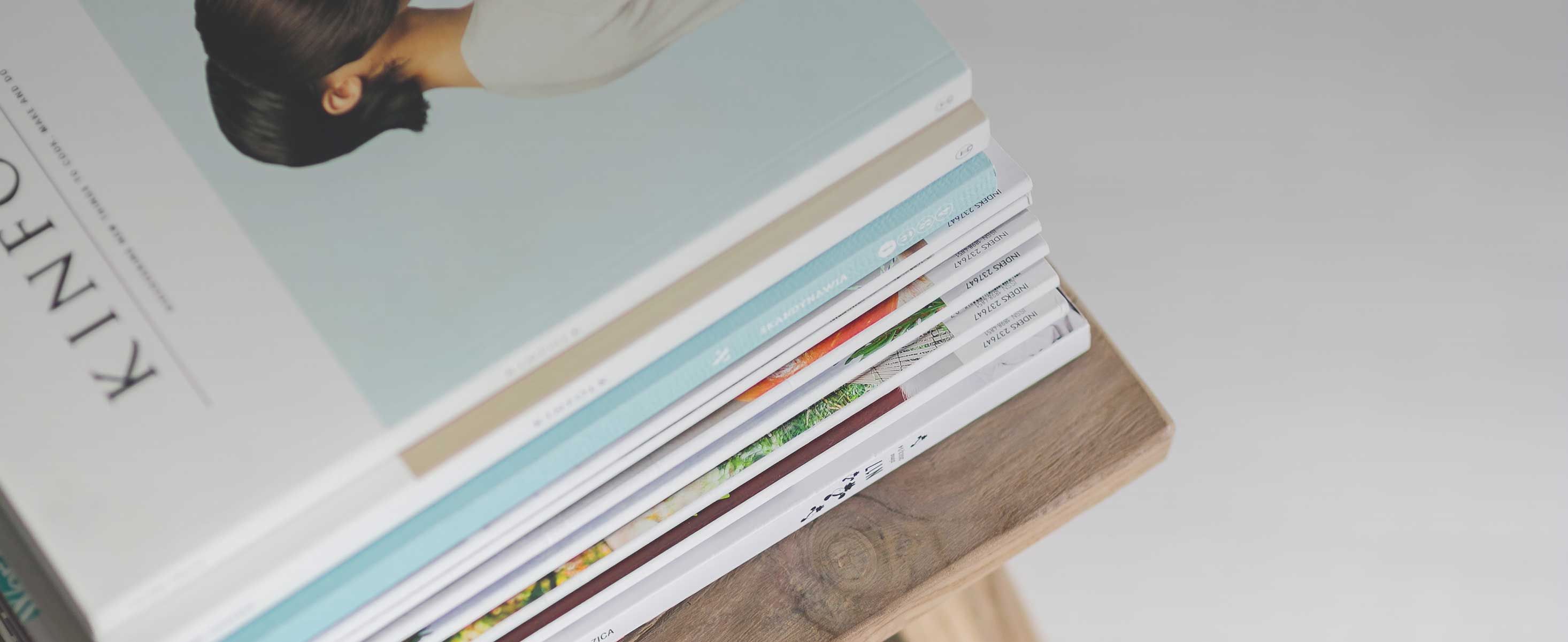
2 minute read
ElevenES starts prototype production
Earlier this year ElevenES, in Serbia, produced the first samples of its LFP prismatic cells for sample ‘A’ testing for applications, including electric cars, buses and energy storage systems.
An ‘A’ sample is a functioning prototype of a battery cell that can be tested by potential customers and can be tested for chemistry as single cells. Several of ElevenES’ partners and potential customers will test the A cells in small systems, by building a module out of eight-15 cells and testing them as a module.
Advertisement
The difference compared to ‘C’ and ‘D’ samples is down to the manufacturing process in ElevenES’s Mini Pilot Plant, which includes manual steps, compared with the fully automated process of ElevenES’ future mega and giga plants where serial production will occur. The company will also supply ‘B’ samples, which are adjusted ‘A’ samples.
Its mini pilot plant, which has begun prototype cell production, will be preceded by the installation of 1GWh of annual production capacity by the third quarter of 2024.
Márton Pap, project manager for ESS and programme development at ElevenES, says: “For the LFP industry in Europe — or anywhere outside of China — the biggest challenge is scaling up. On our mini pilot plant line we are already able to identify and address or iron out issues that could otherwise potentially hinder scaling up to automated production in our planned giga plants.”
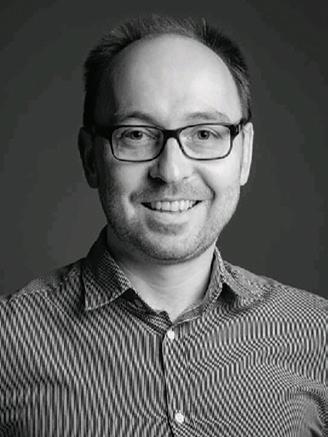
The facilities include a 1GWh factory, as well as planned 8GWh and 40GWh lines.
ElevenES is working towards achieving at least 60% of EU/localized content in its LFP cells within three years’ time. “This is challenging to do. Almost every part of an LFP battery cell in operation in a battery system comes from Asia or China today,” says Pap.
“It requires sourcing local materials and we’re in talks with Chinese companies with regard to their plans to establish in Europe. Ultimately, we’ll produce the cathode active material in-house, which means sourcing supplies of lithium carbonate and iron phosphate. We’re working to a 2026/2027 timetable,” Pap says.
ElevenES was set up in 2019 by its parent company — a manufacturer of aluminium packaging used in the pharmaceuticals and food industries, called AI Pack Group.
The CEO could see that the coating processes used in making the aluminium packaging could be adapted for producing lithium ion battery cells, says Pap.
Future customers for the company’s cells include, besides automotive original equipment manufacturers, producers of turnkey battery systems that also source components down to cell level as well as suppliers of racks and modules to the stationary storage industry.
“Feedback from everyone towards having a localized supply chain for the European and regional ESS market has been positive, for the most because of simpler logistics and shorter supply chains.
“Some see a European lithium ion battery supply chains as a way of avoiding potential trade wars and embargoes. There is, of course, the question about price but we’re happy to see them follow our progress and in some cases we’ll engage in co-development of modules,” Pap says.