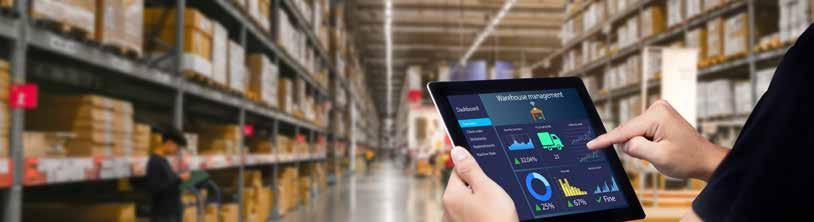
6 minute read
Zero Carbon Design: Nova Scotia warehouse
from CPM October 2020
by MediaEdge
LOW CARBON, LOW COSTS
Warehouse Tenants Minimize Heating Bills By Mark Hutchinson
Advertisement
A 65,000-SQUARE-FOOT warehouse in Dartmouth, Nova Scotia, earned Canada’s first certification for Zero Carbon Building Design (ZCB-Design) in the fall of 2019 as part of the Canada Green Building Council’s (CaGBC) pilot program for the zero carbon standard. East Port Properties, the developer and manager of the five multi-tenant buildings that comprise the Wilkinson Warehouses, leveraged experience delivering energy-efficient projects to demonstrate the potential for a lower-emitting industrial sector.
East Port President Judy Wall took up the challenge, building on the company’s track record as the developer the first multi-tenant warehouse in Halifax to be certified under the LEED program more than 10 years ago. Warehouses have traditionally been designed as a lowestcost product, especially since developers don’t always know what the building’s final use will be or how that usage might change over time. However, developers like East Port are seeing an increased demand for sustainable real estate and are creating a market for smart spaces and value-add property management services.
Signing on to the 15-building CaGBC pilot program is part of that effort. By 2030, Canada has vowed to cut greenhouse gas emissions by 30% below 2005 levels. CaGBC created the ZCB to support that process. It combines design and performance certification; measures the carbon balance of a building; and makes carbon reductions the key indicator for building performance.
The East Port team knew the key elements that would have significant impacts on building energy use: reduced air leakage; better insulation; efficient heating systems; and automated controls to reduce dependence on human intervention to operate the system. The building design started with a tight and well-insulated building envelope. The insulation value of the roof was upgraded to R-40, and then built using airtight, insulated, tilt-up concrete sandwich panels for continuous R-20 insulation value.
According to Wall, one of the prime spots for heat loss is at the loading docks. Verticalstoring dock levelers, a product typically used in cold storage warehouses to keep the cold inside the building, were used to further reduce air leakage.
A central in-floor system supplies heat via air-to-water heat pumps. This central heating system consists of six air-to-water heat pumps and a peak-load/back-up condensing natural gas boiler that provides a constant floor temperature of 17⁰ Celsius. Electronically commutated motor circulator pumps in single-bay zones drive hot water distribution.
Overhead unit heaters, metered and billed directly to the tenant, supply additional heating. Controls were installed to stop in-floor heating circulators from running in areas with open overhead doors.
East Port also installed a net-metered solar photovoltaic system through Nova Scotia Power’s Net Metering program. The system is sized to offset the cost of fuel sources — assuming a heating energy intensity of 1.6 equivalent kilowatt-hours per square foot.
With these heating considerations, it would be possible for tenants to realize a no-cost central heating bill if they were vigilant to limit how long their overhead doors remain open.
The efficiency of the design was especially apparent during an eight-hour power interruption, when it was -15⁰ Cs outside, but the indoor temperature dropped only 0.5 degrees.
Going beyond the Zero Carbon standard, East Port opted for some features not typically found in a warehouse, such as Solera windows and skylights to maximize the use of daylighting. The buildings are also equipped with automated, energy-efficient ventilation systems and LED lights with motion sensors.
While that translated into an approximate 10 to 15% cost premium compared to the Zero Carbon standard, East Port is now seeing a return on that investment. Higher net rents are achieved from tenants seeking lower heating energy bills and more comfortable workspace.
A second warehouse has since been certified and construction is in progress on a third also targeting the standard. In addition, East Port is pursuing ZCB Performance certification. Performance certification proves the project’s operation has earned zero carbon emissions over a one-year period, as required by annual verification. zz Mark Hutchinson leads the Green Building Programs at Canada Green Building Council (CaGBC), including overseeing the LEED and Zero Carbon Building Standard certification programs. For more information, see the website at www.cagbc.org.
