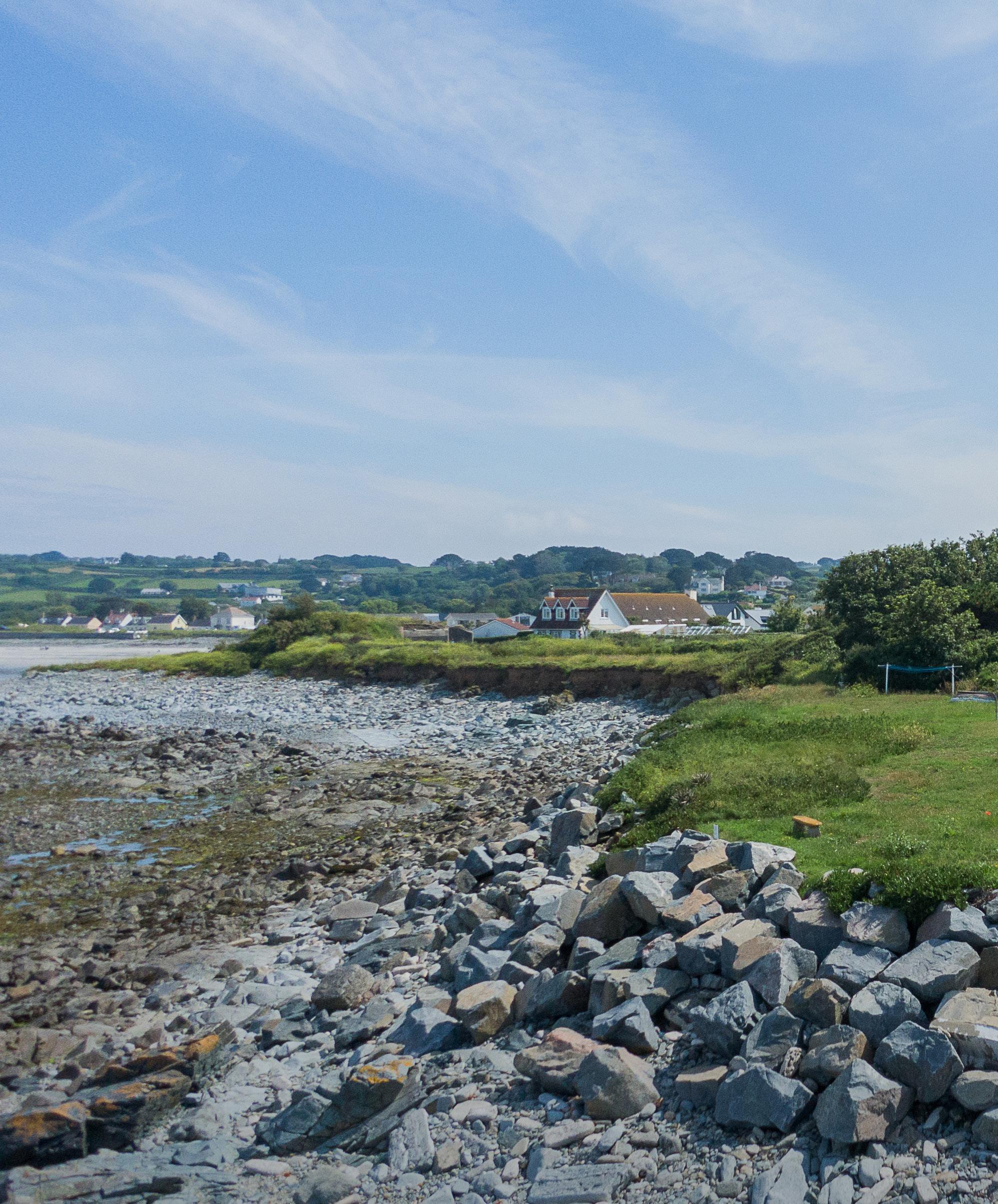
11 minute read
Fort Le Crocq
Perched on a headland on Guernsey’s west coast, Fort Le Crocq has an enviable location. It is also a house with a history – the fort itself was built after 1832 but had been largely demolished. The current house was built on the site in the 1940s, and has a look and feel that the new owners wanted to retain. The challenge for those involved with the project was to create a home that retains the essence of the original structure, while ensuring it is suitable for the requirements of modern living.
When the house owners first approached Peter Falla, founder of design practice PF+A, about Fort Le Crocq, he was expecting them to tell him they wanted to knock it down and rebuild a much larger modern house in its place. Instead, they were clear that they loved the existing house and wanted to retain the core of the building and extend it.
Advertisement
“They originally planned to keep the house at ground floor level, but I said that I felt it should have a first floor element,” said Peter.
“We therefore positioned the top floor element on top of the existing flat roof building which meant we had a lot of freedom to change the ground floor layout and the entrance to the house.

“It made sense to extend the master bedroom on the top floor, and then add a bedroom wing on to the ground floor. Once we started sketching our ideas for the house it all fell into place quite quickly and the clients loved it. Interestingly, some of their most specific requirements centred on the substantial garage space which they wanted built with a link through to the main house.”
With the plans drawn up, planning permission was acquired relatively quickly and easily. For a site of such value, the house is relatively modest in size – albeit with high specifications for everything from glazing to fixtures and fittings. “It is designed to be very specific to the owners and what they value so there was no need to try to put an oversized luxury dwelling on the site as the original house and the location were their priority,” added Peter.
Once the initial plans had been completed by Peter and his team, responsibility for the project moved to technical specialist at PF+A, Tom Bourgaize, and the technical team. For Tom, it has been a technically demanding job that required precise attention to detail.
“We first modelled the house in 3D so that we could co-ordinate all the other elements of the design,” said Tom. “The new building is comprised of a steel structure that sits on top of the existing building. That had to be designed by engineers and co-ordinated by us, and then the whole thing was ordered from the drawings. The steel was prepared in a factory with every steel beam cut to the correct length and drilled. That process took around 12 weeks, but meant that it would only take two weeks to erect on site once it arrived in Guernsey.”
