = 416.6. In 23 days, they can produce (416.6)(23) = 9,581.8 cases, which rounds to 9,582. Adding in Saturdays is equivalent to two additional days of regular production, or (2)(333.3) = 666.6. The total time available is 9,582 + 666 = 10,248.6, which rounds to 10,249.
PTS: 1 REF: 96 a. 188 c. 940 b. 752 d. 1034
6. The production plan at Fitter Snacker calls for 4,134 cases of snack bars in January. If there are 22 days in the month, how many cases of snack bars should be produced in a 4-day week?
ANS: B
To calculate the weekly quantity, we take (4,134 / 22) (4) = 751.63, which rounds to 752.
PTS: 1 REF: 96
Fitter Snacker orders oats in 44,000 lb. batches. Given the following (incomplete) MRP record: a. An order for 44,000 units in week 2 b. An order for 44,000 units in week 3 c. An order for 44,000 units for weeks 2 and 3 d. An order for 88,000 units for week 3
7. What Planned Orders will the MRP logic create?
ANS: A
The completed MRP record is:
PTS: 1 REF: 99
8. What will the On Hand inventory be in week 5 after the system calculated planned orders?
ANS: C
The completed MRP record is:
PTS: 1 REF: 99
9. Immediately after MRP is run in SAP ERP: a. the stock/requirements list and MRP list are both updated and show the same information. b. the MRP list is updated but the stock/requirements list is unaffected. c. the stock/requirements list is updated but the MRP list is unaffected. d. none of the above.
ANS: A
The MRP list shows the results of the MRP calculations, while the Stock/Requirements List shows those results plus any changes that have occurred since the MRP list was generated (planned orders converted to purchase orders or production orders, material receipts, and so on).
PTS: 1 REF: 101
10. In detailed scheduling, longer production runs of a particular product: a. increases the available capacity by reducing the frequency of setups. b. increases finished goods inventory levels. c. reduces finished goods inventory levels. d. both a and b e. both a and c
ANS: D
Longer production runs mean that fewer machine setups are required, reducing production costs and increasing the effective capacity of the equipment. On the other hand, shorter production runs can be used to lower the inventory levels for finished products.
PTS: 1 REF: 105
11. The order of the steps in the SAP R/3 production planning process are: a. Sales Forecasting, Demand Management, Purchasing, Sales and Operations Planning, MRP, Detailed scheduling, Production b. Sales Forecasting, Demand Planning, Detailed scheduling, Purchasing, Demand Management, MRP, Production c. Sales and Operations Planning, Sales Forecasting, MRP, Purchasing, Demand Management, Detailed scheduling, Production d. Sales Forecasting, Sales and Operations Planning, Demand Management, MRP, Purchasing, Detailed scheduling, Production
ANS: D
The order is Sales Forecasting, Sales and Operations Planning, Demand Management, MRP Purchasing, Detailed scheduling, Production.
PTS: 1 REF: 83 a. 500 b. 2100
12. The production plan for Fitter Snacker calls for 7000 cases of the snack bar product group in June. If the snack bar product group consists of NRG-A and NRG-B bars with the proportion 70% NRG-A bars and 30% NRG-B bars, how many NRG-A bars should be produced in June?
ANS: C
7000 * .7 = 4900 NRG-A c. 4900 d. 7000
7000 * .3 = 2100 NRG-B
PTS: 1 REF: 85 a. standard costs b. abbreviated costs
13. The costs normally required to manufacture a product, which are calculated from historical costs and any changes from that, are known as ____.
ANS: A c. known costs d. estimated costs
Standard costs are the normal costs of manufacturing a product; standard costs are calculated from historical data, factoring in any changes in manufacturing that have occurred since the collection of the historical data.
PTS: 1 REF: 81 a. Bills of materials b. Production runs c. Internet sales orders d. Rough-cut plans
14. ____ are disaggregated to generate detailed production schedules.
ANS: D PTS: 1 REF: 88 a. MPS - master production schedule b. QQR - quality query run
15. What is the production plan for all finished goods?
ANS: A c. PPR - production planning run d. RUN - run
The output of the demand management process is the master production schedule (MPS), which is the production plan for all finished goods.
