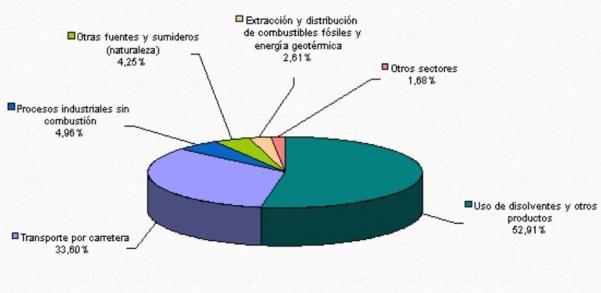
81 minute read
5° Paso Rolado 10
¿QUÉ ES LA PINTURA EN POLVO ELECTROSTÁTICA?
Ing. Carlos Villena Loayza
Advertisement
Una de las industrias que más contaminan el medio ambiente son las pinturas líquidas con un 53% (Figura 1), porque estas emiten gases contaminantes con gran impacto en la capa de ozono, esta preocupación a obligado a los gobiernos de diversos países del mundo, a emitir medidas y regulaciones para disminuir emisiones contaminantes.
La industria de la pintura en general es una de las etapas más importantes en el proceso productivo, sin embargo, en muchas empresas no le dan la atención que merecen. Una de las razones es por el poco conocimiento que se tiene de la pintura en polvo electrostática.
Como consecuencia de estos factores, la pintura en polvo electrostática ha ido ganando popularidad y aceptación en el mercado de recubrimientos industriales básicamente por sus propiedades finales de dureza, resistencia a la corrosión, excelente acabado, fácil aplicación y amigable con el medio ambiente.
Figura 1: Principales fuentes de COV’s. Fuente: http://www.troposfera.org/imagenes/covs/04.gif
El proceso de pintado en polvo se desarrolla a finales de los años 60 como una alternativa a las pinturas líquidas y su crecimiento se debe a 3 factores:
La adopción de nuevas leyes para el control de emisiones de componentes volátiles a la atmósfera. La urgencia de economizar los recursos energéticos no renovables. Los avances tecnológicos en el recubrimiento y los sistemas de aplicación
Para dar a conocer el proceso y aplicación de la pintura en polvo, se presentará el sistema más utilizado en la industria peruana. Este consta de 3 etapas principales:
PRETRATAMIENTO QUÍMICO POR INMERSIÓN
Este método consiste en sumergir el material de manera secuencial en diferentes tanques con productos químicos. Este tratamiento es el más recurrido debido a su practicidad del control y versatilidad para tratar variedad de piezas, tiene la ventaja de llegar a resquicios u otras áreas de las piezas en las cuales no puede ser posible por aspersión. La secuencia es: Desengrase Alcalino Desoxidado o Decapado Fosfatizado de Zinc o de Hierro Pasivado Crómico o Biodegradable Secado
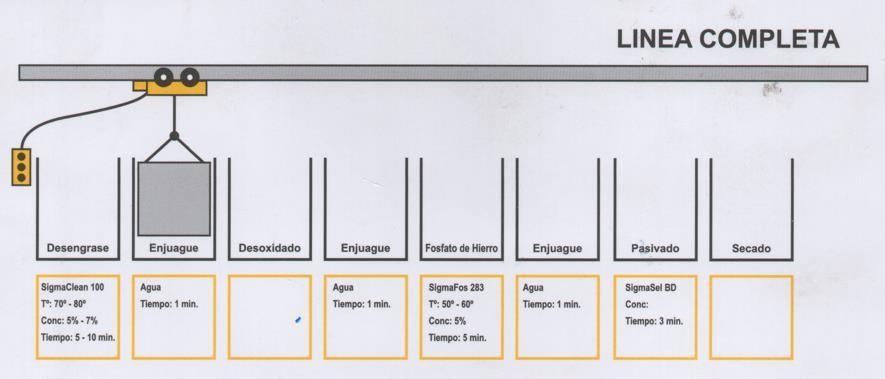
Figura 2. Línea completa del sistema de pretratamiento por inmersión.
Las 3 primeras con sus respectivos enjuagues como se observa en la Figura 2.
Fuente: Elaboración Propia.
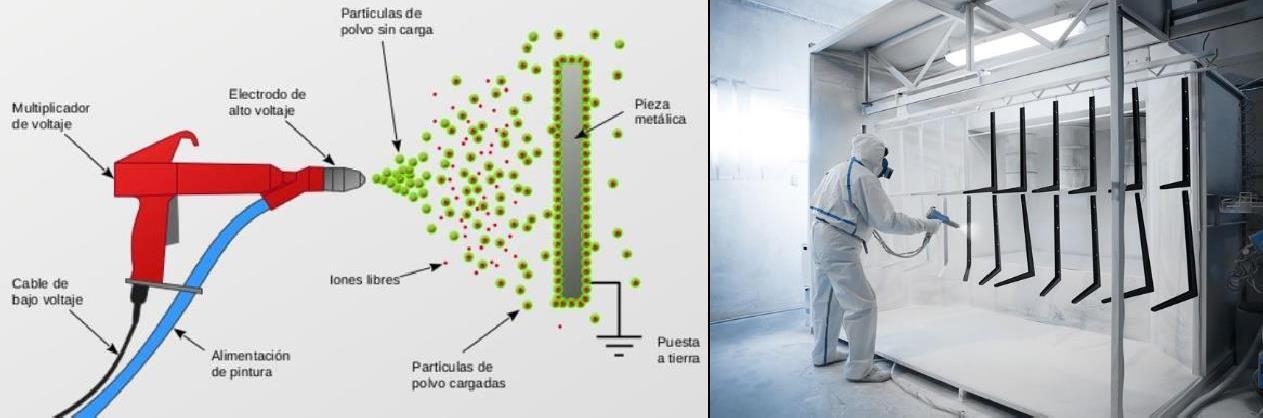
Figura 3a: Sistema de aplicación de pintura electrostática. Figura 3b: Cabina de pintura. Fuente: https://www.finishingsystems.com/equipment/industrial-finishing/powder-coating-booths/
APLICACIÓN DE PINTURA
La tecnología que realiza este principio se conoce como carga por ionización, el cual se basa en el principio de funcionamiento de un imán en el que las cargas opuestas se atraen, por lo tanto, la mayoría de materiales conductivos son apropiados para ser revestidos por este tipo de proceso. Preparada la pieza se cuelga en unos ganchos con carga negativa, una vez que ingresa a la cabina por medio de un transportador, se lanza la pintura en polvo con carga positiva (Ver Figura 3a), siendo que esta se deposite y se adhiera sobre la superficie de la pieza (Ver Figura 3b), la cabina debe tener un ciclón para recuperar el polvo no depositado en la pieza. Las cabinas deben disponer de una extracción de aire a baja velocidad detrás de la pieza y una ranura de aspiración a gran velocidad en la base de la cabina, con el objetivo de que el volumen de aire de la cabina no expulse el polvo fuera de ella. En forma seguida se traslada al horno de curado.
CURADO U HORNEADO
Llamamos“Curado”o“Polimerización”alproceso de conversión química de un monómero o una mezcla de monómeros en un polímero, es decir, en lapráctica es la acción defusionar las partículas de polvo en una película solida única, homogénea e integral, a través de un proceso de calentamiento de las partículas.
Donde surgen unas trasformaciones físicas y reacciones químicas de endurecimiento. Los sistemas más conocidos para curar pintura en polvo son:
Convección de calor Irradiación de calor UV – Lámparas ultravioletas
Siendo el más usado el curado por convección de calor, el cual consiste en realizar el intercambio de calor de la pieza a través del suministro de aire caliente de fuentes de calor como quemadores de GLP o gas natural como se aprecia en la Figura 4. En este sistema, toda la masa de la pieza se calienta a la temperatura nominal establecida. Apto para pieza de pequeño y mediano grosor.
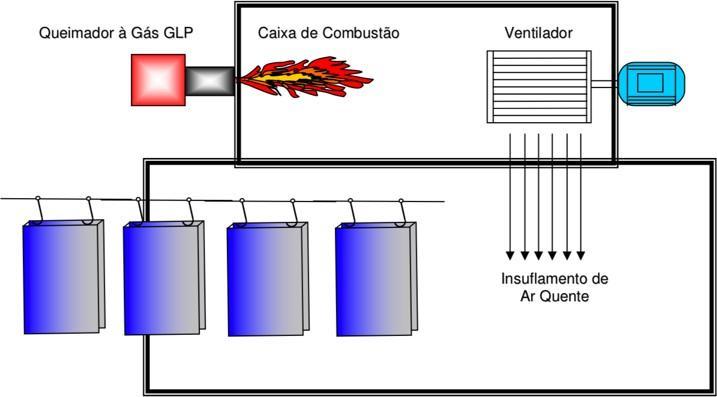
Figura 4: Proceso de convección de calor. Fuente: Manual Técnico de Pintura en Polvo EPRISTINTA (Brasil)
Ventajas y Desventajas de la pintura electrostática
Las características diferenciales con el resto de las pinturas son múltiples, donde encontramos bondades y falencias si se trata de comparar con otros recubrimientos convencionales. A continuación, algunas de ellas:
Ventajas:
El aprovechamiento del producto puede llegar a ser entre un 95 a 98% debido a la reutilización del polvo con un debido proceso. Se utiliza tal cual lo proveen y no es necesario ajustar viscosidades ni realizarmezclas. Es posible lograr la automatización de los procesos tanto de limpieza de lassuperficies como la de aplicación, siempre y cuando la
empresa cuente con la infraestructura y capacidad financiera. En algunos sustratos de figura geométrica redonda solo es necesario aplicar una sola
“mano”, ya que la pintura se adhiere en el contorno de la pieza. Su presentación es en forma de sólido finamente dividido, no contiene solventes, por consiguiente, no emite las grandes cantidades de compuestos orgánicos volátiles como lo generan las pinturas convencionales, minimizando el impacto con el medio ambiente. El almacenamiento de las pinturas no requiere lugares con altas exigencias técnicas y tan solo es necesario un lugar con las normales condiciones ambientales. La aplicación es muy sencilla y no requiere personal calificado paraejecutarla. Homogeneidad en la capa aplicada debido a la atracción electrostática. Altos espesores obtenidos en la pintura final con una sola aplicación. Amplísima variedad de colores, texturas y efectos, como los acabados texturizados, micro texturizado, martillados, entre otros. Facilidad para corregir errores durante la aplicación, ya que durante el proceso el polvo es fácil de retirar y permite reparar la aplicación defectuosa de una manera ágil y sencilla. Altas propiedades mecánicas y resistencia a la abrasión del recubrimiento.
Desventajas:
Para la debida ejecución del proceso se debe contar con el suficiente espacio en las instalaciones donde se contemplen: tanques de pretratamiento, zona de habilitación de piezas, cabina de aplicación, lugar para el equipo de aplicación, horno y zona de descuelgue y manipulación de las piezas.
Los costos de la maquinaria empleada suelen ser altos. Los cambios de color son tediosos pues requieren que se elimine por completo el rastro del color anterior en todo el sistema (cabina y equipo) además de hacer cambio de filtros, ya que estos solo deben utilizarse por color.
El espesor de película alto suele ser una cualidad, pero en algunas ocasiones, como por ejemplo donde las piezas requieran un ajuste especialmente bajo, el espesor de película tan alto es tomado como un defecto. En conclusión, la importancia que tiene el cuidado y conservación del medio ambiente, nos conduce a considerar la pintura electrostática como la alternativa más eco-amigable en el rubro de recubrimientos, ya que se encuentra exenta de uno de los productos más contaminantes como son los solventes. Es necesario difundir las propiedades y característicasdelapinturaelectrostáticaparallegar a estándares internacionales. La consolidación del uso de la pintura electrostática va de la mano del soporte técnico y de los controles de calidad indispensables para obtener los resultados esperados y exigidos por los clientes.
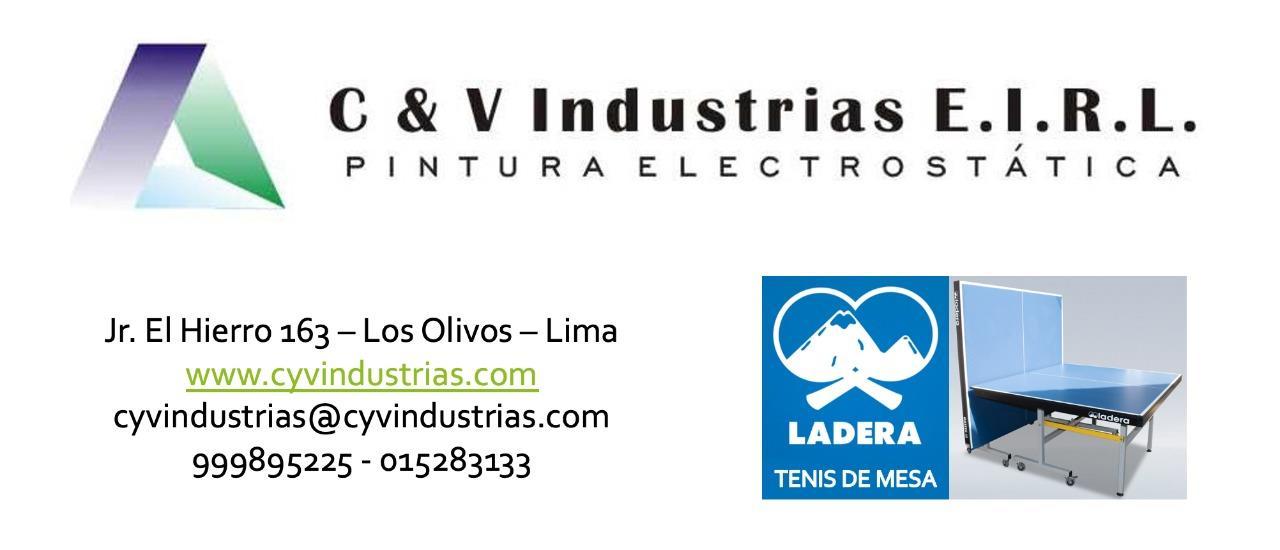
CÁLCULO DE LOS LÍQUIDOS DEL GAS NATURAL (RIQUEZA) DEL GAS NATURAL
Ing. Percy Zevallos Villegas
1. Procesamiento del Gas Natural
El gas natural es procesado en plantas de separación o recuperación de líquidos del gas natural (LGN). Este proceso tiene la finalidad de retirar los hidrocarburos condensables debido a que su precio de comercialización es mayor que el del gas natural.
2. Fraccionamiento de Líquidos del Gas Natural
El fraccionamiento de los líquidos del gas natural consiste en la obtención de los productos comerciales, empleando columnas de destilación o fraccionamiento. El número de columnas de fraccionamiento en un arreglo de columnas depende del número de productos que se desean obtener a partir de los LGN. La determinación de los líquidos del gas natural LGN son calculados por la riqueza del gas natural que a su vez determinara el proceso a usar, por ejemplo.
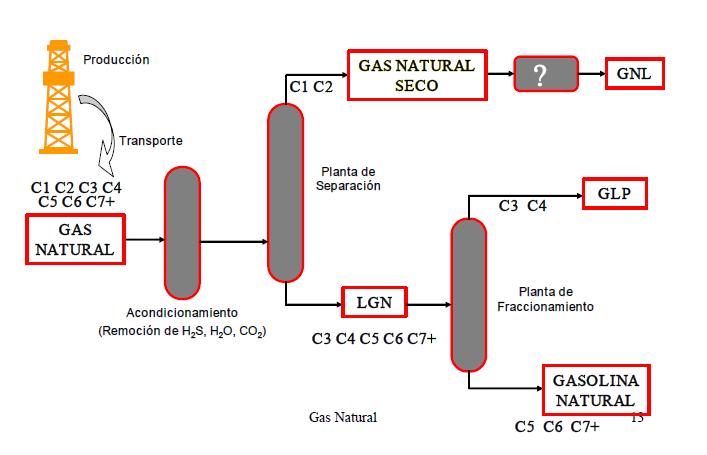
La riqueza de un gas se caracteriza típicamente por la cantidad de hidrocarburos recuperables (propano y más pesados) expresados en galones por mil pies cúbicos estándar (a 60 °F y 1 atm) de gas. A continuación, se muestra la riqueza promedio del gas de los diferentes lotes en los campos del norte y sur del Perú.
3. CÁLCULO DE LA RIQUEZA DEL
GAS NATURAL
La riqueza de un gas es una medida de la cantidad de “líquidos” (propano e hidrocarburos más pesados) contenidos en él. La riqueza del gas natural suele expresarse relacionando los galones de líquidos por cada mil pies cúbicos de gas (gal/Mpie3).
Riqueza del gas:
gal/Mpie3 ó m3/Mm3
Los datos necesarios para calcular la riqueza del gas son: La composición molar del gas (valor obtenido experimentalmente). Coeficientes de relación de volúmenes de gas a líquido para los componentes del gas (valores de tablas).
Ejemplo: Calcúlese la riqueza de un gas natural (en gal/Mpie3) recibido, que tiene la siguiente composición:
Compa ñía Lote
Riqueza (Gal/Mpc s)
SAVIA Z-2B 2.303
CNPC X 1.679
SAPET VI 1.310 NORTE DEL PERU
GMP I 2.585 PLUSPE TROL 88 3.124 CAMISEA
Composición del gas natural
Component e Composición molar
(% molar)
Relación de volumen gas a líquidos
(Gas Ideal @ 101.3250 kPa y 15,5 °C)
Nitrógeno 0.2195 682.48
Dióxido de carbono 0.6793 441.59
Metano 86.073 0 442.15
Etano 5.8764 281.32
Propano 3.3416 272.01
i-Butano 0.9971 229.02
n-Butano 1.3542 237.60
i-Pentano 0.5698 204.61
n-Pentano 0.3324 206.79
NeoPentano 0.0000 195.55
Hexano 0.5567 182.15
El Engineering Data Book (Twelfth edition -
FPS) publicado por GPSA, en la figura 23-2 presenta constantes físicas de hidrocarburos y la relación de volumen de gas a líquidos para los componentes del gas natural.