On site, PF+A have been in constant liaison with the main contractors on the project, Rihoy & Son. Rihoy’s construction director, Dave Tostevin, has been the man in charge of the project from the start. Rihoy’s first
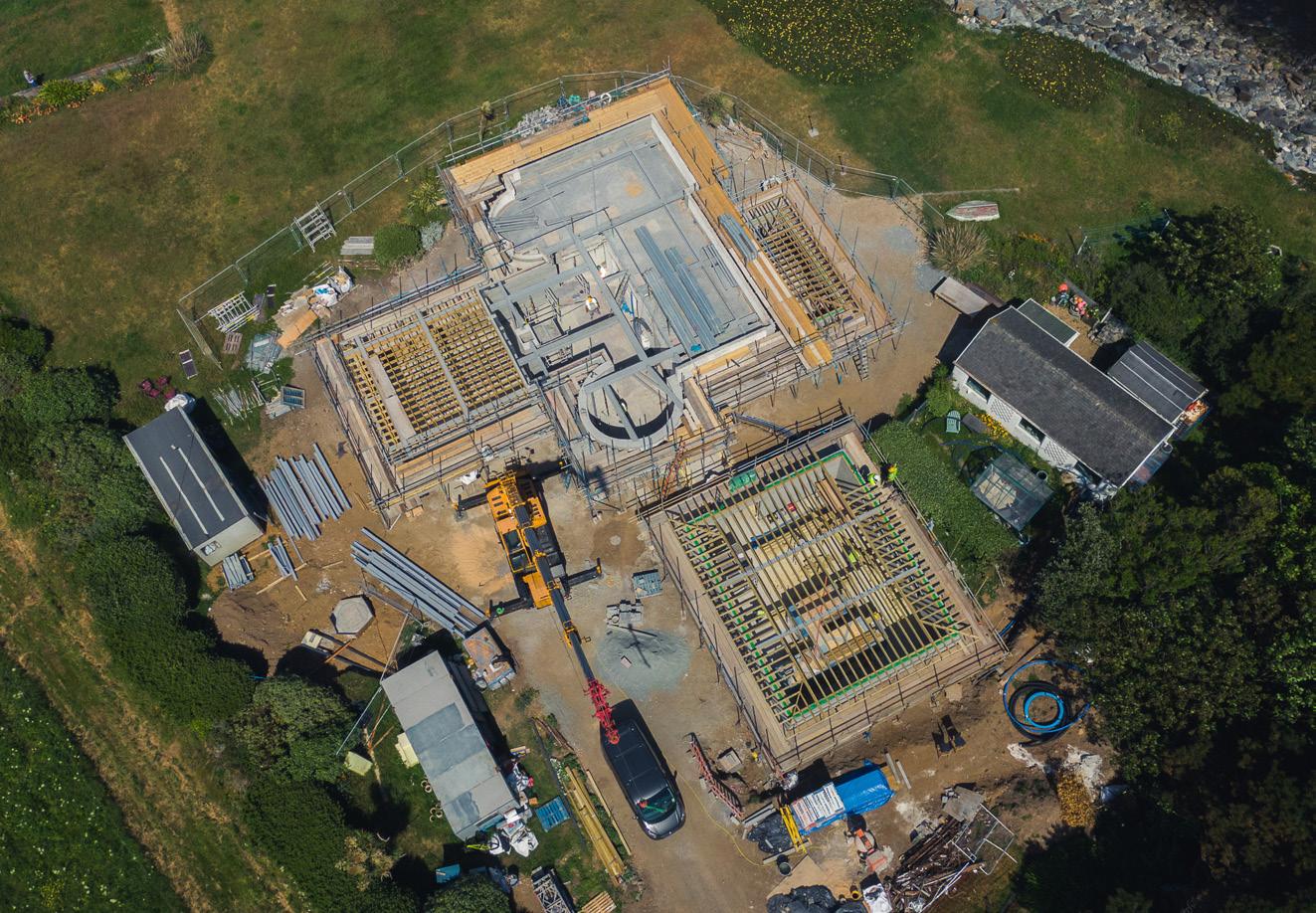
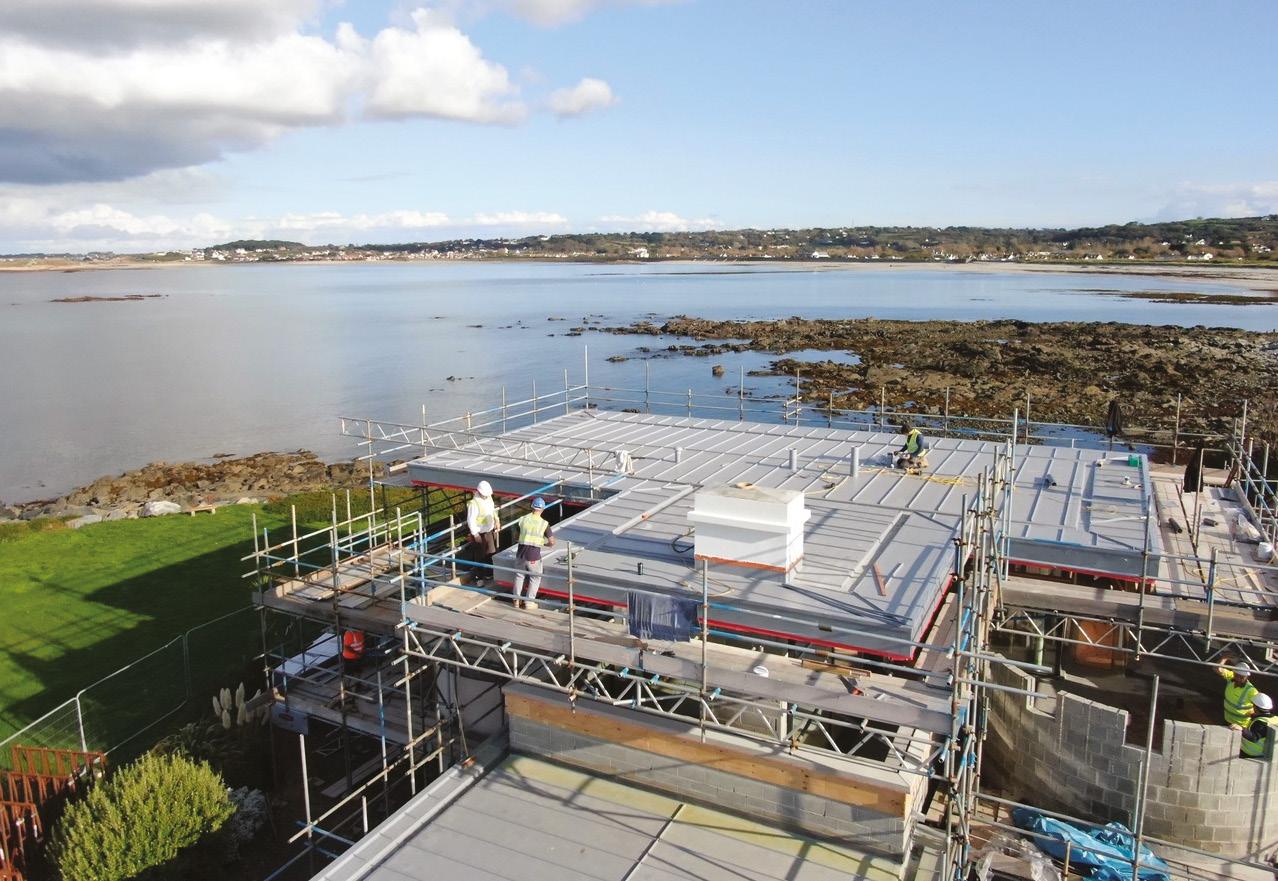
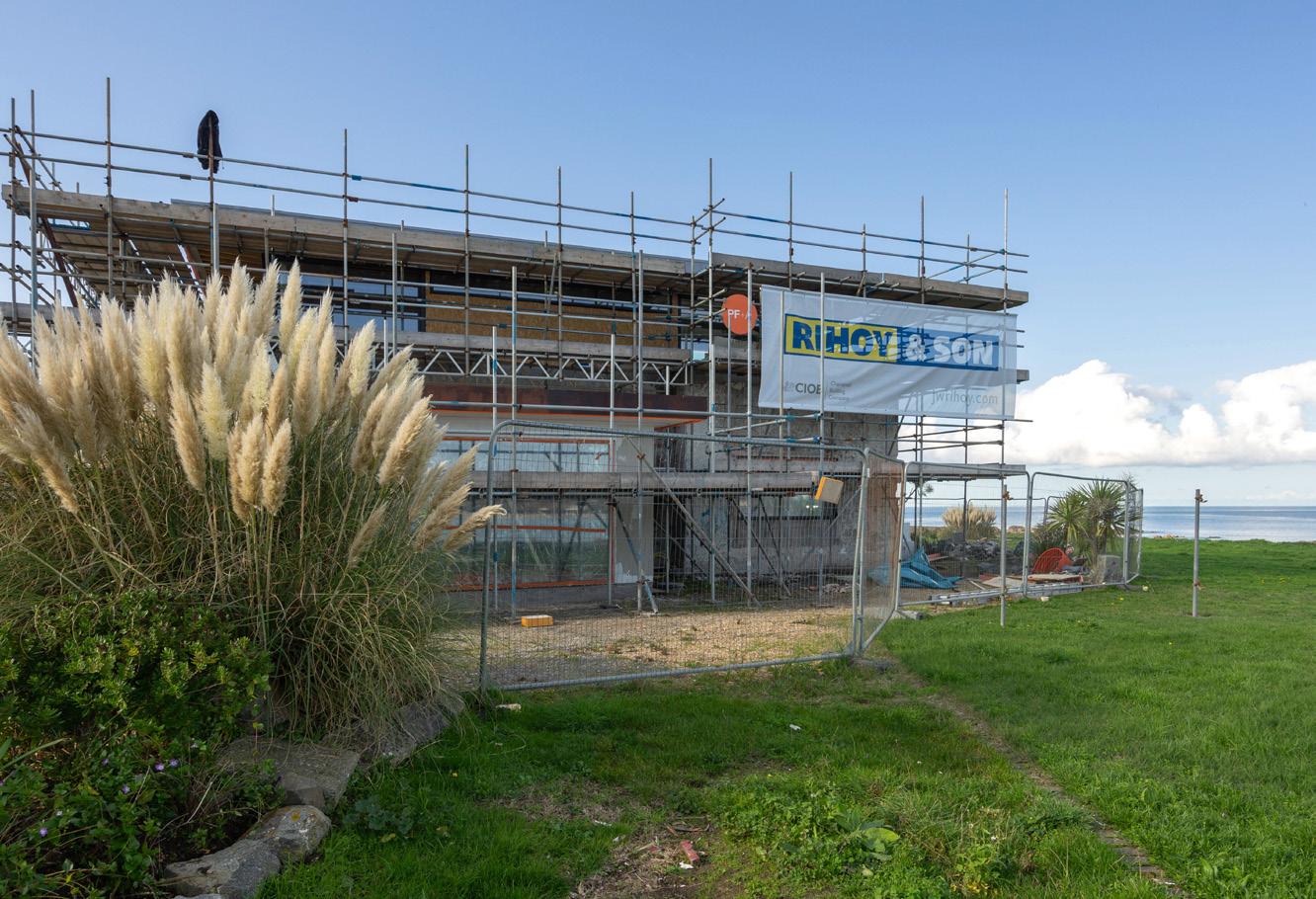
involvement with Fort Le Crocq was a separate contract to strip out the existing house and prepare it for the building work before they returned for the main project.
Once on site, their first task was to lay the foundations for the new extensions to the house, which they wanted to do as quickly as possible to take advantage of the fine weather. Once that base was in, it allowed many of the other trades to come on site to play their roles in the build, such as the blockwork for the new garage. But the project didn’t come without its problems.
“When we first started the build we were expecting the existing house to have thick, solid walls – but it was actually cavity built and in far worse condition than we were expecting,” said Dave. “When we opened the house up and started demolishing certain sections, we found various issues. All the wall ties, for example, had completely corroded with the coastal climate and had to be replaced.”
Not only did the old building have to be strengthened, but new openings had to be created that could be supported by the structure. A large picture window in the kitchen had been added to take advantage of the scenic view, which entailed demolishing and rebuilding that area of the house. New concrete bases had to be formed to hold the new steel structure so sections of the building had to be cut out to allow for that.
Once the first section of steel had been installed, the builders needed to focus on creating a new concrete floor above the existing roof of the main building, as they were unsure that the previous roof could take the weight necessary. The design entailed all weight going on to the new roof, allowing them to take the second layer of steel up on to the first floor. This meant that work could start on the master bedroom and en-suite bathroom that take up the majority of that new space. The new build has retained most of the old structure, with the new additions built through and around it. All steel stanchions and posts have been put in from the existing ground floor and through the concrete. Dave admits that it would have been easier from a building perspective to knock the house down and start again, but Tom is adamant that that wasn’t the answer for this project – and that it shouldn’t be for many others.
“We had said to the client at the start of the project that we could knock the existing house down and start again, but that’s not the principle we are working to with this. It is a far more sustainable approach to avoid demolition and work with the existing building. If you knock it down, there is a lot of energy that has been lost alongside the history of the building. We think more sustainability should be more encouraged in the building industry, even if it has been a challenge to retain the old foundations and walls for the new building.”