PTS: 1 REF: 95
16. What process answers the question “What do we need to order to produce the product, and when do we need to order these raw materials?” a. SF - sales forecasting b. SOP - sales and operations planning
ANS: C c. MRP - materials requirements planning d. DS - detailed scheduling
The raw materials requirements planning process answers the questions, “What quantities of raw materials should we order so that we can meet that level of production?” and “When should these materials be ordered?”
PTS: 1 REF: 97 a. initial fill rate b. initial order lead time c. on-time performance d. cash-to-cash cycle time
17. What metric tracks the number of times a supplier meets the agreed upon delivery date?
ANS: C PTS: 1 REF: 112 a. MRP b. Sales Forecasting c. Starting Inventory d. Detailed Scheduling
18. In the accompanying figure, which shows the SAP ERP production planning process, what is A?
ANS: B PTS: 1 REF: 83 a. Starting Inventory b. Detailed Scheduling c. Sales Forecasting d. MRP
19. In the accompanying figure, which shows the SAP ERP production planning process, what is B?
ANS: A PTS: 1 REF: 83 a. Starting Inventory b. Sales Forecasting c. MRP d. Detailed Scheduling
20. In the accompanying figure, which shows the SAP ERP production planning process, what is C?
ANS: D PTS: 1 REF: 83 a. Starting Inventory b. Detailed Scheduling c. Sales Forecasting d. MRP
21. In the accompanying figure, which shows the SAP ERP production planning process, what is D?
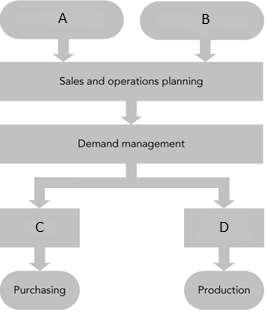
ANS: D PTS: 1 REF: 83 a. Sales Forecasting b. BOM
22. What stage of the production planning process splits Fitter Snacker’s monthly production planning values into finer time periods?
ANS: D c. MRP d. Demand Management
In the Demand Management step, the production plan is broken down into smaller time units, such as weekly or even daily production figures, to meet demand for individual products.
PTS: 1 REF: 84
1. The ____________________, shown in the accompanying figure for Fitter Snacker, is a list of the materials needed to make NRG-A and NRG-B bars.

ANS: Bill of Materials
BOM
Bill of Materials (BOM)
BOM (Bill of Materials
PTS: 1 REF: 97-98
2. ____________________ refers to the process of determining production quantities (for raw materials produced in-house) and order quantities (for purchased items).
ANS: Lot sizing
PTS: 1 REF: 98
MATCHING a. MRP b. Demand Management c. Purchasing d. Sales Forecasting e. Detailed Scheduling f. Starting Inventory g. Production h. Sales and Operations Planning
Match the letters in the accompanying figure with a statement below.
1. What is A?
2. What is B?
3. What is C?
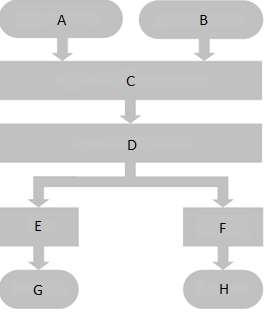
4. What is D?
5. What is E?
6. What is F?
7. What is G?
8. What is H?
1. ANS: D PTS: 1 REF: 83
2. ANS: F PTS: 1 REF: 83
3. ANS: H PTS: 1 REF: 83
4. ANS: B PTS: 1 REF: 83
5. ANS: A PTS: 1 REF: 83
6. ANS: E PTS: 1 REF: 83
7. ANS: C PTS: 1 REF: 83
8. ANS: G PTS: 1 REF: 83
Short Answer
1. How can data be entered into the SAP ERP system on the shop floor?
ANS:
Data can be entered into SAP ERP through a PC on the shop floor, scanned using barcode or RFID technology, or entered using a mobile device. SAP ERP is an open-architecture system, meaning that it can work with automated data-collection tools marketed by third-party hardware and software companies.
PTS: 1 REF: 107
2. When might the SAP ERP system block the entry of the receipt of goods in the receiving department?
ANS:
Depending on the configuration settings, the SAP ERP system might block entry of the receipt if the discrepancy is too large.
PTS: 1 REF: 108
Essay
1. What are the three general approaches to production?
ANS:
1. Make-to-stock items are made for inventory (the “stock”) in anticipation of sales orders. Most consumer products (for example, cameras, canned corn, and books) are made this way.
