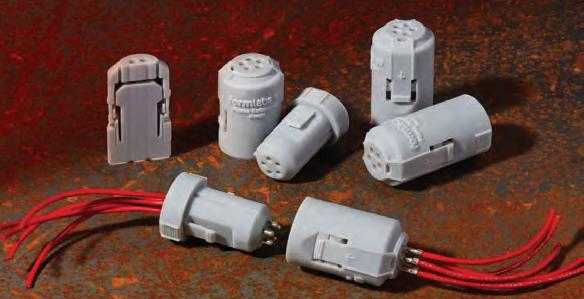
16 minute read
SAFETY IN MATERIALS
by Melissa Donovan
Filaments, powders, and resins are all integral to the creation of three-dimensional (3D) builds. As further advancements in these materials occur, their defined feature sets become integral to meet the demands of the industries using the technology. In particular, there is increased interest in flame retardant (FR) resins and powders. Most notably, aerospace; transportation—automotive, trains, boats; electronics; and even the medical field require FR materials.
“The demand for FR resins has drastically increased among industries looking to leverage in-house additive manufacturing (AM) for all steps of the production process. Many industries commonly integrate some type of 3D printing into prototyping workflows, but often have to move to traditional manufacturing methods while still in the development stage in order to comply with regulatory requirements for flammability. With FR resin, large businesses can not only improve their development timelines, but also use a common material across teams, from design to maintenance and repair operations, as well as manufacturing fixtures,” proposes Elena Austras, product marketing manager, Formlabs.
3D printing on its own offers a host of benefits, from cost efficiency and durability to faster design production. Hason Rolland, SVP of materials, Carbon, says, “adding flame retardancy to the list ensures that manufacturing, electrical, healthcare, and aerospace specialists, among others, are provided with the safest equipment and products possible.”
Keeping it Beneficial
With demand for FR resins and powders deriving from a number of industries and applications, many are poised to benefit.
“For the applications in transportation or consumer goods FR materials are necessary for safety reasons. The associated certifications are required to enable products to be sellable or to pass transportation safety regulations. This is part of the natural progression of applications moving from functional prototyping into more end-use applications, which come with increasing requirements. This is a good indication that we are progressing into more challenging areas,” notes Aric Yackly, product manager, P3, Stratasys.
According to Steven Kubiak, process engineering manager, Jabil Inc., “anywhere the benefits of additive intersect with an FR need will benefit. FR powders will benefit the same way general powders will benefit.”
“With FR resin, users easily and quickly create stiff, creep resistant, and functional plastic parts that perform well long term in high temperature environments without turning to injected molding. FR resin is ideal for producing airplane, automobile, and railway interior parts; protective and internal consumer electronics components; and custom jigs, fixtures, and replacement parts for industrial environments or ignition sources,” shares Austras.
Nirup Nagabandi, VP of materials and process engineering,
Essentium
1. Formlabs’ Flame Retardant par ts open up new opportunities for 3D printing in the transportation, aviation, manufacturing, electronics, and aerospace industries.
Inc., notes how “FR resins and powders serve as a game changer by significantly reducing the risk of fire incidents and enhancing overall safety measures.”
The 3D Process
3D printing processes like fused deposition modeling (FDM), digital light processing (DLP), stereolithography (SLA), and masked stereolithography (LCD) all use FR materials.
“Theoretically, a new process could be designed for these materials. That being said, FR resins/powders are perfectly capable of being processed with common, commercially available 3D printing processes today,” suggests Sylvia Monsheimer, head of industrial 3D printing, Evonik.
In Yackly’s experience, FR materials are developed for both thermoplastic and photopolymer thermosets and are becoming available on an increasing range of systems, with FDM and DLP as the leading technologies.
“All printing processes produce parts in FR material, but the amount and type of additive or modifier to the polymer will depend on the process,” explains Kubiak.
Photocentric Inc. started testing its FR resin on some UV DLP and LCDbased systems to fully validate it.
Formlabs’ FR resin is compatible with SLA printers. “For many industries, maintenance and repair parts have to be ordered to ensure the product remains compliant. SLA 3D printing was not traditionally a viable option, despite its low cost per part and efficiency. With FR resin, SLA 3D printing can finally be deployed as an on demand repair part manufacturing solution,” shares Austras.
According to the company, Essentium Duratem can be used with any open eco-system high-temperature 3D printing machine, including the Essentium High-Speed Extrusion 180 HT and HSE 280i HT 3D printing platforms.
Carbon EPX 86FR works best on Carbon DLS printers, such as the M2, M3, M3 Max, and L1.
Get Certified
Standards are in place to certify whether a resin or powder is FR.
Certification depends on the industry and application. For example, FR materials used in consumer electronics are certified by the Underwriters Laboratories (UL), whereas FR grades for aerospace applications require testing to a different burn standard and are certified in conjunction with the aircraft manufacturer in question and the FAA, shares Kubiak.
