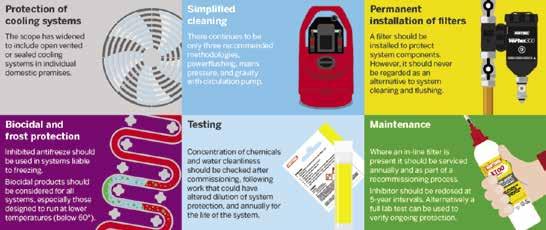
18 minute read
Water treatment and storage
Water treatment to be made mandatory
The next Part L Building Regulation revisions are expected to strengthen the requirements to treat the water in heating systems annually. Registered Gas Engineer explains what this means for heating engineers, and sets out the steps that need to be taken.
The long-awaited updates to Building Regulations Part L are due to be implemented later this year and, after a consultation with the industry in January 2021, are expected to make direct reference to British Standard 7593:2019 for the first time.
The current version of BS 7593 was introduced in 2019, but until now has only been an advisory document, outlining best practice for water treatment and system cleaning, but with no specific legal or regulatory backing.
The standard itself will remain advisory, but compliance becomes mandatory for those working on domestic central heating and cooling water systems because it will be referenced directly in Approved Document L (Conservation of Fuel and Power)
Nisar Afsar, technical director at Sentinel, says: “Previously BS 7593 was a recommendation, but now that there is a direct reference in Part L, it means the document has become mandatory as part of Building Regulations. So now, when commissioning a system, the heating system in that property has to conform explicitly to the British Standard.”
What does this mean?
Once BS 7593:2019 becomes a mandatory requirement under Part L, engineers must comply whenever they install a new boiler, or carry out any annual servicing or maintenance work.
The main steps in BS 7593:2019 that must be followed under Part L include: • An in-line filter must be fitted to every system to protect its components, and should then be serviced annually • The level of inhibitor in the system must be checked each year • Inhibitor must be re-dosed every five years, or a full system water test carried out • Before adding the inhibitor, engineers must carry out a chemical clean and fresh water flush • Cleaning methodologies can be improved through external magnetite capture and/or the mechanical vibration of panel radiators, where fitted • Biocide should be used in low-temperature heating systems, and cooling systems, to prevent fungal growth, and should be considered for all systems • An inhibited antifreeze should be used in systems liable to freezing.
The standard states that cleaning and flushing should be undertaken before commissioning a new system, or repairing an older one “to overcome the loss of effectiveness and efficiency caused by the effects of poor water quality”.2
BS 7593:2019 also outlines three cleaning and flushing options, one of which should always be applied to ensure an effective clean of the system before flushing: • Powerflushing: A cleaning and flushing procedure using an external pump and tank arrangement to effect the circulation of water or chemical cleaner solution at increased velocity and turbulence through the whole circuit and particularly through individually isolated panel radiators, where fitted, such that it reaches the entire inner surfaces of the system with enough force to ensure the cleaning and complete removal of all adherent and settled sludge, foulants and debris.
Sentinel highlghts the key changes in BS 7593:2019
What does Approved Document L say?1
The draft Part L revisions were released for consultation in January 2021, and are due to come into effect later this year. While the final document hasn’t been released yet, the draft guidance issued for consultation in January 2021 says:
“System specific guidance for commissioning Hot water systems for space and domestic hot water heating
8.6 Before a new heating appliance is installed, all central heating and primary hot water circuits should be thoroughly cleaned and flushed out. A suitable chemical inhibitor should be added to the primary heating circuit to protect against scale and corrosion. Domestic central heating systems should be prepared and commissioned to BS 7593:2019.
NOTE: The Benchmark commissioning checklist can be used to show that commissioning has been carried out satisfactorily for the heating and hot water system and its heat generation source. 8.7 In addition to paragraph 8.6, heat pump heating and domestic hot water systems should be commissioned to the Microgeneration Certification Scheme’s MIS 3005, subject to the limitations on scope as outlined in this standard.”
