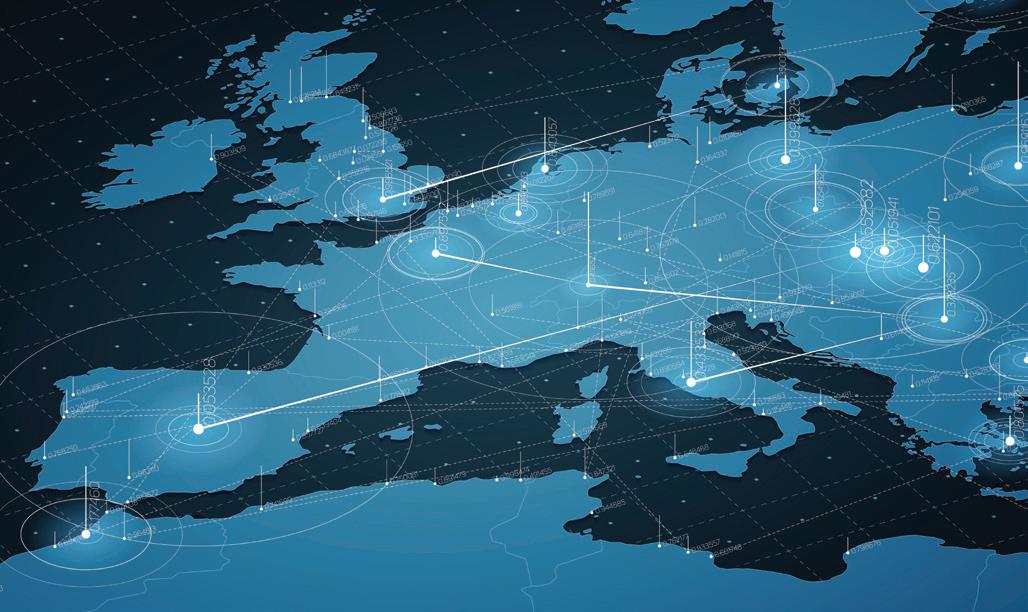
6 minute read
Lithium iron phosphate — the new BESS standard
The demand for utility-scale battery energy storage systems that emerged during the early 2000s unlocked a global market for lithium ion batteries that hadn’t previously existed.
Cells based on nickel, manganese, cobalt chemistry dominated supply of lithium ion batteries for stationary storage as well as electric vehicle markets.
Advertisement
As lead times stretched and prices held, in 2018-2019 cell manufacturers in China began tapping into stationary storage markets in the US and Europe, with cells produced using lithium iron phosphate chemistry, regarded as inferior due to lower energy density.
Compared with China and the US, the two largest markets for grid BESS globally, Europe has lagged despite its mature renewables market, shaped by early policy focused on decarbonizing power supplies.
In the coming years, Europe should pick up the pace of grid battery installations, from existing markets, including the UK and Germany, from Italy and Spain, where solar buildout is driving demand for storage, as well as from new markets, including Greece.
From 5GW to 95GW of grid storage Aurora Energy Research forecasts that Europe will install at least 95GW of grid-scale battery energy storage systems by 2050, surpassing 42GW in 2030, from an installed capacity of just 5GW of installed capacity in 2023.
Average battery duration will increase over time, driven by the buildout of wind and solar generation, which will need storage to meet times of peak demand for power. Aurora predicts that batteries with over four hours’ storage capacity will account for 61% of total installed battery capacity in 2050, compared with 22% in 2025.
Today, Europe’s bid to establish a lithium ion battery industry is still in its infancy.
In the wake of headline-grabbing gigafactory announcements, investors and owners are at vastly different stages of qualifying and preparing their cell technologies for industrialized production. Most aim to capture demand from the grid BESS market as well as EVs and several are backing LFP technology.
Aurora Energy Research forecasts that Europe will install at least 95GW of gridscale battery energy storage systems by 2050, surpassing 42GW in 2030, from an installed capacity of just 5GW of installed capacity in 2023.
Freyr aims to have a gigafactories producing LFP cells from around the mid-2020s in Norway as does ElevenES in Serbia.