UL 94 is a plastics flammability standard released by the UL. “One common standard for assessing plastics flammability is UL 94. There are varying degrees of FR that get assessed by the orientation of the part in the flame, the thickness it will pass the test at, burn rate, and whether or not it will drip flammable plastic drops or not,” explains Yackly.
Another standard to comply with is the FAR 25.853(a) regulation. Carbon
EPX 86FR achieves a 12 second burn compliance for a thickness of one millimeter. It is also accredited for UL 94 rating at a two millimeter thickness.
Formlabs’ FR resin is halogen-free, UL 94 and FAR 25.853(a) certified with favorable flame, smoke, and toxicity (FST) ratings. FR resin produces 3D printed parts that meet necessary certification requirements for enduring hazardous environments, according to the company.
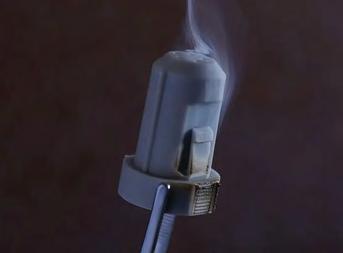
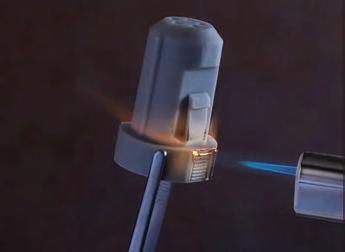
“Our FR materials undergo rigorous testing and certification processes to ensure their FR properties. Essentium’s certificate of conformance provides individual spool traceability through the ISO and AS9100 quality process. Essentium is working with customers, including the U.S. Air Force, to certify materials for uniform, repeatable, and reliable part production. These certifications validate the flame retardancy of our materials, providing confidence to our customers in their safety performance,” explains Nagabandi.
Pricing Structure
FR resins and powders cost more. However, the applications that deem flame retardancy as a critical feature make it so the purpose outweighs the cost.
Development can be challenging, which increases pricing. “The development cost of the material itself needs to be recaptured, and assuring FR performance out of printed parts is a challenging technical problem,” explains Kubiak.
Manufacturing a FR resin or powder can be more complicated, which effects cost. “Various additives must be integrated into the material, requiring additional process steps,” says Kubiak.
“Typically FR materials carry a premium over standard materials due to the additional cost of additives as well as the development cost to create and process 3D printable materials that have the right mix of temperature, mechanical, and FR performance,” agrees Yackly.
Continued quality control, to ensure the customer that the additive will perform as expected-in this case with FR properities,alsoenhancesthecostoftheseresins and powders,according toMonsheimer.
The investment incurred to test and certify an FR material also means the enduserpaysmore,accordingto Kubiak.
Despite the high costs for FR materials, a representative from Photocentric notes thatthe pricing is nodifferentthan other engineering grades of materials. Further noting the desire "to make AM accessible and applicable to all."
Also, when comparing AM to traditional manufacturing process like injection molding, FR materials are less expensive. "FR resin unlocks design freedom to create isotropic and highly detailed parts with an excellent surface finish that have the look and feel of injection molded parts but at much lower cost. It also helps to accelerate time to market without the design constraints and high costs of its injection molding or casting counterparts," notes Austras.
"The investment in FR materials is justified by the significant risk reduction and enhanced safety they offer, which outweighs the incremental cost," notes Nagabandi.
FR Future
It is because of the higher costs and need for certification that Kubiak believes all resins and powders will not be FR in the future.
the basic horizontal burn tests, but as far as the more stringent FR requirements products will be targeted to an application. In the future I expect many more materials to be aligned to increasingly specific applications with their own set ofrequirements."
''While certain industries rely on FR resins to meet strict production regulations, not all AM printing processes and materials require or are conducive to the same characteristics held by this type of resin;' addsAustras.
Keeping in mind that demand for FR materials may grow; Nagabandi suggests "a widerrangeofresinsand powders may have FR propertiesin the future:'
"The next generation of resins and powders will build upon recent software models and I expect that flame resistance will remain a top priority for developers," adds Rolland.
Product Roundup
Carbon EPX 86FR is a photopolymer resin that offers a combination of FR, functional toughness, high strength, and long-term stability. It features dual cure chemistry, utilizing a print and bake process.
Evonik offers INFINAM R TPC, an elastomeric copolyester that exhibits excellent flexibility, durability, and resistance to abrasion, chemicals, and UVradiation-in addition to being FR.
range of applications, from aerospace parts to maintenance uses such as replacing clamping blocks and switch covers.It is also ideal forrailwaycomponents,including ventilators and covers.