The curves and design of the original building may have been part of the appeal for the owners, but they have certainly posed a challenge for the contractors. When the render was removed from the arched windows in the turret, for example, the structure was in very poor condition. But with all the arches and curves required to remain in the design, the builders had to work with the original features.
“All the curves were definitely one of the most complicated parts of the build,” said Dave. “None of them were uniform which makes it very tricky. Everything we’ve built in the house is uniform and perfectly circular, so hopefully we’ve made it easier for anyone working on the house in the future.”
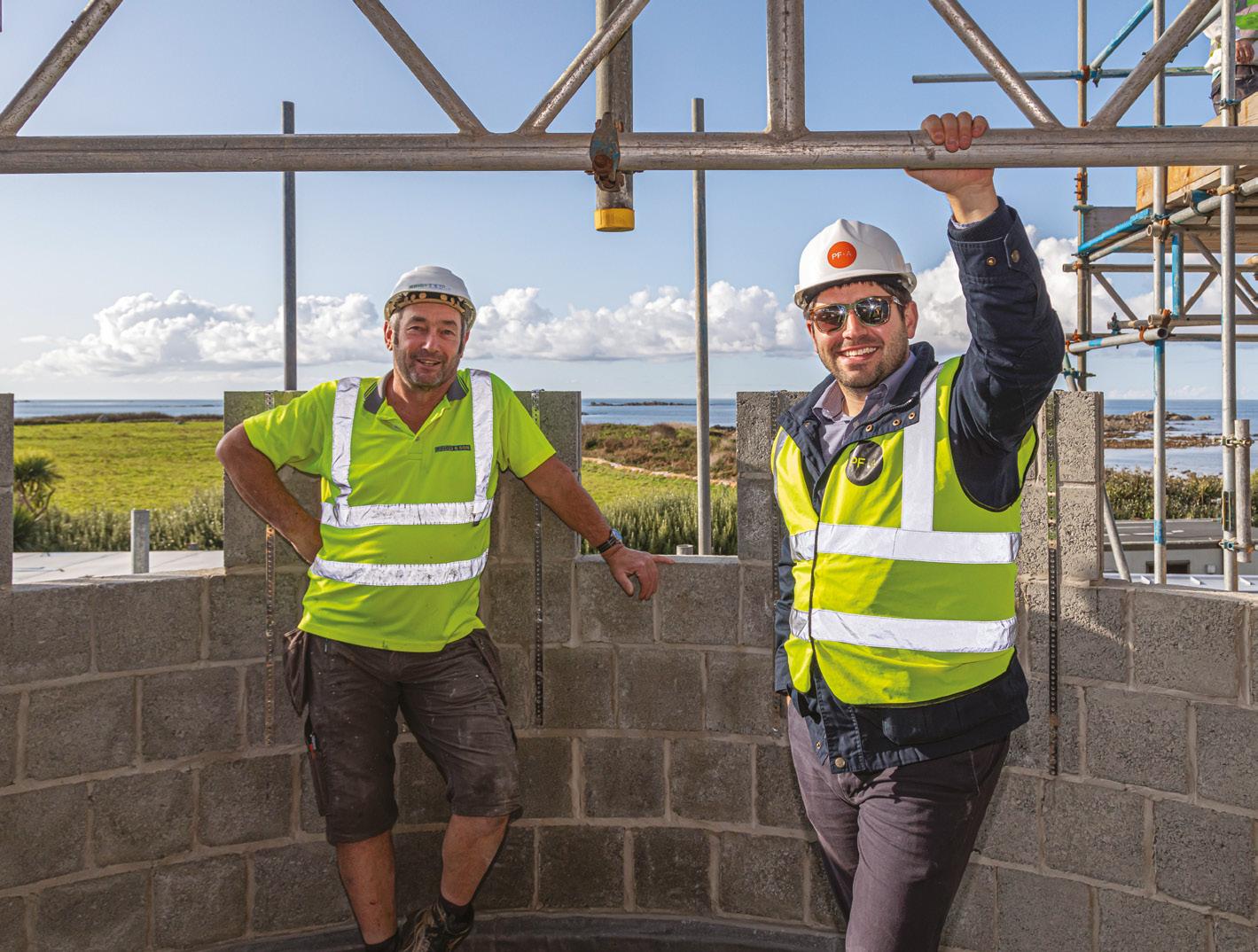
WE THINK MORE SUSTAINABILITY SHOULD BE MORE ENCOURAGED IN THE BUILDING INDUSTRY, EVEN IF IT HAS BEEN A CHALLENGE TO RETAIN THE OLD FOUNDATIONS AND WALLS FOR THE NEW BUILDING.
THE CONTRACTORS
• PF+A • Rihoy & Son • CBL Consulting • Sensible • Lightning Enterprises CI Ltd • Henderson Green • P3 Projection Coatings • Timber & Damp Proof Specialist Ltd • Sexton Green Landscapes • Geomarine • Channel Welders • Phase Mechanical • Paul Rouget • IQ Glass • Channel Island Ceramics • APEX Roofing • Peter Fletcher Tiling • Access Limited • Island Access • Ecoscreed CI Ltd • Stainless Steel Fabrications Once the initial issues regarding the state of the building had been resolved, one of the main challenges for those involved with the project has been the glazing. For Tom, it was a crucial part of the project that would make all the difference to the appearance of the house.
“The house is having very high quality glazing throughout, which is important because of its location, but also from a design perspective. Around a quarter of the costs of the build are taken up by the glazing so it’s really been a key part of the project.
“Many of the rooms are having a large amount of glazing to take advantage of the views that are a huge part of the appeal of this house. We are installing a minimal frame sliding door system where the panels slide over one another, which means that there are very low profile frames which don’t distract from the view.
“Aside from the look of the glazing, it was also very important that it was good quality. The windows and doors are triple glazed with excellent energy efficiency and very resistant to air, noise and water, which was important in this location.”
Of all the design features, the newly installed kitchen window particularly stands out – with a frameless design that takes nothing away from the view and has a built in seat to enjoy it from. For Tom, it’s touches like that which make the difference. “Often the architectural designs that are the most simple are actually the most complicated. Installing the windows so that they appear frameless takes a lot of work, but the result should be worth it.”
Proud to support Guernsey’s construction and property industries
Get the policy that’s built around you.