Sunlight Group, in Greece, which has been expanding its battery ranges to encompass lithium ion as well as lead acid, is installing a prototype/ pilot line for LFP cells to eventually be used in its lithium ion batteries. Italvolt, in Italy, will start with mass production of NMC cells initially but also plans to produce LFP cells at some point.
Rhomotion, a London-based team of analysts keeping tabs on a growing pipeline of more than 3000 energy storage projects globally, says the share of grid BESS projects that use LFP technology has grown markedly.
This growth has been mainly at the expense of NCM but also lead acid and other chemistries. In 2020 NCM accounted for half this share, LFP just over a third, lead acid less than a tenth, with other technologies accounting for the remainder. In 2023 LFP technology accounts for nearly 90% of the BESS grid battery chemistry split.
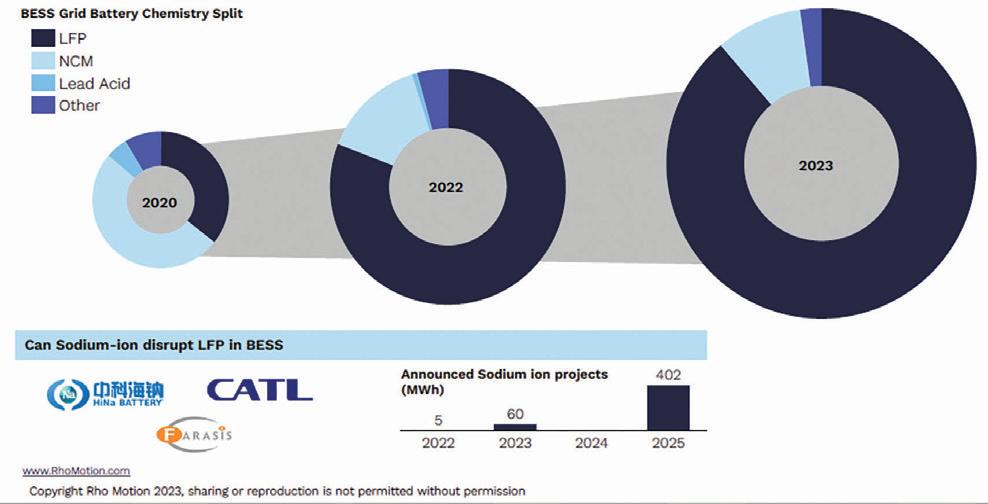
China is the leading market in terms of installed grid BESS capacity, predominantly using LFP cells, which have been exclusively supplied by Chinese manufacturers. Iola Hughes, research manager at Rhomotion, says recent policies around the inclusion of storage with new solar and wind installations have catalyzed even further BESS expansion in China.
The US is the next biggest market for grid BESS. Thanks to last year’s Inflation Reduction Act, standalone BESS will now benefit from the investment tax credit, likely to stimulate more grid storage investments. Hughes says it could still take a year or two for this to reflect in higher volumes of projects getting built and connected.
Europe’s predicted escalation in installations is contingent on changes to energy storage classifications, policy and increased revenue generating mechanisms.
According to Wood Mackenzie, in Europe most regulatory hurdles will be resolved before the end of this decade as demand for flexibility surges and concerns over security of supply increase.
Several factors have contributed to the rising interest in LFP in markets other than China.
One has been around perceptions that batteries made from LFP cells are safer than those made of NMC cells. Hughes refers to a thermal runaway event that led to a fire in one of the Tesla Megapack modules during precommercial testing in 2021 at Neoen’s 250MW Victorian Big Battery in Australia.
“In 2021-2022 dedicated storage system integrators began turning to LFP, following some developers expressing a move away from NMC,” he says Bloomberg also points out that more production can be expected outside of China, following the last of the worldwide patents that control LFP production outside of China having run out in 2022.
Technological progress is another factor, with performance improvements in LFP cells occurring year-onyear.
With a 10-15 year head-start in scaling-up their processes, Asiabased battery cell producers have been able to improve production efficiency, thus pricing, compared with competitor producers in Europe and the US, Hughes says.
Márton Pap, project manager for ESS and programme development at ElevenES says: “We can benefit from the low energy prices in Serbia and the relatively low labour costs. Nevertheless, we agree that the EU should introduce incentives to European players so they can be competitive even in the early phases of their developments.”