Water treatment to be made mandatory
• Mains pressure clean and flush: Mains pressure cleaning is a cleaning and flushing procedure in which cleaning of the system to remove all adherent and settled foulants and debris relies on an adequate circulation, preferably at operating temperature, of an appropriate chemical cleaner solution followed by a flushing procedure. The flushing procedure is characterised by the flush through of water under mains pressure through the whole circuit and also through individually isolated radiators, such that it reaches the entire inner surfaces of the system for an adequate period to ensure the complete removal of all adherent and settled sludge, foulants and debris.
• Clean and flush using gravity
(with the assistance of a
circulation pump): Gravity cleaning is a cleaning and flushing procedure in which cleaning of the system to remove all adherent and settled sludge, foulants and debris relies on an adequate circulation, preferably at operating temperature, of an appropriate chemical cleaner solution followed by a flushing procedure. The flushing procedure is characterised by repeated draining and filling the entire system with an adequate total volume of fresh water, such that agitation thereby effected will assist the removal of adherent and settled sludge, foulants and debris.3
Richard Crisp, head of chemistry at Fernox, says: “The chemical water treatment industry has been championing the lifelong protection of central heating systems for many years,
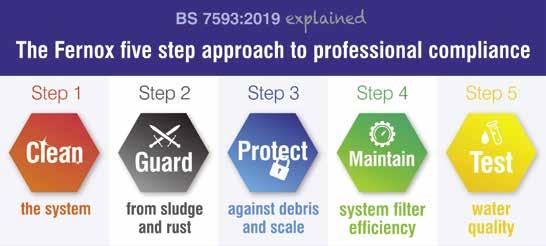
Fernox sets out its recommended five-step approach to professional compliance with BS 7593:2019
to improve energy efficiency, minimise fuel wastage and ensure system longevity.
“The 2019 changes to BS 7593 aimed to clarify and promote best practice, for the lifetime of the system. The code of practice covers five key areas – clean, guard, protect, maintain and test – to not only ensure compliance, but also to ensure that systems perform at their optimum level.
“To protect a central heating system from corrosion, scale, and microbial fouling (for low-temperature heating systems), engineers should dose the system with the correct concentration of chemical water treatment products. This should include protectors to protect against harmful sludge and debris build-up.
“System filters can directly protect the boiler to ensure that any circulating debris present within the system does not reach vulnerable components, such as pumps or heat exchangers.
“For hard water areas with water hardness levels of 200ppm and above, a scale reducer should be fitted to mitigate the effects of limescale. Electrolytic scale reducers offer whole-house protection, while magnetic scale reducers are designed to be fitted next to the boiler, or other appliance, for single appliance protection.”
Regular testing is key
BS 7593:2019 makes it clear that engineers should test the central heating system at the annual service, with a particular focus on checking inhibitor levels. “A central heating system is full of metal components and, when water comes into contact with them, it can lead to corrosion,” says Richard. “If left untreated, limescale, sludge and other corrosion debris will build up over time and can circulate within the system, causing blockages. This forces the system to work harder and results in a sluggish, inefficient performance – as well as higher fuel bills for the customer and increased carbon emissions. It can even cause system breakdown.
“Inhibitor plays a key role in maintaining system efficiency but, if underdosed, the system can still be at risk of scale and debris build-up. It is therefore vital that the system is checked regularly to make sure that the correct concentration of inhibitor is present, and the central heating system remains protected. On-site testing will advise the engineer if levels are too low and allow them to quickly re-dose as required.
“As well as confirming the presence of inhibitor, laboratory testing can confirm the presence of inhibitor and also help identify any other issues, equipping the engineer with the full, diagnostic information needed to rectify them. This will ultimately minimise system problems and extend system life.”
The next steps in water treatment
The water treatment industry spent many years lobbying for the original BS 7593 standard to set out a minimum water treatment standard.
Nisar says: “The standard was first created in 2006 by like-minded people in the industry, because at the time there wasn’t really a code of practice. The standard put best practice into a document to provide a solid framework for the entire industry to work with.