Call 01481 241555 to speak to one of our trained advisors, or alternatively visit us online.
rossborough.co.uk
For Dave, the windows were also a challenge, and one they knew could make a major difference to the project. “The windows were always going to have a fine margin of error with very little tolerance for miscalculations. There is a lot of glass on the top floor as well as the ground floor and we had to make sure that we were millimetre perfect with our measurements as the glaziers were crucial to the whole build.”
For Dave and his team on site, the arrival of the windows fairly late in the build process meant that they wanted to get the building watertight as early as possible. They came up with a temporary solution to build a protective waterproof screen where the windows would be placed, and also put a temporary waterproof membrane on the flat roofs before the final work.
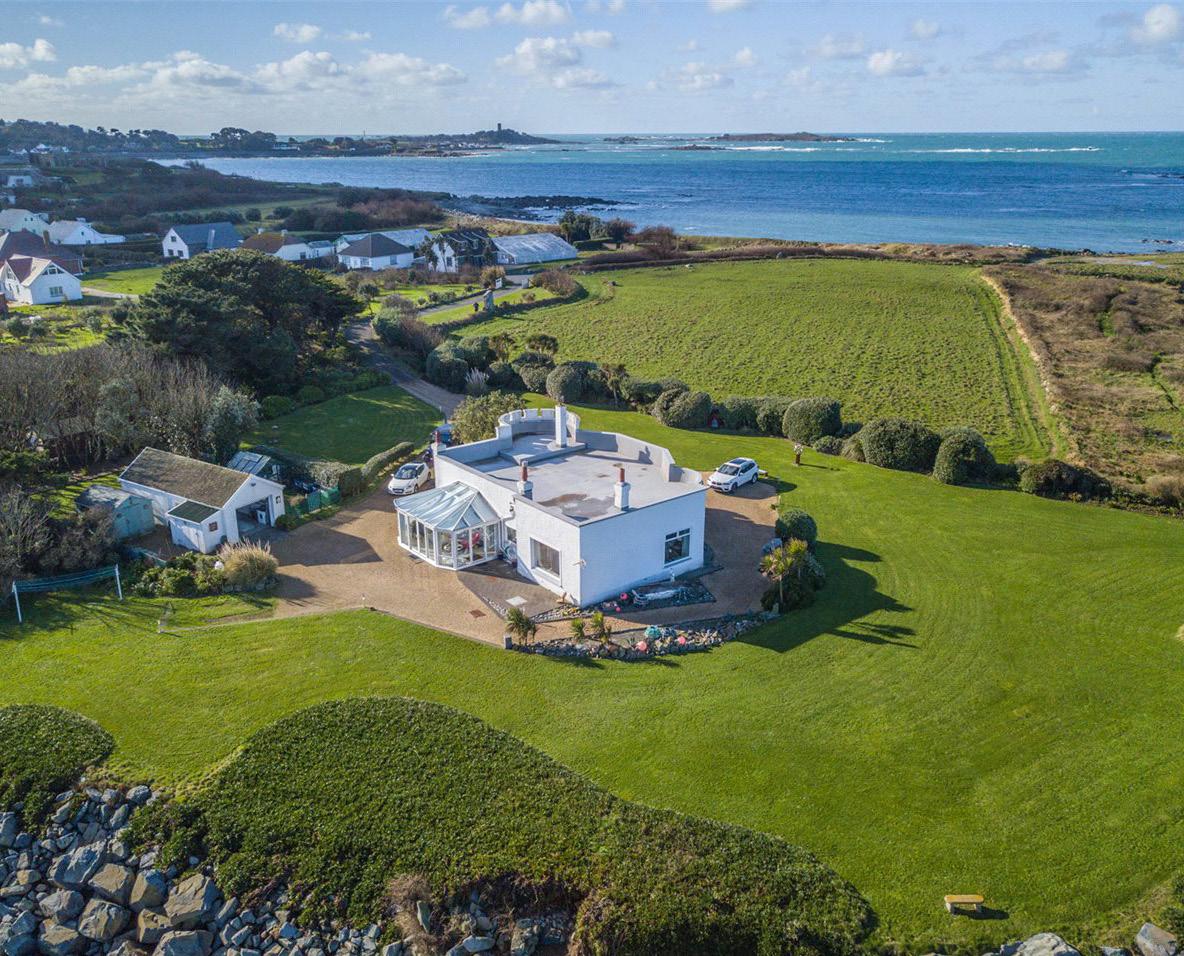
Proud to provide all the following services for Fort Le Crocq:
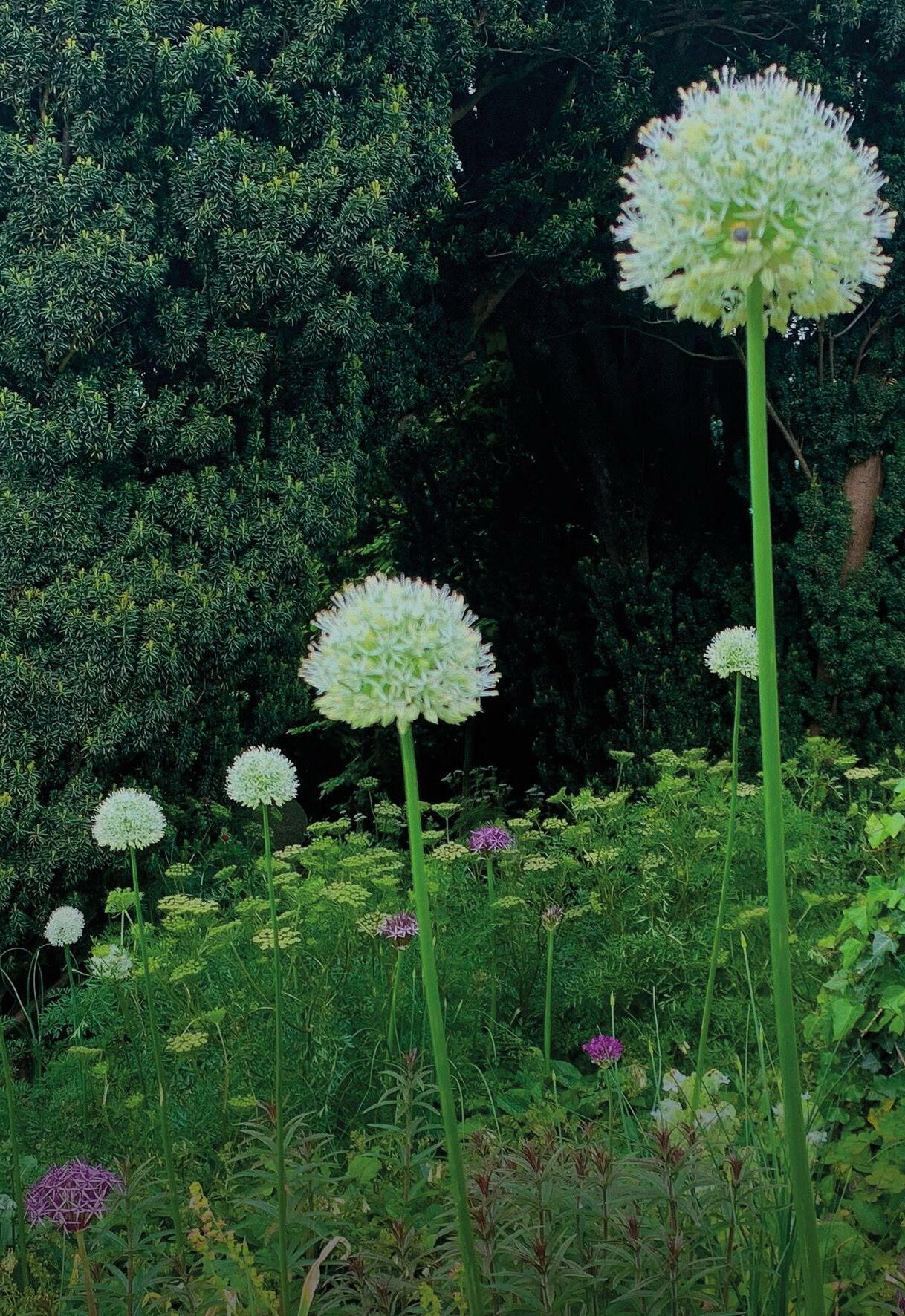
• Heating • Plumbing • MVHR • Air Conditioning • Lighting/Power • Fire Alarm • Data/TV/Telecoms
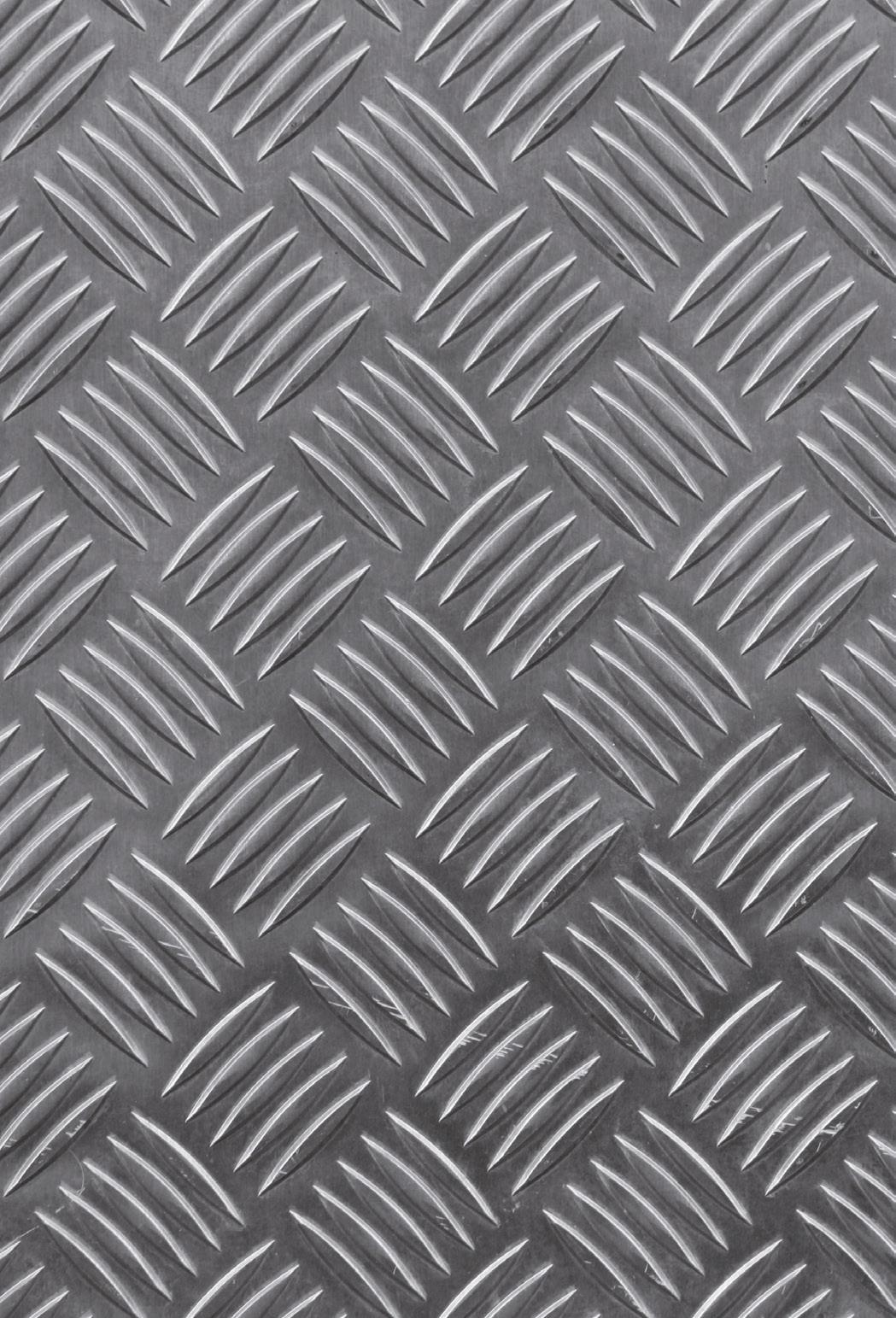
DOMESTIC | COMMERCIAL | INDUSTRIAL
For further information please contact us: Tel: 700080 Email: admin@phase.gg
www.phase.gg
The original residence before the start of the building work
Your complete landscape practice
Sexton Green Landscapes is a multi-discipline landscape practice focusing on providing high quality landscape design, construction, supply and maintenance to both commercial and private sectors in Guernsey.