When establishing partnerships with cell suppliers, BESS suppliers and integrators look for counterparty bankability, scale and track record.
According to Pap, ElevenES is one of the most solid lithium-ion battery projects in Europe, due partly to the industrial experience and heritage of its parent, Al Pack Group, that will help during the scaling up process, and partly due to its step-by-step approach.
“We are moving one step at a time so we can learn and get experience on a smaller scale before moving on to a larger scale: lab, R&D center, Mini Pilot, Mega Plant (1GWh), Giga Phase I (8GWh), Giga Phase II (40GWh).”
ElevenES makes prismatic cells, a format that has been in the market for several years. Blade-like cells are a sub-group of prismatic cells, characterized by relatively thin and long dimensions. The connect points in ElevenES’ cells are at opposite ends, as opposed to on top.
“Customers have to adapt their modules to accommodate this but that isn’t a problem for most of them. In return they can benefit from the advantages of this cell format,
Freyr reaches key milestone, moves toward commercial production for H2 2025
During the past year Freyr, in Norway, has reached key milestones on the journey to industrialized production based on semi-state LFP cell technology, developed by 24M.
Freyr is targeting commercial production in the second half of 2025 from sites in Norway and also in the US to meet demand for stationary storage projects in both markets.
“They need these cells, yesterday. The urgency cannot be understated so we would expect to start seeing them deployed in storage systems for installations in projects soon after,” says Freyr’s investor relations head, Jeffrey Spittel.
In December Freyr formed a company with Nidec. The Japanese company is also a customer.
Nidec Energy will be a customer for Freyr’s cells to use them to manufacture battery energy storage systems for various stationary storage applications.
Before the JV was set up, Nidec had an undisclosed independent lab test a package of 24M sample cells, which showed similar gravimetric energy density performance for LFP graphite batteries similar and stable behaviour across the cells over several cycles, plus ther- mal stability, says Spittel. Freyr is gearing up to begin shipping cells to potential customers to test, from its now completed Customer Qualification Plant — a 13,000 square metre demonstration production line — in Mo I Rana, in northern Norway. The cells will be tested within labs, including at third party facilities, equipped to collect data on how the cells perform and compare against data gathered on cells from other suppliers. mainly the higher volumetric energy density,” Pap says.
While 24M’s semi-state technology is simpler to produce it is not mature, so the plant’s role is a critical step in scaling up the production process, according to Spittel.
One of the next steps for Freyr is to get cells produced on the line out to potential customers so that they can submit them to testing, which would get these potential new accounts to a similar place where Nidec already is.
The majority of output will be to meet demand for stationary storage markets, including front-ofmeter utility-scale installations as well as commercial and industrial applications. “The interest is off the charts,” says Spittel.
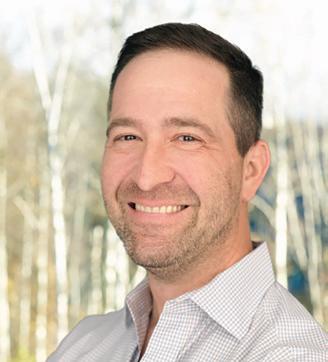
While the blade-like cell format was initially produced for EV applications due to increased volumetric density of around 20%-30%, longer duration BESS — set to grow in Europe in the coming years — will favour cells that hold more energy. Pap says a trend observed in China is for the main LFP producers to offer blade-like cells to the stationary ESS market, which suggests it could be introduced in Europe as well.
ElevenES is working on improving various parameters of its cells such as energy density and cycle life. Each application has different priorities. EVs need higher gravimetric and volumetric energy density for instance, whereas in the case of stationary ESS systems, longer life-time is important.
The company is working on an ESSspecific cell that will feed into serial production which is planned for early 2025 within the company’s 1GWh factory, which could see the BESS installations featuring ElevenES’ LFP cells from 2025-2026.
ElevenES is planning to allocate about 50% of its production to the EV sector, and about 25%-30% to the stationary ESS market. The Mega Plant, with 1GWh capacity, will supply ‘C’ and ‘D’ samples for the automotive industry, but for the ESS market it will already provide serial production. Giga Phase I in 2026 and Giga Phase II in 2028 will serve both market segments with large-scale, highly automated, efficient serial production.