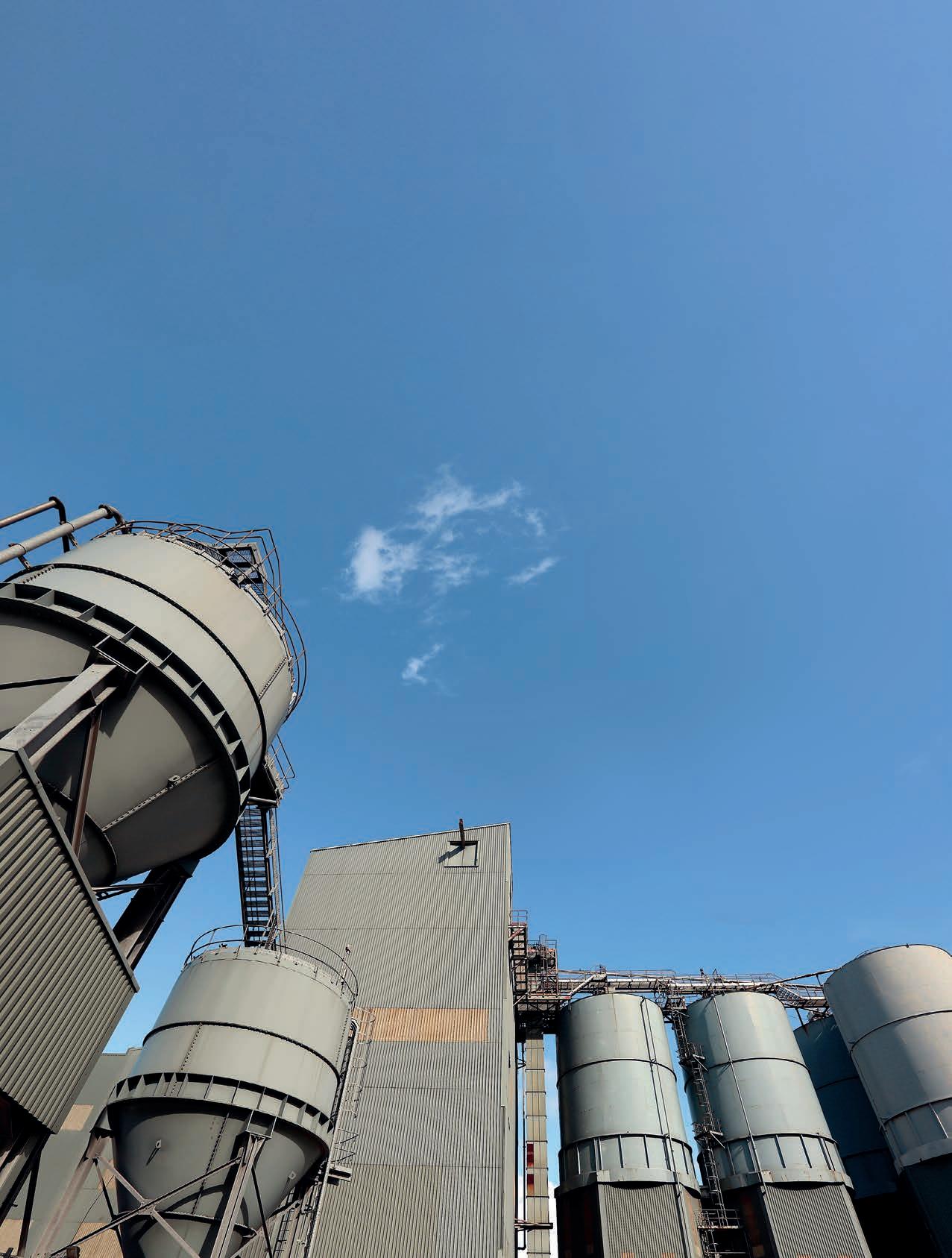
5 minute read
Set for change
Nina Cardinal, National Technical Manager at Hanson Cement, discusses how cement and concrete can be more eco-friendly
Globally the cement industry alone accounts for 7% of CO2 emissions, while in the UK this fi gure is 1.5%.
It is no secret that the production of CEM I Portland cement (PC) is energy intensive and produces CO2. It is for this reason that many manufacturers have invested heavily to improve the effi ciency of the production process and increase the amount of alternative fuels used to power the kilns.
Hanson Cement is taking part in a research project funded by the Department for Business, Energy and Industrial Strategy (BEIS). It is looking at the potential for hydrogen and plasma technology to reduce carbon emissions through switching away from fossil fuels, which could lead to cement and lime kilns operating with a net-zero carbon fuel mix. Its Ribblesdale cement works in Clitheroe, Lancashire, is the site of trials to demonstrate the zero-fossil fuel operation using hydrogen and biomass fuels in the cement kiln. The project’s results will be shared with wider industries to maximise the environmental benefi t of the technology, which could save around two million tonnes of CO2 a year if implemented across the UK cement industry; equivalent to the annual emissions from 266,000 households and reducing UK greenhouse gas emissions by 0.6%.
Cutt ing CO2 emissions and conserving natural resources are obvious priorities for everyone involved in the construction industry. In the UK, Hanson has already achieved a 30% reduction in CO2 emissions since 1990 across the business, and has set an ambitious new target of a 50% reduction by 2030.
