
7 minute read
A mid-life makeover
A fresh look for the veneer industry
By Patrick Laurin, CHPVA Executive Vice-President
The Canadian Hardwood Plywood and Veneer Association (CHPVA) is going through a midlife makeover. The CHPVA took advantage of the disruption caused by the pandemic to reflect and reinvent itself, overhauling the approach they were taking, from the big-ticket items down to smallest minor details.
The pandemic created an unexpected wave of demand. Lockdown measures changed our use of space. Remote working and remote learning increased the need for more room and home office furniture, which energized the real estate, remodelling, and furniture markets to levels never seen before. Now, everybody in the industry is busy and facing challenges to meet this strong demand while respecting complex sanitary rules.
Traditionally, the association focused on updating and communicating quality standards and regulatory issues within its own industry distributors and manufacturers. Now CHPVA wants to expand its focus in promoting these products to the trendsetters, the architects, the designers, and the decorators that help people choose the look of their surroundings. The CHPVA wants to provide inspiration and information about hardwood veneer and plywood, demonstrating that wood is, in fact, the solution.
“‘Wood is the solution’ is the latest calling card to promote the membership and its products,” says Patrick Laurin, newly appointed Executive Vice-President. “Our members produce hardwood veneer and hardwood plywood used to manufacture furniture, cabinets, doors, and other architectural millwork products.”
The 63-year-old association has updated its image to go with its new goals - a new logo, new colours, and a new website for all to see the transformation. The CHPVA also plans to be more active on social media with articles and
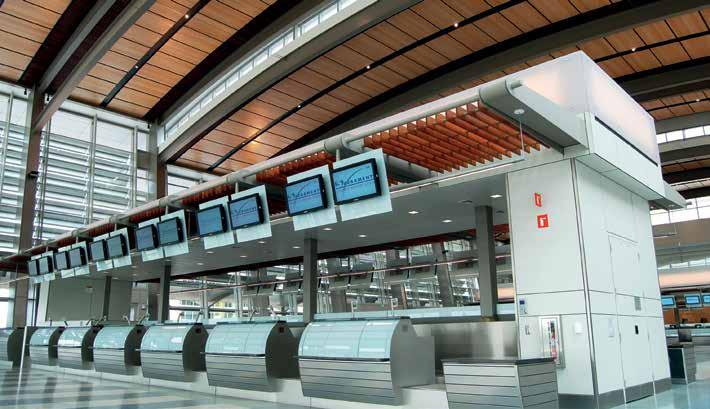
photos of wood species and various decorative hardwood plywood projects. The CHPVA is focused on expanding its message. Although still considered a traditional material, wood is unique, versatile, and timeless. Recently, science has made wood a cool raw material again. Renewable, recyclable, and with a lower carbon footprint than steel and plastic, wood can be a natural canvas of any decorative project with less impact on the environment.
The association plans to redefine its training and seminar offering to better educate designers on hardwood plywood and veneer possibilities within the industry. Most designers are accustomed to the ease of working with melamine and laminates because of all the marketing tools and samples available; it makes using hardwood plywood and veneer a more complex challenge. It is our job to provide more tools to them. Any kitchen or furniture company that does offer these options to their customers will have something over their competition. Traditionally, the organization’s goal was to train industry partners on technical aspects of hardwood plywood and veneer, like grading standards and wood characteristics. Still, the next generation of seminars will focus more on the needs of the trendsetters.
“The goal is to provide the influencers with a solid generic base of knowledge about hardwood plywood and veneer so that they are comfortable enough to recommend our products and include our materials in their projects,” says Laurin.
Still in planning mode, these sessions will be more topic-specific and shorter. They will help the participants understand the various species available, the products’ unique characteristics, and the accessibility from local, North American suppliers. Natural wood has way more possibilities depending on the finish. It’s all about showing designers the possibilities.
One of the tools CHPVA’s using to work towards this goal is the new website. A section called “Inspiration” showcases projects that used decorative hardwood plywood. This section will be regularly updated to showcase the latest projects. A complete listing and contact information about association members makes it easier to get in touch personally with experts. It also contains valuable links to other related associations and several interesting videos about wood in general. A complete online wood encyclopedia is available (The wood database*) to help anyone choose or research a type of wood for their next project. A bookstore is currently being built on the website to offer a selection of books and various guides helpful for any woodworker, designer, or purchaser requiring a reference source. All these resources that CHPVA is putting forward are well on their way to help place the hardwood plywood and veneer industry at the forefront of design trends.
KEEP YOUR FINGER ON THE PULSE OF THE CANADIAN MARKET WITH
WEEKLY E-DIGEST
Canadian industry news, feature articles, product profiles, design and technology updates delivered to your inbox every week.