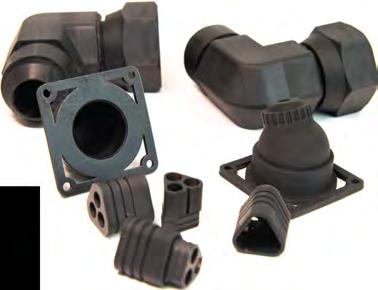
At RAPID + TCT 2023, Formlabs introduced its Flame Retardant Resin, which is its first UL 94 certified resin and first self-extinguishing material. Formlabs is looking forward to expanding its portfolio of FR certified-resins to broaden printing capabilities for the many industries that rely on durable components that can withstand high temperature environments.
Jabil's FR additive polymer currently is the PC 1500 FR, which is an FR polycarbonate filament. Made from UL V-0 YellowCardcertifiedrawmaterials,Jabil's PC 1500FRcanbeprintedondirectdrive and bowden tube 3D printers. This material, with its FR properties, is used in the aerospace and automotive industries.
Photocentric was planning to announce a newFRmaterialat presstime.
Similar to what occurred in the injection molded plastics world, Yackly also doesn't see all resins and powders being FR nor passing all FR tests. "Many 3D
Essentium Duratem,one ofthe company's newest materials, can withstand temperatures of 150° C and is resistant to FST and passed FAR 25.853 FST printing materials today already pass testing. The material is suitable for a
Companies Mentioned
Seepage12formoreinformation.
AtStratasyssomeofitsmoreadvanced FR/FST materials are Loctite 3D 3955 FST, KimyaPC-FR, AddigyPA6/66-GF20 FR LS,andUltem 9085 resin.