La relación de volumen de gas a líquidos está expresada en: m3 gas o bien en: pie3 gas m3 líquidos pie3 líquidos Por lo tanto, cada valor deberá dividirse entre 7.4805 para expresar la relación en pie3/gal (1 pie3 = 7.4805 gal).
Líquidos en el gas natural
Component e % molar Gas a líquidos (pie3/gal) Líquidos en el gas natural (gal/Mpie
3)
Nitrógeno 0.2195 91.2343 --
Dióxido de carbono 0.6793 59.0319 --
Metano 86.073 0 59.1069 --
Etano 5.8764 37.6070 --
Propano 3.3416 36.3624 0.91897
i-Butano 0.9971 30.6155 0.32568
n-Butano 1.3542 31.7625 0.42635
i-Pentano 0.5698 27.3524 0.20832
n-Pentano 0.3324 27.6428 0.12024
NeoPentano 0.0000 26.1412 0.0000
Hexano+ 0.5567 24.3499 0.22862
Los líquidos en el gas natural están compuestos por el propano e hidrocarburos más pesados.
La cantidad de cada “líquido” presente en gas natural se calcula de la siguiente manera:
Gal líquido
M pie3 gas
líquido i (% molar)
100
Gas a líquido (pie3)
(gal) x 1000 pie3
M pie3
La riqueza del gas es la sumatoria de la cantidad de “líquidos” presentes en el gas. Riqueza del gas = 2.228 gal/Mpie3
SEPARACIÓN POR MEMBRANAS
Dra. Tatiana V. R. Alicieo
Los procesos de separación por membranas han sido desenvueltos desde el siglo XVIII pero los avanzos más significativos comenzaron en la década de 60 con la desalinización del agua del mar. Membrana es una barrera selectiva que separa dos fases y restringe total o parcialmente el transporte de una o varias especies químicas presentes en esas fases, MULDER, (1991), (Figura 1).

El desempeño de una membrana se evalúa por el flujo de permeación, por la selectividad y por su resistencia química. El flujo de permeación es el flujo volumétrico (másico o molar) de fluidos que pasan por la membrana por unidad de área y por unidad de tiempo, la selectividad es la capacidad de la membrana de separar los componentes, resistencia química, el material que constituye la membrana debe resistir a las condiciones operacionales y a la composición del material que se desea separar, HABERT et al., (1997).
En procesos que utilizan membranas porosas, la capacidad selectiva está asociada a la relación entre el tamaño de las especies y el tamaño de los poros de la membrana. En procesos que utilizan membranas densas, la capacidad selectiva depende de la afinidad de las diferentes especies con el material que compone la membrana y de la difusión de estas por el material polimérico, HABERT et al., (2006).
Fase II
Potencial baixo
Fonte: HABERT et al., (1997).
La figura 1 muestra una representación de la membrana.
Para que ocurra el transporte de una especie por la membrana es necesaria una fuerza motriz. Esta fuerza motriz puede ser un gradiente de presión, de concentración o de potencial eléctrico. Entre los procesos que utilizan el gradiente de presión están: micro filtración, ultrafiltración y osmosis inversa o reversa, la diferencia entre estos procesos es el diámetro medio de corte de las membranas y la presión utilizada. A seguir vemos las características de cada proceso y sus aplicaciones.
Proceso Fuer za motr iz (∆P)
Micro filtración (MF) (0,5 a 2 atm)
Material retenido
Material en suspensión, bacterias PM> 500.000
Materi al que perme a Aplicaciones
Agua y sólidos disuelt os Esterilización bacteriana, clarificación de vinos y cervezas
Ultrafiltrac ión (UF) (1 a 7 atm)
Coloides, macromoléc ulas PM> 5000 Agua (solven te) sales soluble s de bajo peso molecu lar Fraccionamie nto y concentración de proteínas, recuperación de pigmentos.
Osmosis Inversa (OI) (15 a 80 atm)
Todo material soluble o en suspensión Agua (solven te) Desalinizació n de aguas, concentración de jugos de frutas, desmineraliza ción de aguas.
Adaptado de HABERT et al. (2006).
Una de las principales características de los procesos con membranas es la posibilidad de operar con flujo perpendicular o con flujo tangencial. Cuando ocurre la operación con flujo tangencial, la solución escurre paralelamente a la
membrana, minimizando el acumulo de material retenido en la superficie de la misma (Figura 2).
Figura 3-Modelo esquemático de la operación con membranas, (a) Filtración convencional, (b) Filtración tangencial. Adaptado de MULDER, (1991).
La membrana y el material de suporte son denominados “módulo”. Los criterios para la elaboración de módulos incluyen: una grande área de superficie en un volumen compacto, configuración de la membrana para permitir demandas energéticas adecuadas, ausencia de espacios muertos y capacidad de limpieza local (CIP) y fácil accesibilidad para substitución de la membrana, Figura 3, FELLOWS, (2019).
La separación por membranas puede ser utilizada en diferentes áreas de la industria,
Industria química: quiebra del azeótropo benzeno/hexano, recuperación de H2 de la síntesis de amonio, fraccionamiento de CO2/CH4.
Industria alimenticia: clarificación de bebidas, recuperación de levaduras, concentración de leche, concentración de jugos de frutas.
Biotecnología y farmacia: Separación de substancia termolábil, deshidratación de etanol, purificación de enzimas, fraccionamiento de proteínas, esterilización de medios de fermentación.
Tratamiento de aguas: desalinización de aguas, eliminación de trazos orgánicos, tratamiento de efluentes, desmineralización de agua para calderas, agua ultra pura para utilización en electrónica.
Medicina: riñón artificial (hemodiálisis), pulmón artificial (oxigenadores), esterilización de soluciones inyectables. Las ventajas de utilizar este proceso son: simplicidad de operación (scale up), bajo consumo de energía, separación de termolábiles. Entre sus limitaciones está el mayor costo de equipos, comparados con equipos tradicionales de separación, FELLOWS, (2019).
ALIMENTACIÓN
ALIMENTACIÓN
FILTRACIÓN PERPENDICULAR (a) FILTRACIÓN TANGENCIAL (b)
Referencias
ALICIEO, T.V.R. Aplicação de processos com membranas na clarificação de cerveja. Tese de doutorado PEQ/UEM, Maringá, 2006.
FELLOWS, P. J. Tecnologia do processamento de alimentos. Porto Alegre. Editora Artmed, 2019.
HABERT, A. C.; BORGES, C.P.; NÓBREGA, R.; "Escola Piloto em Engenharia Química - Processos de Separação com Membranas", COPPE/UFRJ, 1997.
HABERT, A. C.; BORGES, C.P.; NÓBREGA, R.; Processos de Separação com Membranas, COPPE/UFRJ, 2006.
MULDER, M. Basics principles of membrane technology. Dordrecht: Kluwer Academic Publisher, 1991.
SEPARACION POR “SORTING”
Ing. Arthur Pinto Chaves
El “sorting” o separación visual es, quizás, el método más antiguo y sencillo de separación. Consiste em separar visualmente partículas de una mena por su color, brillo ó tamaño. Em minería es clásica la separación de oro y piedras preciosas. También en Ingeniería Sanitaria, se hacen, manualmente o mecánicamente, la separación de la basura doméstica y urbana y en demolición, la separación manual de escombros En los últimos años sufrió una evolución muy importante, que pretendemos mostrar en esta charla.
La figura 1 muestra el equipo industrial.

Figura 1- el equipo industrial: 1 –alimentación, 2 – monocamada, 4, 5, 9 –identificación de la especie mineral ó otra y 3 –separación por soplo
Hay dos sistemas de identificación de colores y sus matices, el RGB Colour System y el YUV Colour Model, los mismos utilizados em nuestras computadoras y teléfonos móviles.
Además del color, en el sorting óptico es posible utilizar la transparencia de la partícula y tanto su proyección en dos dimensiones como su perfil ó volumen em tres dimensiones. véase la figura 2.
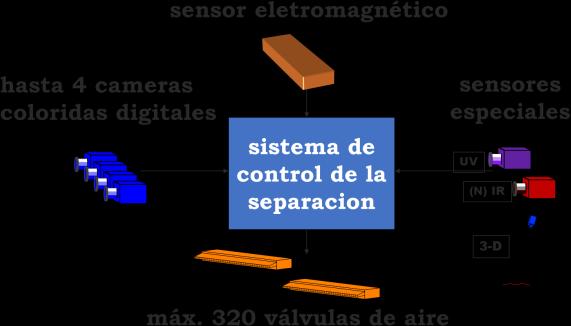
Figura 2. detección visual y por otras propiedades ópticas Todo esto es hecho partícula por partícula, individualmente. Esto es posible porque todo el procesamiento es hecho automáticamente por una computadora de proceso.
La grandeevoluciónmoderna esque hoy, además del color es posible utilizar otras propriedades tales como susceptibilidad magnética, peso específico, capacidad térmica, absorción de rayos X ó rayos g, y mismo hacer el análisis químico por fluorescéncia de rayos X partícula por partícula. Esto amplia mucho es escopo de este método de separación y multiplica su eficiencia y la precisión deseparación.
El proceso entonces consiste em el siguiente: los sensores electrónicos detectan para cada partícula el valor de la característica em análisis. Detectan su posición y la clasifican de acuerdo a una escala preestablecida.
El procesador comanda un chorro de aire em el instante mismo cuando la partícula cae de la cinta transportadora y la envía para uno ó otro producto.
Para el sorting óptico es necesário que la superficiedelaspartículas estémuy limpia, como muestra la figura 3. Para las otras propiedades, no.
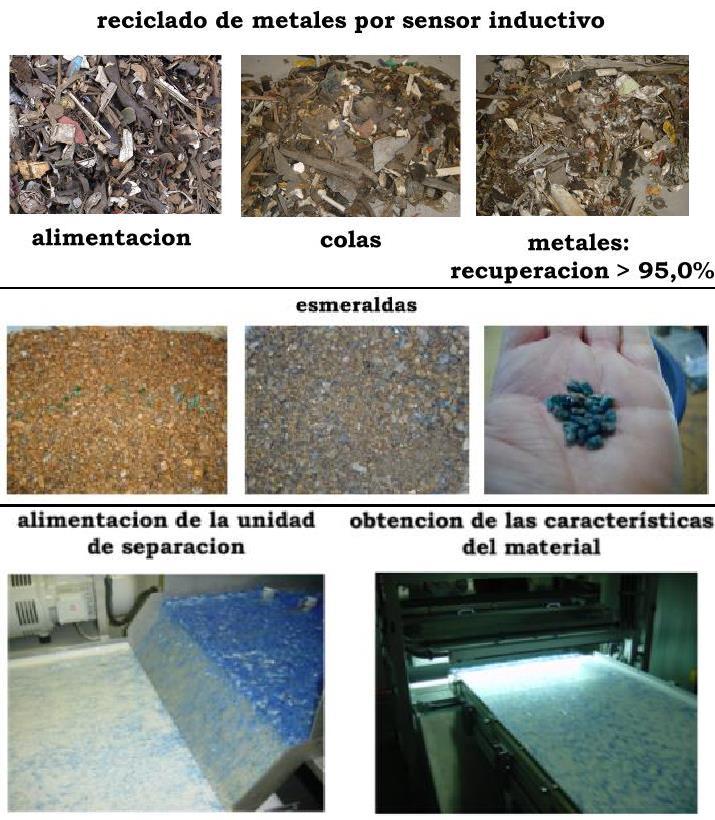
Figura 3. Separación de vidrio Todo esto se aplica para tamaños de partícula de 1 a 150 mm y muy variadas capacidades em los equipos industriales. Son generados dosproductoso, sinecesario otros, hay que repasarlos em otro equipo.
Em secuencia se muestran dosresultados prácticos industriales.
Los equipos tienen bajo consumo de energía y no causan daños ambientales.
Conferencias Virtuales, desarrolladas por el aniversario 59 de la escuela profesional de Ingeniería Química, Días 25 y 26 de Noviembre de 2020


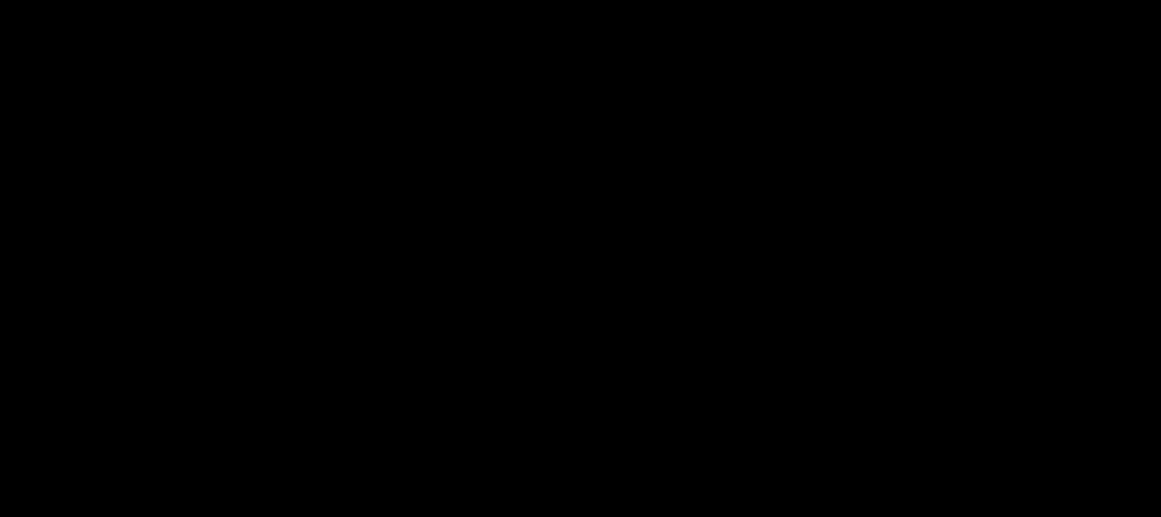

BIORREMEDIACIÓN DE SUELO CONTAMINADO CON HIDROCARBURO USANDO LODOS ESTABILIZADOS Y FERTILIZACIÓN
RESUMEN
Mg. Laura Gutierrez Escarcena
La contaminación del suelo con hidrocarburos es un problema debido a que éste pierde su capacidad agrícola, además genera enfermedades para los seres que están en contacto con ellos, es por eso que el presente estudio tiene como propósito evaluar la influencia lodos residuales estabilizados y la fertilización en la biorremediación del suelo contaminado con hidrocarburos. Para ello se realizó siete tratamientos, se prepararon tres recipientes de plásticos de 20.0 litros de capacidad, dentro de los cuales se mezcló el suelo contaminado con hidrocarburos (familia de varios compuestos químicos originados de petróleo crudo de la cadena C9 -C40), el lodo residual estabilizado en las proporciones de 0, 30 y 50% p/p y el fertilizante se adicionó en función a la necesidad del fósforo. A los tres recipientes restantes se les agregaron las mismas proporciones de suelo y lodo residual estabilizado que a los anteriores con la diferencia que á estos no se les agregaron fertilizante. El último tratamiento fue una mezcla de tierra contaminada con hidrocarburo (familia de varios compuestos químicos originados de petróleo crudo de la cadena C9 -C40), las bacterias aeróbicas benéficas natural enviro 8000 y fertilizante ácido. Periódicamente se aplicó el riego y una labranza manual manteniendo así condiciones óptimas de humedad y aireación. Durante el estudio de 04 meses, se tomaron muestras mensuales de cada tratamiento a las cuales se les realizó determinación microbiológica (heterótrofos (UFC/g)) y físico-químicas (hidrocarburos totales de petróleo (ug/g), nitrógeno total (ppm), fósforo total (ppm), materia orgánica (%), pH y humedad (%)). Se obtuvieron como resultados los porcentajes de remoción en los siete tratamientos TLB-1, TL-1, TLF-1, TL-2, TLF-2, TL-3, TLF-3 de 34.95%,13.84%,41.26%, 60.05%, 53.11%, 46.57% respectivamente. Por tanto se demostró que en todos los tratamientos hubo remoción de hidrocarburos, siendo el más eficiente el tratamiento con 30% de lodo y fertilizante (TLF-2) donde la remoción fue de un 60%, los lodos residuales se utilizaron como esponjante y junto con el fertilizante hicieron más eficiente el proceso de biorremediación en suelo contaminado con hidrocarburo.
I. Introducción:
Las actividades industriales donde se utilizan hidrocarburos han producido y producen alteraciones en el suelo por la ocurrencia de derrames de petróleo y derivados, tanto en forma accidental como por malas prácticas operativas desarrolladas. Como consecuencia de ello, se afectan las propiedades físicas y fisicoquímicas del suelo produciéndose la degradación del mismo. Por ejemplo en las actividades mineras se necesita los hidrocarburos para diferentes actividades como por ejemplo el funcionamiento de grupos electrógenos, vehículos de transporte y maquinaria pesada que si no se manejan acciones como el mantenimiento preventivo de vehículos o bandejas de contención para el suministro de los hidrocarburos se puede ocasionar derrames directamente al suelo. Los derrames de hidrocarburos contaminan los suelos los cuales generan enfermedades y además son considerados residuos peligrosos y deben disponerse de acuerdo al Reglamento de Residuos Sólidos. Sin embargo estos suelos pueden remediarse por medio del uso de microorganismos que consumen el carbono proveniente de los hidrocarburos dejándolo mejorado. Además las empresas mineras por lo general tienen plantas de tratamiento de aguas residuales domésticas y como efluente tenemos los lodos residuales los cuales serán dispuestos por la empresa cumpliendo las normativas ambientales. Este trabajo tiene la finalidad de evaluar la influencia de lodos residuales y la fertilización en la biorremediación del suelo contaminado con hidrocarburos a pequeña escala con el fin de disminuir los contaminantes presentes (TPH: hidrocarburos totales de petróleo) y lograr la recuperación del suelo aprovechando efluentes de plantas de tratamiento.
