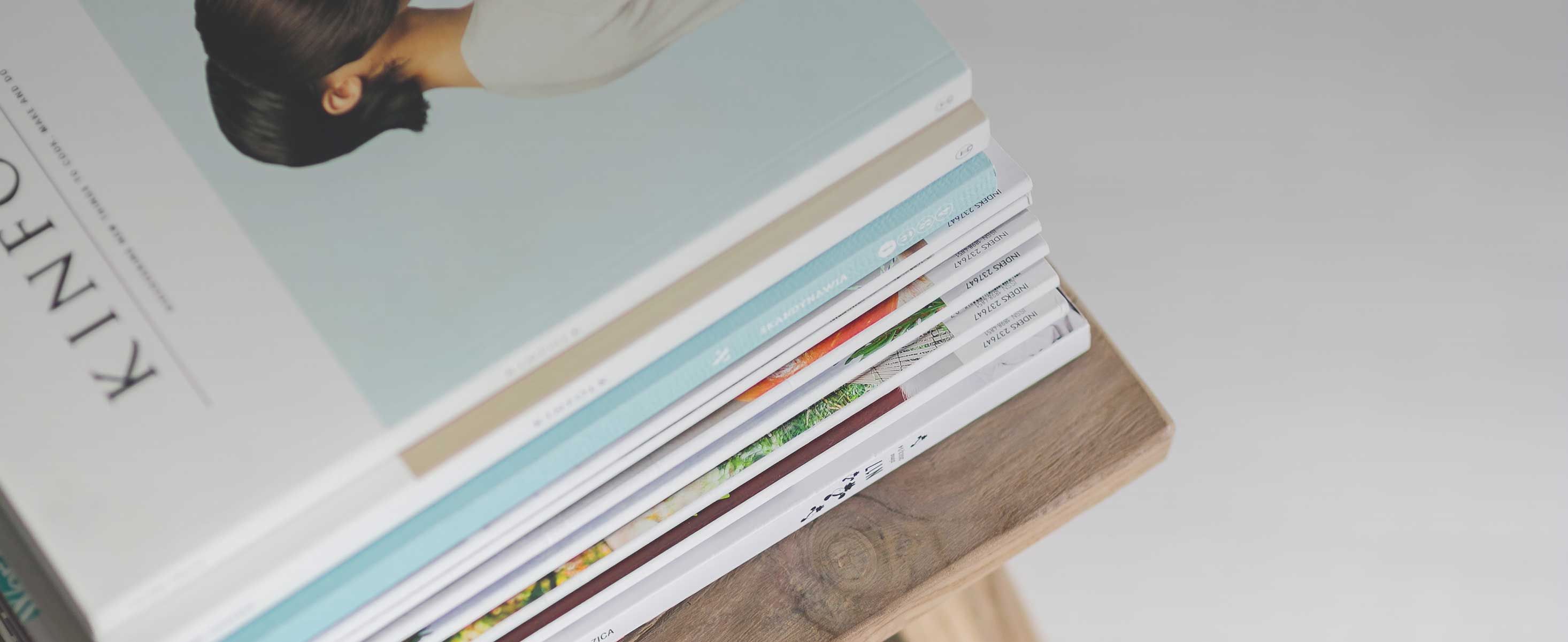
6 minute read
All change for our industry’s survival
We are on the cusp of a change in history: if our trade is to survive and help the UK transition to a low-carbon future, we have to embrace a complete and utter transformation of training, writes gas trainer and assessor Joshua Graves.
We have to completely change the training of new gas engineers and the upskilling of our current workforce to be able to deliver a transition to hydrogen.
Getting the training right is going to be extremely important. There are many people who are far cleverer and more qualified than me, brimming with excellent ideas, innovations, research and ways to deliver the transition to hydrogen. However, to bring those ideas to life safely, we are going to need an army of well-trained and competent gas engineers.
Very soon – within the next five to 10 years – we are going to face a large skills gap. More than one-third of gas engineers are in their late 50s to 70s. The oldest person I have personally retrained is 77 years old. Engineers such as and its future. Where do entrants invest their time? Do they go down the heat-pump route, solar, F-Gas training for air conditioning, or do they stake their future career on gas? The choices that they make will be critical to the future of the gas industry.
Joshua Graves is a gas trainer, assessor and IQA at specialist centre Southwest Peninsular Training. He has carried out research in his classroom and centre into how training for the transition to hydrogen from natural gas would be affected and how he believes it could be improved.
Many thousands will need to be trained to replace those lost through natural attrition and to fill the gaps left by an ageing workforce. The entire current Gas Safe registered workforce will require upskilling to meet the requirements for hydrogen, all with learning programme (MLP). The cost of a domestic MLP typically can be £2,000-£3,000 – but it can be as high as £8,000, depending on class sizes and the centre.
Colleges tend to be cheaper and account for most courses but often take far longer to train entrants because the gas option is included in some Level 3 plumbing courses, which can be four years long. A typical MLP can take up to three years to complete but has a minimum six months’ duration.
The domestic MLP has also just been made harder. Since September 2022, the hourly in-centre training requirement is now 266 hours for core, 35 hours for CENWAT and 7 hours each for CKR1 and HTR1, etc.