“By 2019, technology was changing, and the previous document no longer reflected areas such as cooling systems,
1 https://assets.publishing.service.gov.uk/government/uploads/system/uploads/attachment_data/ file/956100/AD_L_1.pdf 2 https://shop.bsigroup.com/ProductDetail?pid=000000000030396715 3 https://shop.bsigroup.com/ProductDetail?pid=000000000030396715
>
Water treatment to be made mandatory continued
or some of the technology around low-temperature applications and how those systems needed treating with biocidal products to prevent microbiological growth.
“The other aspect we wanted to see introduced in the 2019 version was to simplify the general cleaning and flushing methodology, as there was a perception that some of the language being used didn’t translate well.”
In the two years since the 2019 revisions were introduced, manufacturers have continued to innovate with new technology, as well as investing heavily in training engineers.
“Before the Covid lockdown we used to maintain our own training schedule,” says Nisar, “inviting engineers to learn about the regulations and British Standards, and also what best practice means to an engineer.
“Awareness is much higher now, and we’ve seen a quite positive reception – most engineers have welcomed the idea that there is now a standard that covers best practice.
“At Sentinel, we have a mantra of clean, protect and maintain, and have been promoting that within the industry ever since we were first founded. Those three things ensure you’re prolonging the life of the appliance and the system as a whole. It’s quite encouraging to see that, over the years, the revisions to BS 7593 have brought in a lot of the best practice approaches that we were already promoting.
“The main point we want engineers to take away is that BS 7593 is now integrated into the Building Regulations. That elevates its status to beyond advisory and its points are now mandatory – and engineers need to make sure they understand what they need to do to stay compliant.” ■ *BS 7593: Code of practice for the preparation, commissioning and maintenance of domestic central heating and cooling water systems
Benchmark makes water treatment compliance digital