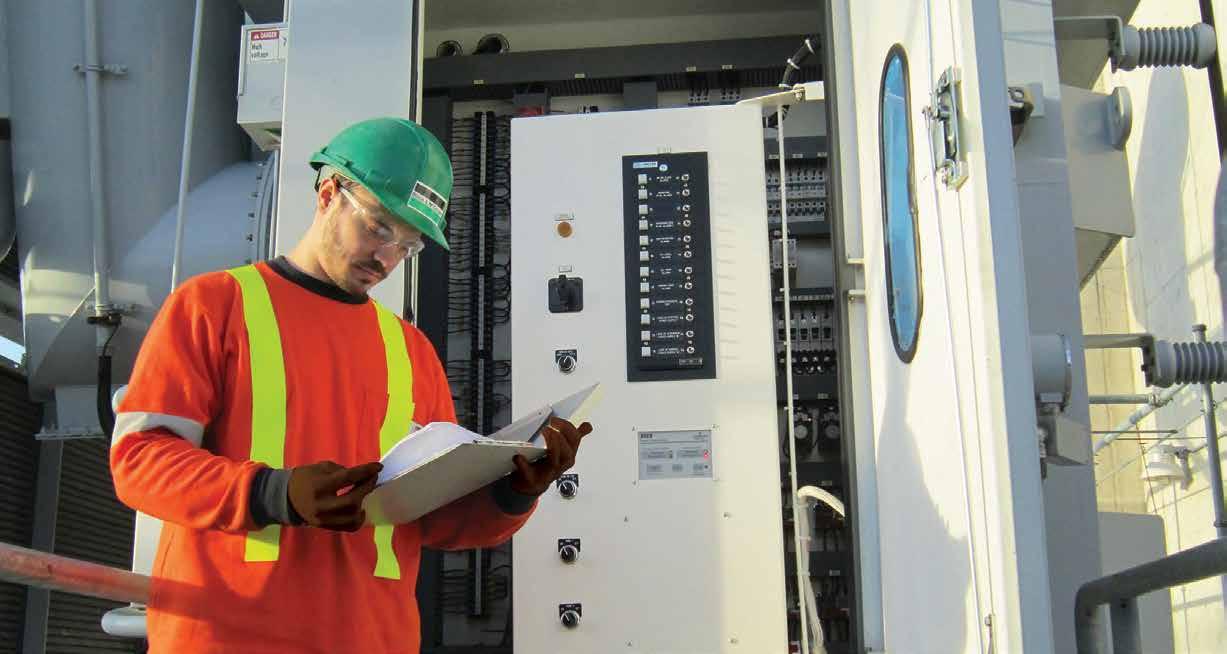
Stop Electrical Damage Before it Occurs
Why thermal imaging should be part of your routine preventative maintenance plan
Thermography is a method of inspecting electrical and mechanical equipment using specialized infrared cameras. By producing detailed images and temperature profiles of specific pieces of equipment, thermal imaging measures the infrared energy of an object’s surface, alerting facility managers to any potential threats.
Aidan Mabbott, Division Manager with Black & McDonald British Columbia Service, has seen all-too often what can happen when building electrical systems aren’t routinely scanned.
“In dusty environments, dirt and debris can build up on the electrical components, which can lead to a short circuit condition,” he says. “This often creates a spark or arc, which can ignite and cause a fire.”
For facility owners and operators, it’s nice to know that early detection and intervention can greatly minimize this risk.
