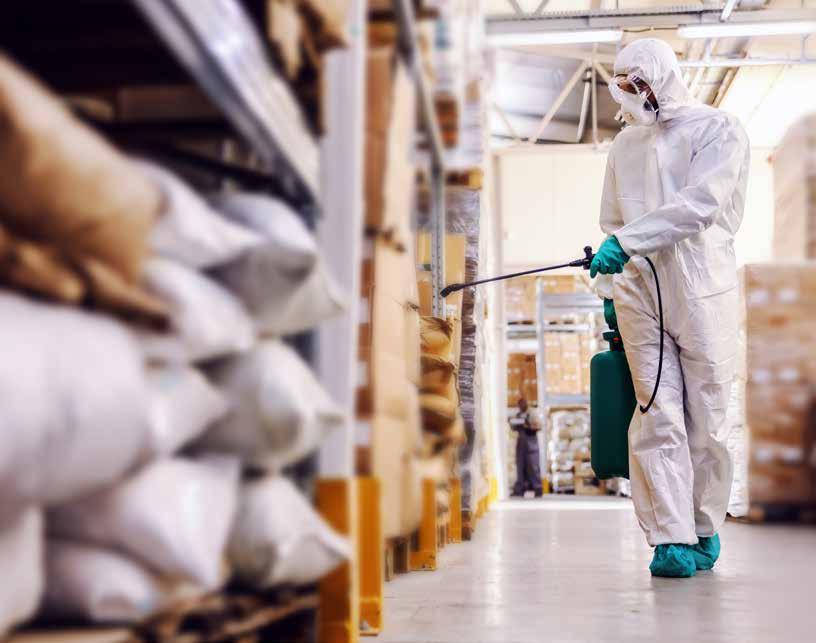
5 minute read
Do You Need a PPE Audit?
from FCM Summer 2020
by MediaEdge
DO YOU NEED A PPE AUDIT? The need for ongoing PPE program checkups is often overlooked
provided by Bunzl Canada
Advertisement
Maintaining the health and safety of cleaning and environmental personnel while they do their jobs is always a top priority, but the importance is heightened when widespread contagious illnesses emerge. The global COVID-19 pandemic has been a serious wake-up call, and too often cleaning staff aren’t provided the personal protective equipment (PPE) they require.
Many facilities have well-established programs that ensure their cleaning teams are regularly provided gloves, masks, and other PPE. However, as environments and cleaning requirements evolve, it’s important to regularly assess these programs to determine whether they address changing needs and concerns.
A PPE program check-up should include three elements: a review of the basic components of each employee’s PPE kit, ongoing employee training on using their PPE properly, and staying up to date on the latest industry news and technology to help continuously improve the program. There’s a common misconception that setting up a PPE program for cleaning and environmental personnel is a one-time job. In fact, continuous updating of PPE products and practices is essential.
THE BASICS
When evaluating your PPE program, start with the basics. Ensure that the main components are current and in working order. Next, look at work areas
for every item. Note important information such as the conditions in dition, how to adjust the size/fit, and spiratory protection devices, for example,
Providing ongoing training also gives require regular maintenance including spe cialized repairs, cleaning, storage, filter re employees an opportunity to offer feedback placement, and periodic testing. on the PPE program. EMPLOYEE TRAINING Hiring and training cleaning and envithat require additional protective gear when worn product should be retired. an ongoing requirement, and updating and any new areas, conditions, or retraining material should be ongoing, quirements that may dictate specialized THE IMPORTANCE OF LEADERSHIP too. This might include updates on the PPE be added to the basic program. As with every aspect of company culture, equipment required for different tasks,
Think about employee demographics a culture of safety comes from the top. information on how to properly don and too. Product selection may need to be adLeadership and supervisory staff must remove safety equipment, and what to justed to ensure well-fitting, comfortable make safety a part of every employee’s look for when inspecting PPE. Don’t PPE for team members of all genders day. Lead by example by wearing PPE, make the mistake of thinking proper and ages. For example, select products asking employees about their PPE, and PPE training is reserved for complex from lines designed to meet the needs of praising those who show attention to safety equipment. Did you know, for instance, a woman’s physicality. Too often, men’s and highlight its importance. Appointing that the benefits of wearing disposable PPE is assumed suitable for women if an employee representative as a program gloves can be negated if employees reprovided in smaller sizes, when in fact coordinator with the responsibility of enmove them incorrectly? Gloves are meant a different shape or design is required in suring each element of the PPE program is to shield hands from dirt, bacteria, and order to keep female workers comfortin place and operational can dramatically chemicals, but if removed incorrectly able and safe. increase PPE program success. they can cross-contaminate hands and Start employee meetings with a discusother surfaces. All staff using disposable SAFETY REGULATIONS AND USAGE sion about safety and encourage employgloves should be trained on how to safely INSTRUCTIONS ees to raise concerns about damaged PPE. remove them. PPE requirements vary by facility, the Employees may hesitate to speak up out of Providing ongoing training also gives type of work performed by cleaning and fear they’ll be blamed for damaging the employees an opportunity to offer feedenvironmental personnel, and applicable PPE. Put such fears to rest by making it back on the PPE program. Compliance government safety standards. Safety regclear that every team member’s safety is of with PPE is a big hurdle for many faulations associated with the specifics of critical concern and that it is a top priority cilities, and typically not because workers hazardous substances or working condito protect them from injury or exposure to don’t put them on at the beginning of a tions can dictate product requirements dangerous chemicals or bacteria. shift. Instead, it’s because workers often and recommendations. In Canada, two remove their PPE during their shift beof the best-known standards that apply PPE MAINTENANCE cause of discomfort and never put it back to personal protection in the workplace Regular PPE maintenance should include on. Employee feedback received during are the Canadian Standards Association cleaning, repair, and proper care and stortraining can help pinpoint areas of im(CSA) and Bureau de normalisation du age. Conduct regular inspections for damprovement and may indicate the need for Québec (BNQ) standards. These outline aged, improperly functioning, or ill-fitting an alternate product choice. the types of PPE recommended for cerequipment before it is used. PPE that is not tain work hazards, classify protection acperforming up to manufacturers’ specificaLOOK FOR INNOVATION cording to the hazard, and establish PPE tions, such as safety glasses with scratched Seek out new products and technologies categories to aid in selecting the prodlenses, which compromise their ability to to help keep cleaning personnel safe. ucts best suited to the hazards of a spewithstand impact, must be discarded. From biohazardous spill mops to eleccific job. You can also request guidance Regular program maintenance also protrostatic disinfecting equipment, innofrom your product supplier’s workplace vides an opportunity to ensure procedures vative cleaning products and equipment health and safety consultants. have been established to enable workers to are continually being introduced to help
On receiving new PPE, thoroughly obtain replacements or replacement parts cleaning teams work more safely, effiread the manufacturer’s instructions for damaged PPE and to keep it clean. Reciently, and get better results. / which you should (and shouldn’t) use Bunzl Canada is a global distributor of cleaning supplies and personal protective equipment to over the equipment, how to store equip45,000 Canadian businesses. For more information, please contact David L. Smith, ESP, director, ment to keep it in good working concleaning, hygiene and sanitation, Bunzl Cleaning & Hygiene, at 613-449-2146. ronmental team members is typically