SUBSCRIBE
for Free
www.woodindustry.ca www.lemondedubois.com
PERFECT RESULTS
Proper grit sequencing
By Robert Philips, Akhurst Sanding Product Manager
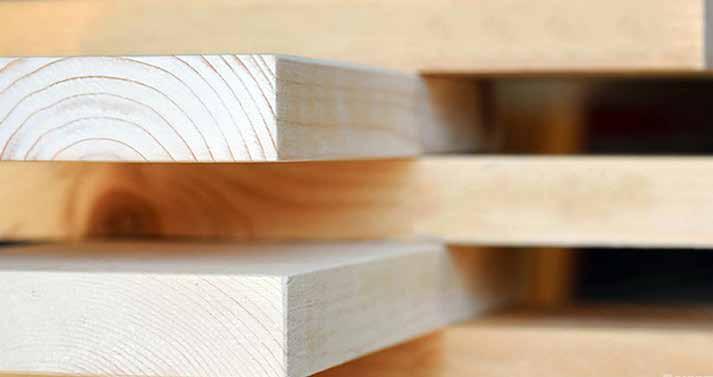
Getting the most from your wide belt sander ensures optimum finishing results and efficient production flow. Poper grit sequencing has a profound effect on both processes. Failure to adhere to proper grit sequencing can lead to a great deal of frustration with a poor quality end product, wasted time, loss of materials, and ultimately expensive unnecessary costs. This article discusses the guidelines to adhere to concerning grit sequencing so that you can achieve maximum performance from your sanding machine. This article will focus on solid wood sanding as the machine configuration varies greatly when sanding veneer products.
The first step is to identify what sanding grit you intend to finish with and determine what grit you need to begin with. From here, we can start to go fill in the gaps. As a starting grit, you want a sanding belt that is aggressive enough to remove any knife marks but not too rough that you spend unnecessary time sanding out the deep scratches left by these courser grits. In most wood applications where the finish is applied, the end grit is usually 180 to 220 grit maximum. Anything above 220 grit risks closing the wood pores, making your workpiece unable to accept the stain or finish. Sanding sealer with grits above 220+ is a topic we will cover another time.
THE SANDING RULE
The rule of thumb is that you can skip a grit when calibrating with grits 36 to 60. When sanding with grits from 80 to 220+, you should not skip a grit. The scratch patterns in the 36-60 grits are coarser and leave deep scratch marks in the material. These deep scratches will be removed by the subsequent sanding operations with grits 80+. When sanding with grits 80+, you do not want to skip a grit as you will not be able to sand down to the depth of the scratch of the rougher grit with the higher grit. If your grit is not enough to sand down to the previous depth, you will simply take the high points off and leave the deeper scratch. This may not be noticeable until you stain and finish the material. Immediately the scratches will show up, leaving blotchy and unbalanced results. This can lead to wasted time in rework, substandard quality, and ultimately lost profits. Below is a graphical explanation of the depth of scratch scenario.
WHY NOT TEST FOR YOURSELF?
Do a test on your wide belt sander and skip a couple of grits. Stain the material in a dark cherry stain, the results of
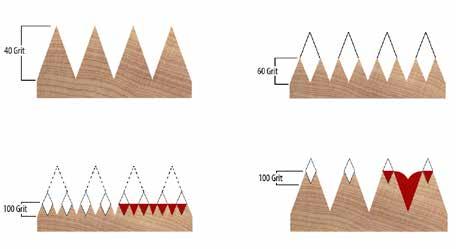
Illustration of grit sequencing patterns.
GRIT INCHES / MM (REMOVAL) APPLICATIONS
40 0.040” / 1.0mm
60 0.035” / 0.9mm
80 0.024” / 0.6mm Starting grits for hardwoods
100 0.017” / 0.4mm Remove shallow scratches
120 0.010” / 0.25mm Starting grits for softwoods
150 0.006” / 0.15mm Prep for enamel paint
Rough Lumber + Remove bumps in wood + Remove old paints and finishes
180 0.004” / 0.1mm Raised grain fibres + Surface irregularities
220 0.002” / 0.05mm Surface finishing + Prep wood stain
improper grit sequencing will become apparent. This is a standard rule, but also recognize that grit sequencing can be affected by the material of the drum (steel/rubber), abrasive coatings, and the speed of the machine. For example, the slower the conveyor belt (feed speed), the more surface contact you will have with the material allowing greater removal. The “Sanding Rule” applies to an optimum production environment. This chart shows the correlation we have with different materials and applications.
Asking detailed questions with your abrasive experts will help you achieve optimum productivity and results from your widebelt sander. The number and type of heads on your sander will determine the number of passes you will require to obtain the optimum sanding results. Ultimately sticking to grit sequencing and understanding how these patterns interact with your material is key for success.