HOW THE TECHNOLOGY WORKS
Though infrared technology has been around for decades, thermal
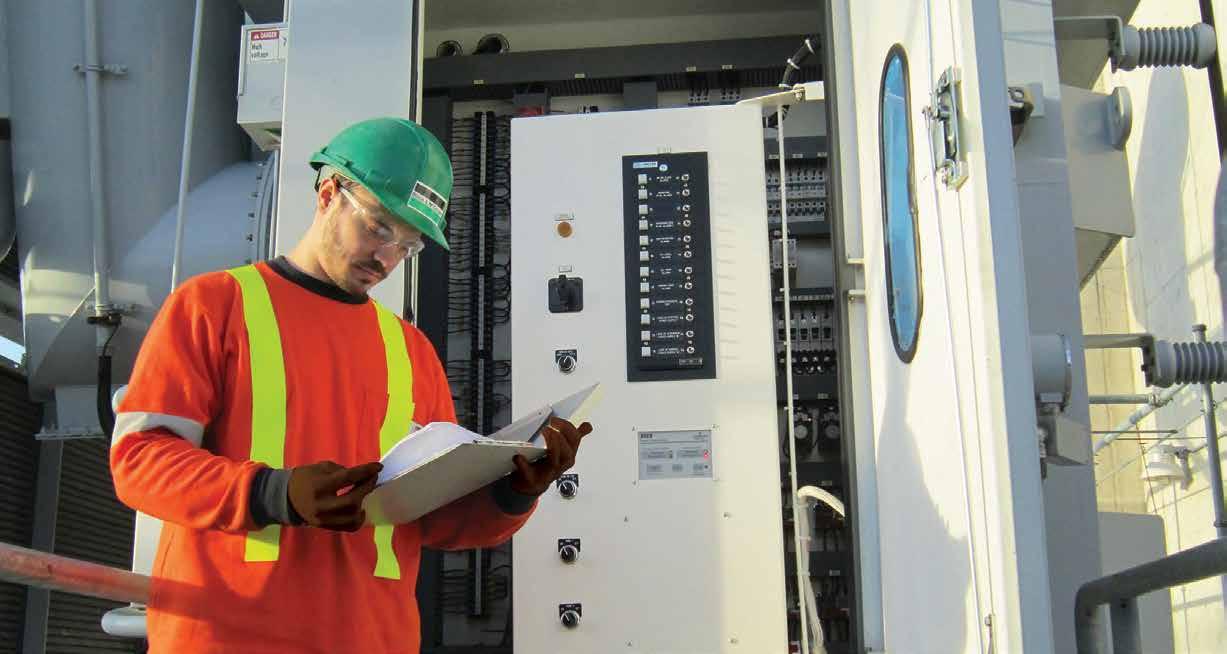
imagers used in building inspections have only been prevalent for about 15 years—and the technology has come a long way.
“Today’s imagers are flexible and detail-oriented, and they are portable enough to take anywhere,” says Mabbott. “Equipped with rotating screens that can deliver real-time temperature graphs, we’re able to produce professional reports for our clients in a matter of minutes.”
Given most system components show an increase in temperature when malfunctioning, today’s high-powered infrared cameras enable qualified inspectors to see the heat signatures associated with high electrical resistance before the circuit becomes hot enough to cause an outage or explosion.
There can be several reasons for a malfunction, but David Carter, an electrician with Black & McDonald, says the most common root causes include: loose connections; aging equipment; and overloaded circuits. Equipment that builds up heat can also be an indication of poor installation or that cooling systems are not functioning properly.
“Whatever the reason for the increase in temperature, detecting it early can lead to substantial cost savings for the facility operator, not to mention peace of mind,” he says.
HOW OFTEN SHOULD THERMAL IMAGERS BE USED?
Though recommended as part of a routine maintenance program, there is no ‘one size fits all’ approach to thermal imaging—it all depends on the type of facility and the age of the equipment.
“We often perform thermal scans on office electrical panels annually, and industrial equipment quarterly,” says Carter. “But there are many components in our electrical, plumbing and HVAC systems that have benefitted from regular thermal image scans.”
The best approach, adds Mabbott, is a custom approach. “At Black & McDonald, we look at several items before proposing a proactive maintenance program for our clients,” he says. “Some of these items include: type of business, age of equipment, run duration of machinery and the client’s budget.”
For electrical panels, Black & McDonald will often propose two options—the first being a basic surface scan of the breakers to see if there are any obvious issues with overheating. “If we discover anything abnormal we would then remove the covers for a closer look as to the cause,” he says.
The second option is a more in-depth inspection involving the complete removal of all covers to expose all of the electrical components. “We then scan all lugs and terminals, check that all wires are tightly connected and measure voltages to ensure that everything is as expected.”
When performing a thermal image scan at a building for the first time, Carter recommends his clients opt for the in-depth inspection as an “initial tune up” and overview of the equipment. Subsequently, surface scans may be all that are required given most of the issues will have been identified up front.
The bottom line is this: electrical outages and fires can be costly, disruptive, and dangerous. Taking the right steps to prevent them is in everyone’s best interest.
For more information on Black & McDonald’s thermal imaging services, please visit www.blackandmcdonald.com