Thousands of pounds
being made more difficult and more expensive to join.
How could training be standardised and simplified?
There was a surge of online qualifications during the Covid pandemic. Now IGEM/IG/1, which covers the standards of training required for new entrants, insists that all guided learning hours need to be taken under the direct supervision of a trainer either in the classroom or online through webinars etc. This is very inflexible and creates the time commitment problem.
I believe that if we are to completely and utterly transform our industry, we need to embrace online learning and put more emphasis on enabling the student to carry out their own research.
these are on the verge of retiring and they regularly tell me that if they have to retrain for hydrogen at this stage in their career, that could be their tipping point to retire earlier than planned.
It’s not just engineers who are looking to leave. Older trainers, assessors, IQAs (internal quality assurers) and EQAs (external quality assurers) are making the same considerations, which will reduce the availability and the quality of training for future engineers.
This is in addition to another challenge facing new entrants: choice. There is a great deal of uncertainty over the gas industry fewer and fewer training centres and trainers to accommodate the demand. Training centres and colleges will require upgrades to their equipment and assessment procedures.
Alongside the transition, regular gas work will still need to be carried out on breakdowns, repairs, upgrades and replacing faulty equipment. It all poses a very significant challenge.
It’s expensive
But there are barriers to training. To become a Gas Safe registered engineer, you need to take a route of entry such as an initial gas qualification through a managed
If an entrant now wants to undertake the CCN1 core with boilers, cookers and fires as appliances, it will take 43 days plus an extra four days for the MLP exams and then a further five days for ACS assessment. So 52 days are required in training and assessment, which can cost tens of thousands of pounds.
As a business owner, what choice do you make? Air source heat pump courses, oil, F-Gas and electrical qualifications can all be gained as short courses delivered in far less time for less cost with fewer prerequisites. The gas industry is losing new entrants simply because it is
My proposal is this: we could take all the classroom theory (at least the first 10 days of an MLP) and turn it into an initial course that anyone can take, rather like the theory driving test. Young people are generally very IT-literate and classroom training is being viewed as less valuable: after all, it’s only as good as the trainer’s knowledge and understanding of the subject.
Quicker engagement
If the new entrant enjoys what they learn online, then they are engaged from the outset. A mixture of videos, simulations, written assignments and tests could make the training more varied and easier to absorb for a wider range of learners. Translation of the online content would also be far simpler and make learning much more accessible. Another benefit is that anyone who feels it’s not for them can abandon it without wasting the trainer’s or employer’s time.
We place a strong emphasis on continuous professional development (CPD) and engineers are required to be computer literate and able to do research for themselves. So why not train them this way from the start? They could then understand and use, for example, the IGEM Hydrogen Knowledge Centre, more effectively.
Online courses open the doors to a wider pool of people, bringing greater diversity to the industry. Upon successful completion of the online course, the learner could sit a reduced MLP with a Gas Safe registered company to gain the practical skillset, greatly offsetting the cost of training to the individual and the employer.
Personally, over the past two years, I have used online courses to gain my assessor and IQA qualifications. I am currently studying Honour’s Degree-level Health & Safety, which is all online at my own pace, time and convenience with very little interaction with my tutors and with no in-class time.
We need to move on Online learning is a powerful tool with huge benefits and we are missing out. We must move on from traditional training and assessment mindsets and techniques if we are to recruit, retain and upskill more engineers.
The assessment process itself could benefit from online learning. Instead of the ACS burden of a series of exams and assessment every five years, why not make online learning a CPD requirement?
Here, the engineer might have to study for a regulated number of hours per year to keep up to date, but at a time and location convenient to them, and with only a smaller set of assessments every five years.
This could also bring down the costs and reduce the load on the engineer being re-assessed, as well as the training centres, which could focus more time on training new entrants. It would also ensure that there are no large gaps in an engineer’s knowledge in the five-year span: technology will have to move very quickly in this transition.
I would also recommend standardising the in-class practical training for new entrants to a set of 18 days for all core qualifications, so that every
32.5 million engineer, regardless of how they joined the industry, receives the same level of input and supervision from the trainer.
The additional benefit of putting the theory online and minimising time on in-person training is that a smaller number of colleges and training centres can potentially train engineers far more quickly to meet the needs of the transition to hydrogen. And augmented reality could be brought in for some practical tasks such as fault-finding.
There is also the possibility of further reducing the practical elements of the cores: for example, hot works such as soldering can be replaced by pipe jointing methods such as press fitting and corrugated stainless steel tube. Some sites don’t allow hot works so could having to train soldering be removed from the practical? Yes it could, in some instances, which could allow for further reduction of in-class time.
Between 1966 and 1978, 32.5 million appliances were converted from town gas to natural gas for 13 million domestic customers.
Embrace the new
It took 12 years for the last transition from town gas to natural gas and now we need to train a workforce capable of delivering a transition to hydrogen. We must embrace new ideas, innovation, research and training methods and step out of our comfort zones to achieve this.
It’s a once-in-a-generation change that could deliver a carbon-neutral future for years to come, and it’s an exciting time to be part of the gas industry.
Is it going to be a challenge? Yes. Is it impossible? No. ■