II. Materiales y métodos 2.1. Materiales:
Suelo contaminado con hidrocarburos (familia de varios compuestos químicos originados de petróleo crudo de la cadena C9 -C40) provenientes de un Almacén de Residuos Peligrosos. Lodos residuales provenientes de una Planta de Tratamiento de Aguas Residuales, como facilitador
del transporte de nutrientes, y super fosfato triple de calcio como fertilizante.
Recipientes (baldes) de plástico de 20L de capacidad para colocar las muestras. Balanza electrónica marca Sartorius, modelo CP8201 y una estufa marca Despatch, modelo LBB2-18-1 para la determinación de la humedad. La medición del pH de las muestras se efectuó por medio de un pHmetro marca OAKTON, modelo PC 300.
2.2 Procedimiento Experimental:
Se seleccionó la tierra contaminada con hidrocarburo que se encontró en el Almacén de Residuos Peligrosos para que no contenga piedras grandes y luego se homogenizó.
Previo al montaje del experimento, los lodos residuales y suelo con hidrocarburo se caracterizaron físico-químicamente para ello se realizó los ensayos de Nitrógeno y Fósforo total por los métodos NOM-021-RECNAT-2000AS-08 y NOM-021-RECNAT-2000 AS-11 respectivamente, los datos se presentan en la Tabla A.2.
Se pesaron lodos residuales provenientes de una Planta de Tratamiento de Aguas Residuales (PLT1), tierra contaminada con hidrocarburos y super fosfato triple de calcio como fertilizante.
Se realizaron siete tratamientos, se prepararon tres recipientes de plásticos de 20.0 litros de capacidad, dentro de los cuales se mezcló el suelo contaminado, el lodo residual en las proporciones de 0, 30 y 50% p/p y el fertilizante super fosfato triple de calcio se adicionó en función a la necesidad del fósforo. A los tres recipientes restantes se les agregó las mismas proporciones de suelo y lodo residual que a los anteriores con la diferencia que a estos no se les agregó fertilizante. El otro tratamiento fue una mezcla de tierra contaminada con hidrocarburo y las bacterias aeróbicas benéficas natural enviro 8000 y fertilizante ácido.
Periódicamente se aplicó el riego y una labranza manual manteniendo así condiciones óptimas de humedad y aireación. Durante el estudio de 04 meses, se tomaron muestras mensuales de cada tratamiento a las cuales se les realizó determinación microbiológica como heterótrofos (UFC/g) por el método EPA METHOD - 9131 y físico-químicas TPH: hidrocarburos totales de petróleo (ug/g) por el método EPA 8015D Nonhalogenated Organics Using GC/FID, Revisión 4, June 2003 , nitrógeno total (ppm) por el método NOM-021-RECNAT2000 AS-08 , fósforo total (ppm) por el método NOM-021-RECNAT-2000 AS-11 , materia orgánica (%) por el método Norma Oficial mexicana NOM-021 RECNAT-2000: Cap.7.1.7. Materia Orgánica AS 07, pH por el método NOM-021RECNAT-2000 AS-11 y humedad (%) por NOM021-RECNAT-2000 AS-11.
La temperatura ambiente de trabajo se realizó aproximadamente a 14ºC y el pH no se reguló con ningún aditivo químico.
III. Resultados:
TABLA A.1 Cantidad de fertilizante super fosfato triple de calcio (g) para las muestras TL-1, TLF-1, TL-23, TLF-2, TL-3, TLF-3
Concentr a. de Lodo (%) Muestr. kgTierr a
kg Lodo fósfor o que falta(g )
super fosfato triple de calcio (g)
0 TL-1 15,00 0,00 0,00 0,00 TLF-1 15,00 0,00 2,95 14,67 30 TL-2 10,50 4,50 0,00 0,00 TLF-2 10,50 4,50 24,33 121,13 50 TL-3 7,50 7,50 0,00 0,00 TLF-3 7,50 7,50 38,58 192,10
s
Fig.A.1 Hidrocarburos Totales de Petróleo (ug/g) en función del tiempo para las 07 diferentes muestras: TLB-1, TL-1, TLF-1, TL-2, TLF-2, TL3, TLF-3 Fig.A.2 Remoción de Hidrocarburos Totales de Petróleo para todas las muestras TLB-1, TL-1, TLF-1, TL-2, TFL-2, TL-3, TLF-3
TABLA A.2 Concentración de Hidrocarburos Totales de Petróleo(C-9-C-40)(ug/g) de las muestras a través del tiempo
Parámetro Hidrocarburos Totales de Petróleo(C-9-C-40)(ug/g)
Código TLB-1 TL-1 TLF-1 TL-2 TLF-2 TL-3 TLF-3
03/09/Sem1 2077.0 2285.0 2738.0 2780.0 2597.0 2151.0 2537.0
07/10/Sem2 1631.0 2205.0 2519.0 2224.0 1817.9 2080.0 2100.0
11/11/Sem3 1600.0 2015.0 2015.2 1650.0 1500.0 1456.0 1470.0
15/12/Sem4 1570.0 1900.0 1780.0 1300.0 1038.0 1150.0 1190.0
TABLA A.3 Heterótrofos (UFC/g) de las muestras a través del tiempo
Parámetr o Heterótrofos (UFC/g)
Código TLB-1 TL-1 TLF-1 TL-2 TLF-2 TL-3 TLF-3
03/09/Se m1 3,6E+14 2E+13 7,5E+14 3,1E+13 5,7E+14 5,9E+14 9,4E+14
07/10/Se m2 2,2E+18 1,5E+19 6E+16 6E+17 3E+17 2E+17 2,3E+18
11/11/Se m3
15/12/Se m4 5,80E+09 4,30E+09 1,40E+09 2,10E+09 2,60E+08 8,00E+07 8,00E+07
8,10E+10 9,00E+10 1,45E+11 7,10E+10 9,60E+10 4,00E+10 4,50E+10
TABLA A.4 %Remoción de Hidrocarburos Totales de Petróleo
TLB-1 TL-1 TLF-1 TL-2 TLF-2 TL-3 TLF-3
%Remoción de Hidrocarburo s
25.08 13.84 34.95 41.26 60.05 46.57 53.11
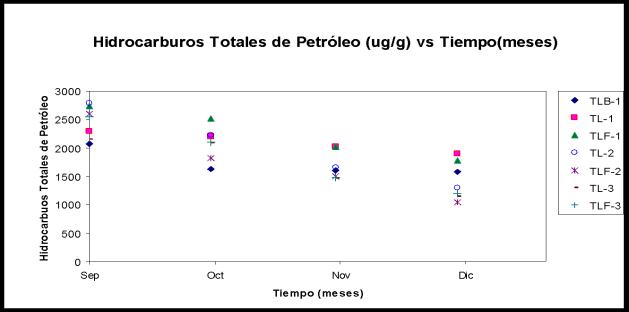

IV. Discusiones:
Según Ismenia Araujo, los resultados obtenidos por ella alcanzaron una remoción del 62.68% de los TPH para 70% de lodo y 7.5% fertilizante fosfato diamónico en 4 meses, nosotros alcanzamos una remoción del 60% con sólo 30% de lodo residual y fertilizante super fosfato triple de calcio aplicado de acuerdo a la relación N:P 10:5 en 4 meses.
La humedad no se mantuvo constante para ambas muestras al momento del muestreo, sobre todo en las muestras sin lodo donde la humedad es rápidamente evaporada, lo que significa que el lodo ayuda a retener el agua, similar lo sugerido por Araujo (2005).
Ramirez (2005), en México evaluaron la eficiencia de remoción de hidrocarburos a nivel laboratorio de un suelo contaminado, mediante la aplicación de lodos provenientes de una planta de tratamiento de aguas residuales de una refinería. Los resultados indican que existe una remoción de los hidrocarburos en la fracción diesel a las 4 semanas de la aplicación de lodos y tensoactivo, obteniendo una eficiencia de remoción del 67 al 73%, en comparación con estos resultados en el presente estudio la remoción fue menor con sólo 60%,
Chávez (2006), en Trujillo demostró que un consorcio microbiano nativo de las lagunas de Quiruvilca presentó una eficiencia del 98% en la biodegradación del petróleo diesel en diez días en un biorreactor de tipo tanque agitado y aireado a temperatura ambiente de laboratorio, lo cual difiere con nuestro trabajo ya que nuestro proceso no se realizó dentro de un biorreactor y no tuvo agitación.
V. Conclusiones:
Se demostró que en todos los tratamientos hubo remoción de hidrocarburos, siendo el más eficiente el tratamiento con 30% de lodo y fertilizante (TLF2) donde la remoción fue de un 60%. Los lodos residuales estabilizados se utilizaron como esponjante e hicieron más eficiente el proceso de biorremediación de hidrocarburos en suelo contaminado con hidrocarburo.
Las condiciones de temperatura baja no influyeron en un porcentaje de remoción baja de hidrocarburos.
VI. Referencias bibliográficas:
1. ARAUJO, I., et al. Biorremediación de suelos con consorcio bacteriano, compostaje y fertilización. Centro de Investigación del Agua,
Facultad de Ingeniería, Universidad del Zulia,
Ciudad Universitaria. Maracaibo 4005,
Venezuela.
2. ARAUJO I., et al. Influencia de la Fertilización en la Biorremediación de suelos Contaminados con Hidrocarburos utilizando Lodos Residuales
Estabilizados. Centro de Investigación del
Agua (CIA), Universidad del Zulia (LUZ).
3. BENAVIDES LÓPEZ DE MESA, J. y
QUINTERO, G. Bioremediación de suelos contaminados con hidrocarburos derivados del petróleo. NOVA -Publicación Científica ISSN: 1794-2470 VOL.4 No. 5 enero - junio de 2006:1-116.
4. CELESTE FERNÁNDEZ, M., et al.
Biodegradación de asfalteno y resinas por microorganismos presentes en suelo contaminado con hidrocarburo. Universidad de
Carabobo, Centro de Investigaciones
Ambientales, Revista de la Facultad de
Ingeniería U.C.V., Venezuela 2008.Vol. 23, N° 4, pp. 7–15, 20.
5. CHAVEZ ARAUJO, E. R. Biodegradación de petróleo Diesel 2 por un consorcio microbiano nativo de las lagunas del distrito de Quiruvilca en un biorreactor aireado y agitado.
Universidad nacional de Trujillo, 2006.
6. FERRERA CERRATO, R. et al. Procesos de biorremediación de suelo y agua contaminados por hidrocarburos del petróleo y otros compuestos orgánicos. Revista latinoamericana de microbiología. Vol. 48, No. 2. Abril - Junio. 2006 pp. 179 – 187
7. RAMÍREZ GONZÁLEZ, A. et al.
Rehabilitación de suelo contaminado con hidrocarburos mediante la aplicación de lodos.
Instituto de Ingeniería, UNAM
FORMACIÓN DE GEOPOLIMERO PARA INMOVILIZAR MERCURIO PRESENTE EN RESIDUOS SÓLIDOS MINEROS DE LA REGIÓN SUR DEL PERÚ
Msc. Ing Gregorio U. Palma Figueroa
Las zonas mineras de Nazca, Chala y Secocha, ubicadas en la región Arequipa y parte de la región Ica; son ricas en polimetales, principalmente el oro, siendo la pequeña minería y minería artesanal las que utilizan el proceso de amalgamación en circuito abierto del material aurífero con mercurio, tal como se aprecia en la fig. 1, generando residuos sólidos mineros (relaves) con alto contenido de mercurio y otros metales tóxicos, generando una gran amenaza para la salud humana y el medio ambiente.
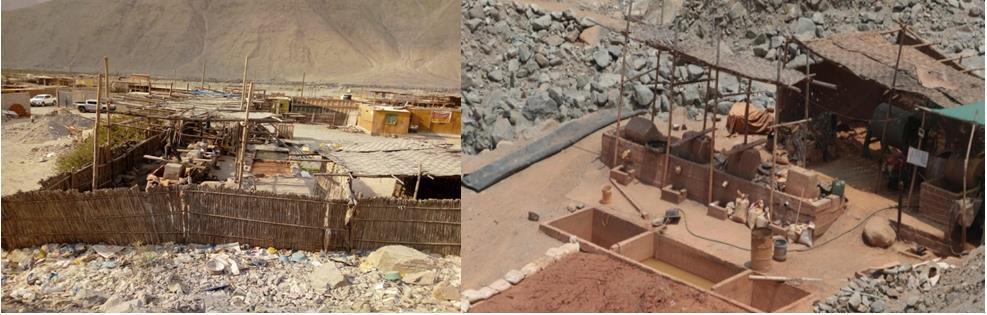
Figura 1: Minería artesanal en zona de Secocha y Alto molino, Prov. Camana-Arequipa Fuente: Elaboración propia, 2018
El objetivo del presente trabajo fue inmovilizar el mercurio presente en éstos residuos mineros mediante la tecnología de Estabilización/Solidificación vía sulfuro de mercurio y matriz polimerizante, formado este último con 55% de piedra pómez, 45 % de metacaolín y una solución altamente alcalina a base de hidróxido de sodio (10 M) y solución de silicato de sodio comercial. Se caracterizó los residuos mineros fisicoquímicamente: pH (UNE 77305), conductividad eléctrica (ISO- 112651994), tamaño de partícula (NTP N° 339.128), humedad (ASTM D- 2216), así como concentraciones de mercurio como metales totales en muestras (EPA 200.7 ICP-OES) y en los lixiviados mediante el test (EPA. TCLP-1311). El mercurio en las muestras alcanzó en promedio concentraciones > 275 mg/Kg, y en el lixiviado una de ellas alcanzó una concentración de 0,43 mg/L, valores muy por encima de los ECA para suelos; resultados que se aprecian en el cuadro 1; Clasificándose como muy peligrosos, requiriendo un proceso de estabilización, para ello se siguió el procedimiento según patente americana N°US-6, 911,570 b, 2005 modificado. Los factores y sus respectivos niveles evaluados fueron: ratio molar de S:Hg, pH y % de material geopolimerizante: residuo sólido minero-estabilizado así como sus puntos centrales. Las variables respuesta evaluadas fueron: concentración de Hg en los lixiviados con un valor promedio de 0,0367 mg/L, reduciendo el mercurio hasta un 92 %, resistencia ala compresión (norma NTP 334.051:2013) alcanzando un máximo de 34,70 MPa
uestra M
Cuadro 1. Concentración de Mercurio en las diferentes muestras y clasificación del residuo.
Procedencia de muestra Concentración de Hg total en muestra (mg/Kg) Concentración de Hg en lixiviado (mg/l) Normativa de clasificación*
Conc. de Hg total en residuo (mg/Kg)
CLASIFICACIÓN RESIDUO
Conc. de Hg en lixiviado (mg/L)
1A El Pajonal Nazca Ica 193,87 <0,001 50-200 <0,8 Residuo peligroso que requiere disposición en relleno especial
2A San Martin Camana Arequipa >275 0,042 >200 No requerido Residuo muy peligroso que requiere disposición en relleno especial, luego de una estabilización
1B El Pajonal Nazca Ica
2B Poscco Misky Camana Arequipa 100,93 0,026 50-200 <0,8
Residuo peligroso que requiere disposición en relleno especial >275 0,01 >200 No requerido Residuo muy peligroso que requiere disposición en relleno especial, luego de una estabilización
1C Secocha Camana Arequipa >275 <0,001 >200 No requerido Residuo muy peligroso que requiere disposición en relleno especial, luego de una estabilización
2C Secocha Camana Arequipa >275 0,43 >200 No requerido Residuo muy peligroso que requiere disposición en relleno especial, luego de una estabilización
A5 Chala Caraveli Arequipa >275 0,05 >200 No requerido Residuo muy peligroso que requiere disposición en relleno especial, luego de una estabilización
Fuente: elaboración propia * Resolución Gerencial Regional N° 006-2014-GRA/ARMA que aprueba el instrumento de Buenas Prácticas de Gestión Ambiental (BPGA) concordada con la estándar de DECCW (2009).
Figura 2. Resistencia a la compresión (Mpa) del monolito conteniendo residuo solido minero estabilizado y material geopolimerizante
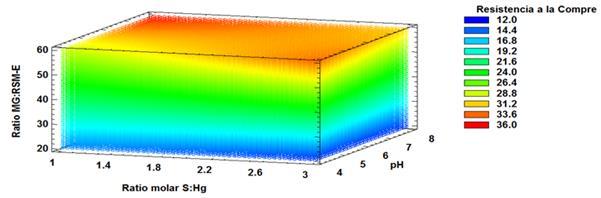
La absorción de humedad tuvo un promedio de 17,27 % y volumen de vacíos de acuerdo a la norma (ASTM C642-13), con promedio de 22,47% para ambos ensayos; por lo tanto se logró inmovilizar el mercurio y garantizar una estabilidad química y física de los residuos sólidos mineros en el ambiente de disposición final. Se utilizó un diseño factorial completo con tres pruebas centrales aplicando el software Statigraphics Centurión XVI. Palabras clave: Mercurio, Geopolímero, Piedra Pómez, Residuo Minero, Resistencia a la compresión. TCLP, absorción de humedad, volumen de vacíos.