2. Make-to-order items are produced to fill specific customer orders. This approach is usually taken when producing items that are too expensive to keep in stock or items that are made or configured to customer specifications. Examples of make-to-order items are airplanes and large industrial equipment.
3. Assemble-to-order items are produced using a combination of make-to-stock and make-to-order processes. The final product is assembled for a specific order from a selection of make-to-stock components. Personal computers are a typical assemble-to-order product.
PTS: 1 REF: 78-79
2. What are the three principles that production planners follow?
ANS:
1. Work from a sales forecast and current inventory levels to create an “aggregate” production plan for all products. Aggregate production plans help to simplify the planning process. The plans are usually aggregated in two ways. First, plans are made for groups of related production rather than for individual products. Second, the time increment used in planning is frequently a month or a quarter rather than the daily or weekly production plans that will actually be executed. Aggregate plans should consider the available capacity in the facility.
2. Break down the aggregate plan into more specific production plans for individual products and smaller time intervals.
3. Use the production plan to determine raw material requirements.
PTS: 1 REF: 82
3. List and explain each step of the production planning process.
ANS:
§ Sales Forecastingisthe process of developing aprediction offuture demandfor acompany’s products.
§ Sales and Operations Planning (SOP) is the process of determining what the company will produce. The Sales Forecast and Starting Inventory levels are inputs to this process. At first glance, it would seem that acompanyshouldjustproduceproductstomatchtheforecastedsales,butdevelopingtheproduction plan can be complicated because capacity must be considered. Many products have seasonal demand, and tomeet demand duringpeak periods, production planners must decide whether to build up inventory levels before the peak demand, increase capacity during the peak period, subcontract production, or use some combination.
§ Demand Management is the process of breaking down the production plan into smaller time units, such as weekly or even daily production figures, to meet demand for individual products.
§ Materials Requirement Planning (MRP) process determines the amount and timing of raw materials orders. This process answers the questions: “What raw materials should we be ordering so we can meet a particular level of production?” and “When should we order these materials?”
§ Purchasing takes the quantity and timing information from MRP and creates purchase orders for raw materials, which it transmits to qualified suppliers.
§ Detailed Scheduling uses Demand Management’s production plans as an input for a production schedule.Methods of detailed schedulingdepend onthe manufacturing environment. For Fitter Snacker, the detailed production schedule will determine when to switch between the production of NRG-A to NRG-B bars.
§ Production uses the detailed schedule to manage daily operations, answering the questions, “What should we be producing?” and “What staffing do I need?”.
PTS: 1 REF: 83-84
4. SAP can provide sophisticated tools to support sales and operations planning. Is that all that is necessary for a company to be successful? Support your answer by discussing the departments of marketing and manufacturing.
ANS:
While an integrated ERP system like SAP can provide sophisticated tools to support sales and operations planning, the plan will only be successful if the interested parties are committed to the process. If Marketing and Manufacturing cannot agree on sales forecasts, promotions, and production plans, then the company will find that it is overstocked in some items, running out of others, and spending a lot of money on overtime production and expedited shipping. Successful sales and operations planning depends on developing a culture of cooperation between Marketing and Manufacturing, which usually requires continuous support, encouragement, and enforcement from top management. Changing a company’s culture is usually a much harder challenge than the technical challenge of installing new hardware and software.
PTS: 1 REF: 92
5. What is repetitive manufacturing?
ANS:
Repetitive manufacturing environments typically have production lines that are switched from one product to another similar product. Most packaged consumer goods are produced in repetitive manufacturing environments. In repetitive manufacturing, production lines are scheduled for a period of time, rather than for a specific number of items, although it is possible to estimate the number of items that will be produced over a period of time.
PTS: 1 REF: 105
6. Describe the measurements of success with Supply Chain Management.
ANS:
Performance measurements (sometimes referred to as metrics) have been developed to show the effects of better supply chain management. One measure is called the cash-to-cash cycle time. This term refers to the time between paying for raw materials and collecting cash from the customer. In one study, the cash-to-cash cycle time for companies with efficient supply chain management processes was a month, whereas the cycle averaged 100 days for those companies without effective supply chain management.
Another metric is total supply chain management costs. These costs include the cost of buying and handling inventory, processing orders, and supporting a company’s information systems. In one study, companies with efficient supply chain management processes incurred costs equal to 5 percent of sales. By contrast, companies without supply chain management incurred costs of up to 12 percent of sales.