GGBS
In addition to the use of alternative fuels, the use of products to replace some of the cement content in concrete, grout and mortar is also helping to signifi cantly reduce CO2 emissions. One of the most eff ective alternatives to PC is ground granulated blastfurnace slag (GGBS). There are environmental
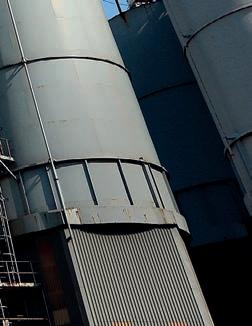
Flood defence walls at the New Cut River in Ipswich used concrete containing up to 70% GGBS
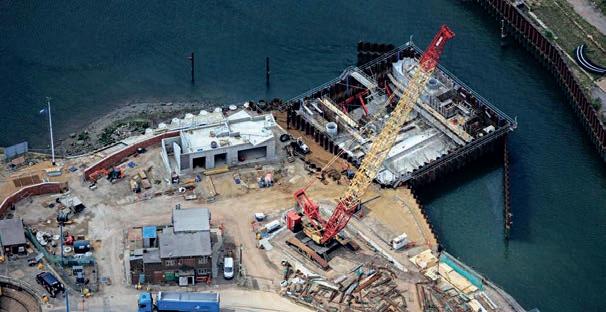
benefi ts to be gained from its use both in its production and throughout the life of the structure.
Portland cement is made by mixing calcium carbonates (eg limestone, chalk) with silica and aluminates (such as clay, marl or shale). They are burned in a rotating kiln at a temperature of 1,450°C and, during the process, the calcium carbonate decomposes to calcium oxide and CO2 is released. At the same time the carbon in the fuel used to power the kilns combines with oxygen to give off further CO2.
The manufacture of GGBS, however, requires less than one-third of the energy and produces less than 10% of the CO2 emissions. This is because it is a byproduct of the iron-making industry: slag is produced simultaneously with iron in a blast furnace and is an inevitable consequence of the iron production. For a comparison of the environmental impacts of GGBS and Portland cement see below.
To optimise the cementitious properties of the molten slag leaving the furnace, it is cooled rapidly before being dried and ground to produce a fi ne white powder that has similar characteristics to those of Portland cement. Energy is only used in the drying and grinding process as the power used in melting is all allocated to the iron produced.
The major use of GGBS is in ready-mixed concrete, with more than a third of all UK deliveries containing the product. Replacing one tonne of CEM I Portland cement with GGBS in a concrete mix reduces the embodied CO2 by approximately 780kg.
GGBS can replace a substantial part of the normal PC content – generally about 50% and up to 95% in
Comparison of environmental benefi ts of GGBS and Portland Cement (PC)
Environmental issue Measured as Impact
One tonne of GGBS 1
One tonne of PC
Climate change CO2 equivalent 0.08 tonnes 0.86 tonnes
Energy use Primary energy 2
1,390 MJ 4,200 MJ
Mineral extraction Weight quarried 0 1.35 tonnes 1. No account has been taken of the impacts of iron making because the slag is created regardless of whether or not it can be used. 2. Includes energy involved in the generation and distribution of electricity.
special applications – and is used in other types of concrete, including site-batched and precast, mortar and grout.
It can be used anywhere concrete is needed – from sustainable housing development and soil stabilisation to wind farms and road building – and is typically used in major construction projects such as bridges and sea defences. There are also other environmental benefi ts: GGBS does not require the quarrying of new materials and the slag used will not be disposed of as landfi ll.
Each year, the UK uses more than two million tonnes of GGBS as a replacement for cement, which: Reduces CO2 emissions by almost 1.56 million tonnes Reduces primary energy use by 1.6 million MWh Saves approximately 2.7 million tonnes of quarrying.
The use of GGBS also increases the long-term durability of concrete, further cutt ing a project’s environmental impact by reducing the amount of repair and maintenance needed, and extending the service life of concrete structures. It provides: Enhanced resistance to sulfate att ack (both the ett ringite and thaumasite forms) Lower ingress of chlorides into the structure Minimised risk of alkali silica reaction Bett er resistance to acid att ack Lower propensity to delayed ett ringite formation Reduced risk of thermal cracking.
GGBS case study
Almost 5,000m3 of concrete containing up to 70% GGBS have been used to construct a 20m-wide tidal barrier gate and piled fl ood defence walls at the New Cut River in Ipswich. The £21m project for the Environment Agency will protect around 2,000 properties that are at risk of fl ooding.
In total approximately 1,000 tonnes of GGBS were used in the project, saving 780 tonnes of CO2 emissions, which is equivalent to taking around 170 cars off the road for a year. The use of GGBS also enhanced the durability of the concrete, as concrete containing GGBS has a fi ner pore structure, reducing its permeability and making it more chemically stable and resistant to sulfate and chloride att ack. The main barrier structure also required a low-heat concrete due to the scale of some of the pours, which were up to 730m3. Using GGBS in the mix reduced the heat of hydration, protecting the structure from early-age thermal cracking.
There is litt le doubt that, within the construction industry, cement and concrete production have been responsible for a signifi cant contribution to CO2 creation globally. It is time now, for these industries to innovate and invest in change.