Bibliografia
• Barbosa, V.F.F., MacKenzie, K.J.D. &
Thaumaturgo, C. 2000. Synthesis and characterisation of materials based on inorganic polymers of alumina and silica: Sodium polysialate polymers, International Journal of
Inorganic Materials, vol. 2, no. 4, pp. 309-317
• Davidovits J. 1994. Properties of geopolymers cements. In: Proceedings of the first international conference on alkaline cements and concretes. Kiev,
Ukraine: Scientific Research Institute on Binders and Materials; p. 131–49
• Dórea, José G. 2012 Los efectos del mercurio sobre la salud humana y el medio ambiente y una consideración especial a la vulnerabilidad en la fase temprana de la vida Arch Argent
Pediatr;110(5):372-374 / 372
• Duxson, P., Fernández -Jiménez, A., Provis, J.L.,
Lukey, G.C., Palomo, A., Van Deventer, J.S.J., 2007a. Geopolymer technology: the current state of the art, J. Mater. Sci. 42 2917–2933 • Hasanbeigi, A.; Menke, C. y Therdyothin, A. 2011
Technical and cost assessment of energy efficiency improvement and greenhouse gas emission reduction potentials in Thai cement industry, Energy
Efficiency, Vol. 4, Nº 1, pp. 93-113. DOI 10.1007/s12053-010-9079-1
• Marathe, S. 2016 A Review on strength and durability studies on Geopolymer Concrete,
ISSN:2319-8753,IJIRSET Vol.5,Special Issue 9,
May -11-23
• Montes N. Valencia, 2014. Cementos Alcalinos:
Materiales de Construcción Ecológicos Revista
CINTEX, Vol. 19, pp.109-125
• Palacios, S., Alfonso, P., Yañez, J., Higueras, P. 2013. Evaluación de la contaminación de mercurio en la cuenca del rio Ocoña, Perú ,libro de actas del
III Congreso Internacional de Geología y minería ambiental para el ordenamiento territorial y el desarrollo. Cardona. I.S.B.N.: 978 - 99920 - 1 - 769 - 2, pp. 241 – 248, Catalunya
• Rieser, Linda A., Bishop paul, Makram T. Suidan,
Haishan Piao, Renee A. Fauche, and Jian Zhang, 2001. Stabilization and testing of mercury containing wastes: Borden catalyst EPA/600/R02/019
• Yao, X., Zhang, Z., Zhu, H., and Chen, Y. 2009.
Geopolymerization Process of Alkali-Metakaolinite
Characterized by Isothermal Calrimetry.
Thermochimica Acta, 493, 49-54
HACIA UNA ECONOMÍA SOLAR
RAKESH AGRAWAL
Escuela de Ingeniería Química Davidson
Universidad Purdue, West Lafayette, IN 47907
Los recursos fósiles han jugado un papel sin precedentes en la historia de la humanidad.
La disponibilidad de fósiles
La energía en alta densidad volumétrica ha impulsado la civilización humana a un ritmo sin precedentes para más de dos siglos. Sin embargo, a pesar del reciente aumento en la disponibilidad de recursos fósiles, con la creciente tasa de demanda de energía, es seguro que eventualmente necesitaremos una fuente de energía sostenible. La energía solar es una de esas fuentes, es abundante y su uso puede satisfacer nuestras necesidades diarias de alimentos, productos químicos, calor, electricidad y transporte para cualquier futuro previsible.
El desafío de la transición de una economía basada en recursos fósiles a una economía solar es que tenemos que aprender a aprovechar, transformar y almacenar la energía solar en la escala de tiempo de nuestro patrón de uso. Esto ha sido un problema debido a la intensidad diluida de la irradiación solar y su intermitente disponibilidad. Por lo tanto, los métodos para recolectar y transformar la energía solar deben ser eficientes y de bajo costo para un uso generalizado. En esta presentación, discutiremos estos desafíos y nuestro enfoque interdisciplinario para encontrar posibles soluciones. Presentaremos soluciones sostenibles para transporte, producción de combustibles y productos químicos, almacenamiento a gran escala y durante todo el día generación de energía. Abogaremos por los fotones locales para satisfacer las necesidades locales a través de agricultura fotovoltaica agroléctrica para permitir un escenario de "tierra completa". Finalmente, discutiremos brevemente nuestra investigación sobre células solares inorgánicas procesadas en solución de bajo costo.
De hecho, estamos viviendo un momento emocionante en el que continuamos debatiendo y preparándonos para la eventual transición de una economía basada en los fósiles a una economía sostenible basada en la energía solar. l
El objetivo de esta presentación es compartir algo de esta emoción de mis propias experiencias.
GESTIÓN INTEGRAL DE RESIDUOS SÓLIDOS MINEROS
Ing. Judith González Salinas
Las actividades mineras generan una cantidad importante de residuos sólidos a lo largo de su cadena productivaEn términos de volumen y tipo de residuos generamos:
Residuos masivos [material estéril, desechos, desmonte, relaves, ripios, escorias muchos de ellos con una gran potencial para ser recuperados y vueltos a poner en valor. Residuos peligrosos y no peligrosos [aprovechables y no aprovechables] de ámbito no municipal Residuos sujetos a un régimen especial de bienes priorizados: [Residuos de Aparatos
Eléctricos y Electrónicos (RAEE)], Neumáticos
Fuera de Uso (NFU), aceite usado, residuos orgánicos que requieren de un tratamiento previo a su valorización comercial y/o disposición final. Dentro del marco de la regulación vigente en el
Perú para el manejo de residuos sólidos en minería, se señala claramente la finalidad del aprovechamiento de los residuos utilizando nuevas tecnologías para optimizar al maximo el uso de los mismos. Esto se dará en todas las etapas del ciclo de vida de un bien o servicio, dentro de una lógica circular reduciendo la huella ambiental y contribuyendo al bienestar de los individuos y la colectividad: Primera finalidad. Prevención o minimización de la generación de residuos en el origen, frente a cualquier otra alternativa. Segundo lugar. Los residuos generados pasan a ser materia prima para otros procesos industriales aplicando la simbiosis industrial a través de la recuperación, valorización material y energética de los residuos entre las cuales se cuenta la reutilización, reciclaje, compostaje, coprocesamiento, entre otras alternativas siempre que se garantice la protección de la salud y del medio ambiente.
Ultima alternativa: Disposición final de los residuos sólidos en la infraestructura autorizada por el Ministerio del Ambiente [MINAM] de acuerdo al tipo del residuo sólido generado, ya sea en un Relleno Sanitario y/o un Relleno de
Seguridad en condiciones ambientalmente adecuadas. De esta manera en Southerrn Peru priorizamos el uso eficiente de los recursos naturales, el reciclaje y la reutilización de los residuos generados en nuestras actividades, promoviendo prácticas ambientales alineadas a una economía circular.
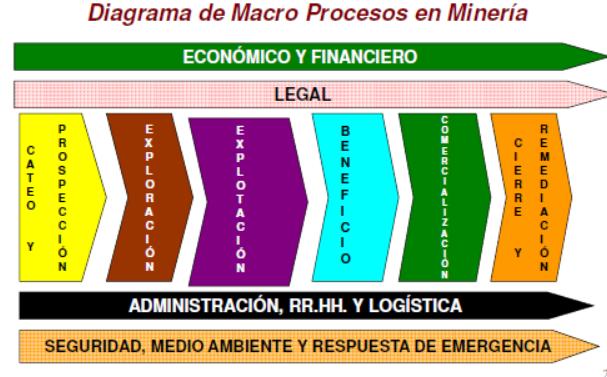
INGENIERIA QUIMICA, ENERGIAS RENOVABLES Y MEDIO AMBIENTE
Ing. Arturo Valero Roque
La reducción del petróleo como fuente de energía, el incremento de la Contaminación ambiental y el desarrollo de la tecnología por la creciente actividad del hombre por alcanzar la satisfacción de sus necesidades. Nos llevan a dar un giro hacia el aprovechamiento de los Recursos Naturales como fuentes de Energías limpias y renovables con una proyección al futuro y con menores costos de producción. Las Energías Renovables como la Eólica, Solar, Hidráulica y otras fuentes aprovechables como la Biomasa y la Geotermia; nos permiten muchas ventajas como la Seguridad Energética, la reducción de los gases de invernadero y la independencia de la importación de energía, permitiendo un mayor desarrollo económico con un aumento de fuentes de trabajo.El empleo de las Energías Renovables en forma de Energía Eléctrica, fuerza motriz y producción de calor permiten un mayor bienestar al ser humano reduciendo los costos de producción . En los últimos años, la producción diaria del Petróleo en el mundo fue de 91,6 millones de barriles y entre Estados Unidos, Rusia y Arabia Saudita la producción fue superior a 10 millones de barriles cada uno de los cuales Estados Unidos consumió 19,4 millones de barriles por día.
CONSUMO CONJUNTO DE ENERGIAS RENOVABLES EN EL MUNDO (SOLAR, EÓLICA, GEOTÉRMICA Y BIOMASA). Las conversiones se hicieron considerando la eficiencia de conversión eléctrica del 38%.
En este cuadro observamos que los Estados Unidos y China, son los mayores consumidores de Energías Renovables. El Perú, con un consumo de 7,7 mil barriles/día calendario, se ubicó en el puesto 42. ENERGIA SOLAR. Es una energía renovable obtenida directamente del sol, mediante dispositivos ópticos para transformarse en calor o electricidad. Estos dispositivos se denominan equipos fotovoltaicos, los cuales convierten la luz del sol en energía eléctrica, recibiendo la energía radiante en celdas compuestas de un material semiconductor que permiten el paso de electrones que se convierten en electricidad. Las celdas se arreglan en módulos los que son dispuestos en arreglos fotovoltaicos. El promedio anual de radiación solar en el Perú está en el rango de 4-5 KWh/m2 día. Respecto a esto la utilización de esta energía es apropiada para nuestra población por su bajo costo , a pesar de que el costo inicial es alto por el valor de los paneles solares.
ENERGIA EOLICA.
En el Perú, la Planta de energía eólica más grande se encuentra en Nazca donde los vientos alcanzan hasta 100 km/h y se denomina “Wayra” y es una excelente alternativa por ser una energía limpia e inagotable, que es entregada al Sistema Eléctrico Interconectado nacional.
ENERGIA HIDRAULICA.
Esta energía es aprovechada por Electro Perú y distribuida a través de Edelnor, Luz del Sur y
Distriluz, con clientes libres como Aceros Arequipa,
Cerro Verde y Compañía Minera Volcán. La Biomasa y las Aguas Residuales, son otros de los problemas que se están convirtiendo en insostenibles por el crecimiento de las poblaciones y la falta de una adecuada Gestión ambiental por parte de los Municipios.
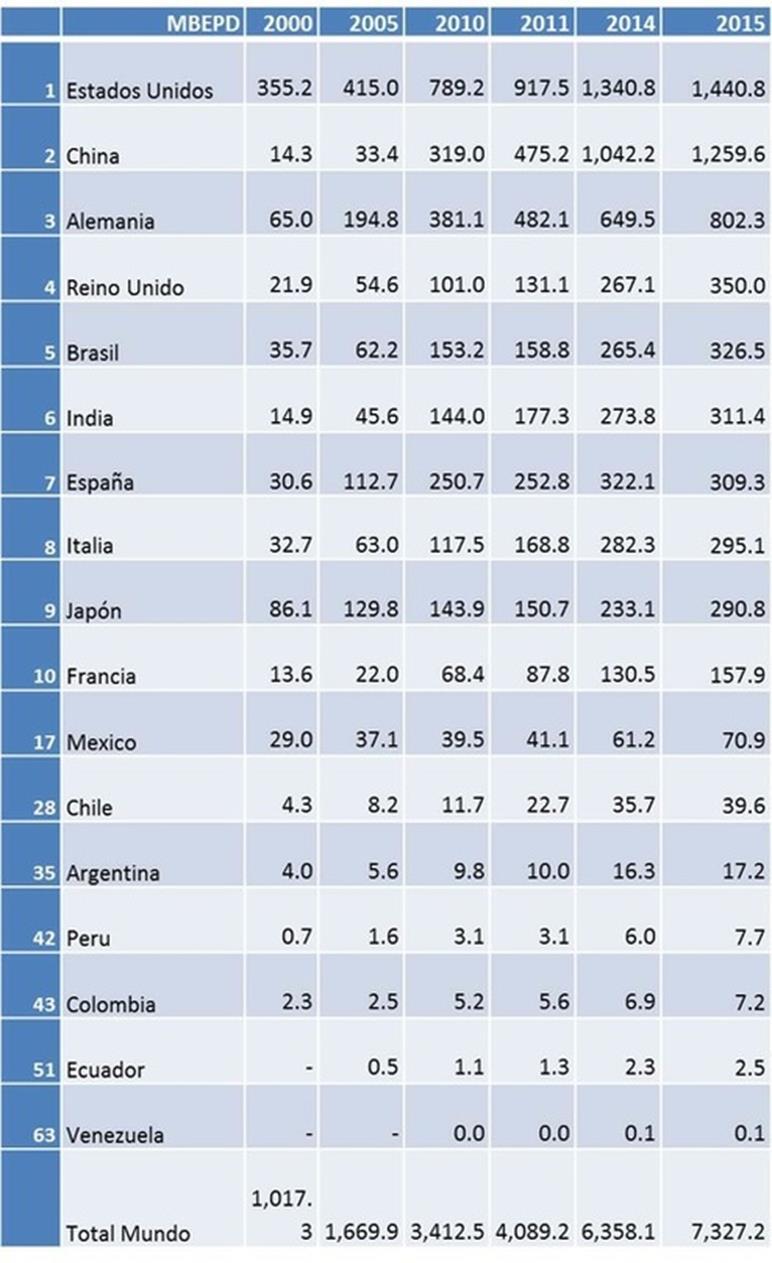
EVALUACIÓN Y SELECCIÓN DE SOLVENTE ISOPARAFÍNICO, PARA EXTRACCIÓN POR SOLVENTES (SX)
Ing. David Ramírez F.
ANTECEDENTES
Las operaciones de SX han venido usando el Kerosene como solvente para el extractante orgánico, (Lix 984 N, o Acorga), utilizado en la extracción de cobre. Este trabajo muestra de forma resumida la evaluación realizada a 3 solventes isoparafínicos, con la finalidad de establecer el de mejor comportamiento metalúrgico en una planta de Extracción por Solventes para cobre, con el fin de usarlo como alternativa de cambio frente al solvente en uso, Kerosene. Las pruebas realizadas son de Evaporación, a nivel de gabinete y de performance operativa, en una planta piloto configurada de igual modo que la planta industrial. Bajo costo y buena performance han sostenido la permanencia del kerosene hasta la actualidad, sin embargo, aspectos de seguridad, relacionados con su bajo punto de inflamación (probabilidad de incendio); su uso en actividades ilegales, siendo por lo tanto un insumo controlado, así como el incremento de los costos operativos debido a la suba de precio de los derivados del petróleo han mostrado que los solventes isoparafínicos son una alternativa de cambio por similar precio y menor consumo.
OBJETIVOS
- Determinar el solvente isoparafínico, metalúrgicamente más apropiado para ser la alternativa de cambio frente al Kerosene. - Estimar y escalar las pérdidas de solvente tanto por arrastre como por evaporación a partir de los inventarios de orgánico y de las pruebas realizadas con cada solvente evaluado.
PRUEBA DE EVAPORACIÓN: DETALLES EXPERIMENTALES
1) Las pruebas de evaporación se realizaron en 2 escenarios: - Junto a las celdas de extracción por solventes, Planta, y - En el laboratorio de pruebas especiales. 2) Además se usó: - Solventes isoparafínicos puros y - Solución Orgánica, esto es, solvente+extractante, (Lix 984N), al 14 %. 3) Se usaron los siguientes solventes: a) Kerosene (blanco) b) Shell AR 2046 c) Orfom SX-80. d) Conosol C-200 A cada uno y de manera aleatoria se le asignó un nombre tal como solvente A, B y C además del Kerosene, que será el blanco de comparación.
PROCEDIMIENTO
La prueba, tanto en Planta como en laboratorio consistió en colocar 770 ml de cada solvente en sendos recipientes de la misma dimensión. Solo cambió el escenario. La prueba se llevó a cabo durante 111 días. El procedimiento consistió en pesar cada día a la misma hora, la masa contenida en cada recipiente contenedor restando luego en cada caso del valor anterior de modo tal que se obtuviera el valor del solvente evaporado, asimismo las taras respectivas del recipiente fueron restadas. Estos datos se fueron acumulando en una tabla y posteriormente graficando de modo que se pudiese distinguir cual es la dirección o pendiente adoptada en cada caso.
Fig.1. Prueba Estática de Evaporación de Solventes RESULTADOS
Para la prueba de evaporación se muestran los resultados en las gráficas siguientes:

Gráfico 1.- Evaporación Solvente Puro en laboratorio
En el gráfico 1 se ve al kerosene como el que más se evapora mientras que todo lo contrario sucede con el Solvente C, puro. Para la prueba llevada en Planta, la tendencia es similar. Se puede ver en el gráfico 2.