Checking system inhibitor levels is included in the Benchmark Commissioning Checklist, which gas engineers must complete whenever they install, commission or service a domestic heating and hot water system.
The new digitised Benchmark consists of apps for homeowners and engineers as an effective means of demonstrating Building Regulation compliance. The apps cover the boiler’s complete installation and servicing history, creating a digital record of all system checks, water treatment testing and procedures that have been carried out on site.
Under Benchmark, engineers must record the system cleaner and inhibitor used, the inhibitor identification number, describe the concentration test used and its methodology, and confirm that the system has been cleaned and treated in accordance with BS 7593 and the boiler manufacturer’s instructions. They must also record details of the system’s primary water system filter, and whether it was serviced.
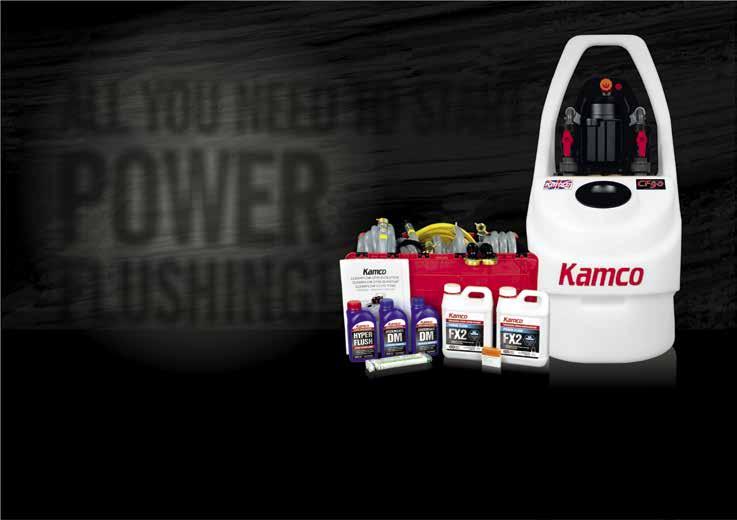
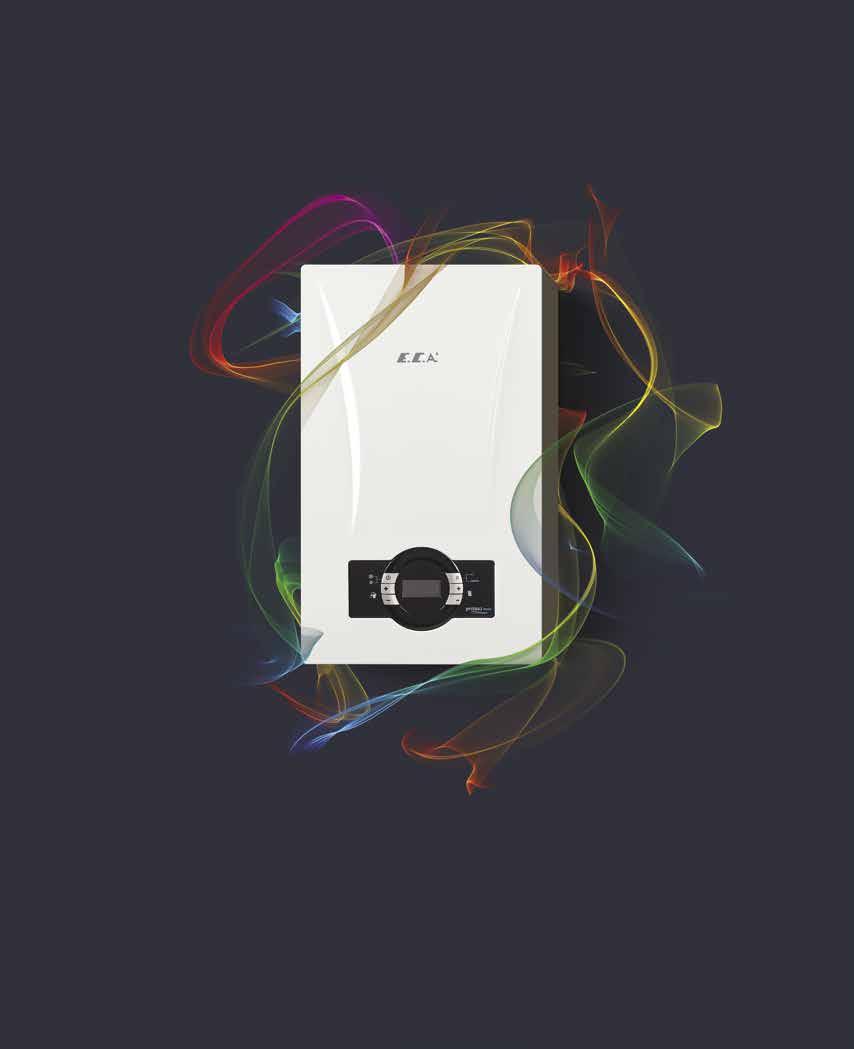
Backflow regulations: what they mean for you
Backflow presents challenges and risk for commercial and public buildings, but it can be prevented with a clear understanding of the regulations and what they mean, writes Richard Bateman, product marketing manager at RWC.
Backflow is when stagnant or contaminated water gets sucked back into the mains water supply. There are two main causes: back-pressure or backsiphonage, which occur when water is pushed in the opposite direction to its standard flow path.
Back-siphonage can occur if there is a sudden drop in pressure upstream of the outlet – for example, from a burst pipe – causing the contents of the pipework to drain towards its source.
If the outlet is open when back siphonage occurs, harmful contaminants can be pulled back into the potable water supply, such as from baths, showers and even washing machines. Ensuring the correct level of prevention or protection is in place is key.
The backflow regulations
The Water Supply (Water Fittings) Regulations (1999) for England and Wales (Bylaws in Scotland) have identified five fluid categories, each representing a higher degree of risk, to help tackle the problem of backflow. Fluid Category 1 is considered safe, while Category 5 presents a very serious health hazard.