FR Materials
The introduction of FR resins and powders in 3D printing means users who relied oninjectionmolding for manyoftheir buildsnolongerhavetoimplementthatas part of the process. In turn, more industries are introduced to the advantages of AM. Meeting requirements like flame retardancy for specificapplications is a sign that AM ismaturing as an industry. /PM
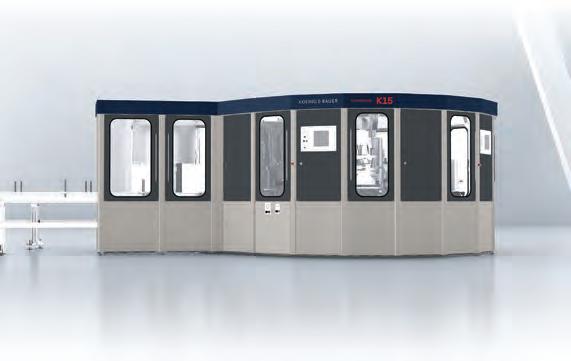
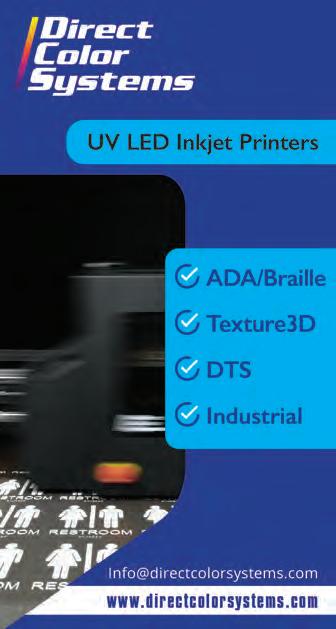
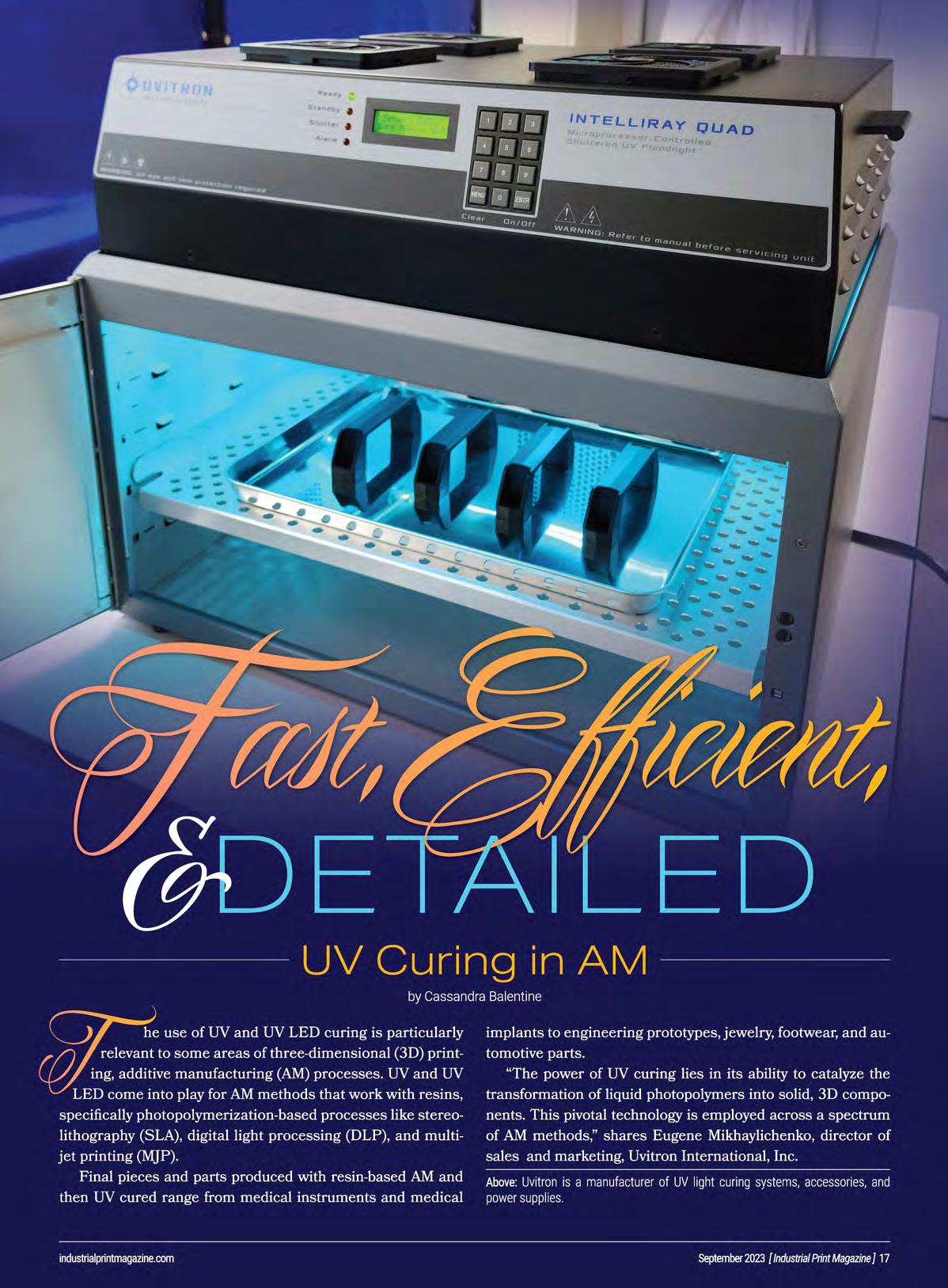
Stacy Hoge, marketing communications manager, Phoseon Technology, points out that UV LED curing presents a stable process that increases the strength, durability, and chemical resistance of 3D/AM printed parts on a commercial scale. “Reliable UV LED curing equipment benefits the 3D printing industry by providing fast, consistent, and reliable curing every time.”
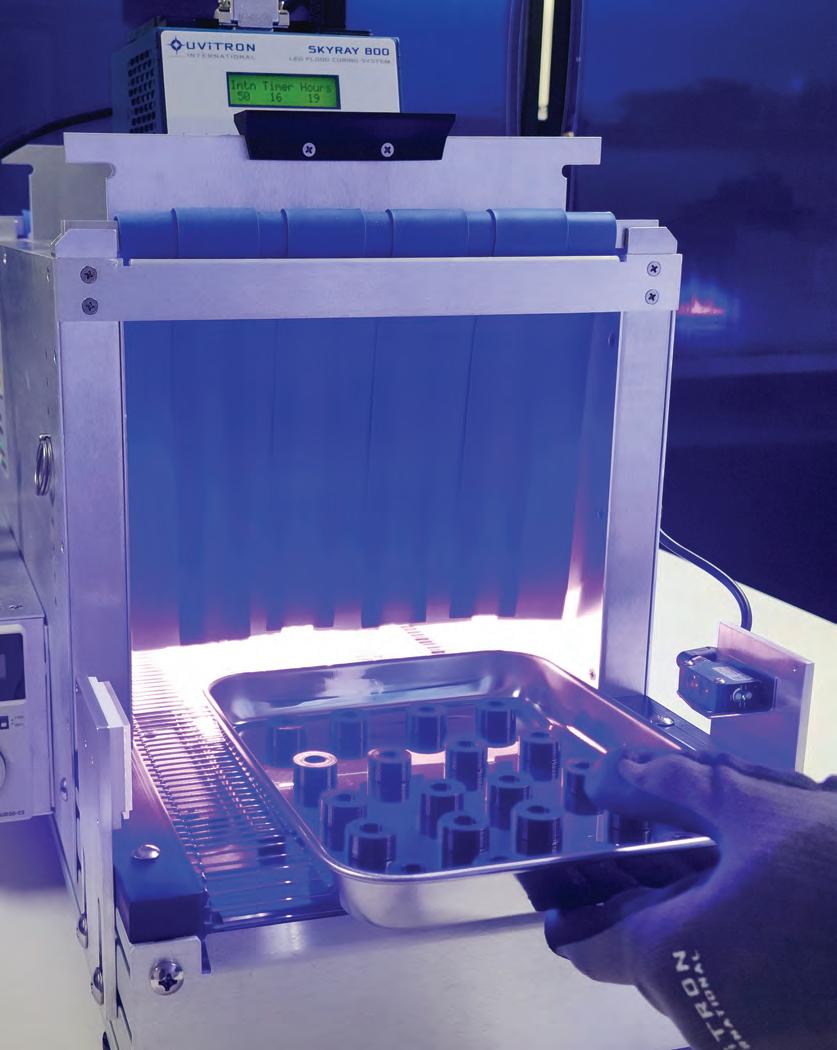
UV curing in AM offers high reaction rate; small footprint—especially UV LED; low emissions as formulations are 100 percent reactive; unique performance properties like toughness; process flexibility and consistency; higher first time quality as the product can be handled immediately after forming; as well as less waste,” according to Colin Bergs, technical sales engineer, AMS Spectral UV, a Baldwin Company.