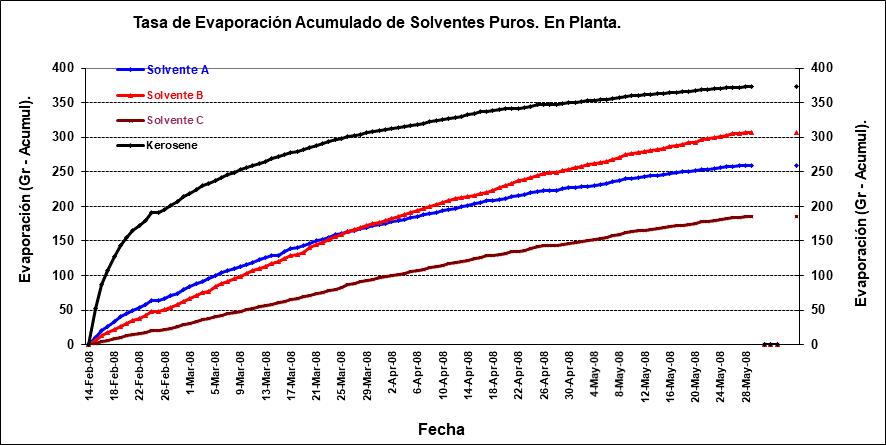
Gráfico 2. Evaporación Solvente Puro en Planta Industrial SX
Para la prueba que se realiza con solución orgánica: solvente + lix 984N, el objetivo es ver si el extractante influye en los resultados, los que se ven en los gráficos 3 y 4:
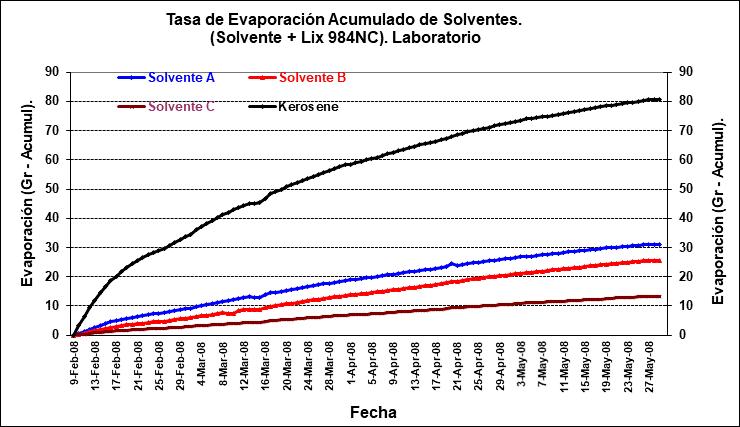
Gráfico 3. Evaporación de solvente +Lix 984N. Laboratorio Gráfico 4. Evaporación de solvente+Lix 984N en Planta Industrial
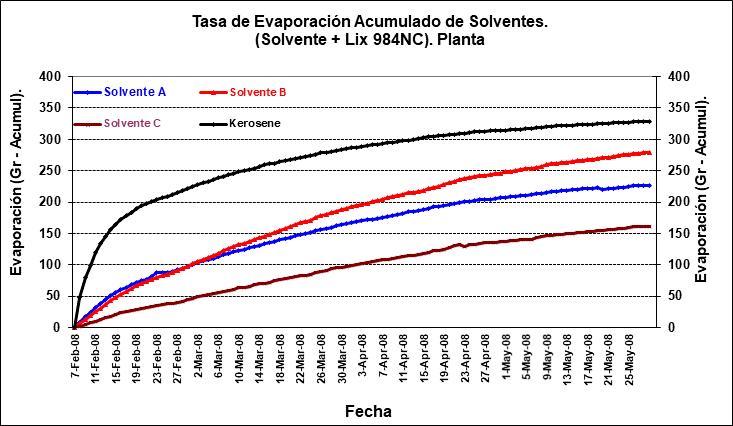
Observaciones Importantes: En todos los casos las pérdidas por evaporación del kerosene son mayores. En las pruebas en planta industrial; a los 45 días para solventes puros y 20 días para la mezcla solvente + Lix984N, vemos que la masa evaporada de solvente A y solvente B llegan a igualarse, y luego muestran un incremento de evaporación del solvente B. Para cada prueba se halló la Tasa de
Evaporación resultante y se tomó la referida a (solvente+Lix 984N) y realizada en planta industrial de SX, por ser la más cercana a la realidad. Se resume en el cuadro1:
Cuadro 1. Tasa Evaporación Solventes
Tasa de Evaporación Solventes
Solventes lt/día-m2 Solvente A 0.056 Solvente B 0.071 Solvente C 0.040 Solv Blanco 0.084
4.- EVALUACIÓN DE LOS SOLVENTES EN PLANTA PILOTO
4.1.- Performance en Planta Piloto
Para evaluar la performance de los solventes en la operación, se configuró la planta piloto tal como el principal tren de la Planta industrial, esto es 2Extracción + 2Reextracción, (2+2). La evaluación principal estuvo alrededor de determinar los arrastres o atrapamientos, los que tienen que ver con los tiempos de separación de fases y con la formación de borras o lodo. Solo se consideró los Solventes A y B, debido a que el Solvente C no proporcionó muestra.
4.1.1.- Eficiencia de Extracción
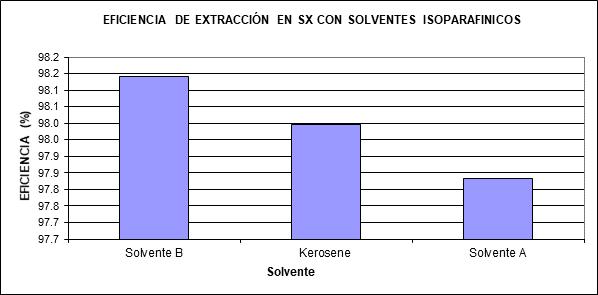
Gráfico 5. Eficiencia de Extracción en Prueba con Solventes Isoparafínicos
Las eficiencias de extracción son muy parecidas, la diferencia entre los solventes A y B es solo de 0.3 puntos porcentuales.
4.1.2.- Atrapamientos o arrastres

Gráfico 6. Atrapamientos en Planta Piloto Prueba con Solventes Isoparafínicos
Donde: Raff : Refino OC : Orgánico Cargado OD : Orgánico Descargado LS : Electrolito Rico
Nuevamente se nota la similitud entre los solventes A y B, en casi todas las etapas de la planta excepto en lo que es atrapamiento en Orgánico Descargado donde el Solvente B, muestra una ligera ventaja.
4.1.3.- Generación de Lodo o Borra
En este importante punto fue el Solvente A, el que mostró menor tasa de formación de lodo en cada celda del circuito donde se evaluó. Esto significa menores pérdidas de orgánico por kilogramo de cobre producido.
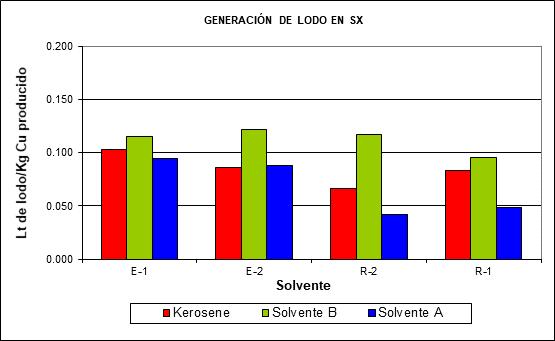
Gráfico 7. Generación de Lodo Prueba con Solventes Isoparafínicos
4.1.4.- Tiempo de Separación de fases
En general, según las mediciones hechas en planta, el TSF del Solvente B es mayor que del Solvente A, excepto en la etapa de Re-extracción 2. Esto se condice con las mediciones hechas de atrapamientos
200
Fig.8. TIEMPO DE SEPARACIÓN DE FASES POR ETAPA SOLVENTES PUROS
100TSF (Seg)
0
E-1 E-2 R-2 R-1 Kerosene Solvente B
Gráfico 8. Tiempo de Separación de Fases Prueba con Solventes Isoparafínicos
Existen adicionalmente evaluaciones relacionadas con la Carga Máxima, Selectividad, así como cinética de Extracción y Re-extracción que están más orientadas a la calidad del extractante y poco tienen que ver con el solvente probado, por lo que no se les consideran aquí.
4.2.- Estimación de Pérdidas Por Arrastres y Evaporación
Para esta evaluación se han tomado en cuenta los datos de consumos de extractante y solvente de la planta industrial desde un año atrás, (junio 2007mayo 2008), en base a los cuales se estimó los consumos de solvente tanto por arrastre como por evaporación.
4.2.1.- Consumo de Solvente por Arrastre o Atrapamiento.
Hay dos formas de estimar los consumos por arrastre de cada solvente a nivel industrial. Uno es utilizando las viscosidades, estimando primero los arrastres de cada solvente. La segunda forma es tomando los datos de arrastres de las pruebas en planta piloto. Nosotros tomamos la primera forma, debido a que el Solvente C, no pudo correr la prueba en la Planta Piloto. Nos basamos en los datos de los cuadros 2 y 3, estimando primero los arrastres de cada solvente y luego se halló un factor de escalamiento, que permita obtener los valores proyectados de pérdidas o consumo, por arrastre, de cada solvente. Se utilizó valores de viscosidad obtenidos en laboratorio. Para el caso kerosene el valor de viscosidad se obtuvo en Internet.
Cuadro N° 2 Viscosidades de Solventes
SOLVENTES Viscosidad cst Solvente A 3.25 Solvente B 3.36 Solvente C 4.22 Solv Blanco 1.90
Con los datos de inventario y consumo de extractante Lix 984N en la planta industrial de SX, para 1 año, se ha calculado que el consumo del Kerosene por arrastre fue de 897 m3/año. Con este valor se estimó también que el atrapamiento promedio es de 21 ppm para los flujos tratados de PLS y electrolito pobre (EP). Esto se muestra en el cuadro 3.
Cuadro 3. Estimación de Consumo de Solventes por Arrastre
CONSUMO TOTAL EXTRACTANTE AÑO 2007-2008
AÑO Produccion Inventario Concentr. Inventario Adición Consumo cobre solución org. extractante extractante forma N 2007 tm m3 % kg kg lt
Jun-07 8050 2,967 0.144 390735 11,970
Jul-07 7932 2,971 0.144 391513 11,970
Ago-07 7783 2,994 0.149 407881 26,334
Sep-07 7123 3,105 0.152 430679 32,319
Oct-07 7160 3,019 0.153 421046 0
Nov-07 6482 3,004 0.150 412048 0
Dic-07 6697 2,956 0.153 412201 9,576
Ene-08 6510 2,860 0.154 402791 0
Feb-08 7106 2,903 0.155 410143 19,152
Mar-08 8200 2,823 0.157 403968 11,970
Abr-08 7897 2,821 0.158 406223 21,546
May-08 8062 2,874 0.153 400803 11,700
89002 0.152 156,537 160,181
Densidad Kerosene Consumo kerosene por arrastre O/A: kg/lt
0.8 lt/año 896653 m3/año 897
Arrastre Global calculado: Consumo extractante,
m3/hr 0.018285 Consumo solvente por arrastre, m3/hr 0.102358 Consumo solución orgánica (extractante+solvente) m3/hr 0.120643 Flujo PLS + EP, m3/hr 5791 ppm 21
El consumo de arrastres escalado a Planta Industrial, se resume en el cuadro 4:
Cuadro 4. Consumo Estimado de Solventes por Arrastres (Atrapamientos)
CONSUMO SOLVENTES POR ARRASTRES O/A PROYECTADOS SOLVENTES ppm factor m3/año
Solvente A Solvente B Solvente C Solv blanco 36 37 46
1534 1992 1586 21 43.0407 897
4.2.2.- Consumo de Solvente por Evaporación
En este caso se utilizó los datos de tasa de evaporación hallados en la prueba estática de evaporación, (Cuadro 1), de soluciones orgánicas, realizada en Planta, por ser más real. Por otro lado, se utilizó los datos de inventarios y adiciones de kerosene para el periodo de Junio 2007-Mayo 2008 (1 año). Esto se resume en el cuadro 5
Cuadro 5. Estimación de Consumo de Solvente por Evaporación
CONSUMO TOTAL KEROSENE JUN 2007-MAY 2008
AÑO Produccion Inventario Concentr. Inventario Adición Consumo cobre solución org. extractante diluyente Kerosene 2007 tm m3 % kg kg kg
Jun-07 8050 2,967 0.144 2032113 119,606
Jul-07 7932 2,971 0.144 2034507 135,654
Ago-07 7783 2,994 0.149 2038122 118,698
Sep-07 7123 3,105 0.152 2107031 101,741
Oct-07 7160 3,019 0.153 2047165 133,253
Nov-07 6482 3,004 0.150 2042817 129,335
Dic-07 6697 2,956 0.153 2004161 59,349
Ene-08 6510 2,860 0.154 1935902 67,827
Feb-08 7106 2,903 0.155 1963696 111,128
Mar-08 8200 2,823 0.157 1904897 111,128
Abr-08 7897 2,821 0.158 1901110 151,400
May-08 8062 2,874 0.153 1948744 129,901
TOTAL 89,002 0.152 1,369,019 1,452,388 Tasa de consumo solvente, kg/tm Cu 16 Densidad Shellsol AR/2046, Kerosene kg/lt 0.8 Consumo total solvente Kerosene m3/año 1815 Area total expuesta planta SX Cerro Verde: m2 1467 Consumo de Kerosene por evaporación: m3/año 919 % 51 lt/día-m2 1.716
Se aprecia que, a nivel industrial, la tasa de evaporación es de 1.716 lt/dia-m2, con este valor y con las tasas de evaporación obtenidas en las pruebas, ver cuadro 1, hallamos un factor de escalamiento, con él podemos estimar el consumo industrial por evaporación para cada solvente. A continuación, se presenta un cuadro resumen donde se puede apreciar por separado el consumo estimado proyectado para cada solvente tanto por arrastre como por evaporación. Cuadro 6:
Cuadro 6. Estimado de Consumo Total de Solventes para SX de Cerro Verde
CONSUMO TOTAL SOLVENTES PROYECTADO: SOLVENTES POR EVAPORACION POR ARRASTRES TOTAL lt/día-m2 m3/año ppm m3/año m3/año Solvente A 1.144 613 36 1534 2146 Solvente B 1.450 777 38 1586 2362 Solvente C 0.817 438 47 1992 2429 Solv Blanco 1.716 919 21 897 1815
CONCLUSIONES
Metalúrgicamente el Solvente Isoparafínico A, es la primera opción de cambio, pues produce menos pérdidas totales de solvente. Técnicamente, no es recomendable cambiar el kerosene. Otras son las razones que exigen el cambio. Todos los solventes isoparafínicos muestran las mayores pérdidas en los arrastres. El solvente C tiene muy poca pérdida por evaporación, pero su peor performance se refleja en las pérdidas por arrastre. Estas conclusiones son solo metalúrgicas, se requiere además un estudio económico, así como considerar el factor logístico, por ser solventes importados.
DISEÑO DE REACTORES INDUSTRIALES INTELIGENTES CON GAS NATURAL
Ing. Percy Castillo Neira
PRESENTACIÓN
La revolución industrial con carbón y su evolución con petróleo cambiaron el mundo, pero sus dificultades de manejo y combustión limitaron el desarrollo tecnológico; transcurridos 2 siglos, el nivel actual de eficiencia termodinámica de procesos industriales y máquinas térmicas es inferior al 50 %.
La situación actual de la pandemia y depresión económica, nos permite plantear la reconversión industrial que posibilite una efectiva reactivación económica, utilizando la tecnología que hemos desarrollado a partir de la formulación de la Teoría Inorgánica de la Combustión que nos permitió demostrar que el proceso fisicoquímico más importante del planeta es maravillosamente simple.
Su aplicación con carbón y petróleo ya nos permitió conseguir resultados importantes optimizando los procesos conocidos, pero al aplicarla con las formidables ventajas y posibilidades del gas natural y comprobar que representa un mundo diferente en el campo científico, establecimos la necesidad y conveniencia de plantear un modelo diferente de procesos, reactores y quemadores industriales, llegando después de 10 años de exitosa aplicación en procesos y proyectos de la mayoría de sectores industriales a perfeccionar el “Diseño de Reactores Industriales Inteligentes con Gas Natural”.
Considerando la grave situación actual que nos afecta a todos, hemos decidido ponerla a disposición de los ingenieros y empresas industriales dispuestos a constituir la alternativa diferente en un mundo caracterizado por la corrupción, combinando la simbiosis perfecta entre innovación y productividad que planteamos, repotenciando la creatividad y ética de la ingeniería, postergada y envilecida por la priorización de factores comerciales y económicos.
LA AFORTUNADA OBLIGACIÓN DE UTILIZAR LA ENERGÍA LIMPIA Y RENOVABLE DE LOS HIDRATOS DE METANO
La maravillosa perfección de la naturaleza se ha encargado de transformar la basura vertida por los ríos en los mares y acumulada durante millones de años en la profundidad de los taludes de los litorales continentales en METANO, la molécula básica fundamental de la química orgánica y el ciclo vital, asegurando la disponibilidad de su energía perfecta, limpia, ecológica y renovable.
Los volúmenes estimados son inmensos y se siguen produciendo; si no los utilizamos masivamente incrementarán su actual afloramiento a la atmósfera, determinando la extinción de cualquier forma de vida sobre la tierra.
En esta forma, la naturaleza nos obliga a utilizar las ventajas y posibilidades del gas natural (Metano) en el campo técnico, económico y ecológico:
Técnicamente, como demostramos más adelante con resultados, la utilización del gas natural con diseños inteligente (adecuados) de procesos, reactores y quemadores nos permite alcanzar niveles máximos de eficiencia termodinámica (promedio 72 % en 10 años de aplicación). Económicamente, representa niveles inferiores de costos de inversión, producción y
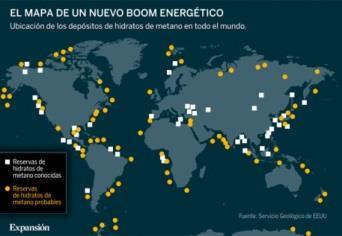
mantenimiento, mejorando la competitividad global. Ecológicamente, además de plantear una realidad nueva y diferente, representa la disminución del 30 % de emisiones de efecto invernadero, por sustitución y optimización de la eficiencia de empleo, equivalentes a los niveles recomendados en Kioto, Lima y París.
El uso del petróleo con tecnología comercial ha convertido la industria en un infierno inmanejable; nuestra tecnología con gas natural lo transforma en un Infierno Inteligente
TECNOLOGÍA SMART HELL
Propiedad Intelectual Exclusiva de COMBUSTIÓN Y ECOLOGÍA S.A.C.
Diseño de Reactores Industriales Inteligentes con GAS NATURAL para Reactivación Económica
La dependencia del petróleo y el poder económico han convertido las plantas y procesos industriales en un caos termodinámico conveniente para su explotación comercial, instalando “llave en mano” tecnología costosa, ineficiente y contaminante. La formación profesional universitaria se ha adaptado convenientemente a esta realidad, con programas obsoletos y posgrados de papel que convierten a los ingenieros en supervisores de planta.
