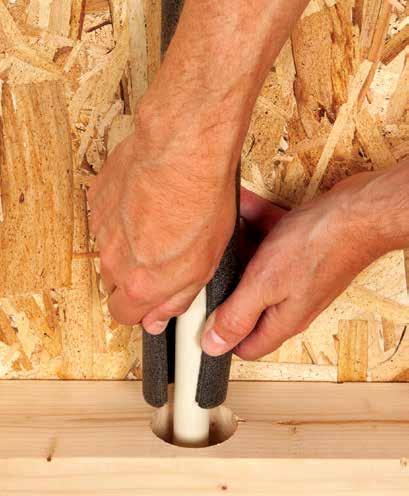
8 minute read
Winter planning
The heating survival guide
How you can help to prevent critical winter-related heating and plumbing issues, by Nigel Sanger, divisional director of technical support at RWC UK.
As the nights grow longer and colder during the winter, gas engineers receive an increasing number of emergency callouts to fix broken plumbing and heating systems.
These issues can range from ineffective heating to frozen pipework. Prevention is the best medicine, so here are three ways that systems can be winterproofed to avoid disruption and keep homeowners comfortable.
Prevent pipework from freezing
Frozen pipes can cause major damage and affect the performance of hot water and central heating systems when they are needed the most. In 2018, £194 million was paid out to help homeowners deal with burst pipes due to bad weather, according to the Association of British Insurers.
Pipework can be futureproofed for all seasons while carrying out the initial installation by keeping these six Ps in mind: preparation, pressure, placement, protection, prevention and programming.
Pipe layouts should be considered carefully to ensure optimal performance. Best practice is to avoid placing pipes outside or in rooms that are prone to getting cold, such as lofts or basements. If pipework does need to be run in these areas, they should be adequately protected and lagged with insulation. Without lagging, water inside them can freeze, creating internal pressure that can cause them to burst.
Plan ahead and drain any external pipes in unoccupied new-builds, and advise your customers to do the same when freezing weather is forecast. This is particularly important for external taps that are exposed to plummeting temperatures. The process of draining external pipes is simple: close the internal shut-off valve to stop the mains supply and then drain the exposed pipe by running the tap. Once the cold weather has passed, open the valve to turn the water supply back on.
Engineers can also avoid the perils of frozen pipes by keeping them warm at all times. As SSE advises, thermostats should be set at 12-15°C when the property is unoccupied to prevent internal pipework from freezing. Smart heating controls can help deal with these concerns when the properties are left vacant, so homeowners can ensure their heating system is safe and can be operated if they are away.
Anti-freeze – not just for your car
Another area that needs winter planning is the installation of underfloor heating (UFH). In new-builds or renovations, UFH projects can span over weeks and even months. It’s not uncommon that UFH pipework is installed and screed is laid months before the property is ready for use.
If the UFH pipework in the screed is subject to sub-zero
conditions while the rest of the project is being completed, the water in the pipes can freeze. This runs the risk of the pipework weakening and splitting as the water expands. Avoid this by adding anti-freeze to the water in the pipework. Once the winter has passed, this water can be flushed out of the system and replaced.
Smart heating controls
Fuel poverty hits home for millions of people in the UK: according to government figures, approximately 2.4 million households lived in fuel poverty in 2018 and couldn’t afford to keep their homes heated adequately.
Smart heating controls can help to battle fuel poverty because they allow people to heat specific rooms rather than the whole house. Heating the whole house can result in energy
wastage and higher heating bills when not all rooms are being used at the same time.
Smart heating controls can manage the heating temperature and schedule for both UFH and radiators through a single control. These controls can be programmed to deliver the desired temperatures in certain rooms, at specific times throughout the day.
Despite the energy saving benefits, smart heating controls still aren’t commonly used because of their perceived cost and disruption. This is where heating engineers can be clever in the way they communicate these options to both the customer and building contractors. While there’s an initial up-front cost of installation, the energy savings over the years do pay for the technology. Managed from a smartphone app or directly through the thermostats, smart heating controls can help to cut energy bills by up to 30 per cent.
Beating the winter blues
With careful planning and the use of innovative technology, most problems that come with the winter season can be avoided. And gas engineers can ensure they help prevent water and energy wastage to build greener and more sustainable homes, ensuring homeowners have comfortable, warm and safe winters. ■
www.johnguest.com
WiFi Inside
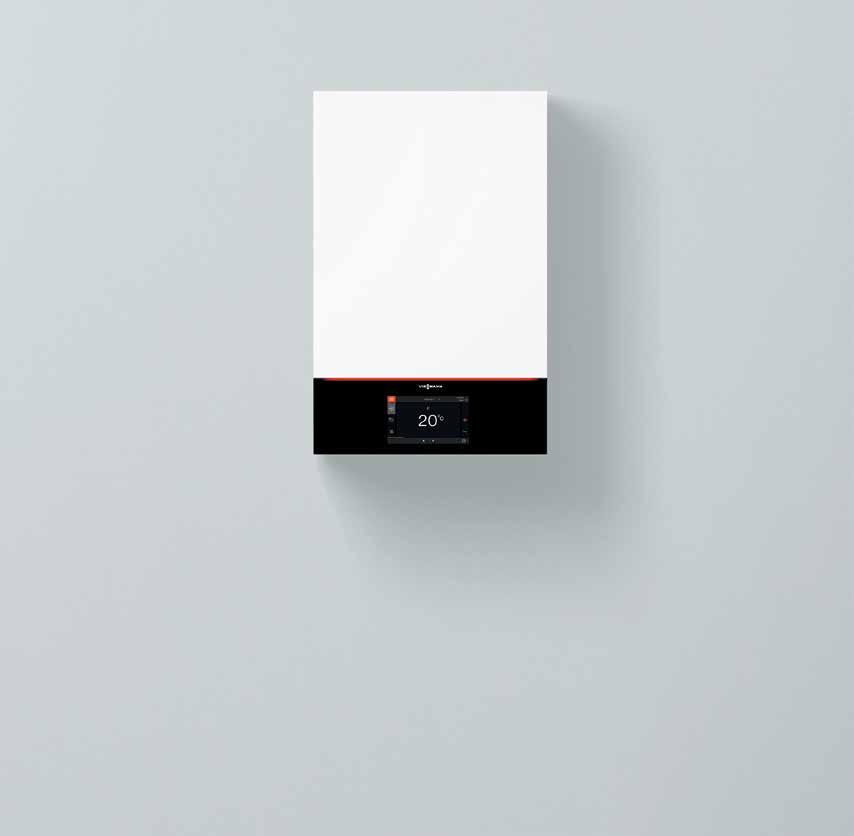
Top tips to avoid frozen condensate
What lessons have we learned about how to avoid the problem of frozen condensate during prolonged cold spells? David Smith, CEO of Condensate Pro, sets out the steps gas engineers should take to help avoid the issue.