UV curing proves its merits in many ways. “Primarily, the materials that are UVcurable bring to the table superior mechanical properties. They span an impressive spectrum, offering everything from extreme flexibility to lasting durability, effectively imitating materials as diverse as rubber and glass,” explains Mikhaylichenko.
This type of versatility opens the door to additional applications, ranging from the creation of prototypes to the production of parts meant for end use.
Another attribute of UV curing is its exceptional speed and efficiency. “In an industry where each tick of the clock represents potential profits, the rapid curing times offered by UV light significantly expedite production timelines and cut down on costs,” notes Mikhaylichenko.
Along with speed, Mikhaylichenko says UV curing also ensures precision and sustainability. “It facilitates layerby-layer curing, providing the ability to create complex geometries, intricate details, and internal features that are difficult to achieve with conventional manufacturing techniques. Moreover, UV curing contributes to the ‘green’ revolution in AM. By utilizing just the right amount of material, it minimizes waste, and the materials it employs are frequently more eco-friendly compared to those used in other manufacturing methods.”
UV Curing Process in AM
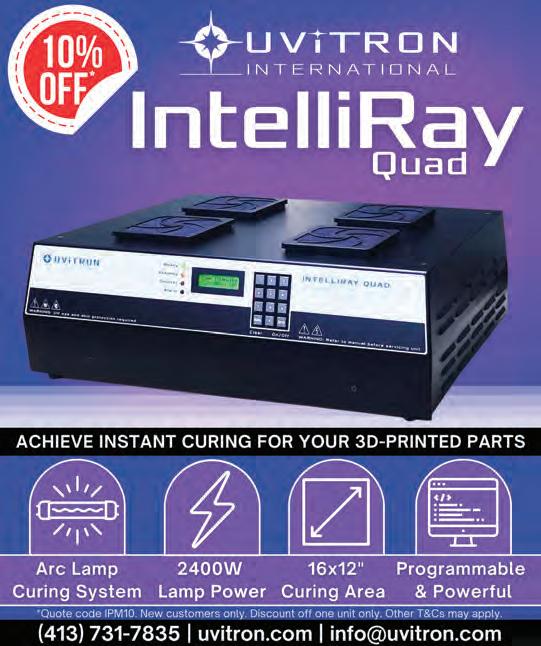
UV curing in AM generally begins with a digital design of the object, which is usually created with 3D modeling software. “This design is then sliced into very thin layers by a specialized software program, preparing it for the AM process,” explains Mikhaylichenko.
Depending on the specific AM method used, steps typically include a layerby-layer construction, UV curing, and post processing.
The process starts in a UV-curable resin tank and the 3D printer constructs the object layer by layer. This is followed by UV curing. “The key role of UV curing in this process is to harden or cure the UV-reactive resin. When exposed to UV light, the resin undergoes a chemical reaction known as photopolymerization,” explains Mikhaylichenko.
Following the completion of the printing process, Mikhaylichenko says it’s often necessary for the printed object to undergo further treatments. “This might include steps such as cleaning of uncured material residue, an additional UV curing stage to improve hardening and reduce surface tack, and occasionally some finalizing procedures to ensure the object’s surface is sleek and immaculate.”
Bergs adds that each layer of 3D printed material is cured with UV light absorbed by photoinitiators (PIs), which are formulated to match the required peak wavelength to cure the product instantly. “The outcome is a product that is ready to use and does not require a secondary cure.”
“AM processes that require a long printing cycle or use heat-sensitive materials benefit the most from UV LED curing,” comments Hoge.
Mikhaylichenko points out that for SLA, UV curing systems create objects by focusing a UV laser onto a vat of photopolymer resin. As the laser traces a pre-defined design, the photopolymer hardens, building the object layer by layer. “Post-processing UV curing systems play a crucial role in solidifying these intricate designs and adding a polished finish,” he shares.