Utilizando un aforismo matemático podemos comparar la utilización del petróleo como un problema algebraico con muchas variables y muy pocas ecuaciones, lo que se ha traducido en una gran complicación en la práctica industrial ; para resolverlo se ha desarrollado toda la complejidad del cálculo infinitesimal y similares, determinando que en la formación de ingenieros se produzca la teorización de conceptos que aleja la formación de ingeniería de la realidad de los procesos industriales, permitiendo la priorización de objetivos comerciales y la corrupción del desarrollo tecnológico comercial.
Al aplicar nuestra tecnología con la molécula básica fundamental del Metano, hemos reducido las variables del problema de su combustión a un número muy reducido, estableciendo la condición de poder disponer de mayor número de ecuaciones que variables. Esta formidable simplificación nos permite visualizar un mundo diferente de la combustión y sus aplicaciones industriales y al plantear una concepción diferente de procesos, reactores y quemadores, hemos conseguido alcanzar los máximos niveles termodinámicos de eficiencia; al mismo tiempo, desarrollar una nueva pedagogía en la formación académica que nos permite recuperar la creatividad, ética y majestad de la ingeniería.
TECNOLOGÍA INTELIGENTE PARA UN MUNDO DIFERENTE
Los fundamentos para desarrollar nuestra tecnología de reactores industriales inteligentes que permitan aprovechar las posibilidades y ventajas del gas natural los definimos a través de la investigación aplicada en los 4 campos fundamentales de la ingeniería de combustión y procesos industriales: Cinética química, mecánica de fluidos, termodinámica y transferencia de calor:
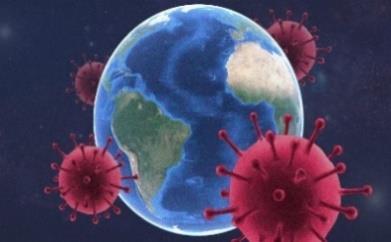
Cinética química
El estudio de la termocinética de esta reacción heterogénea, nos ha permitido establecer una coincidencia fundamental entre las 2 etapas del desarrollo de la combustión y el requerimiento de oxígeno para su desarrollo:
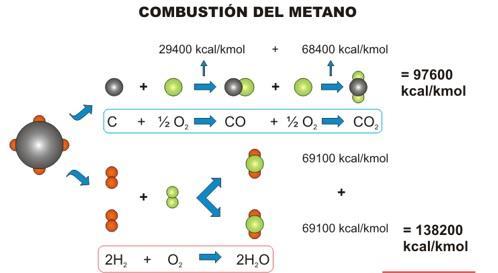
Como puede apreciarse en el análisis estequiométrico de la combustión del metano, la primera etapa heterogénea sólido-gas produce 1/3 del calor total y la segunda homogénea gas/gas los 2/3 restantes.
El manejo adecuado de este factor en el campo práctico nos ha permitido formular diferentes innovaciones y sus aplicaciones industriales, aprovechando los flujos de calor activo de la combustión gas-gas y formar circuitos de recirculación de gas y calor, con máximo aprovechamiento termodinámico.
Mecánica de Fluidos
La utilización de la energía cinética contenida en la presión del gas natural como flujo dominante para el control de la cinética de la combustión y la emisividad de llama, permite mejorar la transferencia de calor por radiación.
La velocidad de combustión del gas natural resulta en muchos casos una importante ventaja para disponer de calor inmediatamente utilizable sin necesidad de una cámara de combustión, pero una aparente desventaja cuando la emisividad de llama resulta necesaria y conveniente para transferencia de calor por radiación.
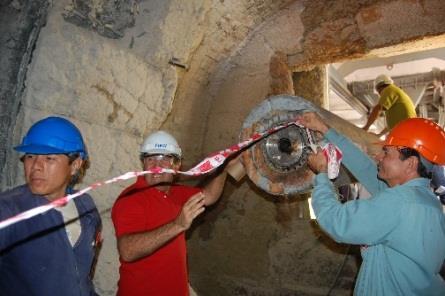
La utilización combinada de los impulsos del gas y el aire primario, nos ha permitido controlar la intensidad de mezcla gas natural y aire primario, aprovechando nuestra alta especialización en mecánica de fluidos, para conseguir un control regulable de la cinética de la combustión que se traduce en un dominio de la formación de llama y su emisividad.
La investigación aplicada en este campo nos ha permitido establecer las condiciones de transferencia de calor convenientes para cada proceso específico y las características del reactor adecuado con la atmósfera requerida en el interior de hornos de oxi reducción y tratamiento térmico.
Transferencia de Calor
Existen tres mecanismos de transferencia de calor, pero no pueden existir simultáneamente los tres en un medio. Así, la transferencia de calor sólo ocurre por conducción en los sólidos opacos, pero por conducción y radiación en los sólidos semitransparentes. Un sólido puede comprender conducción y radiación pero no convección. Sin embargo, un sólido puede presentar transferencia de calor por convección y/o radiación en sus superficies expuestas a un fluido o a otras superficies; las superficies exteriores de un trozo frío de roca se calentarán por convección de gases calientes y radiación de una llama, pero el calor se transfiere hacia la región interior de ella exclusivamente por conducción. Las aplicaciones de esos conceptos nos han permitido establecer y aprovechar un inmenso potencial de optimización de procesos existente en este campo. Termodinámica
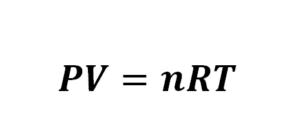
En cualquier proceso industrial el control termodinámico de la atmósfera interna del reactor siempre resulta determinante:
TECNOLOGIA CON RESULTADOS EN EL CAMPO INDUSTRIAL
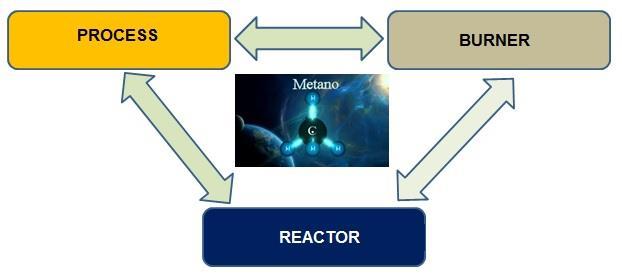
Para demostrar que resulta factible aplicar el ingenio y creatividad que deben caracterizar a la ingeniería sin influencias comerciales, les mostramos algunas de las innovaciones tecnológicas que hemos conseguido al aplicar nuestra tecnología en procesos industriales, trabajando en forma directa y comprometida con los propios ingenieros de planta de nuestros clientes a nivel latinoamericano, previamente capacitados en fundamentos teóricos y especializados con su participación directa y comprometida en el proyecto, garantizando en esta forma la sostenibilidad de resultados conseguidos.
En calderos pirotubulares modificamos el quemador mixto, para utilizar 100 % de gas natural, instalamos turbuladores en los pasos de tubos para mejorar el coeficiente de transferencia chimeneas para precalentar el agua de alimentación , llegando a niveles de eficiencias mayores a 90 % con 5 % de exceso de aire.

AHORRO PROMEDIO: 10 %. Incremento de producción 5%.
En calderos acuotubulares modificamos los quemadores para trabajar con bajo exceso de aire, compensando la menor emisividad de llama y cambiamos recuperadores de precalentamiento del aire por economizadores de diseño de alta eficiencia para precalentar el agua de alimentación. Eficiencia: 87 % y 30 % aumento de producción.
AHORRO PROMEDIO: 7-8 % de costo por TM de vapor.
Los gases de combustión del gas natural son aire caliente perfectamente utilizable para secado directo. La utilización de quemadores en vena de aire nos permite disponer de gases limpios para secado para cualquier temperatura y volumen requeridos en distintos tipos de secadores.Cuando el proceso no contamina klos gases de secado, la recirculación de calor resulta obligatoria.
AHORRO PROMEDIO: 30-40 %.
Los quemadores Doble Swirl Jet con utilización combinada de gas natural y aire primario como flujo dominante, nos permiten llamas emisivas y mayor proporción de recuperación de calor en el aire secundario de hornos rotativos cementeros, estabilizando la temperatura de la zona crítica de clinkerización.
AHORRO PROMEDIO: 15 %.
Los quemadores de combustión sumergida nos permiten aprovechar el poder calorífico superior al inyectar los gases de combustión en el interior de líquidos que deseamos concentrar o calentar para tratamiento metalúrgicos, calentamiento de agua de lavadoras textiles, evaporización, eliminación de agua de aceites, etc.
AHORRO PROMEDIO: 35 %
Utilizando quemadores especiales con impulso y calentamiento, efectuamos simultáneamente las operaciones de transporte y secado de materiales pulverulentos, optimizando costos de inversión, procesamiento y mantenimiento.
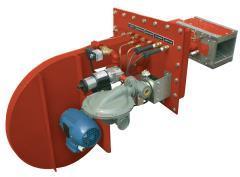
AHORRO PROMEDIO: 35 %
Aplicando el concepto flash calciner con la aplicación de nuestra innovación de flujos de calor activo, desarrollamos los vórtices turbulentos ascendentes que nos permiten conseguir el Calcinador Termodinámicamente Perfecto: Isotérmico, isócoro, isobárico y adiabático, sin atoros en ciclones y anillos en el interior del horno rotatorio.
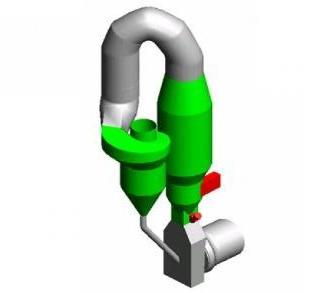
AHORRO PROMEDIO: 15 %. Incremento de producción 15 %
El Horno Vertical de Cal Circular Stone Flash (CSF) con doble anillo de flujos de calor y parrilla de doble disco giratorio para regular el flujo de material, nos permite producción de alta calidad en hornos de capacidad de media producción (300 t/h), baja inversión y alta eficiencia. Convertimos los hornos Maerz de Doble Cuba regenerativos en 2 CSF con el doble de producción y alta reactividad.
AHORRO PROMEDIO: 50 %. Incremento de Producción: 100%
La utilización de precalentadores de hornos cementeros antiguos, los utilizamos para producción de cal con polvo en suspensión de gases, instalando nuestro calcinador termodinámicamente perfecto y un enfriador de cal/recuperador de calor con alta producción y eficiencia. La modificación de hornos cementeros para producción dual clínker/cal resulta una opción importante.
AHORRO PROMEDIO: 50 %. Incremento de Producción: 150 %.
El diseño de reactores inteligentes para recirculación continua de gases y calor de alta eficiencia termodinámica, aplicado al calentamiento de barras y palanquillas de acero desplazadas por rodillos, ha desplazado a los hornos de Vigas Galopantes y ya estudiamos muchos otros campos de aplicación en hornos de tratamiento de acero.
AHORRO: 50 %. Optimización de inversión: 60%.
La utilización de hornos de calentamiento de palanquillas de acero para laminación lineales con transporte de rodillos giratorios con anillos de recirculación total de gases y calor (360°) sustituirán muy pronto a los complicados y costosos sistemas de vigas galopantes.
AHORRO: 50 %. Incremento de eficiencia: 100 %.
La modernización de hornos de OxiReducción de metales para refinación cambiando la posición y diseño del quemador para convertirlo a 2 pasos, nos permite disminuir el tiempo de colada al 50 % y doblar la producción, disminuyendo las pérdidas de calor y contaminantes en un 50 %.
AHORRO 50 %. Incremento de eficiencia: 100 %.
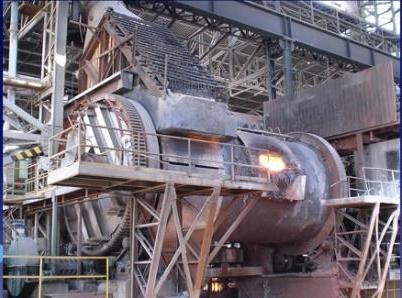
Estas experiencias nos han convencido y demostrado que el DISEÑO DE REACTORES INDUSTRIALES INTELIGENTES CON GAS NATURAL representa la Tecnología adecuada para Reconversión Industrial para Reactivación Económica.
TECNOLOGÍA CON RESULTADOSEN EN EL CAMPO ACADÉMICO
La simplificación de nuestra tecnología nos permite complementar experiencia académica y práctica industrial para desarrollar una Innovación Académica en el dictado de Cursos de Posgrado.
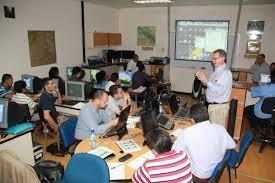

Actualmente estamos dictando 2 modalidades adecuadas para el distanciamiento social obligado por la pandemia:
Curso VIP (Virtual Interactivo
Personalizado) para ingenieros de planta de nuestros clientes industriales, complementado por reuniones virtuales grupales semanales para análisis y discusión de todo el temario y los resultados de evaluaciones.
Cursos Digitales Autodidácticos para ingenieros con entrega de Manuales Audio
Visuales del Temario complementado con consultoría y evaluación para certificación individual.
Las pruebas realizadas en este campo nos demostraron que los Webinares no resultan apropiados para Posgrados de Ingeniería, por lo que combinamos el diseño de un Manual Práctico Audiovisual apropiado, consultoría permanente y Cursos Virtuales con participación de 5/10 ingenieros.
Al volver a la normalidad, mantendremos la condición de cursos virtuales combinados con trabajo de planta.
Al coordinar nuestras actividades académicas con Universidades, estamos trabajando para invertir parcialmente la práctica de que los ingenieros reciban su capacitación en las aulas, para proyectar las universidades al campo industrial, implementando temas de investigación aplicada que enriquezcan la experiencia y fomenten la innovación y desarrollo tecnológíco industrial.
FABRICACION DE ESPUMA FLEXIBLE DE POLIURETANO SIMPLIFICANDO EL PROCESO
Ing. Victor Dember Gomez Larrea
El presente trabajo tiene como objetivo principal hacer ver a nuestros estudiantes y colegas, que muchos procesos que aparentemente son muy complicados, nosotros como ingenieros químicos estamos en la capacidad de simplificarlos conociendo el fundamento de sus procesos.
Si nosotros visitamos la fábrica Paraíso u otros fabricantes de espuma podemos ver una serie de operaciones y procesos aparentemente complicados e inalcanzables de realizar, pero al conocer los fundamentos se puede de una forma simple y al alcance de nuestras posibilidades, lograr un producto similar.
Es importante también inculcar en nosotros la idea de hacer empresa. Al igual que la fabricación de espuma hay otros productos cuyo proceso estamos en la capacidad de simplificarlos (plásticos tecnopor, etc.).
El aporte en este trabajo es la experiencia adquirida en una planta que maneje en Arequipa. En el presente trabajo se está obviando algunas reacciones y otros que son fácilmente accesibles en bibliografía.
USOS DE LA ESPUMA
Entre las numerosas áreas de aplicación de las espumas flexibles destacan: Colchones, Muebles, Almohadas, Componentes Automotores, Componentes para el calzado, Juguetes, Ropa, Artículos de Limpieza, Artículos de Higiene Personal, Artículos de Construcción, Embalaje.
MATERIA PRIMA Y ADITIVOS QUE INTERVIENEN EN LA PRODUCCIÓN DE POLIURETANO
POLIOLES REACCIÓN DE GELIFICACIÓN O DE
POLIMERIZACIÓN. La reacción entre un isocianato y un alcohol.
AGUA.- Determinante para la densidad del producto. Punto importante a tratar es el uso de agua que puede producir TDA el cual puede ser cancerígeno, por eso al final de este tratado se hace referencia a ello.
EQUIPOS PARA LA PRODUCCION DE ESPUMA
ISOCIANATOS isocianato deben entenderse como basadas en el TDI 80/20.
SURFACTANTES DE SILICONA Las siliconas se emplean principalmente como agentes tensoactivos o surfactantes en la producción de espumas mejora la miscibilidad de los ingredientes.
CATALIZADORES DE AMINAS Y DE ESTAÑO.-
Su principal función consiste en balancear y controlar la gelificación y la reacción de expansión de manera que, el proceso de formación de espuma, se pueda controlar adecuadamente.
DISEÑO DEL REACTOR.-
El reactor no es mas que un cilindro, con este diseño de capacidad para 100 kilos de mezcla. Diseño por Dow Chemical, el cual se puede adaptar para la capacidad de producción del usuario.
MOLDES.
-Para evitar el uso de moldes sofisticados de metal u otros materiales, se puede preparar moldes con materiales como triplay o melanina. En la base se debe colocar papel Crap para cada molde y colada, en los costados se puede usar desmoldante (caro) o una película de polietileno(económica)que envuelve toda la parte lateral interior del molde, para evitar se pegue la espuma, estas pueden servir para unas 20 coladas.