Other metrics have been developed to measure what is happening between a company and its suppliers. For example, Staples, the office-supply company, measures three facets of the relationship. Initial fill rate is the percentage of an order that the supplier provided in the first shipment. Another metric is initial order lead time, which is the time needed for the supplier to fill the order. Finally, Staples measures on-time performance. This measurement tracks how often the supplier met agreedupon delivery dates.
Improvements in metrics such as these lead to improvements in overall supply chain cost measurements.
PTS: 1 REF: 112
7. Explain Fitter Snacker’s manufacturing process as shown in the accompanying figure:

ANS:
Raw materials are taken from the warehouse to one of four mixers. Each mixer mixes dough in 500-pound batches. Mixing a batch of dough requires 15 minutes of mixing time, plus another 15 minutes to unload, clean, and load the mixer for the next batch of dough; therefore, each mixer can produce two 500-pound batches of dough per hour. That means the four mixers can produce a total of 4,000 pounds of dough per hour more than the production line can process. Because only three mixers need to be operating at a time to produce 3,000 pounds of snack bars per hour, a mixer breakdown will not shut down the production line.
After mixing, the dough is dumped into a hopper (bin) at the beginning of the snack bar production line. A forming mechanism molds the dough into bars, which will weigh 4 ounces each. Next, an automated process takes the formed bars on a conveyor belt through an oven that bakes the bars for 30 minutes. When the bars emerge from the oven, they are individually packaged in a foil wrapper, and each group of 24 bars is packaged into a display box. At the end of the snack bar line, display boxes are stacked on pallets (for larger orders the display boxes are first packed into shipping boxes, which are then stacked on the pallets).
Switching the production line from one type of snack bar to the other takes 30 minutes for cleaning the equipment and changing the wrappers, display boxes, and shipping cases. Each night, a second shift of employees cleans all the equipment thoroughly and sets it up for the next day’s production. Thus, changing production from NRG-A on one day to NRG-B the next day can be done at the end of the day without a loss of capacity. (Capacity is the maximum amount of bars that can be produced.) On the other hand, producing two products in one day results in a half-hour loss of capacity during the changeover.
PTS: 1 REF: 79
8. Describe Fitter Snacker’s communication problems with regard to the production process.
ANS:
Communication breakdowns are an inherent problem in most companies, and they are magnified in a company with an unintegrated information system. For example, at Fitter, Marketing and Sales personnel do a poor job of sharing information with Production personnel. Marketing and Sales frequently excludes Production from meetings, neglects to consult Production when planning sales promotions, and often fails to even alert Production of planned promotions. Marketing and Sales also typically forgets to notify Production when it takes an exceptionally large order.
When Production must meet an unexpected increase in demand, several things happen. First, warehouse inventories are depleted. To compensate, Production must schedule overtime labor, which results in higher production costs for products. Second, because some materials (such as ingredients, wrappers, and display boxes) are custom products purchased from a single vendor, a sudden increase in sales demand can cause shortages or even a stockout of these materials. Getting these materials to Fitter’s plant might require expedited shipping, further increasing the cost of production. Finally, unexpected spikes in demand result in high levels of frustration for Production staff.
Production personnel are evaluated on their performance how successful they are at controlling costs, keeping manufacturing lines running, maintaining quality control, and operating safely. If they cannot keep production costs down, Production staff receive poor evaluations. Managers are especially frustrated when an instant need for overtime follows a period of low demand. With advance notice of a product promotion by Marketing and Sales, Production could use slack periods to build up inventory in anticipation of the increase in sales.
PTS: 1
REF: 80
9. Describe Fitter Snacker’s inventory problems with regard to their production process.
ANS:
As noted earlier, Fitter’s week-to-week and day-to-day production planning is not linked in a systematic way to expected sales levels. When deciding how much to produce, the production manager applies rules developed through experience. Her primary indicator is the difference between the normal amount of finished goods inventory that should be stocked and the actual inventory levels of finished goods in the warehouse. Thus, if NRG-A or NRG-B inventory levels seem low, the production manager schedules more bars for production. However, she does not want too many bars in inventory because they have a limited shelf life. Her judgment is also influenced by the information she hears informally from people in Marketing and Sales about expected sales levels.