When it comes to DLP, it follows a similar path to SLA, but with a digital projector screen to expose the entire layer of resin at once, rather than a UV laser tracing the design. “This simultaneous exposure and curing by UV light expedites the process, and postprocessing UV curing systems are instrumental in enhancing the speed and efficiency of this method,” notes Mikhaylichenko.
MJP jets photopolymer materials onto a build platform, which are immediately cured by UV light to solidify them. This method is renowned for its high resolution, precision, and ability to print in multiple materials and colors simultaneously. “UV curing systems here in the post-processing stage ensure that high standards of precision are maintained while offering a tack-free and smooth finish to the printed objects,” adds Mikhaylichenko.
Material jetting is a popular technology used for 3D printing, which can be UV cured. “PolyJet belongs to the family of material jetting AM processes. The PolyJet 3D printer sprays photo-sensitive resin material layer by layer onto the print tray until the parts are completed. Each layer of material is cured with UV light while being sprayed and can be taken out and used immediately without secondary curing. It can realize the combination of color and multi-materials in a single printing to produce a prototype close to the real product. It is also used to print quick molds and verify product designs. Full color, multi-material 3D printers can mix six materials at the same time to achieve 500,000 colors, different textures, transparency, and softness. Products are widely used in medicine, education, and engineering models,” shares Hoge.
Each of these processes benefit from UV curing, not only because of the high resolution, fine detail, and smooth surface finish that can be achieved, but also due to the variety of materials utilized and the rapid production times possible, according to Mikhaylichenko.
With a reliable UV LED light source, Hoge says customers can run a stable process for a long time, with some printing cycles reaching over 48 hours. The UV LED printing process offers the highest efficiency, printing accuracy, and most yield to fulfill the end customer’s stringent requirements. LED technology allows users to cure heat-sensitive materials offering new revenue opportunities for printers.
“The final outcome of this process is a 3D object created from a digital design, exhibiting high resolution and detail. The object can be as strong and durable as the UV-curable material allows,” shares Mikhaylichenko. “This gives UV curing a significant advantage over other 3D printing technologies as it can produce parts that are not just prototypes but are also strong enough for end-use applications in various industries.”
Material Considerations
The use of UV curing in AM is recognized for resin-based processes.
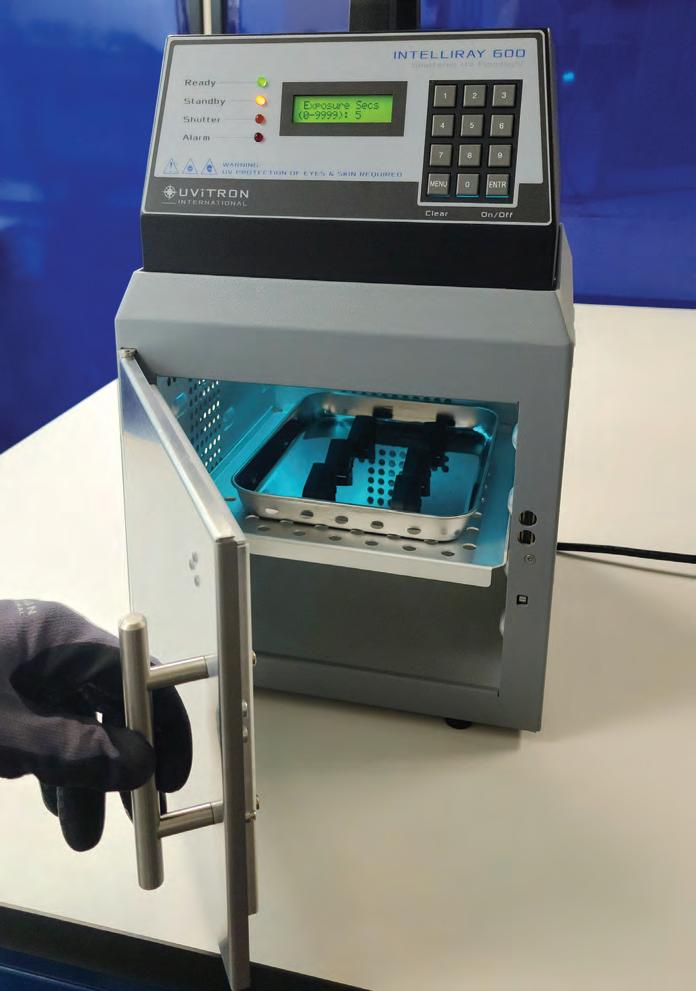
Bergs points out that formulations that can be UV cured must be specifically created to do so. “There is a specific chemical class of PIs that absorb UV energy and then transform to a compound that is highly reactive to start the polymerization process.”