EQUIPOS DE CORTE. -
En esta sección una forma de simplificar el costo es fabricar una cortadora sin fín similar a las cortadoras de carne, con la diferencia que se debe tomar en cuenta las medidas a trabajar. La cinta para el corte es un fleje liso de aprox 1.5” de ancho y 1.5 mm espesor, la cual será afilada constantemente por un par de piedras tipo copa que se regulan al paso del fleje sinfín
La cortadora horizontal es mas complicada porque tiene que tener un sistema de regulación de altura, pero podría obviarse si se diseña adecuadamente la cortadora vertical
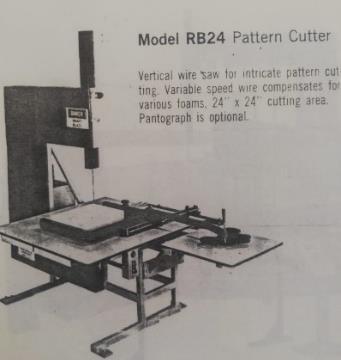
La simplificación consiste en preparar un equipo de izamiento sencillo (con rondanas) que permita colocar el reactor (acoplado al motor eléctrico 0,65HP mínimo y 900 a 1200 RPM ) en el centro del molde y luego ser elevado( ayudándose con un contrapeso para no hacer mucha fuerza y evitar el uso de otro motor eléctrico para la elevación y retirado del molde
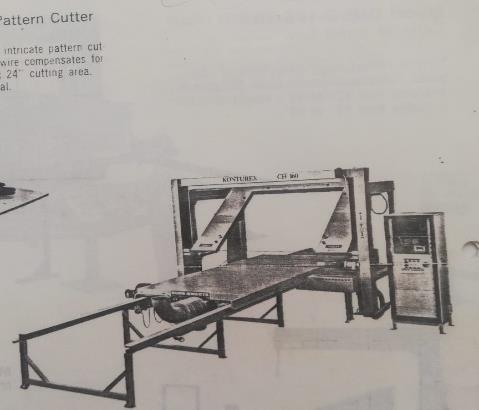
ETAPAS EN LA PRODUCCION Y FORMACIÓN DE ESPUMAS DE POLIURETANO.
La producción de espuma pasa por las siguientes etapas :
DOSIFICACIÓN DE LOS COMPONENTES
DE LA ESPUMA Y MEZCLADO CREMADO CRECIMIENTO. CRECIMIENTO COMPLETO GELIFICACIÓN CURADO
FORMA SIMPLE DE MEZCLA DE COMPONENTES PARA AREQUIPA.
Utilizar el reactor colocado en el centro del molde para mezclar los reactivos en el siguiente orden (usando un embudo para el vaceado.):
- Vaciar la mitad del poliol a utilizar en el reactor - En la otra mitad de poliol mezclar con una espátula la silicona y la amina disuelta en el agua y vaciarla al reactor. Agitar durante 12 segundos - Vaciar el octoato de estaño al reactor y agitar por 15 segundos - Finalmente vaciar en el reactor el isocianato. Agitar 6 segundos
Despues de producirse las diferentes etapas de la reacción se deja reposar el molde por lo menos 3 horas y luego se puede proceder a desmoldar
FORMULACIÓN DE ESPUMA
Tabla 2.16 Formulación típica de espuma de poliuretano
Componentes
Partes por peso pphp Poliol (voranol 3137) 100 Agente químico de expansión (Agua) 3.2 Agente físico de expansión (cloruro de Metileno) 28 Surfactante de silicona 1,5 Catalizador amínico (33-LV) 0.28 Catalizador órgano – metalico (T29) o (T-9) 0.21 Isocianato (TDI 80/20) 41.4 Indice de TDI 105
Fuente: Corporación G.T.M Del Perú S.A
Según mi Experiencia la formulación promedio utilizada en Arequipa para los diferentes tamaños de molde con mejores resultados es :
FORMULACION PARA AREQUIPA
COMPONENTE Kg/m3
Poliol 10.90 TDI 7.64 Silicona 0.196 Amina 0.018 Octoato de Sn 0.034 Agua 0.545-0.600
Fuente: Experiencia Personal
Las formulaciones de espuma no se aplican de modo universal en todas las máquinas de espumas o bajo diferentes condiciones de operación. Siempre resulta necesario regular perfectamente los niveles de los catalizadores
EFECTO DE LAS VARIABLES
Estas variables son fácilmente ubicables en cualquier bibliografía.
PROCEDIMIENTO DE FABRICACION SIN INCORPORACION DE AGUA.
A continuación les presento un extracto del trabajo realizado y patentado por el español Del Carpio Conde, Bernardo, que patento el proceso de fabricación de espuma flexible de poliuretano sin usar agua en su formulación. Esta invención se refiere a una espuma de poliuretano compuesta sustancialmente por moléculas de poliuretano y exenta de tolueno di -amina (TDA) , así como a un procedimiento para la fabricación de dicha espuma, en una única reacción básica, sin la incorporación deliberada de agua a la formulación con el fin de evitar la formación de TDA, un compuesto carcinogénico .
EJEMPLOS
Como ejemplo ilustrativo, no limitativo del alcance, del procedimiento de la invención, se propone una formulación representativa con un intervalo de valores para espumas de poliuretano flexibles, totales, de reacción única:
Poliol 70-100 pph Peso molecular 2.000-4.000 y reactividad 60-80 Copolímero 0-30 pph 15-40% de sólidos Isocianato Según la formulación índice 100% (TDI, otros) Cargas 0-35 pph carbonato calcico, sulfato de bario, etc. C02 2-10 pph a temperatura y presión convencionales. Cloruro de metileno 0-25 pph Tensoactivo 0,8-2 pph silicona Catalizador 0,15-0,3 pph octoato de estaño o cualquier otro catalizador órgano-metálico Entrecruzantes 0-4 pph DEOA o similar, glucosa, glicerina, etc Temperatura 20-26ºC Presión 0,3-2 atm
Desde luego, cada formulación específica caerá dentro del intervalo de los valores mencionados previamente o incluso más allá, de acuerdo con los tipos específicos de espumas y sus características requeridas comercialmente. Naturalmente, siempre habrá un compromiso entre flexibilidad y rigidez puesto que son propiedades opuestas.
“Queda como trabajo para los ingenieros químicos, aplicar esta nueva tecnología al procedimiento convencional explicado anteriormente y aplicarlo en nuestra localidad”
ELABORACIÓN DE BIOCOMBUSTIBLE ECOLÓGICO A PARTIR DE BIOMASA Y RESIDUOS CELULÓSICOS
Resumen
Mg. Mario Alberto Ramos Chávez
Se realizó la fabricación de un tipo de briquetas ecológicas, utilizando residuos sólidos orgánicos generados en el distrito de Yanahuara-Arequipa. Tales residuos comprendían; restos de madera provenientes de podas, palos de escobas, cajas de embalajes de frutas, restos de jardinería y envases de cartón deteriorado. Se probaron distintas formulaciones para lograr un producto firme, poco quebradizo y de alto valor calorífico, que al mismo tiempo utilice los productos orgánicos de desecho indicados; logrando briquetas con buen grado de compactación y granulometrías usado para cocina por los trabajadores de la planta de reciclaje y como insumo de calefacción en parrilladas y otros compromisos sociales. Adicionalmente, se diseñó una cocina artesanal para el uso de tales briquetas.
Palabras Clave. Maderas, combustión, capacidad calorífica, prensados, briquetas.
Abstract: The purpose of the present investigation is to propose the manufacture of an ecological biofuel or ecological briquette, using wood remains from pruning, broomsticks, fruit packaging boxes and cardboard containers that are for single use; achieving a responsible product with the environment, since the consumption of fossil fuels which present highly polluting compounds will be avoided; our tests demonstrate an adequate degree of compaction and grain size and a heat capacity between 4600 to 5000 kcal / kg; likewise, an internal nozzle was added to our briquette, to facilitate and improve combustion; Additionally, a kitchen was designed that will have two functions, the first being that of a heater when it is completely assembled and the second as an artisan kitchen. Keywords: Wood, combustion, heat capacity, pressing, briquettes.
En la actualidad la problemática medioambiental viene siendo vista desde una perspectiva distinta a la convencional, cada vez se toma con mayor relevancia y en consideración los cambios ambientales que vienen sucediendo en el mundo, ya que las consecuencias inmediatas y futuras depende de nosotros mismos, es por ello que se propone una alternativa de cambio y cuidado al medio ambiente, teniendo en cuenta que el incremento de estos fenómenos de cambio climático viene suscitándose con mayor frecuencia y con ello el incremento de los desastres naturales que viene afectando a la flora, fauna y la salud de las personas.
Los objetivos y metas del desarrollo sostenible plantean conseguir un futuro integro de sostenibilidad que beneficie no solo al medio ambiente, sino también a quienes disfrutamos del mismo; por lo que en el objetivo 15 de los citados objetivos y metas del desarrollo sostenible, trata de luchar contra la desertificación, detener e intervenir la degradación de las tierras. (1). Por todos los cambios que viene sufriendo nuestro planeta tierra, surge la idea de implementar un biocombustible el cual reducirá la tala de árboles y fomentar la aplicación de la economía circular al momento de utilizar desechos que normalmente no son reaprovechados en la actualidad. Por otro lado, también se tiene en cuenta la población que actualmente vive en extrema pobreza ya que no solo se brinda una alternativa de emprendimiento a través del desarrollo de la presente propuesta, sino que aquellos que cuentan con los recursos limitados para poder optar por otro tipo de combustible para su alimentación, protección en las épocas de frio y sobre todo en su salud (2), ya no estarán expuestos a grandes cantidades de componentes tóxicos que perjudiquen su salud como lo es el azufre que se encuentra presente en el combustible común.
MATERIAL Y METODOS
Residuos Celulósicos
Comprende los siguientes materiales:
1.- Residuos de cartón y cartoncillo a un 20 %, previamente molido
2.- Residuos de jardinería previamente molidos 34%
Preparación.
Se aplica un diseño estadístico del tipo complex box, para 3 variables, requiriendo 18 ensayos
Preparación de muestras
-Los residuos de biomasa fueron molidos en un molino de martillos con malla de descarga de ¼ de pulgada para las celulosas a emplear, usado normalmente en la planta de reciclaje de plásticos.
-Seguidamente se dejó remojando la biomasa molida por 24 horas.
-Se agregó el aglomerante, y se realizó la mezcla con un agitador a baja rpm
-Se procedió al molido de las muestras en molino de martillos con malla de descarga de ¼ de pulgada para las celulosas a emplear
-Seguidamente se dejo remojando en 10 litros de agua cada lote de muestras, las cuales al día siguiente fueron mezcladas con el aglomerante, estando listas asi para la operación del prensado
-Se sometió a prensado usando una prensa tipo piston de 0 a 500 Kgr/cm2
Llenado de pasta a la prensa
-Se procedió a la preparación de 18 lotes de muestras cada evolución tubo 5 sub muestras, de las cuales una se empleó para rotura, otra para friabilidad, y las 3 restantes para evaluación del poder calorífico en forma de toma de lectura con un pirómetro y su posterior conversión a poder calorífico.
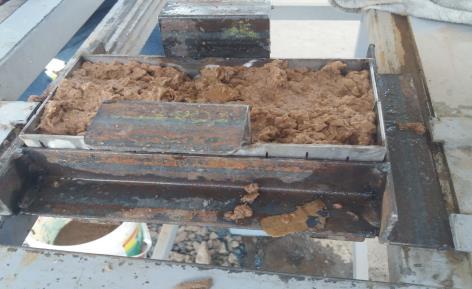
Pruebas de calidad.
Se hicieron tres tipos de pruebas, para evaluar la capacidad de generar calor. Las pruebas de resistencia de las briquetas a la compresión se llevaron en la prensa hidráulica de 50*50 cm Dando valores de la rotura a la compactación fue del orden de 60 a 120 kgf/cm2
Para determinar la friabilidad, las briquetas fueron colocadas dentro de un tambor rotatorio por 15 minutos a una velocidad de rotación de 35 rpm. Se pesaron al inicio y al término del ensayo. Esta prueba fue determinada siguiendo la metodología descrito por Quirino and Otávio, (1991).

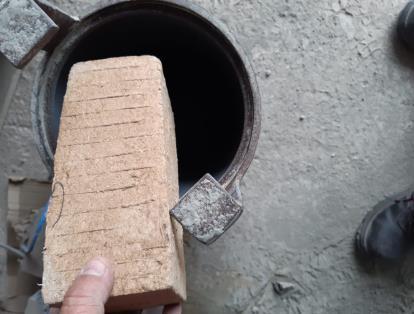
Evaluación
Se evaluó el efecto de tres variables; contenido de material celulósico, contenido de aglomerante y presión, aplicando un diseño experimental boxcomples.
Las variables y niveles del planteamiento experimental son los siguientes:
Tabla 2. Niveles de las variables
Variables Niveles
Z1 Celulósicos (gr) 1500 2000 Z2 Aglomerante (gr) 10 100
Z3
Presión (KgF/Cm2) Fuente: Elaboración Propia 11 34
-La matriz del diseño adopta la forma que muestra la siguiente tabla.
Tabla 3. Matriz del diseño experimental
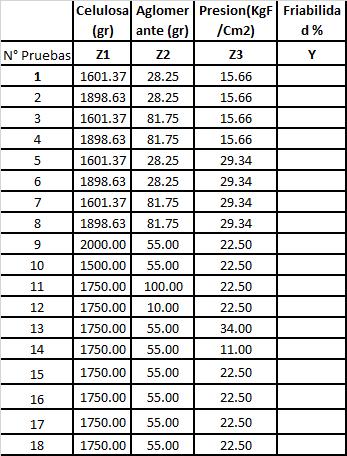
RESULTADOS
A los datos se les evalúa la significancia, mediante una prueba de tukey.
-Las primeras evaluaciones respecto a la friabilidad fueron:
Tabla 4. Resultados de las pruebas
Donde los valores óptimos experimental para la friabilidad se obtendrá con los valores optimos experimentales asi: Tabla 5 Valores óptimos experimentales
Tambien Se llevo a graficas los valores del diseño asi
La superficie de respuesta se construyó aplicando el software minitab, donde se observan zonas optimas centrales
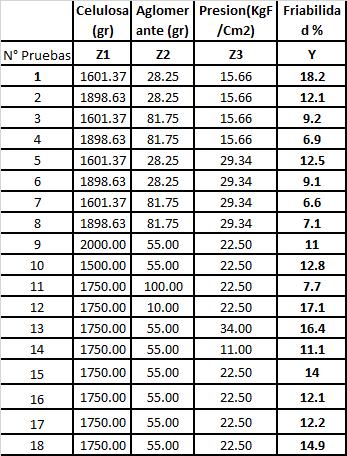
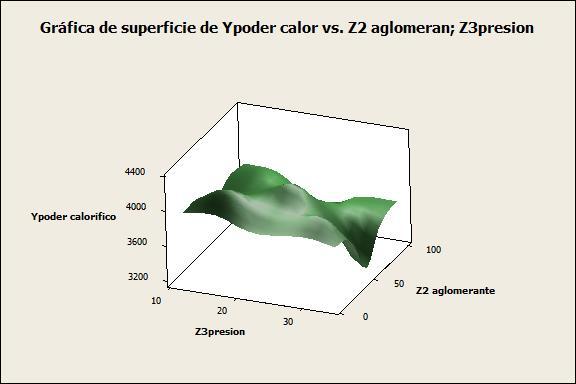
Bibliografia
1
2
3
4
5 Naciones Unidas. Objetivos de Desarrollo Sostenible. [Online].; 2015 [cited 2020 Abril 1. Available from: https://www.un.org/sustainabledevelopment/es /sustainable-development-goals/.
Smith KR. FAO. [Online].; 2005 [cited 2020 Abril 3. Available from: http://www.fao.org/3/a0789s/a0789s09.htm.
Evelin Tamayo Gutiérrez OSMEMQ. Aprovechamieno de residuos ligno-celulósicos en la elaboración de empaques secundarios ecológicos. Industrial Data. 2017 Enero 11; 20(2,2017): p. 37-42.
José Turrado MFDFJFARS. Envases de Cartón para Líquidos como Fuente de Fibra Secundaria. Scielo. 2011 Diciembre; 23 (3)(32012).
Kuo KK. Principles of combustion. Segunda ed. Wiley J, editor. Nueva Jersey: Hoboken; 2005.
ANÁLISIS COMPARATIVO DE RENDIMIENTO DE EXTRACCIÓN DE ACEITE ESENCIAL DE HOJAS Y HOJAS -TALLOS DEL ARBOL DE EUCALIPTO
RESUMEN
Mg. Rodolfo Roque Perez Mendez Dra. Catalina Orfelina Rondon Saravia
El presente trabajo tiene por objeto evaluar la eficiencia en la recuperación de aceite esencial de la materia prima – Eucalipto, en la que se utilizara para la experiencia una muestra de 30kg de solo hojas de eucalipto y se comparara con otra muestra de igual masa, pero considerando tallos y hojas. Mediante dicha experiencia podemos decir que si bien es cierto existe una mayor recuperación de aceite en la muestra de solo hojas, pero por lo observado en las curvas de recuperación en la muestra con tallos la mayor cantidad de recuperación del aceite esencial durante el encendido del equipo extractor ocurre en un menor tiempo, por lo que también se puede decir que es preferible trabajar con muestras de tallos y hojas, a que si se evalúa para una línea de producción, se perdería tiempo en separar los tallos además de que se puede cortar el encendido del equipo extractor para evitar consumir combustible, y ganar tiempo para realizar otra carga en un día de operación.
La materia Prima
Tener en cuenta:
- Tipo de hoja (hoja de brote) - Poca manipulación - Tiempo de reposo - Lavado
1. Acondicionamiento del equipo
Tener en cuenta:
- Limpieza del equipo: (se realiza una corrida únicamente con vapor de agua). - De preferencia en el uso del agua debe ser un agua de baja dureza, tanto para la limpieza como para la extracción.
Limpieza del equipo
- La limpieza es con el vapor de agua, dura aproximadamente unos 15 minutos. El flujo de vapor arrastrara la suciedad adherida a las paredes.
Carga del equipo
- El material es vertido en el equipo, la idea es que toda el área quede cubierta con las hojas de eucalipto y no quede espacios huecos, por donde pueda circular el vapor con facilidad. (si esto ocurre será poco eficiente la recuperación del aceite esencial). Fig.1. Limpieza de vapor del equipo extractor
Fig. 2. Carga del equipo
Encendido del quemador
El quemador se ubica en la parte inferior del equipo, este suministrara calor para lograr la conversión del agua liquida a su fase vapor, mientras mas agua se vaporiza, va generando presión que sera la suficiente
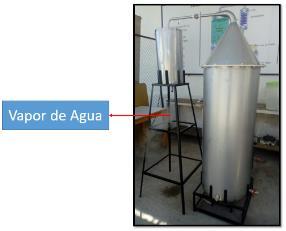
para lograr atravesar toda la carga organica y llevar acabo el arrastre.