The presence of contaminants in clean water presents a real and immediate risk to health. This is never good for any building, but it’s especially concerning in hotels, schools and hospitals, and healthcare facilities. In these spaces, occupancy is high, the system is in constant use, and potentially vulnerable or at-risk people may be using the system.
There’s also the potential for this backflow to enter the mains water supply, posing a wider public health risk to neighbouring homes and communities. In extreme cases, building owners can face prosecution. Moreover, the process of draining and cleaning water supplies results in significant disruption and water waste, with all the sustainability implications that brings.
Backflow prevention is of particular importance to refurbishment projects and heritage buildings.
The only exception where a backflow prevention device is not required relates to a water heater where the expanded water is permitted to flow back into a supply pipe. This means that no backflow protection is required on the permanent cold connection to the boiler, allowing hot water to thermally expand down the cold pipe.
The five fluid categories
The key to navigating backflow regulations is understanding the expected level of fluid risk for the building in question, and what level of protection will be needed.
Fluid categories 1 and 2 Fluid category 1 is ‘wholesome water’ that complies with section 67 of the Water Industry Act 1991 and requires no specific countermeasures or action. Fluid category 2 covers water that has altered in either appearance or taste, with likely causes being either a temperature change or the presence of micro-organisms or other substances. Here, a single check valve will suffice.
An example of this is a basin mixer tap, where hot water can sometimes pass back into the cold supply. Installing a single check valve to the cold pipe feeding the tap would prevent cross-flow.
Fluid category 3 This is water with low levels of toxicity, which nevertheless presents a slight health hazard. In these cases, double check valves must be installed. One instance of this would be a supply to an outside tap (unless this supply is feeding a sprinkler system that uses pesticides, in which case higher protection is required). The valve you choose must be compliant with the Water Supply Regulations 1999.
Fluid category 4 This is water with harmful concentrations of toxic substances. Suitable backflow prevention devices are required in these situations, such as RPZ valves.
In the event of a drop in pressure or back siphonage occurring, RPZ valves protect the mains water supply by diverting the back-fed water from the property out to the waste pipe, therefore diverting it from the main supply and drinking network, and limiting the risk of contamination. Applications include commercial dishwashers and cleaning appliances, commercial heating systems and fire sprinkler systems where antifreeze is not used.
Fluid category 5 The highest risk level, category 5, represents the most serious health hazard because of the presence of pathogens and radioactive or very toxic substances. Fluid category 5 is a highly specialist area calling for a Class 5 backflow prevention device, incorporating a Type AB air gap or equivalent.

RPZ valves protect the mains water supply by diverting the back-fed water from the property out to the waste pipe
Double check when filling new heating systems
Gas engineers need to consider backflow prevention when filling a new heating system, specifically with the heating fill point. Once the new heating system has been filled, any external flexible filling loop must be removed to protect the system from over-pressurising should its isolation valve fail.
While the filling loop is only temporarily connected, it is essential to integrate a doublecheck valve into the flexible filling loop for domestic applications, as the fluids used to clean and inhibit the system are deemed a slight health hazard.
This risk is higher in commercial unvented systems, where Fluid Category 4 prevention should be installed.
Putting maintenance first
In the high-risk fluid categories, maintenance is critical to ensure that backflow prevention devices are working correctly. While RPZ valves are highly effective, they need to be installed, commissioned and tested by an approved RPZ valve tester, who must notify the water authorities of the status of all works.
Because of their vital function, they need to be regularly tested, again by an approved installer. It is a legal requirement that this test is conducted every 12 months to ensure that the RPZ valve is operating correctly and doesn’t require further maintenance. The exact schedules will vary across local water undertakers, but full guidance can be found on their websites.■
www.rwc.co.uk
100 years of Heatrae Sadia
Heatrae Sadia recently celebrated its 100th anniversary. Here, engineering manager Gordon Bush, who has been with the business for 34 years, looks back at its fascinating journey.