Therefore, Bergs explains that UV curing in AM works very well with resins, which aid in enhancing the material properties. “Through the use of UV curing, AM processes are quicker with higher quality product as a final result.”
For the most part, Hoge says LED cured AM materials are acrylate-based, which is the same as what is seen in inks, adhesives, and coatings—i.e. monomers, oligomers, and PIs. “It is likely that some
3D printers are using other atypical chemistries with LED high UVA wavelength energy to cure,” she notes.
In addition to photopolymer, other substances are tailored to respond to UV light. UV-curable inks, coatings, and adhesives are common examples that are employed across various industries. “These substances contain PIs—compounds that react to UV light to trigger hardening or curing. In the realm of AM, efforts are underway to widen the array of UV-curable materials, beyond just photopolymer resins,” says Mikhaylichenko.
UV and UV LED Trends in AM
Experts expect an increase in use of UV curing within certain AM technologies.
Hoge specifically sees growth with UV LED curing technology because it offers a consistent, reliable process that runs on a wide range of heat-sensitive materials for a long period of time.
Bergs predicts growth will come as companies try to move away from conventional UV, which is not as energy efficient as UV LED. “As more formulators make products with LED UV curing capability the market use will increase significantly. LED UV is the future for sustainable curing in almost every industry that uses UV in their processes.”
A primary driving force is the continuous advancement in UV curing and AM technologies. “The constant innovation we are observing in UV light sources, photopolymers, and 3D printing hardware and software ensures a bright future for this sector. As these technologies mature, they create an effective synergy, further enhancing the efficiency and capabilities of UV-cured AM,” comments Mikhaylichenko.
Another compelling factor is the increasing adoption of AM across an array of industries. “Whether it’s aerospace or healthcare, automotive or consumer goods, companies leverage AM for rapid prototyping, customization, and in some areas such as the dental industry, even large-scale production. As more sectors uncover the unique benefits of UV-cured 3D printing— namely, high resolution, superb mechanical properties, and rapid production times—we see continued growth in the demand for UV curing within AM,” states Mikhaylichenko.
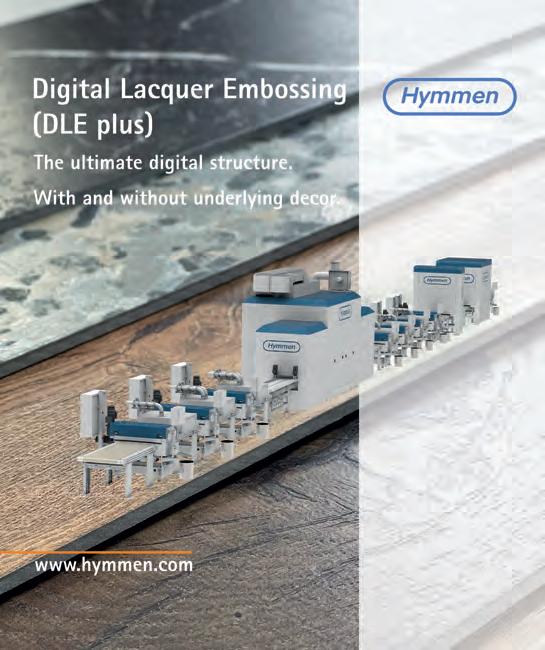
Further, he says the emphasis on sustainability in the manufacturing industry also contributes to this upward trend. UV-cured AM presents a “greener” alternative to traditional manufacturing methods, minimizing waste through efficient material usage and reducing the carbon footprint by consuming less energy. As the shift towards environmentally friendly manufacturing solutions gains momentum with more countries introducing expanding environmental regulations, UV-cured AM is likely to generate increasing attention.
Mikhaylichenko believes the recent COVID-19 pandemic with its supply chain issues underscored the value of AM in fulfilling urgent, large-scale requirements, such as the production of medical equipment and personal protective gear. “This realization may result in more industries incorporating AM as a dependable contingency strategy, thereby broadening the scope for UV curing applications.”
Advantages to AM
UV and UV LED curing bring certain benefits to AM, including faster print speeds, increased durability, consistent curing over time, and reduced environmental impact compared to traditional methods, lists Hoge.
Mikhaylichenko says in its work specializing in the post-processing stage of AM, Uvitron found UV curing systems to be instrumental in enhancing the quality and efficiency of the final product. A few key advantages he’s observed include speed and efficiency, exceptional detail, versatility and robustness, and sustainability.
In terms of speed, UV curing systems rapidly solidify each layer of the product, thereby significantly reducing production times. This increase in speed allows companies to expedite their production cycles, enhancing overall productivity and reducing the time-to-market of their products, according to Mikhaylichenko.
When it comes to detail, Mikhaylichenko feels that the advantage of UV curing systems lies in their capacity to yield high-detail results. "They allow for the creation ofintricatedesigns and complex geometries, whichmightbedifficult or even impossible to achieve with other manufacturing methods."