2. Condensación
- El Condensador cumple la función de condensar los vapores que vienen de la columna de extracción.
- El condensador posee un suministro de agua fría para lograr siempre intercambiar energía calorífica con los vapores. - Posee dos entradas y dos salidas. - La operación de condensación da inicio y se recupera aceite esencial y agua floreada o hidrolato.
- El recipiente colector debe estar totalmente limpio para evitar que aceite se quede pegado en la superficie
Fases
El agua y el aceite son líquidos no miscibles (líquidos que no se pueden mezclar a condiciones normales).
Fig. 3. Recuperación aceite e hidrolato
Aceite esencial de eucalipto
Hidrolato de eucalipto
3. Decantación
- La decantación es la operación de separar el agua del aceite.
- El liquido menos denso se ubicara en la zona superior sobre el liquido mas denso.
- La operación de separación por decantación se desarrolla en una pera de decantación o florentino.
Fig. 4. Decantación
4. Cuantificación
- El aceite recuperado es medido, para su posterior envasado.
- Se debe asegurar que el aceite no debe contener agua
- Si el aceite sale con partículas, es recomendable pasar por papel filtro.
6. Envasado
- El envasado del aceite esencial, debe ser en frascos color ámbar, para protegerlos de luz, ya que la luz tiende a desnaturalizar al aceite y provocando cambios en la estructura del mismo y por ende deteriorando la calidad.
7. Almacenamiento
- El aceite esencial debe permanecer en un ambiente fresco o refrigerado para mantener con mejor efectividad las características originales del aceite.
5. Limpieza del equipo
- Los residuos orgánicos que quedan luego de la extracción (hojas de eucalipto luego de la extracción), al ser carga organica, estas se pueden degradar y pasar a ser me diante un proceso de compostaje un abono para la nutrición de suelos.
- Por otro lado también el residuo se suele hacer secar y puede ser moldeado haciendo uso de un aglomerante para ser transformado en briquetas.
7. Análisis comparativo extracción de aceite esencial de eucalipto
Para el análisis comparativo se toma encuentra la cantidad de materia prima utilizada para ambos casos la cual es de 30 kg, y la procedencia de la materia prima es del distrito de Polobaya de la ciudad de Arequipa.
Luego para graficar, se considera un volumen de 1 litro entre hidrolato y aceite esencial, (por cada litro recuperado entre aceite e hidrolato se medirá el volumen de aceite recuperado).
Los resultados obtenidos se observan en las siguientes tablas.
Tabla 1. Aceite esencial – muestra Solo Hojas
Tabla 2. Aceite esencial – muestra Tallos y Hojas
El volumen máximo de aceite recuperado por una muestra de 30 kilogramos de materia prima para ambos casos corresponde a:
- Muestra solo hojas: 244 ml.
- Muestra hojas y tallos: 232 ml.
Se puede observar que para el caso de la muestra solo hojas se recupera una cantidad mayor siendo la misma masa.
También se observa que el rendimiento a un 95% para cada experiencia se encuentra en el punto 8 en el caso de la muestra solo hojas y en el punto 4 para el caso muestra hojas y tallo. En la siguiente grafica se puede observar las curvas de extracción para ambos casos.
Es posible que los tallos permiten el paso del vapor y con ello el aceite que es arrastrado con mayor facilidad, que en el caso solo hojas, ya que este conformaría una carga compacta.
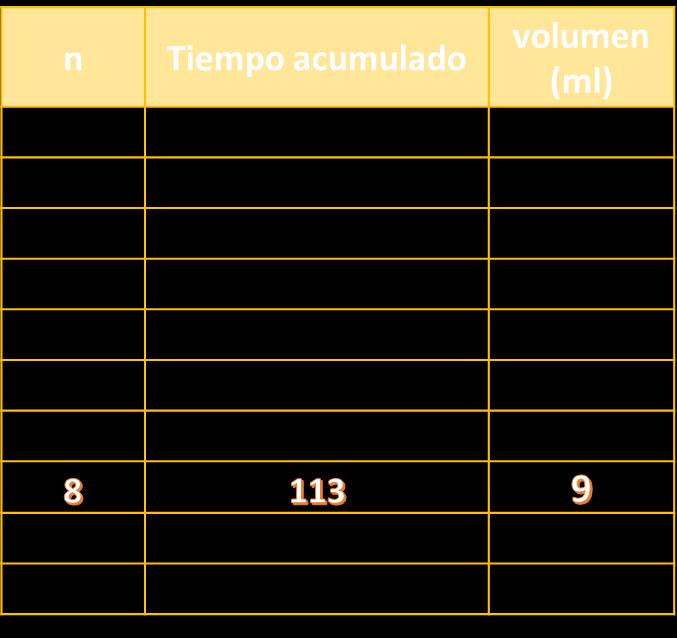
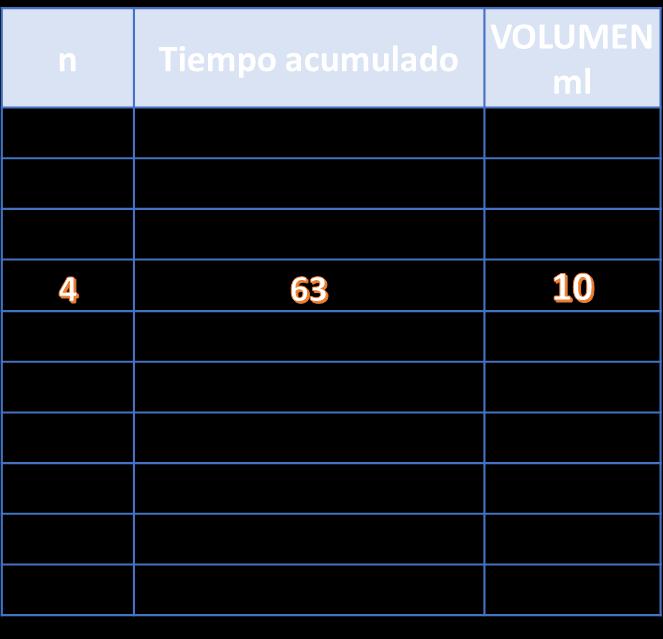
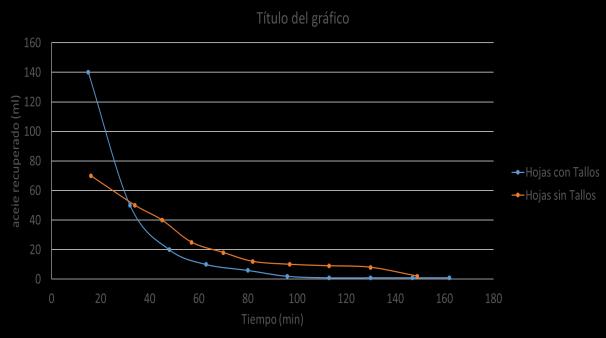
8. Bibliografía
Moreno, J., Lopez, G., & Siche, R. (2010). Modelación y optimización del proceso de extracción de aceite esencial de eucalipto (Eucalyptus globulus). Trujillo - Peru: Scientia Agropecuaria.
Nolazco Cama, D., Villanueva Quejia , E., Hatta Sakoda, B., & Tellez Monzon, L. (2020). Extracción y caracterización química del aceite esencial de Eucalipto obtenido por microondas y ultrasonido. Lima - Peru: Scielo Peru.
RESUMEN
Mg. Rodolfo Roque Perez Mendez Dra. Catalina Orfelina Rondon Saravia
El presente trabajo tiene por objeto realizar un estudio comparativo de dos tipos de fuente de energía para la operación de deshidratado de frutas específicamente manzana, plátano, fresa y piña. Para el análisis comparativo se evalúa el tiempo de deshidratación que está determinada por la masa de agua que va perdiendo cada fruta hasta llegar a ser constante. La fruta es dispuesta en rodajas y trozos con un espesor inicial de 5 mm ± 1mm, que luego de deshidratar dependiendo de la fruta alcanzan un espesor de 2 mm ± 1mm. Como resultados se obtuvo que, aplicando energía eléctrica a través de un horno, la deshidratación a una temperatura constante de 60 °C es alrededor de 8 horas, y en cuanto a la energía solar en un deshidratador solar que varía la temperatura de 16°C y alcanza la máxima temperatura de 50°C, el proceso dura 60 horas.
1. Descripción del funcionamiento del deshidratador solar
Las pruebas de deshidratación se frutos se llevaran a cabo mediante un equipo solar que utiliza la radiación solar de tipo indirecto que consta de una cámara de secado que contiene 2 bandejas de malla de polipropileno de 0.5m x 0.7m para colocar el fruto previamente laminado, además de 2 ventiladores que cumple la función de extraer un flujo de aire saturado de humedad y el otro ventilador para continuar con el ciclo de circular el aire caliente de la cámara que cuenta con un volumen de secado de 0.35 m3. El secador solar tiene un área de 1.2 m2. La capacidad del secador es aproximadamente de 2 kg de producto laminado de las muestras con un espesor que varía entre 4 y 6 mm.
2. Descripción del funcionamiento del deshidratador solar
El horno eléctrico conste en una cámara cuya calefacción es a través de resistencias eléctricas que irán conectadas a la fuente de suministro energético al momento de accionar, el equipo posee sistema conectivo, temporizador y control de temperatura. Se fabrican las bandejas debido a que el equipo no cuenta con ello, estas bandejas son marcos de inox y malla inox.
3. Acondicionamiento de la fruta a) Manzana
Para la manzana es necesario lavar la fruta con agua en una solución de hipoclorito de sodio, posterior a ello se descorazona el interior de la manzana.
Se prepara una solución de ácido cítrico con una concentración del 2%.
Se corta la manzana en láminas de aproximadamente 5 min de espesor e inmediatamente son sumergidas en la solución del ácido cítrico, de esta manera evitaremos el pardeamiento de la manzana para seguir conservando su color blanco original.
b) Piña
La piña pasa por una etapa de pelado y descorazonado, posteriormente se realiza los cortes de 5mm de espesor
c) Plátano
El plátano es pelado, y laminado a un espesor de 5mm.
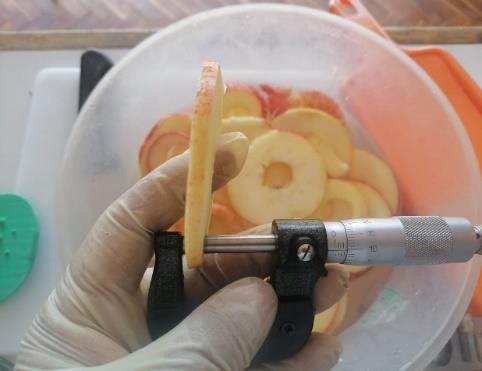
d) Fresa
La fresa es lavada en una solución de agua e hipoclorito de sodio, seguidamente se elimina la parte superior de la cabeza junto con las hojas de la fresa y se desarrolla los cortes laminados a un espesor de 5mm.
4. Deshidratación de los frutos
Los frutos son llevados a deshidratar en ambas tecnologías (energía solar y energía eléctrica) para su correspondiente análisis y recolección de datos, que servirán para construir las curvas de deshidratación para cada fruto en cada tipo de energía empleada.
a) Deshidratación en horno eléctrico

Se puede observar las curvas de deshidratación para las frutas, en el que el comportamiento de deshidratación para el plátano, piña y manzana son muy similares, a diferencia de la curva de deshidratación de la fresa, pero al final es quien alcanza mayor pérdida de agua a diferencia de las demás frutas
5. Deshidratación solar
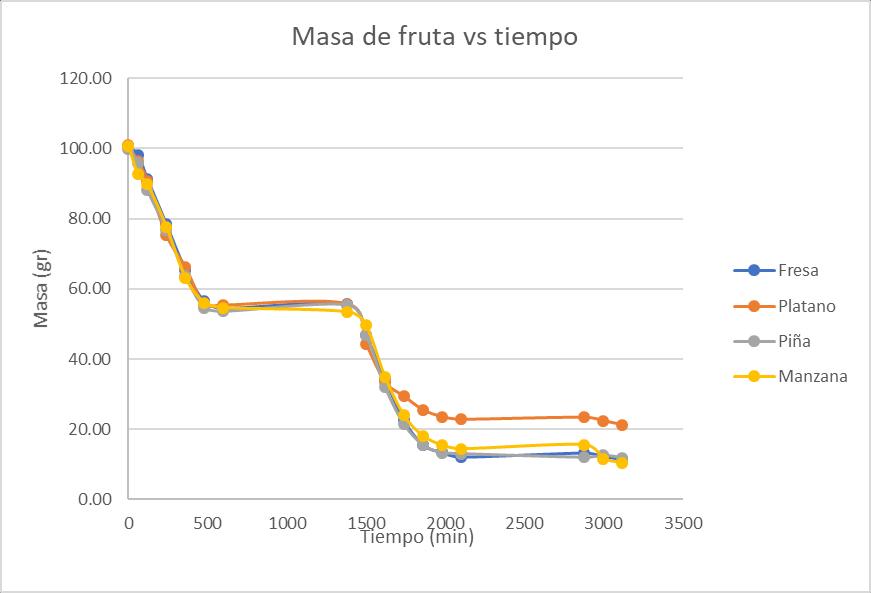
En la gráfica se observa que la manzana es quien pierde mayor cantidad de agua, a diferencia del plátano que según la gráfica se entendería que posee más componente orgánico que agua a diferencia de las demás frutas.
Al igual que todas las frutas todos alcanzan la deshidratación adecuada.

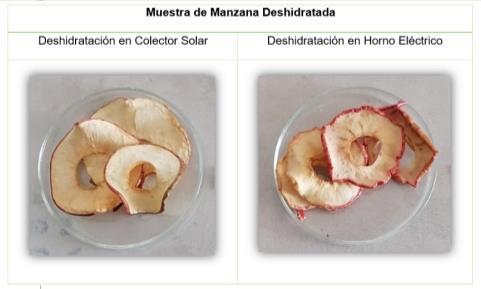
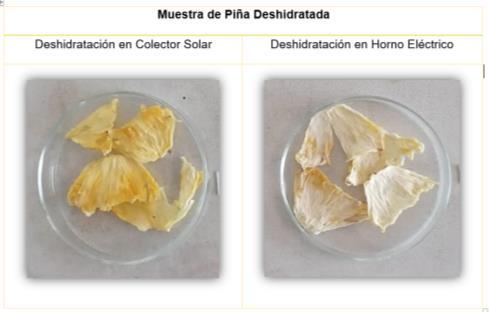
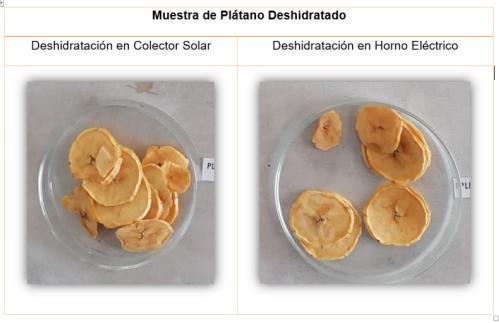
6. Conclusiones
- De acuerdo a la experiencia podemos concluir que en el horno eléctrico demanda un tiempo de deshidratación de 8 horas, mientras que para la deshidratación solar el tiempo requerido es de aproximadamente 2.5 días. - El aspecto visual en el caso de la deshidratación solar es más agradable ya que se observa que conserva colores de la fruta originaria a diferencia de la deshidratación en horno eléctrico.
ÍNDICE
Estrategia para la reducción de costos en el alambre de amarre de cobre..................................................10 Fullerenos inorganicos aditivos de extrema presion en aceites lubricantes……………………………….12 ¿Qué es la pintura en polvo electrostática?.................................................................................................15
Cálculo de los líquidos del gas natural (riqueza) del gas natural ...............................................................19
Separación por “sorting”.............................................................................................................................23 Biorremediación de suelo contaminado con hidrocarburo usando lodos estabilizados y fertilización......25
Formación de geopolimero para inmovilizar mercurio presente en residuos sólidos mineros de la región sur del Perú......................................................................................................................................29 Hacia una economía solar...........................................................................................................................32
Gestión integral de residuos sólidos mineros .............................................................................................33
Ingeniería química, energías renovables y medio ambiente.......................................................................34
Evaluación y selección de solvente isoparafínico, para extracción por solventes (sx)...............................35 diseño de reactores industriales inteligentes con gas natural......................................................................39
Fabricación de espuma flexible de poliuretano simplificando el proceso..................................................45
Eelaboración de biocombustible ecológico a partir de biomasa y residuos celulósicos………………….48 Análisis comparativo de rendimiento de extracción de aceite esencial de hojas y hojas -tallos del árbol de eucalipto .......................................................................................................................................51 Análisis comparativo entre energía eléctrica y energía solar para la obtención de frutas deshidratadas…54
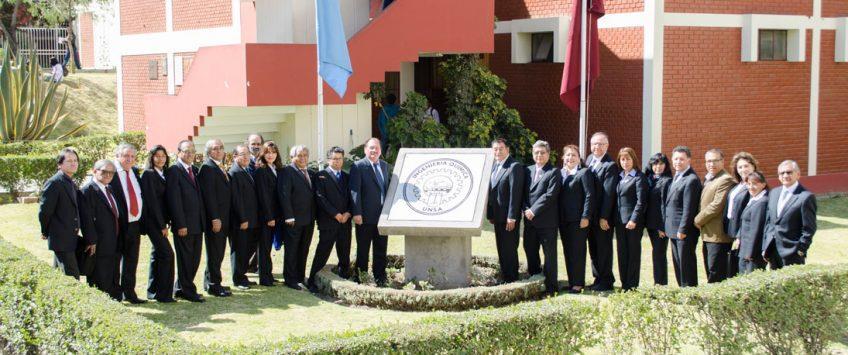