In the beginning
The company’s story began in 1920 with Charles Hubert Smith founding Electric Fires Ltd. Smith is credited with inventing the first mains electric immersion heater and went on to hold many other product design patents. In 1926, the business moved to bigger premises in St Georges Street, where it made a range of electric fires, hot plates and hot water heaters. These early years under Smith’s leadership would provide the foundation for the company’s success into the next century.
In 1934, the company changed its name to Heatrae. Just a few years later, Prime Minister Winston Churchill would use the company’s hot water cylinders to draw a bath in his Downing Street Station bunker.
The 1950s and 1960s saw the business expand through a string of acquisitions. In 1960, Heatrae bought Duncan Low, a manufacturer of industrial electric and steam liquid heating equipment, and become Heatrae Industrial.
In 1961, the business set up Heatrod Elements in Gorleston to produce immersion heaters; just a year later it acquired Electroway, a manufacturer of stainless-steel catering equipment. Around this time, Heatrae’s parent company merged with British South African Co to become Charter Consolidated.
The business we know today
It was not until the 1970s, however, that the business as we know it today began to take shape after its move to its current site, Hurricane Way, Norwich, in 1970. Sadia Water Heating was acquired in 1974 to complement Heatrae’s existing range, and three years later, the business would bring both brands under one banner as Heatrae Sadia.
The 1980s saw further growth as the company was bought by Valor and expanded into new markets through three further acquisitions. Unvented water heating was also adopted in the UK around this time.
Making way for Megaflo
Innovation came in the 1990s when the business secured the design and manufacturing rights from Fabdec for the Megaflo, which would be manufactured in Norwich. Going on to become one of the leading domestic hot water cylinders, Heatrae Sadia’s range of Megaflo hot water cylinders combines high performance with optimum efficiency to give fast-filling baths and powerful showers.
Thousands of G3-qualified gas engineers choose Megaflo to work in conjunction with gas heat-only boiler systems or electric boilers each year.
Heatrae Sadia’s parent company changed hands twice during the decade and, by 1996 the business had its first robot on the production floor.
The new millennium saw major changes as Newmond merged with Baxi Heating. Powermax production was moved to Norwich and Amptec would be acquired from ElectroHeat ahead of Baxi Heating’s merger with De Dietrich and Remeha to form the BDR Thermea Group in 2009.
In 2012, the business again made history as it provided packaged heating solutions for developments at the London Olympics. Heatrae Sadia also produced a chariot included in the Lord Mayor’s procession as the Olympic torched passed through Norwich on its way to the capital.
2021 and beyond
As Heatrae Sadia embarks on the next century of its history, a new chapter is beginning. As part of BDR Thermea Group, the Heatrae Sadia brand has the financial and technical backing to prepare it for the energy transition and the drive for net-zero carbon.
Supporting sustainability and innovation, Megaflo Eco cylinders are taking part in trials for the USER project and test demandside response, by connecting new or existing hot water cylinders to the grid with a smart interface unit.
This then enables the hot water store to become a grid-interactive storage heater, to heat hot water when there is low-cost electricity available. With wholesale electricity prices sometimes dropping to zero, or even negative values, this could potentially lead to households being paid to use electricity in some cases.
While the heating and hot water landscape may change, one constant remains: Heatrae Sadia will continue to support generations of heating engineers now, as it has done for the past 100 years. ■
www.heatraesadia.com
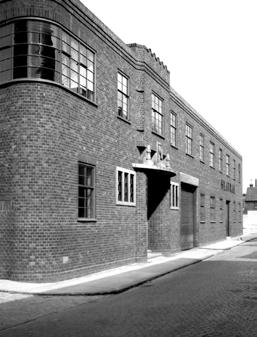
The changing face of advertising in the 1920s and 1930s
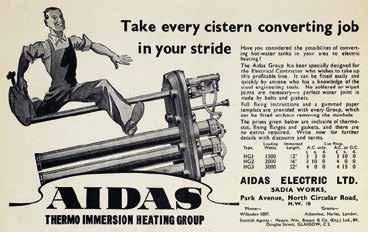