Email: hello@sextongreen.com Office: +44(0)1481 251525
www.sextongreen.com
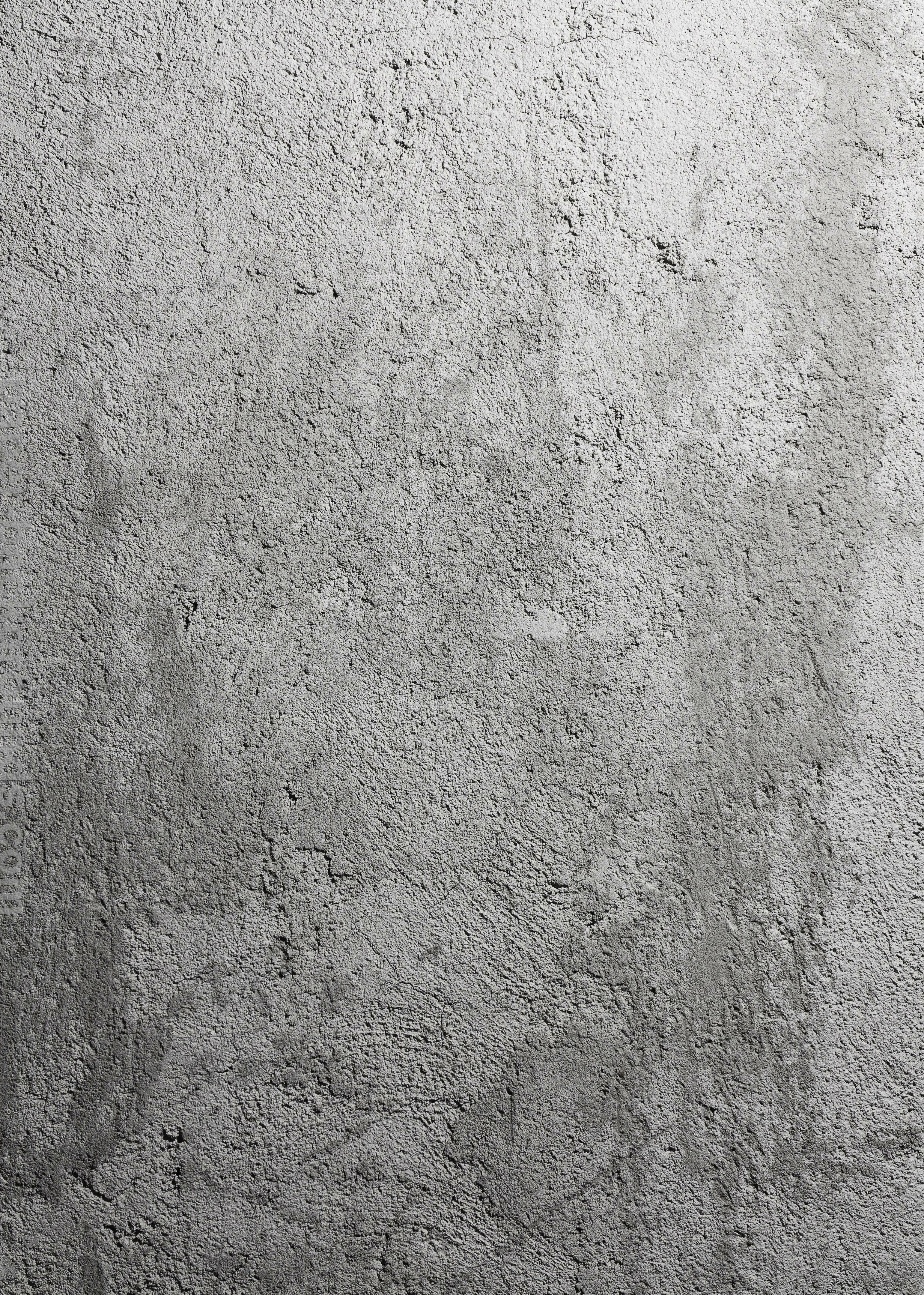
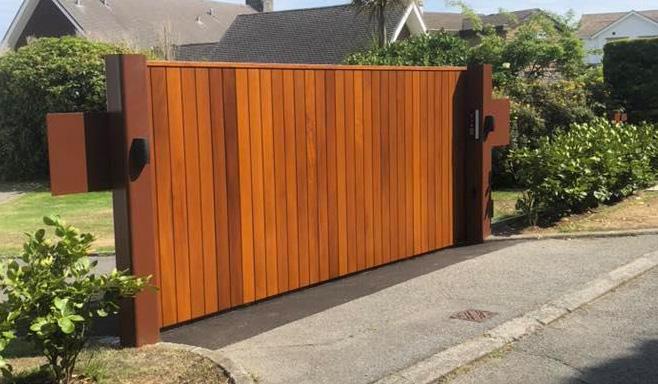
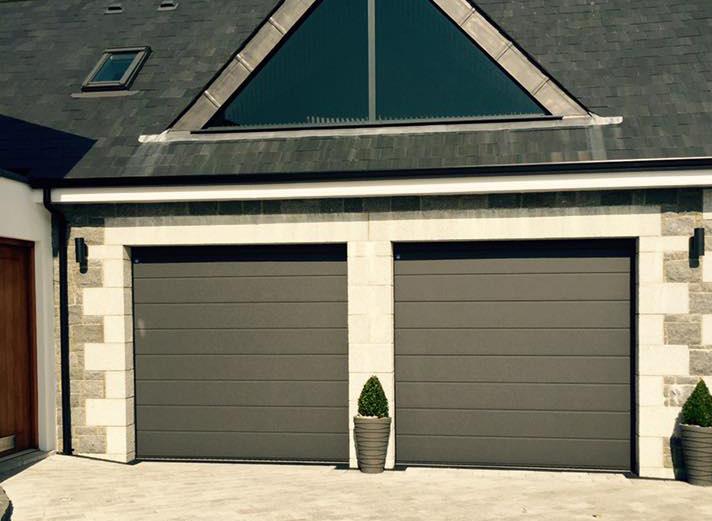
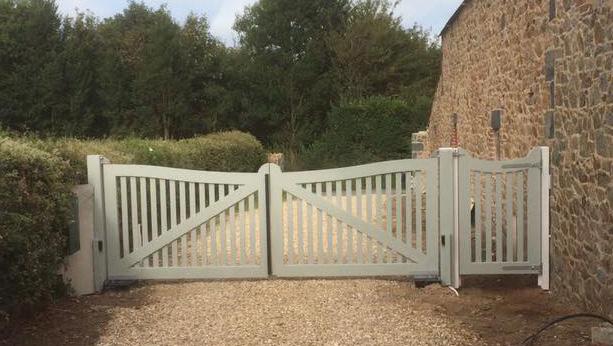
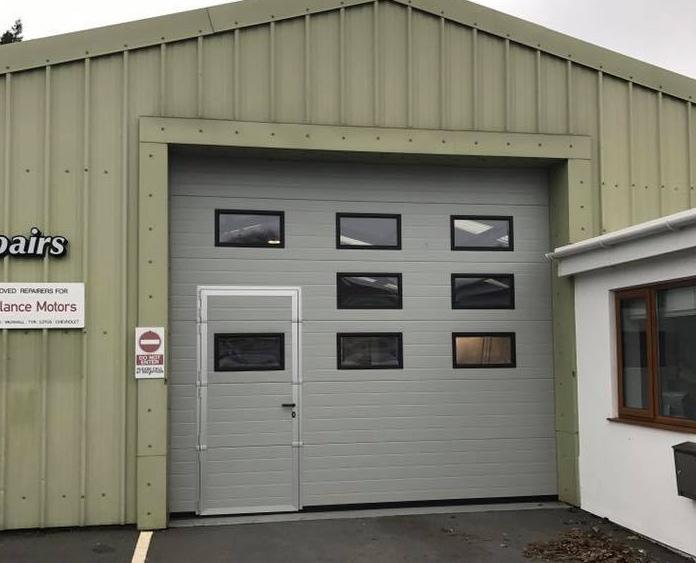
WHEN YOU LOOK AT THE HOUSE WITH THE SCAFFOLDING AROUND IT, IT SEEMS LIKE A HUGE HOUSE BUT THE ROOMS INSIDE AREN’T ENORMOUS “That meant we could get on with all the work we needed to do inside the property, which was crucial with the tight timings on this project. We have lost a few days on site because of the weather conditions as this is such an exposed site – when it’s really windy it’s not safe to work on top of the building and we can’t do much of the external work when it’s raining,” said Dave.