Versatility comes with the ability of UV curing systems to be employed with a wide and continuously expanding array of UV-curable materials. It enables the creation of easily customized products with varying properties, rendering UV curing relevant across a range ofindustries, according to Mikhaylichenko.
And for sustainability, UV curing systems contribute to a more environmentally conscious manufacturing process. They efficiently utilize materials, curing only what's necessary, and typically consume less energy than other techniques. "This aspect can help reduce the overall environmental impact ofthe manufacturing process," says Mikhaylichenko.
Future of UV and AM
The future is bright for 3D printing and AM, and UV is along for the ride.
''As more research and development is done to push the performance of UVcured resins, the future will offer the ability to print on a wider range of materials and substrates enabling new applications," predicts Hoge.
Mikhaylichenko anticipates several developments that will influence its specializationinthepost-processingstageof AM. "Firstly, we foresee a wider range of UV-curable materials. Today, photopolymer resins are primarily used, but ongoingresearchaimstobringUV-curableceramics,composites,andevenmetalsinto the fold. This progression would expand the scope of UV-cured AM, paving the way for more diverse end products and broaderindustrialapplications."
Mikhaylichenko also foreseesimprovementsinUVlight sources, which are crucial for postcuring. Forinstance,LED technology advancements offer lower energy consumption and extended operational life, promising to significantly improve UV curing efficiency. "More precisecontrol over wavelengthandintensity couldalsounlockanewlevelofcuringprecisionandexpandmaterialoptions:'
3. Phoseon air-cooled UV LED curing light sources offer a high performance, consistent, and reliable solution for AM processes. 4. AMS Spectral UV offers many custom solutions for customers' specific needs and is supported in the field by a great service department to complement quality systems. AMS Spectral UV products are manufactured in River Falls, WI.
The fusion of UV curing with other emerging technologies is another exciting prospect. "Integrating artificial intelligence and machine learning, for example, could optimize the curing process, reducingerrorsandenhancingefficiency. Pairing UV curing with 3D scanning technologies may also facilitate real-time monitoringandqualitycontrolduringthe AMprocess;' commentsMikhaylichenko.
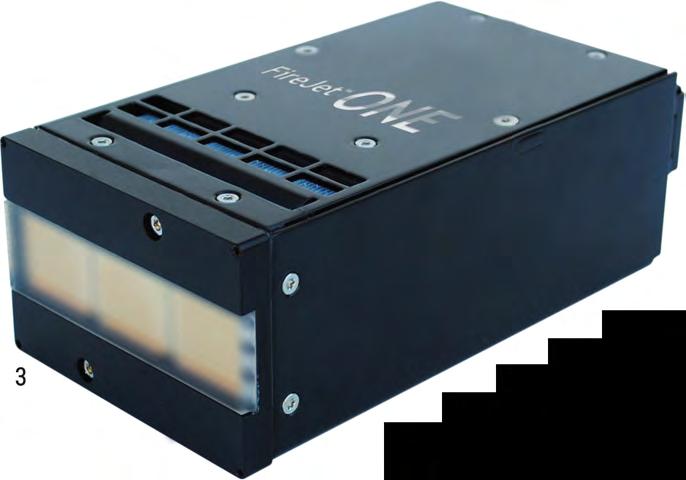
Lastly, the exploration of functional UV-curable materials holds immense potential. "The incorporation of additives or nanoparticles into UV-curable formulations could introduce specific properties like conductivity, thermal resistance, or antimicrobial characteristics. Such advancements would open new opportunities for producing electronic components, heat-resistant parts, or even biomedical devices through UV curing," shares Mikhaylichenko.
"With more industries utilizing this technology there will be an even larger demand for UV curing," advises Bergs.
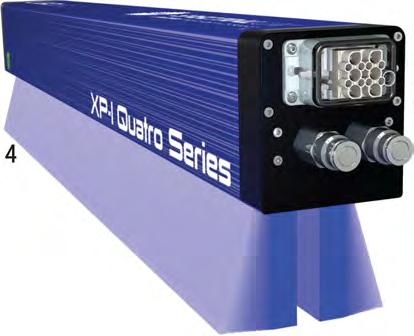
Expanding UV
UV-curablematerialsareutilizedinresinbased processes, most commonly SLA, DLP,andMJP.TheuseofUV andUV curingisexpectedtoexpandintothefuture.
"Inoureffortstodriveinnovationinthe AM industry, we arefocused on exploring andexpandingthe possibilitiesofUVcuring;' says Mikhaylichenko. "Integrating these technologies is keytoreachingnew avenuesforfastprototypingandmasscustomizationacross various sectors such as automotive, aerospace, healthcare, and consumer goods. As we move ahead, our commitment is to deliver reliable and efficient UV curing systems that fuel the futureofAM." /PM