Back in 2018, when the Beast from the East led to tens of thousands of boilers breaking down because the condensate had frozen, the industry called for help. Boiler manufacturers were inundated with customers calling because they thought (wrongly) that they were covered by their boiler warranty.
The period not only put householders at risk because they didn’t have any heating, but also gas engineers who were driving in treacherous conditions. The media and papers got involved, asking how this had happened and what was being done to make sure it does not happen again. And so we learned from the past.
The past two winters have been mild: however, more than 4 million boilers will have been installed. BS 6798* and the manufacturers’ instructions state what must be carried out on all external condensates. Benchmark requires recording that everything installed complies with the required standards and regulations, and the HHIC advises that you must check protection when boilers are serviced.
When you consider that the future may include hydrogen boilers, which will create even more condensate, there has never been a better time to evaluate and highlight what is required.
Professional heating engineers need materials to be fit for the job and easy to install in all weather. This has been an issue in the past because some of the materials that they were advised to use are not compliant without carrying out work that’s nigh on impossible.
Not to forget the time it takes trying to make it look acceptable on the customer’s home.
It’s been a pain for professionals ever since condensing boilers were first introduced, to the point where urban myths have manifested over the years: for example, that 40mm uninsulated is acceptable, or that you don’t need to insulate in certain areas of the country. As we know, both are incorrect.
We don’t start to add anti-freeze to our vehicles just when the winter comes: it’s added as standard and maintained on the annual service to make sure that, when winter arrives, the vehicle is protected. The same goes for us as professionals: householders don’t know whether their condensate needs to be insulated – they trust you to provide that protection and check and maintain.
Looking at issues in the past, let’s look at the salient parts of BS 6798 and the manufacturers’ instructions to which boiler condensates need conform: • All insulation materials used need to conform with the manufacturer’s instructions and, when installed, should be
UV-protected, weather-proof and maintainable. • Make sure the materials used are sealed correctly to make sure there is no ingress of water between the pipe and the insulation. Water ingress is why
many insulated condensates have failed in the past. • Look for an internal solution.
This may involve more work and materials and liaising with your customer to advise why this is the most suitable solution. • If the condensate has to be terminated outside, make sure you reduce the external pipework as much as possible. • External pipework must be a minimum of 30mm interior diameter and fully insulated in line with the insulation manufacturer’s instructions. • Where the condensate pipe enters the building, it must be sealed correctly, be durable in all weathers and temperatures, and maintainable. • All internal pipework in unheated areas must be treated as external pipework. • When connecting to other internal pipework, such as sinks and washing machines, make sure it’s insulated if it then goes outside. You should also make sure that no food or other materials will slow the condensate water or cause a
blockage. It may be better to have a separate condensate waste. • All pipework must be as vertical as possible, keeping bends and 45° angles to a minimum, and making sure the burr of the cut pipe is removed. • If terminating to an open drain, make sure the open end is below the drain and above the water level and cut the end at 45° to protect from wind chill.
This is sometimes impossible: however, the end of the insulated pipe is where there is the main risk of freezing and blocking, so protecting from wind chill is important. • Other protection measures can be added to insulated pipework: for example, trace heating/ high-volume condensate traps.
These must be insulated. • Make sure the householder is made aware of external condensates and where they are terminated and that they should be inspected during prolonged cold weather. • Make sure the condensate is inspected and is to current standards when you’re carrying out boiler servicing and other safety checks.
Boiler manufacturers’ instructions may have other requirements, and you should always refer to these – for example, providing an air break that protects the boiler from flooding but still protects in the winter time.
As we have seen, climate change is bringing extremes in all weathers and, with the introduction of hydrogen in the future, correct condensate protection has never been so important. Let’s show that we have learned from the past and make condensate problems history. ■
condensatepro.co.uk
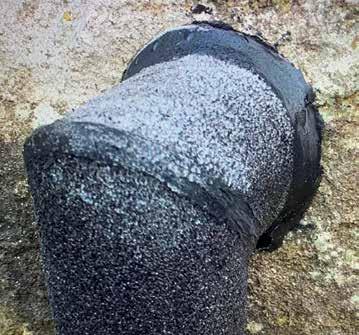
*BS 6798:2014 – Specification for selection, installation, inspection, commissioning, servicing and maintenance of gas-fired boilers of rated input not exceeding 70kW net