For such an impressive site, the building team working on the project has also had to stay relatively small, as Dave explained. “At the moment we have four carpenters working on site, a couple of labourers and the mechanical and electrical team, so around ten people in total. When you look at the house with the scaffolding around it, it seems like a huge house but the rooms inside aren’t enormous and we therefore can’t have too many people working there at the same time.” Given those restrictions, the timings on this project have been surprisingly quick. The owners first spoke to PF+A about their plans for the house in August 2018, before buying it in November 2018 with planning permission for the renovations already in place. They had hoped to have the project completed by the end of 2019 and PF+A had accelerated their usual timings to accommodate that.
Despite building work starting on schedule in January of this year and having a comprehensive schedule of works in place, the problems with the glazing have led to a slight delay in completion. The original plan to be in for Christmas lunch has been pushed back four weeks to January 2020. But those involved with the project hope that for the owners, their new home will be worth the extra wait.
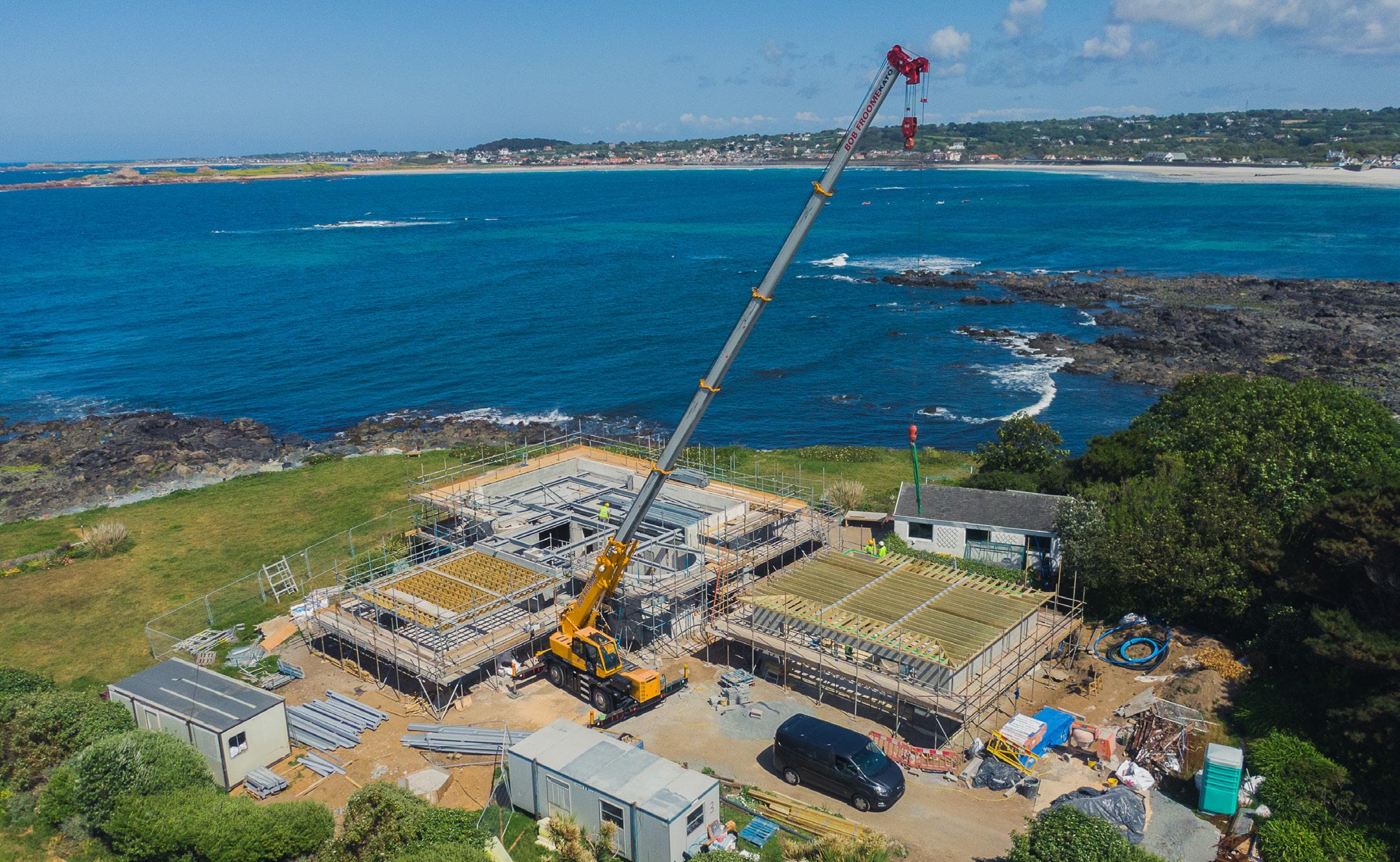